钻镗专用机床液压系统课程设计Word下载.docx
《钻镗专用机床液压系统课程设计Word下载.docx》由会员分享,可在线阅读,更多相关《钻镗专用机床液压系统课程设计Word下载.docx(24页珍藏版)》请在冰豆网上搜索。
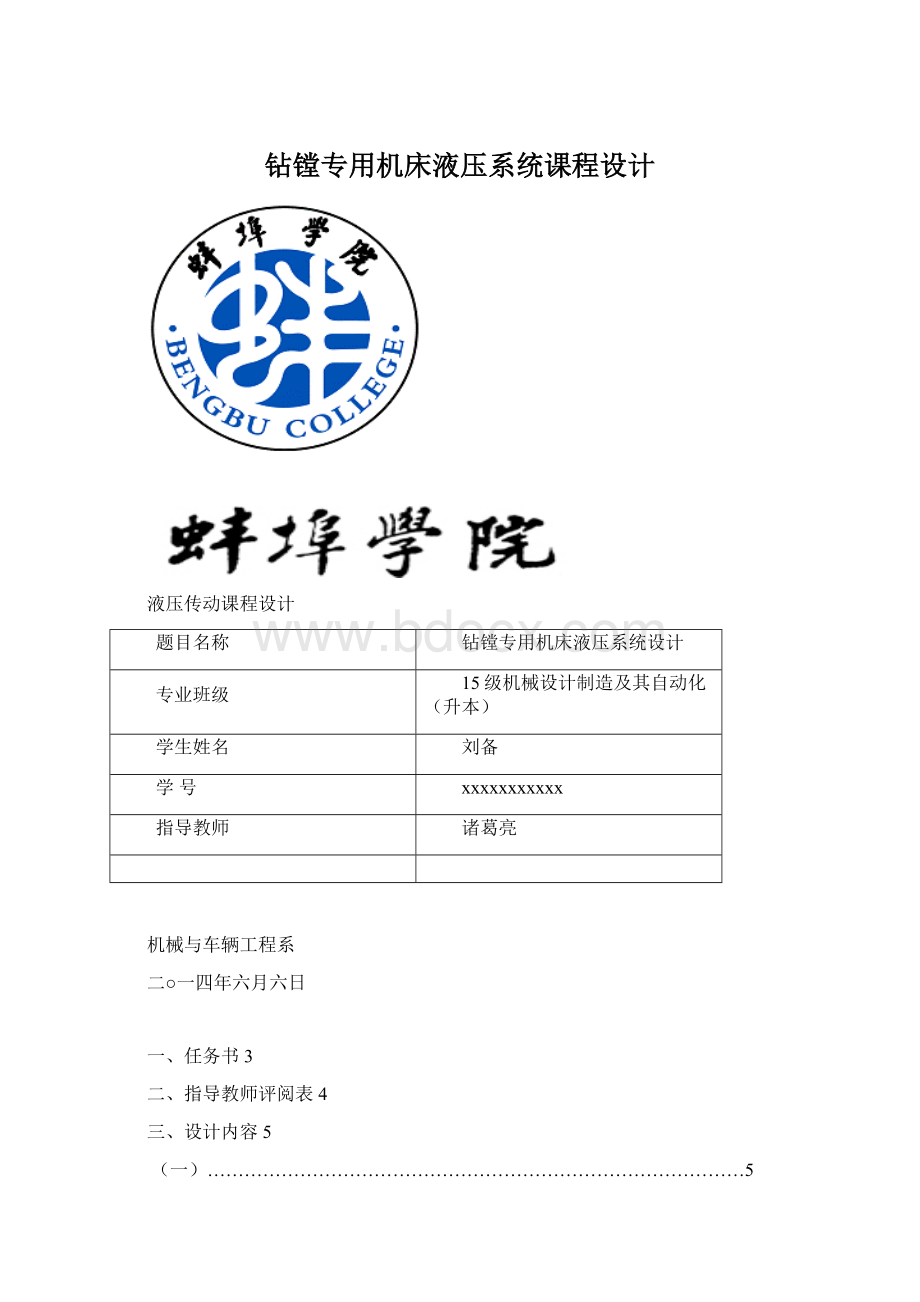
XXXXXXX
课题名称
指导教师评语:
指导教师(签名):
2016年6月16日
评定成绩
引言
液压系统已经在各个部门得到越来越广泛的应用,而且越先进的设备,其应用液压系统的部门就越多。
液压传动是用液体作为来传递能量的,液压传动有以下优点:
易于获得较大的力或力矩,功率重量比大,易于实现往复运动,易于实现较大范围的无级变速,传递运动平稳,可实现快速而且无冲击,与机械传动相比易于布局和操纵,易于防止过载事故,自动润滑、元件寿命较长,易于实现标准化、系列化。
液压传动的基本目的就是用液压介质来传递能量,而液压介质的能量是由其所具有的压力及力流量来表现的。
而所有的基本回路的作用就是控制液压介质的压力和流量,因此液压基本回路的作用就是三个方面:
控制压力、控制流量的大小、控制流动的方向。
所以基本回路可以按照这三方面的作用而分成三大类:
压力控制回路、流量控制回路、方向控制回路。
第1章明确液压系统的设计要求
第二章负载与运动分析
负载分析中,暂不考虑回油腔的背压力,液压缸的密封装置产生的摩擦阻力在机械效率中加以考虑。
因工作部件是卧式放置,重力的水平分力为零,这样需要考虑的力有:
夹紧力,导轨摩擦力,惯性力。
在对液压系统进行工况分析时,本设计实例只考虑组合机床动力滑台所受到的工作负载、惯性负载和机械摩擦阻力负载,其他负载可忽略。
(1)工作负载FW
工作负载是在工作过程中由于机器特定的工作情况而产生的负载,对于金属切削机床液压系统来说,沿液压缸轴线方向的切削力即为工作负载,即
Ft=120000N
(2)阻力负载
阻力负载主要是工作台的机械摩擦阻力,分为静摩擦阻力和动摩擦阻力两部分。
导轨的正压力等于动力部件的重力,设导轨的静摩擦力为
,则
静摩擦阻力
动摩擦阻力
(3)惯性负载
最大惯性负载取决于移动部件的质量和最大加速度,其中最大加速度可通过工作台最大移动速度和加速时间进行计算。
已知启动换向时间为0.05s,工作台最大移动速度,即快进、快退速度为4.5m/min,因此惯性负载可表示为
如果忽略切削力引起的颠覆力矩对导轨摩擦力的影响,并设液压缸的机械效率
=0.9,根据上述负载力计算结果,可得出液压缸在各个工况下所受到的负载力和液压缸所需推力情况,如表1所
表1液压缸总运动阶段负载表(单位:
N)
工况
负载组成
液压缸负载F/N
液压缸推力
启动
4400
4889
加速
3134
3482
快进
2200
2444
工进
24200
26889
快退
反向启动
制动
1265.58
1406.2
第三章负载图和速度图的绘制
负载图按上面数值绘制,如下图a所示。
速度图按已知数值
和工进速度
绘制,如下图b所示
图a负载图
图b速度图
第四章确定液压系统主要参数
4.1确定液压缸工作压力
由表2和表3可知,组合机床液压系统在最大负载约为12000N时宜取3MP。
表2按负载选择工作压力
负载/KN
<
5
5~10
10~20
20~30
30~50
>
50
工作压力/MPa
0.8~1
1.5~2
2.5~3
3~4
4~5
≥5
表3各种机械常用的系统工作压力
机械类型
机
床
农业机械
小型工程机械
建筑机械
液压凿岩机
液压机
大中型挖掘机
重型机械
起重运输机械
磨床
组合机床
龙门刨床
拉床
0.8~2
3~5
2~8
8~10
10~18
20~32
表4执行元件背压力
系统类型
背压力/MPa
简单系统或轻载节流调速系统
0.2~0.5
回油路带调速阀的系统
0.4~0.6
回油路设置有背压阀的系统
0.5~1.5
用补油泵的闭式回路
0.8~1.5
回油路较复杂的工程机械
1.2~3
回油路较短且直接回油
可忽略不计
表5按工作压力选取d/D
≤5.0
5.0~7.0
≥7.0
d/D
0.5~0.55
0.62~0.70
0.7
表6按速比要求确定d/D
2/1
1.15
1.25
1.33
1.46
1.61
2
0.3
0.4
0.5
0.55
0.62
0.71
注:
1—无杆腔进油时活塞运动速度;
2—有杆腔进油时活塞运动速度。
4.2计算液压缸主要结构参数
由于工作进给速度与快速运动速度差别较大,且快进、快退速度要求相等,从降低总流量需求考虑,应确定采用单杆双作用液压缸的差动连接方式。
通常利用差动液压缸活塞杆较粗、可以在活塞杆中设置通油孔的有利条件,最好采用活塞杆固定,而液压缸缸体随滑台运动的常用典型安装形式。
这种情况下,应把液压缸设计成无杆腔工作面积
是有杆腔工作面积
两倍的形式,即活塞杆直径d与缸筒直径D呈d=0.707D的关系。
工进过程中,当孔被钻通时,由于负载突然消失,液压缸有可能会发生前冲的现象,因此液压缸的回油腔应设置一定的背压(通过设置背压阀的方式),选取此背压值为p2=0.8MPa。
快进时液压缸虽然作差动连接(即有杆腔与无杆腔均与液压泵的来油连接),但连接管路中不可避免地存在着压降
,且有杆腔的压力必须大于无杆腔,估算时取
0.5MPa。
快退时回油腔中也是有背压的,这时选取背压值=0.6MPa
。
工进时液压缸的推力计算公式为
,
式中:
F——负载力
m——液压缸机械效率
A1——液压缸无杆腔的有效作用面积
A2——液压缸有杆腔的有效作用面积
p1——液压缸无杆腔压力
p2——液压有无杆腔压力
因此,根据已知参数,液压缸无杆腔的有效作用面积可计算为
液压缸缸筒直径为
mm
由于有前述差动液压缸缸筒和活塞杆直径之间的关系,d=0.707D,因此活塞杆直径为d=0.707×
112.63=79.63mm,根据GB/T2348—1993对液压缸缸筒内径尺寸和液压缸活塞杆外径尺寸的规定,圆整后取液压缸缸筒直径为D=115mm,活塞杆直径为d=80mm。
此时液压缸两腔的实际有效面积分别为:
工作台在快进过程中,液压缸采用差动连接,此时系统所需要的流量为
工作台在快退过程中所需要的流量为
工作台在工进过程中所需要的流量为
q工进=A1×
v2=0.59L/min根据上述液压缸直径及流量计算结果,进一步计算液压缸在各个工作阶段中的压力、流量和功率值如下
计算液压缸各工作阶段的工作压力、流量和功率
设快进、快退时,回油腔压力Δp=0.5MPa,工进回油腔背压p2=0.8MPa。
1.快进(差动)
(1)进油腔压力p1=(F0+ΔpA2)/(A1-A2)
p1=(2444+0.5×
10^6×
53.6×
10^-4)/(103.82-53.6)×
10^-4=1.02MPa
(2)所需流量q=(A1-A2)V1
q=(103.82-53.6)×
10^-4×
6/min=3.013×
10^-2m3/min=30.13L/min
(3)输入功率P=P1q
P=1.02×
3.013×
10^-2/60(w)=0.512kw
2.工进
(1)进油腔压力p1=(F0+p2A2)/A1
p1=(26889+0.8×
10^-4)/103.82×
10^-4(Pa)=300.299×
10^4=3.003MPa;
(2)所需流量q=A1V2
q=103.82×
0.05=5.191×
10^-4m3/min=0.52L/min;
(3)输入功率P=p1q
P=3.003×
0.52×
10^-3/60(w)=0.026kw
3.快退
(1)进油腔压力p1=(F0+ΔpA1)/A2
取Δp=0.6MPa作为快进时的油管中压降Δp,快退时回油腔中有背压p2也可按0.6MPa估算;
因此,p1=(2444+0.6×
103.82×
10^-4)/53.6×
10^-4(Pa)=1.618MPa;
(2)所需流量q=A2V3
q=53.6×
6(m3/min)=32.16L/min;
(3)输入功率P=p1q
P=1.618×
32.16×
10^-3/60(w)=0.867kw
如表4所示。
推力F’/N
回油腔压力P2/MPa
进油腔压力P1/MPa
输入流量q/L.min-1
输入功率P/Kw
计算公式
快
进
1.02
——
2482
1.735
1.135
快速
1.727
1.127
30.13
0.512
0.6
2.899
0.52
0.026
起动
0.912
P=p1q
1.812
1.618
32.16
0.867
1.425
表4各工况下的主要参数值
表3各工况下的主要参数值
注:
第五章液压系统方案设计
根据组合机床液压系统的设计任务和工况分析,所设计机床对调速范围、低速稳定性有一定要求,因此速度控制是该机床要解决的主要问题。
速度的换接、稳定性和调节是该机床液压系统设计的核心。
此外,与所有液压系统的设计要求一样,该组合机床液压系统应尽可能结构简单,成本低,节约能源,工作可靠。
5.1选用执行元件
因系统运动循环要求正向快进和工进,反向快退,且快进,快退速度相等,因此选用单活塞杆液压缸,快进时差动连接,无杆腔面积A1等于有杆腔面积A2的两倍。
5.2速度控制回路的选择
工况图表明,所设计组合机床液压系统在整个工作循环过程中所需要的功率较小,系统的效率和发热问题并不突出,因此考虑采用节流调速回路即可。
虽然节流调速回路效率低,但适合于小功率场合,而且结构简单、成本低。
该机床的进给运动要求有较好的低速稳定性和速度-负载特性,因此有三种速度控制方案可以选择,即进口节流调速、出口节流调速、限压式变量泵加调速阀的容积节流调速。
钻镗加工属于连续切削加工,加工过程中切削力变化不大,因此钻削过程中负载变化不大,采用节流阀的节流调速回路即可。
但由于在钻头钻入铸件表面及孔被钻通时的瞬间,存在负载突变的可能,因此考虑在工作进给过程中采用具有压差补偿的进口调速阀的调速方式,且在回油路上设置背压阀。
由于选定了节流调速方案,所以油路采用开式循环回路,以提高散热效率,防止油液温升过高。
从工况图中可以清楚地看到,在这个液压系统的工作循环内,液压要求油源交替地提供低压大流量和高压小流量的油液。
而快进快退所需的时间
和工进所需的时间
分别为
=2.6s
亦即是
=27.69因此从提高系统效率、节省能量角度来看,如果选用单个定量泵作为整个系统的油源,液压系统会长时间处于大流量溢流状态,从而造成能量的大量损失,这样的设计显然是不合理的。
如果采用一个大流量定量泵和一个小流量定量泵双泵串联的供油方式,由双联泵组成的油源在工进和快进过程中所输出的流量是不同的,此时液压系统在整个工作循环过程中所需要消耗的功率估大,除采用双联泵作为油源外,也可选用限压式变量泵作油源。
但限压式变量泵结构复杂、成本高,且流量突变时液压冲击较大,工作平稳性差,最后确定选用双联液压泵供油方案,有利于降低能耗和生产成本,如图3所示。
图3双泵供油油源
5.3选择快速运动和换向回路
根据本设计的运动方式和要求,采用差动连接与双泵供油两种快速运动回路来实现快速运动。
即快进时,由大小泵同时供油,液压缸实现差动连接。
本设计采用二位二通电磁阀的速度换接回路,控制由快进转为工进。
与采用行程阀相比,电磁阀可直接安装在液压站上,由工作台的行程开关控制,管路较简单,行程大小也容易调整,另外采用液控顺序阀与单向阀来切断差动油路。
因此速度换接回路为行程与压力联合控制形式。
5.4速度换接回路的选择
所设计多轴钻床液压系统对换向平稳性的要求不高,流量不大,压力不高,所以选用价格较低的电磁换向阀控制换向回路即可。
为便于实现差动连接,选用三位五通电磁换向阀。
为了调整方便和便于增设液压夹紧支路,应考虑选用Y型中位机能。
由前述计算可知,当工作台从快进转为工进时,进入液压缸的流量由30.13L/min降为0.52L/min,可选二位二通行程换向阀来进行速度换接,以减少速度换接过程中的液压冲击,选用双作用叶片泵双泵供油,调速阀进油节流阀调速的开式回路,溢流阀做定压阀。
为了换速以及液压缸快退时运动的平稳性,回油路上设置背压阀,初定背压值Pb=0.8MPa。
a.换向回路b.速度换接回路
图4换向和速度切换回路的选择
5.5组成液压系统原理图
选定调速方案和液压基本回路后,再增添一些必要的元件和配置一些辅助性油路,如控制油路、润滑油路、测压油路等,并对回路进行归并和整理,就可将液压回路合成为液压系统,即组成如图5所示的液压系统图。
图5液压系统图
为便于观察调整压力,在液压泵的进口处,背压阀和液压腔进口处设置测压点,并设置多点压力表开关,这样只需一个压力表即能观察各压力。
要实现系统的动作,即要求实现的动作顺序为:
启动→加速→快进→工进→快退→停止。
则可得出液压系统中各电磁铁的动作顺序如表5所示。
表中“+”号表示电磁铁通电或行程阀压下;
“—”号表示电磁铁断电或行程阀复位。
表5电磁铁的动作顺序表
5.6系统图的原理
1.快进
快进如图所示,按下启动按钮,电磁铁1YA通电,由泵输出地压力油经2三位五通换向阀的左侧,这时的主油路为:
进油路:
泵→向阀10→三位五通换向阀2(1YA得电)→行程阀3→液压缸左腔。
回油路:
液压缸右腔→三位五通换向阀2(1YA得电)→单向阀6→行程阀3→液压缸左腔。
由此形成液压缸两腔连通,实现差动快进,由于快进负载压力小,系统压力低,变量泵输出最大流量。
2.工进
挡块还是压下,行程开关使3YA通电,二位二通换向阀将通路切断,这时油必须经调速阀4和15才能进入液压缸左腔,回油路和减速回油完全相同,此时变量泵输出地流量自动与工进调速阀15的开口相适应,故进给量大小由调速阀15调节,其主油路为:
进油路:
泵→向阀10→三位五通换向阀2(1YA得电)→调速阀4→调速阀15→液压缸左腔。
回油路:
液压缸右腔→三位五通换向阀2→背压阀8→液控顺序阀7→油箱。
3.死挡铁停留
当滑台完成工进进给碰到死铁时,滑台即停留在死挡铁处,此时液压缸左腔的压力升高,使压力继电器14发出信号给时间继电器,滑台停留时间由时间继电器调定。
4.快退
滑台停留时间结束后,时间继电器发出信号,使电磁铁1YA、3YA断电,2YA通电,这时三位五通换向阀2接通右位,,因滑台返回时的负载小,系统压力下降,变量泵输出流量又自动恢复到最大,滑快速退回,其主油路为:
泵→向阀10→三位五通换向阀2(2YA得电)→液压缸右腔。
液压缸左腔→单向阀5→三位五通换向阀2(右位)→油箱。
5.原位停止
当滑台退回到原位时,挡块压下原位行程开关,发出信号,使2YA断电,换向阀处于中位,液压两腔油路封闭,滑台停止运动。
这时液压泵输出的油液经换向2直接回油箱,泵在低压下卸荷。
第六章液压元件的选择
6.1确定液压泵
本设计所使用液压元件均为标准液压元件,因此只需确定各液压元件的主要参数和规格,然后根据现有的液压元件产品进行选择即可。
(1)计算液压泵的最大工作压力
由于本设计采用双泵供油方式,根据液压系统的工况图,大流量液压泵只需在快进和快退阶段向液压缸供油,因此大流量泵工作压力较低。
小流量液压泵在快速运动和工进时都向液压缸供油,而液压缸在工进时工作压力最大,因此对大流量液压泵和小流量液压泵的工作压力分别进行计算。
根据液压泵的最大工作压力计算方法,液压泵的最大工作压力可表示为液压缸最大工作压力与液压泵到液压缸之间压力损失之和。
对于调速阀进口节流调速回路,选取进油路上的总压力损失
,同时考虑到压力继电器的可靠动作要求压力继电器动作压力与最大工作压力的压差为0.5MPa,则小流量泵的最高工作压力可估算为
大流量泵只在快进和快退时向液压缸供油,图4表明,快退时液压缸中的工作压力比快进时大,如取进油路上的压力损失为0.5MPa,则大流量泵的最高工作压力为:
(2)计算总流量
表3表明,在整个工作循环过程中,液压油源应向液压缸提供的最大流量出现在快进工作阶段,为30.13L/min,若整个回路中总的泄漏量按液压缸输入流量的1.1计算,则液压油源所需提供的总流量为:
工作进给时,液压缸所需流量约为0.52L/min,但由于要考虑溢流阀的最小稳定溢流量3L/min,故小流量泵的供油量最少应为3.52L/min。
据据以上液压油源最大工作压力和总流量的计算数值,因此选取PV2R126/20型双联叶片泵,其中小泵的排量为6mL/r,大泵的排量为20mL/r,若取液压泵的容积效率
=0.9,则当泵的转速
=960r/min时,液压泵的实际输出流量为
由于液压缸在快退时输入功率最大,这时液压泵工作压力为2.118MPa、流量为32.16r/min。
取泵的总效率
,则液压泵驱动电动机所需的功率为:
根据上述功率计算数据,此系统选取Y100L-6型电动机,其额定功率
,额定转速
6.2确定其它元件及辅件
(1)确定阀类元件及辅件
根据系统的最高工作压力和通过各阀类元件及辅件的实际流量,查阅产品样本,选出的阀类元件和辅件规格如表6所列。
表6液压元件规格及型号
序号
元件名称
通过的最大流量q/L/min
规格
型号
额定流量qn/L/min
额定压力Pn/MPa
额定压降∆Pn/MPa
1
双联叶片泵
—
PV2R12-6/26
(6+20)
16/14
三位五通电液换向阀
36
35DY
63
6.3
0.5
3
行程阀
22C-63(B)
0.3
4
调速阀
Q-10(B)
0.05
0.5~6.3
单向阀
I-63(B)
0.2
6
7
液控顺序阀
XY-63(B)
0.3~6.3
8
背压阀
B-10(B)
10
9
溢流阀
Y-63(B)
0.02
11
滤油器
42
wu-63×
100
12
压力表开关
KF3-E3B3测点
16
13
14
压力继电器
DP1-63(B)
*注:
此为电动机额定转速为960r/min时的流量。
(2)确定油管
在选定了液压泵后,液压缸在实际快进、工进和快退运动阶段的运动速度、时间以及进入和流出液压缸的流量,与原定数值不同,重新计算的结果如表9所列。
表9各工况实际运动速度、时间和流量
流量、速度
输入流量
=46.43
=22.46
排出流量
=23.97
=0.27
=43.50
运动速度
=4.47
=0.5
=4.19
由表9可以看出,液压缸在各阶段的实际运动速度符合设计要求。
根据表9数值,按表10推荐的管道内允许速度取=4m/s,由式计算得与液压缸无杆腔和有杆腔相连的油管内径分别为
为了统一规格,按产品样本选取所有管子均为内径20mm、外径28mm的10号冷拔钢
6.3确定油箱
油箱的容量按式估算,当取
为7时,求得其容积为
,按JB/T7983-1999规定,取标准值V=250L。
第七章液压