模具设计基础文档格式.docx
《模具设计基础文档格式.docx》由会员分享,可在线阅读,更多相关《模具设计基础文档格式.docx(32页珍藏版)》请在冰豆网上搜索。
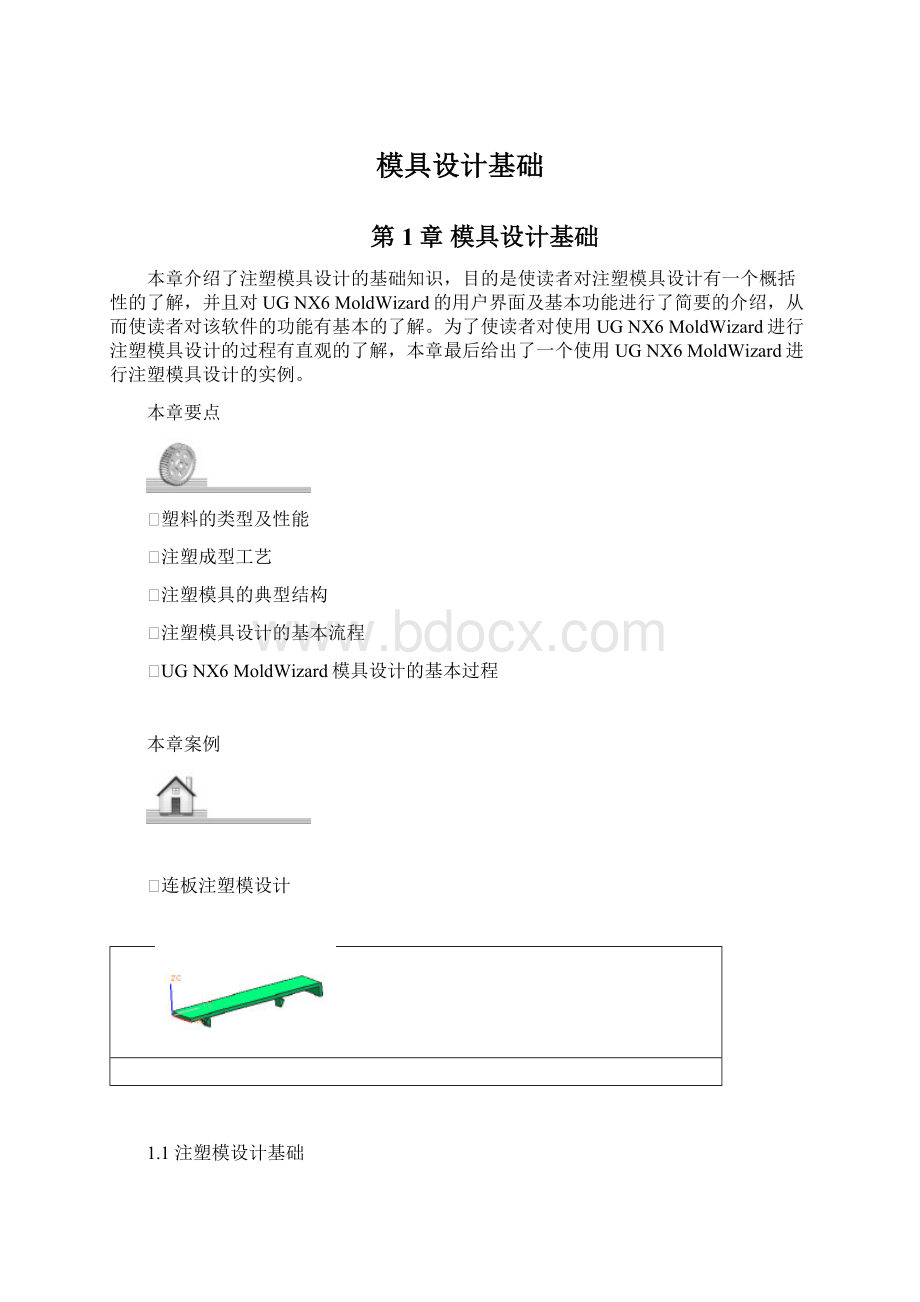
通用塑料是指常用的塑料品种,这类塑料产量大、用途广、成型性好,价格便宜,包括聚氯乙烯、聚乙烯、聚丙烯、聚苯乙烯、酚醛和氨基塑料6种。
(2)工程塑料
工程塑料是具有优良力学性能的一类塑料,它能代替金属材料,制造承受载荷的工程结构零件。
常见的工程材料包括ABS、聚甲醛、聚碳酸脂和聚酰胺等。
在工程塑料中又将其分为通用工程塑料和特种工程塑料两大类。
通用工程塑料包括聚酰胺、聚甲醛、聚碳酸脂、改性聚苯醚、热塑性聚酯、超高分子量聚乙烯和甲基戊烯聚合物等。
特种工程材料又有交联型和非交联型之分。
交联型的有聚氨基双马来酰胺和耐热环氧树脂等;
非交联型的有聚酰亚胺和聚醚酮等。
(3)特种塑料
特种塑料一般是指具有某一方面特殊性能的塑料,用于特殊需求场合。
常见的有氟塑料和有机硅等。
3)按加工方法分类
根据各种塑料不同的成型方法,可以分为膜压、层压、注射、挤出、吹塑、浇铸塑料和反应注射塑料等多种类型。
膜压塑料多为物性的加工性能与一般固性塑料相似的塑料;
层压塑料是指浸有树脂的纤维织物,经叠合、热压而结合成为整体的材料;
注射、挤出和吹塑塑料多为物性和加工性能与一般热塑性塑料相类似的塑料;
浇铸塑料是指能在无压或稍加压力的情况下,倾注于模具中能硬化为一定形状制品的液态树脂混合料,如MC尼龙等;
反应注射塑料是用液态原材料加压注入膜腔内,使其反应,固化为一定形状制品的塑料,如聚氨酯等。
2.塑料的性能
塑料性能主要是指塑料在成型工艺过程中所表现的成型特性。
在模具的设计过程中,要充分考虑这些因素对塑件的成型过程和成型效果的影响。
(1)成型收缩
塑料注射成型的过程是在较高温度下将熔融的熔料注入型腔内,固化、冷却后成型。
塑件自模具中取出冷却至室温后,发生尺寸收缩,这种性能称为收缩性。
塑料制件的收缩不仅与塑料本身的热胀冷缩性质有关,而且还与模具结构及成型工艺条件等因素有关,故将塑料制件的收缩通称为成型收缩。
收缩性的大小以收缩率表示,即单位长度塑件收缩量的百分数。
设计模具型腔尺寸时,应按塑件所使用的塑料的收缩率给予补偿,并在塑件成型时调整好模温、注射压力、注射速度及冷却时间等因素,以控制零件成型后的最终尺寸。
(2)流动性
塑料的流动性是指在成型过程中,塑料熔体在一定的温度和压力作用下填充模腔的能力。
流动性差的塑料在注塑成型时不易填充模腔,易产生缺料,在塑料熔体的汇合处不能很好地熔接而产生接痕,这些缺陷会导致零件报废。
反之,若材料的流动性太好,注塑时易产生溢料飞边和流延现象。
浇注系统的形式、尺寸、布置,包括型腔的表面粗糙度、浇道截面厚度、型腔形式、排气系统和冷却系统等模具结构对塑料的流动性有着重要影响。
热塑性塑料按流动性可分为以下3类。
●流动性好的尼龙、聚乙烯、聚苯乙烯、聚丙烯、醋酸纤维等。
●流动性一般的ABS、有机玻璃、聚苯醛、聚氯醚。
●流动性差的聚碳酸脂、硬聚氯乙烯、聚苯醚、氟塑料。
(3)取向和结晶
取向是由于各向异性导致的塑料在各个方向上收缩不一致的现象。
影响取向的因素主要有塑料品种、塑件壁厚和温度等。
除此之外,模具的浇口位置、数量和断面大小对塑件的取向方向、取向程度和各个部位的取向分子情况有重大影响,是模具设计中必须重视的问题。
结晶是指塑料中树脂大分子在空间呈现有序排列现象,影响结晶的主要因素有塑料的类型、添加剂、模具温度和冷却速度。
结晶率对于塑料的性能有重要的影响,因此在模具设计和塑件成型过程中应注意。
(4)吸湿性
吸湿性是指塑料对水分的亲疏程度。
在成型加工过程中,当塑料的水分含量超过一定的限度时,水分在高温料筒中变为气体,促使塑料高温分解,导致成型缺陷。
根据吸湿性,塑料大致可以分为两类,一类是具有吸湿或黏附水分倾向的塑料,如聚酰胺、聚碳酸脂、ABS和聚苯醚等;
另一类是吸湿或黏附水分极少的塑料,如聚乙烯和聚丙烯等。
(5)热敏性
某些热稳定性差的塑料在高温下受热时间长、浇口截面过小或剪切作用大时,料温增高就容易发生变色、降解、分解的倾向,塑料的这种特性称为热敏性。
为防止热敏性塑料出现过热分解现象,可采取加入稳定剂、合理选择设备、合理控制成型温度和成型周期、及时清理设备等措施。
另外,也可以采取给模具表面镀铝、合理设计模具的浇注系统等措施。
1.1.2注塑成型工艺
注塑成型又称注射成型。
注射成型是使热塑性或热固性成型料先在加热料筒中均匀塑化,而后由柱塞或移动螺杆推挤到闭合模具的模腔中成型的方法。
注射成型的成型周期短(几秒到几分钟),成型制品的质量范围可以是几克到几十千克,能一次成型外形复杂、尺寸精确、带有金属或非金属嵌件的成型品。
因此,注塑成型工艺在整个塑料制品生产行业中占有非常重要的地位。
1.注塑成型的工作原理
利用塑料的可挤压性和可塑性,首先将松散的粒料或粉状成型物料从注射机的料斗送入高温的机筒内加热熔融塑化,使之成为黏流态熔体;
然后用柱塞或螺杆压缩并推动塑料熔体向前移动,使熔体以最大的流速通过机筒前端的喷嘴,并以最快的速度注射入温度较低的闭合模具型腔中;
经过一段保压冷却成型时间后,开启模具便可从模腔中脱出具有一定形状和尺寸的塑料制品。
这个过程经注塑成型机和注塑模具来实现。
注塑成型工作原理如图1-1所示。
图1-1注塑成型的工作原理
2.注塑成型的工艺参数
注塑成型工艺的核心问题,就是采用一切措施以得到塑化良好的塑料熔体,并将塑料熔体注射到型腔中,在控制条件下冷却成型,使塑件达到所要求的质量。
注塑成型有3大工艺条件,分别为温度、压力和成型时间。
1)温度
注塑成型过程需控制的温度主要包括模具温度、料筒温度和喷嘴温度。
(1)模具温度
模具温度直接影响塑料熔体的充模能力以及塑件的内在性能与外观质量。
通常,提高模具温度可以改善熔体的流动性、增强制件的密度和结晶度并减小充模压力。
但制件的冷却时间、收缩率和脱模后的翘曲变形将会延长和增大,且生产率也会因为冷却时间的延长而下降。
因此模具冷却系统的设计对于塑件的成型质量和成型效率有非常重要的影响,是模具设计中应特别注意的问题。
(2)料温
料温是指塑化物料的温度和从喷嘴注射出的熔体温度。
其中,前者称为塑化温度,后者称为注射温度,分别取决于机筒和喷嘴两部分的温度。
料温应根据塑料的熔点和软化点、制件的大小、厚薄及成型时间来确定。
通常靠近料斗处温度较低,喷嘴端较高。
2)压力
注塑成型时需要选择与控制的压力包括注射压力、保压力和背压力。
其中,注射压力和注射速度相辅相成,对塑料熔体的流动和充模具有决定作用。
注射压力的大小根据塑料的性能、制件的大小、厚薄和流程长短来确定。
在塑料熔体黏度较高、壁薄、流程长等情况下,适合采用较高的注射压力。
3)成型时间
成型时间是指完成一次注射成型全过程所需的时间。
成型时间过长,在料筒中原料因受热时间过长而分解,制件会因内应力大而降低机械强度。
成型时间过短则会因塑化不完全导致制件易变形。
因此,合理的成型时间是保证制件质量、提高生产率的重要条件。
1.1.3注塑模具的基本结构和分类
1.注塑模具的基本结构
模具基本结构一般分为两板模(单分型面注射模)、三板模(双分型面注射模)和热流道3种。
模具结构一般由客户或者依据产品来决定的。
在这里主要介绍两板模的结构组成。
1)两板模(单分型面注塑模)
注射模具由动模和定模两部分组成,动模安装在注射成型机的移动模板上,定模安装在注射机的固定模板上。
在注射成型时动模和定模闭合构成浇注系统和型腔。
开模时动模与定模分离以便取出塑料制品。
如图1-2所示为典型的两板模(单分型面注射模)结构,根据模具中各个部件的作用,一般可将注射模分为以下几个基本组成部分。
1—定位圈;
2—主流道衬套;
3—定模座板;
4—定模板;
5—动模板;
6—动模垫板;
7—动模底座;
8—推出固定板;
9—推板;
10—拉料杆;
11—推杆;
12—导柱;
13—型芯;
14—凹模;
15—冷却水通道
图1-2典型的两板模(单分型面注射模)结构
(1)成型部件
成型部件由型芯和凹模组成。
型芯形成制品的内表面形状,凹模形成制品的外表面形状。
合模后型芯和凹模便构成了模具的型腔(如图1-2所示),该模具的型腔由型芯13和凹模14组成。
按工艺和制造要求,型芯或凹模有时由若干拼块组成,有时做成整体,仅在易损坏、难加工的部位采用镶件。
(2)浇注系统
浇注系统又称为流道系统,它是将塑料熔体由注射机喷嘴引向型腔的一组进料通道,通常由主流道、分流道、浇口和冷料穴组成。
浇注系统的设计十分重要,它直接关系到塑件的成型质量和生产效率。
(3)导向部件
为了确保动模与定模合模时能准确对准中心,在模具中必须设置导向部件。
在注射模中通常采用4组导柱与导套来组成导向部件,有时还需在动模和定模上分别设置互相吻合的内、外锥面来辅助定位。
为了避免在制品推出过程中推板发生歪斜现象,一般在模具的推出机构中还设有使推板保持水平运动的导向部件,如导柱与导套。
(4)推出机构
在开模过程中,需要有推出机构将塑件及其在流道内的凝料推出或拉出。
如在图1-2中,推出机构由推杆11和推出固定板8、推板9及主流道的拉料杆10组成。
推出固定板和推板用于夹持推杆。
在推板中一般还固定有复位杆,复位杆在动模和定模合模时使推出机构复位。
(5)调温系统
为了满足注射工艺对模具温度的要求,需要有调温系统对模具的温度进行调节。
对于热塑性塑料用注射模,主要是设计冷却系统使模具冷却。
模具冷却的常用办法是在模具内开设冷却水通道,利用循环流动的冷却水带走模具的热量;
模具的加热除可用冷却水通道通热水或蒸汽外,还可在模具内部和周围安装电加热元件。
(6)排气槽
排气槽用于将成型过程中的气体充分排出。
常用的办法是在分型面处开设排气沟槽。
由于分型面之间存在有微小的间隙,对于较小的塑件,因排气量不大,可直接利用分型面排气,不必开设排气沟槽,一些模具的推杆或型芯与模具的配合间隙均有排气作用,有时不必另外开设排气沟槽。
(7)侧抽芯机构
有些带有侧凹或侧孔的塑件,在被推出以前必须先进行侧向分型,抽出侧向型芯后方能顺利脱模,此时需要在模具中设置侧抽芯机构。
(8)标准模架
为了减少繁重的模具设计与制造工作量,注射模大多采用了标准模架结构,如图1-2中的定位圈1、定模座板3、定模板4、动模板5、动模垫板6、动模底座7、推出固定板8、推板9、推杆11和导柱12等都属于标准模架中的零部件,它们都可以从有关厂家订购。
2)三板模(双分型面注塑模)
双分型面注射模具有两个不同的分型面用于分别取出流道凝料和塑件,与两板式的单分型面注射模具相比,双分型面注射模具在动模板与定模板之间增加了一块可以移动的中间板(又名浇口板),故又称三板式模具。
在定模板与中间板之间设置流道,在中间板与动模板之间设置型腔,中间板适用于采用点浇口进料的单型腔或多型腔模具。
如图1-3所示为典型的双分型面注射模结构简图。
从图中可见,在开模时由于定距拉板1的限制,中间板13与定模板14做定距离的分开,以便取出这两块板之间流道内的凝料,在中间板与动模板分开后,利用推件板5将包紧在型芯上的塑件脱出。
双分型面注射模具能在塑件的中心部位设置点浇口,但制造成本较高、结构复杂,需要较大的开模行程。
1—定距拉板;
2—弹簧;
3—限位销;
4—导柱;
5—推件板;
6—动模板;
7—动模垫板;
8—模底座;
10—推出固定板;
13—中间板;
14—定模板;
15—主流道衬套
图1-3三板模(双分型面注射模)结构
3)热流道注塑模
热流道模具是无流道注射模具(无流道凝料注射模具)的一种,无流道注射模具还包括绝热流道模具,它们都通过采用对流道加热或绝热的办法来保持从注射机喷嘴到浇口处之间的塑料保持熔融状态。
这样在每次注射成型后流道内均没有塑料凝料,这不仅提高了生产率,节约了塑料,而且还保证了注射压力在流道中的传递,有利于改善制件的质量。
此外,无流道凝料注射模具还易实现全自动操作。
这类模具的缺点是模具成本高,浇注系统和控温系统要求高,对制件形状和塑料有一定的限制。
如图1-4所示为热流道注塑模具。
1—动模座板;
2—垫块;
3—推板;
4—推出固定板;
5—推杆;
7—导套;
8—动模板;
9—型芯;
10—导柱;
11—定模板;
12—凹模;
13—支架;
14—喷嘴;
15—热流道板;
16—加热器孔道;
17—定模座板;
18—绝热层;
19—主流道衬套;
20—定位圈;
21—注射机喷嘴
图1-4热流道注塑模具
2.注塑模具的分类
注射模的分类方法很多。
例如,可按安装方式、型腔数目和结构特征等进行分类,但是从模具设计的角度上看,按注射模的总体结构特征分类最为方便。
除了上述已介绍的几种模具外,还有带有活动镶件的注射模具、带侧向分型抽芯的注射模具、自动卸螺纹的注射模具、推出机构设在定模一侧的注射模具几类。
1)带有活动镶件的注射模具
由于塑件的外形结构复杂,无法通过简单的分型从模具内取出塑件,这时可在模具中设置活动镶件和活动的侧向型芯或半块(哈夫块),如图1-5所示。
开模时这些活动部件不能简单地沿开模方向与制件分离,而在脱模时必须将它们连同制品一起移出模外,然后用手工或简单工具将它们与塑件分开。
当将这些活动镶件嵌入模具时还应可靠地定位,因此这类模具的生产效率不高,常用于小批量或试生产。
1—定模板;
2—导柱;
3—活动镶件;
4—型芯;
7—模底座;
8—弹簧;
9—推杆;
11—推板
图1-5带有活动镶件的注射模具
2)带侧向分型抽芯的注射模具
当塑件上有侧孔或侧凹时,在模具内可设置出由斜销或斜滑块等组成的侧向分型抽芯机构,它能使侧型芯作横向移动。
如图1-6所示为一斜导柱带动抽芯的注射模具。
在开模时,斜销利用开模力带动侧型芯横向移动,使侧型芯与制件分离,然后推杆就能顺利地将制品从型芯上推出。
除斜销和斜滑块等机构利用开模力作侧向抽芯外,还可以在模具中装设液压缸或气压缸带动侧型芯作侧向分型抽芯动作。
这类模具广泛地应用在有侧孔或侧凹的塑料制件的大批量生产中。
1—楔紧块;
2—斜销;
3—斜滑块;
5—固定板;
7—垫块;
8—动模座板;
12—拉料杆;
13—导柱;
14—动模板;
15—主流道衬套;
16—定模板;
17—定位圈
图1-6带侧向分型抽芯的注射模具
3)自动卸螺纹的注射模具
当要求能自动脱卸带有内螺纹或外螺纹的塑件时,可在模具中设置转动的螺纹型芯或型环,这样便可利用机构的旋转运动或往复运动将螺纹制品脱出,或者用专门的驱动和传动机构带动螺纹型芯或型环转动,将螺纹制件脱出。
自动卸螺纹的注射模具如图1-7所示,该模具用于直角式注射机,螺纹型芯由注射机合模机构的丝杠带动旋转,以便与制件相脱离。
1—螺纹型芯;
2—模座;
3—动模垫板;
4—定距螺钉;
6—衬套;
7—定模板
图1-7自动卸螺纹的注射模具
4)推出机构设在定模一侧的注射模具
一般当注射模具开模后,塑料制品均留在动模一侧,故推出机构也设在动模一侧,这种形式是最常用、最方便的,注射机的推出机构就在动模一侧。
但有时由于制件的特殊要求或形状的限制,制件必须要留在定模内,这时就应在定模一侧设置推出机构,以便将制品从定模内脱出。
定模一侧的推出机构一般由动模通过拉板或链条来驱动。
如图1-8所示的塑料衣刷注射模具,由于制品的特殊形状,为了便于成型采用了直接浇口,开模后制件滞留在定模上,故在定模一侧设有推件板7,开模时由设在动模一侧的拉板8带动推件板7,将制件从定模中的型芯11上强制脱出。
1—模底座;
2—动模垫板;
3—成型镶片;
4—螺钉;
5—动模;
6—螺钉;
7—推件板;
8—拉板;
9—定模板;
10—定模座板;
11—型芯;
12—导柱
图1-8推出机构设在定模一侧的注射模具
1.1.4注塑模具设计的基本流程
一套好的模具首先需要高水平的设计。
而一套模具的好坏,牵涉面非常广,包括对制品工艺性的分析、模具结构的设计、模具材料的选用、加工方法以及注射机和成型工艺等众多方面的研究。
因此,设计者除了要有模具方面理论知识和经验外,对设计前的周详思考也同样重要。
下面将介绍注塑模具设计的一般流程。
1.注塑成型制品的分析
(1)明确制品的设计要求
通常,模具设计人员通过制品的零件图就可以了解制品的设计要求。
但对形状复杂和精度要求较高的制品,就一定要了解制品的使用目的、外观及装配要求。
(2)明确制品的材质
塑料材料种类繁多,要确定材质以决定收缩率,了解流动性以决定浇口及流道设计。
(3)明确制品的生产批量
大批量生产时,为了缩短生产周期,提高生产率,只要制品适宜多型腔成型,通常采用多型腔模具和自动化生产。
但应该注意,模具中每增加一个型腔,所成型的制品精度将下降4%,因此,在确定型腔数目时,设计人员应根据具体情况选出最佳方案。
2.注射机的技术规范
进行注塑模设计时必须掌握现有注射机的有关技术规范,如注射机定位圈的直径、喷嘴前端孔径及球面半径、注射机的最大注射量、锁模力、注射压力和注射速度、固定模板和移动模板面积大小及安装螺孔位置、注射机拉杆间距、模具安装部位的尺寸、顶出杆直径及其位置、顶出行程等。
3.模具结构设计
(1)确定分型面
确定分型面是模具设计的重要环节,由设计人员灵活运用,需综合考虑各项原则,如制品外观、顶出方式和模具加工等。
(2)确定浇注系统
流道方式需考虑断面形状、分布形式及热流道、无流道等其他方式。
浇口方式种类繁多,因需求而异,需注意浇口是否有外观要求及流动、平衡、熔接痕、排气等问题,还应注意浇口形式、尺寸是否足以充满整个制品。
(3)确定排气系统
确定排气系统对保证产品品质至关重要,考虑利用多种形式进行排气,注意防止产品真空吸附和模具拉不开。
(4)确定模具成型零件的结构形式及数目、排列方式
由产品的投影面积、形状、外观、精度、加工方式、产量及效益来确定模具成型零件的结构形式及数目、排列方式。
各方面互相协调制约,应多方面考虑以达到最佳组合。
(5)顶出机构设计
顶出机构有多种方式,如顶杆、顶管、推板、二级顶出、油(气)压等,应注意脱模平稳、模具强度、外观、功能、冷却效果。
(6)确定侧凹处理方法,进行侧面成型与抽芯机构的设计
灵活运用斜销、斜滑块、油(气)缸、齿轮齿条、强行脱模及其他方式确定侧凹处理的方法,进行侧面成型与抽芯机构的设计。
(7)冷却装置设计
冷却装置对模具生产影响很大,设计工作较繁杂,既要考虑冷却效果及冷却一致性,又要考虑冷却系统对模具整体结构的影响。
(8)模具工作零件设计
根据模具材料,做强度刚度计算或依据经验数据确定模具各部分厚度及外形尺寸、外形结构及所有连接、定位、导向件的位置。
为提高生产效率,应尽量考虑采用标准模架。
(9)拉料杆形式选择
顶杆、顶管顶出机构一般用Z形拉料杆,推板、推块顶出机构一般采用球形拉料杆。
4.注塑模具的相关计算
(1)型腔型芯工作尺寸的计算。
(2)型腔壁厚、底板厚度的确定。
(3)模具加热、冷却系统的有关计算。
5.绘制模具图
要求按照国家制图标准绘制,但是也可以结合本厂标准和国家未规定的工厂习惯画法。
(1)绘制模具结构总装图
绘制总装图尽量采用1:
1的比例,其画法与一般机械制图画法原则上没有区别,只是为了更清楚地表达模具中成型制品的形状和浇口位置的设置,在模具总装图的俯视图上,可以将定模拿掉,而只画动模部分。
模具总装图应包括以下内容:
●模具成型部分结构。
●浇注系统和排气系统的结构形式。
●分型面及分模取件方式。
●外形结构及所有连接件,定位、导向件的位置。
●标注型腔高度尺寸(不强求,根据需要)及模具总体尺寸。
●辅助工具(取件卸模工具,校正工具等)。
●按顺序将全部零件序号编出,并且填写明细表。
●标注技术要求和使用说明。
(2)绘制全部零件图
由模具总装图拆画零件图的顺序应为:
先内后外,先复杂后简单,先成型零件,后结构零件。
具体要求如下:
●图形要求。
一定要按比例画,允许放大或缩小。
视图选择应合理,投影应正确,布置应得当。
为了使加工专利号易看懂、便于装配,图形应尽可能与总装图一致,图形要清晰。
●标注尺寸要求统一、集中、有序、完整。
标注尺寸的顺序为,先标注主要零件尺寸和出模斜度,再标注配合尺寸,然后标注全部尺寸。
在非主要零件图上应先标注配合尺寸,后标注全部尺寸。
●表面粗糙度。
把应用最多的一种粗糙度标于图纸右上角,如标注“其余3.2”。
其他粗糙度符号在零件各表面分别标出。
●其他内容。
例如零件名称、模具图号、材料牌号、热处理和硬度要求、表面处理、图形比例、自由尺寸的加工精度、技术说明等都要正确填写。
●校对、审图。
6.模具设计的标准化
一套模具由设计到制造完毕周期较长,因此如何设法减少繁重的设计和制造工作量,与缩短生产准备时间和降低造价是有很大关系的。
实践证明,模具的标准化是达到上述目的的有效措施。
标准化包括以下内容。
(1)整体结构标准化
根据工厂塑料生产用设备规格,订出若干种标准典型结构和外形尺寸,在设计模具时,仅绘制部分模具零件图,其余的模具零件图按标准典型结构制造。
这样,就可以预测