烟雾报警器上壳体模具设计毕业设计Word下载.docx
《烟雾报警器上壳体模具设计毕业设计Word下载.docx》由会员分享,可在线阅读,更多相关《烟雾报警器上壳体模具设计毕业设计Word下载.docx(62页珍藏版)》请在冰豆网上搜索。
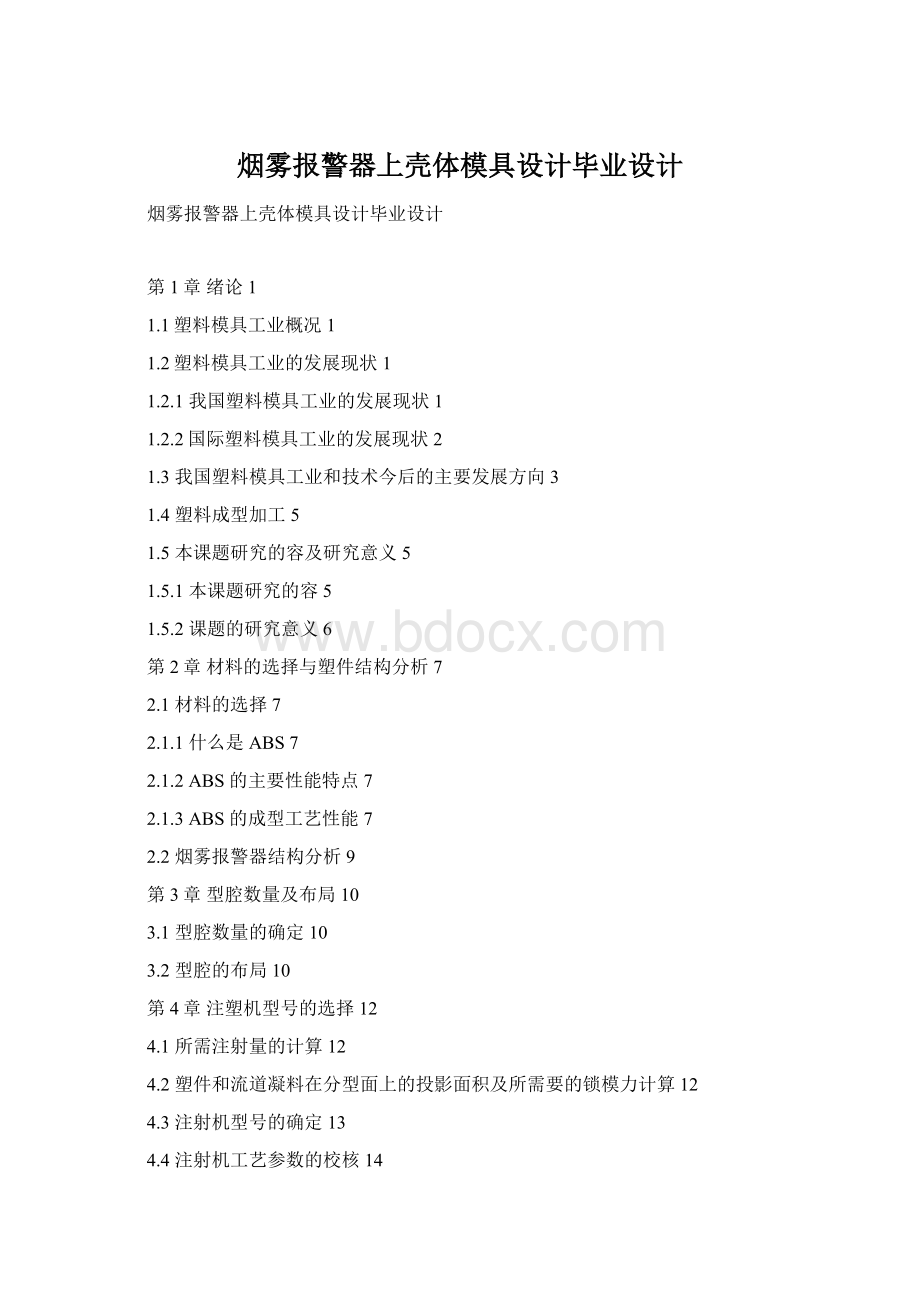
5.2.1凸模结构设计16
5.2.2按刚度计算型腔侧壁的厚度S17
5.2.3模镶件经验确定法17
5.2.4定模板、动模板基本尺寸的确定18
5.2.5模架(模体)尺寸的确定18
5.2.6方铁、复位杆、限位钉的设计19
5.3排气系统的设计19
5.4浇注系统设计19
5.4.1对浇注系统进行整体设计时,一般应遵循如下基本原则:
20
5.4.2主流道的设计20
5.4.3分流道的设计21
5.4.4浇口的设计22
5.4.5冷料穴的设计23
5.5冷却系统的设计24
5.6合模导向机构的设计24
5.6.1机构的功用25
5.6.2导向结构的总体设计25
5.6.3导柱的设计25
5.6.4导套的设计26
5.7脱模推出机构的设计26
5.7.1脱模机构的设计原则27
5.7.2推出方式的选择27
5.7.3塑件的推出机构的设计原则27
第6章SolidWorks的简介29
第7章塑料制品常见问题分析34
第8章总结与展望39
8.1总结39
8.2展望39
致谢40
参考文献41
外文资料原文及翻译42
毕业设计进度表及任务书
第1章绪论
1.1塑料模具工业概况
随着注射成型技术的不断发展,塑料制品已经深入到日常生活中的每—个角落。
由于塑料件具有重量轻,生产方便,价格便宜等优点,大到成人用品,小到儿童玩具,几乎全部采用塑料件生产。
在高分子材料加工领域中,用于塑料制品成形的模具,称为塑料成形模具,简称塑料模.塑料模优化设计,是当代高分子材料加工领域中的重大课题。
塑料件的模具结构设计,应根据企业实际生产的具体要求来进行模具结构设计。
模具生产水平的高低,已成为衡量一个国家产品制造水平高低的重要标志,因为模具在很大程度上决定着产品成本质量、效益和新产品的开发能力。
我国塑模技术近几年取得很大发展。
大型塑料模已可生产34英寸大屏幕彩电塑壳模具,6千克容量洗衣机全套塑模及汽车保险杠。
精密注射模方面,已能生产多型腔小模数齿轮模具和600腔塑封模具。
汽辅成型技术已得到广泛应用。
现在日本有名模具生产企业,如东芝机械、富士TACHNICA,三精密、名古屋金型和三贵金型株式会社等及我国,,等地已使用一些先进模具生产与制造技术。
如用PRO/E或UG进行产品的3D造型和分模,使用MASTERCAM或者CIMATRON来做刀路,用日本的FANUC系统或的加工中心进行模具型腔和型芯的加工,用高速加工中心做铜电极,用三坐标测量仪来检验。
1.2塑料模具工业的发展现状
1.2.1我国塑料模具工业的发展现状
80年代以来,在国家产业政策和与之配套的一系列国家经济政策的支持和引导下,我国模具工业发展迅速,年均增速均为13%,1999年我国模具工业产值为245亿,2003年模具进出口统计中,我国模具的出口总额为2.52亿美元,我国模具的出口总额3亿美元,进口额则达到13亿多美元,在进口模具中的塑料模具占到50%左右。
目前,根据国际模具网模具行业专家的初步统计,中国约有模具生产厂点2万余家,从业人员有50多万人,全年模具产值达534亿元人民币。
可以看出,在塑料模具方面,我国与国外产品还存在较大差距。
在引进的塑料模具中,以科技含量较高的模具居多,如高精度模具、大型模具。
热流道模具、气辅及高压注射成型模具等。
现代塑料制品对表面光洁度、成型时间都提高了更高的要求,因而也推动了塑料模具的发展。
以电视机塑料外壳模具为例。
其精度已由以前的0.05~0.1mm提高到0.005~0.01mm,制造周期也由8个月缩短到了2个月,并且使用寿命也由过去可制10万~20万件制品延长到了可60万件制品。
从电视机外壳塑料模具的发展可以看到,高精密、长寿命、短周期、低成本是模具的发展方向。
目前我国使用覆盖率和使用量最大的模具标准件为冷冲模架、注塑模架和推杆管这三类产品。
以注塑模架为例,目前全国总产值有20多亿元,按照需求,国约需注塑模架30多亿元,而实际上国市场并未达到这个规模,其中主要一个原因就是模具厂家观念旧,注塑模架自产配
比例较高,外购很少。
这样做厂家不仅重复制造本应标准化的购件,延长了模具生产周期,又不利于维修。
很多相关的模具标准件并没有相关的国家标准,因此制定模具构件的标准规工作也是当务之急。
1.2.2国际塑料模具工业的发展现状
美国1991年发表的“国家关键技术报告”认为:
材料领域的进展几乎可以显著改进国民经济所有部门的产品性能,提高它们的竞争能力;
因此把材料列为六大关键技术的首位。
这是由于先进材料与制造技术是未来国民经济与国防力量
表1.1国外塑料模具技术比较
发展的基础,是各种高、新技术成果转化为实用产品与商品的关键。
当前各种新材料市场规模超过1000亿美元,预计到2000年将达4000亿美元。
由新材料带动而产生的新产品新技术则是一个更大的市场。
以上参展项目基本上代表了当前国际和国的先进水平和发展趋势,具体表现在如下五个方面。
(1)网络的CAD/CAE/CAM一体化系统结构初见端倪。
随着计算机硬件与软件的进步以及工业部门的实际需求,国外许多著名计算机软件开发商已能按实际生产过程中的功能要求划分产品系列,在网络系统下实现了CAD/CAM的一体化。
解决了传统混合型CAD/CAM系统无法满足实际生产过程分工协作要求的问题,以便更能符合实际应用的自然过程。
例如英国达尔康公司在原有软件DUCT5的基础上,为适应最新软件发展及工业生产实际而在最近推出的CAD/CAM集成化系统Delcam'
sPowerSolution,该系统覆盖了几何建模、逆问工程、工业设计、工程制图、仿真分析、快速原型、数控编程、测量分析等领域。
(2)AM软件日益深人人心并发挥越来越重要的作用
在90年代,能进行复杂形体几何造型和NC加工的CAD/CAM系统主要是在工作站上采用UNIX操作系统开发和应用的,如美国的Pro-E、UGⅡ、CADDS5软件,法国的CATIA、EUCLID软件和英国的DUCT5软件等。
随着微机技术的突飞猛进、在90年代后期,新一代的微机CAD/CAM软件,如Solidworks、Solidadae崭露头角,深得用户的好评。
这些微机软件不仅在采用诸如NURBS曲面、三维参数化特征造型等先进技术方面继承了工作站级CAD/CAM软件的优点,而且在Windows风格、动态导航、特征树、面向对象等方面具有工作站级软件所不能比拟的优点。
(3)AM软件的智能化程度正在逐渐提高
由于在现阶段,模具设计和制造在很大程度上仍然依靠着模具设计与制造工程师的经验。
仅凭CAD/CAM软件有限的数值分析功能无法为用户提供完善和正确的设计结果,软件的智能化功能必不可少。
面向制造、基于知识的智能化功能是衡量模具设计与制造软件先进性与实用性的重要标志之一。
在模架的设计过程中实现了模架零件的全相关,并能自动产生材料明细表和供NC加工的钻孔表格。
在NC加工方面,实现了智能化的粗加工、加工参数的设定以及对整个加工过程进行加工结果的校验分析,这些具有智能化的功能可以显著地提高注塑模具的生产效率和产品质量。
1.3我国塑料模具工业和技术今后的主要发展方向
1)提高大型、精密、复杂、长寿命模具的设计制造水平及比例。
2)在塑料模设计制造中全面推广应用CAD/CAM/CAE技术。
基于网络的CAD/CAM/CAE一体化系统结构初见端倪,CAD/CAM软件的智能化程度将逐步提高;
塑料制件及模具的3D设计与成型过程的3D分析将在我国塑料模具工业中发挥越来越重要的作用。
3)推广应用热流道技术、气辅注射成型技术和高压注射成型技术。
气助注射成型可在保证产品质量的前提下,大幅度降低成本。
气体辅助注射成型比传统的普通注射工艺有更多的工艺参数需要确定和控制体辅,而且其常用于较复杂的大型制品,模具设计和控制的难度较大,因此,开发气体辅助成型流动分析软件,显得十分重要。
4)开发新的塑料成型工艺和快速经济模具。
以适应多品种、少批量的生产方式。
5)提高塑料模标准化水平和标准件的使用率。
首先要制订统一的国家标准,并严格按标准生产;
其次要逐步形成规模生产、提高商品化程度、提高标准件质量、降低成本;
再次是要进一步增加标准件规格品种。
6)应用优质模具材料和先进的表面处理技术对于提高模具寿命和质量显得十分必要。
7)研究和应用模具的高速测量技术与逆向工程。
采用三坐标测量仪或三坐标扫描仪实现逆向工程是塑料模CAD/CAM的关键技术之一。
研究和应用多样、调整、廉价的检测设备是实现逆向工程的必要前提。
8)“十一五”期间我国塑料模具发展方向,塑料模具占模具总量近40%,而这个比例仍不断上升。
塑料模具中为汽车和家电配套的大型注塑模具,为集成电路配套的精密塑料模具,为电子信息产业和机械及包装配套的多层、多腔、多材质、多色精密注塑模,为新型建材及节水农业配套的塑料异型材挤出模及管路和喷头模具等,目前虽然已有相当技术基础并正在快速发展,但技术水平与国外仍有较大差距,每年进口达几亿美元,因此“十一五”期间应重点发展。
图1.1螺杆式注射机
1.4塑料成型加工
通常,热塑性塑料采用注射成型法,热固性塑料采用压缩成型法。
塑料成型加工是一个比较复杂的过程,其原理是利用塑料的固有物理性质,加热使塑料变成可塑的或可流动的状态,然后再施加压力使其充满模具型腔而
成为所需的零件制品。
一般的零件加工是用注射成型或压缩成型来完成的;
型材可以用挤出成型方法加工;
而瓶、薄膜则采用中空成型方法加工。
塑料成型加工中需要加热,根据不同的温度可以用不同的加工方法。
注射成型也称为注塑成型,其成型原理是:
首先将颗粒状或粉状的塑料连续输入到注射机的料筒中受热并逐渐熔融,使其成为黏性流动状态;
料筒中的螺杆或柱塞将塑料熔体推到料筒端部,通过料筒端部的喷嘴和模具的浇注系统注入闭合的模具型腔中,充满型腔后经过保压、冷却,固化定型;
然后开模并由模具推出装置将塑料制件推出。
注射成型的生产是周期性的,使用注射机,可以实行自动化生产,生产效率极高。
主要用于加工成型热塑性塑料,现在也可用于成型部分热固性塑料。
注
射成型在塑料制件成型中占有很大比例(工程塑料占80%以上)。
现在注射成型已发展到新型的注射工艺,如双色或多色注射可以生产出颜色丰富、美观的塑料制品;
低发泡注射成型可以生产具有缓冲、隔声、隔热的塑料制品;
热流道注射工艺可以生产大型塑料制品,并降低浇注系统的凝料等。
1.5本课题研究的容及研究意义
1.5.1本课题研究的容
本课题主要是应用SOLIDWORKS软件对烟雾报警器上盖进行模具设计,具体设计容如下:
1.首先进行烟雾报警器上盖模具的理论设计和参数的确定,其主要容有:
(1)注塑模成型零件设计;
(2)排气系统设计;
(3)浇注系统设计;
(4)冷却系统设计;
(5)脱模系统设计;
(6)导向定位系统设计。
2.使用SOLIDWORKS软件对烟雾报警器上盖模具进行设计。
其主要包括:
应用SOLIDWORKS软件进行成型零件设计、浇注系统设计、型腔组件水道设计、创建铸模与模具打开、塑料成型分析、模架与标准件设计、其他操作以及绘制三维实体仿真图和模具平面三视图等。
3.分析常见注塑制品的缺陷及产生原因,并提供解决方法。
主要包括龟裂、填充不足、溢边、翘曲变形、凹痕及气泡、熔接线、等几种主要缺陷产生的原因和解决方法。
1.5.2课题的研究意义
随着现代家庭用火、用电量的增加,家庭火灾发生的频率越来越高。
家庭火灾一旦发生,很容易出现扑救不及时、灭火器材缺乏及在场人惊慌失措、逃生迟缓等不利因素,最终导致重大生命财产损失。
探讨家庭火灾的特点及防火对策,对于预防家庭火灾,减少火灾损失具有现实意义在现代城市家庭里,许多人因不懂家庭安全常识引起火灾事故,使好端端的幸福家庭转眼间毁于一旦,有的导致家破人亡,而且一旦发生居民家庭火灾,处置不当、报警迟缓,是造成人员伤亡的主要原因。
所以说,人们应该积极了解家庭火灾的主要起因,掌握防止发生火灾的知识和万一发生火灾时保护自己的方法,及时消除火灾隐患。
所以本文对烟雾报警器上盖注塑模CAD一体化的研究和应用不仅对实现产品的快速更新及大批量生产具有重要意义,而且对人们的生命财产的保障也具有重要的意义。
第2章材料的选择与塑件结构分析
2.1材料的选择
2.1.1什么是ABS
根据塑件的工艺性分析可知,本设计选用选用ABS塑料较为恰当。
ABS是ArcrylomtrileBidadieneStyrene的缩写形式,全称为丙稀腈-丁二稀-苯乙稀三元共聚物,属于无定性聚合物,密度为1.05g/cm³
。
在ABS的三种单体中,每种单体都有不同的特征:
丙稀腈有高强度、热稳定性以及化学稳定性;
丁二稀具有抗冲击性;
苯乙烯具有易加工、高光洁度及高强度。
ABS的特性主要取决于三种单体的比率及两项中的分子结构。
这样就可以形成多种性能的材料,所以ABS有非常广泛的用途。
2.1.2ABS的主要性能特点
ABS具有较强的综合性能,具有较好的韧性、刚性、抗冲击性、抗拉强度、很好的耐热、耐寒性能;
具有较好的化学稳定性;
很易加工、染色。
但是,在大气中老化性较差。
2.1.3ABS的成型工艺性能
〈1〉使用前的准备工作
ABS的吸湿性和对水分的敏感性较大,在加工前要进行充分的干燥和预热。
不单能消除水气造成的制品表面烟花状气泡带,而且还有助于塑料的塑化,减少制品表面色斑和云纹。
ABS原料要控制水分在0.3%以下。
干冬季节,干燥温度为75~80℃,厚料层厚度为20~30mm,干燥时间为2~3h.夏季雨水天要在80~90℃下干燥4~8小时。
表面要求光泽的塑料须长时间预热干燥达8~16小时。
此外,还要根据原料产地、储存、运输状况,对干燥条件适当调整。
ABS具有较好的染色性,一般采用浮染法。
原料要加入紫外线吸收剂和抗氧剂,以提高耐老化能力。
〈2〉ABS的成型温度控制
ABS是无定性材料,分解温度为270℃,耐热性不是太好。
因含有橡胶成分,过高的成型温度并不会使流动性增加,相反会引起橡胶分解,流动性降低。
同时,长时间的高温作用会造成降解和炭化。
所以成型时应严格控制温度在允许围。
对柱塞式料筒温度应控制在160~230℃,螺杆式料筒温度应控制在160~220℃,喷嘴温度在170~180℃围。
ABS成型易取高料温、高模温,但料温过高易分解。
对精度较高的塑件,模温宜取50~60℃,对高光洁度,耐热塑件,模温宜取60~80℃。
较高的模具温度,制品外表面能够达到较光洁,可以避免合模线和陷坑等不良现象,减少制品变形,但收缩率较大。
一般的模具温度应尽可能低些。
〈3〉注射压力的确定原则
注射压力的大小主要取决于制品的结构和壁厚,一般控制在60~120Mpa。
壁薄流道较长,流动阻力较大时,注射压力可高至130~150Mpa。
壁厚,浇口截面较大,流动阻力小时,注射压力可略低些。
提高注射压力可以提高ABS制品的光泽度。
注射过程中,保压压力的大小,对制品的表观质量和银丝状缺陷都有较大的影响。
压力过小,塑料收缩大,与型腔表面脱离接触的机会大,在温度较高时,制品表面易雾化。
压力过大,塑料型腔表面摩擦作用强烈,容易造成黏模。
所以一定要调整配好保压压力和保压时间。
保压压力为注射压力的30%~60%。
背压控制得越低越好,背压最高时可采用1.5Mpa。
螺杆前进速度采用慢速,一般不超过
0.55~0.65m/s。
〈4〉注射速度的确定
ABS采用中等注射速度效果较好。
当注射速度过快时,塑料容易分解,甚至烧焦,从而在制品上出现熔接缝,光洁度差,及浇口附近的物料发红等缺陷。
表2.1ABS材料的主要特性
本塑件所用材料为丙烯烃-丁二烯-苯乙烯共聚物(ABS),由此查塑料模具设计手册可知,本塑件宜选用一般精度5级。
2.2烟雾报警器结构分析
本文设计的烟雾报警器上盖外形较简单,外壳外部如图2.1a所示,部如图2.1b所示,是简单的圆形外形。
图2.1a烟雾报警器上盖外部结构图图2.1b烟雾报警器上盖部结构图
该烟雾报警器上盖为一曲面结构,壁厚均匀,结构如图2.2所示,最大外围轮廓直径为107mm,高度为40mm,厚度为1.5mm。
总体积约为24cm³
,总质量约为24g。
第3章型腔数量及布局
3.1型腔数量的确定
型腔数目的决定与下列条件有关:
1、塑件尺寸精度
型腔数越多时,精度也相对地降低,1、2级超精密注塑件,只能一模一腔,当尺寸数目少时,可以一模二腔。
3、4级的精密级塑件,最多一模四腔。
2、模具制造成本
多腔模的制造成本高于单腔模,但不是简单的倍数比。
从塑件成本中所占的模具费比例看,多腔模比单腔模具低。
3、注塑成形的生产效益
多腔模从表面上看,比单腔模经济效益高。
但是多腔模所使用的注射机大,每一注射循环期长而维持费较高,所以要从最经济的条件上考虑一模的腔数。
4、制造难度
多腔模的制造难度比单腔模大,当其中某一腔先损坏时,应立即停机维修,影响生产。
塑料的成形收缩是受多方面影响的,如塑料品种,塑件尺寸大小,几何形状,熔体温度,模具温度,注射压力,充模时间,保压时间等。
影响最显著的是塑件的壁厚和同何形状的复杂程度。
为了制模具与注塑机的生产能力相匹配,提高生产效率和经济性,并保证塑件精度,模具设计时应确定型腔数目。
型腔数目的确定一般可以根据经济性、注射机的额定锁模力、注射机的最大注射量、制品的精度等。
一般来说,大中型塑件和精度要求高的小型塑件优先采用一模一腔的结构,但对于精度要求不高的小型塑件(没有配合精度要求),形状简单,又是大批量生产时,若采用多型腔模具可提供独特的优越条件,使生产效率大为提高。
该塑件精度要求不高,生产批量适中,且具有两边抽芯,抽芯距较长,从模具加工成本,制品生产时的成本考虑,故拟定为一模两腔。
采用一模两件,能够适应生产的需求,采用侧浇口,浇口去除方便,模具结构孔不复杂,容易保证塑件质量。
3.2型腔的布局
多型腔模具设计的重要问题之一就是浇注系统的布置方式,由于型腔的排布与浇注系统布置密切相关,因而型腔的排布在多型腔模具设计中应加以综合考虑。
型腔的排布应使每一个型腔都通过浇注系统从总压力中心中均等地分得所需的压力,以保证塑料熔体同时均匀地充满每个型腔,使各型腔的塑件在质量均一稳定。
这就要求型腔与主流道之间的距离尽可能最短,同时采用平衡的流道和合理的浇口尺寸以及均匀的冷却等。
合理的型腔排布可以避免塑件的尺寸差异、应力形成及脱模困难等问题。
平衡式型腔布局的特点是从主流道到各型腔浇口的分流道的长度、截面形状及尺寸均对应相同,可以实现均衡进料和同时充满型腔的目的;
非平衡式型腔布局的特点是从主流道到各型腔浇口的分流道的长度不相等,因而不利于均衡进料,但可以缩短流道的总长度,为达到同时充满型腔的目的,各浇口的截面尺寸制作得不相同。
需要指出的是,多型腔模具最好成型同一尺寸及精度要求的制件,不同塑件原则上不应该用一
副多模腔模具生产。
在同一副模具中同时安排尺寸相差较大的型腔不是一个好的设计,不过有时为了节约,特别是成型配套式塑件的模具,在生产实践中还使用这一方法,但难免会引起一些缺陷,如有些塑件发生翘曲、有些则有过大的不可逆应变等。
本设计成型同一塑件,且壁厚均匀,故采用平衡式,布局如图3.1所示:
图3.1烟雾报警器上壳体模腔布局
第4章注塑机型号的选择
注射模是安装在注射机上使用的工艺装备,因此设计注射模时应该详细了解注射机的技术规,才能设计出符合要求的模具。
注射机规格的确定主要是根据塑件的大小及型腔的数目和排列方式,在确定模具结构形式及初步估算外形尺寸的前提下,设计人员应对模具所需的注射量、锁模力、注射压力、拉杆间距、最大和最小模具厚度、推出形式、推出位置、推出行程、开模距离等进行计算。
根据这些参数选择一台和模具相匹配的注射机,倘若用户已提供了注射机的型号和规格,设计人员必须对其进行校核,若不能满足要求,则必须自己调整或与用户取得商量调整。
4.1所需注射量的计算
利用SolidWorks三维软件定性测得该塑件的实际体积为
=23.91cm³
,塑件质量
=23.91×
1.=25.23g.设浇注系统的体积为塑件的0.6倍,则
流道凝料的质量
=2×
0.6
=30.27gm=2×
25.23+30.27=80.73g
体积
=2×
=28.70cm³
所以可得一次总的注射量为:
=2
+
=23.91×
2+28.70=76.52cm³
公称注射量为:
=
/0.8=76.52/0.8=95.65cm³
=95.65×
1.=100.92g
4.2塑件和流道凝料在分型面上的投影面积及所需要的锁模力计算
根据Solidworks建模,对塑件投影面积分析得
为8786.35mm²
流道凝料(包括浇口)在分型面上的投影面积
,在模具设计前是个未知数,根据多型腔模的统计分析,大致是塑件在分型面上的投影面积的0.2~0.5倍,结合本设计的实际情况取0.3,则总的投影面积计算为:
A=nA+sA(式4-1)
所以:
A=2×
8786.35+0.3×
8786.35=20208.605mm²
从而得到
≥
=AP(式4-2)
式中,
——注射机的额定锁模力(N);
——模具型腔塑料熔体平均压力(MPa),一般为注射压力的0.3~0.65倍,通常为20~40Mpa,根据《注塑模具设计实用教程》书中表1-4,因本设计所用材料为ABS,所以选型腔压强值为40MPa;
≥
=20208.605×
40=808344.2N,则F≥810KN
4.3注射机型号的确定
注射机规格主要是根据塑件的大小及型腔的数目和排列方式来确定,在确定模具结构形式及初步估算外形尺寸的前提下进行注射机相关参数的计算。
在本设计中,根据每一生产周期的注射量和锁模力的计算值,初步选用葛兰TZ120A卧式注射机,主要技术参数如表2-1所列:
表4.1所选注塑机的主要技术参数
螺杆直径(mm)
40