回焊炉设备操作与维护教材720Word格式.docx
《回焊炉设备操作与维护教材720Word格式.docx》由会员分享,可在线阅读,更多相关《回焊炉设备操作与维护教材720Word格式.docx(44页珍藏版)》请在冰豆网上搜索。
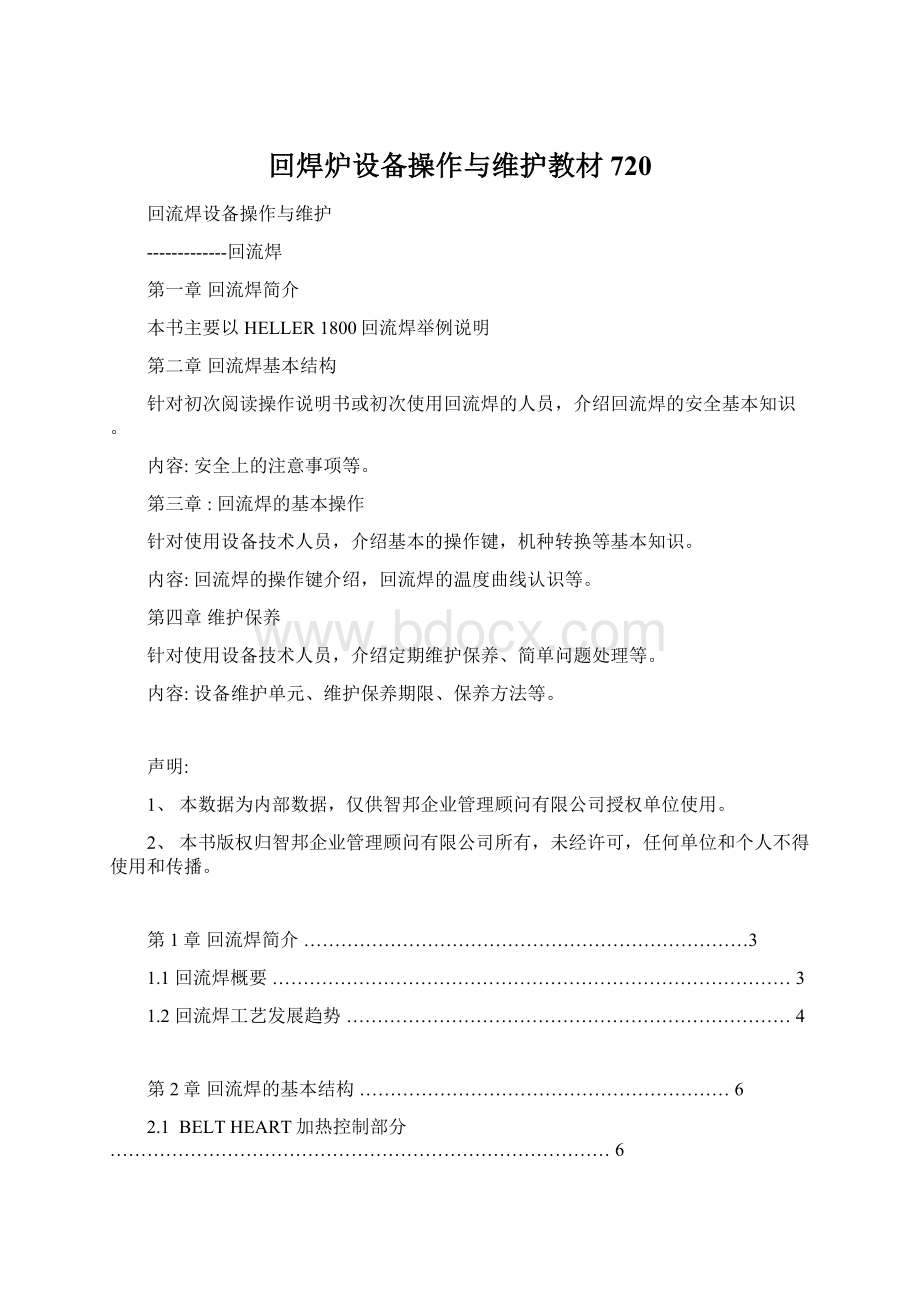
3.2回流焊炉的进板……………………………………………………………………11
3.3回焊炉的温度曲线认识……………………………………………………………11
3.3.1、标准曲线的认识………………………………………………………………12
3.3.2、实际测量的炉温曲线认识……………………………………………………14
3.4HELLER回焊炉基本操作菜单介绍……………………………………………15
3.5回焊炉的机种转换………………………………………………………………20
第4章回流焊的维护与保养……………………………………………………23
4.1保养的目的……………………………………………………………………………23
4.2保养的用品……………………………………………………………………………23
4.3保养计划……………………………………………………………………………23
4.3.1日保养………………………………………………………………………………23
4.3.2月保养………………………………………………………………………………24
4.3.3季保养………………………………………………………………………………25
4.3.4年保养………………………………………………………………………………30
第1章回流焊简介
一、回流焊概要
由于电子产品不断小型化的需要,出现了片状元件,传统的焊接方法已不能适应需要。
首先在混合集成电路组装中采用了回流焊工艺,组装焊接的组件多数为片状电容、片状电感,贴装型晶体管及二极管等。
随着SMT整个技术发展日趋完善,多种贴片组件(SMC)和贴装器件(SMD)的出现,作为贴装技术一部分的回流焊工艺技术及设备也得到相应的发展,其应用日趋广泛,几乎在所有电子产品领域都已得到应用,而回流焊技术,围绕着设备的改进也经历以下发展阶段。
1.热板(Hot-plate)及推板式热板传导回流焊:
这类回流焊炉依靠传送带或推板下的热源加热,通过热传导的方式加热基板上的组件,用于采用陶瓷(Al2O3)基板厚膜电路的单面组装,陶瓷基板上只有贴放在传送带上才能得到足够的热量,其结构简单,价格便宜。
我国的一些厚膜电路厂在80年代初曾引进过此类设备。
2.红外线辐射回流焊:
此类回流焊炉也多为传送带式,但传送带仅起支托、传送基板的作用,其加热方式主要依红外线热源以辐射方式加热,炉膛内的温度比前一种方式均匀,网孔较大,适于对双面组装的基板进行回流焊接加热。
这类回流焊炉可以说是回流焊炉的基本型。
在我国使用的很多,价格也比较便宜。
3.红外线加热风(Hotair)回流焊:
这类回流焊炉是在IR炉的基础上加上热风使炉内温度更均匀,单纯使用红外辐射加热时,人们发现在同样的加热环境内,不同材料及颜色吸收热量是不同的,即
(1)式中Q值是不同的,因而引起的温升ΔT也不同,例如IC等SMD的封装是黑色的酚醛或环氧,而引线是白色的金属,单纯加热时,引线的温度低于其黑色的SMD本体。
加上热风后可使温度更均匀,而克服吸热差异及阴影不良情况,IR+Hotair的回流焊炉在国际上曾使用得很普遍。
4.充氮(N2)回流焊:
随着组装密度的提高,精细间距(Finepitch)组装技术的出现,产生了充氮回流焊工艺和设备,改善了回流焊的质量和成品率,已成为回流焊的发展方向。
氮气回流焊有以下优点:
(1)防止减少氧化
(2)提高焊接润湿力,加快润湿速度
(3)减少锡球的产生,避免桥接,得到很好的焊接质量
得到列好的焊接质量特别重要的是,可以使用更低活性助焊剂的锡膏,同时也能提高焊点的性能,减少基材的变色,但是它的缺点是成本明显的增加,这个增加的成本随氮气的用量而增加,当你需要炉内达到1000ppm含氧量与50ppm含氧量,对氮气的需求是有天壤之别的。
现在的锡膏制造厂商都在致力于开发在较高含氧量的气氛中就能进行良好的焊接的免洗焊膏,这样就可以减少氮气的消耗。
对于中回流焊中引入氮气,必须进行成本收益分析,它的收益包括产品的良率,质量的改善,返工或维修费的降低等等,完整无误的分析往往会揭示氮气引入并没有增加最终成本,相反,我们却能从中受益。
在目前所使用的大多数炉子都是强制热风循环型的,在这种炉子中控制氮气的消耗不是容易的事。
有几种方法来减少氮气的消耗量,减少炉子进出口的开口面积,很重要的一点就是要用隔板,卷帘或类似的装置来阻挡没有用到的那部分进出口的空间,另外一种方式是利用热的氮气层比空气轻且不易混合的原理,在设计炉的时候就使得加热腔比进出口都高,这样加热腔内形成自然氮气层,减少了氮气的补偿量并维护在要求的纯度上。
二、回流焊的发展趋势
最近几年来,随着众多电子产品往小型,轻型,高密度方向发展,特别是手持设备的大量使用,在元器件材料工艺方面都对原有SMT技术提出了重大的挑战,也因此使回焊炉得致到了飞速发展的机会。
IC发展到0.5mm,0.4mm.0.3mm脚距;
BGA已被广泛采用,CSP也崭露头角,并呈现也快速上涨趋势。
物料上免清洗低残留锡膏得到广泛应用。
所有这些都给回流焊工艺提出了新的要求,一个总的趋势就是要求回流焊采用更先进的热传递方式,达到节约能源,均匀温度,适合双面板PCB和新型器件封装方式的焊接要求,并逐步实现对波峰焊的全面代替。
1.双面回流焊
双面PCB已经相当普及,并在逐渐变得复杂起来,它得以如此普及,主要原因是它给设计者提供了极为良好的弹性空间,从而设计出更为小巧,紧凑的低成本的产品。
到今天为止,双面板一般都有通过回流焊来焊接上面(组件面),然后通过波峰焊来焊接下面(引脚面)。
目前的一个趋势倾向于双面回流焊,但是这个工艺制程仍存在一些问题。
大板的底部组件可能会在第二次回流焊过程中掉落,或者底部焊接点的部分熔融而造成焊点的可靠性问题。
已经发现有几种方法来实现双面回流焊:
一种是用胶来粘住第一面组件,那当它被翻过来第二次进入回流焊时组件就会固定在位置上而不会掉落,这个方法很常用,但是需要额外的设备和操作步骤,也就增加了成本。
第二种是应用不同熔点的焊锡合金,在做第一面是用较高熔点的合金而在做第二面时用低熔点的合金,这种方法的问题是低熔点合金选择可能受到最终产品的工作温度的限制,而高熔点的合金则势必要提高回流焊的温度,那就可能会对组件与PCB本身造成损伤。
对于大多数组件,熔接点熔锡表面张力足够抓住底部组件话形成高可靠性的焊点,组件重量与引脚面积之比是用来衡量是否能进行这种成功焊接一个标准,通常在设计时会使用30g/in2这个标准,第三种是在炉子低部吹冷风的方法,这样可以维持PCB底部焊点温度在第二次回流焊中低于熔点。
但是潜在的问题是由于上下面温差的产生,造成内应力产生,需要用有效的手段和过程来消除应力,提高可靠性。
以上这些制程问题都不是很简单的。
但是它们正在被成功解决之中。
勿容置疑,在未来的几年,双面板会断续在数量上和复杂性性上有很大发展。
2.通孔回流焊
通孔回流焊有时也称作分类组件回流焊,正在逐渐兴起。
它可以去除波峰焊环节,而成为PCB混装技术中的一个工艺环节。
一个最大的好处就是可以在发挥表面贴装制造工艺的优点的同时使用通孔插件来得到较好的机械联接强度。
对于较大尺寸的PCB板的平整度不能够使所有表面贴装元器件的引脚都能和焊盘接触,同时,就算引脚和焊盘都能接触上,它所提供的机械强度也往往是不够大的,很容易在产品的使用中脱开而成为故障点。
尽管通孔回流焊有许多好处,但是在实际应用中仍有几个缺点,锡膏量大,这样会增加因助焊剂的挥发冷却而产生对机器污染的程度,需要一个有效的助焊剂残留清除装置。
另外一点是许多连接器并没有设计成可以承受回流焊的温度,早期基于直接红外加热的炉子已不能适用,这种炉子缺少有效的热传递效率来处理一般表面贴装组件与具有复杂几何外观的通孔连接器同在一块PCB上的能力。
只有大容量的具有高的热传递的强制对流炉子,才有可能实现通孔回流,并且也得到实践证明,剩下的问题就是如何保证通孔中的锡膏与组件脚有一个适当的回流焊温度曲线。
随着工艺与组件的改进,通孔回流焊也会越来越多被应用。
3.无铅回流焊
出于对环保的考虑,铅在21世纪将会被严格限用。
虽然电子工业中用铅较极小,不到全部用量1%,但也属于禁用之列,在未来的几年中将会被逐步淘汰。
现在正在开发可靠而又经济的无铅焊料。
目前开发出多种替代品一般都具有比锡铅合金高40C左右的熔点温度,这就意味着回流焊必须在更高的温度下进行。
氮气保护可以部分消附除因温度提高而增加的氧化和对PCB本身的损伤。
不过工业界大概必须经这一个痛苦的学习期来解决所遇到的问题,尽快应用该制程,时间已经所剩不多,现在所使用的许多炉子被设计成高不超出3000C的作业温度,对于无铅焊料或非共溶点焊锡(用于BGA,双面板等)来讲,则需要更高的炉子温度,这些新的制程通常要求回流区中的温度达到3500C~4000C,炉子的设计必须更改以满足这样的要求,机器中的热敏感部件必须被修改,或者要采取措施防止热量向这些部件传递。
4.连续柔性板回流焊
特殊的炉子已经被开发出来处理贴装有SMT组件的连续柔性板。
与普通回流炉最大不同点是这种炉子需要特制的轨道来传递柔性板。
当然,这种炉子也需要能处理连续板的问题。
对于分离的PCB板来讲,炉中的流量与前几段工位的状况无依赖关系,但是对于成卷连续的柔性板,柔性板在整条在线是连续的,线上任何一个特殊问题,停顿就意味着全线必须停顿,这样就产生一个特殊问题,停顿在炉子中的部分会因过热而损坏,因此,这样的炉子必须具备应变随机停顿的能力,继续处理完该段柔性板,并在全线恢复连续运转时回到正常工作状态。
5.垂直烘炉技术
市场对于缩小体积的需求,使CSP(如FLIPCHIP)得到较多应用,这样组件贴装后具有更小的占地面积和更高的信号传递速率。
填充或灌胶被用来加强焊点结构使其能抵受住由于硅片与PCB材料的热膨胀系数不一致而产生的应力,一般常会采用上滴或围填法来把芯片用胶封起来。
许多这样的封装胶都需要很长的固化时间,对于在线生产的炉子来讲是不现实的,通常会使用成批处理的烘炉,但是垂直烘炉已经被证明可以成功地进行固化过程,并且其温度曲线比普通回流炉更为简单,垂直烘炉使用一个PCB传输系统来扮演缓冲区/堆积区的作用,这样就延长了PCB板在一个小占地面积的烘炉中驻留的时间。
以上我们介绍了围绕着设备改进、回流焊装备的发展沿革。
事实上回流焊工艺的发展受到以下两方面的推动:
1.电子产品向短、小、轻、薄化发展。
组装高密度化,SMC/SMD微细间距化,SMC/SMD品种规格系列化,特别是异型组件与机电组件日益增多,这诸多的新发展迫使作为SMT中的重要工艺——回流焊工艺亦面临着挑战,需要不断地发展和完善以提高焊接质量和成品率。
2.人类文明发展到今天,控制三废(废气、废料、废水)保护环境已成为共识。
传统的锡膏中含有助焊剂,其焊接后的残留物需要用氟里昂(CFC)及丙酮等溶剂来清洗,而这些溶剂都会对环境造成污染,为了避免污染相应出现了水清洗工艺和免清洗工艺,还有新型焊锡膏。
第2章回流焊基本结构
一、BELTHEATER控制部分
1:
BELT控制部分
主要通过马达带动链条运行,马达运行的状况通过ECODER来反馈给主机,主机根据Encoder反馈的信息再来控制马达的运行。
2:
HEATER控制部分
加热部分主要是通过发热管来发热升温,温度的高低通过热敏传感器来检测,传感器将信息反馈给主机,主机再根据反馈的信息来控制发热管的加热。
二FLUX过滤系统与冷却系统
(图2)
(图2)中A处为FLUX过滤系统的重要组成部分,它将回焊炉焊接过程中挥发的FLUX集中到FLUX过滤装置,进行分离过滤,再冷却并将其输送到FLUX回收装置,进行集中处理。
(图2)中B处为热风冷却循环系统。
它将回流焊冷却区中的热空气进行冷却再将冷空气输送到回流焊冷却区,达到更好的冷却效果。
三吹风系统
(图3)
(图3)中A处为回流焊的热风马达,它将回流焊炉膛中的热量均匀分散,产生良好的焊接状态,炉膛上方Blower排列,加热模块之间无间隔,使炉膛内的热量更加均匀。
(图3)中B处为回流焊FLUX过滤制冷风扇,它将集中的FLUX进行冷却,利于FLUX的回收与处理
四操作系统
(图4)
(图4)中A处为回流焊的操作键盘,机器的基本操作和机器参数的编写与修改都是通过键盘来实现的。
(图4)中B处为回流焊的显示屏,机器的参数设置及信息等都是通过显示屏来显示出来的。
五轨道系统
(图5)
(图5)为回流焊的轨道,它的功能是将PCB板从进口端输送到出口端,完成整个焊接过程。
HType铝挤型轨道系统依链条形状而制成,不变型,不掉板。
3:
链条来回行程皆在炉膛内,不会影响炉膛内温度变化。
4:
电动调整轨道宽度,速度可调整,MESH及CHAIN均有张力调整机构设计,不松弛,不抖动。
第3章回流焊的基本操作
一操作键的认识
1,操作键盘主要用来机器的操作及参数的调整。
机器所有参数的设定都是通过键盘来实现。
2,显示屏幕主要用来显示机器的运行状态及参数设置。
3,轨道宽度调节速度旋钮主要用来控制轨道宽度调整时的速度,以确保轨道调整时的最佳状态。
4,宽度调节开关只有打开此开关时才能调整轨道的宽度。
5,炉盖上升,下降开关当需要上升或下降回焊炉的炉膛时,须打开此开关。
6,紧急按钮开关只有发生紧急状况时方能按下此开关,当按下此开关时,机器停止运行。
7,复位开关当处理完错误报警或紧急事故,需重新开机时,须将复位开关按灭方能正常运行。
二回流焊炉的进板
回流焊炉的进板注意事项:
1确认回焊炉的温度.链条速度.及其它参数设置是否与该机种的设置一致。
2确认回焊炉进板端轨道与前段流水线的轨道是否对齐,轨道高低是否一致。
3确认PCB板放置的状态是否良好,有无偏斜。
4确认回焊炉的轨道宽度是否合适,PCB板板边与轨道之间大概要有0.5mm-1.0mm的预留量。
5确认回焊炉的轨道运行状况是否良好,有无抖动现象。
三回焊炉的温度曲线认识
1、标准曲线的认识:
回焊炉的温度曲线可分为四段:
升温区恒温区回焊区冷却区
(1)升温区:
升温斜率为:
1—4℃/sec
功能:
把PCB尽快加热到第二个特定目标温度,但升温斜率要控制在适当范围内。
注意事项:
a.过快锡膏中的助焊剂成分急速软化而产生塌陷造成短路及锡球的产生,甚至造成冷焊。
b.过快会产生较大的热冲击,使PCB及组件受损。
c.过慢会会使溶剂达不到预期目的,影响焊接质量和CycleTime。
(2)恒温区:
温度:
120—160℃
时间:
60—120S
a使助焊剂中挥发物成分完全挥发。
b缓和正式加热时的热冲击。
c使正式加热时的温度分布均匀。
d促进助焊剂的活化等。
e如果恒温(T或t)不足,由于其与Reflow区之间温差较大,易产生因流移而引起锡球产生,以及因温度分布不均所导致的墓碑效应和灯芯效益。
f反之,则将引起助焊剂成分的老化以及锡粉的氧化,而导致微小锡球或未熔融的情形发生。
(3)回焊区
升温斜率:
1.5—2.5℃/S
183℃以上时间:
30—90S200℃以上时间:
15—30S
峰值温度:
210—230℃
a回焊区如有不足,则由于无法确保充足的熔融焊锡与Pad及Pin的接触时间,很难得到良好的焊接状态,强度不够以及焊锡的沾湿扩散,同时由于熔融焊锡内部的助焊剂成分和气体无法排出,而易发生空洞(Void)、锡爆。
b峰值温度太高或者200℃以上的时间太长,则可能熔融的焊锡将被再氧化而导致结合程度降低或者有部分零件被烧坏。
(4)冷却区:
降温斜率:
-1—-4℃/S
冷却区基本上应是熔融爬升段的”镜像”(以peak值为对称轴)。
Cooling区应以尽可能快的速度来进行冷却,有利于得到明亮的焊点,并有好的外形和低的接触角度,缓慢冷却会导致PCB的更多分解,从而使焊点灰暗,极端情况下,它能引起沾锡不良和减弱焊点的结合力。
2、实际测量的炉温曲线认识:
ABCDEFGHIJK
A:
代表在基板上固定的7个测试点。
B:
代表每个测试点在经过回焊炉时的最高温度。
C:
代表每个测试点在130-160℃时所用的时间。
D:
代表每个测试点在经过180℃以上时所用的时间。
E:
代表每个测试点在某一时间时的具体温度。
F:
代表每个测试点在升温区的升温斜率。
G:
H:
代表每个测试点在恒温区的斜率。
I:
J:
K:
实际测量的炉温曲线是通过炉温测量仪与测试基板进行实际测量所得,它反映的是基板上固定的某几个测试点在经过回焊炉时的实际温度,它反映的是基板实际受热情况。
四HELLER回焊炉基本操作菜单介绍
(1)温度设定菜单(图1)
(图1)
此操作菜单的主要功能:
1设定回焊炉每个温区的温度。
2实际温度及功率输出均可实时显示,严密监控实际生产状况。
注释:
此处为温度设定处,根据需要自行设定或修改。
B:
此处为回焊炉温区显示处,可以自行指定温区。
(2)密码设定菜单(图2)
(图2)
1设定个人账号及密码
2密码设定分两种模式,严密保护
3生产数据可设定LevelPassword,可分为:
Operator
Engineer
Supervisor
此处设定用户名称
此处设定用户密码
此处设定用户级别
(3)操作权限范围设定菜单(图3)
(图3)
1设定每个级别使用者的操作范围
2一旦层级设定完成,输入名字及密码后,就只能执行限定之修改区域
此处为每个级别操作者所能使用的范围
此处为每个不同级别操作者是否控制
(4)警报设定菜单(图4)
(图4)
1自动监控生产状况
2使用者自行设定警报的类型.信息.时间等相关数据
此处是为警报选择项,选择报警的依据
此处是为警报的类型
此处设定报警的极限
此处设定报警的延时
此处是为警报的信息
F:
此处为警报的输出设定
(5)自动开机与关机的设定菜单(图5)
使用者自行设定生产排程。
使用者自行设定自动启动及自动关机。
此项设定具体的开机日期。
此项设定具体的开机时间。
此项设定自动开机的具体次数。
此项设定每天.每周日.周末等是否采用此项功能。
此项设定自动开机后所使用的生产程序。
五回焊炉的机种转换
(图6)
(一)调出生产机种:
1:
首先点击(图6)A项菜单,会出现logon菜单,点击logon进入输入用户名及密码菜单,输入用户名及密码后方有权限进行机种调出。
其次点击(图6)B项菜单,会出现open菜单,点击open进入文件名菜单,选择与生产机种相对应的文件名,生产机种已调出。
(二)调整轨道宽度:
打开轨道调整开关,选择合适的轨道调整速度,先将轨道调至最宽,再调窄直至合适的宽度。
(三)注意事项:
调出生产机种时,应将该机种的资料与作业指导书中的资料相核对,确保数据正确性。
如数据有误须进行修改时,可直接在(图6)C,D项进行修改,数据修改完后,要退出密码,防止他人改动数据。
轨道的宽度应以板边与轨道边有0.5-1.0mm的预留量为宜。
只有当回焊炉的温度升温稳定后方能进行进板焊接作业。
5:
建议每次机种转换后,温度稳定后必须进行炉温曲线测试,确认正常后方能进
行正常作业。
第4章回流焊维护与保养
一保养目的
1延长机台使用寿命
2保障SMT稳定生产,提高产量.
3保证产品质量.
二保养用品
1.吸尘器,无尘纸或碎布.毛刷,铁刷。
.
2.清洁剂(CP-02),炉膛清洗剂,D-TEK高温链条油,WD-40,煤油,酒精。
3.英制内六角扳手,活动扳手.铲刀,十字螺丝刀,一字螺丝刀.铁皮箱.风速测量仪.万用表.游标卡尺.。
三保养计划
1日保养每班为一个保养周期。
2月保养每隔一个月为一个保养周期。
3季保养每隔三个月为一个保养周期。
4年保养每隔一年为一个保养周期。
日保养
1用无尘纸或碎布蘸少量清洁剂擦拭清洁回焊炉表面灰尘等脏物。
如(图1)
(图1)
2.注意勿将手深入炉膛内。
3.检查自动加油器中高温链条油的存量。
如(图2)
月保养
1.选