塑料碗模具设计Word格式文档下载.docx
《塑料碗模具设计Word格式文档下载.docx》由会员分享,可在线阅读,更多相关《塑料碗模具设计Word格式文档下载.docx(15页珍藏版)》请在冰豆网上搜索。
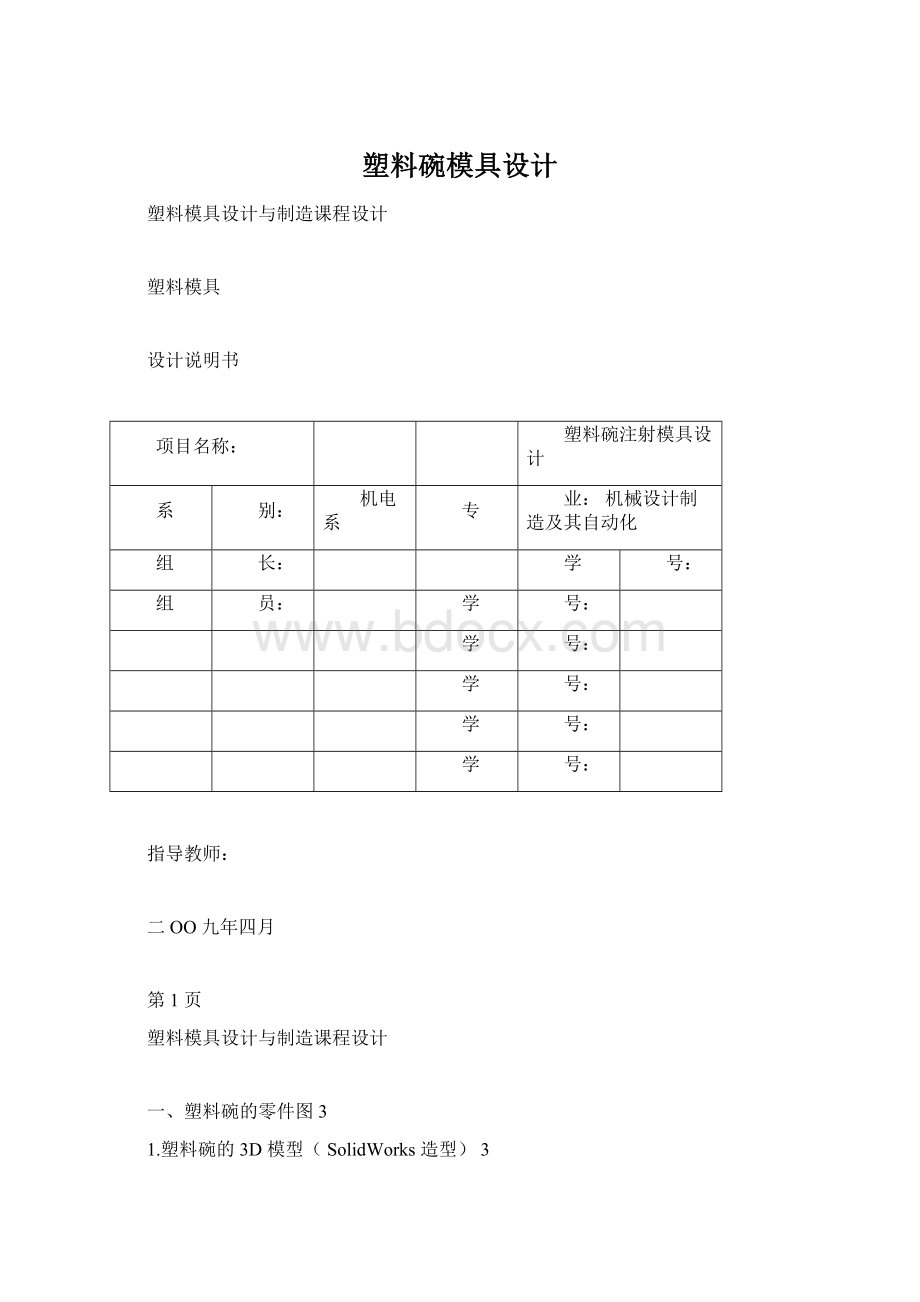
1、注射机的组成8
2.锁模力的校核9
3.注射量的校核10
4.核膜机构的尺寸的校核10
六、模具型腔和型芯尺寸计算10
1、型腔的内形尺寸计算11
2、型腔的深度尺寸计算12
3、型芯的外形(外径)尺寸12
4、型芯的高度尺寸计算13
六、确定模架尺寸13
1、导柱的结构13
2、导套的结构14
七、参考资料14
第2页
一、塑料碗的零件图
1.塑料碗的3D模型(SolidWorks造型)
2.塑料碗的尺寸图
第3页
二、塑料碗制品的结构特点
1.餐具外观酷似瓷器或象牙,不易脆裂又适宜机械洗涤。
2.刚性和强度比传统的塑料制品好,制品不易变形。
3.耐高温性能较好,可以能用作微波炉餐具但低温脆性高。
4.在室温下不固化,一般在130~150℃热固化,加少量酸催化可提高固化速度。
5.塑料碗采用凹模结构设计,凹模是成型产品外形的主要部件。
其结构特点:
随产品的结构和模具的加工方法而变化。
镶拼的组合方式的优点:
对于形状复杂的型腔,若采用整体式结构,比较难加工。
所以采用组合式的凹模结构。
同时可以使凹模边缘的材料的性能低于凹模的材料,避免了整体式凹模采用一样的材料不经济,由于凹模的镶拼结构可以通过间隙利于排气,减少母模热变形。
对于母模中易磨损的部位采用镶拼式,可以方便模具的维修,避免整体的凹模报废。
组合式凹模简化了复杂凹模的机加工工艺,有利于模具成型零件的热处理和模具的修复,有利于采用镶拼间隙来排气,可节省贵重模具材料。
第4页
三、选择的塑料及其性能、成型条件
1.选择的塑料:
PP(聚丙烯)
2.PP塑料的性能:
PP是一种半结晶性材料。
它比PE要更坚硬并且有更高的熔点。
由于均聚物型的PP温度高于0℃以上时非常脆,因此许多商业的PP材料是加入1~4%乙烯的
无规则共聚物或更高比率乙烯含量的钳段式共聚物。
共聚物型的PP材料有较低的热扭曲温度(100℃)、低透明度、低光泽度、低刚性,但是有更强的抗冲击强度。
PP的强度随着乙烯含量的增加而增大。
PP的维卡软化温度为150℃。
由于
结晶度较高,这种材料的表面刚度和抗划痕特性很好。
PP不存在环境应力开裂
问题。
通常,采用加入玻璃纤维、金属添加剂或热塑橡胶的方法对PP进行改性。
PP的流动率MFR范围在1~40。
低MFR的PP材料抗冲击特性较好但延展强度较低。
对于相同MFR的材料,共聚物型的强度比均聚物型的要高。
由于结晶,PP的收
缩率相当高,一般为1.8~2.5%。
并且收缩率的方向均匀性比PE-HD等材料要好得多。
加入30%的玻璃添加剂可以使收缩率降到0.7%。
均聚物型和共聚物型的
PP材料都具有优良的抗吸湿性、抗酸碱腐蚀性、抗溶解性。
然而,它对芳香烃
(如苯)溶剂、氯化烃(四氯化碳)溶剂等没有抵抗力。
PP也不象PE那样在高温下仍具有抗氧化性。
3.PP的成型条件:
塑料碗在注射成型时,要经过三个阶段的转换:
一是塑料未进入料筒时的颗粒状态;
二是塑料在料筒中的塑化流动而达到的熔融状态;
三是塑料通过注射模浇注系统的冲模流动及冷却定型。
在每个阶段中,都要有特定的工艺成型条件。
3.1颗粒状态
(1)预热干燥
原料应先进行预热干燥处理,预热时间为1.5-2min,料温升至80C°
-100C°
。
原因是原料中往往水分含量太高,如果直接放入料筒,会导致制品表
面暗淡,色泽不均匀以及表面气泡等故障。
但是预热时间要适当,温度也不能过高。
温度太高会导致制品表面产生焦斑;
预热温度太高或预热时间太长会导致制品表面色泽不均匀。
(2)加料计量
进料量要准确。
如果原料过多会造成制品飞边多,清理困难;
如果原料太少,会造成成型压力不够,制品不能完全固化等弊端。
3.2熔融状态
(1)控制成型温度和压力
根据PP塑料的最佳成型条件要求,应将模具的成型温度控制在150-220C°
之间;
初压控制在70Mpa-90Mpa之间,加压时间为1-5s。
原料温度太高,容易导致制品表面有焦斑及制品色泽不均匀;
初压时间太长,会导致制品表面疏松;
成型温度和压力不适当,会导致塑料流动性能太差。
(2)排气
在成型时会产生缩合水及挥发性气体,所以应当在成型时进行排气以
防止制品表面疏松。
通常放气的次数和时间长短凭经验确定,放气动作力求迅速。
只要卸除一下压力,再立即恢复到原来的压力,放气动作就算完成了。
我们的塑料碗结构不复杂,所以不必从模具方面考虑排气结构。
第5页
3.3冲模流动及冷却定型
(1)固化阶段
排气后即刻合模升压至70-90Mpa,时间70s左右。
在此阶段,固化时间应当充足,否则会导致制品表面暗淡。
(2)出模
完成固化之后,风冷制品,顶出机构将制品顶出。
(3)出模后的加工
我们制作的是食品器具,所以制品出模后,应入120C°
以上的烘箱中加热30—60min,使之进一步固化。
最后进行打磨飞边,完成塑料碗的制作。
四、确定型腔数、排列方式和分型面
1、型腔数目的确定
型腔数目的确定,应根据塑件的几何形状及尺寸、质量、批量大小、交货长短、注射能力、模具成本等要求来综合考虑。
根据注射机的最大锁模力确定型腔数目n,即
F锁
fA废
n
fA件
式中F锁——注射机的额定锁模力(N)
A废——模具上浇注系统及飞边在分型面上的投影面积(
2
m)
A件——塑件在分型面的投影面积(m)
f——单位面积所需的锁模力(N/m2)
大多数小型件常用多型腔注射模,面高精度塑件的型腔数原则上不超过
4
个,生产中如果交货允许,我们根据上述公式估算,采用一模二腔。
2、型腔的排列方式
考虑到模具成型零件和抽芯结构以及出模方式的设计,模具的型腔排列
方式如下图所示:
第6页
图
(1)
3、分型面的设计
分型面位置选择的总体原则,是能保证塑件的质量、便于塑件脱模及简化模具的结构,分型面受到塑件在模具中的成型位置、浇注系统设计、塑件的结构工艺性及精度、嵌件位置形状以及推出方法、模具的制造、排气、操作工艺等多种因素的影响,因此在选择分型面时应综合分析比较具体可以从以下方面进行选择。
a)确保塑件尺寸精度,有同轴度要求的部分全部在动模部分成型,选分型面时,还应考虑减小由脱模斜度造成塑件的大小端尺寸差异。
b)确保塑件表面要求,分型面尽可能选择在不影响塑件外观的部位以及塑件外观的要求,而且分型面处产生的飞边应容易修整加工。
c)考虑锁模力,尽可能减少塑件在分型面上的投影面积。
d)考虑模板间距。
第7页
e)便于塑件顺利脱模,尽量使塑件开模时留在动模部分。
f)考虑侧抽芯机构,应尽量避免侧抽芯机构。
g)尽量方便浇注系统的布置。
h)便于排溢。
i)便于嵌件的安放。
j)模具整体结构简化,尽量减少分型面的数目,尽量采用平直分型面。
k)考虑模具制造难易性。
五、选择注射机和注射机参数
1、注射机的组成
注射机的全称应为塑料注射成型机。
注射机主要由注射装置、合模装置、液压传动系统、电器控制系统及机架等组成。
工作时模具的动、定模分别安装于注射机的移动模板和定模固定模扳上,由合模机构合模并锁紧,由注射装置加热、塑化、注射待融料在模具内冷却定型后由合模机构开模,最后由推出机构将塑件推出。
1、锁模油缸2、锁模机构3、移动模板4、顶出杆5、定模固定板6、控制台
7、料筒及加热器8、料斗9、定量供料装置10、注射油缸
第8页
注塑机的选择与参数校核
根据课程设计实际要求我们选用型号为XS-Z-60的注射机,如图其主要技术参数如下:
最大注射容量为60cm3;
注射压力为122Mpa;
锁模力为500kN;
最大注射面积为130cm2;
最大模具厚度为200cm;
最小模具厚度为70mm;
喷嘴圆弧半径R12mm;
喷嘴孔半径R2mm;
中心顶出孔半径R25mm;
模板开模行程180mm。
根据上述所选注射机进行参数校核。
2.锁模力的校核
按F≥KpA分公式校核锁模力。
其中,F为注射机的最大锁模力;
p为模内平均压力(型腔内熔体的平均压力);
A分为所有制品、流道和浇口在分型面上的投影面积之和。
K为压力损耗系数,一般取1.1-1.2。
由于制品材料为pp,属于中等粘度塑料和有精度要求的制品,查相关资料得:
p为29.6-34.4MPa,取p=30MPa进行校核。
A分是分型面上的投影面积,经计算(可利用软件的分析功能进行计算),得到单个塑件的投影面积为4755mm2,浇注系统的投影面积约为80mm2,则两个
制品、流道和浇口在分型面上的投影面积之和A分为9710mm2
第9页
因此:
KpA分=1.1X30X106X9710X10-6N=321X103N=321kN
F=500kN≥321kN
所以锁模力足够,满足锁模要求。
3.注射量的校核
经计算得到单个塑件的体积为15.86cm3,浇注系统的体积约为2cm3,因此,模具中塑件和浇注系统的总重量Gmax=2x15.86cm3+2cm3=33.72cm3.
注射机的注射量G=60cm3,按校核公式GX0.8=60x0.8cm3=48cm3≥33.72cm3,满足注射成型的要求。
4.核膜机构的尺寸的校核
(1)模具厚度的校核注射机允许安装的模具最高厚度为200mm;
注射机允许安装的模具最小厚度为70mm。
模具实际厚度H=定模座厚度+型腔板厚+型芯固定板厚+垫铁厚+垫块厚+动模座板厚=20mm+30mm+30mm+32mm+35mm+20mm=167mm
显然,注射机允许安装的模具最小厚度≤模具实际厚度H≤注射机允许安装的模具最大厚度,模具厚度满足要求。
(2)开模行程的校核
按开模取件的最小开距进行校核。
该模具的浇注系统为侧浇口形式,单分型面注射模,可按下式校核:
S≥H1+H2(5-10)mm
其中,注射机最大开模行程S为180mm;
制品的推出距离H1为10mm:
制品的总高度H2为50mm。
H1+H2+(5-10)mm=10mm+50mm+10mm=70mm显然,注射机最大开模行程S≥70mm,模具的开模行程足够
六、模具型腔和型芯尺寸计算
下图为我们所设计的塑料碗的结构尺寸图,我们根据图示的尺寸大小计算出型腔和型芯的尺寸。
第10页
1、型腔的内形尺寸计算
碗口部分的型腔内形尺寸:
D腔1
=
dS1Qcp
mz
dS1
xs10
1.14
=1151152%)
3
=116.44500.38
上述计算中,塑件公差s1取1.14mm,塑料平均收缩率Qcp取2%,综合修正系
数x取3/4。
碗底部分的型腔内形尺寸:
D腔2=
dS2
dS2Qcp
4s2
0.74
=5555
2%
=56.450
0.25
上述计算中,塑件公差s1取0.74mm,塑料平均收缩率Qcp取2%,综合修正系
第11页
2、型腔的深度尺寸计算
mz
碗口部分型腔深度尺寸:
H腔1=hs1
hs1Qcp
s1
=57(1
2%)
=57.6500.25
数x取2/3。
碗底部分型腔深度尺寸:
H腔2=hs2
hs2Qcp
=33
2%0.20
s2
0.20
=2.9300.07
上述计算中,塑件公差s2取0.2mm,塑料平均收缩率Qcp取2%,综合修正系数
x取2/3。
3、型芯的外形(外径)尺寸
碗口部分型芯的外形尺寸:
d凸=
DS1QCP
DS1
xs1mz
=100100
1.0
=102.750
0.33
上述计算中,塑件公差
s1取1.0mm,塑料平均收缩率Qcp取2%,综合修正系数
x取3/4。
碗底部分型芯的外形尺寸:
d凸
DS2DS2QCP
xs2mz
第12页
47(1
0.64
48.580
0.21
上述计算中,塑件公差s2取0.64mm,塑料平均收缩率Qcp取2%,综合修正系
4、型芯的高度尺寸计算
碗口部分型芯的高度尺寸:
h凸1=Hs1
Hs1Qcp
xs1
0z
m
=50
50
0.64
=51.43
0.21
上述计算中,塑件公差
s1取0.64mm,塑料平均收缩率Qcp取2%,综合修正系
碗底部分型芯的高度尺寸:
h凸2=
Hs2
Hs2Qcpx
s2m
=4(1
0.24
=4.240
0.08
s2取0.24mm,塑料平均收缩率Qcp取2%,综合修正系
六、确定模架尺寸
1、导柱的结构
带头导柱如图(3)所示:
第13页
图(3)
2、导套的结构
带头导套如图(4)所示:
图(4)
七、参考资料
陈万林等编著.实用塑料注射模设计与制造.北京:
机械工业出版社,2006
第14页