污水处理工艺基本方案Word文档下载推荐.docx
《污水处理工艺基本方案Word文档下载推荐.docx》由会员分享,可在线阅读,更多相关《污水处理工艺基本方案Word文档下载推荐.docx(16页珍藏版)》请在冰豆网上搜索。
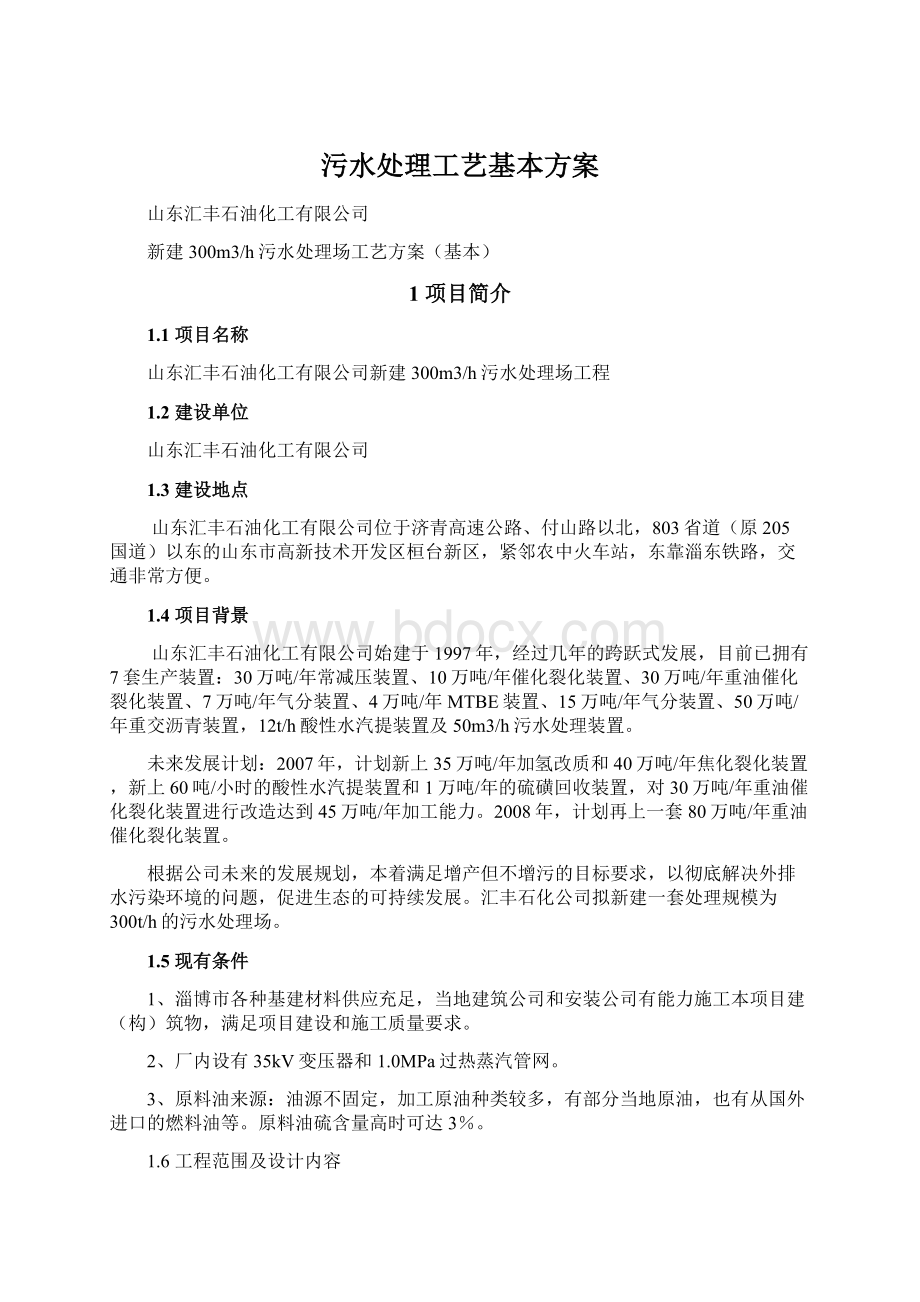
Ø
山东汇丰石化有限公司关于增建污水处理场的会议纪要200611.16
《室外排水设计规范》GB50014-2006
《室外给水设计规范》GB50013-2006
《污水综合排放标准》GB8978-1996
《石油化工污水处理设计规范》SH3095-2000
《建筑给水排水设计规范》GB50015-2003
《石油化工生产建筑设计规范》SH3017-1999
《石油化工企业设计防火规范》GB50160-92
《石油化工给水排水工程系统设计规范》SH3015-2003
《石油化工给排水水质标准》SH3099-2000
2.1.2编制原则
选用在国内已有成功应用业绩,成熟可靠的工艺,同时力求先进;
所有处理单元的数量按照≮2座考虑,设计应满足50~120%操作弹性需要;
结合出水执行严格的排放标准的要求;
为提高出水达标率,应设置有出水把关单元;
设计污水处理系统时,应尽量避免二次污染,尽可能减少对周围环境的影响;
运行成本省,能耗低。
2.2设计规模
系统划分:
整个污水处理场按一个含油污水系统设计;
设计规模:
300m3/h。
污水量:
最大值Qmax=360m3/h
正常水量Q正常=300m3/h
实际水量Q=250m3/h
水量时变化系数:
50%~120%
2.3设计进水水质
COD:
800~1400mg/lBOD:
300~400mg/l
NH3-N:
60-80mg/lSS:
50-100mg/l
油:
500-1000mg/l
2.4设计出水水质
设计污水处理出水水质执行国标《污水综合排放标准》(GB8978-96)二类一级指标,即:
pH:
6-9SS:
70mg/l
BOD5:
20mg/lCOD:
60mg/l
NH3-N:
15mg/l油类:
5mg/l
2.5工艺设计
2.5.1设计进出水水质分析
污水处理工艺的选择,取决于加工原油的性质及其加工工艺,以及由此产生的污水水质特征和对污水处理后出水的出路要求。
尤其与污水中所含主要污染物的特性息息相关。
根据本厂炼油装置的组成以及炼制原油不固定的特点,原料油应归于杂质原油。
常减压蒸馏装置的电脱盐将排出部分含盐污水,排出含油污水的大户主要是常减压、几套催化裂化装置。
一些含硫和氨较高的污水経酸性水汽提,得到进一步回收和处理。
杂质原油含油污水的主要特点主要有:
●污水含油量较高,重油的比重较大;
●有机污染物含量高,特别是烃类及其衍生物含量高。
表现为污水的COD指标较高,且含有大量生物难降解的成分;
●污水的pH值波动较大;
水温较高,一般在38℃以上;
2.5.2处理工艺选择
根据2006.11.16会议纪要,污水处理后暂不考虑回用,全厂污水仅按含油污水一个系统进污水处理场,污水处理按含油污水一个系统设计。
2.5.2.1含油污水处理工艺
⑴含油污水处理工艺流程介绍
1方案一
格栅泵提升调节除油罐平流斜板隔油涡凹气浮
部分回流水加压溶气气浮水解酸化A/O生物脱氮处理
曝气生物滤池BAF污水监测排放
2方案二
3
格栅泵提升调节储油罐平流斜板隔油LPC(高效固液浓缩沉降分离装置)CAST(循环活性污泥技术)生物处理曝气生物滤池BAF
污水监测排放
4方案三
格栅泵提升调节储油罐平流斜板隔油涡凹气浮
部分回流水加压溶气气浮水解酸化CAST(循环活性污泥技术)生物处理
曝气生物滤池BAF污水监测排放
注:
三个方案中除水处理工艺外,均含有三泥的处理工艺,此处暂未例入。
⑵含油污水处理工艺流程说明
方案一:
物化处理段:
污水进入污水处理场先进机械格栅池,将系统管网流来的杂物清除掉;
污水进入提升泵房,污水经泵提升送至调节储油罐,调节储油罐的作用是将污水中污油及水中的悬浮杂物,由于各自密度的不同,油浮于液面,悬浮杂物沉于罐底。
浮于液面的油品,通过收油设施将浮油回收,沉于罐底的悬浮杂物,通过一定措施排出罐体;
污水通过调节除油罐污水中含油量将在500mg/l以下;
调节罐及其内收油设施
调节除油罐中的污水自流进入平流斜板隔油池,污水在隔油池内,仍然是通过自净(靠自身的密度差)方式,油珠経近2h的上浮飘浮于水面,通过刮油刮泥机油集中到集油管内,排至收油管路中。
而池底沉积的油泥経刮板刮至集泥坑,开启排泥阀将污泥排至污泥回收管道;
经平流隔油池的出水含油量大约降至150mg/l左右,経斜板除油水的含油量将降至60mg/l左平流斜板隔油池立面示图
右;
隔油后的污水再次自流进入气浮除油阶段,气浮除油阶段分为两级,一级气浮采用涡凹CAF气浮,涡凹CAF系统主要有曝气区、气浮区、回流系统、刮渣系统及排水系统等几部分组成,其工作原理为:
未经处理的污水首先进入装有涡凹曝气机的曝气区,该区设有专利的独特曝气机,通过底部的中空叶轮的快速旋转在水中形成了一个真空区,此时水面上的空气通过中空管道抽送至水下,并在底部叶轮快速旋转产生的三股剪切力下把空气粉碎成微气泡,微气泡与投加的絮凝剂形成的絮凝体粘合,将污水中微细油粒有机地结合在一起,上浮于液面,从而达到气浮除油的目的。
到达液面后含油絮凝体便依靠这些微气泡支撑和维持在水面上形成浮渣,通过刮渣机将浮渣刮入污泥收集槽,净化后的水由溢流槽溢流排放。
该系统实行自动化控制,完全摒弃了过去溶气气浮系统中的压力溶气罐、电耗很高的空压机、循环泵以及易堵塞的喷嘴或释放器,具有结构简单、设备整体性好、占地小、能耗低、操作维修简单、去除率高、无噪音、安装方便等优点。
涡凹CAF气浮系统的工作原理完全不同于DAF(压力溶气气浮)。
它是通过特制的专利曝气机来产生微气泡的,因此不需要空压机、高压泵、压力溶气罐、循环泵、喷嘴等附属设备。
由于CAF产生的微气泡是DAF的4倍,确定CAF的尺寸只需要流量这一参数,不象DAF还需要考虑污染物的浓度。
CAF每台曝气机的气泡量为28.32升/秒,气泡粒径为5um~500um,其中200um以下的占大多数,气浮池的停留时间约为17分钟。
在一级气浮阶段,涡凹气浮设备出口污水的含油量可降至50mg/l以下;
二级气浮一般采用部分污水回流加压溶气气浮,部分污水回流加压溶气气浮是将气浮分离段的出水,其30%~40%回流加压至0.4MPa进溶气罐,然后带压的污水连同带压的空气再次进入气浮分离段,通过压力释放器将带压的污水和空气变为常压,压力溶气释放后形成细小气泡,通过细小而分散的气泡粘附污水中经过混凝剂凝聚的分散微细油和悬浮物形成为絮凝漂浮物,使分散微细油和悬浮物从污水中分离出来。
为降低能耗,溶气气源目前一般不再选用空压机,而采用一种新的溶气装置:
内循环压力溶气装置。
(内循环压力溶气装置内分别置于两个与大气相连的水射器,分别接到压力回流水管和内循环压力水管上,当溶气罐外回流水泵和内循环水泵分别工作时,罐内分别为回流水泵和内循环水泵服务的水射器将空气带进罐内,罐中空气宜相应地被溶解而又被溶气水带走。
罐内空气量逐渐减少,罐中液面慢慢上升,液面升至一定位置时,液面控制仪表开始工作,启动内循环水泵,在泵压力作用下,串联于内循环泵上的水射器又将罐外的空气再次带进罐内并部分溶入水中,使液面下降,液面降至某一水位,内循环泵停止工作。
由于工作水泵在连续工作,罐内空气也会慢慢减少,最低水位将随着罐内空气量的减少而回升,直至液位重新升至最高水位。
为内循环压力溶气装置服务的内循环水泵周而复始的间断工作,回流水泵连续的工作,造成灌内水位一会儿升至最高一会儿降到最低,从而保持罐内压力稳定于一定值和溶解于水中的空气量,无需另设空压机供气。
)
在二级气浮阶段,部分污水回流加压溶气气浮设施出口含油量可降至20mg/l以下。
污水通过物化处理阶段,即污水调节储油罐、平流斜板隔油池、两级气浮,基本完成除油任务,部分有机污染物(约20%~30%)也将被除掉,就可以进入下一步去除有机污染物阶段。
生物处理段:
物化处理后污水中剩下的污染物绝大部分是有机物染物,这部分污水自流进入生物处理阶段。
生物处理阶段本方案所采用的工艺为:
A/O(前置兼氧段+好氧段+二沉池)工艺。
即硝化段和反硝化段均为活性污泥法反应池,在两段反应池后,配备相应的二次沉淀池。
设计负荷值应由试验求得,在无试验数值情况下一般按经验选用:
有机负为0.24kgCOD/(kgMLSS·
d)、
氨氮负荷为0.033kgNH3-N/(kgMLSS·
d)。
二次沉淀池立面示图
当污水进入反硝化池(缺/兼氧池),与二沉池送来的回流(硝态)液(100
%~200%硝态液)和回流污泥(50%~100%)混合,在厌氧或兼氧环境下进行生物化学反应。
反硝化细菌是异养型兼性厌氧细菌,它能利用各种有机物作为反
硝化过程中电子供体(能源),利用硝态液(硝酸盐)代氧作用,成为电子最终受体(氧源),将亚硝态氮在硝化菌作用下氧化为硝酸盐和气态氮,将水中氨氮指标降到设计要求的数值。
在生物反硝化过程中,不仅可使氮化合物被还原,还可使有机物底物得到氧化分解,即反硝化作用将同时起到去碳、脱氮的效果。
反硝化菌是一种异氧型兼性厌氧菌,它需在缺氧条件下生存。
因此,反应器的溶解氧过多,将会抑制反硝化菌的异化作用。
但氧对反硝化菌本身并非如此,因菌体内某些酶系统是在有氧条件下才能合成,因此,缺氧池内溶解氧应控制在0~0.5mg/l。
缺/兼氧池出水重力流进好氧池(硝化池),主要去除水中的COD(碳化)和在亚硝化菌作用下将NH3-N(硝化)转换为亚硝酸盐,处理后污水进二沉池。
经二沉池处理后的水,其中100%~200%的回流量,作为硝态氮液送至缺氧池,作为水中的亚硝态氮的电子最终受体(氧源),将水中NH3-N转化为氮气最终除掉。
剩余处理后污水排放至场外。
经二沉池沉置和分离的污泥,其中50%~100%回流至缺氧池,用于提高池内污泥浓度,以利于生物对污水的分解吸附作用。
好氧池内溶解氧控制在2mg/l。
为了达到硝化的目的,反应器的负荷率应低,微生物停留时间应长。
即反应器容积要大些,剩余污泥量少些。
污水经A/O工艺处理后其出水污染有机物指标COD将降至100mg/l~60mg/l,NH3-N将降至50mg/l~15mg/l左右;
污水経生物脱氮(A/O)工艺处理后,尚不能进一步达到国标二类一级排放标准,污水在进入曝气生物滤池(BAF),将进一步去除有机污染物和滤掉水中的悬浮物,从而达到国标《污水综合排放标准》(GB8978-96)二类一级指标。
污水经BAF工艺处理后其出水污染有机物指标COD将降至60mg/l以下,NH3-N将降至15mg/l以下;
污水经生物处理后自流进监测池,污水经检测达到国标《污水综合排放标准》(GB8978-96)二类一级指标,即可就地排放或进一步处理后回用。
方案二:
根据环保技术的最新发展,方案二与方案一有所不同点有两项:
物化部分隔油后增加LPC除油技术,生物处理过程改用循环活性污泥工艺(CAST)。
简述如下:
物化处理段的主要设施称为高效固液浓缩分离器(LPC)。
石油化工污水是一种高浓度难处理的污水,污水中的COD主要是由污水中的烃类、醇类、醛类、羧酸类、酚类等类物质所提供的。
生产装置正常运行时的CODcr为800~1200mg/L、BOD5在300~500mg/L,石油类含量高达200~300mg/L。
这些高浓度的污染物质在生物处理工艺很难将它们降解,所以,生物处理工艺一般要求污水中CODcr≤500mg/L;
而且,石化生产污水通常存在COD高、BOD低,BOD/BOD的比值小于0.3,其水质的生化性能很差。
所以,石化污水在处理时,必须先采用优良的物化工艺技术,将污水中的污染“峰值”去掉,提高BOD/COD的比值,使其生化性增强,将污水中的污染物平稳控制在生物易于降解的范围,才能使污水进入二级生物处理系统,使处理后的水质达到良好的处理效果。
石化炼油污水处理一般分两步进行,首先,将污水中石油类除掉;
其次,才能对有机物染物进行处理。
石油类物质在水中存在的形式有三种,即机械混溶(称浮油)、油水乳化形成的O/W型乳液(称乳化油)、油水真溶液(称饱和溶解油)。
浮油可通过撇油装置除去60%~80%,而乳化油在水中一般能稳定存在,必须要通过有效地破乳工艺才能除去。
如果选择的处理工艺和LPC工艺原则流程
药剂不能在物化段,将这种O/W型的乳化油破乳并有效地除去,污水进入二级生物处理系统时,油乳将很快将生物膜或菌胶团包裹、覆盖,使水中的溶解氧不能进入菌胶团,生物的代谢受阻,传质速度减慢,乃至终止,轻则严重影响处理效果,重则使菌类缺氧死亡,所以,良好的物化处理工艺和高效的混/絮凝破乳剂是炼油污水处理系统能否有效、稳定正常运行的关键。
石化炼油污水处理完成第一步即物化处理,就是在污水调节和隔油后,采用LPC工艺。
石化炼油污水进入污水处理场,通过均质和隔油后,进入LPC前反应器,加入混凝剂PPA,对乳化的石油类物质破乳,进入后反应器,再加入絮凝剂PPM,污水然后进入LPC高效固液浓缩分离器中进行沉渣分离和浓缩,沉渣送干燥系统干燥,达到控制标准的废水进入二级生物处理系统,不达控制标准废水返回LPC前反应器。
LPC物化处理工艺特点:
●LPC物化法、配套的设备及加药系统处理效率高、用药少。
●该工艺采用的水处理混凝剂和絮凝剂—PPA、PPM具有高效的破乳和絮凝
能力,能将石油类中的乳化油破乳,乳化油进入二级生物处理段后,将生物膜或菌胶团包裹、覆盖,使水中的溶解氧不能进入菌胶团,造成生物代谢受阻,传质速度减慢,乃至终止,轻则严重影响处理效果,重则使菌类缺氧死亡的问题,这是二级生物处理装置能否有效、稳定正常运行的关键。
●LPC工艺的固液分离中采用了“高效固液浓缩分离器”,避免其它工艺
采用气浮分离所造成混凝体破坏从而影响处理效果的问题,沉渣也不需要再浓缩,直接送干燥。
●所采用的成套设备为钢制设备,同时,由于设备内表面在运行较短的时
间后能覆盖一层生物膜,使设备免于腐蚀,可以防止采用钢筋混凝土池难于避免的腐蚀和高浓度污水渗漏对地下水造成污染的问题。
●LPC工艺能根据水质的变化自动确定加药量,使各种水质的污水处理后
始终保持不对二级生物系统造成冲击。
由于PPA具有的特殊破乳功能,将沉渣从亲水性变成疏水性极易干燥,干燥后的污泥含水率60-70%,干污泥片易于处理。
根据该技术的工程实测,LPC工艺的处理效率较高,污水中含油量进口150mg/l,出口小于15mg/l;
生物处理段地主要构筑物称为循环活性污泥工艺(CAST)。
循环式活性污泥法(CAST,CyclicActivatedSludgeTechnology)主要完成进水中大部分有机物的去除,同时通过硝化作用去除氨氮,并通过同步反硝化作用降低出水的总氮,回收能量和碱度。
CAST工艺系统的一个重要特性是在工艺过程中不设缺氧混合阶段的条件在下,高效地进行硝化和反硝化,从而达到深度去除氮的目的。
在一个周期内,硝化和反硝化在曝气阶段同时进行(co-currentorsimultaneously)。
运行时控制供氧强度以及曝气池中溶解氧浓度,使絮体的外周能保证有一个好氧环境进行硝化,由于溶解氧浓度得到控制,氧在污泥絮体内部的渗透传递作用受到限制,而较高的硝酸盐浓度(梯度)则能较好地渗透到絮体的内部,因此在絮体内部能有效地进行反硝化过程。
实际监测的数据也证明了其同步硝化和反硝化功能。
CAST工艺的建立是基于同步硝化反硝化理论,带有生物选择器和除磷功能的一种改进的序批式活性污泥法污水处理工艺。
单个池体运行方式为间歇进水、间歇出水,组合后系统为连续均匀进、出水。
CAST工艺每一操作循环由下列四个阶段组成:
进水、曝气、沉淀、撇水、闲置(视具体运行条件而定)。
下图是循环活性污泥工艺一个周期的运行示意图:
上述各个阶段组成一个循环,并不断重复。
循环开始时,开始充水,池子中的水位由某一最低水位开始上升,经过一定时间的曝气和混合后,停止曝气,以使活性污泥进行絮凝并在一个静止的环境中沉淀,在完成沉淀阶段后,由一个移动式撇水堰排出已处理的上清液,使水位下降至池子所设定的最低水位。
完成上述操作阶段后,系统进入下一循环过程,重复以上操作。
综上分析,相比A2/O等其他工艺,CAST工艺的主要优点如下:
⏹占地面积省,布置紧凑,无需初沉池和二沉池;
⏹在一个反应池内完成硝化和反硝化;
⏹所有的操作都在一个反应池内,便于模块化建设;
⏹抗冲击负荷能力强,不会有污泥流失;
⏹有效控制污泥膨胀;
⏹操作简单,完全自动化,运行能耗省。
CAST主要由以下几部分组成:
选择区、主反应区、撇水设备、污泥回流和剩余污泥排放设备、控制系统。
如下图所示:
回流污泥泵将反应区的活性污泥回流到选择器中。
在选择器中,基质浓度梯度较大,污泥负荷较高,可有效避免污泥膨胀,提高系统运行的稳定性。
另外,通过间歇曝气方式,可使活性污泥周期性地经历好氧和厌氧阶段,生物选择器的设置可以有效的防止污泥的膨胀,抑制丝状菌的繁殖,增强了系统的稳定性。
在循环式活性污泥法中,通过设置选择器可以允许以任意进水速率进水而不会产生污泥膨胀,因此,循环式活性污泥法系统无需设置独立的厌氧搅拌阶段、缺氧搅拌阶段以及进水贮水池等,从而可以大大简化工艺过程,节省工程投资(无需搅拌装置)和能耗。
循环式活性污泥法系统较之传统序批式SBR法其工艺设置和操作得到很大程度的简化,为在大中型污水处理厂的应用创造了良好的条件。
在曝气阶段主要完成生物降解过程,在非曝气阶段虽然也有部分生物作用,但主要是完成泥水分离过程。
因此,循环式活性污泥法系统无需设置二沉池,可以省去传统活性污泥法中曝气池和二沉池之间的连接管道。
完成泥水分离后,利用撇水堰排出每一操作循环中的处理出水。
根据活性污泥实际增殖情况,在每一处理循环的最后阶段(撇水阶段)自动排出剩余污泥。
经循环活性污泥工艺(CAST)处理的污水,其出水指标:
COD≤100~60mg/l,NH3-N≤50~15mg/l。
方案三
该方案在前两方案基础上进行局部调整演变而来的。
物化处理段采用方案一物化处理段,生化处理段采用方案二生化处理段。
⑶两工艺方案工程量(主要的)
方案一
格栅井L=2.04m
B=0.7m
H=1.0m
格栅机:
回转式格栅除污机
格栅井间数:
2
调节储油罐3000m3钢制拱顶罐2座
罐内设置除油和清渣设备
平流斜板隔油池L=21.6+斜板段m
B=4.5m
Ho=2m
n=4间
每间设置一套刮油刮泥机、一套集油管、两套排泥阀
涡凹气浮装置L=15.09m
B=2.41m
H=1.83m
n=2台套
部分回流污水加压溶气气浮池
L=10m
B=4.5m
H=2m
每间配置一台套内循环回流水加压溶气气浮设备、一台套刮沫机
水解酸化池L=12.5m
B=9m
H=6.4m
n=2间
生物脱氮(A/O)曝气池
A(缺氧段)L=43m
B=10m
H=4.5m
n=1间
O(缺氧段)L=43m
n组鼓风曝气头、配套的鼓风机数台套
曝气生物滤池(BAF)L=5.0m
B=5.3m
H=7.0m
配套的鼓风机数台套
方案二
格栅井L=2.04m
高效固液浓缩分离器(LPC)(暂缺)
循环活性污泥(CAST)曝气池
L=40m
H=4.0m
每间池内出水口设置一台套滗水器、一台套污泥回流泵、n组鼓风曝气头、配套的罗次鼓风机等
⑷含油污水工艺流程选择(暂缺)
方案一、方案二、方案三技术经济比较:
2.5.2.2主要工艺单元(暂缺)
⑴物化处理过程(着重阐述除油过程及其效果)
1调节储油罐(含罐中罐)
2隔油池(罐)
3气浮除油池(罐)
⑵生物处理过程
①水解酸化
②主处理构筑物-A/O或CAST
5深度处理构筑物-曝气生物滤池(BAF)、砂滤、活性炭吸附、氯气消毒
2.5.2.3各处里单元处理效果预测
生物处理前后效果预测
序