CD盒盖的塑料模具设计Word下载.docx
《CD盒盖的塑料模具设计Word下载.docx》由会员分享,可在线阅读,更多相关《CD盒盖的塑料模具设计Word下载.docx(12页珍藏版)》请在冰豆网上搜索。
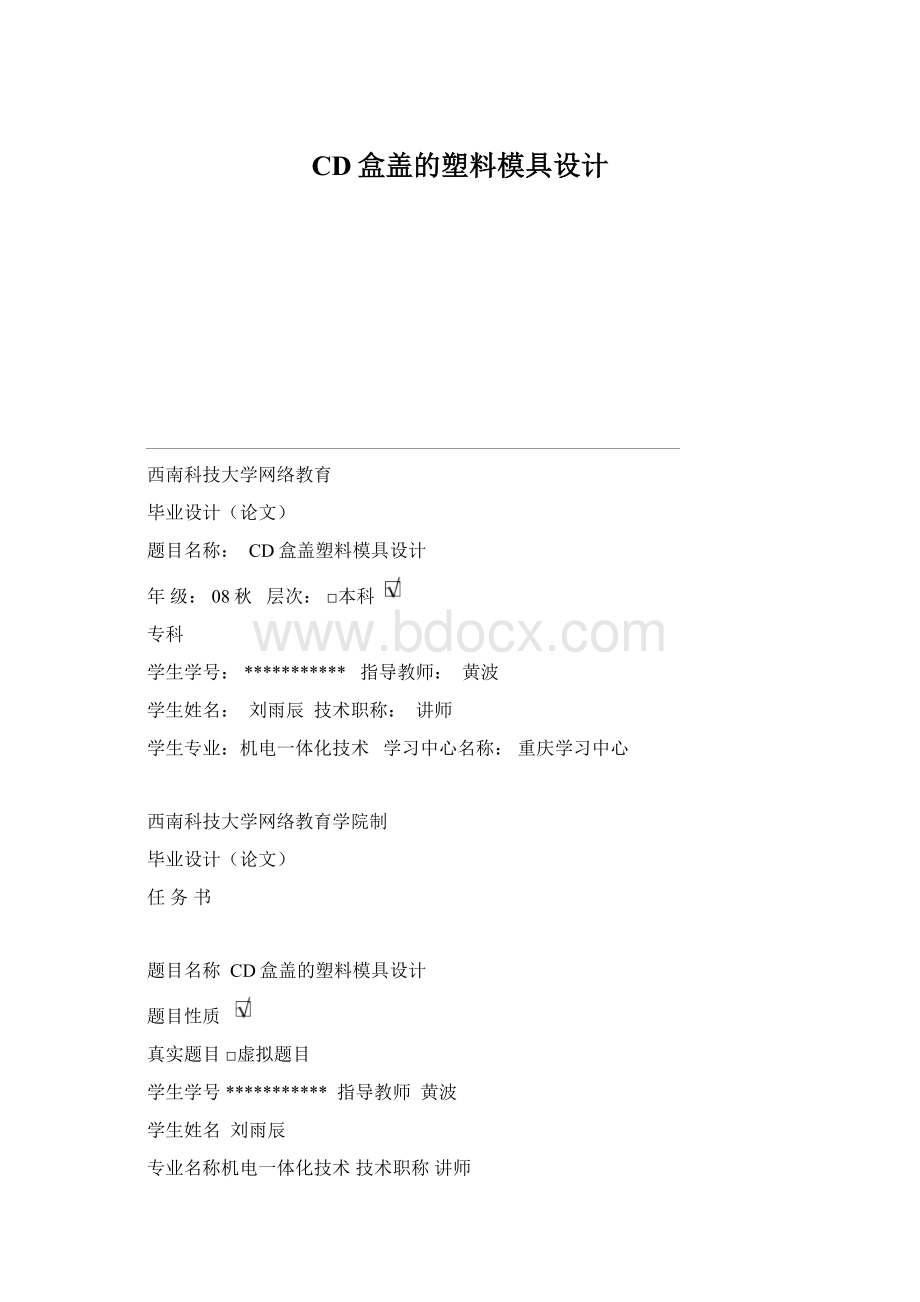
1.本课题是《CD盒盖的塑料模具设计》,根据我国实际国情,为适应注塑模向大型化、自动化发展的要求而设计出的合理,经济,实用的注塑模盒盖。
2.该盒盖的设计是在参考。
吸收国外先进经验结构基础上研发设计出来的。
通过对侧壁双向抽芯机构的合理利用避开了以前CD盒盖模具设计存在的多种不足之处。
保证了生产工作的稳定并大大节省了制造成本。
3.本设计从CD盒盖的性能进行全面的分析,并从实践中得到证明,同时为开发新一代的CD盒盖理清了思路。
毕业设计领导小组负责人:
(签字)
2010年月日
成绩考核表
过程评分
评阅成绩
答辩成绩
总成绩
百分制
等级制
1、指导教师评语
建议成绩指导教师签字:
2010年月日
2、论文评阅教师评语
建议成绩评阅教师签字:
2010年月日
3、毕业答辩专家组评语
建议成绩答辩组长签字:
年月日
4、毕业设计领导小组推优评语
组长签字:
摘要
介绍了CD盒盖目前常用的结构,说明了其存在的问题,提出了设计、改进方案,取得了良好效果。
该CD盒盖的设计是在参考、吸收国外先进经验的基础上研发设计出来的。
通过对零件性能及结构工艺特性的分析,完成了一套侧壁双向抽芯机构注射模具设计。
整套模具方案合理、结构紧凑、工作可靠,保证了CD盒盖使用的方便并大大节省了制造成本。
本次设计使用了当前比较流行的制图软件AutoCAD及Pro/E软件。
此次设计过程中查阅了大量的模具设计资料,通过模具的设计与应用,同原有的设计方案相比,模具的应用提高了产品的质量,模具整体设计的思路和要求符合现代设计潮流和未来的发展方向。
关键词CD盒盖侧壁双向抽芯注射AutoCADPro/E
ABSTRACT
IntroducedthestructureofcurrentlyusedlidCDandtheexistingproblems,andputsforwardthedesignandimprovementscheme,andachievedgoodresults.Thelidofthedesignisontoothpickabsorbingforeignadvancedexperienceandreferenceonthebasisoftheresearchanddesign.Throughtheprocessofpartsandstructureanalysis,completeasetoflateraltwo-waycore-pullingmechanisminjectionmolddesign.Wholemouldschemeisreasonable,compactstructure,reliablework,guaranteesthelidoftheconvenientusetoothpicksandgreatlyreducetheproductioncost.ThisdesignUSESthecurrentpopulardrawingsoftwareAutoCADandPro/E.Thedesignprocessofmoulddesignthelidmold,throughthetoothpick,withthedesignandapplicationoftheoriginaldesign,mouldapplicationscomparedtoimprovethequalityoftheproducts,moulddesignideasandmoderndesignrequirementsandthefuturetrendsofthedevelopmentdirection.
KeywordsCDsidecore-drawingtwo-wayinjectionAutoCADPro/E
引言
模具是制造业的一种基本工艺装备,它的作用是控制和限制材料(固态或液态)的流动,使之形成所需要的形体。
用模具制造零件以其效率高,产品质量好,材料消耗低,生产成本低而广泛应用于制造业中。
模具工业是国民经济的基础工作,是国际上公认的关键工业。
模具生产技术水平的高低是衡量一个国家产品制造水平高低的重要标志,它在很大程度上决定着产品的质量,效益和新产品的开发能力。
振兴和发展我国的模具工业,正日益受到人们的关注。
早在1989年3月中国政府颁布的《关于当前产业政策要点的决定》中,将模具列为机械工业技术改造序列的第一位。
随着CAD/CAM/CAE技术的快速发展及市场对模具集成需求的日益增加,在模具企业推广普及相关的CAD、CAM、CAE知识、提高其生产能力和市场竞争力是我国模具发展的必由之路。
应用Pro/E机械自动化软件建立模具模型为模具制造提供必备的图纸、为后续的CAE、CAM提供基础数据支持,是模具设计制造集成化的前提。
我国的塑料成型模具设计制作技术起步较晚,整体水平还比较低。
目前占30%左右。
当前,国内塑料模具市场以注塑模具需求量最大,其中发展重点为工程塑料模具。
据预测,在未来的模具市场中,塑料模具的发展速度将高于其他模具,在模具行业中的比例将逐步提高。
第一章概述
1.1塑料模具简介
塑料加工工业中和塑料成型机配套,赋予了塑料制品以完整构型和精确尺寸的工具。
由于塑料品种和加工方法繁多,塑料成型机和塑料制品的结构又繁简不一,所以,塑料模具的种类和结构也是多种多样的。
1.2我国塑料模具工业的发展现状
80年代以来,在国家产业政策和与之配套的一系列国家经济政策的支持和引导下我国模具工业发展迅速,年均增长均为13%,1999年我国模具工业产值为245亿,至2002年我国模具工业总产值约为360亿,其中塑料模约为30%左右。
在未来的模具市场中,塑料模在模具总量中的比例还将逐步增高。
我国塑料模具工业从起步至今,经历半个多世纪,有了很长远的发展,模具水平有了很大提高。
在大型模具方面和精确塑料模具方面都有长足的进步,模具的质量、寿命、精确度和工期都得到了有效的提高,但和国外相比仍有较大差距,具体数据见表1.1。
表1.1国内外塑料模具技术比较
项目
国外
国内
注塑模型腔精度
0.005~0.01mm
0.02~0.05mm
型腔表面粗糙度
ra0.01~0.05µ
m
ra0.20µ
非淬火钢模具寿命
10~60万次
10~30万次
淬火钢模具寿命
160~300万次
50~100万次
热流道模具使用率
80%以上
总体不足10%
标准化程度
70~80%
小于30%
中型塑料模生产周期
一个月左右
2~4个月
在模具行业中占有量
30~40%
25~30%
1.3我国塑料模具工业和今后主要发展方向
提高大型、精密、复杂、长寿命模具的设计水平及比例。
这是由于塑料模成型的制品日益大型化、复杂化和高精度要求以及因生产率要求而发展的一模多腔所致。
在塑料模设计制造中全面推广应用cad/cam/cae技术。
推广应用热流道技术、气辅注射成型技术和高压注射成型技术。
开发新的成型工艺和快速经济模具。
以适应多品种、少批量的生产方式。
提高塑料模标准化水平和标准件的使用率。
应用优质材料和先进的表面处理技术对于提高模具寿命和质量显得十分必要。
研究和应用模具的高速测量技术与逆向工程。
采用三坐标测量仪或三坐标扫描仪实现逆向工程是塑料模cad/cam的关键技术之一。
研究和应用多样、调整、廉价的检测设备是实现逆向工程的必要条件。
第二章注塑模的可行性分析
2.1材料选择
根据以上制品的特点及经济方面的考虑,选用使用比较广泛的ABS塑料作为该制品的材料
ABS塑料:
化学名称:
丙烯腈-丁二烯-苯乙烯共聚物。
英文名称:
AcrylonitrileButadieneStyrene。
比重:
1.02克/立方厘米成型收缩率:
0.4-0.7%。
成型温度:
200-240℃。
干燥条件:
80-90℃2小时。
熔点:
130-160℃。
热变形温度:
90-108℃(0.46MPa)83-103℃(0.185MPa)。
抗拉屈服强度:
50MPa。
拉伸弹性模量:
1.8×
MPa。
抗弯强度:
80MPa。
冲击强度:
261(无缺口)11(缺口)。
硬度:
9.7HB。
体积电阻系数:
击穿强度:
15.7-19.7。
2.2确定成型方法
1.定形料,流动性中等,吸湿大,必须干燥,表面要求光泽的塑件须长时间预热干燥80-90度,3小时;
2.宜取高料温,高模温,但料温过高易分解(分解温度为>
270度)对精度较高的塑件,模温宜取50-60度,对高光泽、耐热塑件,模温宜取60-80度;
3.要解决夹水纹,需提高材料的流动性,采取高料温、高模温,或者改变水位等方法;
4.如成形耐热级或阻燃级材料,生产3-7天后模具表面会残存塑料分解物,导致模具表面发亮,需对模具及时进行清理,同时模具表面需增加排气位置。
其成型特点为:
ABS树脂吸水性较大,在加工前应对ABS树脂进行预干燥处理,使其含水量下降至0.1%以下。
ABS的流动性较好,溢边值为0.04mm左右,易于充模。
ABS的最大流动长度与制品的厚度之比为190:
1。
ABS的使用温度为-40~-100℃,260℃时即分解产生有毒的挥发性物质,其热变形温度在载荷为1.82MPa时约为93℃。
当模具温度为40℃时,成型收缩率最小,故模温控制在40℃左右为宜。
料温应低于260℃。
为了获得内应力较小的制品,要求保力不宜过高。
ABS树脂注射压力对于薄壁、长流程、小浇口的制品或耐热、阻燃等品级,要求较高些;
对于厚壁、大浇口的制品则可低些。
模具设计时要注意浇注系统对料流阻力较小,进口处外观不良,易发生熔接痕,应注意选择进料口位置、形式,顶出力过大或机械加工时表面呈现白“色痕”。
2.3制品成型工艺参数
预热和干燥:
80~85℃螺杆转速:
30~60r/min。
料筒温度:
前部200~210℃。
中部210~230℃。
后部180~200℃。
模具温度:
50~70℃,注射压力:
70~90MPa。
保压压力:
50~70MPa,注射时间:
3~5S。
保压时间:
15~30S,冷却时间:
15~30S。
总周期:
40~70S。
其它参数:
相对密度:
1.02~1.06,密度:
1.0~1.1g/cm3。
收缩率:
0.3%~0.6%。
查《塑料成型与模具设计》。
比热容单位热流量导热率注射压力1047J/kg?
℃,0-40104J/kg1055J/m?
h?
℃60-100MPa。
第三章注塑件的三维建模
CD盒盖的零件图如图3.1所示。
图3.1塑件图
根据图3.1提供的基本信息,在Pro/e软件中建立注塑件的三维模型。
先创建一个圆柱形薄壁筒,并倒圆角,在拉伸出侧面凸台,去除凸台处的多余材料,最后在凸台侧面开两个通孔。
第四章塑料模具的结构设计
4.1分型面的选择
该零件近似缸体,但结构不对称,考虑到侧向抽芯结构的抽出。
选择如图4.1所示的水平分型方式,既可降低模具的复杂程度,减少模具的加工难度,又便与成型后注塑件的提取。
图4.1分型面
4.2型腔排列方式的确定
由于该零件体积较小,生产批量较大,从经济性因素考虑,应采用一模多腔结构。
由于零件结构不规则且需要侧向抽芯,从模具结构复杂程度和制造成本方面考虑根据选定的注塑机最大注塑量,确定模具型腔数目为2。
采用如图4所示的两种型腔排列方式。
图4.2型腔排列方式
4.3浇注系统设计及计算
1、主流道和分流道的设计
主流道的尺寸直接影响溶体的流动速度和充模时间,由于主流道与高温塑料溶体及注射机喷嘴反复接触,所以在注射模中主流道部分设计成可拆卸的浇口套,以便与更换,如图4.3所示。
根据参考文献,应用公式D=d+(0.5-1)mm和Rz=R1+(1-2)mm,确定相应的尺寸分别为:
主流道小端直径为3mm,主流道入口的凹坑球面半径为14mm,根据参考文献,选择主流道的半锥角1.5°
。
图4.3主流道衬套
分流道的形状及尺寸,应根据注塑件的体积、壁厚、形状、注射速率、分流道长度等因素来确定。
由于分流道较短,为便于加工,选用截面形状为半圆形分流道,根据参考文献取分流道直径为6mm。
2、浇口设计
根据注塑件的成型要求及型腔排列方式,选择从壁厚为2mm处进料,料由厚处往薄处流,,在模具结构上采用镶拼式型腔、型芯,为便于填充、排气,采用截面为矩形的侧浇口。
根据参考文献[1]由公式A=2
Rh+
R²
+bh+1/2
r²
+b2h2确定塑件外侧表面积为4067.79mm²
;
侧浇口宽度由公式b=
确定,取1.6mm;
侧浇口深度由公式t=(0.6-0.9)
确定为1.8mm。
3、主要成型零件设计
考虑加工的难易程度和材料的价值利用等因素,凹模采用整体嵌入式结构,而型芯主要与凹模相结合,构成模具的型腔,故选用如图4.4所示的型芯形式。
图4.4型芯形式
4.4侧向分型与抽芯机构设计
1、抽拔距和抽拔力的确定
根据参考文献[1],由公式S=S1+(2̅3)mm确定抽拔距,将相关数据代人公式计算后取4mm。
式中,S1为侧向分开至不影响制品脱模的距离;
S为分开拼合凹模所需的抽拔距。
由公式F=Pacos(f-tan
)/(1+fsin
1cos
1),确定抽拔距为7.4
10-4N。
2、斜导柱的设计
斜导柱侧抽芯机构采用侧向分型与抽芯机构,其中斜导柱有一定的安装斜角
取20°
,经过计算斜导柱的直径为9mm、长度为469mm。
3、滑块与导向槽设计
为使模具结构紧凑,降低模具装配复杂程度,采用整体式滑块和导向槽形式,为提高导向精度,装配时可对导向槽或滑块采用配磨等加工工艺。
由于侧抽芯距离较短,导滑长度只要符合滑块在开模时的定位要求即可,滑块的定位采用弹簧圆头销定位。
4、楔紧块的设计
考虑模具结构和侧抽芯的要求,采用一对楔紧块,使其中心对称,要保证楔紧机构的强度。
楔紧块用螺钉固定于动模板上,楔紧块的楔角略大于斜导柱的斜角,以保证在开模过程中楔紧块能限制滑块的后退动作。
由于斜导柱的斜角为20°
所以楔紧块的楔角确定为22°
结论
针对大量生产的牙签盒盖零件,在Pro/E软件环境下进行了注塑件三维CAD模型的建立,完成了CD盒盖注塑成形模具的设计。
为后续相应注塑模具械零件图装配图绘制、注射过程模拟、模具复杂型面的数控加工等提供了必备的基础数据。
模具设计进入21世纪,在经济全球化的新形势下,随着资本、技术和劳动力市场的重新整合,我国装备模具制造业在加入WTO以后,将成为世界注塑模具制造业的基础。
而在现代制造业中,无论哪一行业都越来越多地采用由模具工业提供的产品。
为了适应用户对模具制造的高精度、短交货期、低成本的迫切要求,模具工业正广泛应用现代先进制造技术来加速模具工业的技术进步,满足各行各业对模具这一基础工艺装备的迫切需求。
致谢
在完成本篇毕业论文的过程中,本人得到了指导老师的帮助,是他为此付出了心血和精力,在此请允许我向他表示最衷心的感谢!
我要感谢我的导师。
当然,这些都离不开父母和老师们平时的谆谆教诲和的尽心辅导。
本篇论文从提纲到初稿乃至成稿,都经过他们精心的指导和修改,提出了严格的要求和许多宝贵的意见。
可以说,我的整篇论文凝聚着他们的心血。
其次,我要感谢教学中心的老师。
是他们对论文选题、选材、编写格式等方面给予了细心的指导,使本人的毕业论文设计得以有条不紊地进行。
最后,我要感谢所有参考文献的作者。
我论文是建立在他们研究基础上的。
参考文献
1.文朴、李田.《机械设计》,北京.机械工业出版社,2001
2.机械设计手册.编写组《机械设计手册》,北京.化学工业出版社,2006
3.王爱玲.《现代数控编程技术及应用》,国防工业出版社,2002
4.濮良贵.《机械设计》,西安西北工业大学出版社,1996
5.林栋梁.《英汉机电工程词典》,机械工业出版社,1997
6.王卫兵.《CimatronE6.0数控编程实用教程》,清华大学出版社,2005
7.黄俊明等.《unigraghicsII模型设计高级篇》.北京:
中铁道出版社,2001
8.王华山.《塑料注塑技术与实例》[M].北京:
化学工业出版社,2006