基于ADAM4000控制系统的A3000高级复杂实验培训Word文档格式.docx
《基于ADAM4000控制系统的A3000高级复杂实验培训Word文档格式.docx》由会员分享,可在线阅读,更多相关《基于ADAM4000控制系统的A3000高级复杂实验培训Word文档格式.docx(61页珍藏版)》请在冰豆网上搜索。
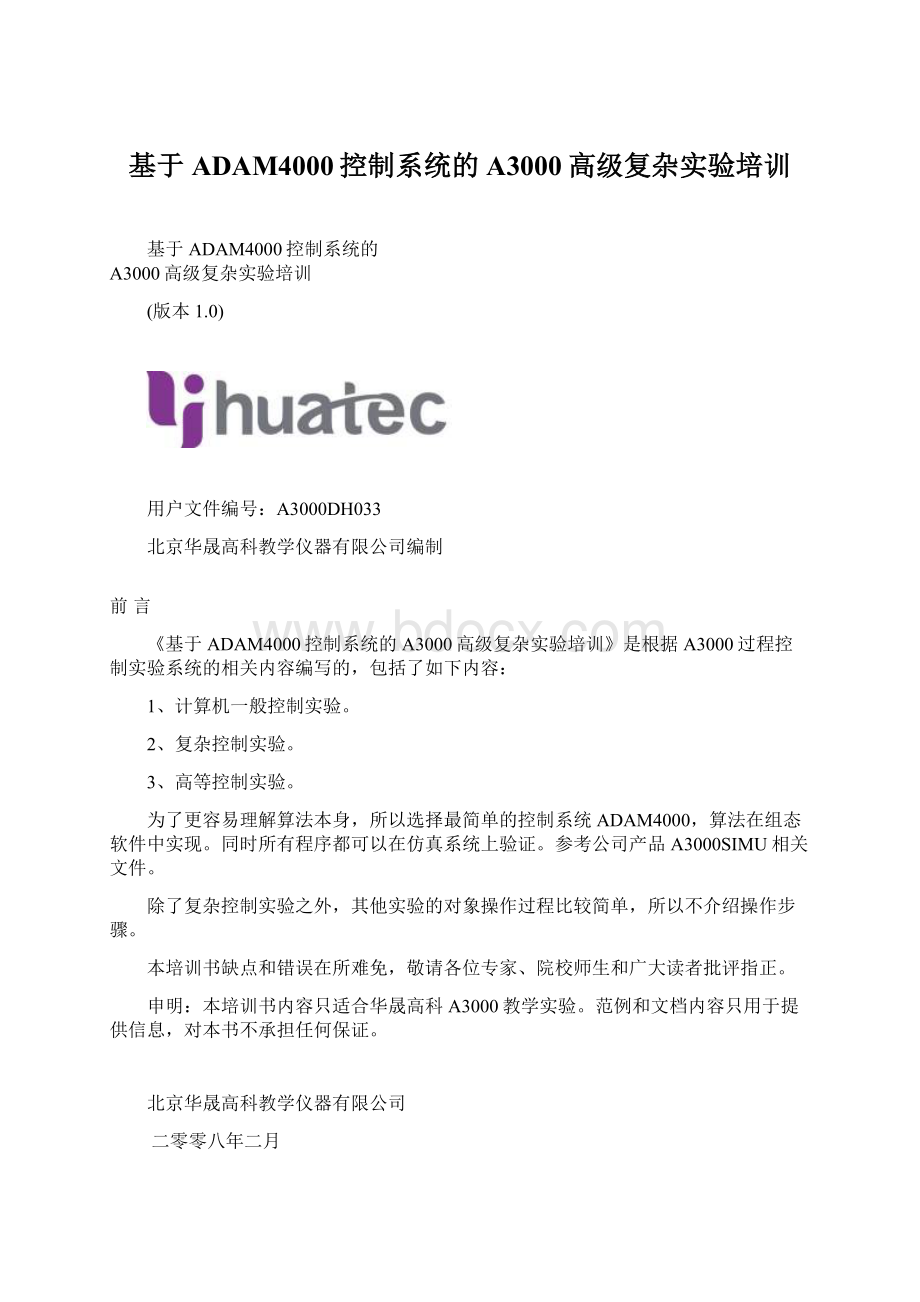
0.5立方/小时
1立方/小时
控制流程图如图1.1.1所示。
图1.1.1程序控制流量流程图
1.1.2算法实现和关键操作步骤
采用PID控制。
两个PID,但是程序控制其给定值。
界面如图所示。
程序代码如下:
//1000毫秒执行一次。
中间变量1=中间变量1+1;
if(中间变量1>
400)
中间变量1=0;
//输入
PID0_PV=AI0;
PID1_PV=AI1;
if(PID0_SP==0)
AO0=0;
else
AO0=PID0_MV;
if(PID1_SP==0)
AO1=0;
AO1=PID1_MV;
=0&
&
中间变量1<
=100)
{
PID0_SP=33;
PID1_SP=0;
}
100&
=200)
PID0_SP=16.5;
PID1_SP=16.5;
300&
=400)
PID0_SP=0;
PID1_SP=33;
注意开启两个水泵,两个流量控制。
一支路使用调节阀,一支路使用变频器。
1.1.3实验结果及记录
控制曲线如图1.1.2所示。
多个值的控制曲线绘制在同一个图上。
1.2数字滤波技术、标度变换、非线性校正实验
1.2.1工艺过程描述
数字滤波技术、标度变换、非线性校正实验就是单容下水箱液位控制,流程图如图1.2.1所示。
图1.2.1数字滤波技术和非线性校正实验
1.2.2算法实现和关键操作步骤
由于液位具有波动,所以数据不是非常稳定,采用数字滤波技术采用,进行滤波。
滤波算法:
PV过滤=PV旧值*0.9+PV新值*0.1。
由于ADAM4000内部已经有了滤波,所以效果不如使用PCI1711好。
标度变换,使用线性算法,把4-20毫安转换成0-25厘米。
非线性校正则考虑到水箱的出口流量和液位高度的开方成正比。
所以采取开方算法,把输入的过程值直接校正,随输出流量成为线性。
//工程量尺度变换
floata;
a=(AI0-4.0)*25.0/16.0;
//数字滤波
中间变量1=中间变量1*数字滤波加权系数+a*(1-数字滤波加权系数);
//同时对给定值和输入值校正
给定值1=Sqrt(中间变量2);
测量值1=Sqrt(中间变量1);
//输出
AO0=操作值1;
1.2.3实验结果及记录
控制器控制曲线如图1.2.2所示。
1.3数字PID控制实验
1.3.1题目工艺过程描述
单容下水箱液位PID控制流程图如图3.1.1所示。
图3.1.1单容下水箱液位调节阀PID单回路控制
测点清单如表3.1.1所示。
表3.1.1单容下水箱液位调节阀PID单回路控制测点清单
序号
位号或代号
设备名称
用途
原始信号类型
工程量
1
FV-101
电动调节阀
阀位控制
2~10VDC
AO
0~100%
2
LT-103
压力变送器
下水箱液位
4~20mADC
AI
2.5kPa
1.3.2算法实现和关键操作步骤
实验界面如图所示。
PID运算可以采用标准的直接计算法和增量计算法。
上次的计算值
两次相减:
输出时加上上次输出就可以了。
从公式可见,直接计算法很可能导致积分饱和,所以需要抗饱和的操作。
定义ET0、ET1、ET2,要求变量可以负值和正值。
例如定义到-100000到100000
PID_KI,PID_KD
在画面中每1秒执行一次。
//数字PID控制。
//关联到IO数据
if(PID_I==0)//避免除0
PID_I=0.01;
数字PID_KI=PID_P*1/PID_I;
//1运算周期
数字PID_KD=PID_P*PID_D/1;
数字PID_ET0=PID0_SP-PID0_PV;
If(\\本站点\数字PID算法选择==1)//'
=1采用增量计算
{//保留了上次\\本站点\操作值1
PID0_MV=PID0_MV+PID_P*(数字PID_ET0-数字PID_ET1);
//比例作用
If(PID_I<
10000)//积分作用
{
PID0_MV=PID0_MV+数字PID_KI*数字PID_ET0;
//积分作用
}
PID0_MV=PID0_MV+数字PID_KD*(数字PID_ET0-2*数字PID_ET1+数字PID_ET2);
//微分作用
数字PID_ET2=数字PID_ET1;
数字PID_ET1=数字PID_ET0;
ELSE//采用直接计算
{
//清除了\\本站点\操作值1
PID0_MV=0;
PID0_MV=PID0_MV+PID_P*数字PID_ET0;
IF(PID_I<
10000)//积分作用有意义
\\本站点\数字PID_ISUM=\\本站点\数字PID_ISUM+数字PID_KI*数字PID_ET0;
//积分作用
IF(\\本站点\数字PID_ISUM>
100)//抗积分饱和
\\本站点\数字PID_ISUM=100;
PID0_MV=PID0_MV+\\本站点\数字PID_ISUM;
}
PID0_MV=PID0_MV+数字PID_KD*(数字PID_ET0-数字PID_ET1);
IF(PID0_MV>
100)//输出限制
PID0_MV=100;
IF(PID0_MV<
0)//输出限制
1.3.3实验结果及记录
控制器控制曲线如图2.2.3所示。
1.4BANG-BANG控制
该控制的复杂算法可以解决一些高等控制问题,但是我们将采用比较简单的算法,来验证这类控制的意义。
1.4.1工艺过程描述
如果要求单容下水箱液位PID控制的具有快速响应特性,并且在给定点位置还要准确控制,那么如何控制呢。
系统的工艺流程如图1.4.1所示。
图1.4.1单容下水箱液位调节阀BANG-BANG单回路控制
1.4.2算法实现和关键操作步骤
BANG-BANG控制最早由厐特里亚金提出,属于开关控制的非线性控制。
如果一个系统控制有以下要求;
即控制要实时性好,系统要稳定,控制精度要求高。
则可以采用非线性的Bang-Bang控制和线性的PID控制结合,其控制效果比较好。
如果采用线性的PID控制,虽然稳态精度容易满足,但是大偏差时就容易出现较大的偏差,而且过度的时间比较长,如果采用非线性的Bang-Bang控制,虽然能使过渡时间最短,但是容易出现超调,而且在零点附近容易产生振荡造成系统不稳定。
鉴于这种情况,设计了一种变结构的控制器是两者的优点有机的结合起来,从而使系统运行起来既快又稳。
设计的变结构式的双模控制器如图3所示:
图3变结构式的双模控制回路结构图
此结构控制就是使系统的结构可以在控制过程的各个瞬间,根据某些参数的状态以跃变的方式有目的的变化,从而将不同的结构揉和在一起,取得比固定结构系统更加完善的性能指标。
据此,针对流浆箱的液位和总压控制,提出了一种将非线性的Bang-Bang控制与线性的控制结合的变结构双模控制方法。
如图2所示:
当设定值(SP)与检测值(PV)产生一个偏差,由识别机构通过不同的偏差来选择不同的控制器,当偏差大于某个值的时候采用非线性Bang-Bang控制,当偏差小于某个值的时候系统自动切换到线性的PID控制。
Bang-Bang控制器的设计
Bang-Bang控制也称为开关式控制,对于较大的偏差,例如∣En∣≥a,控制量变化u取+Um或-Um,实行非线性开关控制模态,以提高系统的响应速度。
其表达式如下:
其中a为选择开关的切换值
对于液位控制如果直接使用PID,就必须在快速性和稳定性之间进行抉择。
但是如果实现了解了对象的特性,然后选择了合适的bang-bang控制结合PID,则可能有比较好的结果。
我们这里的bang-bang控制选择比较简单的控制算法。
首先测量液位和控制量在稳态情况的一个对应曲线。
这在系统特性测量中已经获取,当然也可以依据闸板的高度不同,重新测量。
例如SP下,控制量该是A稳定。
那么:
如果PV<
SP-a,MV=A-U,如果PV>
SP-a,MV=A+U,其他情况使用PID控制。
最好在切换时增加跟随程序,保证切换时没有扰动。
选择合适的a,A,以便获得最好的效果。
实验的组态界面如图所示。
1.4.3实验结果及记录
测量稳态液位对应的控制量如表所示。
我们可以简化一下,在液位30-60之间使用直线表示。
如果我们要控制液位60%,此时对应的控制量为43。
那么如果PV<
60-a,MV=43-U,如果PV>
60-a,MV=43+U,其他情况使用PID控制
1.5校正网络数字滤波器实现
1.5.1工艺过程描述
单容非线性上水箱液位PID控制流程图如图1.5.1所示。
图1.5.1校正网络数字滤波实验流程
1.5.2算法实现和关键操作步骤
这里的算法和自适应不同,而是把一个非线性的系统通过校正网络,使得它成为线性特性。
非线性截面积
等截面积特性
校正网络滤波
并且最好能够把液位高度继续校正为正比流量。
把等截面积系统液位高度开方。
液位控制,调节阀控制的是流量,那么液位变化率。
如果输入流量为Q,则高度变化率具有如下特性:
采用H对应到
来进行滤波。
在H=R时的PI控制参数,获得一定的控制效果。
注意开启时,需要让水进入上水箱。
在组态软件中的具体算法如下:
//数字滤波,按照S=积分:
K*sqrt(100h-h*h),
//不考虑开方,积分h*h/2.0-h*h*h/300归一化
//中间值0作为给定值
PID1_SP=中间值0;
//仅仅用于显示
PID0_PV=sqrt(AI0*AI0/2.0-AI0*AI0*AI0/300.0);
PID0_SP=sqrt(中间值0*中间值0/2.0-中间值0*中间值0*中间值0/300.0);
控制界面如图所示。
1.5.3实验结果及记录
使用普通PID进行实验,然后找到最好的控制参数,得到控制曲线。
然后使用校正网络的方法进行控制。
然后找到最好的控制参数,得到控制曲线。
要求在各自最好的情况下,使用校正网络的方法可以得到更好的控制效果。
第二章复杂控制实验
2.1比值控制系统实验
2.1.1测试题目描述
流量比值控制系统控制流程图如图2.1.1所示。
图2.1.1流量比值控制流程图
流量比值控制测点清单如表2.1.1所示。
表2.1.1流量比值控制控制测点清单
FT-101
1#流量计
测量管路1流量
0-3m3/h
FT-102
2#流量计
测量管路2流量
3
U-101
变频器
频率控制,手动控制1#流量
4
调节阀
控制跟踪的流量
水介质一路(简称为I路)由泵P101(变频器驱动,手动控制作为给定值)从水箱V104中加压获得压头,经电磁阀XV-101进入V103,水流量可通过变频器或者手阀QV-106来调节;
另一路(简称为II路)由泵P102从水箱V104加压获得压头,经由调节阀FV-101、水箱V103、手阀QV-116回流至水箱V104形成水循环,通过调节阀FV-101调节此路的水流量;
其中,I路水流量通过涡轮流量计FT-101测得,II路水流量通过电磁流量计FT-102测得。
2.1.2控制算法和编程
这是一个单闭环流量比值控制系统,或者说是随动系统。
可以让一个流量梗跟随另一个流量的变化。
有两个算法。
(1)流量计FT-101流量与流量计FT-102成比例控制,如2.1.2所示,把FT101乘以比值系数,然后作为调节器的给定值。
被调量为调节阀开度,控制目标是水流量,通过两个流量不同比例下的比较,然后输出控制值到调节阀。
实行PID控制,看控制效果,进行比较。
这样方式下,由于FT101的测量不是非常稳定,所以调节器的给定值是有些变动的。
控制稳定性可能不是很好,另外在实时曲线上可以直接看到稳定的曲线。
(2)流量计FT-101流量与流量计FT-102成比例控制,如2.1.3所示,把FT101/FT102,然后作为调节器的测量值,而比值K作为调节器给定值。
FT
102
2#
调节阀FV101
101
比值K
调节器
Q2
Q1
1#
图2.1.3比值控制系统原理图
SP
PV
MV
除法器
被除数
这样方式下,调节器的给定值是稳定的,控制稳定性较好,但是在实时曲线上可以显示K值,最好的范围是0.1-10(我们设置k的范围就是0-10,而曲线上刻度是0-100,所以有些差异。
2.1.3操作过程和调试
1、编写控制器算法程序,下装调试;
编写测试组态工程,连接控制器,进行联合调试。
这些步骤不详细介绍。
2、在现场系统上,打开手阀QV-102、QV-105,QV115,QV106,电磁阀XV101直接打开(面板上DOCOM接24V,XV101接GND)或打开QV111。
3、在控制系统上,将支路1流量变送器(FT-101)输出连接到控制器AI1,将支路2流量变送器(FT-102)输出连接到控制器AI0,变频器控制端连接到AO0,调节阀FV-101控制端连接到AO1,且变频器手动控制。
注意:
具体哪个通道连接指定的传感器和执行器依赖于控制器编程。
对于全连好线的系统,例如DCS,则必须按照已经接线的通道来编程。
4、打开设备电源,包括调节阀电源,变频器电源,变频器设为外部信号操作模式。
5、连接好控制系统和监控计算机之间的通讯电缆,启动控制系统。
6、启动计算机,启动组态软件,进入测试项目界面。
启动调节器,设置各项参数,将调节器切换到自动控制。
7、启动水泵P102。
8、设置PID控制器参数,可以使用各种经验法来整定参数,这里不限制使用的方法。
具体可以参考2.4节。
建议:
因为PID的SP值会有一定的波动,所以控制的稳定性稍差,有一些难度。
注意控制目标是比值的稳定,而给定值也是比值。
干扰可以是K值的改变,也可以是变频器控制量的改变(从而改变了FT-101)。
2.1.4实验结果及记录
流量比值控制曲线如图1.1.4所示。
比值系数3。
P=24,I=2.5秒。
图1.1.4流量比值控制曲线
2.2串级控制实验
2.2.1测试题目描述
液位和进口流量串级控制流程图如图2.2.1所示。
图2.2.1液位和进口流量串级控制流程图
液位和进口流量串级控制测点清单如表2.2.1所示。
表2.2.1液位和进口流量串级控制测点清单
V103液位变送器
测量液位
0-2.5kPa
控制流量
U101
固定给值
0-10VDC
A0
0-100%
水介质一路(I路)由泵P101(变频)从水箱V104中加压获得压头,经流量计FT-101、电动阀FV-101、水箱V-103、手阀QV-116回流至水箱V104而形成水循环,负荷的大小通过手阀QV-116来调节;
其中,水箱V103的液位由液位变送器LT-103测得,给水流量由流量计FT-101测得。
本例为串级调节系统,调节阀FV-101为操纵变量,以FT-101为被控变量的流量控制系统作为副调节回路,其设定值来自主调节回路――以LT-103为被控变量的液位控制系统。
以FT-101为被控变量的流量控制系统作为副调节回路――流量变动的时间常数小、时延小,控制通道短,从而可加快提高响应速度,缩短过渡过程时间,符合副回路选择的超前,快速、反应灵敏等要求。
下水箱V103为主对象,流量FT-101的改变需要经过一定时间才能反应到液位,时间常数比较大,时延大。
由上分析知:
副调节器选纯比例控制,反作用,自动。
主调节器选用比例控制或比例积分控制,反作用,自动。
实际上,串级控制相对于单PID控制而言,稳定性差,好处是在同样的副回路干扰下,超调非常小。
为了比较串级的这样好处,我们设计了如图2.2.1所示的工艺流程。
首先进行单PID实验,然变频器输出35Hz。
然后找到最好的控制参数,一般P=1,I=20000毫秒,等系统稳定后,改变变频器输出为50Hz,然后不断记录系统的超调量和稳定时间。
之后开始串级实验,同样设定变频器输出35Hz,系统稳定后,改变变频器输出为50Hz,然后不断记录系统的超调量和稳定时间。
如果控制好,可以发现在同样的变频器干扰下,串级超调量远远少于单PID的超调量。
2.2.2控制算法和编程
串级控制系统方框图如图2.2.2所示。
X
主调节器
LIC101
副调节器
LIC102
下水箱液位LT103
LT103
主回路干扰
给定值+
-
图2.2.2液位流量串级控制系统框图
流量计FT101
流量FT102
副回路干扰
以串级控制系统来控制下水箱液位,以第一支路流量为副对象,右边水泵直接向下水箱注水,流量变动的时间常数小、时延小,控制通道短,从而可加快提高响应速度,缩短过渡过程时间,符合副回路选择的超前,快速、反应灵敏等要求。
下水箱为主对象,流量的改变需要经过一定时间才能反应到液位,时间常数比较大,时延大。
将主调节器的输出送到副调节器的给定,而副调节器的输出控制执行器。
由上分析副调节器选纯比例控制,反作用(要想流量大,则调节阀开度加大),自动。
主调节器选用比例控制或比例积分控制,反作用(要想液位高,则调节阀开度加大),自动。
流量干扰通过变频器频率的变动来实现。
变频器频率从40-50Hz变动。
工业上串级的投入是逐步的,最好可以做到无扰切换,具体实现投入无扰的方法可以参考网络资料。
这里不考虑这么复杂。
2.2.3操作过程和调试
1、首先完成单PID调节阀流量控制,获得变频器35Hz变动到50Hz的超调量和稳定时间。
2、在现场系统上,打开手动调节阀QV-103、QV-115、QV-105,调节QV-116具有一定开度(闸板高度6毫米左右),其余阀门关闭。
3、在控制系统上,将流量计(FT-101)连到控制器AI1输入端,下水箱液位(LT-103)连到控制器AI0输入端,电动调节阀FV-101连到控制器AO0端。
把变频器设置为面板操作。
4、打开设备电源,包括变频器电源。
7、启动变频器到40-50Hz,系统开始运行。
8、首先将主调节器置手动状态,调整其输出为某个输出值,将它作为副调节器的SP值。
9、在上述状态下,整定副调节器的P参数。
要求可以稳定,而且比较快。
10、预置主调节器的P、I参数(不要设置的太大),再将主调节器切换到自动状态。
11、依据记录曲线,调整主调节器的P、I参数、副调节器的P参数,一般是副调节器较大,主调节器较小。
副调节器:
一般纯比例(P)控制,反作用,自动,KC2(副回路的开环增益)较大。
主调节器:
比例积分(PI)控制,反作用,自动,KC1〈KC2(KC1主回路开环增益)。
12、待系统稳定后,类同于单回路控制系统那样,对系统加扰动信号,扰动的大小与单回路时相同。
就是把变频器从40变动到50Hz。
13、通过反复对副调节器和主调节器参数的调节,使系统具有较满意的动态响应和较高的静态精度。
14、使用单回路进行液位控制,流程和串级一样。
增加流量干扰,就是把变频器从40变动到50Hz。
控制曲线进行对比,看效果如何。
2.2.4实验结果及记录
如果串级超调量远远少于单PID的超调量,则效果效果比较好了。
思考一下,如果干扰在主回路又如何?
例如在单PID的情况下,把闸板从开口11毫米突然变化到5毫米,看系统的超调量如何。
在串级下进行同样的操作,看系统的超调量如何。
分析理论上这个超调量是否不同。
2.3前馈-反馈控制系统实验
2.3.1工艺过程描述
前馈控制又称扰动补偿,它与反馈调节原理完全不同,是按照引起被调参数变化的干扰大小进行调节的。
在这种调节系统中要直接测量负载干扰量的变化,当干扰刚刚出现而能测出时,调节器就能发出调节信号使调节量作相应的变化,使两者抵消。
因此,前馈调节对干扰的克服比反馈调节快。
但是前馈控制是开环控制,其控制效果需要通过反馈加以检验。
前馈控制器在测出扰动之后,按过程的某种物质或能量平衡条件计算出校正值。
前馈-反馈控制的工艺和串级完全一样,这是一个让人迷惑的地方。
实际的好处可能就是体现在比例调节