年产750万吨全连铸转炉车间物料热平衡计算DOCWord格式文档下载.docx
《年产750万吨全连铸转炉车间物料热平衡计算DOCWord格式文档下载.docx》由会员分享,可在线阅读,更多相关《年产750万吨全连铸转炉车间物料热平衡计算DOCWord格式文档下载.docx(24页珍藏版)》请在冰豆网上搜索。
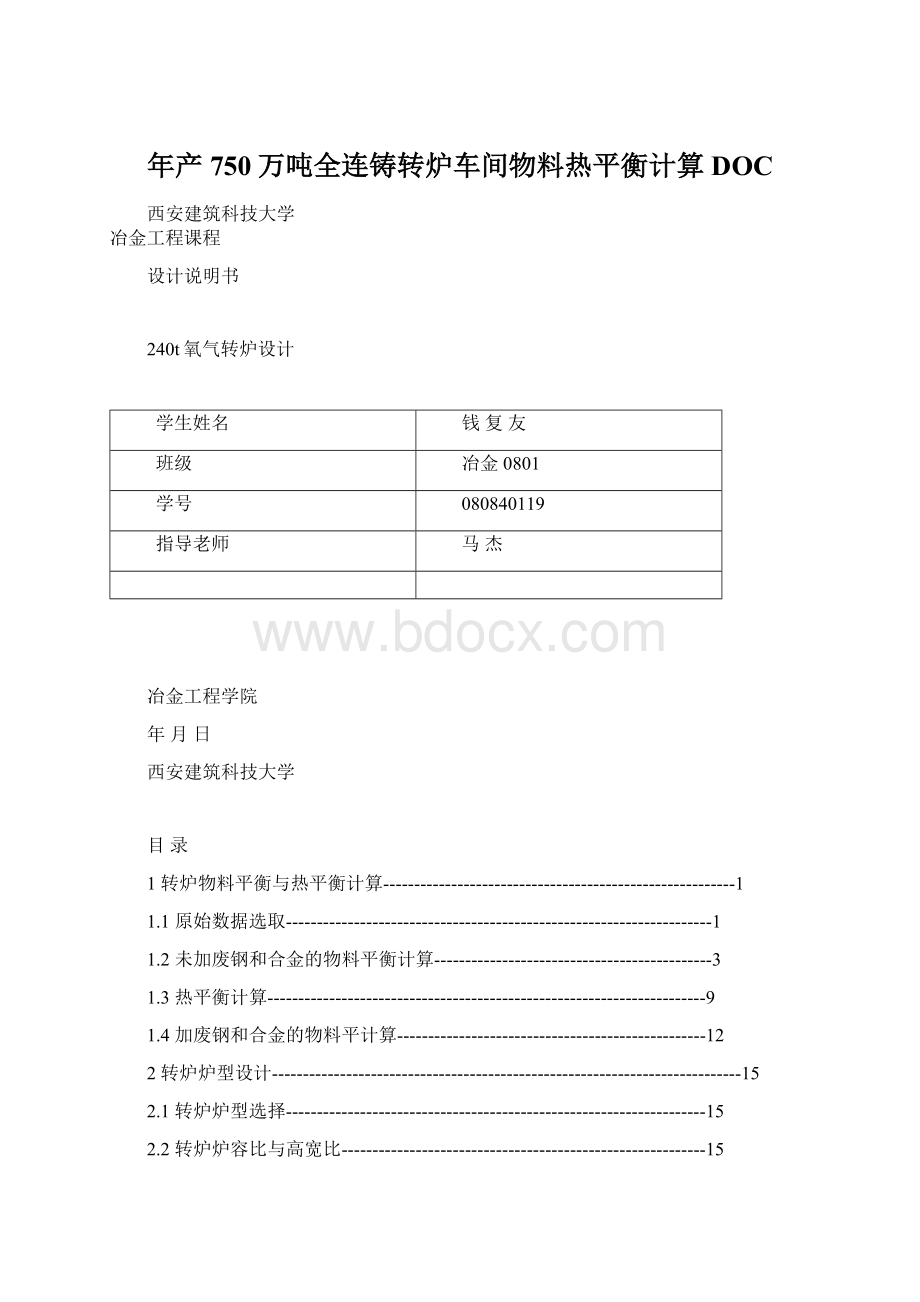
CaO
SO2
MgO
Al2O3
CaF2
FeO
Fe2O3
烧减
H2O
石灰
91.0
2.0
1.5
0.05
3.45
焦炭
29.4
61.8
0.60
81.5
萤石
6.0
0.58
1.78
0.09
89.0
2.00
白云石
55.0
3.0
33.0
1.0
5.0
炉衬
54.0
38.0
表1-3各材料的热容(kJ/kg.K)
项目
固态平均热容
熔化潜热
液(气)态平均热容
生铁
0.745
217.568
0.8368
钢
0.699
271.96
炉渣
209.20
1.247
炉气
1.136
烟尘
1.000
矿石
1.046
表1-4反应热效应(25℃)
元素
反应
反应热/kJ·
kg-1元素
[C]+1/2O2=CO
10950
[C]+O2=CO2
34520
[Si]+O2=SiO2
28314
2[P]+5/2O2=P2O5
18923
[Mn]+1/2O2=MnO
7020
Fe
[Fe]+1/2O2=FeO
5020
[Fe]+3/2O2=Fe2O3
6670
SiO2
SiO2+2CaO=2CaOSiO2
2070
P205
P2O5+4CaO=4CaOP2O5
表1-5铁合金成分(分子)及其回收率(分母)
Al
硅铁
---
73.00/75
0.50/80
2.50/0
0.05/100
0.03/100
23.92/100
锰铁
6.60/90
0.50/75
67.8/80
0.23/100
0.13/100
24.74/100
1.1.2假设条件
名称
参数
终渣碱度
萤石加入量
白云石加入量
喷溅铁损
%CaO/%SiO2=3.5
为铁水量的0.5%
为铁水量的2.5%
铁水量的1%
渣中铁损
烟尘量
为渣量的6%
为铁水量的1.5%(FeO75%,Fe2O320%)
1.1.3冶炼钢种及规格成分
要求冶炼低碳钢,以Q235钢为例,其规格成分为(%):
C0.14~0.22,Si0.12~0.30,Mn0.40~0.65,P≤0.045,S≤0.050
1.2未加废钢和合金的物料平衡计算
物料平衡基本项目:
(1)收入项:
铁水、废钢、溶剂(石灰、萤石、白云石)、氧气、炉衬蚀损、铁合金。
(2)支出项:
钢水、炉渣、烟尘、渣中铁珠、炉气、喷溅。
根据铁水、渣料质量及其冶炼钢种的要求,采用单渣法操作。
为了简化运算,以100kg铁水为计算基础。
1.2.1渣量及其成分计算
(1)铁水中元素氧化量(表1-6)
氧化量=元素在铁水中的含量–元素在钢水中的含量
表1-6铁水中的元素氧化量
元素/%
0.70
0.20
0.10
钢水
氧化量
4.7
0.0176
由表1-6知:
脱磷率=0.09/0.10×
100%=90%;
脱硫率=0.0176/0.044*100%=36%;
钢中残锰量=0.1/0.2×
100%=34%.
(2)各元素耗氧量及氧化产物量(表1-7)
表1-7铁水中元素氧化量、氧化产物量
反应
元素氧化量/kg
耗氧量/kg
氧化产物量/kg
[C]+1/2O2=CO
4.70×
90%=4.23
4.23×
16/12=5.64
28/12=9.87
[C]+O2=CO2
4.7×
10%=0.47
0.47×
32/12=1.253
44/12=1.723
[Si]+O2=SiO2
0.7×
32/28=0.8
60/28=1.5
[Mn]+1/2O2=MnO
0.1×
16/55=0.029
71/55=0.129
0.009×
80/62=0.116
0.09×
142/62=0.206
[S]+O2=SO2
0.0176×
1/3=0.00587
0.00587×
32/32=0.00587
64/32=0.0117
[S]+(CaO)=(CaS)+[O]
2/3=0.0117
0.0117×
(-16)/32=-0.00585
72/32=0.0263
[Fe]+1/2O2=FeO
0.31×
56/72=0.241
16/72=0.069
0.31
[Fe]+3/2O2=Fe2O3
0.166×
56/160=0.0406
48/160=0.0498
0.166
总计
5.8896
7.957
*:
假定炉内气化脱硫1/3;
铁的氧化由表1-13得出。
(3)渣料的加入量
1)萤石加入量:
根据冶金局(部)转炉操作规程,并参考《炼钢工艺学》,取萤石加入量4kg/t,在本设计中,即为:
4=0.4kg,其成分质量计算见表1-9.(质量计算中各成分质量百分数见表1-2)
表1-9萤石加入量及成分
成分
质量/kg
0.4×
89.0%=0.356
0.58%=0.002
6%=0.024
0.55%=0.002
1.78%=0.007
0.09%≈0.000(忽略)
2%=0.008
其中:
2[P]+5/2O2=P2O5
(P2O5)生成量=0.002×
142/62=0.005kg
3)白云石加入量:
为了提高转炉寿命,采用白云石造渣,控制渣中(MgO)含量在6%~8%范围内。
根据已投产转炉的经验,取生白云石30kg/t,在本设计中即为:
30×
0.1=3kg,其成分质量计算见表1-10。
(质量计算中各成分质量百分数见表1-2)
表1-10生白云石加入量及成分
3×
55%=1.65
33%=0.99
3%=0.09
1%=0.03
5%=0.15
烧减是白云石中
分解产生的
气体。
4)炉衬侵蚀量:
转炉炉衬在炉渣作用下,将被侵蚀和冲刷进入渣中,本设计中取铁水量的0.5%,即100×
0.5%=0.5kg,其成分质量计算见表1-11.(质量计算中各成分质量百分数见表1-2)
表1-11炉衬侵蚀量及成分
0.5×
54%=0.27
2%=0.01
38%=0.19
5%=0.025
1%=0.005
炉衬中碳的氧化与金属中氧化生成的CO和CO2比例相同。
即:
[C]+1/2O2=CO:
氧化产物CO量为:
0.025×
90%×
28/12=0.053kg
耗氧量为:
16/12=0.03kg
[C]+O2=CO2:
氧化产物CO2量为:
10%×
44/12=0.009kg
32/44=0.007kg
共消耗氧量=0.03+0.007=0.037kg
5)石灰加入量:
根据铁水成分,取终渣碱度R=3.5,石灰加入量计算如下:
∑(SiO2)=铁水[Si]生成(SiO2)+炉衬、矿石、白云石、萤石带入的(SiO2)
=1.5+0.01+0.0561+0.09+0.024=1.68kg
∑(CaO)=白云石、矿石、炉衬带入(CaO)—铁水、矿石中S消耗CaO量
=1.65+0.01+0.27—0.0117×
56/32–0.001×
56/32=1.908kg
石灰加入量={∑(SiO2)×
R-∑(CaO)}/%CaO有效×
100%
=(1.68×
3.5–1.908)/(91–3.5×
2)×
100%=4.73kg
其成分质量计算见表1-12.(质量计算中各成分质量百分数见表1-2)
表1-12石灰加入量及成分
4.73×
91%=4.3
2%=0.0946
0.05%=0.0024
1.5%=0.071
3.45%=0.16
生成的(CaS)=0.0024×
72/32=0.005kg
6)渣中的铁氧化物:
对于冶炼Q235钢,根据已投产转炉渣中含∑(FeO)量,取(FeO)=5.2%,(Fe2O3)=7%。
7)终渣总量及成分:
根据表1-7~表1-12中的数据,确定终渣总量及成分,见表1-13,若不计(FeO)、(Fe2O3),由表1-13中可得:
CaO+MgO+SiO2+P2O5+MgO+Al2O3+CaF2+CaS
=6.23+1.282+1.775+0.211+0.129+0.189+0.356+0.033=10.205kg
已知(FeO)=5.2%,(Fe2O3)=7%,则其余渣应占渣量总数的87.8%。
故总渣量为10.205/87.8%=11.623kg
由此可知:
(FeO)=11.623×
5.2%=0.604kg,
(Fe2O3)=11.623×
7%=0.814kg。
由于矿石和白云石中带入部分(FeO)和(Fe2O3),其含量参见表1-8和1-10,实际铁氧化物为:
(FeO)=0.604—0.31=0.166kg;
其值列入表1-7.
(Fe2O3)=0.814—0.618—0.03=0.166kg.其值列入表1-7
表1-13终渣总量及成分
氧化产物/kg
石灰/kg
矿石/kg
白云石/kg
炉衬/kg
萤石/kg
总计/kg
%
4.3
1.65
0.27
6.23
53.6
0.095
0.005
0.99
0.19
0.002
1.282
11.03
0.056
0.024
1.775
15.27
P2O5
0.206
0.211
1.82
MnO
0.129
1.11
0.071
0.011
0.09
0.007
0.189
1.63
0.356
3.50
CaS
0.0263
0.033
0.28
0.294
0.604
5.2
0.618
0.814
7
11.623
100
1.2.2冶炼中的吹损计算
根据假设条件,渣中铁珠量为渣量的8%,喷溅损失为铁水量的1%,烟尘损失为铁水量的1.6%。
故可得到:
渣中铁珠量=11.623×
8%=0.93kg
喷溅损失量=100×
0.1%=0.1kg
烟尘铁损失量=100×
1.6%×
(77%×
56/72+20%×
112/160)=1.182kg
元素氧化损失=5.89kg(见表1-7)
吹损总量=0.93+0.1+1.182+5.9=8.102kg
钢水量=100—8.102=91.898kg.
1.2.3氧气消耗量计算
1)元素氧化耗氧=7.957kg(见表1-7);
2)烟尘铁氧化耗氧=100×
1.6%(77%×
16/72+20%×
48/160)=0.37kg;
3)炉衬中碳氧化耗氧=0.037kg(见表1-10下)。
故总耗氧量=7.957+0.37+0.037=8.364kg.换算为标准体积为:
8.364×
22.4/32=5.85m3
即冶炼100kg铁水需要5.85
氧气。
取氧气利用率为80%,则冶炼1t铁水的实际供氧量为:
5.85/80%×
10=73.125m3/t
由于氧气不纯,含有1.5%的氮气,故供氧时带入的氮气为:
8.364×
1.5%=0.125kg
其体积量为:
0.125×
22.4/28=0.1m3,则冶炼1t铁水将会带入1m3的氮气。
1.2.4炉气量及成分计算
炉内产生的炉气由CO、CO2、SO2、H2O、N2和自由O2组成。
CO来源于铁水和炉衬中的碳氧化;
CO2来源于铁水、炉衬中碳氧化,以及白云石和石灰石中的烧减量;
SO2来源于铁水中硫氧化;
H2O来源于矿石和萤石中;
N2来源于供氧时被带入。
自由O2约占炉气总量的0.5%,即以上气体占炉气总量的99.5%,则炉气总量为:
(7.938+1.014+0.004+0.016+0.1)/99.5%=9.118m3
自由O2量为9.118×
0.5%=0.046m3,其质量为0.046×
32/22.4=0.065kg
表1-14炉气量及成分
体积/m3
体积/%
CO
9.87+0.053=9.923
9.923×
22.4/28=7.938
87.06
CO2
1.723+0.009+0.11+0.15=1.992
1.992×
22.4/44=1.014
11.12
0.0117
22.4/64=0.004
0.04
0.005+0.008=0.013
0.013×
22.4/18=0.016
0.17
N2
0.125
1.1
O2
0.065
0.046
0.5
12.13
9.118
1.2.5未加废钢和合金时的物料平衡表
把以上各种物质的总收入和总支出汇总起来,得到未加合金时的物料平衡表1-15.
表1-15未加废钢和合金时的物料平衡表
收入
支出
86.67
91.147
79.11
2.93
2.54
10.163
8.82
2.60
10.498
9.11
0.87
1.60
1.39
0.4
0.35
喷溅
0.43
铁珠
0.813
氧气
7.433
6.44
氮气
0.111
115.374
115.221
计算误差=(收入项—支出项)/收入项×
100%
=(118.119—118.281)/118.119×
100%=-0.137%.
1.3热平衡计算
为了简化运算,取加入炉内的炉料温度均为25℃。
1.3.1热收入
热收入主要是铁水的物理热和元素氧化的化学热。
(1)铁水物理热
铁水凝固温度Tf可用表达式Tf=(1536—∑[%i]△Ti—6)计算,,即
Tf=1536—(100×
4.8+8×
0.7+5×
0.2+30×
0.1+25×
0.044)—6
=1039.3℃
铁水物理热Q物=CsTf+Qf+Cl(T—Tf)
=100×
[0.754×
(1039.3—25)+218+0.837×
(1230—1039.3)]
=114239.8kJ
注:
式中[%i]---铁水中元素含量;
△Ti-----1%的元素使纯铁凝固温度的降低值,参考/王令福《炼钢厂设计原理》表7-20
Cs、Cl----分别为液态、固态的热容量,kJ/kgK,参考表1-3;
Tf、T---分别为冷却剂(生铁)的熔点和熔池温度,K,Tf见表1-3.
(2)铁水中元素氧化放热和成渣热
根据表1-4、表1-7、表1-12数据计算如下:
[C]+1/2O2=CO4.23×
10950=46318.5kJ
[C]+O2=CO20.47×
34520=16224.4kJ
[Si]+O2=SiO20.7×
28314=19819.8kJ
[Mn]+1/2O2=MnO0.1×
7020=702kJ
2[P]+5/2O2=P2O50.09×
18923=1703.07kJ
[Fe]+1/2O2=FeO0.241×
5020=1209.8kJ
[Fe]+3/2O2=Fe2O30.0406×
6670=207.8kJ
SiO2+2CaO=2CaOSiO21.775×
2070=3674.25kJ
P2O5+4CaO=4CaOP2O50.211×
5020=1059.22kJ
总计90981.8kJ
(3)烟尘氧化放热
1.6×
56/72×
5020+20%×
112/160×
6670)=6304.4kJ
(4)炉衬中碳氧化放热
0.5×
5%(90%×
10950+10%×
34520)=332.7kJ
因此,炉内热收入总量为:
114239.8+90981.8+6304.4+332.7=211858.7kJ
1.3.2热支出
(1)钢水物理热
钢水熔点Tf=1536—(65×
0.1+5×
0.1+30×
0.01+25×
0.0264)—6
=1522℃
T=1522+70+8+50=1650℃
钢水物理热
=91.898×
[0.699×
(1522—25)+272+0.837×
(1650—1522)]
=131