红酸果案例讨论分析A1.docx
《红酸果案例讨论分析A1.docx》由会员分享,可在线阅读,更多相关《红酸果案例讨论分析A1.docx(10页珍藏版)》请在冰豆网上搜索。
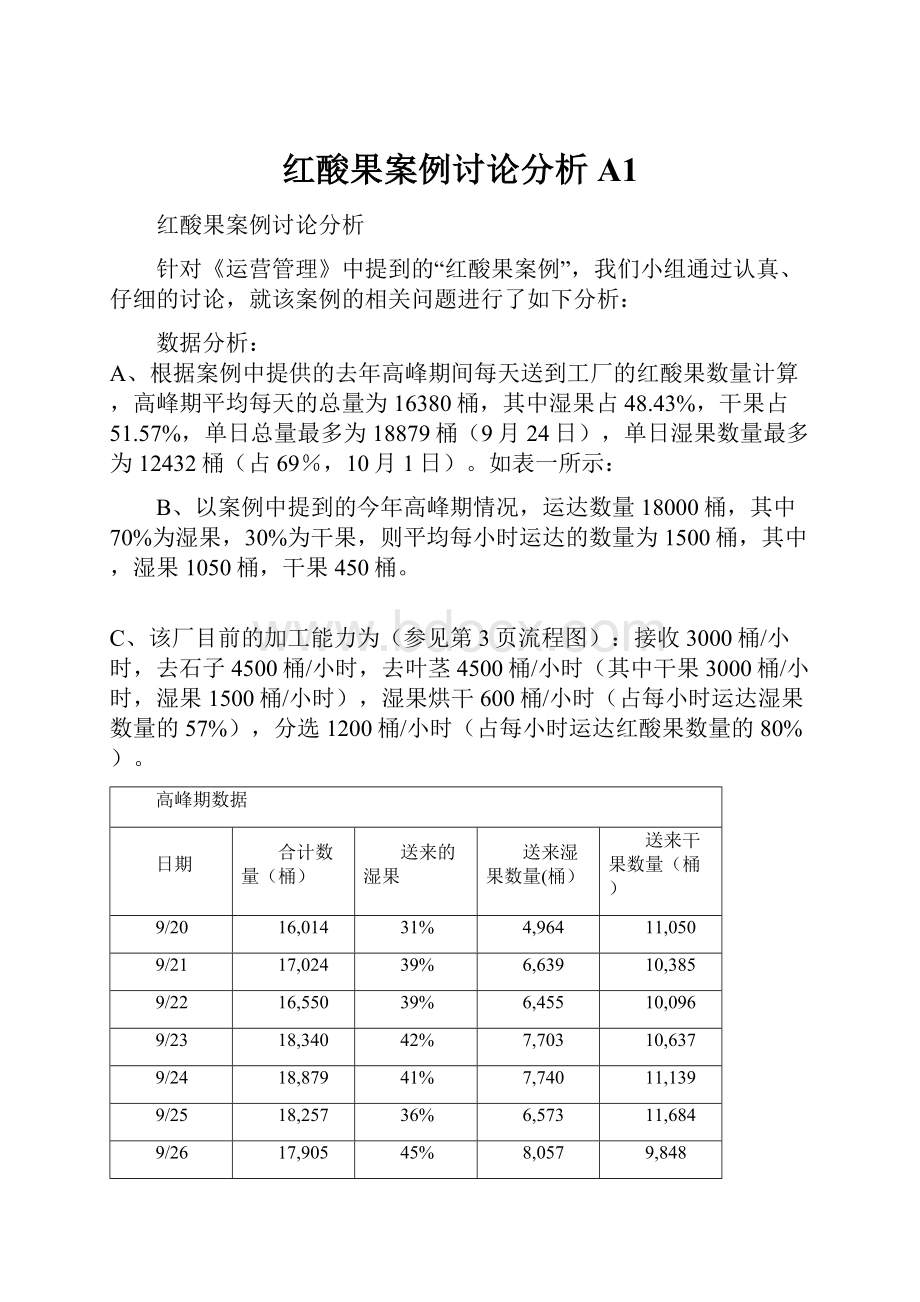
红酸果案例讨论分析A1
红酸果案例讨论分析
针对《运营管理》中提到的“红酸果案例”,我们小组通过认真、仔细的讨论,就该案例的相关问题进行了如下分析:
数据分析:
A、根据案例中提供的去年高峰期间每天送到工厂的红酸果数量计算,高峰期平均每天的总量为16380桶,其中湿果占48.43%,干果占51.57%,单日总量最多为18879桶(9月24日),单日湿果数量最多为12432桶(占69%,10月1日)。
如表一所示:
B、以案例中提到的今年高峰期情况,运达数量18000桶,其中70%为湿果,30%为干果,则平均每小时运达的数量为1500桶,其中,湿果1050桶,干果450桶。
C、该厂目前的加工能力为(参见第3页流程图):
接收3000桶/小时,去石子4500桶/小时,去叶茎4500桶/小时(其中干果3000桶/小时,湿果1500桶/小时),湿果烘干600桶/小时(占每小时运达湿果数量的57%),分选1200桶/小时(占每小时运达红酸果数量的80%)。
高峰期数据
日期
合计数量(桶)
送来的湿果
送来湿果数量(桶)
送来干果数量(桶)
9/20
16,014
31%
4,964
11,050
9/21
17,024
39%
6,639
10,385
9/22
16,550
39%
6,455
10,096
9/23
18,340
42%
7,703
10,637
9/24
18,879
41%
7,740
11,139
9/25
18,257
36%
6,573
11,684
9/26
17,905
45%
8,057
9,848
9/27
16,281
42%
6,838
9,443
9/28
13,343
38%
5,070
8,273
9/29
18,717
43%
8,048
10,669
9/30
18,063
59%
10,657
7,406
10/1
18,018
69%
12,432
5,586
10/2
15,195
60%
9,117
6,078
10/3
15,816
60%
9,490
6,326
10/4
16,536
57%
9,426
7,110
10/5
17,304
55%
9,517
7,787
10/6
14,793
46%
6,805
7,988
10/7
13,862
61%
8,456
5,406
10/8
11,786
56%
6,600
5,186
10/9
14,913
54%
8,053
6,860
平均每天送来的数量
16,380
48.65%
7,969
8,411
表一:
去年高峰期数据
问题1、绘制红酸果处理的流程图:
卡车卸货3000桶/小时
湿果干果
储存箱储存箱
干果
湿果去除石子
4500桶/小时
4500桶/小时去除茎叶
湿果干果
烘干600桶/小时分选1200桶/小时
散装与袋装
问题2、在高峰期此过程的瓶颈是什么工序?
从上述流程图上不难发现,工厂大部分配置的生产能力高于实际工作的需求,但是存在两个环节严重延缓了工序的进展:
一是湿果烘干每小时仅600桶,根据表一数据显示,去年高峰期内,平均每天运达的湿果数量为:
7969桶,每天必须工作13.3小时才能完成全部工作;二是分选每小时1200桶,根据表一数据显示,去年高峰期内,平均每天运达的红酸果总数量为:
16380桶,每天必须工作13.7小时才能完成全部工作。
这两个环节完成的时间均超过其他工序每天正常完成的时间,因此,我们认为案例中加工过程存在的瓶颈工序是:
烘干和分选。
问题3、计算卡车的平均等待时间是多少?
表二去年红酸果平均送达数据
阶段
合计数量(桶)
送来的湿果
送来湿果数量(桶)
送来干果数量(桶)
高峰期9.20-10.9
16,380
48.65%
7,969
8,411
非高峰期9.1-9.19
2,209
54.00%
1,193
1,016
非高峰期10.10-12.10
3,845
75.00%
2,884
961
根据案例中给出的信息,去年高峰期时,工厂各环节的处理数据如下:
A由于卡车早上7点开始运达,除接收工序以外的工人中午11点开始上班,因此在除接收工序以外的工人上班以前的4个小时内,一共运达的红酸果数量为:
16380/12*4=5460桶,其中湿果数量为:
5460*48.56%=2651桶.工厂的接收储存能力为:
总数量7200桶,其中湿果的最大接收储存能力为:
3200桶.因此,该阶段,卡车不存在等候情况.
B去年高峰期,除接收工序以外的工人开始上班后,生产的瓶颈在于烘干和分选,其中分选完成全天工作的时间长于烘干工序,是现有状态下最大的瓶颈,因此,以分选工序的处理能力进行卡车等候时间的分析,从中午11点到下午7点之间,接收环节每小时新增储存的红酸果数量为:
16380/12-1200=165桶.一共165*8=1320桶.连同中午11点以前,接收环节储存的红酸果5460桶,一共为6780桶,小于接收环节的最大储存能力7200桶,因此,在此阶段,卡车也不存在等候现象.同样,以烘干环节处理能力进行分析,从中午11点到下午7点之间,接收环节每小时新增储存的湿果数量为:
7969/12-600=64桶,一共64*8=512桶,连同中午11点以前,接收环节储存的湿果2651桶,一共为3163桶,小于接收环节湿果的最大储存能力3200桶,卡车也不存在等候现象.
C工厂卡瓦基型倾倒机的处理能力为3000桶/小时,远大于高峰期每小时运达的红酸果数量16380/12=1365桶.
综上,去年高峰期,卡车并不存在排队等待现象.
问题4、处理过程中的安排是符有问题?
在去年高峰期时段,烘干工序每天需要13.3小时才能完成工作,分选工序每天需要13.7小时才能完成工作,这主要是由于这两个工序中,设备能力的限制造成的.
在去年非高峰期间,如表二所示:
9月1日—9月19日,平均每天运来2209桶,其中湿果1193桶.平均每小时接收红酸果184桶,其中湿果100桶。
每小时接收湿果远远小于它的贮存能力,这种情况下,生产的最小加工能力工序是烘干工序,600桶/小时,全天工作量2小时可以完工。
这样具备缩短工人加工时间的条件。
在非高期间,10月10日—12月10日,平均每天运来3845桶,其中湿果2884桶,平均每小时接收红酸果321桶,其中湿果241桶。
这种情况下,生产的最小加工能力工序是烘干工序600桶/小时,全天工作量4.1小时可以完工。
同样具备缩短工人加工时间的条件。
因此,在非高期间,除接收工序以外,其他工序的工作时间可以调整为下午3:
00上班,下午8:
00前下班。
这样可以降低工厂的人员费用,同时满足该阶段的生产要求。
问题5、假设卡车等待的成本是10美元/小时,计算高峰期(按18000桶,70%湿果计)的总成本是多少?
(假设卡车是均匀到达)
假设高峰期按18000桶,70%湿果计算,平均每小时送来的红酸果量为1500桶,其中湿果数量为1050桶,烘干工序每小时处理600桶,处理完当天的湿果需要时间为21小时,分选工序处理完全部红酸果的时间为15小时。
因此,在整个生产过程中,烘干工序成为“瓶颈”,该工序的产能将会导致卡车长时间等待。
A接收环节湿果的最大储存能力为3200桶,湿果运来的速度为1050桶/小时,早上7点至中午11点,由于只有接收环节工人上班,所以湿果的积压速度为1050桶/小时,也就是说从上午的10点3分开始(3200/1050=3.05小时,3.05+7=10.05小时),接收环节的储存箱已经装满,开始造成卡车等待。
B中午11点以后,其他工序工人开始上班,湿果的积压速度为1050-600=450桶/小时。
C截止到19点,不再有新的卡车运达时,湿果的积压数量达到全天的最大值7800桶(1050*4+450*8=7800)
D从19点开始,要将剩余在卡车上的湿果4600桶(7800-3200=4600)烘干完毕需要4600/600=7.67小时。
湿果库存量(桶)
7800
7000
4200
4000
3200
3000
1500
7:
0010:
0011:
00
19:
00
2:
00
表三湿果库存数量表
E从卡车开始等待的时间上午10点3分,到下午19点之间
湿果卡车到达率
车/小时
烘干设备可处理率
车/小时
(说明该生产线已经不是一个稳定的服务系统。
)
为计算卡车的平均等待时间,需要将案例转变成一个稳定的服务系统,通过分析,我们认为:
因为从早上7点,一直到所有卡车上的湿果全部卸掉(即凌晨2:
40分)这段时间内,系统是稳定的(能够将除储存箱内3200桶以外的湿果全部加工完毕),因此,设想卡车是在这段时间内均匀到达的,那么
车/小时
烘干设备可处理率
车/小时
卡车的平均等待时间为:
小时
这个时间段里,一共新到达运输湿果的卡车数量为:
(12600-3200)/75=125辆,该时间段内,卡车的等待时间是:
61小时
结论是:
按等待的成本是10美元/小时计算,总成本为610美元。
问题6、对奥布理恩的建议你怎么看?
奥布里恩提出的方案,增加烘干机,减低了烘干机对整个生产过程的阻碍作用,有助于问题的解决。
假如增加两个烘干机,可以使每小时的生产能力提高到1000桶,占每小时运达湿果数量的95%,即用12.6小时就可以完成一天中所有湿果的加工,基本可以满足生产的需求。
而耗资240000元改造干果贮存箱,表面上看似乎可以解决卡车长时间等候的问题,但实际上,增加2台烘干机,(再增加1台分选机)可以将整个生产线的瓶颈解决,从而大大减少了卡车的等待时间。
而且在解决了生产线的瓶颈问题以后,通过调整工人的工作时间,一样可以让卡车不用等待,从而不需要花钱改造储存箱。
问题7、你对整个作业系统有什么建议?
请尽量扩展思路
就该工厂的实际情况而言,暂时不需要储备过多生产能力,只需要能够满足生产要求就可以了,因此我们建议
1、减少产能过剩的加工设备。
目前生产能力盈余较多的有倾倒机、去石子设备、去叶茎设备,可以卖掉两台倾倒机、两套去石子设备和一套去叶茎设备,所得的资金可用于购置烘干机、分选机等设备或作他用。
2、增加产能不足的瓶颈部位加工设备。
需增加三台烘干机和一台分选机,这样使产能相对于目前要求的最大值稍大,从而完全满足生产的需求。
3、改变工人的工作安排,高峰期,除接收工序的工人以外,其他工序的工人需要在上午10开始上班,从而避免卡车等待地现象发生。
加强对工人的培训,努力提高其工作效率。
每年高峰期到来之前,应至少培训一个星期,使其熟悉操作规程和设备的运用。
4、改进临时用工的措施,尽量与临时雇工形成较为长期的合作关系;制订严格的制度,减少缺勤率,使临时用工对生产的负面影响尽量降低。