汽车某支架冲压工艺及模具设计毕业论文docWord文件下载.docx
《汽车某支架冲压工艺及模具设计毕业论文docWord文件下载.docx》由会员分享,可在线阅读,更多相关《汽车某支架冲压工艺及模具设计毕业论文docWord文件下载.docx(49页珍藏版)》请在冰豆网上搜索。
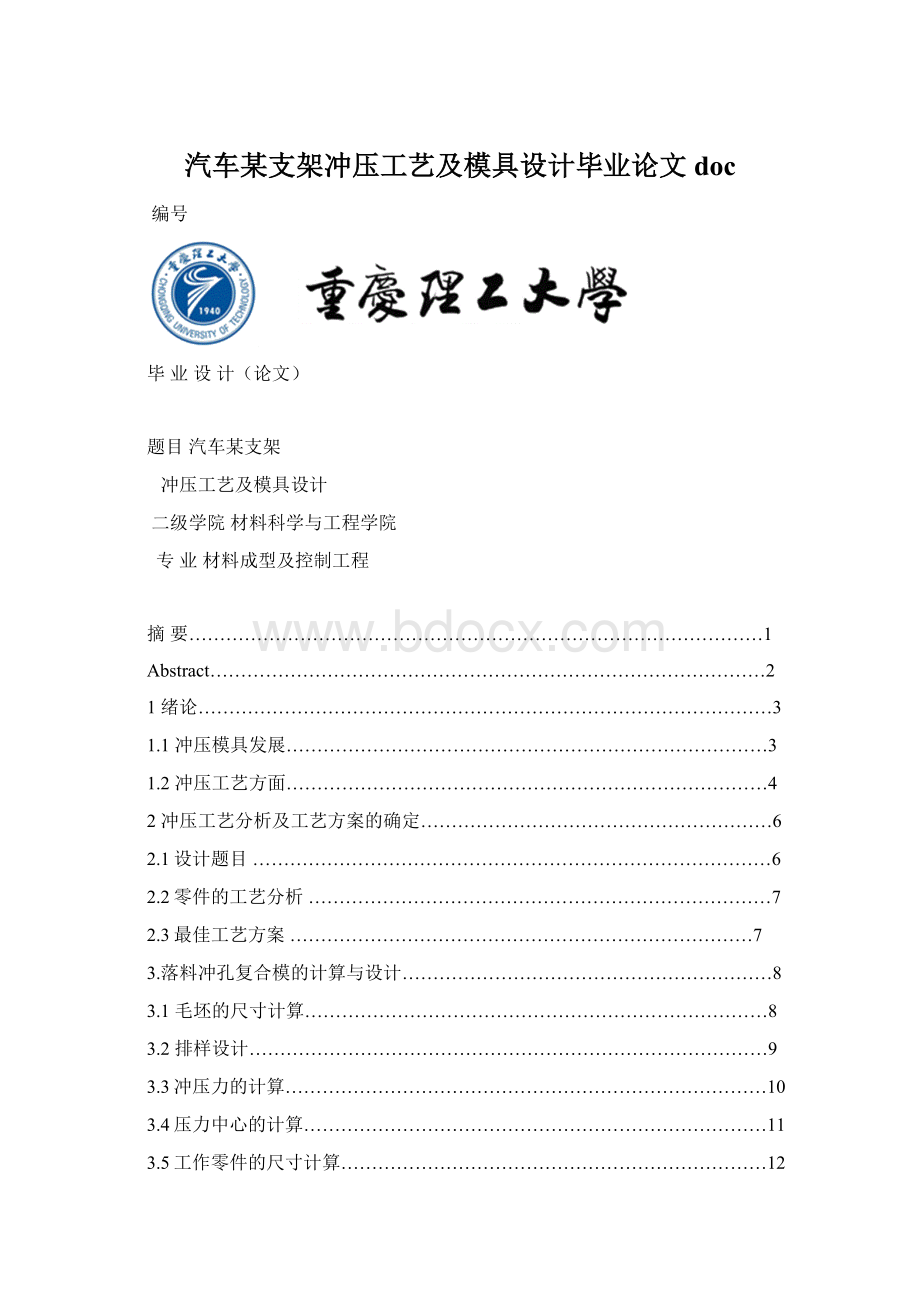
6.2模具工作零件的计算与设计…………………………………………………39
6.3冲压设备的选择………………………………………………………………41
6.4模具主要零件的设计和确定…………………………………………………42
结束语………………………………………………………………………………45
参考文献……………………………………………………………………………46
摘要
冲压工艺及模具设计既是冲压生产准备工作的基础,又是组织正式冲压生产的依据。
冲压工艺及模具设计水平标志着冲压工艺的先进性、合理性及经济性,它在很大程度上反映了工厂的生产技术水平。
生产实践证明,合理的冲压工艺方案和模具结构,不仅为稳定产品质量、降低冲压成本提供了技术保证,而且也为冲压成产的组织与管理创造了有利的条件。
反之,冲压工艺及模具设计的任何失误,都会给冲压生产带来不应有的损失,甚至造成人身、设备事故。
本文主要阐述汽车某支架的冲压工艺及其模具设计。
根据设计工艺要求,确定设计的大体思路。
通过对产品零件的工艺分析,确定最佳工艺方案。
由于工件相对比较复杂,主要经过冲裁落料、冲孔、成形、翻边和弯曲等工序。
产品的成形工艺难点主要有异形坯料的冲裁,成形时工件和翻边时的起皱和破裂,弯曲时的定位和回弹等等。
关键词:
冲压工艺模具设计支架
Abstract
Sheetmetalformingtechnologyandmolddesignisnotonlythefoundationofpreparationworkinstampingproduction,butalsothebasisoforganizingformalstampingproduction.Thelevelofstampingprocessandmolddesignmarkstheadvancement,reliabilityandeconomicsofstampingprocess,anditreflectsthefactories’productiontechnologylevel.Productionpracticeprovesthatthereasonablestampingprocessschemeanddiestructure,notonlyprovidestechnicalassurancetostabilizetheproductqualityandreducethecostofstamping,butalsohavecreatedfavorableconditionsforstampingintoproductionorganizationandmanagement.Conversely,anyerrorofstampingtechnologyanddiedesign,willbringunduelossestotheproductionofstamping,andevencausehumaninjuryandequipmentdamage.
Thisarticlemailyexpoundsthestampingprocessandmolddesignofacarbracket.Accodingtothedesignprocessrequirements,determinethegeneraldesignthought.Throughtheanalysisofprocessofpruductparts,determinethebestprocesssolution.Duetotheworkpieceisrelativelycomplax,shouldbethroughtheblanking,punchingforming,flangingandbendingect.Therethemaindifficultiesofproductinformingaretheblakingofunusalshapedblank,theworkpiecewrinkleandruptureinformingandflanging,aswellasthepruduct’slocationproblemandspringbackinbending,ect.
Keywords:
stampingprocessmolddesignbracket
1绪论
1.1冲压模具方面
1.1.1模具在现代工业中的作用
模具是用来成形各种工业产品的一种重要工艺设备,是机械制造工业成形毛坯或零件的一种手段。
它在现代工业生产中具有重要作用,用模具成形产品的工艺应用非常广泛,可实现少、无切削的加工,具有优质、高产、低消耗和低成本等特点,因此应用范围很广。
现代工业产品的发展和技术水平的提高,在很大程度上取决于模具工业的发展水平,因此模具工业对国民经济和社会的发展将会起越来越大的作用。
模具工业的薄弱将严重影响工业产品造型的变化和新产品的开发。
模具水平的高地和模具质量的好坏,对产品的精度、余量、生产率、成本及先进设备的利用率起决定性作用。
1.1.2模具工业的现状
近年来,我国的模具生产发展速度较快,已能满足国内对中、低档模具100%的需求,少量模具已开始向日本、美国、新加坡、泰国等地出口。
模具工业逐渐发展成为国民经济的基础工业。
虽然国内模具工业近十多年中取得了令人瞩目的发展,但许多方面与工业发达国家相比仍有较大差距。
主要表现在精密加工设备在模具加工设备中的比重较低,CAD/CAE/CAM技术的普及率不高,许多先进的模具技术应用不够广发,。
据统计,我国目前的模具生产只能满足需要的60%,其余需要完全通过进口。
我国模具中、长期的科技发展战略是以国内市场为导向,以开发精密、大型、长寿命成套模具为重点,减少进口,促进出口。
发展模具基础技术,如数控加工、快速制模、特种加工等;
发展高技术,如CAD/CAM、加工中心等;
加速模具新结构、新工艺、新材料的研究,提高精度和寿命;
发展模具成套加工精密设备。
1.1.3模具工业和技术的发展趋势
模具工业的发展和现代工业的发展紧密相联的。
随着机械、电子、轻工、国防等工业生产的不断发展,特别是电子工业和汽车工业的飞速发展,对模具的需求量与日俱增,给模具工业带来了广阔的前景,同时也带来了新的挑战。
模具技术的发展趋势有:
1)模具CAD/CAE/CAM正向集成化、三维化、智能化和网络化方向发展;
2)模具制造向精密、高效、复合和多功能方向发展;
3)快速经济制模技术得到应用;
4)特种加工技术有了进一步的发展;
5)高速铣削加工将得到更广泛的应用;
6)模具高速扫描及数字化系统将在逆向工程中发挥更大的作用;
7)超精加工和复合加工将得到发展;
8)模具标准化程度将不断提高,发展专业化成产;
9)模具材料及表面处理技术发展迅速。
1.2冲压工艺方面
在常温下,利用安装在冲床上的模具对板材施加压力,使其分离或成形,从而获得一定形状和尺寸的产品,这种加工方法称为冲压(又称冷冲压)。
板材、冲压、模具和冲床是冲压加工的三个必备要素,称为冲压三要素。
1.2.1冲压加工的特点
与其他加工方法相比,冲压加工有以下优点:
1)材料利用率高,操作方便,生产效率高,生产成本低。
2)产品质量好,尺寸稳定,精度较高,互换性好。
3)特别适用于大批量生产。
但是,冲压加工也存在以下缺点:
1)模具制造周期较长、成本较大。
2)冲压加工产生的振动大、噪声大。
3)在单件小批量生产中应用受限制。
1.2.2冲压工序的分类
由于冲压件的形状特点、尺寸大小、精度要求及生产批量等各不相同,所用的冲压工序也是种类繁多。
冲压工序的分类方法如下:
1)按照变形性质分类
A.分离工序:
切断、冲孔、落料、切边、切舌和剖切等。
B.成形工序:
弯曲、拉深和局部变形等。
2)按照基本变形方式分类
A.冲裁:
普通冲裁、精密冲裁。
B.弯曲
C.拉深
D.局部变形
3)按照工序组合方式分类
A.简答冲压工序
B.复合冲压工序
C.连续冲压工序
1.2.3冲压工艺和模具设计
1)冲压工艺设计
冲压工艺设计是指针对给定的产品图,考虑产品的生产批量,现有冲压设备、模具制造条件及技术水平等因素,从冲压工艺分析入手,经过必要的冲压工艺计算,合理制定出冲压工艺方案,并以冲压展开图、冲压工序图等形式表达。
冲压工艺设计的几本要求如下:
A.遵循材料的变形规律,保证冲出合格的产品。
B.经济合理,安全高效。
C.符合具体的生产条件,便于冲压生产的组织与管理。
2)冲压模具设计
冲压模具设计是指根据已有的冲压工艺方案,考虑产品的定位、卸料、出件及模具的制造、使用、维修等问题,构思符合现有生产条件的模具结构,合理确定相关尺寸,并以模具装配图、模具零件图、模具开发备料单、五金零件需求表等形式表达。
冲压模具设计的几本要求如下:
A.模具结构合理、动作灵活,保证冲出合格的产品。
B.模具结构简单,制造、维修方便,成本合理。
C.模具操作方便、安全可靠、寿命合理。
D.符合具体的生产条件,满足客户的特殊要求。
2冲压工艺分析及工艺方案的确定
2.1设计题目
图1所示工件,材料为08钢,厚度为1.2mm,大批量生产。
对支架零件进行冲压工艺分析研究,找到产品的成形工艺的难点所在,并在工艺方案上提供相应的解决措施。
结合生产实际,对支架零件进行冲压工艺设计和全套模具设计,以生产能用为目标。
零件名称:
汽车支架零件生产批量:
大批量
材料:
08钢t=1.2mm
图2-1汽车支架零件CAD平面图
图2-2汽车支架零件UG三维图
2.2零件的工艺分析
该零件是对称的,属于异形件,分析零件的成形工艺,主要经过的工序有落料、冲孔、成形、翻边、弯曲等工序。
由于工件的边缘精度要求不是很高,不需要切边和修边工序,所以落料的时候,可以一次性冲裁出坯料的外形。
零件两侧异形孔中间的凸起部分的成形,必须在冲出异形孔后再进行压弯或成形,并且其上的矩形孔也只能同时冲出或者后冲制,否则矩形孔可能会发生变形和位置不能得到保证。
中间的加强筋和两边的凸包,在为弯曲前是同一方向凸起,所以可以同时进行冲压。
零件最后进行弯曲,这一工序需单独完成,制成要求的形状和尺寸。
2.3最佳工艺方案的确定
由前面分析可知,零件所需的成形工艺有落料、冲孔、成形、翻边、弯曲。
现在将所有可能的方案列举如下:
方案一:
单工序模,落料、冲圆孔和异形孔、成形、冲矩形孔、翻边、弯曲。
方案二:
落料和冲圆孔、异形孔复合,成形、冲矩形孔和翻边复合,弯曲。
方案三:
落料和冲圆孔、异形孔复合,成形,冲矩形孔和翻边复合,弯曲。
方案四:
连续模。
方案一是由单工序模组成,此方案模具制造简单,维修方便,但是工序过多,生产效率低,制造成本高。
方案二采用复合模,生产效率较高,成本也较低,但是模具结构复杂,维修比较麻烦。
方案三和方案二一样采用复合模,生产效率也较高,成本也较低,但是和单工序模结合,使得模具制造比较和维修比较方便。
方案四采用连续模,生产效率更高,但是本工件的尺寸比较大,用连续模的话,模具会比较大,占地大,且维修不那么方便。
通过以上方案的分析比较,方案三比较优越,所以确定为最佳工艺方案,并采用方案三进行模具设计。
3落料冲孔复合模的计算与设计
3.1毛坯的尺寸计算
3.1.1工件展开
把工件的弯曲部分和翻边部分进行展开,就可以得到坯料外形,按有圆角半径的弯曲展开,方法如下:
图3-1有圆角半径的弯曲
圆角部分的展开长度等于对应的中性层的长度,式子3-1,即
式中
——各圆角部分的展开长度(mm);
——弯曲度(°
);
r——弯曲半径(mm);
x——中性层位移系数,与相对弯曲半径r/t、弯曲方式等因素有关,见表3-1;
t——材料厚度(mm)
表3-1中性层位移系数x
r/t
0.1
0.2
0.3
0.4
0.5
0.6
0.7
0.8
1
1.2
x
0.21
0.22
0.23
0.24
0.25
0.26
0.28
0.32
0.33
1.3
1.5
2
2.5
3
4
5
6
7
≥8
0.34
0.36
0.38
0.39
0.42
0.44
0.46
0.48
由式子3-1和表3-1可以计算工件的弯曲部分和翻边部分,得到坯料的外形尺寸见图3-2所示:
图3-2坯料的外形尺寸
由于工件在落料之后没有大的变形影响外形尺寸,所以落料时的形状和大小为展开时的外形尺寸。
3.2排样设计
毛坯的外轮廓最大尺寸为249.9×
168.51mm,尺寸比较大,考虑到送料等问题,采用单排形式进行排样,如图3-3所示。
查参考文献[1]表2.25,查出侧面废料宽度为a=2.5mm,工件间的间隙b=3mm。
则有:
条料的宽度为B=249.9+2a=254.9mm
步距为S=168.51+b=171.51mm
图3-3排样图
一个步距内的材料利用率为
×
%100≈62.56%
3.3冲压力的计算
3.3.1冲裁力计算
经计算:
落料冲裁的总长L=1718.3mm
冲裁力
式中P——冲裁力(N);
L——冲裁总长度(mm);
t——料厚(mm);
——材料的抗拉强度(Mpa),查表得330~450Mpa。
则有P=1718.3×
1.2×
450N=927882N≈927.9kN。
3.3.2卸料力、顶件力
采用上取件的方式进行落料
卸料力
顶件力
以上
查参考文献表[1]2.32,所以总的冲压力为
927.9+46.4+55.7=1030kN
3.4压力中心的计算
冲裁力合力的作用点称为冲模的压力中心。
在进行冲模设计时,必须使模具的压力中心与压力机滑块中心重合,否则冲压时会产生偏载,导致模具以及压力机滑块与导轨的急剧磨损,降低模具和压力机的使用寿命,严重时甚至损坏模具和设备,造成冲压事故。
所以,冲模压力中心的准确确定,在模具设计中起着至关重要的作用。
另一方面使加工出来的制件不合格。
冲模的压力中心按下述原则确定:
(1)对称形状的单个冲裁件,冲模的压力中心就是冲裁件的几何中心。
(2)工件形状相同且分布位置对称时,冲模的压力中心与零件的对称中心相重合。
(3)形状复杂的零件,多孔冲模,级进模的压力中心可用解析法求出冲模压力中心。
由于工件左右对称,根据直线段的重心在线段的中点,圆弧的重心位置按照
进行计算,式中
R——圆弧半径
——为圆弧二分之一角度
b——圆弧弦长
在工件图上建立坐标系,则有
压力中心到Y轴的距离
压力中心要X轴的距离
按照此方法计算出来的压力中心如图所示
图3-4压力中心
3.5工作零件的尺寸计算
落料冲孔复合模,属于异形零件,采用配合加工,以落料凹模为基准进行计算,落料凸模按照间隙以凹模为基准计算,查参考文献[1]表2.34,取初始单边间隙Ⅱ类>
(0.07-0.10)t,再由表2.36可得单边间隙0.063mm<
C<
0.09mm,这里取0.08mm。
工件制造公差为IT14级,则零件尺寸按IT11级计算。
3.5.1刃口尺寸计算
1.落料凹模
此为落料冲孔模,故以落料凹模为基准计算,落料凸模按间隙值配制。
磨损后尺寸变大的A类
磨损后尺寸变小的B类
磨损后尺寸不变的C类
式中:
-基准件尺寸,mm
、B、C-毛坯尺寸,mm;
工件制造公差,mm;
-基准件制造偏差;
x-磨损系数,见参考文献[3]表2-5,此处取0.5。
落料凹模一些主要尺寸的计算①249.9②168.51③72.88④129.51
A类尺寸
①=(249.9-0.5×
0.81)
=249.5
②=(168.51-0.5×
0.63)
=168.2
B类尺寸
③=(72.88+0.5×
0.46)
=72.65
C类尺寸
④=(129.51+0.5×
0.63)±
0.08=129.2±
0.08
凹模的其他刃口尺寸可以类似的计算出来
2.凸凹模
凸凹模的外形各尺寸与落料凹模进行配合加工,间隙为0.08mm。
所以凸凹模如图3-5所示:
图3-5凹凸模的外形和尺寸
3.冲孔凸模
冲孔凸模的尺寸则根据凸凹模进行配合加工,且冲孔凸模1装配的时候要铆接,且上平面需要磨。
冲孔凸模公差也按IT11计算。
如图所示:
图3-6冲孔凸模1
图3-7冲孔凸模2
3.6冲压设备的选择
3.6.1冲压设备的选用原则
冲压设备的选择主要是根据冲压工艺性质、生产批量大小、冲压件的几何形状、尺寸及精度要求等因素来确定。
冲压生产中常用的设备种类很多,选用冲压设备时主要应考虑一下因素:
1)冲压设备的类型和工作形式是否适用于应完成的工序,是否符合安全生产和环境要求;
2)冲压设备的压力和功率是否满足应完成工序的需求;
3)冲压设备的装模高度、工作台面尺寸、形成等是否适合应完成工序所用的模具;
4)冲压设备的行程次数是否满足生产率的要求等。
3.6.2压力机的选用
根据模具的总冲压力
1030kN,模具的闭合高度,凹模的外形尺寸,现有的设备和工作台的大小,查阅参考文献[1]表13.11,选用闭式单点单动压力机。
压力机参数:
标称压力:
1600kN
滑块行程长度:
250mm
滑块行程次数:
20次/min
最大装模高度:
450mm
装模高度调节量:
200mm
工作台尺寸(前后/左右):
800×
mm
3.7落料冲孔复合模的主要零部件的设计
(1)落料凹模结构尺寸
根据参考文献[1]式2.18计算凹模高度:
查参考文献[1]表14-5以及参考文献[3]表2-10得凹模壁厚:
C=48mm
垂直于送料方向的尺寸:
B=b+2C=249.9+2×
48=345.9mm
送料方向的尺寸:
A=a+2C=168.51+2×
48=264.51mm
考虑到模具刃磨并参考参考文献[5]附录F1标准举行凹模板尺寸,对以上尺寸适当放大、取整可确定长、宽、高尺寸为:
400mm×
315mm×
50mm。
落料凹模的结构尺寸如图:
图3-8落料凹模
(2)标准模座初步设计
根据凹模周界尺寸,查参考文献[6]可以确定模座,采用滑动导向中间导柱标准模架,初定下模座尺寸号为400mm×
75mm,上模座尺寸为400mm×
60mm。
图3-9上模座
图3-10下模座
(3)凸模固定板
凸模固定板的厚度取凹模厚度的0.6~0.8倍,即H=30~40mm,查参考文献[5]附录F1,选取标准凸模固定板厚度为H=30mm。
平面尺寸和凹模外形尺寸形同,确定凸模固定板的结构尺寸为400mm×
30mm。
图3-11凸模固定板
(4)凸模垫板
厚度取8mm,平面尺寸和凹模外形尺寸形同,确定凸模垫板的结构尺寸为400mm×
8mm。
图3-12凸模垫板
(5)凸凹模固定板
厚度可取35mm,平面尺寸和凹模外形尺寸形同,确定凸凹模固定板的结构尺寸为400mm×
35mm。
图3-13凸凹模固定板
(6)弹压卸料装置
卸料板:
查参考文献[1]表15.31得知厚度取18mm,其结构尺寸为400mm×
18mm。
图3-14卸料板
橡胶:
根据模板形状及安装活动挡料销与导料销的需要,选取聚氨酯弹性体作为弹性元件,其轮廓尺寸与凹模板一致。
卸料板的工作进程:
根据参考文献[5]式4-7可确定聚氨酯弹性体的自由高度
:
6~12=14.8~20.8mm,适当放大取整为25mm。
根据参考文献[5]式4-9可确定聚氨酯弹性体安装高度:
25-0