钛合金盒体的数控加工工艺研究文档格式.docx
《钛合金盒体的数控加工工艺研究文档格式.docx》由会员分享,可在线阅读,更多相关《钛合金盒体的数控加工工艺研究文档格式.docx(14页珍藏版)》请在冰豆网上搜索。
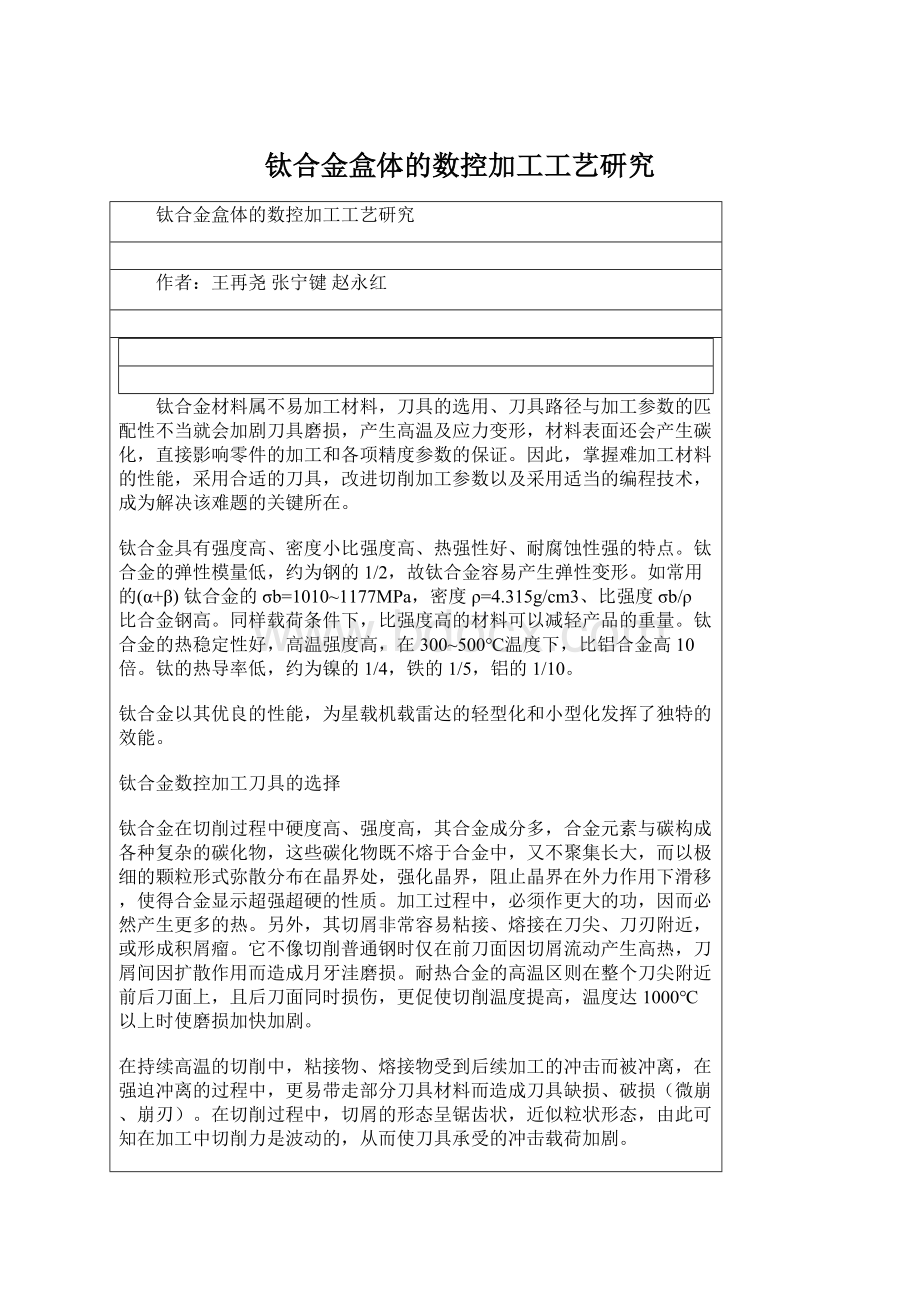
1铣削方式
对于型腔铣,采用顺铣的走刀方式。
在切削参数允许的范围内采用较大的径向分层和较小的轴向分层加工;
对于侧壁两面都需加工时采取台阶式来回铣削,充分利用零件的整体刚性,可提高加工效率。
但在切削过程中,不允许刀具中途停顿,切削结束,立即退刀,以免形成坚硬的氧化皮,加速刀具磨损。
对于加工中心可采用圆弧进刀和圆弧退刀的方法,减少刀具在某一点的停留时间。
2编程控制
(1)进刀方式。
合理选取起刀点、退刀点、切入点和切入方式。
采用圆弧切入方式,切入平稳、冲击力小。
这可以保证刀具不易受到刚性损伤。
避免沿工件轮廓垂直方向进刀,在切入材料时要采用斜插式切入,可以避免刀具刃齿的崩损,从而可以有效地保证了后续加工及工件的精度、粗糙度等要求。
精加工时,考虑刀具的切入和切出路线,尽量减少在轮廓处停刀,以避免切削力突然变化造成弹性变形而留下刀痕。
(2)走刀路径。
走刀路径对提高钛合金整体结构件的加工精度有着重要的影响,对于具有定位功能的表面,尽可能采用由内向外的铣削方式,这样形成内凹的微观结构,有利于定位。
对于具有单元框结构的零件,尽可能采用由内向外或由外向内的铣削方式,以利于材料均匀去除,使残余应力均匀释放并保持工件刚度的均衡性,以减小加工变形[4]。
切削路径尽可能采用直线切削,减少在拐点处走圆弧切削。
3切削参数控制
钛合金的强度高、粘性大,切削中更容易在切削区产生和积聚热量。
加之导热性差,在切削速度过快时有引起燃烧的危险,这就是铣削钛合金零件一定不能选择高切削速度的原因。
采用小径向切入法切削钛合金零件,能极好地控制切削温度,实现高速加工。
在工厂中使用该方法,可提高加工精度。
采用低转数、快速进给、小切削深度,使材料快速分离,不会产生高热及大应力,刀具磨损也较小。
切削速度、进给速度、径向切深对钛合金表面粗糙度产生不同的影响。
随着切削速度增加,表面粗糙度在径向切深方向略有减小,而在进给方向先增加然后减小。
4装夹要求
对薄壁工件在装夹时注意一个“实”字,即要把底面垫实。
零件的底面为曲面,所以夹具体应设计成相同的凹面,同时满足精度要求。
装夹时,利用定位孔销定位,轮廓用辅助夹具固定,刀具路径采用一粗一精,分几次加工到最后尺寸,或采取对称去余量法安排进给路线。
不要使用低熔点金属及其合金(铅或锌基合金,铜、锡和镉及合金)制作的工、夹具或临时紧固件。
与钛合金接触的工、夹具或其他装置必须清洁无垢。
加工后的钛合金表面不允许残留铅、锌、铜、锡和镉等低熔点金属。
如有残留,应使用氢氟酸和硫酸亚铁溶液仔细清洗。
装卸清洗过的钛合金工件时,必须防止油脂及指纹污染,以免发生盐应力腐蚀,使钛合金工件断裂。
5钻孔和攻丝
钻孔:
钛合金回弹性大,钻头进入工件后受较大径向及轴向力。
钛合金化学活性高,易造成粘刀,切屑不易排除,往往产生钻头被咬住、扭断钻头等现象。
选取专用于钛合金加工的高速钢钻头,通过增厚钻芯和尽量减小其长度的方法提高刚性。
加工时避免钻头不进给而在孔中打转,以免引起加工硬化。
实际加工中测得孔径比钻头直径小0.1mm左右,这是钛合金材料特性的表现之一,故钻孔可使用比标准直径大0.1mm左右的钻头。
钻孔前需用中心钻点孔,并在对刀机上检查钻头端部,控制刀刃跳动量小于0.02mm。
攻丝:
钛合金攻丝加工,特别是小孔攻丝加工很困难。
其主要原因是在攻丝加工过程中,造成钛合金热膨胀。
另外,钛合金加工后回弹大,易造成丝锥折断。
具体可通过以下2种途径得以解决。
改进丝锥结构形式,将锥芯增粗和减少各段丝锥切削刃宽度或使用跳牙丝锥可以提高刚性及减小同被加工材料的接触面积。
另外,采用螺旋槽可增加丝锥锋利程度,减小切削力,避免丝锥折断,有利于排屑,使冷却液能够较容易进入切削区,改善丝锥冷却及润滑性能。
对螺纹底孔设计提出公差要求需对螺纹底孔直径公差提出要求。
6润滑要求
钛合金盒体零件在以上的几种加工方式中,需注意下列2点:
(1)在钻削攻丝及铣削加工时使用的冷却液相同,不推荐使用含氯冷却液。
因为在切削过程中,切削液在高温下分解释放出氢气,被钛吸收后引起氢脆,同时,氯还可能引起钛合金高温应力腐蚀开裂。
钻削浅孔时,可用电解切削液;
钻削深孔时,用N32机械油加煤油,配比是3∶1.5,也可用硫化切削液。
可见,钛合金加工的冷却液配制适合,可延长刀具寿命。
通过以上分析,采用规格为φ4mm、φ6mm、φ8mm的三刃TiC(N)基硬质合金刀具和Miracle涂层硬质合金刀具对各加工参数分别进行试验,在加工条件良好的情况下测得具体加工参数对比如表2、表3。
结束语
从加工后零件的检测结果及实验数据可知,使用涂层硬质合金刀,转速2500r/min、进给速度400m/min、切削深度0.07mm这组数据,基本到达了设计工艺要求。
由此可得出:
(1)涂层硬质合金刀可满足钛合金加工。
(2)采用低转速,可降低刀具磨损、延长刀具使用寿命。
(3)快进给速度,每齿切削量在0.08mm左右,不易产生加工硬化。
(4)小切削量,可避免造成切削温度过高而产生零件变形。
(end)
航空航天特殊材料加工技术之钛合金的加工
点击数:
56
发布时间:
2012-06-25
来源:
超音频感应加热设备|中频电炉|机床导轨淬火设备|数控淬火机床|高频机-郑州国韵电子技术有限公司
编辑:
近年来,对汽车和飞机零件高强度化和轻量化的要求越来越高。
因此,这些零件所使用材料中的钛、镍合金等也在不断增加。
这种材料一般称为切削加工性差的“难切削材料”。
加工此类材料的切削刀具也必须能够适应难切削材料特有的加工条件和加工方法。
飞机机身部件以及喷气发动机的压缩机零部件越来越多地采用了钛合金。
目前,金属钛生产的工业方法是可劳尔法,产品为海绵钛。
制取钛材传统的工艺是将海绵钛经熔铸成锭,再加工而成钛材。
钛采用塑性加工,加土尺寸不受限制,又能够大批量生产,但成材率低,加工过程中产生大量废屑残料。
针对钛塑性加工的上述缺点,近年来发展了钛的粉末冶金工艺。
钛的粉末冶金流程与普通粉末冶金相同,只是烧结必须要在真空下进行。
它适用乎生产大批量、小尺寸的零件,特别适用于生产复杂的零部件。
这种方法几乎无须再经过加工处理,成材率高,既可充分利用钛废料作原料,又可以降低生产成本,但不能生产大尺寸的钛件。
钛合金即在工业纯钛中加入合金元素,以提高钛的强度。
钛合金可分三种:
a钛合金,b钛合金和a+b钛合金。
a
b钛合金是由a和b双相组成,这类合金组织稳定,高温变形性能、韧性、塑性较好,能进行淬火、时效处理,使合金强化。
钛合金的性能特点主要表现在:
1)
比强度高。
钛合金密度小(4.4kg/dm3)重量轻,但其比强度却大于超高强度钢。
2)
热强性高。
钛合金的热稳定性好,在300~500℃条件下,其强度约比铝合金高10倍。
3)
化学活性大。
钛可与空气中的氧、氮、一氧化碳、水蒸气等物质产生强烈的化学反应,在表面形成TiC及TiN硬化层。
导热性差。
钛合金导热性差,钛合金TC4在200℃时的热导率l=16.8W/m·
℃,导热系数是0.036卡/厘米·
秒·
℃。
1.刀具材料的选择
刀具材料选用应满足下列要求:
1)足够的硬度。
刀具的硬度必须要远大于钛合金硬度。
2)足够的强度和韧性。
由于刀具切削钛合金时承受很大的扭矩和切削力,因此必须有足够的强度和韧性。
3)足够的耐磨性。
由于钛合金韧性好,加工时切削刃要锋利,因此刀具材料必须有足够的抗磨损能力,这样才能减少加工硬化。
这是选择加工钛合金刀具最重要的参数。
4)刀具材料与钛合金亲合能力要差。
由于钛合金化学活性高,因此要避免刀具材料和钛合金形成溶敷、扩散而成合金,造成粘刀、烧刀现象。
2.精度、条件和正确的切削参数
经过对国内常用刀具材料和国外刀具材料进行试验表明,采用高钴刀具效果理想,钴的主要作用能加强二次硬化效果,提高红硬性和热处理后的硬度,同时具有较高的韧性、耐磨性、良好的散热性。
铣刀的几何参数
钛合金的加工特性决定刀具的几何参数与普通刀具存在着较大区别。
螺旋角β
选择较小的螺旋升角,排屑槽增大,排屑轻易,散热快,同时也减小切削加工过程中的切削抗力。
前角γ
切削时刃口锋利,切削轻快,避免钛合金产生过多切削热,从而避免产生二次硬化。
后角α
减小刀刃的磨损速度,有利于散热,耐用度也得到很大程度的提高。
切削参数选择
钛合金机加工应选择较低的切削速度,适当大的进给量,合理的切深和精加工量,冷却要充分。
切削速度Vc
Vc=30~50m/min
进给量f
粗加工时取较大进给量,精加工和半精加工取适中的进给量。
切削深度ap
ap=1/3d为宜,钛合金亲合力好,排屑困难,切削深度太大,会造成刀具粘刀、烧刀、断裂现象。
精加工余量αc适中钛合金表面硬化层约0.1~0.15mm,余量太小,刀刃切削在硬化层上,刀具轻易磨损,应该避免硬化层加工,但切削余量不宜过大。
3.钛合金的加工方法
(1)
将刀尖温升控制到最小程度
①切削速度不宜过高(40~60m/min)
切削速度过高会产生大量切削热,导致刀具寿命降低,因此应避免采用过高的切削速度。
②缩短刀具与工件的接触时间
刀具与工件接触时间越长,产生的热量就越多,会导致刀具寿命降低。
而刀具直径越大,接触时间就越长,因此在允许的范围内,应尽可能使用小直径刀具。
③不宜加大切削宽度
切削宽度越大,接触时间越长,会增加发热量。
因此,加工时不宜加大切削宽度,而通过增加切削长度来提高加工效率。
使用长刃刀具等对于粗加工很有效。
切削宽度小的台肩铣削能减少切削热,使提高切削速度成为可能。
④使用45°
主偏角刀具
只要工件形状允许,应尽可能使用45°
主偏角的刀具,以减薄切屑,延长刀具寿命。
⑤充分使用切削液,提高冷却效果
充分使用切削液,尤其是15MPa以上的超高压切削液,以降低刀尖温度、改善切屑处理效果、防止产生积屑瘤。
从而能够提高切削速度和生产率。
(2)提高刀具刚性
通过缩短刀具悬伸长度、增大刀具直径,可提高刀具刚性、减小刀具挠曲度。
在因工件形状必须采用较大悬伸量的场合,应用插铣加工也很有效。
(3)锯齿切削刃刀具的使用
由于锯齿切削刃可减小接触宽度,从而可减少热量的产生。
此外,切削液可从锯齿之间到达被切削面,因此锯齿切削刃刀具对钛合金的加工十分有效。
钛的各种属性使之成为具有强大吸引力的零件材料,但其中许多属性同时也影响着它的可加工性。
钛具备优良的强度-重量比,其密度通常仅为钢的60%。
钛的弹性系数比钢低,因此质地更坚硬,挠曲度更好。
钛的耐侵蚀性也优于不锈钢,而且导热性低。
这些属性意味着钛金属在加工过程中会产生较高和较集中的切削力。
它容易产生振动而导致切削时出现震颤;
并且,它在切削时还容易与切削刀具材料发生反应,从而加剧月牙洼磨损。
此外,它的导热性差,由于热主要集中在切削区,因此加工钛金属的刀具必须具备高热硬度。
4.稳定性是成功的关键所在
某些机加工车间发现钛金属难以有效加工,但这种观点并不代表现代加工方法和刀具的发展趋势。
之所以困难,部分是因为钛金属加工是新兴工艺,缺少可借鉴的经验。
此外,困难通常与期望值及操作者的经验相关,特别是有些人已经习惯了铸铁或低合金钢等材料的加工方式,这些材料的加工要求一般很低。
相比之下,加工钛金属似乎更困难些,因为加工时不能采用同样的刀具和相同的速率,并且刀具的寿命也不同。
即便与某些不锈钢相比,钛金属加工的难度也仍然要高。
我们固然可以说,加工钛金属必须采取不同的切削速度和进给量以及一定的预防措施。
其实与大多数材料相比,钛金属也是一种完全可直接加工的材料。
只要钛工件稳定,装夹牢固,机床的选择正确,动力合适,工况良好,并且配备具有较短刀具悬伸的ISO50主轴,则所有问题都会迎刃而解——只要切削刀具正确的话。
5.必须考虑振动和热
非理想环境还包含其它因素,其中之一就是,大多数机床目前装配的是IS040主轴。
如果高强度地使用机床,就无法长时间保持新刀状态。
此外,如果零件结构较复杂的话,通常就不易有效夹紧。
当然挑战还不止于此,切削工序有时必须用于全槽铣、侧削或轮廓铣削,所有这些都有可能(但并非必定)产生振动及形成较差的切削条件。
重要的是,在设定机床时,必须始终注意提高稳定性以避免振动趋势。
振动会造成刀刃崩碎、刀片损坏并产生不可预见和不一致的结果。
一种改进措施便是采用多级夹紧,使零件更靠近主轴以有助于抵消振动。
钛合金的优点:
①重量轻;
②比强度高;
③耐金属疲劳;
④化学性能稳定。
钛合金的缺点:
①切削加工性差;
②温度超过400℃则强度降低(因此用于发动机的低温部分)。
钛和钛合金塑性加工具有变形抗力大;
常温塑性差、屈服极限和强度极限比值高、回弹大、对缺口敏感、变形过程易与模具粘结、加热时又易吸咐有害气等特点,塑性加工较钢、铜困难。
故钛和钛合金的加工工艺必须考虑它们的这些特点。
国外钛合金的研究与发展
(2009-09-14)
来源:
中国船舶在线
阅读次数:
213次
大力发展钛工业对巩固国防和国民经济建设具有极其重大的战略意义。
本文对国外钛合金的研究现状及发展、国外钛合金加工工艺研究及钛合金的应用等情况进行了综述。
钛是50年代以后登上世界工业舞台的年轻金属,具有储氢、超导、耐蚀、重量轻、形状记忆、超弹和高阻尼等特殊功能,是新型的功能材料和重要的生物材料。
从工业价值、资源寿命和发展前景看,它是继铁、铝之后,被誉为正在崛起的“第三金属”。
大力发展钛工业对巩固国防和国民经济建设具有极其重大的战略意义,世界各国的经济发展表明,先进的钛工业是综合国力的重要标志。
钛合金的研究与发展
国外钛工业主要集中在美国、俄罗斯和日本三个国家。
由于军事需求减少,近10年来世界钛材产量一直徘徊在5万吨左右。
在生产技术方面,克劳尔法仍是生产海绵钛的主导工艺。
电子束冷床炉熔炼技术已在钛铸锭的制备上进行了商业化应用,大型锻件和精密锻造技术正在不断地发展,激光成型等近净成型技术正在不断地得到应用。
一些常规加工技术如锻造、轧制等已完全实现了计算机自动控制,人工神经网络模型在钛合金中的应用解决了一些钛合金的实际问题。
有报道说,钛生产厂家发现钛很难进入其它市场的主要原因是价格太高。
在美国,海绵钛的平均价为3.8美元/磅,而在俄罗斯是3.2美元/磅。
而且民用飞机制造工业还有一个周期问题直接影响钛的价格。
FFC–剑桥法是一种新的生产钛金属或合金的低成本电解法。
世界上钛的生产仅限于部分工业国家,海绵钛只有美国、哈萨克斯坦、俄罗斯、日本和中国5国生产,大约有20多家海绵钛厂;
加工材有美、日、俄、英、德、法、意、中8国生产。
全世界海绵钛的生产能力约为11万吨,产量约8万吨。
钛铸锭的熔炼能力为22万吨,钛加工材的生产能力约为23万吨。
目前,世界钛技术的发展趋势为:
钛的低成本化制备、加工技术,包括海绵钛生产、钛合金材料设计及加工过程等的低成本化;
大型优质钛合金坯料制备技术,包括新型电子束和等离子冷床炉熔炼技术;
高效、短流程钛合金加工技术,包括单次冷床炉熔炼直接轧制技术,钛带连续加工技术生产等;
近净成型技术,包括激光成形、精密铸造、精密模锻、超塑成型/扩散连接、喷射成形等;
钛的推广应用技术,包括生物医用钛、汽车用钛、建筑用钛等。
钛合金加工工艺研究
1.钛合金机加工特性分析
首先,钛合金导热系数低,仅是钢的1/4,铝的1/13,铜的1/25。
因切削区散热慢,不利于热平衡,在切削加工过程中,散热和冷却效果很差,易于在切削区形成高温,加工后零件变形回弹大,造成切削刀具扭矩增大、刃口磨损快,耐用度降低。
其次,钛合金的导热系数低,使切削热积于切削刀附近的小面积区域内不易散发,前刀面摩擦力加大,不易排屑,切削热不易散发,加速刀具磨损。
最后,钛合金化学活性高,在高温下加工易与刀具材料起反应,形成溶敷、扩散,造成粘刀、烧刀、断刀等现象。
国外钛及其合金加工的主要企业是美国Timet公司、RMI公司、俄罗斯的VSMPO公司,日本的神户制钢和住友公司,他们代表了世界钛及其合金加工材生产技术的最高水平。
美国的钛及其合金锭约60%以先进的等离子或电子束冷床炉进行生产,其扁形锭可直接轧制板材,美国RMI公司和Timet全面掌握丁TC4薄板(厚度为0.4毫米–0.5毫米)的生产技术,其产品已在波音和空客公司得到大量应用。
美国和俄罗斯采用挤压、法生产钛合金型材,已在飞机和舰艇上得到广泛应用,俄罗斯甚至可以用挤压+脉冲缎打的方法生产薄壁钛合金型材。
从钛及其台金锭到成品零部件,其成品率仅10%–20%,因此残钛及其合金的回收利用,就成了降低成本,扩大应用的关键。
美国有5家专业的残废钛料的回收处理企业,有专门的设备,专门的技术,大规模、高自动化地从事残废钛的回收处理,其产品通过航空级认证,回收生产的钛材可以重新用于航空产品的生产。
2.钛合金特种加工技术
(1)激光加工技术
利用高功率密度的激光束照射工件,使材料熔化气化而进行穿孔、切割和焊接等的特种加工,英文简称LBML–I。
国外激光加工设备和工艺发展迅速,现已拥有100千瓦的大功率CO:
激光器、千瓦级高光束质量的Nd:
YAG固体激光器,有的可配上光导纤维进行多工位、远距离工作。
激光加工设备功率大、自动化程度高,已普遍采用CNC控制、多坐标联动,并装有激光功率监控、自动聚焦、工业电视显示等辅助系统。
激光表面重熔是一种好的方法,可提高钛的点蚀抗力,扩大钛在苛刻环境中的应用范围。
激光制孔的最小孔径已达0.002毫米,成功地应用自动化六坐标激光制孔专用设备加工航空发动机涡轮叶片、燃烧室气膜孔,达到无再铸层、无微裂纹的效果。
激光切割适用于由耐热合金、钛合金、复合材料制成的零件。
目前薄材切割速度可达15米/分钟,切缝窄,一般在0.1毫米–1毫米之间,热影响区只有切缝宽的10%–20%,最大切割厚度可达45毫米,已广泛应用于飞机三维蒙皮、框架、舰船船身板架、直升机旋翼、发动机燃烧室等。
使用激光直接沉积制造先进材料,激光直接制造实现了高能密度热源,粉末金属原料和在近净成型中用计算机驱动机器控制来生产大块材料。
粉末冶金和快速固化工艺相结合允许生产具有新成分和独特性质的大块结构材料。
(2)电子束加工技术
电子束加工是利用高能量的会聚电子束的热效应或电离效应对材料进行的加工。
例如对材料表面进行热处理、焊接、刻蚀、钴孔、熔炼或直接使材料升华。
电子束加工技术在国际上日趋成熟,应用范围广。
国外定型生产的40kV–300kV的电子枪(以60kV、150kV为主),已普遍采用CNC控制,多坐标联动,自动化程度高。
电子束焊接己成功地应用在特种材料、异种材料、空间复杂曲线、变截面焊接等方面。
目前正在研究焊缝自动跟踪、填丝焊接、非真空焊接等,最大焊接熔深可达300毫米,焊缝深宽比20:
1。
电子束焊已用于运载火箭、航天飞机等主承力构件大型结构的组合焊接,以及飞机梁、框、起落架部件、发动机整体转子、机匣、功率轴等重要结构件和核动力装置压力容器的制造。
如:
F-22战斗机采用先进的电子束焊接,减轻了飞机重量,提高于整机的性能;
“苏–27”及其它系列飞机中的大量承力构件,如起落架、承力隔框等,均采用了高压电子束焊接技术。
国外真空电子束物理气相沉积技术,已用于航空发动机涡轮叶片高温防腐隔热陶瓷涂层,提高了涂层的抗热冲击性能及寿命。
电子束刻蚀、电子束辐照固化树脂基复合材料技术正处于研究阶段。
(3)离子束及等离子体加工技术
聚焦离子束的工作原理是利用聚焦后的离子束扫描样品表面,通过检测从样品中被激发出的二次电子,形成二次电子像进行观测。
在扫描过程中,因为离子有着较大的质量,同时可以对样品进行加工。
表面功能涂层具有高硬度、耐磨、抗蚀功能,可显著提高零件的寿命,在工业上具有广泛用途。
美国及欧洲国家目前多数用微波ECR等离子体源制备各种功能涂层。
等离子体热喷涂技术已经进入工程化应用