奇瑞整车开发流程DOC文档格式.docx
《奇瑞整车开发流程DOC文档格式.docx》由会员分享,可在线阅读,更多相关《奇瑞整车开发流程DOC文档格式.docx(30页珍藏版)》请在冰豆网上搜索。
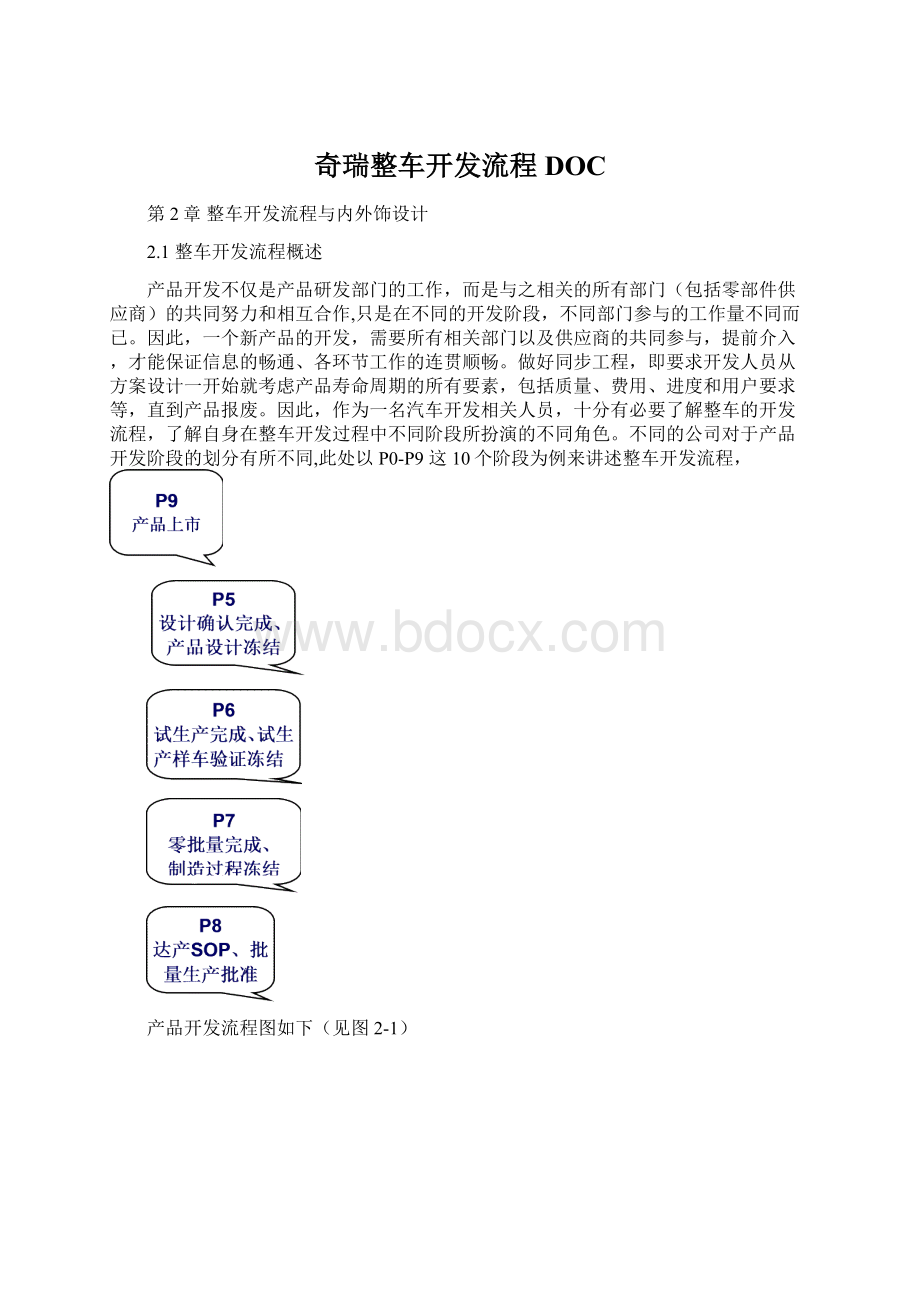
有了概念设计,再结合造型效果图即可进行相关技术可行性分析,如效果图上仪表板是否存在制造工艺完全不可能实现的造型,或者是否存在四个部件匹配产生的“老鼠洞”;
同时在第一轮总布置图上特别去关注布置在仪表台上的各种操作件,如组合仪表、开关、换挡等是否满足相关法规和人机工程。
总之,在整车规划阶段,产品工程师介入的越早,发现问题也会越早,对于规避原则性问题、重大问题有很好的预防作用,同时亦能打好后期详细设计的基础,做到设计工作有的放矢、不盲目,避免造成产品设计的先天不足,对后期工作开展有利无弊。
2.1.2先期整车开发阶段
先期整车开发阶段一般是P2阶段(见图2-3),即项目启动。
开始进行油泥制作至冻结,该阶段概念设计如效果图、造型、总布置方案等得到批准;
规划部门开始策划总体工艺路线,制定初始设备、设施、工装等清单;
采购部门会制作潜在供应商目录、进行供应商询价等;
销售部门会对产品概念的市场进行验证。
在该阶段,油泥等造型方案会根据市场需求及技术可行性分析结果反复修改,最终会得到确认,设计人员也将启动并完成部分零部件初始设计。
由于造型设计是整车设计中确定产品形象的过程,是汽车参与市场竞争的重要因素,是整车设计非常重要且最具创造性的工作,也是工程设计与美工设计完美结合的产物,一方面造型设计应适合时代特点和人类的审美爱好,另一方面,造型设计又要满足结构强度的要求和整车布置设计的要求,满足车身空气动力学的要求和适应各种材料技术的发展,可以说该阶段是产品技术与艺术技巧高度交融的结晶。
内外饰是除了车身之外与造型关系最为密切的模块,产品工程师在该阶段需要与造型工程师保持良好的信息沟通,一方面通过详细设计去尽量满足造型师的意图,另一方面及时向造型师提出工艺或结构难以实现的困难并给予合理的优化建议。
同时,该阶段总布置初始方案已经确定,完成如H点等重要设计硬点、内/外部空间主要尺寸、法规校核、主要部件布置分析等;
产品性能确定并分解,结合造型及总布置进行总体工艺可行性分析以及产品技术方案的可行性分析,期间会运用设计软件(CATIA/CAD等)、计算机辅助设计(CAE)、潜在失效模式及影响分析(DFMEA)、设计验证计划(DVP)等工具,将在第三章着重介绍。
产品工程师在此阶段非常重要的工作即对造型和主断面进行可行性分析,比如通过关键零部件的典型断面,校核组合仪表是否反光,A柱障碍角是否满足法规,方向盘是否挡组合仪表的视野,前后排假人的头部空间,驾驶员的腿部空间,开启前舱盖的人机性等等;
还可以通过典型断面定义各个关联件的配合方式,比如前舱盖与保险杠和大灯的配合关系,立柱护板与密封条以及顶棚的搭接方式,这些断面输入给造型师,可以对造型细节进行优化,以便将来的产品结构设计更加合理,满足制造要求,并达到良好的外观匹配效果。
图2-3P2阶段流程简图
2.1.3整车项目开发阶段
进入到整车项目开发阶段,此阶段一般包括P3-P9(见表2-1),即进入产品设计的实质性阶段,经过设计、验证、设计确认、试制生产等过程直至产品上市,以下将按照新车设计开发流程进行概述。
表2-1P3-P9节点定义及交付物
节点
P3
整车设计
完成
P4
设计验证
P5
设计确认
P6
试生产
P7
零批量
P8
达产SOP
P9
产品
上市
交付物
数字
样车
设计确认样车
生产试制
批量车
(PVS车)①
零批量车
(0S车)②
批量生产车(SOP车)③
项目终结报告
①PVS车:
使用100%工装模具生产的零件和部分生产件批准程序批准的外购件装配,用试生产控制计划控制,在生产线上但非生产节拍生产的非销售整车。
②0S车:
使用100%生产件批准程序批准的零件装配、正式的生产工装、正式生产控制计划控制、连续生产线上,按正式生产节拍在一定时间内生产一定量的可带条件销售整车.
③SOP车:
按正式生产控制计划控制、正式生产节拍等正常生产条件和定单需求下制造的销售整车。
1.整车设计完成
该阶段用虚拟手段将零部件组成整车,一般是指P3阶段(见图2-4)。
验证产品设计的可行性,并获得工艺部门的认可,是整车数据设计完成的节点;
产品设计已经提供了对产品和零部件的所有要求和细节,不会发生重大的设计更改,几乎所有部门都要介入对数据设计的评价和确认。
比如销售部门对备件可维修性进行分析,并根据市场需求对产品提出改进要求;
规划部门针对设计数据进行过程设计和生产准备,如装配工艺、工位布局、过程控制点、设备工装及设施清单、技术要求等等;
采购部门会依据技术方案、成本分析、质量评估进行供应商询价和敲定零部件供应商;
质量部门会针对售后市场及历史常见问题核查新车数据质量,全程监控数据设计及过程设计质量,综合评估项目风险。
图2-4简单显示了P3阶段的主要工作。
设计部门在该阶段投入大量精力对整车及零部件进行详细的数据设计,根据A面和典型断面完成详细的结构设计,形成一版工艺数模,主要用于定位点讨论和结构分析,启动检具、夹具、模具的概念设计,方便供应商介入,同时根据产品设计任务的标准和技术要求与供应商签署技术合同,借助专业零部件供应商的结构设计及分析能力,对数据进行工艺分析,以确保数据的可加工性。
最终经过校核完成的试制正式数模将用于模具正式设计,可以进行制造手工样件和试制模具。
该阶段有两个非常重要的原则是:
1.整车三维数据均具规模,虽然前期做过布置及空间分析,但仍需对所有关联件三维数据进行装配和校核,要求相关设计人员保持数据传递及时、最新和完整。
比如在典型断面中有线束的布置,但由于线束属于柔性体,如果仅仅在某些位置的断面中体现而不在三维数据中完整体现,很容易出现与其他覆盖件的配合问题。
2.数据设计的过程不是单一的建模操作,需要融入众多的可行性分析和反复的校核,因此在设计过程中数据评审的工作尤为重要,一方面借助如CAE分析、校核规范等工具进行全面性校核,另一方面需要针对常见历史问题进行逐一排查,还需要有丰富设计和试制经验的工程师参与校核并提出宝贵意见,这样不仅能全方位规避设计问题,还能将数据设计最优化。
图2-4P3阶段流程简图
2.设计验证完成
为了验证设计,一般是指P4阶段(见图2-5),保证正式模具最低风险的投入,在该阶段会完成一轮样车试制,根据试制数模,进行手工样件的制作、试制模具的制造,包括两方面的验证:
(1)零部件产品设计验证:
如材料试验验证、尺寸匹配验证、功能件可靠性试验验证,主要是对产品的尺寸设计、结构设计、功能定义等进行验证,评估过程中如果发现设计问题,将由设计部门提出整改方案、优化设计,将P3阶段的试制数据进行更改后,最终将设计数据冻结,以开始正式模具的制作。
同时,有一部分简单、制作周期相对较短的零部件很快会得到设计验证的确认,会立即进行模具制作,进而在后续的试制样车过程中可以提供正式模具件。
(2)整车设计验证:
周期较长的系统匹配试验可以在该阶段根据设计验证计划进行匹配验证。
由于试制样件的种类较多,有手工件、CNC加工件、软模件等等,整车验证项目中需要装配对实验结果不造成影响的样件。
比如空调系统的环境模拟试验,对风管风口等塑料件强度无要求,只需尺寸满足设计状态,所以提供CNC加工件即可,后续章节中会进行详细介绍。
在该阶段参与的部门与P3阶段雷同,只不过参与的是对试制样车的评价和确认,更为直观和准确,比如规划部门可以根据试制样车的装配过程,制定将来生产线上的工艺装配路线。
图2-5P4阶段流程简图
3.设计确认样车
经历了设计验证阶段,正式模具已经投入,工装样件陆续提供。
该阶段主要是设计确认样车一般是指P5阶段(见图2-6),完成规定的试验项目,发现的问题已查明原因,产品设计更改完成,产品设计冻结,工艺设计完成,开始对用于批量工装生产的零件进行认可。
图2-6P5阶段流程简图
4.生产试制小批量阶段
生产试制小批量阶段,一般是指P6阶段。
这是一种批量生产练习,所有的单件和总成件都到位,并都是用批量生产的设备及工装模具、试生产控制计划制造出来的件;
对作业人员进行理论、线下、线上的培训,整个生产过程可以在不连续的条件下进行生产,从而对各工序加工能力、生产设备、试生产控制计划是否适当以及生产线的制造可行性、装配可行性、通过性、批量生产的适应性进行实际验证,获得哪些设备和过程可以确保所有要求的批量节拍和质量要求。
若发现薄弱环节必须在零批量生产启动前得到消除,其主要目的是通过生产的试运行来对其批量生产和确保产品质量进行验证,这个阶段小批量试制的车主要用来提供特定评价用车和培训用车,以及用于部分系统验证试验的整车或路试车。
同期,应该完成对整车和零部件的认证工作。
在这个阶段,会暴露很多可能在批量生产过程中出现的问题,比如流水线零部件装配困难会影响到生产节拍,需要对产品结构进行更改或者调整装配顺序,进而对已经认可的产品进行设计变更。
同时,在P5阶段会遗留一部分制作或试验周期较长的零部件在P6阶段继续进行相关认可工作,最终需要完成所有零部件的工装样件认可。
质量和采购部门启动生产件批准程序的工作,对零部件供应商进行相关审核。
销售部门开始进行上市研究,制定维修手册、备件手册,进行服务培训等等。
5.零批量和批量阶段
零批量阶段一般是指P7/P8阶段。
是在批量生产条件下,按规划的批量生产节拍进行批量生产前的总演习。
其前提条件是外购件都成功通过了批量条件的两日生产验收(供应商批量生产前的总演习,来考察供应商是否能够确保其在批量生产运行进度下保持良好的供货状态);
生产线、装配线、物流和各验收区域都已经达到了批量生产状态,整个系统如生产、物流、质量保证、人员培训都按照批量的要求接受检查。
该阶段主机厂会对外协件进行生产件批准(即PPAP)。
批量阶段即所有要求的各种认可都已获得;
车型检验和型式认证已经成功完成并获得政府部门的使用批准;
所有小批量阶段、零批量阶段的问题都已经得到了解决;
整个生产线都具有批量能力,所有零部件都已经供应到位,整个生产线能按照设计节拍、正式控制计划等正常条件下连续生产可销售状态的整车。
不论是零批量还是批量阶段,一旦发现设计或质量问题,均需要对产品进行相应变更和切换工作。
6.市场导入—P9阶段
市场导入一般是指P9阶段。
该阶段产品正式上市获得批准,按既定销售策略和方案进行导入市场。
对于整车项目开发阶段来说可以画一个句号,这时会对项目目标和实际情况进行总结和评价,分享经验和教训,为下一款新车开发做充分的积累。
产品上市后,难免会出现一些售后问题,还有批量生产中也会暴露一些过程质量问题,因此市场问题与批量过程问题的发现与解决仍需要相关部门的配合工作,需要对出现的问题进行整改,进而做产品变更和批量切换。
各大主机厂为了提高产品竞争力,会在产品上市后某个特定阶段提出改款需求,比如精细化提升、特定市场适应性开发、年型车改款等等,为满足这些需求将会重新成立项目组,但不同于整车开发,而是在沿用底盘、发动机等平台的前提下,仅从P2阶段开始重新对车身或内外饰造型,开发流程与整车相似,在此不再详述。
本节主要介绍了整车开发流程,下面将针对整车开发流程中的内外饰设计进行着重介绍。
2.2整车概念设计中的内外饰设计
概念设计(又称造型设计)属于产品设计的前期工作,是在产品目标设定之后,指从产品构思到确定产品设计指标(性能指标)、确定造型和总布置定型、并下达产品设计任务书为止这一阶段的设计工作。
按照整车P0-P9的开发节点,概念设计阶段主要是P2阶段,概念设计在汽车内外饰设计中,尤其是内饰设计中占有极其重要的地位。
现代汽车的概念设计(造型设计)的主要流程如下图2-7:
图2-7造型设计主要流程
2.2.1前期定义
1.标杆分析
做任何设计都不能从零开始,都需要有一定的积累。
汽车内外饰设计也是如此。
一百多年的汽车制造史,给我们留下了丰厚的积淀,给我们积累了宝贵的经验和教训。
这些积淀部分体现在书本中,但从汽车产品中体现得更加形象直观,尤其是最新的产品。
我们获取这些知识的最有效的办法就是使用标杆比对。
世界汽车行业部分后进而崛起的汽车企业当年一般都曾用过此类方法。
首先购买几款不同厂家的同类型汽车,然后解体测量,分析收集相关数据,最后根据自己设计的车型定位,进行分析借鉴和应用。
一般标杆车分析,根据产品细节的不同所做的分析科目也不同,但总的方向大致相同,一般包括:
间隙面差的测量,细部结构分析(包括安装点的布置/产品定位/特殊结构等),布置空间,操作舒适性,可维修性等。
下表(见表2-2)是一个立柱护板系统竞争分析的简单概述。
表2-2标杆分析示例
立柱护板系统-左A柱上护板
结构图
材料
重量/g
料厚/mm
制造工艺
紧固方式
固定座形状
紧固力矩/(N·
m)
紧固件类型
典型截面
与边界的配合
与顶棚的配合方式,搭接距离
与仪表板本体的配合方式
与玻璃黑边的距离
在造型设计时,就要对标杆车型进行分析。
此阶段对于标杆车型分析,主要是针对零部件的结构设计、间隙面差、安装点的布置、目标市场、配合概念等的分析。
对于仪表板来说,欧标与美标的头部碰撞区域的划分方法及测试方法就有着很大的差异,而膝部保护、除霜除雾要求等也是如此。
对零部件的配合结构等的分析,不同车型的结构相差也很大,我们要通过对竞争车型的结构进行分析,找出其优缺点,来优化我们的结构设计等等。
比如说立柱护板的配合结构,目前比较流行的结构有对接结构和搭接结构,对接结构对零件本身和车身焊接精度等要求比较高,需要控制多个方向的配合;
但搭接结构相对对接来说要好控制一些,对车身等的要求也低一点;
如B柱上下护板的配合,对接要控制Y和Z向的配合,而搭接只要控制Y向的配合就可以了。
具体请见图2-8和图2-9。
图2-8对接结构图2-9搭接结构
2设计构想
汽车造型确定后,就可以着手进行汽车结构设计。
但在开始结构设计之前,先对A面进行分析,阶次、曲率等参数是否满足设计要求,并且分析此内饰面拔模角度是否足够。
汽车的结构设计,是确定汽车整车、部件(总成)和零件的结构。
也就是说,设计师需要考虑由哪些零件组合成部件,又由哪些部件组合成整车。
零件是构成产品的最基本的、不可再分解的单元。
毫无疑问,零件设计是产品设计的根基。
零件设计时,首先要考虑这个零件在整个部件中的作用和要求;
其次,为了满足这个要求,零件应选用什么材料和设计成什么形状;
最后,零件如何与部件中其他零件相互配合和安装。
作为设计师,必须充分考虑零件的受力情况,经过周密的计算,确保零件的强度和刚度的数值在允许的范围内。
3目标设定及造型输入
在新车型的开发设计中,一些原则性的问题必须在产品设计正式展开以前加以明确,从而做到设计工作有的放矢,避免产品设计的先天不足。
在概念设计阶段应明确一些指导产品设计的原则性问题,明确产品的目标设定。
这些原则性问题一般包括以下内容:
新车型的开发目标,开发的必要性与可行性,产品的基本型式、系列产品发展规划,产品投放市场及相关交通法规,汽车标准、法规及发展动向,生产纲领,产品的设计水平,产品的造型、内部布置及结构要求,未来市场上的竞争力等各个方面。
一般造型输入是将整车的关键性指标进行约束,根据整车的目标客户,来定义整车的风格。
包括整车的舒适性,操作空间的方便性,需要满足的法规要求等。
表2-3是内外饰造型输入的一个简单列举。
表2-3内外饰造型输入要求
造型输入要求
名称
重要度级别
布置空间
驾驶员最大有效腿部空间
☆
方向盘最大直径
驾驶员有效的头部空间(带/不带天窗)
PRP到方向盘中心的距离
☆☆
方向盘最后端至躯干线的距离
脚踵点到方向盘中心的水平距离
方向盘至大腿的距离
方向盘安装角度
H点的水平移动行程,H点的垂直移动行程
前排座椅的角度调节范围
两R点间的距离
进入方便性
前排脚部进入空间
后排脚部进入空间
前排进车门高度
舒适性
方向盘中心至踵点的垂直距离
第二排乘员腿部空间
第二排有效头部空间
第二排最小乘座空间
☆☆☆
第二排膝部空间
第二排肘部空间(扶手处的整车宽度)
前排座椅深度
第二排座椅深度
前排有效坐垫深度
第二排有效坐垫深度
法规要求
前方视野要求
行人保护要求
内部突出物/外部突出物
前后座椅的高度范围
A柱障碍角
对内外饰造型设计来说,舒适性和操作空间是比较关键的要素。
因此对关键要素的约束值及经验值的输入要做到清晰明确。
下图(图2-10)是对座椅人机舒适性的一个简单的输入(图中的输入要求仅是参考值)。
图2-10座椅人机造型输入
2.2.2造型设计
1.草图设计
草图设计主要使用手绘方式来表现设计师的基本构思及造型的初步效果,可以是单纯用线条表示的白描方式,也可以带色彩,一般都比较粗糙,只是基本原始概念的体现,是设计的开始阶段。
一个整车外饰草图一般都是三张视图,至少要有两张前后2/3视角的草图(如图2-11所示)。
图2-11草图
2渲染效果图
渲染效果图,主要是在草图的基础上进行细化,尽量做到逼真的效果。
表现手法有手绘,电脑绘制,手绘和电脑的结合,目前常用的表现手法是手绘和电脑的结合。
手绘是比较原始的表现技法,主要工具是使用色粉,马克笔,颜料,彩色铅笔等。
电脑使用的主要软件有:
Photoshop,3D–MAX,ALIAS等。
一般先手绘出主要的大纲轮廓线和结构线,再扫描进电脑用Photoshop进行处理,一张比较细致的效果图都要体现造型的关键点(如图2-12所示)。
图2-12仪表板渲染效果图
3计算机辅助造型设计(CAS)
计算机辅助造型设计,是现代造型设计中的新应用。
主要是根据造型要求的硬点及相关数据布置要求,用一些计算机软件如ALIAS,按照效果图生成一个三维的数字模型,用来进行相关的布置及法规的校验。
4模型
模型主要包括油泥模型和验证模型。
油泥模型就是根据造型效果体现的实物。
一般有1:
1和1:
5两种。
虽然现代科技技术发达,但是制作油泥模型依然是汽车设计生产中的必要环节。
油泥是一种类似橡皮泥的黏土,成型的细节需要用刀刮削才能完成。
一般先要制作比例小的油泥模型作为提案,通常由设计师亲自操刀,一般的周期大约2~3个月(如图2-13所示)。
图2-13油泥模型制造
验证模型是当硬模型做完后,按照造型效果进行喷涂,就得到了验证模型,验证模型就是平常所说的数字样车,以后的真车便是在验证模型的基础上来进行开模和验证的。
2.2.3初步可行性分析
1.造型可行性分析
造型效果完成后,要经过不断的评审优化并最终确定产品造型。
然后通过做油泥和扫描,进行数字模型的优化,进行一系列的可行性分析和校核,大体内容如下简介。
2.内饰法规可行性分析
根据车型所定义的不同市场进行相关法规的校核。
例如满足北美市场的车要符合FMVSS和IIHS标准,满足欧洲市场的车要符合ECE和EEC标准,国内市场的车要满足GB的标准要求等。
满足法规要求是整车设计的最低门槛。
例如仪表板系统和方向盘系统要满足中国国标要求,设计校核和相关实验中一般要考虑到如下标准(见表2-4)
表2-4
仪表板
1
GB11552-1999
轿车内部凸出物
2
GB11562-1994
汽车驾驶员前方视野要求及测量
3
GB11556
风窗玻璃除霜系统的性能要求
4
GB8410-2006
汽车内饰材料的燃烧特性
5
GB16735
道路车辆车辆识别代码(VIN)
方向盘
GB11557-1998
汽车防止汽车转向机构对驾驶员伤害的规定
GB11551