HT150阀体的铸造工艺设计毕业论文Word文档下载推荐.docx
《HT150阀体的铸造工艺设计毕业论文Word文档下载推荐.docx》由会员分享,可在线阅读,更多相关《HT150阀体的铸造工艺设计毕业论文Word文档下载推荐.docx(28页珍藏版)》请在冰豆网上搜索。
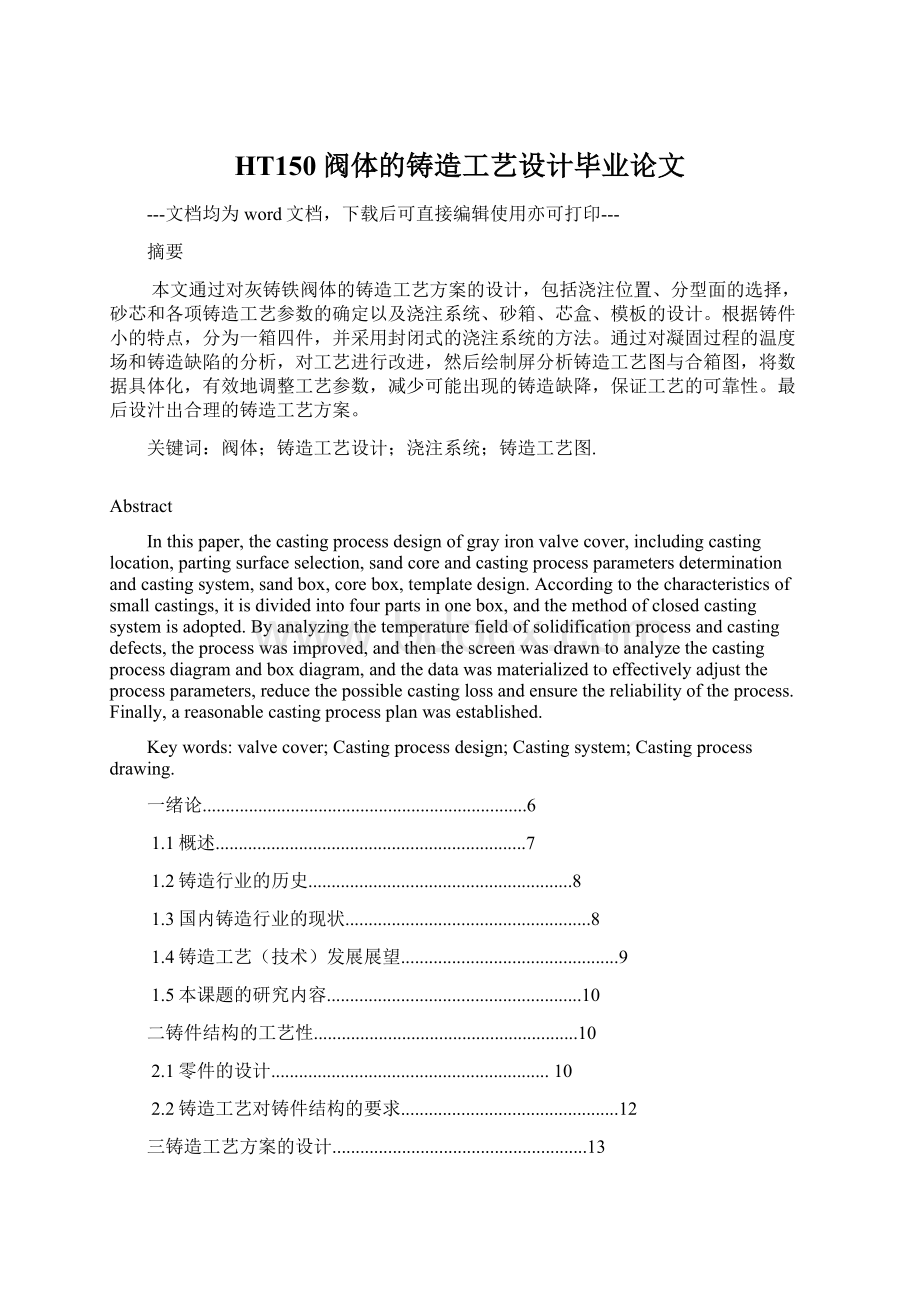
2.1零件的设计............................................................10
2.2铸造工艺对铸件结构的要求...............................................12
三铸造工艺方案的设计.......................................................13
3.1造型和造芯方法的选择...................................................13
3.2浇注位置的确定.........................................................14
3.3分型面的选择...........................................................15
3.4砂箱中铸件的数量及排列方式.............................................16
四铸造工艺参数及砂芯的设计..................................................16
4.1铸造工艺参数的确定.....................................................16
4.2砂芯的设计.............................................................21
五浇注系统的设计...........................................................22
5.1浇注系统类型的选择.....................................................22
5.2浇注系统尺寸的确定.....................................................225.3直浇道的设计.............................................................25
5.4横浇道的设计...........................................................25
5.5内浇道的设计...........................................................26
5.6浇口杯的设计...........................................................27
5.7冒口的设计.............................................................27
5.8冷铁的设计.............................................................27
六铸造工艺装备设计.........................................................27
6.1模样的设计.............................................................27
6.2模板的设计.............................................................28
6.3芯盒的设计.............................................................31
6.4砂箱的设计.............................................................32
七铸件的落砂、清理及后处理.................................................35
7.1铸件的冷却.............................................................35
7.2落砂...................................................................35
7.3表面清理...............................................................35
7.4铸件的矫形.............................................................35
7.5铸件的缺陷修补.........................................................36
7.6铸件的内应力消除.......................................................36
结论与展望.................................................................36
参考文献...................................................................38
小结
引言
重力铸造是指金属液在地球重力作用下注入铸型的工艺,也称浇铸。
广义上的重力铸造包括砂型浇铸、金属型浇铸、熔模铸造,泥模铸造等;
窄义的重力铸造专指金属型浇铸。
压力铸造是指金属液在其他外力(不含重力)的作用下注入铸型的工艺。
广义的压力铸造包括压铸机的压力铸造和真空铸造、低压铸造、离心铸造等;
窄义的压力铸造专指压铸机的金属型压力铸造,简称压铸。
这几种铸造工艺是目前有色金属铸造中最常用的、也是相对价格最低的。
铸造工艺过程可分为三个基本部分,即铸造金属准备、铸型准备和铸件处理。
铸造金属指铸造生产中用于浇注铸件的金属材料,它是以一种金属元素为主要成分,并加入其他金属或非金属元素而组成的合金,习惯上称为铸造合金,主要有铸铁、铸钢和铸造有色合金。
铸造金属熔炼不仅仅是单纯的熔化,还包括冶炼过程,使浇进铸型的金属,在温度、化学成分和纯净度方面都符合预期要求。
为此,在熔炼过程中要进行以控制质量为目的的各种检查测试,液态金属在达到各项规定指标后方能允许浇注。
有时,为了达到更高要求,金属液在出炉后还要经炉外处理,如脱硫、真空脱气、炉外精炼、孕育或变质处理等。
熔炼金属常用的设备有冲天炉、电弧炉、感应炉、电阻炉、反射炉等。
铸造是比较经济的毛坯成形方法,对于形状复杂的零件更能显示出它的经济性。
如汽车发动机的缸体和缸盖,船舶螺旋桨以及精致的艺术品等。
有些难以切削的零件,如燃汽轮机的镍基合金零件不用铸造方法无法成形。
此外,铸造的零件尺寸和重量的适应范围很宽,金属种类几乎不受限制;
零件在具有一般机械性能的同时,还具有耐磨、耐腐蚀、吸震等综合性能,是其他金属成形方法如锻、轧、焊、冲等所做不到的。
因此在机器制造业中用铸造方法生产的毛坯零件,在数量和吨位上迄今仍是最多的。
一绪论
1.1概述
铸造是指将熔炼好的金属浇入铸型,待其凝固后获得一定形状和性能铸件的成形方法。
用铸造方法得到的金属件称为铸件。
铸造的方法很多,主要有砂型铸造、金属型铸造、压力铸造、离心铸造以及熔模铸造等,其中以砂型铸造应用最广泛。
砂型铸造的典型工艺过程包括模样和芯盒的制作、型砂和芯砂配制、造型制芯、合箱、熔炼金属、浇注、落砂、清理及检验。
铸造的优点是可以铸出各种大小规格或形状复杂的铸件,且成本低,材料来源广,所以铸造是机械制造中生产零件或毛坯的主要方法之一。
而铸造的主要缺点是铸件的力学性能及精度较差,使铸造在生产中受到一定的限制。
但在机器设备中,铸件所占的比重还是很大的,如机床、内燃机、轧钢机等机械中,铸件的重量约占机器总重量的75%以上,可见铸造生产在机器制造中的重要性。
1.2铸造行业的历史
铸造是人类掌握比较早的一种金属热加工工艺,已有约6000年的历史。
中国约在公元前1700~前1000年之间已进入青铜铸件的全盛期,工艺上已达到相当高的水平。
中国商朝的重875公斤的司母戊方鼎,战国时期的曾侯乙尊盘,西汉的透光镜,都是古代铸造的代表产品。
20世纪以来铸造业的重大进展中,灰铸铁的孕育处理和化学硬化砂造型这两项新工艺有着特殊的意义。
这两项发明,冲破了延续几千年的传统方法,给铸造工艺开辟了新的领域,对提高铸件的竞争能力产生了重大的影响。
1.3国内铸造行业的现状
铸造工艺是机械制造工业的基础工艺之一,因此铸造业的发展标志着一个国家的生产实力。
由于中国封建社会的历史过于漫长,进入近代后,中国铸造技术长期处于停滞状态。
新中国成立以后,尤其是改革开放后的30多年,我国的铸造技术又有了很大的发展,突出的表现在三个方面:
造型造芯的机械化、自动化程度明显提高;
取代干型粘土砂和油砂的化学硬化砂的广泛应用;
伴随着计算机技术的应用,铸造工艺技术由凭经验走向科学化。
这些对于提高生产率,降低劳动强度,改善铸件的内在质量和外观质量,节约原材料和能源,起了重大作用。
1.4铸造工艺(技术)发展展望
20世纪末到21世纪以来,伴随着国民经济的快速发展,我国铸造业业迅猛发展,2009年,我国铸件年产量达3400多万吨,与居其后2-5位的美国、印度、俄罗斯、日本的总和相当,约占世界总产量的1/3,铸造厂点近3万多个,从业人员300多万人。
我国已是世界上名副其实的铸造第一大国。
我国未来的经济发展,要转变经济增长方式,把节约资源作为基本国策,发展循环经济,保护生态环境,加快建设资源节约型、环境友好型社会。
要走新型工业化道路,坚持节约发展、清洁发展、安全发展、实现可持续发展。
1.5本课题的研究内容
本次毕业设计的题目是:
HT150阀体的铸造工艺设计。
我查阅了相关资料和书籍后,主要进行了铸件结构的工艺性分析、铸造工艺设计及铸造工艺装备设计。
这个过程看似一目了然,但具体工作却十分繁琐,首先,我们要确定这个零件是否适合铸造工艺性的要求;
其次,我们还要确定浇注位置,分型面以及造型、造芯的方法;
然后,开始铸造工艺参数的选择以及砂芯的设计;
再然后,我们要进行浇注系统的设计;
最后,要对铸造工艺装备进行选择和设计。
当这一切完成后,我们还要用CAD绘制零件图和铸造工艺图,并填写铸造工艺卡片。
二铸件结构的工艺性
生产铸件,不仅需要采用先进合理的铸造工艺和设备,而且还要使零件结构本身符合铸造生产的要求。
这种对于铸造工艺过程来说的铸件结构的合理性,称为铸件的“铸造工艺性”。
铸件的结构是否合理,和铸造合金的种类和性能,对铸件的质量要求和产量的多少、铸造工艺方法和生产条件等均有密切的关系。
在一些情况下,改善结构工艺性所带来的技术经济效果可以和生产过程合理化、机械化、自动化的作用相提并论。
2.1零件的设计
零件结构的铸造工艺性指的是零件的结构应符合铸造生产的要求,易于保证铸件品质,简化铸造工艺过程,降低生产成本。
每一种铸造合金的铸件,都有其合适的壁厚范围,如果选择得当,既可保证铸件的力学性能要求,又可方便铸造生产,同时还可节约金属材料,减轻铸件质(重)量。
分析铸件的零件图,有助于判断铸件是否具有合适的壁厚。
HT150阀体零件图如下所示:
为了保证零件具有良好的铸造工艺性,在设计零件时应考虑以下几个方面的问题:
(1)铸件应有合适的壁厚
在一定铸造条件下,铸造合金能充满铸型的最小厚度称为该铸造合金的最小壁厚。
为了避免铸件的浇不足和冷隔等缺陷,铸件的设计壁厚应不小于最小壁厚。
最小壁厚的数值除与铸造合金的种类有关外,还与铸造方法、铸件形状、大小等因素有关。
表1砂型铸造铸铁件的最小壁厚(mm)
在确定铸件壁厚时,为了充分发挥金属的强度潜力,必须考虑铸造合金的力学性能对铸件壁厚的敏感性。
各种铸造合金都存在一个临界壁厚,当铸件的壁厚超过这个厚度以后,铸件的强度并不是按比例地随着铸件厚度的增加而增加。
砂型铸造各种铸造合金铸件的临界壁厚可按其最小壁厚的三倍来考虑。
表2砂型铸造临界壁厚(mm)
由零件图分段计算得出该阀体的体积V=84027mm³
=0.000084027m³
,又查知HT150的密度为7000kg/m³
所以其重量(质量):
M=ρ·
V=7000kg/m³
×
0.000084027m³
=0.58kg
2.2铸造工艺对铸件结构的要求
铸件结构还应考虑到模样制造、造型、造芯、清理等操作方便,以简化工艺、稳定质
量、提高生产率和降低成本。
因此要求:
(1)简化或减少分型面;
(2)减少型芯数量;
(3)方便起模;
(4)有利于型芯的固定和出气;
(5)设计出铸造工艺孔,用以支撑型芯和型芯出气,方便吊运和清砂等;
(6)有利于铸件的清砂和精整;
(7)有利于控制铸件尺寸公差。
三铸造工艺方案的设计
3.1造型和造芯方法的选择
造型和造芯方法的选择可参照以下原则:
1.优先采用湿型
当湿型不能满足要求时再考虑使用表干砂型、干砂型和其他砂型。
采用湿型时应注意以下几种情况:
(1)铸件过高,一旦金属静压力超过湿型的抗压强度时,会造成塌箱或者型壁移动。
(2)浇住位置上铸件有较大水平壁时,用湿型容易引起夹砂缺陷。
(3)湿型放置过久会风干,使表面强度降低,易出现冲砂缺陷。
(4)采用湿型会导致冷却吸潮,浇注后引起气孔缺陷。
表干砂型,只进行表面烘干,根据铸件大小及壁厚,烘干深度在15mm-80mm。
它具有湿型的许多优点,而在性能上却比湿型好,减少了气孔、冲砂、胀砂、夹砂的倾向。
多用于手工或机器造型的中大件。
对于大型铸件,可以应用树脂自硬砂型、水玻璃砂型以及黏土干砂型。
用树脂自硬砂型可以获得尺寸精确、表面光洁的铸件,但成本较高。
2.造型、造芯方法应与生产批量相适应
大量生产的工厂,应创造条件采用技术先进的造型、造芯方法。
对于小型铸件,可采用水平分型或垂直分型的无箱高压造型机生产线、实型造型线,生产效率高,占地面积也少;
对于中件可选用各种有箱高压造型机生产线、气冲造型线。
为适应快速、高精度造型生产线的要求,造芯方法可选用:
冷芯盒、热芯盒及壳芯等方法。
中等批量的大型铸件可以考虑应用树脂自硬砂造型和造芯、抛砂造型等。
单件小批量生产的重型铸件,手工造型仍是主要的方法,手工造型适应各种复杂的要求,比较灵活,不要求很多工艺装备。
3.造型方法应适合工厂条件
如有的工厂生产大型机床床身等铸件,多采用组芯造型法。
着重考虑设计、制造芯盒的通用化问题,不制作模样和砂箱,在地坑中组芯;
而另外的工厂则采用砂箱造型法,制作模样。
不同的工厂生产条件、生产习惯、所积累的经验各不一样。
如果车间内吊车的吨位小、烘干炉也小,而需要制作大件时,用组芯造型法是行之有效的。
4.要兼顾铸件的精度要求和成本
各种造型、造芯方法所获得的铸件精度不同,初投资和生产率也不一致,最终的经济效益也有差异。
因此,应当兼顾到各个方面。
应对所选用的造型方法进行初步的成本估算,以确定经济效益高又能保证铸件的造型、造芯方法。
3.2浇注位置的确定
铸件的浇注位置是指浇注时铸件在型内所处的位置。
浇注位置是根据铸件的结构特点、尺寸、重量、技术要求、铸造合金特性、铸造方法以及生产车间的条件决定的。
选择正确的浇注位置能保证获得健全的铸件,并使造型造芯和清理方便。
根据对合金凝固理论的研究和生产经验,确定浇注位置时,应考虑以下原则:
(1)铸件的重要部位应尽量置于下部;
(2)重要加工面应朝下或呈直立状;
(3)铸件大平面朝下,避免夹砂结疤类缺陷;
(4)应保证铸件能充满;
(5)应有利于铸件的补缩;
(6)避免吊砂、吊芯或悬臂式砂;
(7)应使合箱位置、浇注位置和铸件冷却位置相一致
综合考虑以上原则,本次设计的阀体的浇注位置应选在法兰盘朝上的大平面位置上。
图1浇注位置示意图
3.3分型面的选择
分型面是指铸型组元间的接合面。
合理的选择分型面,对于简化铸造工艺、提高生产率、降低成本、提高铸件质量等都有直接关系。
分型面的选择应尽量与浇注位置一致,尽量使两者协调起来。
在选择时,应该注意以下原则:
(1)尽量将铸件的全部或大部分放在同一箱内,以减少错型和不便验型造成的尺寸偏差;
(2)尽量将加工定位面和主要加工面放在同一箱内,以减少加工定位的尺寸偏差;
(3)尽量减少分型面数量,在机器造型中一般采用一个分型面;
(4)在机器造型中,选择分型面时,应尽量避免使用活块,必要时用砂芯代替活块;
图2分型面方案一图3分型面方案二
方案一:
如图2所示,分型面选在阀体法兰盘的大平面上,这样就保证了铸件的大部分都在同一个半型内,而且是重要部位尽量置于下箱,这样的话,下部金属液就会在上部金属液的静压力下形成致密的组织,保证了重要部位的质量。
方案二:
如图3,分型面选在对称的面上,起模相当方便。
但圆柱内壁的精度不能保证,而且浇注位置也不易确定。
圆柱必须垂直浇注,方能保证精度,若水平放置,浇注时圆柱壁易遭冲刷,造成缺陷,圆柱的垂直度也不易保证。
而圆柱内壁的加工又不方便,费工费时。
综上两种方案,选择方案一,虽免不了有些不合理的地方,但总体来讲还是要优于方案二,故选择方案一分型面选在阀体法兰盘的大平面上更适合。
3.4砂箱中铸件的数量及排列方式
铸件轮廓尺寸为80mm×
80mm×
42mm,单件质量约为0.58kg,属于小型铸件,由于是大批量生产,采用的是机器造型、造芯。
查表3得:
铸件与箱壁的距离为c=30mm,铸件与砂箱底部的距离为b=40mm,浇注系统内浇道的长度为f=30mm。
表3按铸件重量确定吃砂量(mm)
铸件重量(kg)
a
b
c
d
e
f
0-5
40
30
5-10
50
但这些数据也要根据实际情况来具体修改,以上数据在选择砂箱的时候可能会有所变动。
因为在选择砂箱时,砂箱的尺寸是有规格的,所以会有相应的调整。
四铸造工艺参数及砂芯的设计
4.1铸造工艺参数的确定
铸造工艺设计参数通常是指铸型工艺设计时需要确定的某些数据,它包括了铸造收缩率(缩尺)、机械加工余量、起模斜度、最小铸出孔的尺寸、工艺补正量、分型负数、反变形量、非加工壁厚的负裕量、砂芯负数(砂芯减量)及分芯负数。
4.1.1铸件尺寸公差
铸件尺寸公差是指铸件公称尺寸的两个允许极限尺寸之差。
在这两个允许极限尺寸之内铸件可满足加工、装配和使用要求。
表4铸件尺寸公差(mm)
4.1.2铸件重量公差
铸件质量公差定义为以占铸件公称质量的百分率为单位的铸件质量变动的允许值。
按照规定,质量公差应与尺寸公差同级,所以,铸件重量公差等级为MT10,由于重量为0.58kg,故查表5得,本次设计的铸件的质量公差数值为18%。
表5铸件重量公差
4.1.3机械加工余量
机械加工余量是铸件为了保证其加工面尺寸和精度,应有加工余量,即在铸造工艺设计时预先增加的,而在机械加工时又被切除的金属层厚度。
表6Ⅲ级精度灰铸铁铸件机械加工余量(mm)
4.1.4铸造收缩率
铸件收缩率又称铸件线收缩率或铸造收缩率,以模样与铸件的长度差除以模样长度
的百分比表示:
式中ε—铸件收缩率;
L1—模样长度;
L2—铸件长度。
铸件收缩率是受各种因素影响后铸件的实际线收缩率,不仅与铸造金属的