液氯生产过程中的安全要点Word文档格式.docx
《液氯生产过程中的安全要点Word文档格式.docx》由会员分享,可在线阅读,更多相关《液氯生产过程中的安全要点Word文档格式.docx(6页珍藏版)》请在冰豆网上搜索。
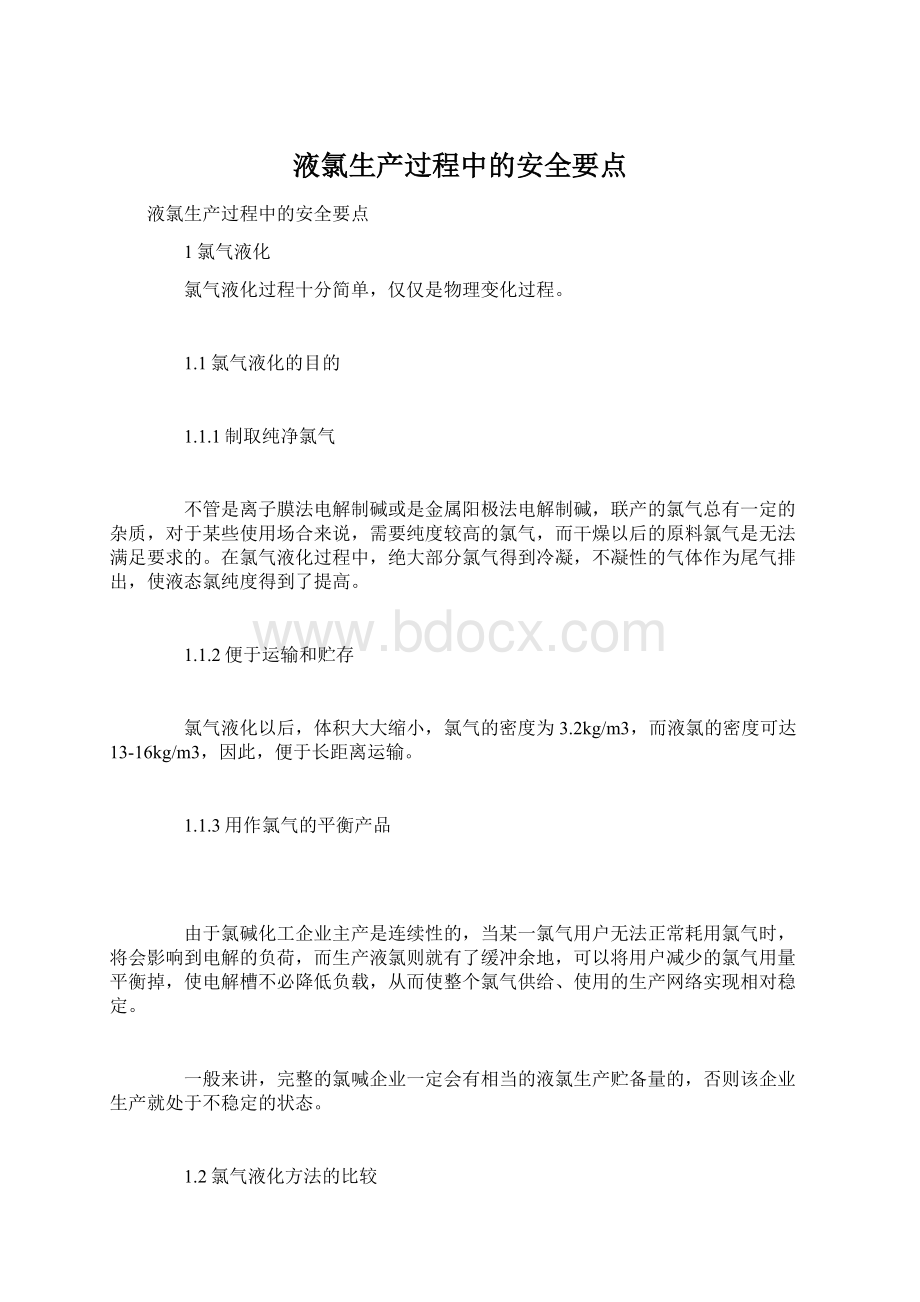
1.1.2便于运输和贮存
氯气液化以后,体积大大缩小,氯气的密度为3.2kg/m3,而液氯的密度可达13-16kg/m3,因此,便于长距离运输。
1.1.3用作氯气的平衡产品
由于氯碱化工企业主产是连续性的,当某一氯气用户无法正常耗用氯气时,将会影响到电解的负荷,而生产液氯则就有了缓冲余地,可以将用户减少的氯气用量平衡掉,使电解槽不必降低负载,从而使整个氯气供给、使用的生产网络实现相对稳定。
一般来讲,完整的氯喊企业一定会有相当的液氯生产贮备量的,否则该企业生产就处于不稳定的状态。
1.2氯气液化方法的比较
氯气是一种比较容易液化的气体。
由于气相氯气中含有不凝性组分,实际的液化温度要比纯氯气的液化温度低些。
而不同的温度与压力液化氯气所消耗的能量是不同的,氯气液化就有高温高压法、中温中压法和低温低压法之区别。
三种制备液氯方法的电能消耗不同。
高压法消耗的电能仅为低压法的一半,节能效果十分明显。
而且氯气压力越高,氯气液化越容易。
氯气压力上升至1MPa以上时,普通的冷却水就可以实现氯气的相变化,根本不需要冷冻装置。
随着高性能、高排出压力的氯气压缩机的问世,液氯生产过程采用高压法的企业会越来越多。
据了解,日本德山曹达就有单台氯气离心式压缩机出口压力达到1.2MPa(G)在线运行中。
一般来讲,要想取得较高的氯气压力,就必须将氯气压缩机串联使用,但生产工艺相对复杂许多。
2液氯的生产工艺过程
来自氯气处理后的净化干燥氯气(氯气的体积分数约为96%,氢的体积分数小于0.4%)经分配台进入氯气液化器(液化箱槽式、列管式的液化器),用-25—35℃的冷冻氯化钙盐水溶液(或氟利昂冷冻液)进行冷凝热交换;
使大部分氯气冷凝为液氯,然后气液混合物进入气液分离器将液化尾气进行分离,液化尾气从顶部进入尾气管,去盐酸尾气缓冲罐(供合成氯化氢之用)或去除害塔处理制备次氯酸钠;
而液氯则由气液分离器底部流入液氯计量槽或液氯贮槽。
氯气冷凝器所需的冷冻盐水或氟利昂冷冻液由氨冷冻机组或氟利昂冷冻机组进行制冷和回收循环使用。
来自液氯计量槽或液氯贮槽的液体氯从容器底部流向立式贮槽,由液氯液下泵(该泵密封是采用充入高压氮气)进行抽吸送入液氯包装钢瓶。
也可以直接从液氯计量槽或液氯贮槽底部用屏蔽液氯泵进行抽吸送入包装钢瓶。
也有采用气化氯包装的方法,即在液氯气化器中压入稍许液体氯,将汽化器夹套注入95℃热水,使气化器内液体氯迅速气化,气化压力可达1.1MPa,然后将气化氯压入液氯计量槽或液氯贮槽,将计量槽或贮槽内的液体氯压送入钢瓶进行包装。
但是每次包装完毕以后,气化器内气化氯将直接排入氯气管网或者直接排往除害塔。
另外还必须将气化器内剩余物(带液)进行排污和碱处理,以策安全。
气化器内气化氯带压排放进入氯气管网时,必须放慢排放速度,一旦过快,容易使盐酸合成炉火焰压熄,造成合成炉氯气外溢事故发生。
在盐水总铵指标超标的情况下,一定要包装一次排污一次(带液排放),在碱性的情况下消除三氯化氮,防止其积累发生爆炸事故。
包装钢瓶的尾气由纳氏泵抽吸直接送往除害塔。
氯气的液化是在有毒、有害、高压、高温的生产工况下进行的。
美国公布的液氯生产过程事故树逻辑分析报告称,整个液氯生产过程几乎没有一个“与门”,全是“活门”。
也就是说几个“与门”一起打开造成事故的几率是零,而1个“活门”打开造成事故的几率为100%。
稍有不慎,氯气外溢、爆炸不可避免。
3液氯生产过程中事故隐患的原因及防范措施
3.1氯气内含氢超标
原料氯气中含有氢气。
一定比例的氯气与氯气是爆炸性气体混合物。
在开始进行氯气液化时,由于氯气能液比而氢气则未达到液化条件不能液化,氢气在混合气体中的比例较小,以不凝性的组分形式存在于气相之中,尚未达到爆炸范围的下限,所以氯气内氢的存在不会影响系统的安全。
随着氯气的液化量增多,不凝性气体中氢的含量由于积聚而增加,达到爆炸范围,威胁着液氯生产的安全。
在液氯制备过程中,必须根据不凝性气体中的氢含量(液氯尾气含氢)来控制原料氯气的液化程度,就是控制它的液化效率。
一般尾气中氢的体积分数不能超过4%,由此可见氯气的液化程度必须处于受控状态,受到一定的限制。
一旦尾气含氢超标,就会发生爆炸事故,这种事故在氯碱行业曾经发生过。
不同含氢量的原料氯气的液化效率见表1。
表1
不同含量的氯气的液化效率
Φ(H2)
液化效率
0.3
97.5
0.4
94.8
0.5
92.1
0.6
89.4
0.7
87.0
0.8
84.1
0.9
81.5
1.0
79.0
液化效率可以用下式计算。
η%=液氯产量/原料氯气量×
100%
或η%=[1-(100-C1)/C1·
C2/(100-C2)]×
100/%式中:
η为液化效率,%;
C1为原料氯气中氯气体积分数,%;
C2为尾气中氯气体积分数,%。
由上可见,氯气氢含量(含原料气及尾气)是相当重要的中控指标,并且是可以控制掌握的,关键在于加强分析和调节。
发现氯内含氢超标可以采用如下措施:
(1)继续分板原料氯气的氯气纯度和液化尾气中的氯气纯度,以观察氯内含氢是否继续上升或下降;
(2)适当升高氯气的液化温度,降低液化效率;
(3)适当开大气液分离器顶部尾气出口的阀门(通往盐酸合成炉或除害塔处理),尽可能增加尾气的流通量,以降低液化效率和加速排除不凝性气体。
但是尾气阀门千万不能开得太大,否则很有可能将液体氯一起带往尾气流通管道,造成尾气压力突然升高,使氯化氢合成炉氯气过量;
若与乙炔气接触,会生成氯乙炔而发生爆炸。
对于设计者来说,相应的分析条件以及相应的阀门安置尽可能要考虑得周到一些。
尤其是关键阀门(如气液分离器出口尾气阀门)的设置以及工艺控制点的设置一定要合理,尽可能把所能发生的安全隐患考虑周到。
另外离子膜法生产烧碱的氯内含氢量要比金属阳极隔膜法生产烧碱的氯内含氢量低得多,因此尽可能采用先进的制碱方法也是防止氯气内含氢量超标的一种方法。