常见腐蚀形态特征及防护对策分析Word下载.docx
《常见腐蚀形态特征及防护对策分析Word下载.docx》由会员分享,可在线阅读,更多相关《常见腐蚀形态特征及防护对策分析Word下载.docx(15页珍藏版)》请在冰豆网上搜索。
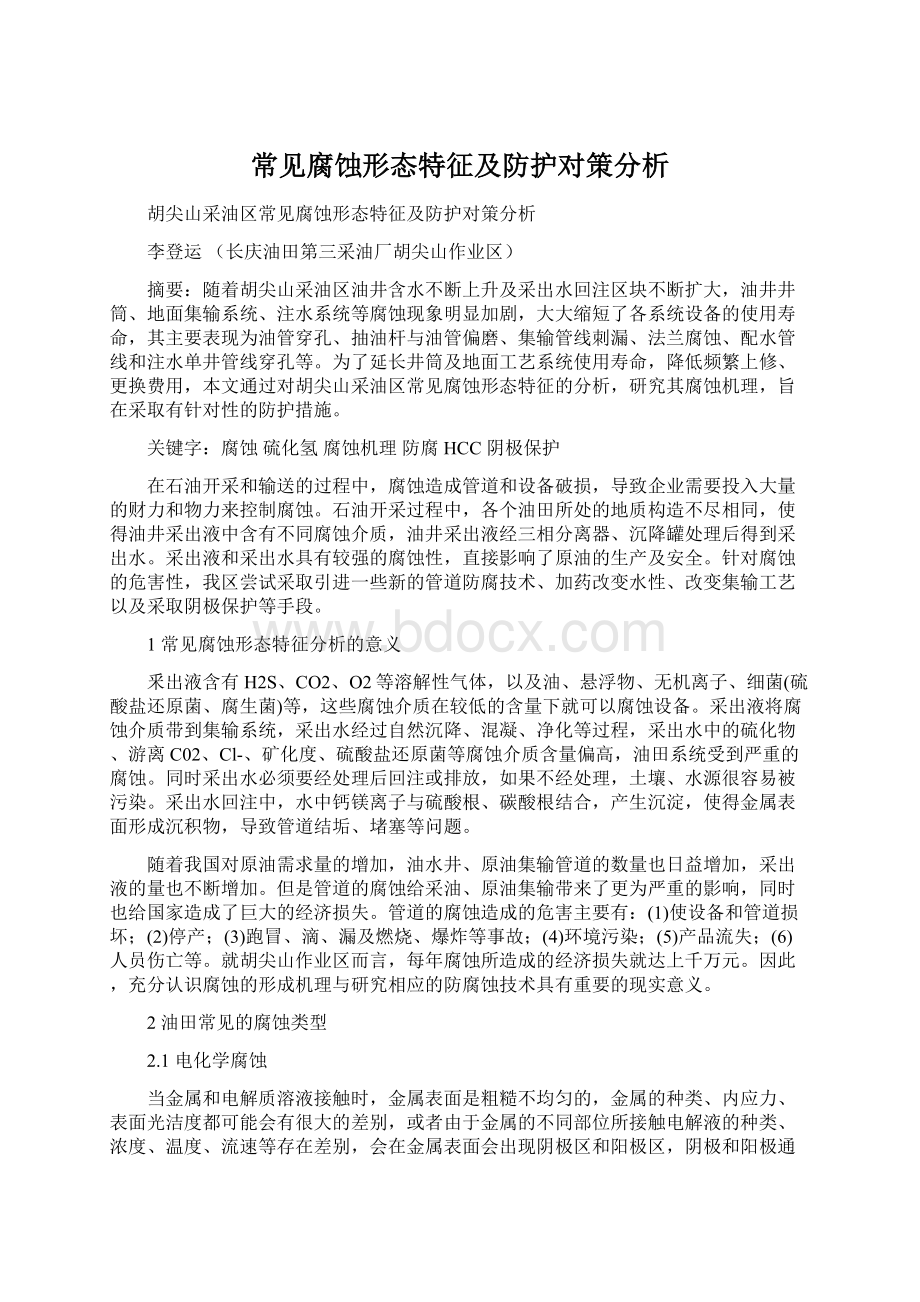
(4)环境污染;
(5)产品流失;
(6)人员伤亡等。
就胡尖山作业区而言,每年腐蚀所造成的经济损失就达上千万元。
因此,充分认识腐蚀的形成机理与研究相应的防腐蚀技术具有重要的现实意义。
2油田常见的腐蚀类型
2.1电化学腐蚀
当金属和电解质溶液接触时,金属表面是粗糙不均匀的,金属的种类、内应力、表面光洁度都可能会有很大的差别,或者由于金属的不同部位所接触电解液的种类、浓度、温度、流速等存在差别,会在金属表面会出现阴极区和阳极区,阴极和阳极通过金属本身互相闭合而形成腐蚀电池。
金属电化学腐蚀就是通过阳极和阴极反应过程进行的。
2.2盐类腐蚀
Ca2+、Mg2+离子会增大油田采出水的矿化度,使局部腐蚀更为严重。
它们也能够沉积在金属表面形成良好的覆盖层,能起到保护金属的作用;
但如果覆盖层分布不均匀,覆盖部分与未覆盖部分之间又会形成浓差电池,并将产生点蚀。
油田开采时带有少量油田水,经过脱水处理仍有少量水存在于原油中。
这些水中含有盐类,主要是氯化钠,还有氯化镁、氯化钙以及少量的硫酸盐。
这些氯化物受热水解生成腐蚀性很强的盐酸,使介质中存在大量的Cl-。
腐蚀介质中的Cl-能够吸附在保护膜上并与金属表面的阳离子生成氯化物,使金属设备产生点蚀,当介质中含有溶解氧时会加剧点蚀,在金属设备表面造成穿孔。
若介质中Cl-的浓度较大,Cl-可直接穿透保护膜,加剧局部腐蚀。
Cl-对碳钢和低合金钢的腐蚀最为严重。
2.3溶解氧腐蚀
氧腐蚀是最常见的腐蚀,只要有空气和水存在就会发生这种腐蚀。
在中性及弱碱性油田注水系统中,氧去极化是这类腐蚀的主要原因。
电子从阳极流向阴极,使Fe失去电子,油田水中溶解氧获得电子,从而生成Fe(OH)2,Fe(OH)2脱水,被氧化成Fe(OH)3,脱水后即形成铁锈(Fe2O3·
xH2O)。
如果此反应氧被消耗且Fe(OH)3附在金属表面形成一层膜会抑制腐蚀作用。
但是由于油田水中的氧来自大气,空气源确保了腐蚀反应长期持续发生。
在酸性条件下,油田注水系统中碳钢的腐蚀过程反应原理如下:
8H2O→8OH-+8H+
4Fe→4Fe2++8e-
8H++e-→8H吸附
Fe2++8H2O→Fe(OH)2+8H吸附
氧在油气田生产中还常生成氧浓差电池,其中氧浓度高的部分是阴极,浓度低的是阳极。
碳钢在水与空气的界面上发生的腐蚀可归因于氧浓差腐蚀。
由于在界面处水可从空气中充分得到氧,而水的下层氧的浓度较低且得不到及时补充,因而产生氧的浓度差,形成氧浓差腐蚀。
2.4二氧化碳腐蚀
二氧化碳作为油田采出液中的伴生气溶于水形成碳酸,使溶液中存在氢离子pH显酸性,发生电化学腐蚀。
油气井中的二氧化碳对碳钢的腐蚀主要是局部腐蚀,严重的局部腐蚀经常使设备遭到破坏。
油田中含有的Ca2+、Mg2+等金属离子可以在二氧化碳溶液中生成碳酸盐垢附着在碳钢表面。
碳钢在二氧化碳水溶液中产生腐蚀后会在碳钢表面生成腐蚀产物,即少量松软且不致密的FeCO3膜。
所发生的反应主要有:
Fe2++CO32-→FeCO3
Fe2++2HCO3-→Fe(HCO3)2
Fe(HCO3)2→FeCO3+CO2+H2O
腐蚀产物、结垢产物和金属表面不同的生成物膜在钢铁表面不同区域的覆盖程度和均匀程度是不同的,金属不同区域之间存在实际腐蚀电位差,形成了腐蚀电偶,使得电位较负的金属区域加速腐蚀,造成局部腐蚀。
该研究结论在实际的油气田生产中已经得到证实。
这种局部腐蚀由于阳极面积小,往往穿孔的速度很快。
影响二氧化碳腐蚀的主要因素是温度、CO2分压、pH值、流速、介质组成、以及管材材质。
2.5硫化氢腐蚀
油田采出水中的H2S一部分来自于油层及伴生气中,另一部分是原油和水中的含硫物质通过微生物的作用转化而来的。
当油田水中既有溶解的硫化氢又有溶解氧时,腐蚀会更加的严重。
在酸性油气田的腐蚀中,H2S作为阳极过程的催化剂促进碳钢表面铁离子的溶解,碳钢的阳极产生的亚铁离子与腐蚀介质中的硫离子生成FeS膜覆盖在碳钢设备的表面。
当生成的这层膜致密时,有抑制腐蚀的作用;
当这层膜不致密时就极其容易破裂,FeS膜成为腐蚀电池的阴极,此时会出现大阴极和小阳极的情况,加速了阳极碳钢表面铁离子的溶解,易发生点蚀,使碳钢在低应力状态下也会发生晶间应力腐蚀开裂产生较大裂纹,甚至造成断裂。
H2S腐蚀的影响因素主要有硫化氢的浓度、pH值、温度、流速、介质组成以及暴露时间等。
2.6微生物腐蚀
油田生产系统中存在着各种各样的微生物群体,它们对油田设备和管线腐蚀造成的损失是非常巨大的,其中最常见的细菌是硫酸盐还原菌(SRB),它在特定的条件下会参与金属的腐蚀过程,是对油田生产影响最大的微生物。
硫酸盐还原菌是一种在缺氧条件下以有机物为养料的特殊微生物,它能在pH值为5~10,温度为5~100℃的环境中生长。
油田回注水水质适合硫酸盐还原菌的生长,使其大量繁殖。
硫酸盐还原菌含有一种氢化酶,氢化酶能使硫酸盐还原菌利用在金属表面阴极区产生的氢把SO42-还原成H2S,从而减少了阴极上氢的极化,使阴极反应加快。
反应生成的S2-与阳极的Fe2+反应生成FeS,加速了金属的腐蚀。
硫酸盐还原菌常造成油套管的局部腐蚀甚至出现穿孔。
3胡尖山作业区腐蚀现状调查
3.1油井的腐蚀现状
胡尖山采油作业区采出液主要来自侏罗系和三叠系,矿化度高,呈中性偏弱碱性。
所管辖区油井开井240余口,2013年1月至今,通过对躺井的腐蚀情况的调查统计,由于腐蚀引起的躺井多达37口,腐蚀躺井共影响产量约90吨,管杆损坏更换费用上万元。
据分析,油井腐蚀是上述腐蚀类型共同的作用结果,但其主要以二氧化碳腐蚀、硫化氢腐蚀、微生物腐蚀和电化学腐蚀为主。
1)抽油杆的腐蚀
由于介质的腐蚀性和冲刷作用,抽油杆及接箍出现不同程度的腐蚀现象。
在抽油杆接箍偏磨,以及H2S、CO2酸性介质作用,电化学作用等的情况下,抽油杆及接箍腐蚀严重,腐蚀后呈现麻斑,严重的有深坑。
抽油杆偏磨破坏其表面的保护层,而抽油杆表面腐蚀后材质变得疏松,又使得磨损更容易,腐蚀与偏磨相互促进,使得腐蚀加剧。
在含水高且成酸性腐蚀的油井中,由于腐蚀疲劳、氢脆、应力腐蚀等原因,经常出现抽油杆断裂。
如图3-1、图3-2、图3-3、图3-4所示:
图3-1接箍腐蚀图3-2接箍腐蚀
图3-3抽油杆腐蚀图3-4抽油杆腐蚀
2)井下工具的腐蚀
油井井下工具是在油井出现游离水后腐蚀才严重的,这是因为游离水中含有H2S、CO2酸性介质以及细菌等。
由于活塞、阀等处于运动状态,因此损坏程度更大。
抽油泵腐蚀主要发生在凡尔球和球座,占95%以上,其中又以固定凡尔球和球座最严重,被腐蚀的球座表面有麻点。
这是因为球座始终处于受磨损状态,而凡尔球受流体的冲击,易形成涡流导致腐蚀。
如图3-5、图3-6、图3-7、图3-8所示:
图3-5固定凡尔点蚀图3-6固定凡尔总承腐蚀
图3-7活塞腐蚀图3-8凡尔球腐蚀
3)油管的腐蚀
油管的腐蚀大致上可分为均匀腐蚀和局部腐蚀,其中影响最严重的是局部腐蚀造成的腐蚀穿孔。
然而局部腐蚀主要是二氧化碳腐蚀、微生物腐蚀以及电化学腐蚀造成的。
油管腐蚀大部分呈圆形或椭圆形,外小内大,呈八字形,油管的腐蚀是从管内开始的。
一旦油管外壁发现腐蚀现象,那么对应内壁会有更大面积的腐蚀。
油管内壁既有腐蚀又有结垢,甚至发生垢下腐蚀。
随着油管的腐蚀,大量的腐蚀残渣掉入井筒,而这些残渣容易进入固定凡尔座内,导致凡尔坐封不严,最终形成固定凡尔漏失。
如图3-9、图3-10、图3-11、图3-12所示:
图3-9油管腐蚀图3-10油管腐蚀
图3-11油管腐蚀图3-12眼管腐蚀
4)套管的腐蚀
套管的腐蚀主要出现在动液面以下,这是因为油水混合中含H2S、CO2、O2等溶解性气体。
由于这些腐蚀介质的存在,套管往往出现大面积的腐蚀,在胡尖山采油作业区的元162井区最为严重。
典型案例有:
①定594-21的套管因腐蚀发生套破现象;
②定593-16在2012年多次检泵时发现固定凡尔总承堵死,尾管被杂质填满,经化验后得知杂质主要成分为氧化铁。
以此判断元162区块套管存在严重腐蚀现象。
3.2地面集输管线腐蚀现状
胡尖山采油作业区目前所管辖区有元162、安42和黄30三个井区,井组数共计约120个,增压站4个,300方沉降罐6个,300方储油罐2个,铺设管线约89km,其中管线均为埋地管线。
由于胡尖山采油区釆出液含有H2S、CO2、O2等溶解性气体,以及油、悬浮物、无机离子、细菌(硫酸盐还原菌、腐生菌)等,这些腐蚀介质在较低的含量下就可以腐蚀管线和储罐。
据分析,腐蚀的类型主要为硫化氢腐蚀、溶解氧腐蚀、电化学腐蚀和二氧化碳腐蚀。
1)埋地管线腐蚀
油区大部分地区为黄土高原,主要以黄土梁峁及沟壑地貌为主,地形破碎,质地疏松,植被稀疏,腐蚀总体上为弱腐蚀,本质是电解质腐蚀。
这种腐蚀常常造成埋地管线的外部腐蚀。
图3-13埋地管线外腐蚀图3-14沉降罐内腐蚀
采油区采出液所含各种腐蚀介质,在原油集输过程中,最常见的埋地管线腐蚀当属管线的内介质腐蚀。
元一增至元162站输油管线最为典型。
分析其原因:
元一增至元162管线输送的是油水混合物,含水较多,同时原油在输送过程中极易发生油水分离,具有较高腐蚀性污水集中于管线底部,水作为腐蚀媒介,水含量越大,管线的腐蚀就越明显,故元一增管线底部腐蚀速度明显高于管线顶部。
2)储罐腐蚀
胡尖山采油区沉降罐的罐底、油水界面以下管壁及罐内附件腐蚀主要是由于污水中含有的溶解氧能加速腐蚀,且由于污水质矿化度高、pH值低,含有Cl-、SO42-、HCO3-等易形成酸性腐蚀;
而罐顶腐蚀主要由硫化氢造成。
如图3-14所示。
3.3注水系统腐蚀现状
胡尖山采油区所管辖区的三个井区均无污水处理装置、杀菌剂加药装置。
然而采出水中含有H2S、CO2、O2等溶解性气体,以及油污、悬浮物、无机离子、硫酸盐还原菌等腐蚀介质,直接影响金属设备及管线的腐蚀。
污水罐的腐蚀同沉降罐腐蚀大致相同,主要腐蚀部位是污水罐内部的罐底、罐壁与含水层接触的部位及内部附件。
分析腐蚀产物和腐蚀现象发现:
①油田污水中含有的溶解氧使腐蚀加剧,是污水罐内表面腐蚀的主要原因。
当有溶解氧存在时,氧的电极电位高,容易形成阴极,对储罐的腐蚀性增强,其腐蚀产物主要为Fe2O3、Fe(OH)3;
②污水中含有大量的硫酸盐还原菌(SRB),罐内介质流动越慢越容易滋生SRB。
SRB的存在将硫化物和SO42-还原为H2S。
H2S能够与Fe2+反应,生成FeS沉淀,进一步加速腐蚀;
③油田水质具有矿化度高、Cl-含量高和pH值低的特点,同时含有一定量SO42-、HCO3-等。
注水井筒在污水回注过程中,管壁往往受到污水中二氧化碳、溶解氧、矿物质、氯离子以及细菌的作用而产生不同程度的局部腐蚀。
腐蚀过程中产生的腐蚀残渣掉入井筒底部,在高压作用下,这些渣子被挤入地层极易造成地层堵塞。
除污水罐腐蚀和注水井筒腐蚀之外,注水管线及其它注水设备也相应存在严重腐蚀,元162井站污水注水系统腐蚀情况便为典型案例,如图3-15、图3-16所示。
图3-15配水阀组腐蚀图3-16注水管线腐蚀
4腐蚀治理措施现状
胡尖山采油作业区针对所管辖区腐蚀现状,采取了相应的防护措施。
4.1井筒的腐蚀治理措施
1)针对普通抽油杆腐蚀问题,我区采用高分子涂层防腐抽油杆,从根本上解决了普通抽油杆腐蚀问题。
高分子涂层防腐抽油杆是引进美国ICO公司先进技术生产的,是在精选的D级或H级抽油杆表面喷涂一层耐腐蚀高强度的复合材料,经特殊工艺使其固化而成。
具有以下优点:
1、具有很高的抗腐蚀性能,适应不同腐蚀介质的油井;
2、减少结垢,增加流体效率;
3、寿命长,在腐蚀介质中寿命是普通抽油杆的5倍以上,而价格不到普通抽油杆的2倍;
4、减少抽油杆作业次数,停产率低,综合效益高。
目前,我区已在89口油井中使用高分子涂层防腐抽油杆3.6848万米,取得良好的经济效益。
如图4-1、图4-2所示:
图4-1防腐抽油杆图4-2阳极保护器
2)针对普通油管腐蚀问题,我区采取内衬油管+防腐杆的搭配模式。
内衬油管是采用专门技术在钢制普通油管内内衬一层特种超高分子聚乙烯耐磨管材,使衬管与油管紧贴在一起,形成“管中管”结构。
与金属管材相比,内衬油管具有质量轻、耐腐蚀、耐磨损、不生锈、导热系数低、摩擦系数低、绝缘性能好、自洁性强、流体阻力小等优点。
自2012年4月起,我区引进并逐步推广金湖支点内衬油管。
截止目前,我区已在44口油井中使用内衬油管22582m,在防偏磨、防腐蚀方面均取得良好的经济效益。
3)除了使用防腐抽油杆和内衬油管以外,我区从腐蚀根源着手,针对井底腐蚀类型,采取两种不同的措施:
①、井口投加MH-46型缓蚀剂,其主要作用是提高介质的pH值,调解流体介质的pH接近7,此时流体介质对金属的腐蚀最小,能有效缓解H2S、CO2、Cl-等多种腐蚀介质对井下管柱和地面集输系统的腐蚀。
②、引进阳极保护器,解决井筒内电化学腐蚀;
其原理为牺牲阳极而保护阴极,将需要保护的金属作为阴极,通过阳极向阴极不间断地提供电子,首先使结构极化,进而在金属表面富集电子,使其不易产生离子,因而大大地减缓了结构的腐蚀速度。
4.2集输、注水管线的腐蚀治理措施
据目前集输系统和注水系统的腐蚀情况,胡尖山采油作业区采取了有针对性的防腐措施,具体措施如下所示:
1)针对埋地管线内腐蚀情况,我区采取两种措施予以解决。
①针对外输等重要管线,引入HCC加强级内防腐技术,该内防腐以防腐性能优异的双酚F环氧树脂为基体树脂,有机纤维为增强体,所以其表现出的防腐、力学性能都很优异,在严苛的酸、碱、盐腐蚀环境下可长期使用;
由于填料的引入,其硬度、耐磨性、阻燃性、防静电等方面的性能都有着很大的提高。
典型案例:
元一增至元162站的外输管线,该条管线由于输送的是油水混合物。
油水混合物中存在CO2、H2S酸性介质,从而引起油水界面蚀线腐蚀;
也含有Ca2+离子,从而形成CaSO4、CaCO3等垢后引起垢下腐蚀,此类腐蚀缓蚀剂无法保护;
同时含有的Cl-会加速局部腐蚀,引起管线腐蚀穿孔。
将该条管线更换做HCC内防腐后,既可以延长使用寿命,又可以降低管壁结垢速率。
如图4-3、图4-4所示。
②针对其他管线,采取加药措施。
图4-3HCC内防腐图4-4HCC涂片
2)针对整个注水管网系统,我区主要采取向污水罐投加MH-46型缓蚀剂和SW-60/80型杀菌剂的方法。
SW-60/80型杀菌剂能够抑制细菌繁殖,从根源上减少采出液中的腐蚀介质,从而达到防腐的作用;
MH-46型缓蚀剂是一种咪唑啉类缓蚀剂,主剂成份中的膦酸盐的分子结构含有-OP(OH)(膦酸基),与Fe原子形成多重配位键,结合的十分牢固,并生成一个环状化合物,而牢固地吸附于铁表面,使腐蚀金属的表面状态改变,从而改变腐蚀中的阳极或阴极反应的过程。
使反应速率常数减小,使整个腐蚀过程的速率下降而达到缓蚀目的。
5下步治理措施展望
胡尖山作业区虽然在腐蚀方面采取了不少的治理措施,但是对于该区复杂的腐蚀情况来看,某些措施的防腐效果并没有达到理想的效果。
采取更为有效的措施迫在眉睫,为此,本文对该区下步治理措施提出以下几个建议:
1)胡尖山作业区油水井普遍存在套管腐蚀现象。
针对这一现象,开发阳极的防腐技术可以有效的延长油水井套管的使用寿命,但是真正的实现长期保护阳极的工作需要对阳极有十分严格的要求:
①化学性能要好,并且在使用阳极电流密度时候溶解度比较低。
②在高阳极电流密度下极化比较小,在一定的电压下阳极的单位面积通过的电流要大,排流量要低。
③具有非常好的导电性能,在阳极的所有介质中接界要低。
④有一定的机械强度,耐磨损,可靠性能高。
但是开发阳极防腐技术成本比较昂贵,很难在低产油水井中应用。
因此,我们可以采用井下牺牲阳极与套管内涂层联合防腐技术,其基本原理是采用性能优良的有机涂料隔绝腐蚀介质,同时利用比钢铁活泼、电极电位低的镁基、铝基、锌基等有色金属合金作为阳极,阳极在腐蚀过程中首先被腐蚀,产生的电流使钢铁极化而免遭腐蚀。
通过这一组合,一旦涂层遭受破坏,阳极就可以提供保护。
2)针对单井集油等管线,计划采取管线加药方式。
这是因为井筒加药只是针对井底腐蚀而言,而采出液到达地面管线时,井筒所加缓蚀剂的浓度已经明显降低,已经无法起到管线防腐的作用。
但可以采取管线加药方式进行单井管线防腐,管线加药方式可以根据管线长度、采出液所含腐蚀介质情况、管线内壁材料等因素进行缓蚀剂类型及浓度的调整。
3)胡尖山采油作业区的沉降罐和污水罐在采出液的作用下腐蚀严重。
因此,对于沉降罐和污水罐的防腐,我们可以引进牺牲阳极保护阴极+HCC内防腐涂层联防技术。
该技术是采用性能优良的有机涂料隔绝腐蚀介质,同时将电位更负的金属与被保护金属连接,并处于同一电解质中,使该金属上的电子转移到被保护金属上去,使整个被保护金属处于一个较负的相同的电位下。
图5-1钢制储罐牺牲阳极保护阴极技术
4)新型缓蚀剂的引进
查阅相关文献得知,IM-S型缓蚀剂也是一种咪唑啉类缓蚀剂,具有较好的抗H2S、CO2的腐蚀的能力,并能同时抑制碳钢腐蚀的阴、阳极反应过程,最高缓蚀效率可达92.74%。
YZHS-1缓蚀剂也是一种高效的缓蚀剂。
该缓蚀剂不仅能防止H2S、CO2的腐蚀,还能抑制硫酸盐还原菌和不均匀结垢引起的腐蚀。
缓蚀效率高,对于腐蚀严重的油井和地面系统都有很好的缓蚀作用,用量为100mg/L时缓蚀率可达到80%以上。
ZSY92-1缓蚀剂是以合成的炔氧甲基胺及其衍生物和醚类化合物复配而成,为水溶油分散吸附成膜型的缓蚀剂。
该缓蚀剂主要适用于高Cl-、高矿化度的腐蚀介质的油井。
油井加缓蚀剂采用周期性加药,用泵将缓蚀剂注入到油套管环形空间,靠缓蚀剂的自重降到井底,随产出液从油管内返出,在这一过程中,缓蚀剂大部分溶解于产出水中,少量分散在油中,随着上返,缓蚀剂在金属表面被吸附而形成保护膜,由此起到了防护作用。
然而我区三叠系和侏罗系地层水水质主要水型为CaCL2和MgCL2,而且矿化度非常高。
故ZSY92-1缓蚀剂适合我区地层。
6结论
1)、通过对井下油管系统腐蚀现状的调查分析,可以看出H2S或CO2、硫酸盐还原菌是主要的腐蚀因素,其次是高矿化度采出液的电化学腐蚀,Cl-对腐蚀的发生具有强烈的催化作用,而原油中的水是腐蚀剂的载体,温度、pH值为腐蚀提供有利境。
此外,由于油井投产时间长,管壁蚀坑和垢物导致井壁粗糙,油井井口部分有结蜡出现,受这些因素及其交互作用的影响,腐蚀已成为影响油气田安全生产和阻碍经济效益进一步提高的重大不利因素。
2)、缓蚀剂技术是油井防腐蚀的最有效的手段,它不但可以保护油管、套管及井下设备,而且可以起到保护集油管线和设备的作用,是一项成本低、容易实施、见效快的措施。
IM-S型缓蚀剂、YZHS-1缓蚀剂和ZSY92-1缓蚀剂对于腐蚀严重的油井和地面系统都有很好的缓蚀作
用,建议明年尝试性试用。
3)、油田注水系统地面管网及储罐由于随溶解氧含量、氯离子浓度和硫酸盐还原菌数量增加,介质腐蚀速度增强,主要以氧腐蚀为主,微生物腐蚀为辅;
还发生了以氢去极化为主的二氧化碳腐蚀。
4)、对杆管偏磨、腐蚀均严重的油井,阴极保护技术与防偏磨治理技术配套应用才能取得理想效果。
对污水罐腐蚀,阴极保护技术与HCC内防腐涂层联防技术可以达到很好的防腐效果。