大连海洋大学船舶辅机拆装实习报告文档格式.docx
《大连海洋大学船舶辅机拆装实习报告文档格式.docx》由会员分享,可在线阅读,更多相关《大连海洋大学船舶辅机拆装实习报告文档格式.docx(41页珍藏版)》请在冰豆网上搜索。
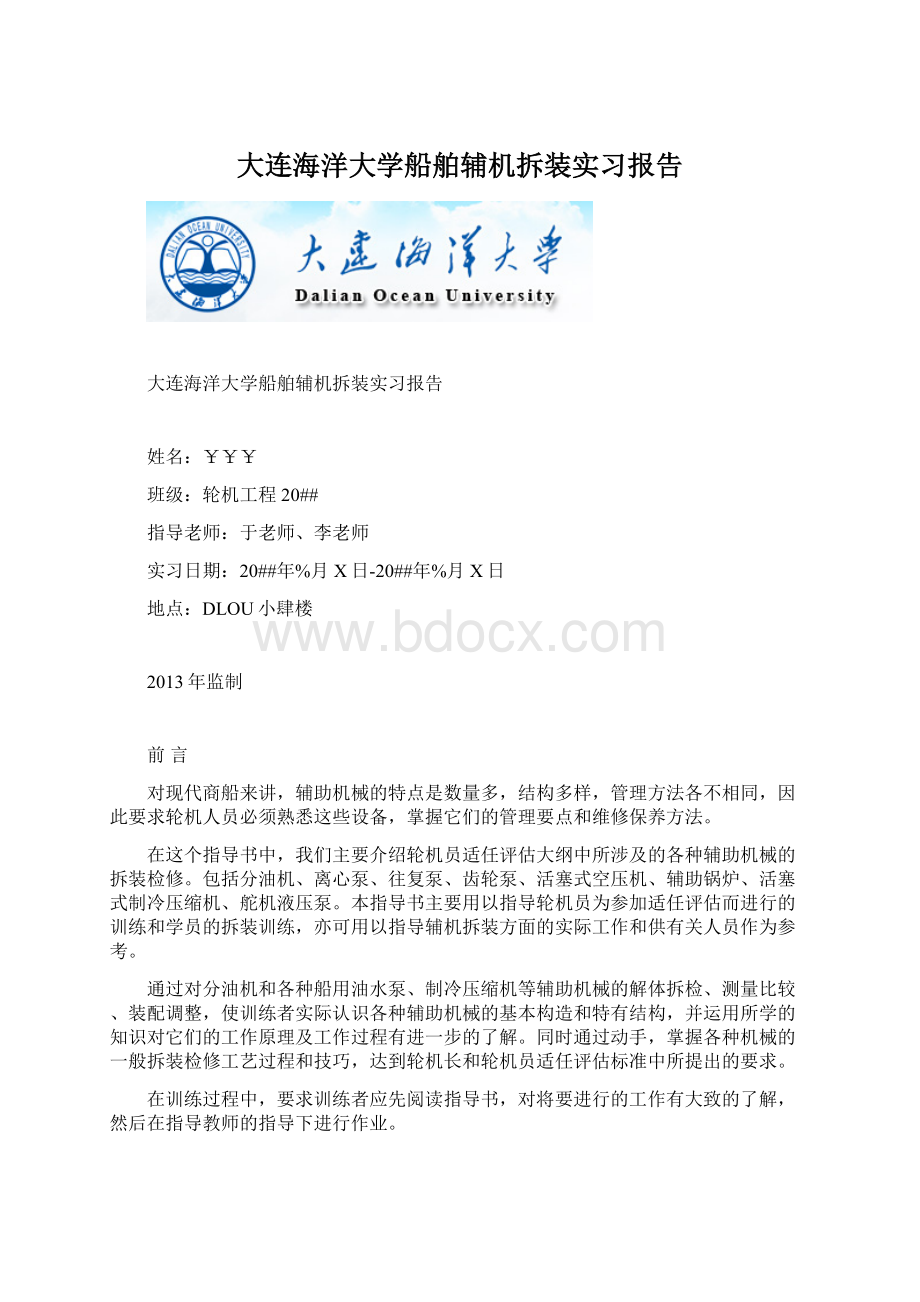
我们所说的一般意义的拆装工艺,通常包括拆卸、清洁、检查、修理、装配、调试等过程,而在这些工艺过程中,检查、修理是我们的主要目的。
众所周知,由于长期工作和工作条件的影响,机件一般都会出现磨损、疲劳、腐蚀等故障。
这些不可避免的故障其后果大体上有因磨损而尺寸改变,从而伴随着配合间隙的改变;
由于多半是不均匀磨损而带来几何形状的改变;
疲劳的后果是裂纹和破断;
腐蚀将改变机件的表面质量。
因此设备的拆解检验一般可归纳为下列几个方面:
1.机件的尺寸和磨损程度,以及配合间隙的变化情况。
2.机件的几何形状。
如椭圆度、圆锥度、垂直度、弯曲和扭曲、外形轮廓的变化。
3.机件的表面形状。
如裂纹、拉毛、剥落、腐蚀麻坑、表面粗糙度的改变;
机件的过热变色。
4.机件物理化学机械性能。
如弹簧的弹力、机件的表面硬度、轴承合金和瓦底的结合强度等。
5.组件的配合情况。
如组件的同轴度、平行度、径向跳动及啮合情况、连接件的连接强度、机件配合的严密性等。
有关机件的配合间隙可以参考设备说明书。
机件的椭圆度和圆锥度可以参考以下经验公式计算:
椭圆度:
圆柱体同一水平剖面内最大与最小直径之差δ
δ=D-d(mm)
D—圆柱体同一剖面内最大直径
d—圆柱体同一剖面内最小直径
圆锥度:
圆柱体在沿直径的纵剖面内其直径由一端向另一端逐渐增大或减小的形状偏差ε
ε=D-d(mm)
D—圆柱体在同一纵剖面内的最大直径
d—圆柱体在同一纵剖面内的最小直径
第二节常用规则与技巧
一、拆卸和装配的一般技术要求
1.拆卸的一般原则
①拆卸的同时就要考虑到下一步检修和装配
把拆卸过程看成调查研究的过程。
②能不拆的尽量不拆,不随意扩大拆卸范围。
③先拆成部件,再拆成零件。
先拆外部件,再拆内部件——先外后内;
要先拆易损件、附属件,后拆主要机件;
2.装配的一般要求
应严格按照装配工艺的技术要求进行安装。
总的要求是:
①保证各相对运动机件之间的正确配合和适当间隙
②保持机件固定连接的可靠性:
不松,也不可过紧。
③保持各机件轴心线的正确关系(同心度问题)。
④保证定时、定量机构连接正确。
⑤保证运动机构动力平衡,特别是高速旋转机构。
⑥保证装配过程充分清洁:
用油、空气洗吹干净。
二、一般机件的拆装技巧
1.记号及标签:
相配合件要做记号或贴标签。
用样冲、号码或油漆等。
注意不能做在精加工面上。
2.螺纹连接的拆装技巧
A.拆卸
①.双头螺柱的拆卸
在没有必要时,无需拧出双头螺柱。
如确需拆卸拆卸的简便方法是在双头螺柱的螺纹上拧两个螺母,其中一个作锁紧螺母,拧动另一个螺母,就可将双头螺柱拧出。
②.对于生锈的螺母不能旋出时,可用下列方法:
a.先将其拧紧1/4圈,然后旋出。
b.在螺母棱边轻轻震动,然后旋出。
c.在螺母和螺柱之间灌入煤油或渗透剂,浸泡20~30min后再旋出。
d.用酒精喷灯将螺母均匀加热后再旋出。
以上办法不奏效时,才将螺母破坏取出。
③拧断的螺柱可用下列方法取出
如断头螺栓有一部分仍在螺纹孔外,可采用
a.螺柱顶端锯一个槽,用螺丝刀拧出。
b.把螺柱两侧锉平,用扳手旋出。
c.在断头螺柱上焊一根折角钢棍,转动钢棍拧出螺柱。
d.焊上一个螺母,拧转螺母带出螺柱。
如螺栓全部断在孔内,可用下列方法
a.在螺柱顶部钻一个小孔,攻反丝,旋入螺钉,带出螺栓。
b.在断头螺栓中钻孔,孔中打入一根经过淬火处理的矩形截面钢棍或有左旋螺纹槽的圆锥杆,把螺栓拧出。
c.如以上方法不奏效,可用比螺纹底径小0.5~1.0mm的钻头钻去螺柱,再用与原螺柱螺距相同的丝锥攻一下,即将螺柱破坏掉即可。
B.装配
螺纹连接装配中应注意以下几点:
①.螺母必须能用手较容易地拧到配合位置,然后再用扳手拧紧。
②.安装时螺纹必须清洁无物,必要时要进行润滑。
③.螺母端面必须垂直于螺纹的轴线。
④.一个机件上有多个螺柱固定时,应按一定程序逐次拧紧。
拧紧程序:
一般是从中间到两边,对角交叉,按拧紧力矩要求逐次上紧。
3.紧配合的拆装
紧配合包括过渡配合和过盈配合,如轴承、齿轮等,在拆装时要特别注意防止损坏。
A.紧配合件的拆卸
①.用专用冲头:
如拆卸气阀导管;
②.用专用拆卸器:
如用丝杠顶出齿轮、叶轮或皮带轮;
③.拉马:
如拉出轴承。
B.紧配合件的装配
①.严格保证清洁,以防杂质破坏配合表面;
②.了解配合性质和要求,避免出现不正常配合。
过松——机件会形成相对运动,影响运动精度。
过紧——机件装配应力过大,引起机件过早损坏。
三、拆装安全技术规则
1.使用工具要恰当
①.尽量少用活动扳手。
能用梅花、套筒扳手的地方不用呆扳手、活动扳手。
②.不要随意在扳手上接加长杆,以防力臂过大拧断小螺栓。
③.不要随意用锤击打扳手进行螺母的拆装。
④.扳手,尤其是活动扳手不能当锤子使用。
⑤.拆装螺母时姿势要站稳,左手尽量抓住固定物,右手用力,一般向怀里拉,不要向外推。
这样便于用力,又不伤人。
⑥.一般螺丝刀不能当凿子用,容易打坏木柄,伤及工件表面。
⑦.不同材料、不同表面用不同材料的锤子击打。
⑧.用锤击打机件时应隔着垫块,否则会造成机件变形损坏。
2.防止事故和损伤
①.拆不开的机件应了解具体结构,不可硬拆。
尤其要查明有无暗螺丝,以免拆坏机件。
②.拆下的机件应有次序地放置,零部件放在容器中要妥善保管,以防丢失。
精加工面应置于木板上,防止碰伤。
笨重机件应放稳。
③.如检修过程较长,应防止机件变形。
一般轴类应竖直放置或经常变动摆放的位置。
④.拆下的螺母应集中放置,在不影响其他机件拆装时,螺母可拧在原来的螺柱上。
⑤.拆下的管子和机件的孔口,应用木板、厚纸板或木塞封口,或用破布封口包扎,但不可用棉纱或破布堵塞。
⑥.精密偶件应成对放置,对用平面配合密封的机件不能任意调换。
⑦.用台钳夹机件应选择合适方向、位置,防止机件变形。
钳口与工件间应以退火铜垫隔开。
⑧.拆装过程中严防各种杂物落入机器内部。
3.关于起重工作
进行起重工作时,应注意和遵守如下主要安全规则:
①.禁止起吊超重机件。
②.捆绑机件时应避开仪表、管路,防止绳索拉紧时将其压坏。
③.绳索与机件尖角处接触时,应垫上纸板或抹布防止磨断。
④.吊钩的位置和绳索的悬挂中心线应与机件中心线一致,防止起吊时机件甩荡伤人。
⑤.吊前应仔细检查吊索是否可靠,各处绑扎是否正确且平均拉紧。
起吊重机件不要太猛,在离地5~10cm时,应用橇杠敲打绳索数次以检验索具可靠性。
⑥.起重过程要统一指挥,协调配合。
在吊起机件下面不准有人,并避免在机器上空吊运机件。
第三节拆装的准备工作及工艺文件
一.拆装的准备工作
1.熟悉资料
①.阅读说明书
了解设备的结构及性能参数,以及各部件尺寸、装配间隙等。
②.查阅图纸
主要是装配图。
搞清各零部件的位置关系,初步掌握拆装顺序;
了解各结构的关键部位,从而确保在拆装过程中给予充分的注意。
2.对设备进行检查、试验
通过对设备的起动、运行、停车等过程,以听、看、摸、做等手段进行检查。
在实验室中进行拆装操作,虽然可以免去上述步骤,但对于这些基本方法一定要了解,并养成习惯。
3.工具、仪器、材料、备件的准备和清理场地
①.工具:
根据说明书、图纸及工艺规程等资料,将拆装过程所用的通用工具、专用工具准备好。
②.量具:
内、外径千分尺、百分表、游标卡尺、塞尺、内径量表等。
③.起重工具:
撬杠、手动吊车、钢丝绳、千斤顶等。
④.物料:
油料、机器布、棉纱、标签等。
⑤.备件:
设备用备件、各种垫床材料等。
⑥.场地:
清理场地、平板、机件架子,备好垫木、垫板等。
第二章船舶辅机拆装
(一)船用分油机的拆装与检修
一、结构概述
分油机是船舶机舱净化燃油、润滑油的设备。
目前船上广泛使用叠片式(亦称转盘式)自动排渣分油机。
现以国产DZY-50型分油机为例加以说明。
图2-1DZY-50型自动排渣分油机
1-放油旋塞;
2-油面观察镜;
3-大螺旋齿轮;
4-水平轴;
5-加油孔;
6-计速器;
7-配油盘;
8-分离筒;
9-压紧螺钉;
10-分油上盖;
11-观察镜;
12-控制阀;
13-上部轴承;
14-立轴;
15-小螺旋齿轮;
16-下部轴承;
17调节螺旋;
18-上轴承座;
19-向心球轴承;
20-轴承外衬套;
21-固定螺母;
22-压紧盖;
23-支承帽;
24-径向减震弹簧;
25-弹簧座;
26-下轴承套;
27-轴向减震弹簧;
28-弹簧盘;
29-滚珠;
30-垫块;
31-推力弹簧;
32-球面双列向心球轴承;
33-固定螺母;
34-轴承止圈
二、拆检要求
1.要正确使用专用工具进行拆装,不能蛮干。
2.要按次序进行拆装,不能盲目乱拆乱装。
3.将拆下的部件按照顺序排好。
4.必须保持接合面、配合面及光加工面的清洁,不能碰伤或损坏。
5.仔细清洗分离筒的所有零件,检查各密封环的完好性,并疏通各通道和小孔,特别是分离筒本体上的小孔M。
6.分离筒部件刻有记号,第二次重新装配时,不许随意换零件,必须对准原来的装配记号。
7.除分离筒底部的平衡块不得移动和修正外,颈盖上的去重或加重部分也不许随便更动。
8.绝不允许将这台分离筒上的零件装到另一台分离筒上,否则分离筒的平衡受到破坏,分油机工作时将产生强烈振动。
四、拆解.
分油机的拆解主要是指分离筒的拆解,现简介如下:
1.打开顶盖并固定好。
松开刹车装置和锁紧装置。
2.顺时针旋掉比重锁环(小锁紧环),拿掉比重环。
3.顺时针旋掉主锁紧环(应用分离筒刹车装置固定分离筒)。
4.吊出分离筒盖,拿掉颈盖。
5.取出分离盘片,拿出盘架(也可将盘架及分离盘片一起吊出)。
6.顺时针旋下立轴螺母(将军帽)。
7.用专用工具取出活动底盘或差动活塞。
8.用专用工具取出分离筒本体。
9.将分离筒倒置,松掉弹簧座上的六只螺栓,拿掉弹簧座,复位弹簧、滑动圈。
10.松开螺栓,拔下水管,拿出配水盘。
11.松开螺钉,拿出甩水盘和罩壳。
12.松开螺钉,拿出控制阀芯。
分油机拆解完毕。
四、装复
1.装好罩壳、甩水盘,拧紧螺钉。
2.装上底盖、配水盘,拧紧螺栓。
3.用专用工具装上分离筒本体。
4.上紧刹车装置,用专用工具装上差动活塞和活动底盘。
在装配活动底盘时注意将底盘底部和本体中部上的标记对准,保证底盘下部的定位销孔与分离筒本体上的定位销对正。
5.旋紧立轴螺母,装好推力挡块。
6.将分离盘装于盘架上,然后共同装入。
装时注意将盘架支脚上的销孔和底盘上定位销对正。
7.装好颈盖、分离筒盖,将分离筒盖边缘的缺口与推力挡块对正。
8.松开刹车装置,逆时针旋紧主锁紧环到标记处。
9.装上比重环,逆时针旋紧比重锁环。
10.转动分离筒,检查有无磨擦、卡阻。
如正常则盖上顶盖并锁紧。
11.对正位置,装好控制阀芯,连同指示盘共同用螺钉上紧。
至此,分油机拆装完毕。
(二)立式单级离心泵拆装与检修
船用离心泵的结构型式虽然很多,但由于作用原理相同,其一般构造、主要零件的形状是相似的,检修方法基本一样,下面就以立式单级离心泵3CZL-9型为例加以介绍。
一.结构概述
图3-1绘出的是3CZL-9型离心泵的具体结构。
该泵呈立式结构。
置于泵上的原动机通过弹性联轴节1,直接驱动泵轴回转。
泵轴6一般用不锈钢制成,支承于上部一个和下部两个滚动轴承上。
轴承的支座固定在泵的托架上。
主要零部件有泵盖、叶轮、泵壳、泵轴、轴承等。
其工作原理是:
泵在工作时,泵中的液体在叶片的推动下被迫随叶轮一起回转,把液体自叶轮进口向叶轮外周甩出。
在此过程中液体的动能和压力能都得到增加,其中前者的增加更大。
当液体流入蜗壳后,因蜗壳截面面积逐渐增大,液体的大部分动能就在这里转化为压力能,然后沿排出管排出。
与此同时,在叶轮中心形成一定的真空,在吸入液面上的大气压作用下,液体又会不断地经吸入管吸入叶轮的中心。
图3-13CZL-9型自吸式离心泵
1-弹性联轴节;
2-叶轮;
3-密封装置;
4-反牙螺帽;
5-泵体;
6-泵轴;
7-泵盖
二.解体
1.电机拆卸。
将电动机的接线脱开,拆除固定电动机的螺栓和弹性联轴节螺栓,然后将电动机卸下。
2.泵盖的拆卸。
在拆卸泵盖时,首先拆去泵体中开式部分的可去部分,拆下止推轴承盖(CL型需开排水管接管,拆去进水弯管和进水盖及固定其上的阻漏环)。
然后将泵盖拆下。
若难以取下,可利用顶丝顶活。
3.拆下轴承箱上的紧固螺栓,拧松轴承压盖的螺栓,即可将泵轴连同轴承及其端盖、轴封装置和叶轮一起轴向取出。
4.叶轮的拆卸。
拆卸叶轮时先用专用扳手卸下轴头上的反向螺母和止退垫圈,叶轮即从轴上脱下,当拿不下来时,如果无平衡孔的叶轮可用套管套住轴头,用手锤轻轻敲打套管头,使叶轮松动。
有平衡孔的叶轮,可用专用工具,将两只螺钉旋入叶轮平衡孔中,丝杠顶住轴头,转动丝杠拉出叶轮。
如叶轮锈在轴上,可先用煤油浸泡后再拆。
5.轴封的拆卸。
取下叶轮后,可依次从轴上取下填料密封,填料压盖(CL型可依次从轴上取下机械式轴封装置的弹簧、动环座及其销钉、胶环、动环、静环和轴承压盖,注意切勿碰伤动环)。
机械密封拆卸时不得用工具敲打,如密封元件被污垢或被凝聚物粘结,应清除粘结物后进行拆卸。
6.联轴器的拆卸。
拆下弹性联轴节的固定螺丝,再用拉马把联轴节慢慢拉出。
操作时,拉马的丝杠一定要顶正泵轴中心,并使联轴节两侧受力均匀。
切忌用手锤猛烈击打,以免造成泵轴、轴承或联轴节的损坏。
如果拆不下来,可用棉纱沾上油,沿着联轴器四周燃烧,使其受热均匀膨胀,在燃烧时要用湿布把泵轴包好,再用冷水淋浇湿布,防止轴和联轴器一起受热膨胀。
这样联轴器就容易拆下来了。
7.轴承的拆卸。
从轴上取下轴承端盖,然后取下轴承。
轴承一般用特制的拉马(拿子、拔子)拆出。
拉马的钩齿一定要抓住轴承的内圈,否则要拉坏轴承。
若配合力紧,可将滑油加热至100℃后用油壶浇在轴承内圈上,同时用拉马将轴承拆下。
至此拆解完毕。
1.将上滚动轴承装在轴上,然后装上轴承下盖(对CL型还需装下滚动轴承),再装上轴承上盖。
若轴承内径与泵轴采用紧配合,装配时先把轴承放入热机油中,等受热膨胀后再套到泵轴上去,等冷却后即可符合要求。
轴承装好后,将其压入轴承座内(滚动轴承外圈与轴承座一般采用动配合),再套上轴承盖、并用螺钉固定,轴承盖与轴承座间要垫上一纸垫。
2.套上挡水橡皮圈,装复弹性联轴节,应注意保持其端面与轴线的垂直。
装联轴器时,可在它的外侧垫上木块,用锤子敲打。
为了不损伤轴承和不使离心泵移动,在叶轮螺母外应垫一木块,顶在花铁板上或工作台上。
3.若采用机械密封(CL型)将轴封压盖、密封环(填料)及静环套在轴的下端,然后将动环套在胶环内,用紧密配合推入动环座内,一起装复轴上。
同时将动环座用销钉定位在轴上。
动环座与轴之间的间隙很小,装复时可加肥皂水或油类润滑。
动环安装在轴上后,必须保证能在轴上灵活移动。
最后将弹簧套在轴上。
另外因这些密封件的工作间隙都很小,安装时应用轻柴油或煤油再次清洗干净(船上一般油洗后,还应用适当压力的低压空气吹洗一次)。
上紧压盖时应在联轴器找正完毕后进行,压紧螺丝应均匀上紧。
把压盖上紧后转动泵轴手感轻快,说明配合良好。
4.将叶轮进口阻漏环套在轴上,然后将叶轮装复。
套上止退垫圈并用反向细牙螺帽固定。
再装上止推轴套。
装叶轮时,应用量具检查叶轮外缘的摆动范围(应在0。
12毫米以内),装好后应能在泵壳内灵活转动,而无碰撞和磨擦。
5.将小装后的轴、轴承及叶轮一起装入轴承座内,同时把密封环压入泵体,并用沉头螺钉固紧。
再上好另一半轴承盖并用螺栓把紧,紧力为-0.01~+0.01mm,不合适时可调整轴承盖结合面上的垫片。
然后用手轻轻转动,以手感轻快为宜。
6.将泵侧盖装复(若有密封环,勿忘将密封环压入泵盖,用平头螺丝固定。
),拧紧双头螺栓。
要注意交叉对角上紧。
7.用填料密封的泵,填料要一圈圈地放进去,要求平整服贴,各圈的切口应相互错开,一般交错120°
。
水封环要对准水封环口,压盖的松紧应适当(详细见检修部分)。
8.将泵壳其余部分装复,将下止推套盖装复(对CL型泵将阻漏环固定在进入盖上并一起装复)。
9.将电动机装复,进行泵和电机对中找正并固定。
找正通常以联轴节作为依据,利用直尺和塞尺来进行。
找正时应同时转动两轴,并在0°
、90°
、180°
、270°
等位置上,仔细检查两轴轴节的高度和彼此间轴向间隙的大小,一般两轴中心线的误差应不超过0.05mm。
联轴节的轴向距离,考虑到电动机转子的轴向窜动,因泵而异,一般在2~8mm之间。
将泵和吸、排管路接通,并再一次复查轴中心线变化。
至此泵组装完成。
(三)往复泵的拆装与检修
在船上,电动往复泵被广泛地用作舱底水泵、锅炉给水泵等。
一、结构概述
图4-1示出国产2DSL型电动双缸四作用往复泵。
他主要由电动机1、曲柄连杆机构3、水泵4以及润滑油泵5等所组成。
(1).该泵可配用船用直流电动机或交流异步封闭电动机,电机须按规定之旋转方向转动,以防由转轴所带动的齿轮油泵因反转而不能供油。
(2).齿轮减速器装在电机的输出轴端,由电机经挠性联轴节带动回转。
减速器的输出轴就是曲拐轴,拆卸曲轴时必须拆卸减速器的壳体,使曲轴能通过减速箱侧面的圆孔中取出。
(3).由机架、曲轴、连杆、十字头、滑道等所组成的传动机构,除机架和滑道采用铸铁件外,其它部件均用锻钢、铸钢和球墨铸铁等制成。
(4).活塞的材料是硅黄铜,用螺母将活塞固定在活塞杆上。
活塞环用耐磨擦的夹布胶木制成。
活塞杆用铬镍钛钢制成,在密封处设有填料箱。
填料箱内套用铸锡青铜制成。
(5).泵缸本体和阀箱两者连成一体,采用优质生铁浇铸。
(6).往复泵设有一套润滑系统,由安装在曲轴左侧的随车齿轮泵供油,去各磨擦部位进行强力润滑。
(7).为了防止泵的工作压力超过规定值,故在液缸的右侧装有安全阀。
(8).为使泵的排量趋于均匀,还装设了空气室。
1.选用工具正确。
要合理使用专用工具,不能蛮干。
2.将拆下的螺帽、螺栓、键、垫圈等小零件,按照顺序排好。
3.拆装操作程序正确。
要按次序进行拆装,不能盲目乱拆乱装。
4.对胶木胀圈的测量正确。
5.正确研磨往复泵的泵阀。
6.正确装复往复泵的胶木胀圈。
7.必须保持接合面、配合面及光加工面的清洁,不能碰伤或损坏
三.准备工作
1.人员准备。
解体往复泵一般需两人。
2.技术准备。
通过观看实物和图纸,熟悉结构,拟定拆装顺序。
有条件的要阅读随机拆装说明书,了解技术要求。
3.工具准备。
准备好所需的工具,包括放置零部件的工作台(或木板)和小木箱。
4.对象准备。
即通过一系列工作将被拆对象——往复泵准备好,使之处于可拆状态。
这些工作包括:
切断电源,在开关处挂上“禁用”牌。
关闭往复泵的吸、排截止阀。
如是热水泵使降温至常温。
打开往复泵放残水旋塞。
如有必要,拆掉有关管子。
用油性记号笔或钢字码等工具在泵壳上各部件配合处标上号码和接缝记号,以保证装配时能按原来的顺序和位置装复。
判明可能损坏的部件,并准备好备件、物料。
四、拆卸
1.拧下储油箱底部的螺丝堵,将滑油放空。
再拆下滑油系统所有的连接管路及其仪表。
2.将电机的接线脱开,拆除固定电机的地脚螺栓和电机与减速齿轮箱连接的挠性联轴节螺栓,然后就可以将电机从曲轴箱盖上拆出。
3.拆下固定滑油泵的螺丝,用顶丝顶活之后再拆下滑油泵。
4.拆下接油盘,松开活塞杆和十字头之间的锁紧螺母及活塞杆和十字头的连接,然后旋出泵侧的堵头,拆去十字头销上的定位弹簧圈,用提环螺栓就可将十字头销轴取出,为取出连杆作好准备。
5.取下曲轴箱有机玻璃观察孔盖,松开连杆大端螺栓,取出连杆大端下瓦,然后将曲轴转动一个适当的角度,这时就可以将连杆连同十字头一起从观察孔吊出。
6.拆下固定减速齿轮箱的螺栓,将曲轴连同齿轮箱一起吊出,然后再单独对齿轮箱进行解体清洗和检查。
7.松去填料压盖和水缸盖上的固定螺帽,将水缸盖打开并提起,然后将活塞、活塞杆一起向上提,直到活塞全部露出时为止,最后再将泵缸盖和填料箱盖从活塞杆上头取出。
8.拆去水阀箱盖上的紧固螺帽,拆下水阀箱盖,取出里面的吸水阀和排水阀。
9.拆除固定的安全阀,进行单独解体清洗和检查。
至此,解体工作基本结束,然后可用煤油或轻柴油等将所拆下之零部件进行清洗,以备进行检查和测量。
五、检修
1.缸套的检测
往复泵工作一定时间以后,由于缸套的磨损会影响泵的正常工作,因此要定期对缸套进行检查和测量。
检测前,先用煤油或轻柴油将缸套的工作镜面清洗干净,再仔细检查缸套是否有单边磨损、擦伤或划痕等现象,缸套的两端是否出现凸台。
如果发现上述情况,可用细油石打磨后再用细帆布抛光。
缸套磨损情况要用内径千分尺定期进行测量和检查,若磨损量达到极限标准时,就应换新活塞或换新缸套。
水缸套与水缸的安装公差按过盈量0.01~0.02mm选配.如工作介质为冷却水时,允许用环氧树脂粘结,此时的配合间隙为0.20~0.25mm.
水缸套活塞与缸套的安装间隙应符合表3-2.
泵缸磨损极限标准(mm)表3-1
缸径
允许镗缸或更换水缸
套时直径最大磨损量
必须换新缸套时
直径最大磨损量
圆度误差
圆柱度误差