第六章化工新技术综合Word文档格式.docx
《第六章化工新技术综合Word文档格式.docx》由会员分享,可在线阅读,更多相关《第六章化工新技术综合Word文档格式.docx(13页珍藏版)》请在冰豆网上搜索。
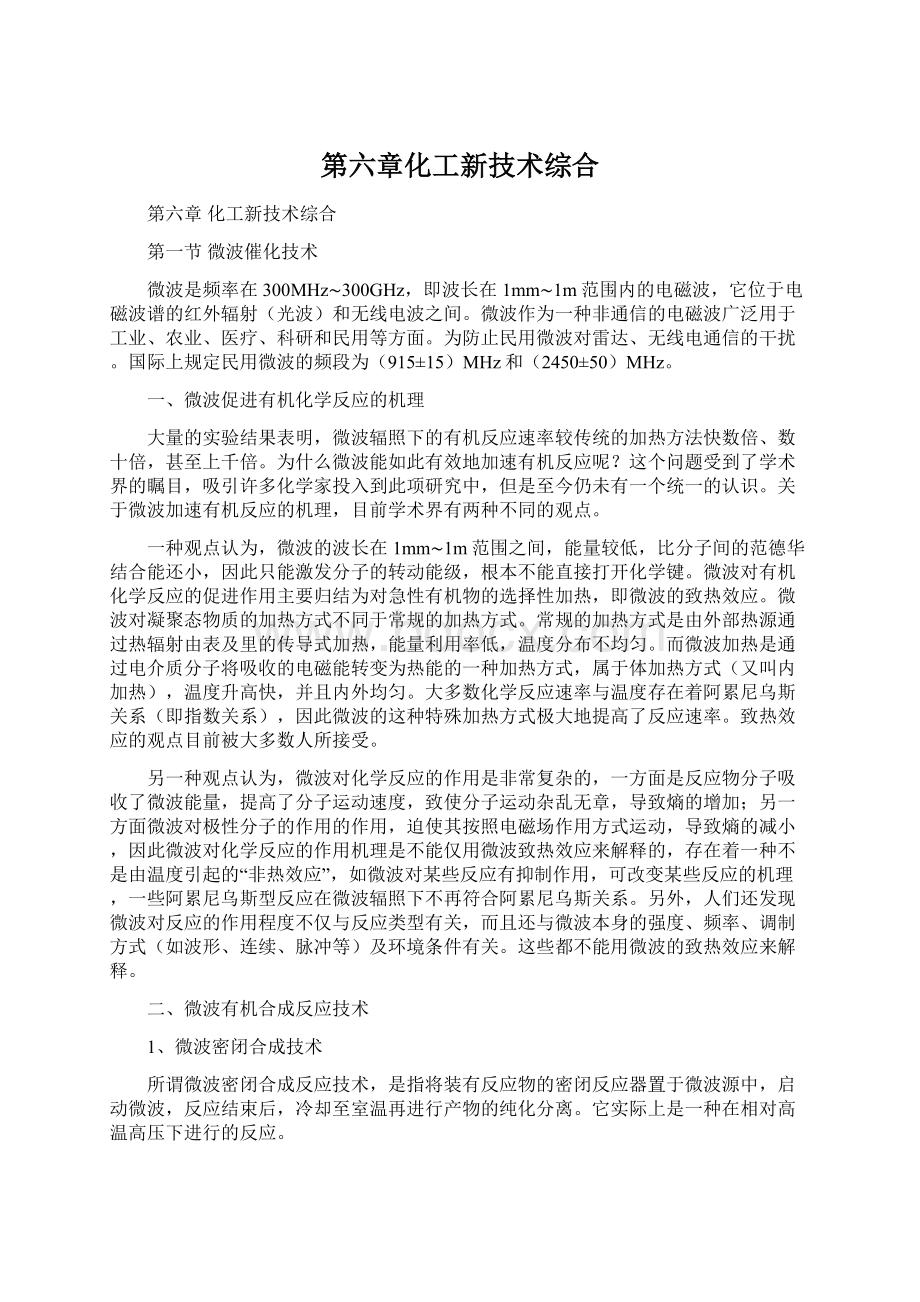
另一方面微波对极性分子的作用的作用,迫使其按照电磁场作用方式运动,导致熵的减小,因此微波对化学反应的作用机理是不能仅用微波致热效应来解释的,存在着一种不是由温度引起的“非热效应”,如微波对某些反应有抑制作用,可改变某些反应的机理,一些阿累尼乌斯型反应在微波辐照下不再符合阿累尼乌斯关系。
另外,人们还发现微波对反应的作用程度不仅与反应类型有关,而且还与微波本身的强度、频率、调制方式(如波形、连续、脉冲等)及环境条件有关。
这些都不能用微波的致热效应来解释。
二、微波有机合成反应技术
1、微波密闭合成技术
所谓微波密闭合成反应技术,是指将装有反应物的密闭反应器置于微波源中,启动微波,反应结束后,冷却至室温再进行产物的纯化分离。
它实际上是一种在相对高温高压下进行的反应。
该方法的特点是能使反应体系瞬间获得高温高压,因而反应速率大大提高。
但这一技术的安全性较差,且不易控制。
因而该技术对于挥发性不大的反应体系,可采用密闭合成反应技术。
该技术已成功用于甲苯氧化、苯甲酸甲酯化等。
见图1。
2、微波常压合成技术
为了使微波常压有机合成反应在安全可靠和操作方便的条件下进行,人们对微波炉进行料改造,使加液、搅拌和冷凝过程在微波炉腔外进行。
微波常压反应装置如图所示。
微波常压合成技术的出现,大大推动了微波合成技术的发展。
与密闭技术相比,常压技术采用的装置简单、方便、安全,适用于大多数微波有机合成反应,操作与常规方法基本一致。
3、微波干法合成技术
在微波常压技术发展的同时,英国科学家Villemin等发明了微波干法合成技术。
微波干法合成装置如图2所示。
反应器置于微波炉中心,聚四氟乙烯管从反应器的底部伸出微波炉外与一氮气源连接。
当在微波辐射下反应时,氮气流吹进反应器底部起到搅拌作用;
当微波辐射停止时,聚四氟乙烯管与真空泵相连接,将反应生成的液体产物吸走。
用该装置合成了常规方法难以合成的多肽。
图1微波有机合成常压反应装置
图2微波干法合成装置
4、微波连续合成技术
既然微波辐射能大大提高反应速率,将反应速率从几个小时缩短到几分钟,那么当控制反应液体的流量以一定的流速通过微波辐射源,完成反应后送到接收器,使反应连续不断地进行,效率将大大地提高。
其装置如图3所示。
在微波辐照有机合成设计中,除选用适当的反应器外,还需选用适当的反应介质。
为了使体系能很好地吸收微波能量,一般选用极性溶剂作为反应介质。
溶于水的有机化合物一般应以水为溶剂,这样可使成本和污染大大降低。
对于不溶于水的有机物,可采用低沸点的醇、酮、酯作溶剂。
三、微波合成的优点及其发展趋势
微波有机合成的优点:
1)反应速率较传统的合成方法快数倍,甚至上千倍。
2)对有些反应的选择性较好,产率较高,产品容易提纯。
3)特别适合无溶剂合成,因而有利于解决有机合成中因使用溶剂而造成的环境污染等问题。
4)微波有机合成操作简单。
微波有机合成还处于实验室阶段。
第二节耦合反应技术
所谓的偶合反应主要是指在同一个设备内进行两个可以单独进行的反应,以快反应促进慢反应,或者一个反应的中间产物,作为另一个反应的原料。
为便于理解,以对叔丁基甲苯和丙醛的共氧化反应生产对叔丁基苯甲醛和丙酸为例,总结偶合反应的优点。
1、反应机理
丙醛氧化生成丙酸的反应
C2H5CHO+O2===C2H5COOOH
C2H5COOOH===C2H5COOH+O•
2O•===O2
对叔丁基甲苯氧化生成对叔丁基苯甲醛的反应
R-CH3+1/2O2===R-CHO
R-CHO+1/2O2===R-COOH
2、各自的反应特点
丙醛氧化非常容易,空气中的氧在50℃左右即可将其快速氧化,也就是说丙醛的氧化对氧化剂的氧化能力要求不高。
而氧化过程的中间产物过氧丙酸不稳定,分解后生成的初生态的氧具有较强的氧化能力,不仅可以氧化丙醛,还可以氧化丙酸成醋酸和二氧化碳。
因而丙醛单独氧化时容易出现过氧化,如果能降低过氧丙酸的量,则可有效提高丙酸的收率。
对叔丁基甲苯的甲基与叔丁基相比更容易氧化,即使如此,对叔丁基甲苯的氧化也较为困难。
如以空气为氧化剂,则需要高温。
而在高温下,芳烃更容易脱氢生成稠环芳烃,进而降低产品的收率。
通常情况下氧气氧化对叔丁基甲苯生成对叔丁基苯甲醛的反应收率低于40%.
3、共氧化的优点
1)反应体系中对叔丁基甲苯过量,过氧丙酸分解产生的初生态的氧主要用于氧化对叔丁基甲苯,而不是氧化丙酸,从而提高了丙酸的收率。
2)初生态的氧的氧化能力强,在较低温度下即可有效地氧化对叔丁基甲苯,从而减少了芳烃在高温条件下发生的一系列副反应。
第三节隔壁塔精馏
精馏是技术最为成熟、应用最为广泛的分离单元操作,同时也是在过程工业中能耗高、投资高的设备,在炼油、石化等行业中,其能耗占全过程的比例甚至高达70%,设备投资超过50%。
因此,蒸馏过程节能技术的研究具有极其重要的意义。
一、热耦合蒸馏塔
对于具有N组分的混合物,采用传统的分离序列需要N-1个分馏塔才能得到所有组分的产品,组分需经过多次蒸发冷凝,从能耗上讲并不经济。
20世纪40年代提出的热耦合蒸馏技术,近年来得到迅速发展,因其在节能的同时降低了设备投资。
最简单的三组分热耦合蒸馏的流程如图1所示。
1、侧线精馏SR(SideRectifier)
三组分原料A、B、C进入主塔进行蒸馏,塔顶和塔底分别得到轻组分产品A和重组分产品C,在主塔的下部,不含轻组分处(轻组分浓度极低)侧线采出气相进行精馏,进一步脱除重组分C,从而得到中间产品B。
低温精馏空气分离过程中氩气的分离就是采用此原理,原理图如图1所示。
图1侧线精馏塔示意图
2、侧线提馏SS(SideStripper)
其原理与SR相似,主塔的塔顶和塔底分别得到轻、重组分产品A和B,从主塔上部不含重组分处采出液相进行提馏,脱除其中的轻组分A,得到中间产品B。
原理图如图2所示。
图2侧线提馏塔示意图
3、完全热耦合蒸馏FC(FullyThermallyCoupledDistillationColumn)
最早由Petlyuk提出,因此又称为Petlyuk蒸馏。
进料在预分馏塔中进行初步分离,轻、重组分得到彻底分离,中间组分分布于整个预分馏塔中,无重组分的塔顶气相与无轻组分的塔底液相分别进入主塔进一步蒸馏,中间组分B在主塔中间富集提纯,轻、重组分A和B分别在塔顶、塔底得到分离,从而实现三个产品的完全分离。
热耦合蒸馏与传统的精馏序列分离相比,原本需要的四个换热设备减少为2~3个,从而达到节能的目的。
SR与SS的设计及控制相对简单,已经获得广泛应用,FC没有成熟的设计方法,在控制上比较复杂,相当长时间内未能得到工业应用。
近年来随着人们对精馏技术及其控制技术的进一步研究,根据完全热耦合蒸馏原理开发的隔板塔已经获得成功应用。
其工作原理图如图3所示
图3预精馏塔示意图
二、隔板蒸馏塔
隔板蒸馏塔DWC(DividingWallColumn)的原理与完全热耦合蒸馏FC的分离原理一样(其原理如图2所示),只是利用隔板把塔的中部分成两部分,进料侧相当于FC中的预分馏塔,另一侧以及塔未分隔的上下部合起来相当于FC中的主塔。
隔板塔巧妙地使单塔实现了多塔功能。
从理论上讲,N个隔板可以把一个单塔分隔成N+1个塔,实现N+1组分的分离,而总共只需要一对冷凝器与再沸器。
其工作原理图如图4所示。
图4隔板馏塔示意图
与传统的精馏序列相比,能耗与设备投资都能降低30%左右,一些特殊的物系,节能幅度甚至达到50%~60%。
此外,结构紧凑还带来占地面积小、管线短等相关的优势。
目前广泛应用的商用过程模拟软件都可以用来精确计算隔板蒸馏塔,比如ASPENPLUS和HYSYS等,前者有现成的隔板蒸馏塔模块,HYSYS则需要用两个塔并联来实现。
无论采用哪种方法来模拟计算,其自由度都有五个:
冷凝器、再沸器、三个产品。
典型的设计指定(DesignSpecification)为三个产品的浓度(或产量)、隔板塔上部液体进入隔板两侧的比例以及隔板下部气体进入隔板两侧的比例。
隔板蒸馏塔的模拟计算并不是十分困难,但是其优化却相对困难得多,只有隔板两侧流体的比例分配得合理才能够真正达到节能的目的。
除了设计和优化外,更大的难点在于对隔板蒸馏塔的控制,因此研究隔板蒸馏塔的动态特性才能确定其控制方案:
参数、控制点及方法,并进一步优化塔的设计,调整其理论板数在不同部位的合理分布及余量。
对于许多物系,与传统蒸馏塔一样,温度灵敏板仍然是一个很好的控制选择。
隔板蒸馏塔的传质单元可以采用塔板,也可以采用填料。
由于隔板部位的截面不再是对称的圆形,因此必须采用专门设计的塔板。
填料只要恰当处理好壁流即可。
填料隔板塔的结构如图3所示。
隔板下部气体按照设计的比例,通过计算两侧
填料阻力,调整两侧的截面积之比来实现;
隔板上部液体的分配通过液体再分布器实现,并设置液体分流器来调控隔板两侧的气液比。
隔板蒸馏塔并非适合所有物系的分离,以下两种情况下隔板塔具有明显的优势
1)中间产品浓度要求高的物系
如果从隔板蒸馏塔侧线采出的中间产品的纯度要高于侧线塔分离得到的中间产品的浓度,则应优先选用隔板塔。
即使中间产品浓度要求不高,在对能耗和投资有限制的情况下,隔板蒸馏塔仍然有优势。
2)进料组成中中间组分含量高,轻、重组分含量相当的物系。
进料中的中间组分浓度达到2/3左右,则是非常理想的物系,当然相对挥发度也会影响隔板塔的分离难度,轻组分/中间组分与中间组分/重组分的相对挥发度差异比较大,则隔板蒸馏塔就没有显著的优势。
虽然隔板蒸馏塔早在1949年Wright就申请了美国专利,但直到近年来才得到实际应用。
蒸馏技术专业公司Montz公司为BASF等公司提供了60多座隔板蒸馏塔,KBR,Uhde、UOP、Linde等公司也都采用了此项技术,其中Linde公司建造的最大规模的隔板塔直径5m、塔高107m。
国内天津大学化学工程研究所蒸馏与填料研究室也已成功地把此项技术应用于工业生产。
三、在二甲醚生产中的应用
空气低温分离过程是一个比较特殊的过程,其原料为空气,没有成本,整个过程的经济性主要决定于设备投资及能耗。
该过程的核心设备就是个三~四个互相耦合在一起的蒸馏塔。
因此,如果具有节能、投资低的优点的隔板蒸馏塔如果能够用于空气分离,则可以提高空气分离的经济性。
空气三个产品组成是轻组分氮气、中间组分氩气和重组分氧气。
中间产品氩的纯度要求最高,利于把隔板蒸馏塔用于氮—氩—氧的分离,但是氩的含量最低、与氮易分离而与氧难分离等因素则不利于隔板蒸馏塔的应用。
模拟计算表明,把现有流程中的上塔简单地替换为隔板塔,并不能得到侧线纯氩产品,氩—氧相对挥发度太低是一个方面的原因,隔板塔内的气液比也不能满足分离要求。
那么具有节能、投资低的隔板蒸馏塔是否就不能应用于要求节能、投资低的空分设备中呢?
笔者认为,上塔采用隔板蒸馏塔技术后,不改变整个流程,取消粗氩塔,直接得到纯氩当然是不可能的。
但是通过改变流程,调整换热循环,优化塔内气液比,得到质量更好的氩馏分还是可能的。
氩馏分中氩的浓度有所提高,氮浓度降
图5侧线精馏
至极限,不仅杜绝氮塞的发生,还可以省去精氩塔。
另外,在应用隔板蒸馏塔的时候不能简单地生搬硬套,尤其是在气液比难以调整到位时,有时需要做较大的调整,隔板塔还可以衍生出不同的流程,两个衍生隔板塔的原理如图4所示。
为了更清楚地说明其变化,把隔板塔拆成了两个塔,但是原理是一样的。
总之,随着隔板蒸馏塔技术的日益成熟,其应用会越来越广泛。
第四节热泵技术
世界各国的能源消耗中,以热能消耗量为最大。
在一次能源变成热能再转换成各种形式能量的过程中,约有58.5%的能量是以排气、蒸汽、热水(低温)等排热形式而损失的。
而这些排热损失中,低于100℃的热能占很大比重。
热泵技术的开发为利用低温热能提供了有力的手段,满足了节约能源和保护生态环境的要求。
它是一种在外界能量的协助下,把热能从低温物体转移到高温物体的设备。
热泵的分类有多种,按原理来分有:
压缩式热泵、吸收式热泵、化学热泵、吸附式热泵。
热泵技术的发展经历了一个多世纪。
1824年卡诺首先提出热力学循环理论之后,1852年开尔文具体提出了热泵的设计思想,当时由于条件所限并没有立即得以实现。
直到1917年德国卡赛伊索达制造厂首次把热泵应用于工业生产上。
在30年代,从热泵本身来说由于设备的一次投资比采暖系统的一次投资要高,以及因冬季温度低而使蒸发器表面容易结霜,要用电阻丝加热除霜,这无疑阻碍了热泵在西欧国家的应用。
另外当时的发电厂效率低,电能成本高,压缩机和换热器的
制造技术也不精良,且燃料的价格相对便宜,因此用热泵技术来采暖在经济上并不合算。
到了20世纪50年代,科学技术进步很快,电能成本降低,而燃料价格不断上涨,又由于精密工业和公共建筑大量要求进行空气调节。
于是国外又积极开展
热泵研究工作,并有了较大的发展,这段时间主要发展的是蒸气压缩式热泵,目前已在空调方面获得广泛应用,产品已成系列化。
70年代以来,欧洲各国和苏(前苏联)、日、美、澳等国对热泵研究工作十分重视,各工业国均投入了大量的资金致力于更经济、输出温度更高、工业更为先进的新型热泵的开发。
美国研究热泵的两个权威机构是电力中央研究所(EPRI)和煤气研究所(GRI)。
电力中央研究所开发的方向是供产业用的新型热泵,探讨供蒸馏过程和180℃以上的高温加热过程的应用;
而煤气研究所的主要研究方向是:
采用太阳能为辅助热源的燃气式热泵,以提高商业大楼的采暖和制冷,具体项目有:
太阳能/气体连接的吸收式热泵;
日本通产省工业技术院开发的超级热泵能量收集系统,其目的主要是提高热泵的性能系数,使供热温度达到100~200℃,扩大热泵适用范围。
此外,原联邦德国也投入大量资金开发新型热泵技术。
在此期间,吸收式热泵、吸附式热泵、化学式热泵均得到了较大的发展,在欧洲、日本和美国,已进入了商品化生产阶段,但实际应用的数目还很少。
我国热泵技术发展较为落后。
20世纪50年代,我国对热泵的研究尚处于起步阶段。
那时虽然有一些科研机构(如天津大学)开始了热泵的研究,但一直发展缓慢。
到了20世纪80年代初,随着经济发展和人们生活水平的提高,能源问题变
得突出,为了节约能源和有效利用能源,国内部分高校、研究所掀起了对热泵研究的热潮。
1989年中国科学院广州能源研究所举行的“热泵在我国的应用发展专家研讨会”肯定了热泵在我国应用发展的可能性和重要性,从而进一步将热泵研究推向高潮。
但研究的种类多限于压缩式热泵,而且只有有限的几种应用形式——干燥去湿热泵、蒸发蒸馏热泵、热水型热泵。
近年来,以热源为动力的吸收式热泵、化学热泵、吸附式热泵才有了一定的发展。
一些科研院所已经开始着眼于新型热泵技术的研究,如太阳能热泵的研究、地源热泵、吸收压缩复合式热泵等。
一、热泵技术的发展动态
1、压缩式热泵
压缩式热泵按驱动源来分,可分为电动型和动力型两种。
电动型蒸气压缩式热泵是依靠马达(电动机)驱动的;
而动力型蒸气压缩式热泵是直接由柴油机、煤气机驱动的。
它由电动型热泵发展而成。
动力型热泵的性能系数比电动型的大,
同时还具有能量较大、调节简单、部分负荷性能良好等优点。
目前,国内外研究开发工业上用的高温蒸气压缩式热泵重点放在选择和改进现有的制冷机和制冷剂上,对于制热量较小的热泵系统通常选用往复式压缩机,以及在一定工作压力下提高换热器的换热性能。
此外,还研制用气体来润滑的压缩机组,选择性能良好的制冷剂等。
图6压缩致冷
2、吸收式热泵
吸收式热泵是单纯以热能为补偿热能,在吸收式制冷循环基础上发展起来的。
常用的制冷剂是溴化锂水溶液。
它又分为两种类型:
Ⅰ型吸收式热泵—它是借消耗一部分高温热量将低温热量的温度提高到可以利用的中温程度的一种热泵,其性能系数大于1;
Ⅱ型吸收式热泵不需要消耗高温热能就能使低温热量的温度提高,性能系数小于1。
图7吸收制冷
3、化学热泵
化学热泵是利用物质化学反应时产生的吸热和放热来组成热力循环的一种热泵,它可用于加热、制冷及提高能量的品位,具有其它类型热泵所没有的优点,即当化学反应停止时,它具有蓄能的功能。
在80年代初,化学式热泵还处于实验阶段,近年来发展很快。
能把废热提高到165℃的化学热泵已在美国、日本、俄罗斯和一些欧洲国家商品化,美国火箭研究所工业化学热泵公司研制成了44kW的硫酸水溶液化学热泵,而瑞典则研制了称之为“TEPIDUS”硫化钠水溶液化学热泵。
国内近年来尽管已开展了对化学热泵的研究,但由于已开发工质的化学性能不很稳定,且腐蚀性较强,对热泵系统材料要求较高,增加了热泵的投资费用,故至今实例化例子不多。
图8化学热泵
4、吸附式热泵
吸附式热泵的原理与吸附式制冷循环相同。
其工质由具有良好的吸附、解吸性能的固体微孔吸附剂和作为制冷剂的吸附介质组成,利用吸附和解吸的温度不同来组成热力循环,吸附介质在被吸附剂吸附时放出热量,解吸时则吸收热量。
其热源可直接利用矿物燃料,也可利用太阳能等。
国内外对吸附式热泵的研究较多,其发展和生产已有60多年。
固体吸附式热泵噪声小、维护方便、寿命长,几乎不受地点限制,广泛用于工厂、农村、牧场、渔场、山区和民用设施的空调系统,对电力不足的地区尤为适用,固体吸附式制冷系统的非氯氟工质选择余地大,因此,这一技术成为近年来各国竞相研究开发的热点课题。
由于节能的需要,吸附式热泵得到了迅速发展,在欧洲、日本和美国已进入了商品化生产阶段。
美国沸石动力公司近几年正致力于高效能的吸附式制冷机和热泵的研究。
经济分析表明,吸附式制冷机和热泵的运行费用比电动压缩式热泵低得多,且前者的制造成本与后者不相上下。
二、热泵技术的应用
1、精馏
2、回收低品位热能