形变和实效对非调质螺栓钢耐疲劳性能的影响文档格式.docx
《形变和实效对非调质螺栓钢耐疲劳性能的影响文档格式.docx》由会员分享,可在线阅读,更多相关《形变和实效对非调质螺栓钢耐疲劳性能的影响文档格式.docx(23页珍藏版)》请在冰豆网上搜索。
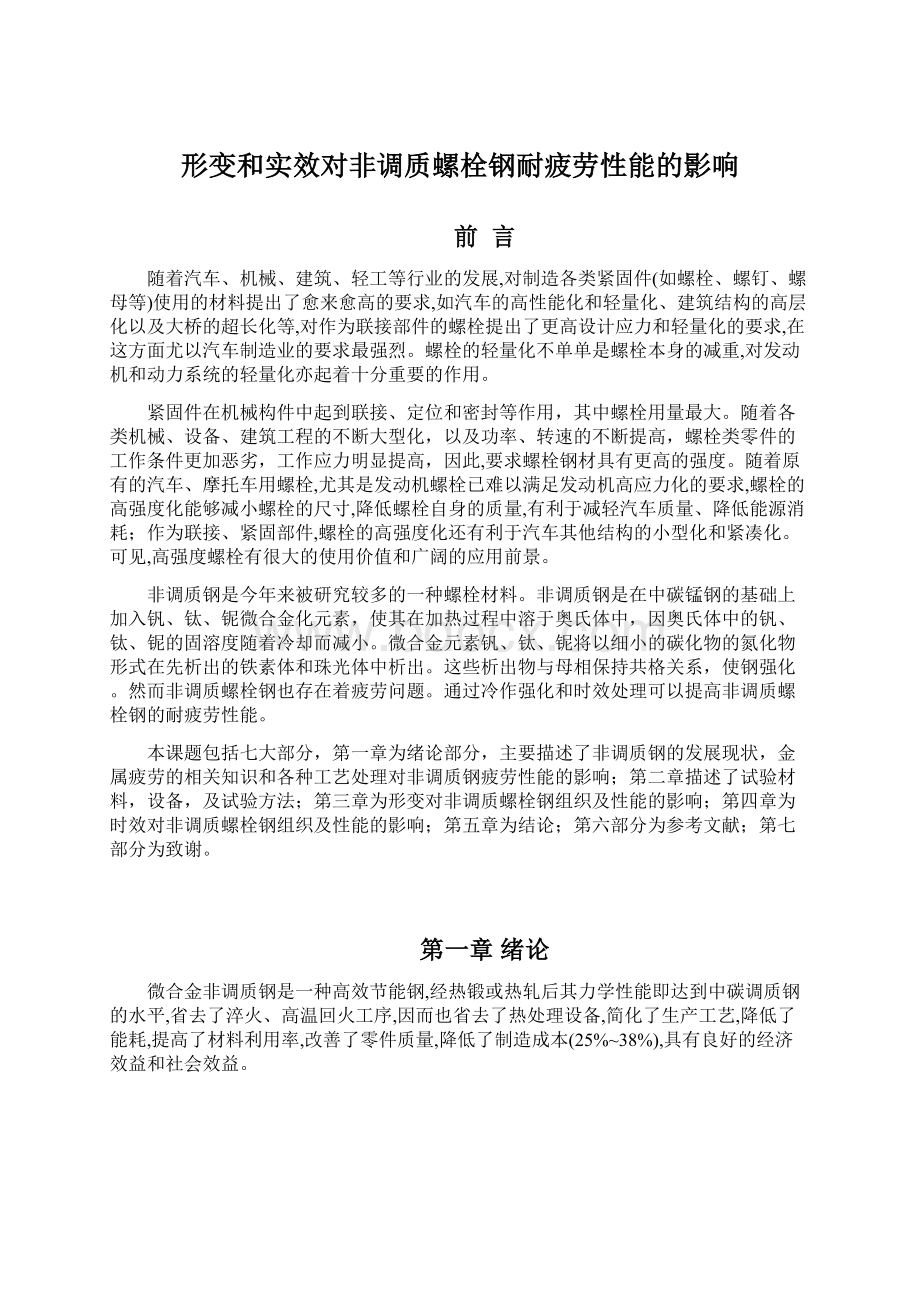
这类钢在热轧状态、锻造状态或正火状态的力学性能既缩短了生产周期,又节省了能源。
非调质钢的力学性能取决于基体显微组织和析出相的强化。
非调质钢分为热锻用非调质钢、直接切削用非凋质钢、冷作强化非调质钢和高韧性调质钢。
热锻用非调质钢用于热锻件(如曲轴、连杆等),直接切削用非调质钢用热轧件直接加工成零件,冷作强化非调质钢用于标准件(如螺母等),高韧性非调质钢用于要求韧性较高的零部件。
1.1.2非调质钢的分类
按用途不同非调质钢可分为热加工用非调质钢、冷作硬化用非调质钢和直接切削用非调质钢。
热加工用非调质钢主要用于各种热加工锻件[2],如履带链轨节、支重轮轮体、引导轮轮体、回转齿圈、标准件、各挖臂关节连接部、齿轮、油缸连接头、阀体连接块等,可以省去调质及其后的表面清理。
根据所需机械性能不同可代替40Cr,45,35CrMo,40Mn2,35MnB等钢种的调质材。
冷作硬化非调质钢是综合应用冷作强化和微合金元素的细晶强化、沉淀强化技术而开发的,可用作各种高强度紧固件。
直接切削用非调质钢可替代现有40Cr及45调质钢制作轴类零件,可以减少加工余量。
根据非调质钢基体组织的不同则可分为:
铁素体和珠光体型、马氏体型、贝氏体型。
早期开发的微合金非调质钢具有铁素体和珠光体混合组织,主要通过基体组织上弥散析出细微的碳化物及碳氮化物来改变材料的机械性能[3],利用了微量合金元素在奥氏体、铁素体和珠光体一铁素体片中析出产生的晶粒细化和析出强化效果,其强度和硬度可以达到相应调质钢水平。
这类钢是在中碳钢或中碳锰钢的基础上添加微量的V,Ti,Nb元素形成的,热锻或热轧后,空冷条件下靠微合金元素的沉淀析出与晶粒细化达到某些机械零件所要求的强度、塑性和韧性[4]。
铁素体一珠光体型非调质钢的最大缺点是钢中先共析铁素体易沿原奥氏体晶界析出,得到粗大的铁素体一珠光体组织,韧性较差[5]。
1.1.3非调质钢的强化原理[6-8]
非调质钢的强化方式是沉淀强化、细化铁素体晶粒强化和固溶强化。
起沉淀强化作用的元素主要是钒,这是由于钒在1100℃可完全溶入奥氏体,在钢冷却时析出细小、弥散的VC或V(C,N),提高铁素体的强度。
铌沉淀强化的作用是次要的,其主要作用是阻碍奥氏体的再结晶,含铌钢在通常的热加工条件下不发生再结晶,在热加工时晶粒被拉长,增加奥氏体晶界面积。
另外,由于形变诱发析出Nb(C,N)质点阻止奥氏体发生静态再结晶。
在钢冷却过程中,先共析铁素体不但可以在奥氏体晶界上形核,还能在奥氏体晶粒内的位错阵列上形核,因而细化了铁素体晶粒,并使其分布均匀。
钛的主要作用是细化奥氏体晶粒,使钢在加热或热加工时保持细小的奥氏体晶粒。
锰的作用是固溶于铁素体中引起固溶强化,提高铁素体的强度;
由于增加过冷奥氏体的稳定性而增加相变的过冷度,细化铁素体和珠光体;
促进钒在高温下溶解而提高钒的沉淀强化作用。
应该强调指出,细化铁素体晶粒在提高强度的同时又改善了钢的韧性,是非调质钢最有效的强韧化措施。
1.2非调质螺栓钢
1.2.1非调质螺栓的生产工艺
70年代世界性的能源危机,使制造业出现了一个以简单化工序、节省能源来降低成本,提高竞争力的新潮流。
日本新日铁公司首先研制出一种用于制造8.8级高强度螺栓的强度高塑性好的低碳微合金化非调质钢,省去热处理工艺。
其生产工序为:
热轧盘棒料—酸洗—冷拔—冷镦—切边—搓丝—时效—电镀—成品。
我国从80年代中期开始非调质钢的研制,并取得了良好的效果。
1.2.2冷变形对非调质螺栓强度的影响
冷变形或冷加工是金属在再结晶温度以下所进行的变形或加工,如钢的冷拉或冷冲压等。
在外力作用下,晶粒的形状随着工件外形的变化而变化。
当工件的外形被拉长或压扁时,其内部晶粒的形状也随之被拉长或压扁,导致晶格发生畸变,使金属进一步滑移的阻力增大,因此金属的强度和硬度显著提高,塑性和韧性明显下降,产生所谓“变形强化”现象。
同时也要理解疲劳是材料受交变(载荷)应力作用经一定的应力循环后发生的断裂现象,其微观表现为在交变应力作用下疲劳裂纹的产生及扩展。
当应力一定时,材料在断裂前所经历的循环次数(疲劳寿命)与疲劳裂纹的扩展速率da/dN的大小有关,而da/dN在很大程度上取决于材料的强度、塑性、弹性及其相对高低、是材料各种性能的综合反映[9]。
在金属整个变形过程中,当外力超过屈服强度之后,塑性变形并不像屈服平台那样连续流变下去,而需要不断增加外力才能继续进行。
这表明金属材料有一种阻止继续塑性变形的能力,这就是形变强化性能。
为提高材料的强度对原材料进行冷变形,冷拔后金相组织及晶粒度变化不大,但铁素体内部形成大量的位错,并且位错纠缠形成了胞状亚结构,胞壁处位错密度高于胞内。
经300℃/2h时效处理后,铁素体中的位错发生了回复现象,生成明显的亚晶界。
位错的回复及亚晶界的形成将降低位错密度,消除内应力,改善螺栓尺寸的稳定性[10]。
1.2.3碳含量对非调质钢力学性能的影响[11]
a)随着试验钢中碳含量的减少,基体中铁素体含量增加,强度和加工硬化率降低,塑性升高,因而变形抗力降低,临界压缩比升高。
所以在保证强度的基础上,降低碳含量有利于改善钢的强韧性和冷加工性能。
b)冷拔减面率达到一定值之后,由于鲍辛格效应的作用,试验钢的压缩真应力下降。
随着碳含量的降低,压缩真应力降低的幅度变大,且开始下降所需的减面率降低。
超过此值,由于加工硬化率增大,压缩真应力又重新上升。
因此,最佳减面率受碳含量的影响,应该在保证强度的条件下选取鲍辛格效应较大,而加工硬化率没有明显上升的阶段。
1.2.4时效工艺对微观组织和力学性能的影响
时效处理[12]指合金工件经固溶处理,冷塑性变形或铸造、锻造后,在较高的温度放置或室温保持其性能、形状、尺寸随时间而变化的热处理工艺。
在冷作强化的状态下使用的非调质钢螺栓,形变组织中存在着高密度的可动位错和其他缺陷,使其处于不稳定状态。
在螺栓加载时,这些可动位错就会攀移,引起微小屈服,影响其使用性能。
时效处理可稳定可动位错,同时还可使非调质螺栓具有良好的综合性能。
由于时效处理刃位错可获得足够的能量产生攀移,使滑移面上不规则的位错重新分布,排列成墙,形成亚晶,所以时效后应变硬化指数有所恢复,而塑性基本保持不变,较高的残余应变硬化指数保证了螺栓在使用时抗偶然过载的能力。
时效前后螺栓组织经SEM观察均为铁素体+碎化珠光体,晶粒度经超细化均达到12级,放大的铁素体晶粒中有明显的析出物。
未经时效处理的螺栓中铁素体内部形成了大量的位错,并且位错纠缠形成了胞状亚结构。
经时效处理后,铁素体中形成了亚晶界,位错形态发生了变化[13]。
1.2.5表面处理对抗拉强度的影响[14-15]
为了发挥高强度钢所具有的性能潜力,提高其疲劳强度,常常使用表面强化技术来减少材料对应力集中的敏感度、防止表层中裂纹的产生和扩展。
目前适用于钢的表面强化技术有磨削加工、振动强化、喷丸强化以及强化后镀铬等等。
高强度螺栓最新表面处理方法是锌铝铬涂层,又称“达克罗”处理,其耐盐雾腐蚀性能高达500h以上,并且涂层不会引起氢脆,其成膜温度在约300℃左右,厚度约几个微米。
试验结果表明,螺栓经表面“达克罗”处理后,抗拉强度无明显变化。
1.3非调质螺栓钢的耐疲劳性能
1.3.1金属的疲劳
工程中很多机件和构件都在变动载荷下工作的,如曲轴、连杆、齿轮、弹簧、辊子、叶片及桥梁等,其失效形式主要是疲劳断裂。
据统计,疲劳破坏在整个失效件中约占80%左右,极易造成人身事故和经济损失,危害性极大。
因此,工程技术界对其极其重视,从力学、设计、材料、及工艺方面开展疲劳研究,寻求有效对策,至今已有百余年历史,取得了很大进展,成为材料强度科学领域中的一个重要组成部分。
1.3.2疲劳裂纹的扩展机理
疲劳过程包括疲劳裂纹萌生、裂纹亚稳扩展及最后失稳扩展三个阶段,其疲劳寿命Nf由疲劳裂纹萌生期Ni和裂纹亚稳扩展期Np所组成。
疲劳裂纹一般产生于应力集中处,或通过腐蚀疲劳而产生裂纹。
通过对疲劳断裂的断口进行显微分析知道,在疲劳裂纹的扩展中,在均匀的循环应力作用下,只要应力值足够大,每一次应力循环都会在断裂面产生一道裂纹。
每经过一次加载循环,裂纹尖端即经历一次锐化-钝化-再锐化的过程。
裂纹扩展一段冲离,断口表面上便会产生一道辉纹,这样,随着应力循环的作用,裂纹不断向前扩展,当裂纹扩展到一定程度,结构即进入最后的断裂失效阶段[16]。
1.3.3材料、结构及工艺对耐疲劳性能的影响
实验证明材料因素不是影响高强度螺栓疲劳性能的主要因素。
其他条件相同,由于热处理波动导致螺栓的硬度在不大的范围内变动时,其疲劳性能无明显变化。
对于先热处理后滚丝的高强度螺栓,为保证其优良的疲劳性能,在滚丝之后不允许再次回火(比如在试图降低螺栓过高的硬度的情况下),也不允许长时间靠近温度较高的热源(这将类似于去应力退火),否则其疲劳性能将产生大幅度下降。
在这两种情况下,螺栓疲劳性能下降的主要原因可能是较高的温度改变了滚压螺纹表面有利的残余压应力条件。
高强度螺栓表面存在脱碳现象时,其疲劳性能将产生较大幅度下降。
螺栓先滚丝后磷化比先磷化后滚丝的疲劳强度低。
主要原因可能是磷化膜在滚丝过程中起到了减磨作用,从而改善了滚丝后螺栓螺纹上的应力分布,提高了螺纹表面光洁度。
由于在滚丝时施加润滑油也可起到减磨的作用,因此,为了提高螺栓的疲劳强度,延长滚丝轮的使用寿命,在螺纹滚丝时应采用性能良好的润滑油予以润滑。
螺栓头下圆角过渡形式、粗糙度、滚丝轮螺纹牙形等结构、工艺因素将显著影响高强度螺栓的疲劳性能[17]。
1.3.4提高抗疲劳寿命的工艺方法[18]
1)采用加强螺纹
加强螺纹的显著特点就是小径比普通螺纹大些,压根圆角半径增大,减小螺栓的应力集中。
目前航空、航天器螺栓多采用加强螺纹。
2)用毛坯热处理强化后滚压螺纹来改善螺纹疲劳性能
采用滚压螺纹的工艺方法,由于冷作硬化的作用,表层有残余压应力,可使螺栓内部金属纤维线走向合理且不被切断,其疲劳强度可较车制螺纹高30%~40%。
若热处理后再滚压螺纹,使零件表面得到强化并获得残余压力层,其材料表面疲劳极限可提高70%~100%。
这种工艺还具有材料利用率高、生产率高和制造成本低等优点。
3)严格控制收尾尺寸
螺栓螺纹与光杆过渡区是重要的疲劳源之一,严格按收尾尺寸控制过渡区形状是提高该区域疲劳寿命的重要措施。
因此,在设计制造滚丝轮时,必须按标准严格修磨收尾处,且在滚丝时严格控制滚丝位置。
1.4非调质螺栓钢的应用与发展
1.4.1高强度螺栓用钢
新日钢铁开发了从12T到16T不同等级的高强度螺栓钢。
除了用常见的措施来提高抗延迟断裂性能,即减少如磷,硫等杂质元素在晶界中的含量,并通过细化晶粒来分离杂质元素的含量。
同时可以用纳米尺寸的颗粒来诱捕氢从而使氢无害,还可以用高的回火温度来改变显微组织从而获得有效的作用[19]。
1.4.2低碳微合金非调质螺栓钢[20]
低碳微合金以铁素体-珠光体为主要组织的非调质钢用于制造8.8级~10.9级的外螺纹紧固件。
尤其在制造细长杆螺栓、螺柱、U型螺丝和螺杆时,因为不需调质热处理,避免弯曲变形更显优势。
在节约能源、保护环境、降低成本方面有显著效果。
因此,在国内外推广应用较为普遍。
近年来,我国钢铁生产和超常速度的科研开发,在这方面也取得了成果,有良好冷加工性的非调钢材料研制成功,并获得了工业化批量生产应用。
例如马鞍山钢铁股份有限公司,通过技术改造不但拥有了世界上最先进的高速轧机生产线,而且依靠自己的力量拥有了自主的知识产权,开发出了生产非调钢8.8级螺栓。
它拥有世界首创的单线多通道柔性切换系统(马钢与SMS公司共有专利)真正实现了线材750℃低温轧制;
采用闭路控轧、控温技术,在线按程序设定自动控制精轧机组之前、精轧机组与减径定径机组之间、减径定径机组之后的所有水箱的温度闭环控制(十分有利轧钢过程中的形变诱导铁素体相变、配合控制冷却,使线材的组织晶粒度达到12级)。
马钢开发的低碳微合金非调质钢牌号为MFT8。
经过四年多的生产使用,制成的8.8级~10.9级的外螺纹紧固件的力学性能指标能达到国家标准(等同采用国际标准ISO898-1)的要求。
1.4.3高强度螺栓钢的发展动向
1)洁净螺栓钢
降低S含量可提高钢的变形能力,降低P含量可降低钢的变形抗力,同时可减少P、S在晶界的偏聚而减轻晶界脆化。
降低S还可以减少钢中的非金属夹杂物,改善钢的韧塑性。
因此降低钢中的P、S含量不仅可以改善钢的冷镦性能,还可以改善钢的耐延迟断裂性能。
2)微合金非调质钢
用微合金非调质钢制造螺栓可省略螺栓冷拔前的球化退火和螺栓成形后的淬火回火处理,还可减轻螺纹丝扣的脱碳倾向,提高螺栓成品率,因此经济效果十分明显。
1.5本文研究目的与内容
1.5.1研究目的
冷变形和相应时效处理是提高非调质钢螺栓疲劳性能的主要途径,本课题通过对非调质螺栓钢MFT8,进行不同的冷变形及时效处理,通过OM,硬度试验,疲劳测试等方法研究非调质钢螺栓在不同冷变形程度和相应时效处理后疲劳性能所受的影响,有助于寻找最佳的形变强化工艺,对于标准件非调质钢螺栓的生产具有十分重要的现实意义。
1.5.2研究内容
1)对非调质螺栓钢MFT8进行拉拔和时效处理;
2)对原材料,冷变形后,时效后的材料分别进行疲劳性能测试和显微组织观测;
3)根据所得实验结果分析不同冷变形程度和相应时效处理对非调质钢螺栓疲劳性能的影响。
第二章试验材料和方法
本章主要介绍了非调制螺栓钢的研究路线,以及金相试样、疲劳试样的制备;
并
对金相法、洛氏硬度测试法、疲劳性能测试法这三种测试方法进行了说明。
2.1研究路线
图2.1为论文研究的方案和路线设计图。
先对原材料进行拉拔变形,获得两种形变量的材料。
对其中一种形变量的材料进行时效处理,对形变后的材料和时效后的材料进行金相观察分析。
将以上材料加工成疲劳实验的标准试样,通过两种形变量不同的材料的疲劳实验对比形变对耐疲劳性能的影响,通过形变后的材料和时效后的材料对比时效对耐疲劳性能的影响。
组织结构分析
冷变形
原材料
OM:
组织观察
试样制备
分析讨论
力学性能测试
洛氏硬度
图2.1非调质螺栓钢的研究路线
2.2样品制备
2.2.1原材料化学成分
试验采用MFT8冷作强化非调制钢,其化学成分如表2.1,基体组织为铁素体+珠光体,用于制作8.8级螺栓标准件。
表2.1MFT8钢的化学成分
元素
C
Si
Mn
P
S
Nb
Al
质量分数(%)
0.21
0.13
1.37
0.015
0.005
0.04
0.047
原材料直径为9mm,经过冷变形拉拔成直径分别为Φ6.98mm和Φ7.55mm的两种尺寸的材料。
在冷拔、冷镦、搓丝等冷加工过程中,螺栓微观组织中存在着高密度的可动位错和其他缺陷,其组织和使用性能均不稳定,螺栓在服役中容易发生过量的塑性变形,故需要对成型后的螺栓进行时效处理。
时效不仅能够消除冷加工产生的残余应力,防止螺栓镦头部位断裂,而且还可以进一步提高螺栓的强度。
将Φ6.98mm和Φ7.55mm的材料按表2.2进行不同温度下的时效处理。
表2.2时效处理工艺
直径/mm
时效温度/℃
Φ6.98
250
300
350
Φ7.55
2.2.2金相样品制备
金相实验包括,取样、磨制、抛光、腐蚀、照相。
将经过不同处理的材料镶嵌好后,依次用由粗到细的砂纸进行磨样,同一砂纸向同一方向磨样,看不见上一张砂纸磨出的划痕就换下一张细砂纸。
每换砂纸磨样方向变换90°
。
将磨好的试样在抛光机上进行抛光,使用氧化铝抛光剂,直至其抛光面光亮平坦无划痕。
将抛光好的试样用4%的硝酸酒精溶液进行腐蚀,腐蚀5~10s,然后用酒精进行冲洗。
并用吹风机将试样吹干。
最后选取晶界显示明显、合金相清晰、层次感强的区域进行拍照。
2.2.3疲劳试样制备
根据GB3075-82《金属轴向疲劳试验方法》设计加工试样尺寸如图2.2(a),为配合疲劳试验机进行疲劳试验,设计夹具尺寸如图2.2(b)。
图2.2尺寸图:
(a)试样尺寸图;
(b)夹具尺寸图
2.3表征与测试方法
2.3.1显微组织观察
利用金相显微镜(GX51,日本奥林巴斯公司)对原材料、冷变形后及时效后试样进行显微组织观察。
通过金相研究形变和时效对非调质螺栓钢组织合金相的构成、形态、分布及其形成机理,合金组织的均匀性,以及时效处理对材料析出相的形态和分布的影响,比较冷变形前后组织的变化,晶粒大小及形态的改变。
2.3.2硬度测试
利用洛氏硬度机(HR-150A,山东掖县材料试验机厂)对原材料、冷变形以及时效(250℃、300℃、350℃)处理后的试样进行硬度测试。
将试样两面打磨基本平行,在载物台上摆放好后,对试样表面施加150kgf的载荷,保载10秒后卸载,从表盘上读出硬度值。
重复上述操作,在每个试样上取五个点测出硬度值,取平均值即为试样硬度值。
根据国家标准ASTMA370《非奥氏体钢近似硬度换算表(C标尺洛氏硬度与其他硬度值换算)》,如下为摘录的部分表格如表2.3,C标尺洛氏硬度,负荷为150kgf下,压头为金刚石压头。
表2.3非奥氏体钢近似硬度换算表
负荷为150kgf
金刚石压头
近似抗拉强度ksi(MPa)
32
1030
31
995
30
965
29
950
2.3.3疲劳性能测试
利用疲劳试验机(HFP5100)分别测量原材料,冷变形后以及时效处理后的试样的疲劳性能。
材料疲劳寿命是一个特殊的机械性质。
疲劳寿命的主要因素是应力水平。
在不同的应力水平下材料具有不同的疲劳寿命。
在测定了各级应力水平的疲劳寿命时,可以确定一条材料的疲劳寿命曲线,即S-N曲线(应力-寿命曲线)。
疲劳实验是在如图2.3的循环应力下通过图2.4的高频疲劳试验机下进行的。
图2.3的循环应力
图2.4PWM脉冲调制型控制器原理框图
高频疲劳试验机是基于系统共振原理进行工作的,其主机系统采用了多个自由度的力学模型进行优化设计。
它主要由框架、电磁激振器、主振弹簧、测力传感器、试样、及主振系统的配置质量构成机械振动系统,振动由电磁激振器来激励和保持。
当激振器产生的激振力的频率和相位与振动系统的固有频率基本一致时,系统便发生了共振,这时配置质量在共振状态下所产生的惯性力,往复作用在试样上,来完成对试样的疲劳试验。
主机谐振性能设计的好坏直接关系到系统是否能够正常的工作,是关键环节。
测控系统的工作主要有两个作用:
一是准确的测量出试件所受的力值(均值和动态峰值);
二是产生一个幅度可控的与主机共振频率相一致,与振动系统阻尼力相位相反的激振力来抵消阻尼力,以维持系统振动。
电气系统根据不同的控制方式,结构
及组成也不相同。
但具备的共性部分有:
测力传感器及其对应的放大器、峰谷值及均值测量部分、指令设定、比例控制、功率驱动等部分组成。
由于该系统是建立在系统共振原理的基础上工作,所以高频疲劳试验机比其它各种类型的疲劳试验机效率都高,主要体现在工作频率高、能量消耗低。
另外,试验波形好,其波形失真度在动态试验机中最小。
如图2.4为实验用高频疲劳试验机的PWM脉冲调制型控制器。
基本原理是利用负荷传感器的直接反馈信号进行鉴相和积分,使其产生一个相位同步并且斜率与振幅成正比例关系的斜波,该斜波与设定的电平进行比较后产生一个方波信号,这个方波信号的宽度与斜波斜率成正比,方波信号的输出经过隔离电路后,送到开关功率放大器,驱动电磁激励器工作。
它与线性扫频幅度控制型系统的区别是:
作用在激励电磁铁上的信号是脉冲宽度随着设定振幅变化可调的方波信号,其自动鉴相电路自动实现振荡的相位同步,这样消除了以往需操作者繁琐的移相工作,使起振变得十分容易。
已知试样截面直径为3.0mm,根据拟定的应力水平σmax,和应力比R,由此可以计算出最大载荷和最小载荷,见式(2.1),再根据式(2.2)计算平均静载荷和动载荷。
R
=σmin/σmax
Fmax=σmax×
π×
d2/4
Fmin=σmin×
(2.1)
式中
σmax—应力水平(MPa);
σmin——最小应力(MPa);
Fmax—最大载荷(N);
Fmin——最小载荷(N);
—应力比。
Fj=(Fmax+Fmin)/2
Fd=(Fmax-Fmin)/2
(2.2)
Fj
—平均静载荷(N);
Fd
——平均动载荷(N)。