精品注射模毕业设计密封罩塑料注射模设计说明书Word文档下载推荐.docx
《精品注射模毕业设计密封罩塑料注射模设计说明书Word文档下载推荐.docx》由会员分享,可在线阅读,更多相关《精品注射模毕业设计密封罩塑料注射模设计说明书Word文档下载推荐.docx(23页珍藏版)》请在冰豆网上搜索。
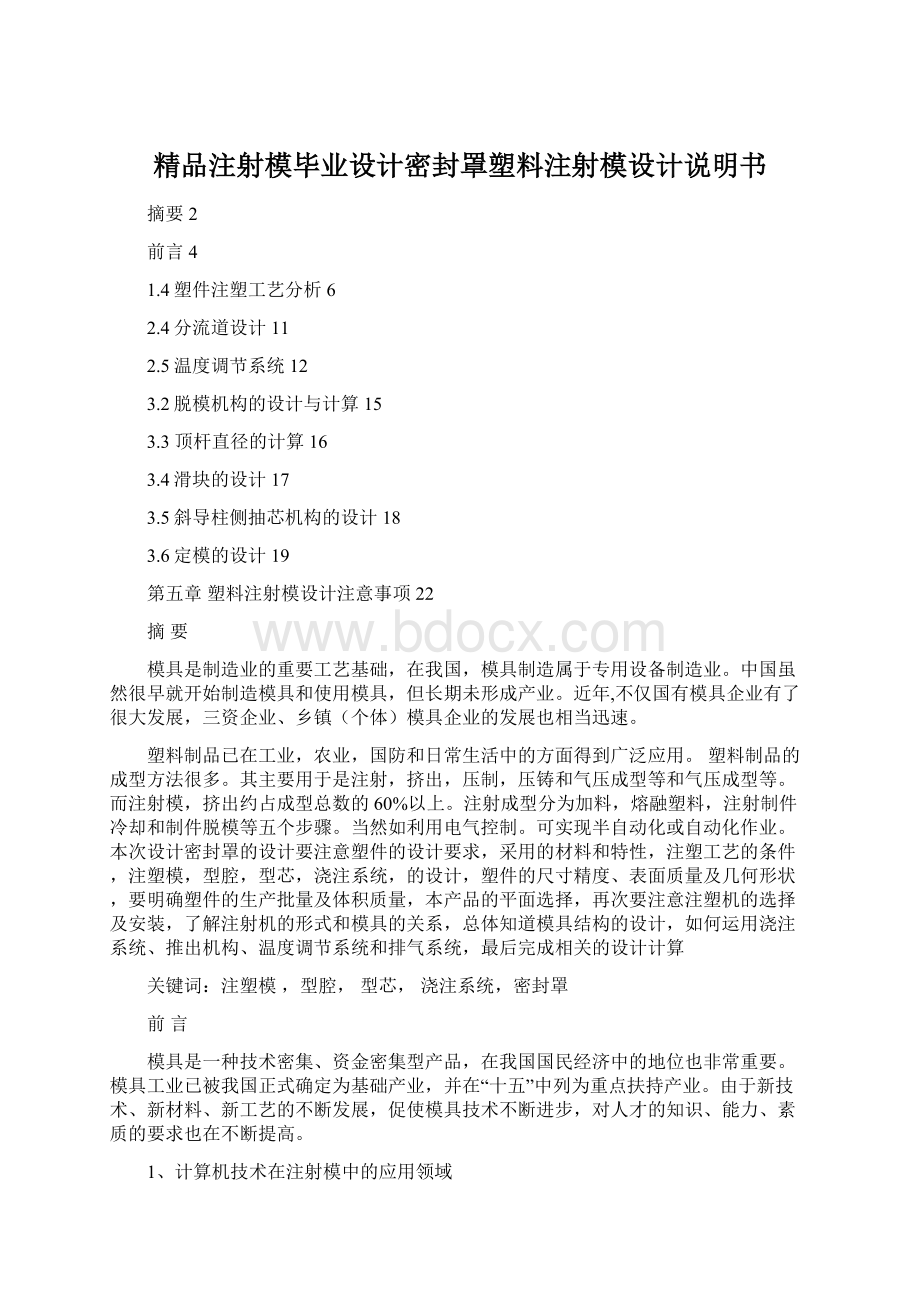
利用有限元分析软件可以对制品的强度、应力等进行分析,改善制品的结构设计。
(3)模具结构设计:
根据塑料制品的形状、精度、大小、工艺要求和生产批量,模具设计软件会提供相应的设计步骤、参数选择.计算公式以及标准模架等,最后给出全套模几结构设计图。
(4)模具开合模运动仿真:
运用CAD技术可对模具开模、合模以及制品被推出的全过程进行仿真,从而检查出模具结构设计的不合理处,并及时更正,以减少修模时间。
(5)注射过程数值分析:
采用CAE方法可以模拟塑料熔体在模腔中的流动与保压过程,其结果对改进模具浇注系统及调整注塑工艺参数有着重要的指导意义,同时还可检验模具的刚度和强度、制品的翘曲性、模壁的冷却过程等。
大专五年学习即将结束,毕业设计是其中最后一个环节,是对以前所学的知识及所掌握的技能的综合运用和检验。
在完成大专两年的课程学习和课程、生产实习,我熟练地掌握了机械制图、机械设计、机械原理等专业基础课和专业课方面的知识,对机械制造、加工的工艺有了一个系统、全面的理解,达到了学习的目的。
对于模具设计这个实践性非常强的设计课题,我们进行了大量的实习。
经过五个月的毕业实习,我对于模具特别是塑料模具的设计步骤有了一个全新的认识,丰富了各种模具的结构和动作过程方面的知识,而对于模具的制造工艺更是实现了零的突破。
在指导老师的协助下和在工厂师傅的讲解下,同时在现场查阅了很多相关资料并亲手拆装了一些典型的模具实体,明确了模具的一般工作原理、制造、加工工艺。
并在图书馆借阅了许多相关手册和书籍,设计中,将充分利用和查阅各种资料,并与同学进行充分讨论,尽最大努力搞好本次毕业设计。
在设计的过程中,将有一定的困难,但有指导老师的悉心指导和自己的努力,相信会完满的完成毕业设计任务。
由于学生水平有限,而且缺乏经验,设计中不妥之处在所难免,肯请各位老师指正。
第一章塑件的工艺分析
1.1塑件原材料分析
查《中国模具设计大典》表8.3-7得材料PP的特如下:
使用性能:
乳白色、无臭、无味、无毒的热塑性塑料。
密度为0.91g/cm3,熔点1650C,燃点5900C,弹性模量3500Mpa,不吸水,导热性低,耐酸碱盐腐蚀,有良好的绝缘性能,化学稳定性和良好的物理机械性能及加工性能.
加工性能:
1耐强酸或氧化性酸。
2流动性好。
3结晶度高。
收缩率不大。
4不吸水。
一般可不用干燥处理。
5磨擦系数低,弹性高。
6宜用螺杆式注塑机成型。
7模具浇注系统以料流阻力要小,进料口小。
物理热性能如下表
参数
密度(g/cm3)
熔点()
收缩率
数值
0.91
165
0.6%-2%
零件二维图1.1
(1)材料:
塑件材料采用ABS,ABS是由丙烯腈、丁二烯和苯乙烯共聚物三种化学单位合成,每种单体都有不同特性;
丙烯腈有高强度,热稳定性及化学稳定性;
丁二烯具有坚韧性,抗冲击特性;
苯乙烯具有易加工,高光洁及高强度。
从形态上看,ABS是非结晶性材料。
三种单体的聚合产生了具有两相的三元共聚物,一个是苯乙烯—丙烯腈的连
续相,另一个是聚丁二烯胶分散相。
这就决定了ABS材料的耐高温性、抗冲击性及易加工性等多种特性。
ABS的流动性中等,较易成形,收缩率为0.4%~~~0.7%,取平均值0.55%,变化范围大,吸湿性强,成形前必须充燥。
特别对于表面要求光泽的塑件要经过长时间的预热干燥。
ABS的表观黏度对剪切速率的依赖性强。
ABS的比热容低,塑化效率高,凝固也快,故成形周期短。
1.2塑件结构、尺寸精度及表面质量分析
1)塑件的结构分析
该零件的总体形状为圆形,结构比较简单。
2)塑件尺寸精度的分析
该零件的重要尺寸,如,30.9±
0.09mm的尺寸精度为3级,次重要尺寸3.75±
0.07mm的尺寸精度为4级,其它尺寸均无公差要求,一般可采用8级精度。
由以上的分析可见,该零件的尺寸精度属中等偏上,对应模具相关零件尺寸的加工可保证。
从塑件的壁厚上来看,壁厚最大处为4.5mm,最小处为2.25mm,壁厚差为2.25mm,较为均匀。
3)表面质量的分析
塑件对表面的精度要求较高,根据经验,ABS可取一般精度为3级精度,表面要光滑。
因此在设计模具时应加以考虑。
1.3塑件的体积重量
计算塑件的重量是为了选用注射机及确定模具型腔数。
计算得塑件的体积:
V=6598mm3
计算塑件的质量:
公式为W=Vρ
根据设计手册查得聚甲基丙烯酸甲酯的密度为ρ=1.18kg/dm3,故塑件的重量为:
W=Vρ
=6598×
1.18×
10-3
=9.776g
从图可知,塑件形状为一壳类塑件,其壁厚均匀,但是形状比较复杂,且需要双面抽芯加斜顶机构,给模具设计制造和加工成形工艺的确定都带来了不小的麻烦。
1.4塑件注塑工艺分析
分析塑胶件的工艺性包括技术和经济两方面,在技术方面,根据产品图纸,只要分析塑胶件的形状特点、尺寸大小、尺寸标注方法、精度要求、表面质量和材料性能等因素,是否符合模塑工艺要求;
在经济方面,主要根据塑胶件的生产批量分析产品成本,阐明采用注射生产可取得的经济效益。
1、塑胶件的形状和尺寸:
塑胶件的形状和尺寸不同,对模塑工艺要求也不同。
2、塑胶件的尺寸精度和外观要求:
塑胶件的尺寸精度和外观要求与模塑工艺方法、模具结构型式及制造精度等有关。
3、生产批量
生产批量的大小,直接影响模具的结构型式,一般大批量生产时,可选用一模多腔来提高生产率;
小批量生产时,可采用单型腔模具等进行生产来降低模具的制造费用。
4、其它方面
在对塑胶件进行工艺分析时,除了考虑上诉因素外,还应分析塑胶件的厚度、塑料成型性能及模塑生产常见的制品缺陷问题对模塑工艺的影响。
第二章拟定成型方案
2.1分型面的选择
分型面是指分开模具取出塑件和浇注系统凝料的可分离的接触表面。
一副模具根据需要可能有一个或两个以上的分型面,分型面可以是垂直于合模方向,也可以与合模方向平行或倾斜,我在这里选用与合模方向倾斜。
1、分型面的形式:
如何确定分型面,需要考虑的因素比较复杂。
由于分型面受到塑件在模具中的成型位置、浇注系统设计、塑件的结构工艺性及精度、嵌件位置形状以及推出方法、模具的制造、排气、操作工艺等多种因素的影响,因此在选择分型面时应综合分析比较,从几种方案中优选出较为合理的方案。
选择分型面时一般应遵循以下几项原则:
a型面应选在塑件外形最大轮廓处。
b便于塑件顺利脱模,尽量使塑件开模时留在动模一边。
c保证塑件的精度要求。
d满足塑件的外观质量要求。
e便于模具加工制造。
f对成型面积的影响。
g对排气效果的影响。
h对侧向抽芯的影响。
综上所述,选择注射模分型面影响的因素很多,总的要求是顺利脱模,保证塑件技术要求,模具结构简单制造容易。
当选定一个分型面方案后,可能会存在某些缺点,再针对存在的问题采取其他措施弥补,以选择接近理想的分型面。
为了便于模具加工制造,应尽是选择平直分型面工易于加工的分型面.但由于本塑件形状复杂,不适合平直分型面,因此改用阶梯式分型分型面开设在底面位置最为合理。
这样选取的塑件的外表面可以在整体的定模型腔内成型,表面
质量好。
图(4)分型面
2、分型面的选择原则:
a)、便于塑件脱模:
Ⅰ、在开模时尽量使塑件留在动模内
Ⅱ、应有利于侧面分型和抽芯
Ⅲ、应合理安排塑件在型腔中的方位;
b)、考虑和保证塑件的外观不遭损坏
c)、尽力保证塑件尺寸的精度要求(如同心度等)
d)、有利于排气
e)、尽量使模具加工方便
2.2确定型腔布置
型腔数的确定有多种方法,本题采用注射机的注射量来确定它的数目。
其公式如下:
n2=(G-C)/V
式中:
G——注射机的公称注射量/cm3
V——单个制品的体积/cm3
C——浇道和浇口的总体积/cm3
生产中每次实际注射量应为公称注射量G的(0.75-0.45)倍,现取0.6G进行计算。
每件制品所需浇注系统的体积为制品体积的(0.2-1)倍,现取C=0.6V进行计算。
n2=0.6G/1.6V=0.375G/V=(0.375×
60)/90132=1.46
由以上的计算可知,可采用一模一腔的模具结构。
确定型腔的排列方式型腔的数量是由于制件形状复杂,两侧需斜倒柱侧抽芯,为“一出一”即一模一位,主要考虑了本产品的生产数量和注射机型号。
模具成型零件和抽芯结构以及出模方式的设计,又考虑到单分型面的成本相对较低,结构也较为简单,故初步设计为单分型面环行式浇口。
由于塑件形状复杂,重量一般,采用一模一位
2.3浇注系统的设计
浇注系统设计包括主流道的选择、分流道截面形状及尺寸的确定、浇口的位置的选择、浇口形式及浇口截面尺寸的确定。
2.3.1主流道的设计
主流道是一端与注射机喷嘴相接触,另一端与分流道相连的一段带有锥度的流动通道。
主流道小端尺寸为3mm。
主流道的半锥角α通常为1°
-2°
过大的锥角会产生湍流或涡流,卷入空气,过小的锥角使凝料脱模困难,还会使充模时熔体的流动阻力过大,此处的锥角选用2°
。
经换算得主流道大端直径D=φ8.5mm,为使熔料顺利进入分流道,可在主流道出料端设计半径r=5mm的圆弧过渡。
主流道的长度L一般控制在60mm之内,可取L=55mm。
主流道衬套的固定
因为采用的有托唧咀,所以用定位圈配合固定在模具的面板上。
定位圈也是标准件,外径为Φ100mm,内径Φ70mm。
2.3.2浇口的设计
浇口指流道末端与型腔之间的细小通道。
〈1〉作用:
a、使熔体快速进入型腔,按顺序填充。
b、冷却材料作用
〈2〉浇口参数:
a、形状一般为圆形或矩形。
b、面积与分流道比为0.03~0.09。
c、长度一般:
0.5~2.0mm。
〈3〉小浇口的优点:
a、改变塑料非牛顿流体的表观粘度,增剪切速率。
b、小浇口改变流体流速,产生热量,温度升高。
c、易冻结,防止型腔内熔体的倒流。
d、便于塑件与浇注系统的分高。
根据浇口的成型要求及型腔的排列方式,选轮辐浇口较为合适。
轮辐式浇口是在环形浇口基础上改进而成,由原来的圆周进料改为数小段圆弧进料,容易去除浇口,因为该制件无表面质量的特殊要求,又是中小型制品的一模一腔结构,所以可以采用轮辐浇口。
在轮辐浇口的三个尺寸中,以浇口的深度h最为重要。
它控制着浇口内熔体的凝固时间和型腔内熔体的补缩程度。
浇口宽度W的大小对熔体的体积流量的直接的影响,浇口长度L在结构强度允许的条件下以短为好,一般选L=0.5-0.75mm。
通常要考虑以下几项原则:
a尽量缩短流动距离。
b浇口应开设在塑件壁厚最大处。
c必须尽量减少熔接痕。
d应有利于型腔中气体排出。
e考虑分子定向影响。
f避免产生喷射和蠕动。
g浇口处避免弯曲和受冲击载荷。
h注意对外观质量的影响。
确定浇口深度和宽度的经验公式如下:
h=nt①
W=nA1/2/30②
式中:
h——侧浇口深度(mm)中小型制品常用h=0.5-2mm,约为制品最大壁厚的1/3-2/3, 取1.5mm
t——制品的壁厚(mm)3.38mm
n——塑料材料的系数 查表得 0.8
W——浇口的宽度(mm)
A——型腔的表面积(mm2)计算得2940mm2
将以上各数据代入公式得:
h=1.5mm,W=1.5mm,L取0.5mm。
计算
后所得的侧浇口截面尺寸可用r=6q/(Wh2)≥104s-1作为初步校验。
制品的体积V=9.132cm3,设定充模时间为1s,于是:
q=9.132/1=9132mm3/s
r=6q/Wh2=(6×
9132)/(1.5×
1.52)=1.6×
104>104s-1
图:
浇口
2.4分流道设计
为了便于加工及凝料脱模,分流道大多设置在分型面上,分流道截面形状一般为圆形梯形U形半圆形及矩形等,工程设计中常采用梯形截面加工工艺性好,且塑料熔体的热量散失流动阻力均不大,一般采用下面的经验公式可确定其截面尺寸:
(式1)
(式2)
式中B―梯形大底边的宽度(mm)
m―塑件的重量(g)
L―分流道的长度(mm)
H―梯形的高度(mm)
梯形的侧面斜角a常取5°
-15°
,在应用式(式1)时应注意它的适用范围,即塑件厚度在3.2mm以下,重量小于200g,且计算结果在3.2-9.5mm范围内才合理。
2.5温度调节系统
模具温度调节的重要性
1)模具温度极其调节系统对塑件质量的影响表现为以下几个方面:
(1),塑件的力学性能。
对于结晶型塑料,结晶度越高,塑件的应力开裂的倾向越大,从减少应力开裂的角度出发,降低模温是有利的。
但对于聚碳酸酯一类的高黏度无定性塑料,其应力开裂的倾向与塑件的内应力的大小有关,提高模温,有助于减少塑件中的内应力,从而减少了有于应力而硬气开裂的可能。
(2),塑件的表面质量。
提高模具的温度可以改善塑件的表面光洁;
过低的模温会使塑件的轮廓不清晰,并产生明显的熔和纹。
(3),模具温度及其调节系统对生产效率的影响据实验表明,塑料熔体在注射模中稳定注射时,其温度由200℃降到60℃,其释放热量中的5﹪是以辐射,对流的方式散发到大气中,其余95﹪的热量都是由冷却介质(一般是水)带走,模具的冷却时间一般约占整个注射循环周期的2/3,可见注射的生产效率主要取决于模具的冷却时间,也可以从下式来理解模具温度与生产效率的关系:
Q=A1h1△at2
式中Q——塑料传给模具的热量(J);
A1——模具型腔的表面积(㎡);
h1——塑料对模具材料的传热系数(W/㎡.k);
△a——模具型腔内塑料与模具型腔表壁的温度差(℃);
t2——塑件在模具内停留的时间(min)。
如果塑料种类、模具设计和成型工艺已定,那么Q,A1及h1也就确定了,则:
t2∝1/△a
由上式可知,塑料在模具内停留的时间t2与模具型腔内塑料与模具型腔表壁的温度差△a成反比,如果要提高生产效率的话,即减少t2的值,必须在工艺条件允许下增大△a的值。
然而,模具型腔接受塑料熔体传给的热量,会逐渐升温△a必然减小,如果模具没有调节系统的话,必然靠增加塑料在模具中停留的时间来完成换热,因此除去薄壁小型件的注射可利用自然冷却以为,大部分的塑件的模具都要设置冷却系统,进行人工冷却,以增大△a的值,提高生产效率。
第三章模具成型零件的设计与计算
模具中决定塑件几何形状和尺寸的零件称为成型零件,包括型腔、型芯、动定模板,动定模镶块、滑块,斜顶等。
成型零件工作时,直接与塑料接触,塑料熔体的高压、料流的冲刷,脱模时与塑件间还发生摩擦。
因此,成型零件要求有正确的几何形状,较高的尺寸精度和较低的表面粗糙度,此外,成型零件还要求结构合理,有较高的强度、刚度及较好的耐磨性能。
设计成型零件时,应根据塑料的特性和塑件的结构及使用要求,确定型腔的总体结构,选择分型面和浇口位置,确定脱模方式、排气部位等,然后根据成型零件的加工、热处理、装配等要求进行成型零件结构设计,计算成型零件的工作尺寸,对关键的成型零件进行强度和刚度校核
3.1确定模具结构形式及外形尺寸
模具结构为单分型面注射模,如图所示。
模具的开模距离应大于70mm,方便取出塑件和浇口。
选择模架为国标中小型模架(GB/T12556.1-1990),选择基本型的A2型,模具的外形尺寸160×
160mm,其各板料厚度如下图所示:
本设计中零件工作尺寸的计算均采用平均尺寸、平均收缩率、平均制造公差和平均磨损量来进行计算,已给出这ABS的成型收缩率为0.005,模具的制造公差取z=Δ/3。
型腔型芯工作尺寸的计算
类别
塑件尺寸
计算公式
模具尺寸
型
腔
计
算
型腔板
φ35.250-1.0
Lm=(Ls+Ls.Scp%-3/4Δ)0+δz
φ34.680+0.33
R7.5±
0.64
R7.060+0.21
19.2±
0.44
Hm=(Hs+Hs.Scp%-2/3Δ)0+δz
18.710+0.15
推件板
φ30.9±
0.09
φ30.880+0.06
芯
主型芯
φ26.250+0.96
Lm=(Ls+Ls.Scp%+3/4Δ)0-δz
φ27.100-0.32
R2.2±
0.24
R2.620-0.16
17.2±
0.48
Hm=(Hs+Hs.Scp%+2/3Δ)0-δz
17.980-0.32
小型芯
φ3.75±
0.07
φ3.870-0.05
7.5±
0.32
8.050-0.11
型腔侧壁厚度和底板厚度的计算
1)型腔侧壁厚度的计算
根据圆形整体式型腔的侧壁厚度计算公式:
S≥0.90[Pr4/E(δ)]1/3①
S——侧壁厚度(mm)
P——型腔压力(Mpa)40
r——型腔半径(mm)17.625
E——模具材料的弹性模量(MPa)2.1×
105
[δ]——刚度条件,即允许变形量(mm)0.05
将以上各数代入式得:
S≥1.15[(40×
19.84)/(2.1×
105×
0.05)]1/3
=9.62mm
2)底板厚度的计算公式如下:
hs≥0.56(Ph4/E[δ])1/3
将各参数代入式中得:
hs≥4.68mm
型腔的厚度h腔hc+h=4.68+19.8=24.48mm
S可取10mms腔取32mm
根据计算,型腔侧壁厚度应大于9.62mm,而型腔的直径为35-25mm。
根据浇注系统的条件及制件的大小,初选标准模架,依据《塑料注射模中小型模架及技术条件》(GB/T12556-90),根据模板的参数确定导柱、导套、垫块等的有关尺寸。
3.2脱模机构的设计与计算
使塑件从模具上脱出来的机构称脱模机构或称顶出机构脱模机构的动作方向与模具的开模方向是一致的。
要求脱模时塑件不变形,不损坏,顶件位置位于制件不明显处。
〈一〉脱模力的计算
①(脱模)塑件在模具中冷却定型时,由于体积收缩,产生包紧力。
②不带通孔壳体类塑件,脱模时要克服大气压力。
③机构本身运动的磨擦阻力。
④塑件与模具之间的粘附力。
初始脱模力,开始脱模进的瞬间防要克服的阻力。
相继脱模力,后面防需的脱模力,比初始脱模力小,防止计算脱模力时,一般计算初始脱模力。
a.脱模力与塑件壁厚,型芯长度,垂直于脱模方向塑件的投影面积有关,各项值越大,则脱模力越大。
b.塑件收缩率,弹性模量E越大,脱模力越大。
c.塑件与芯子磨擦力俞大,则脱模阻力俞大。
d.排除大气压力和塑件对型芯的粘附等因素,则型芯斜角大到,塑件则自动脱落。
〈二〉脱模机构的形式
1.顶杆脱模机构
一般用于脱模力小的腔类塑件:
1顶杆的导向配合部分较短。
2筋部由于局部脱模力大,需加筋位。
3顶出盘式的顶出。
④顶杆材料:
45钢,T8或T10钢,HRC50以上。
4与顶杆孔的配合间隙配合。
⑥顶杆的固定形式。
⑦顶杆的结构形式。
2.点浇口自动切断和脱落机构
注射成型模具零部件的设计
塑件的推出形式,有机械推出、液压推出、气动推出三大类,常用为机械推出。
它包括推杆推出、推管推出、推板推出、推块推出及复合推出,推杆推出是最广泛的应用形式。
制品推出是注射成型过程中最后一个环节,推出质量的好坏将最后决定制品的质量,因此制品的推出是不可忽视的环节。
因为此制品比不大且壁薄又加上有内抽机构,相对来说推出机构设计就比较重要,如果没做好容易产生毛边和拉裂。
那么对后加工来说会有一定难度,所以我的设计从整体全面的考虑推出机构的设计,所以选择斜顶推出机构。
斜顶如图10
图(10)
3.3顶杆直径的计算
推杆推顶推件板时应有足够的稳定性,其受力状态可简化为一端固定、一端铰支的压杆稳定性模型,根据压杆稳定公式推导推杆直径计算式为:
d=K(l2Qe/nE)1/4 ①
推杆直径确定后,还应用下式进行强度校核:
σc=4Qe/nπd2≤σs ②
式中:
d——推杆直径(mm)
K——安全系数,通常取K=1.5-2 2
l——推杆的长度(mm)102
Qe——脱模力(N) 1372.45
E——推杆材料的弹性模量(MPa) 2.1×
n——推杆根数4
σc——推杆所受的压应力(MPa)
σs——推杆材料的屈服点(MPa)360
将以上各数据代入①式得:
d=4