模板 塑料模具设计说明书讲解文档格式.docx
《模板 塑料模具设计说明书讲解文档格式.docx》由会员分享,可在线阅读,更多相关《模板 塑料模具设计说明书讲解文档格式.docx(12页珍藏版)》请在冰豆网上搜索。
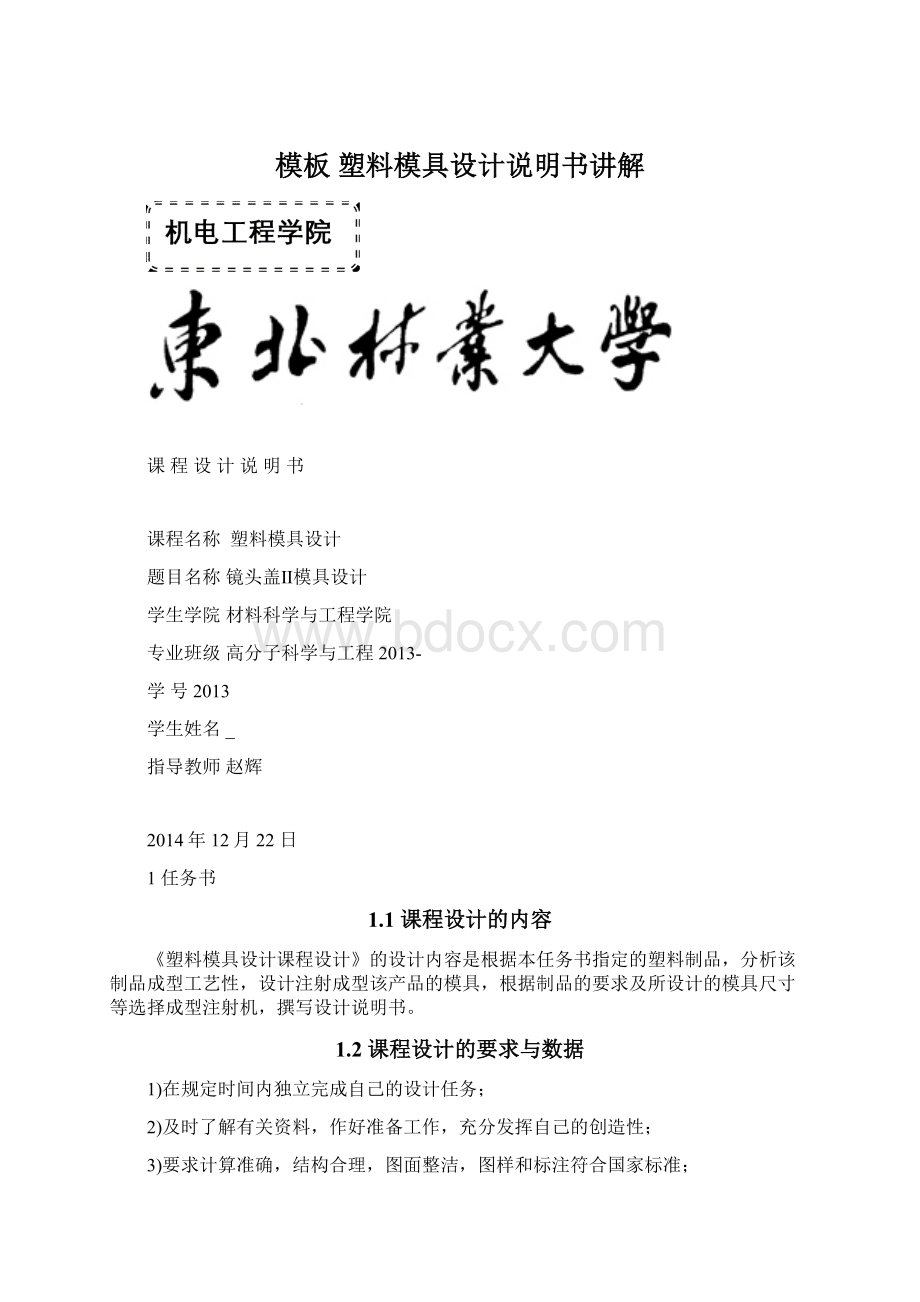
LDPE无毒、无味、无臭,密度为0.910~0.940g/cm3,它是在100~300MPa的高压下,用氧或者有机过氧化物为催化剂聚合而成,也称高压聚乙烯。
低密度聚乙烯在聚乙烯树脂中是质量最轻的品种。
与高密度聚乙烯相比,其结晶度(55%~65%)和软化点(90~100℃)较低;
有良好的柔软性、延伸性、透明性、耐寒性和加工性;
其化学稳定性较好,可耐酸、碱和盐类水溶液;
有良好的电绝缘性和透气性;
吸水性低;
易燃烧。
性质较柔软,具有良好的延伸性、电绝缘性、化学稳定性、加工性能和耐低温性(可耐-70℃)。
不足之处是其机械强度、隔湿性、隔气性和耐溶剂性较差。
分子结构不够规整,结晶度(55%-65%)低,结晶熔点(108-126℃)也较低。
其力学强度低于高密度聚乙烯,防渗系数、耐热性和抗日光老化性差,在日光或高温下易老化分解而变色,导致性能下降,所以低密度聚乙烯在制成塑料卷材时添加了抗氧化剂和紫外线吸收剂来改善其不足之处。
2.3成型特性及条件
(1)LDPE吸水率很小(<
0.01%),而成型水分允许含量可达0.1%左右,因此加工前不必要进行干燥处理。
(2)LDPE熔点不高,料筒温度对熔体流动性的影响不如压力。
由于结晶晶核的熔融需要吸收大量的热量,故料筒温度的选择点应比熔点高,通常要高出十多度。
提高熔体的流动性。
一般为108~204℃。
(3)LDPE的流动性能好,较低压力下既能成型大多数制品。
薄壁件、长流程、窄浇口的制品一般用120MPa;
一般制品用100MPa。
(4)模具温度对LDPE制品的质量有较大的影响,模具温度大概为60~70℃以保证侧壁的易变性问题。
以提高其韧性及尺寸稳定性。
3注射机的选择
3.1注射成型工艺参数
注射剂类型:
柱塞式
干燥:
70~80℃,预干燥1h左右
温度:
料桶后端
140~160℃
料桶中端
料桶前端
170~200℃
喷
嘴
150~170℃
模
具
35~55℃
压力:
注射压力
60~100Mpa
时间:
高压时间
0~5s
保压时间
15~60s
冷却时间
成型周期
40~140s
螺杆转速(r/min):
说明:
料斗干燥
3.2结构工艺性
(1)、零件壁厚为3mm,盖面壁厚1mm,大于塑件的最小壁厚0.6mm注射成型时应不会发生填充不足现象。
(2)、该塑料制件有3个侧孔,需设置侧向抽芯
(3)、考虑塑件的尺寸不是很大,为了提高生产率,采用一模两腔;
并且用侧浇口,用拉料杆使浇注系统冷凝料拉断、顶出脱落,以利于生产自动化。
3.3零件体积及质量估算
(1)、单个塑件体积V=5.51cm3(利用UG软件分析所得),质量m=5.51
0.92=5.06g
(2)两个塑件和浇注系统凝料总体积V总=16.53cm3,总质量m总=15.2g。
3.4初选注射成型机的型号和规格
由公式4-1
(《塑料成型工艺与模具设计》,第107页)可得注射机最大注射量
=20.7cm3。
料筒内应还有比vg/0.3=69cm3大才能保证注塑机不停地正常运行
查表2-40(《塑料模具设计资料》,第48页),选择SX—ZY-125型号的注射机。
SX—ZY-125注射机参数如下:
理论注射量:
125cm3
锁模力:
900kN
螺杆直径:
42mm
公称注射压力:
119Mpa
柱杆距离:
260×
290(mm×
mm)
定位圈尺寸:
直径100mm
喷嘴球半径:
R12mm
模板行程:
300mm
模具最大厚度:
模具最小厚度:
200mm
4模具基本结构设计
4.1模具型腔排列方式的确定
根据材料的尺寸形状及成型性能要求,本模具采用一模两腔,呈对称分布,如下图。
图4.1塑件排样图
4.2模架的选择和A、B板厚度的确定
由图1的塑件形状尺寸、各成型板的厚度要求,并考虑注射机的最大装模厚度,可参考标准模架180×
250A2(《塑料模具设计资料》,第141页)。
确定A、B板厚度:
A板布置了冷去水管和浇注系统主流道,该板厚度主要考虑塑件高度和冷去水管的布置,取A板厚度HA为32mm。
B板其厚度主要考虑嵌入型芯的高度,以及抽芯滑块的高度。
选B板厚度HB为32mm。
4.3模具分型面的选择
经分析,该塑件圆周方向有侧孔,成型时必须采用侧向抽芯。
中间的孔用嵌入式型芯成型。
考虑到加工的方便性和加工的自动化,选择侧浇口。
分型面设计如下图:
图4.2塑件分型面设计图
设计分析:
型芯由组合滑块组成,流道设在定模一侧,分流道采用半圆形流道。
分型面分开,拉料杆将冷凝料拉出留在动模一侧;
开模一定距离后,当推板推出时,推动型芯滑块推出并抽芯,塑件与浇注系统靠自重落下。
4.4注射模浇注系统设计
(1)主流道的设计
根据设计资料查得XS-ZY-125型注射机喷嘴的有关尺寸为:
注射机喷嘴直径d1=4mm;
喷嘴球半径R1=12mm。
根据模具主流道球面半径R=R1+(1~2)mm及小端直径d=d1+(0.5~1)mm,故取主流道球面半径R=14mm;
小(上)端面直径d=5mm。
(《塑料成型工艺与模具设计》 图4浇注系统冷凝料
另外,为了便于将冷凝料从主流道中拔出,将主流道设计成圆锥形,其斜度为:
2°
~4°
。
经换算得主流道大(下)端直径D=8mm。
(2)、冷料穴的设计
冷料穴设置在主流道的末端,采用Z形的冷料穴,便于将浇注系统冷凝料和A板分开。
(3)分流道的设计
分流道的形状及尺寸,应根据制件的体积、壁厚、形状的复杂程度、注射速率、分流道长度、成型工艺条件等因素来确定。
多型腔通常要设置分流道。
为了便于制造、加工,本模具选用截面为半圆形的分流道,只设在定模一侧。
分流道宽度同主流道直径,高度h=4mm,长度L=10mm,其中冷料穴较长,只要考虑了拉料杆位置的设计。
(《塑料成型工艺与模具设计》,第233页)
(4)浇口设计
根据塑件的成型、外观要求及型腔的排列方式,并便于冷凝料的自动脱落,并使塑件外观质量好,在塑件上留下的痕迹小等特点,选用结构简单的侧浇口。
侧浇口与塑件表面水平连接。
高度h=1mm,宽度b=4mm,长度L=2mm。
(《塑料成型工艺与模具设计》,第126页)
(5)定位环及浇口套设计
根据注射机定模板中心孔尺寸,选取定位环直径为100mm(相关尺寸见《塑料模具设计资料》表2-138,第270页);
浇口套公称直径为25mm(相关尺寸见《塑料模具设计资料》表2-118,第257页)。
4.5确定型腔、型芯的结构及固定方式
(1)、型腔结构设计型腔以镶嵌块形式固定在定模上,一模两腔。
(2)型芯结构设计、固定方式
为了便于热处理和节约优质模具钢,型芯采用整体镶块式结构,加工成台阶形状。
型芯如零件图所示。
4.6确定顶出机构类型
顶出机构的结构因塑件的脱模要求的不同而有所变化,但对顶出机构所应达到的基本要求是一致的:
使塑件在顶出过程中不会损坏变形;
保证塑件在开模的过程中留在设置有顶出机构的动模内;
若塑件需留在定模内,则要在定模上设置顶出机构。
其中,一次顶出机构是最常用的顶出机构。
本模具采用组合型芯,斜滑块在抽芯的同时顶出塑件。
4.7确定导向机构(本模具采用导柱导向机构)
(1)导柱导套结构形式为便于加工导柱导套安装孔,获得较好的技术经济效益,使用有肩导柱,导套也使用有肩导套。
(2)导柱的布置为确保动模和定模只按一个方向合模,采用等直径导柱的不对称布置,导柱设在动模一侧。
4.8排气机构
该零件结构简单,且热塑性塑料模具排除的气体量比较少,利用模具分型面之间以及滑块与型芯之间的缝隙排气。
4.9模具冷却系统的确定
因塑料的加热温度对塑件的质量影响较大,温度过高易于分解(分解温度为300℃),成型时要控制模温在50-80℃,具体措施是布置冷却水管。
(1)冷却水管直径8mm。
(2)冷却系统布置见装配图
(3)冷却水嘴采用伸入型腔的形式,以防止液体泄漏。
4.10模具材料
型腔、型芯、镶块等非标准模具零件的材料为Cr12,淬火加低温回火硬度≥55HRC,或45钢,热处理硬度≤240HBS,或P20、优质P20(预硬塑胶模具钢)、S136、S316H(镜面塑胶模具钢)。
各种模板、垫板、固定板、支承块、压紧块、推板、挡块等选材。
材料:
45钢,热处理后硬度≥200HBS;
或材料Q235钢,正火。
5校核计算
5.1注射量的校核
所需的注射机的注射量V=16.53cm³
注射机最大注射量Vz=125cm³
满足要求,初选注射机合适。
5.2锁模力的校核
当高压塑料熔体充满型腔时,会产生很大的压力,使模具沿分型面涨开。
这个涨力,等于塑料制品和浇注系统在分型面上的投影之和乘以型腔内熔体的压力,应小于注塑机的锁模力。
Fz≥kPA=450kN
初选注射机满足要求
5.3模具闭合高度的校核
安装模具的厚度应满足:
<H<。
设计的模具高度H=208mm;
初选的注射机XS-ZY-125,,满足要求,初选合适。
5.4模具的开模行程校核
模具的开模行程应满足:
Sm<Sz
其中:
Sz为注射机的最大开模行程,初选设备参数中可知Sz=300mm,
Sm为模具的开模行程,
Sm=H1+H2+5~10=59+18+5~10=89<Sz=300mm,所以初选的注射机满足要求。
5.5注射机压力的校核
注射机压力应满足:
为注射机的最大注射压力,
为成型塑件所需的注射压力。
该注射产品属于中小型制品,取
=100MPa,由初选的注射机的参数可知,
=119MPa,满足要求。
综合验证,XS-ZY-125注射机完全满足此模具的注射要求。
6模具工作部分设计计算
6.1型腔与型芯的设计:
考虑到该模具结构的特点,在镶块上加工型腔,型腔的结构见零件图。
结合塑件材料性能要求和模具结构及排气等方面,并考虑加工,型芯采用台阶式,采用车床加工,与B板的配合按H7/m6的配合,其结构及相关尺寸见型芯零件图。
6.2成型零部件的尺寸计算:
由《塑料模具设计资料》表2-16查得LDPE的平均收缩率为S=3.3%。
塑件要求的公差等级为7级。
根据对塑件尺寸公差分析,修正系数取1/2,模具的制造公差取δz=Δ/3。
查《塑料模具设计资料》表2-17,第18页,得各个
成型零件各部分尺寸计算如下:
(1)型腔径向尺寸:
AM1+δz=[(1+S)×
As1-xΔ]+Δ/3
=[(1+3.3%)×
56-1/2×
0.92]+0.92/3
=57.4+0.31
AM2+δz=[(1+S)×
52-1/2×
=53.3+0.31
BM1-δz=[(1+S)×
Bs1+xΔ]-Δ/3
48+1/2×
0.80]-0.80/3
=50.00-0.27
(2)型腔成型部分的深度:
HM1+δz=[(1+S)×
Hs1-2/3Δ]+Δ/3
=[(1+3.35%)×
8.5-2/3×
0.40]+0.40/3
=8.5+0.130
HM2+δz=[(1+S)×
Hs2-2/3Δ]+Δ/3
=[(1+3.3%)×
7.5-2/3×
=7.5+0.130
(4)型芯成型部分的高度BM2-δz=[(1+S)×
Bs2+xΔ]-Δ/3
50+1/2×
=52.10-0.27
BM3-δz=[(1+S)×
54+1/2×
0.92]-0.92/3
=56.20-0.31
2+1/2×
0.32]-0.32/3
=2.20-0.11
(4)型芯成型部分的高度:
hM1-δz=[(1+S)×
hs1+2/3Δ]-Δ/3
1.5+2/3×
=1.80-0.11
hM2-δz=[(1+S)×
6.5+2/3×
0.40]-0.40/3
=35.510-0.33
(5)中心距部分:
CM+δz/2=[(1+S)×
Cs]+δz/2
=[(1+3.3%)×
4]+0.12/2
=4.1+0.06
6.3脱模力的计算
分析塑件,得平均壁厚δ=2mm,平均直径d=53mm,则δ/d=0.03≤0.05为薄壁塑件。
由《塑料成型工艺与模具设计》P161公式4-60可得脱模力。
式中:
E——塑料的弹性模量,查《塑料模具设计资料》第15页表2-16可知E=0.8×
10³
MPa
型芯的平均半径r=d/2=26.5mm;
S——塑料平均成型收缩率,S=3.3%;
——塑件对型芯的包容长度,由塑件高度可知
=6.5mm;
k——无因次系数,k₂=1
——塑件与型芯之间的静摩擦系数,常取为0.1~0.2,这里取
=0.15
——是模具型芯的脱模斜度,查《塑料模具设计资料》第19页表2-19可知型芯脱模斜度为20′~45′,现取
=30′
——塑料的泊松比,查资料得知
=0.33
A——塑件型芯在脱模方向上的投影面积,A=2290mm²
代人式4-60得F=545kN
7设计小结
通过对注塑模具的设计,对常用的塑料在成型过程中对模具的工艺要求有了更深一层的理解,掌握了塑料成型模具的结构特点及设计计算方法,对独立设计模具具有了一次新的锻炼。
在设计过程充分利用了各种可以利用的方式,参考各类书籍,同时在反复的思考中不断深化对各种理论知识的理解,在设计的后一阶段充分利用CAD软件就是一例,软件的利用,大大提高了工作效率。
模具CAD技术是模具传统设计方式的革命,大大提高了设计效率,尤其是系列化或类似注射模具设计效率更为提高。
以计算机为手段,模具分析设计软件为工具设计模具。
软件可直接调用数据库中模架尺寸,金属材料数据库及加工参数,通过几何造型及图形变换可得模板及模腔与型芯形状尺寸,迅速完成模具设计。
通过课程设计的又一次锻炼,了解注塑模的整个设计过程,同时充分利用CAD技术进行,并在实际中不断的累积经验,以设计出价廉物美并且实用性更强的模具。
参考文献
[1]张留成等编著.高分子材料基础[M].北京:
化学工业出版社.2005
[2]王昆,何小柏,汪信远主编.机械设计、机械设计基础课程设计.北京:
高等教育出版社,1996(2006重印).
[3]齐晓杰主编.《塑料成型工艺与模具设计》[M].机械工业出版社,2005
[4]左宗义主编.《画法几何与机械制图》/冯开平.-广州:
华南理工大学大学出版社,2001.9(2004.7重印).
[5]自编.《塑料模具设计资料》.广东工业大学,2007.
[6]自编.《塑料成型工艺及模具设计课程设计指导书》.广东工业大学,2007
千万不要删除行尾的分节符,此行不会被打印。
“结论”以前的所有正文内容都要编写在此行之前。