电镀工序作业指导书Word下载.docx
《电镀工序作业指导书Word下载.docx》由会员分享,可在线阅读,更多相关《电镀工序作业指导书Word下载.docx(19页珍藏版)》请在冰豆网上搜索。
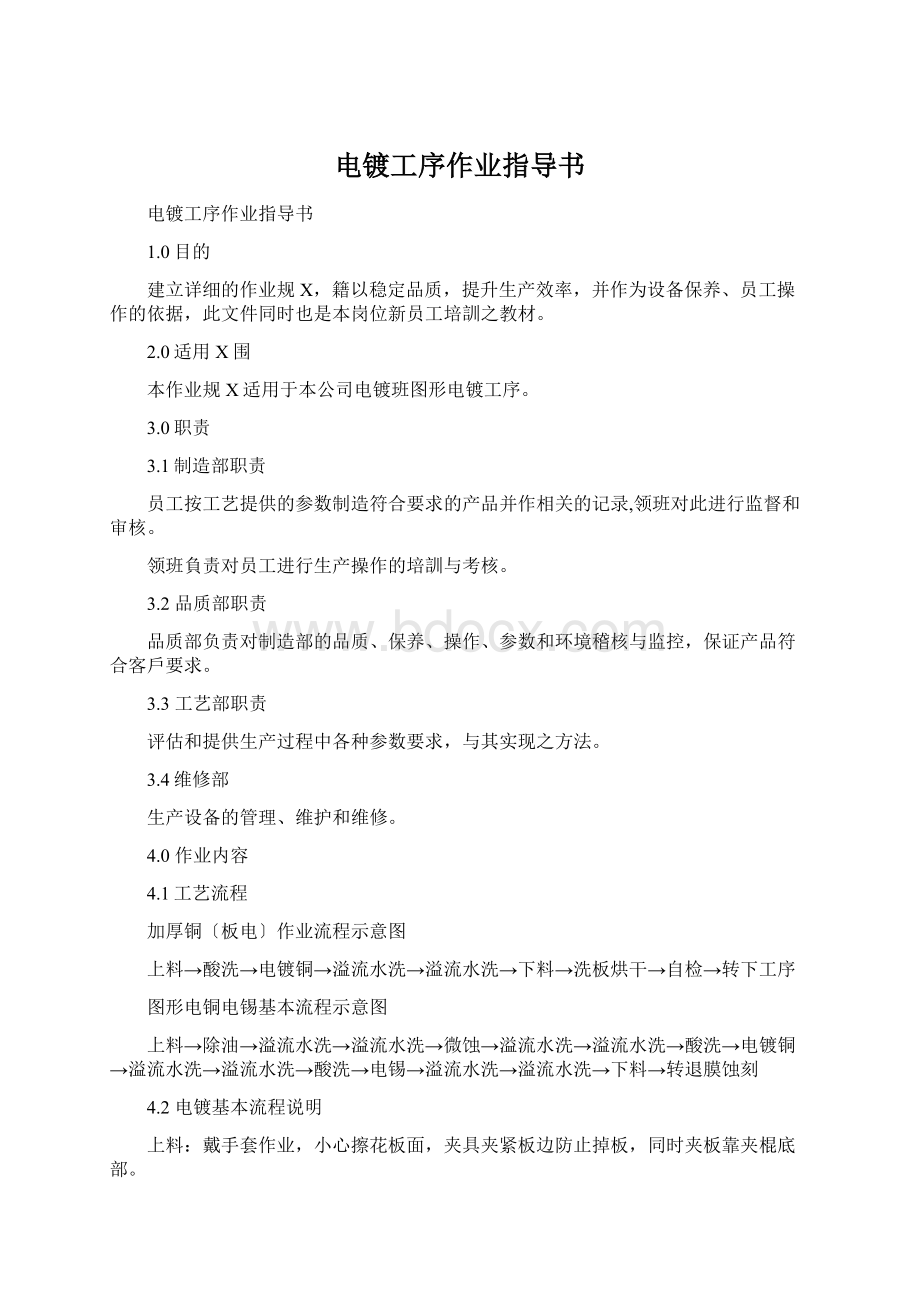
容积
除油
XP070302-6
30-50ml/l
1次/天
温度:
35±
2℃循环过滤,
非空气搅拌震荡振动
5"
3´
15s
PP
800L
水洗
自来水
/
非空气搅拌
2"
51´
无
空气搅拌
10´
微蚀
H2O2
8-18ml/l
30±
2℃循环过滤
1"
42´
H2SO4
2-4%
Cu2+
<4g/l
1次/周
微蚀速率
μm
24´
54´
浸酸
4-6%
常温
52´
电
镀
铜
CuSO4
55-80g/l
2次/周
25±
空气搅拌震荡振动
光剂补加:
HV-101AN按250ml/KAH,HV-101BN按130ml/KAH
由不同工艺决定
4000L
90-130ml/l
Cl-
40-70PPM
铜光亮剂HV-101AN
2-4ml/L
1次/2周
铜光剂辅助剂HV-101BN
5-20ml/L
铜光剂开缸剂
HV-101M
开缸添加5ml/L
开缸和碳处理后进行添加5ml/L,平时不做添加
空气搅拌
3"
13´
预浸
30´
10S
锡
SnSO4
35-45g/l
20±
光剂补加:
A:
250ml/KAH
B:
125ml/KAH
15"
00´
3600L
80-110ml/l
EC.partA
5-10ml/l
1次/月
EC.partB
10-20ml/l
38´
50´
下板
下板时需戴胶手套且必须插
架,避免板件擦花
7"
退镀
HNO3
20-40%
非空气搅拌手动完成
以退干净为原则
空气搅拌手动完成
手动
具体见夹板规X
同上板
4.4行车操作程序
行车操作程序参照文件:
电镀操作规程〔编号:
MTL-PI-033〕的4.1-4.4内容进行操作。
4.5生产前准备
4.5.1开启所有过滤泵和加热器。
补充所有槽中的水位,通知化验室分析药水浓度。
检查所有槽的温度。
检查所有过滤泵性能,并定时更换过滤棉芯。
检查水槽的流量与各槽的打气是否正常。
检查自动添加控制器。
检查飞巴运行是否正常。
检查摆动是否正常。
检查各整流器输入、输出状态是否正常。
检查阴极座V槽接电位置是否正常。
检查夹具是否有异常。
4.6工艺操作注意事项。
4.6.1夹板方式
1)上板需戴手套上板,手指不可伸入有效图形内。
2)图电板件上板统一采用GTL面朝上板人方向,沉铜加厚板除外。
3)板与板之间必须紧密排列,在一般生产情况下是夹短边的,在不满一飞巴时可以考虑夹长边。
4)盲孔、盘中孔、压接孔板加厚镀时以与所有图电板件,上板后每个飞巴需在最外面夹棍的外螺栓上夹边条,边条长度控制在100-250mm,边条宽度控制在20-40mm。
如无边条用时,可将使用过的边条退锡后再行使用,但需确保退锡干净,未退锡的边条条绝对不允许直接循环使用。
浸泡稀除油操作
1)浸泡除油液操作:
在图电上料夹板前,需要进行浸泡除油液操作的板件为:
最小孔径0.3mm以上、厚径比5以上和最小孔径0.25mm以下、厚径比4以上的板件。
2)浸泡除油液操作流程:
双手持板缓慢将板件水平放入配制好的除油液,浸泡2-5S后,缓慢将板件水平取出,停滴2-5S后将板件水平放入清洗水槽中漂洗2-5S后,板件水平取出,停滴2-5S后直接夹板。
3)浸泡除油液槽配制;
上板浸泡除油槽内加40L清水,取电镀线除油缸槽液4L加入搅拌均匀即可使用。
4)清洗水槽配制;
在胶盆内直接注入清水即可。
5)稀除油液与清洗水槽的使用周期:
稀除油液与清水每班配制一次,当班使用后直接更换。
打气控制
对于板厚小于0.4mm的板件电镀时,需使用薄板挂具上板,并需将打气关小到1/2,但做厚板前又要恢复。
电流计算
详细电流计算方式见编号为:
MTL-PI-034《电镀电流设定作业指导书》
1)加厚铜电流计算:
单面电流=[板长(in)*板宽(in)*0.0645*挂板数+边条面积]*电流密度(A/dm2)
2)图形电镀电流计算:
单面电流=[单面电镀面积〔dm2〕*挂板数+边条面积]*电流密度(A/dm2)
电镀锡电流计算:
备注1、图电板件和平板加厚镀板件必须夹边条。
2、边条长度需控制在200-250mm,边条宽度控制在20-40mm。
3、当生产板件单面电镀面积小于40dm2时必须算边条电流。
单面面积超过40dm2时可忽略不计。
边条面积计算方法:
边条面积=边条长度(in)*边条宽度(in)*0.0645*边条数量
4.7工艺操作
挂具浸泡:
1)挂具的浸泡:
下料退镀后的挂具需进行浸泡清洗后才可上板使用。
2)挂具浸泡的操作流程:
上料处有酸洗和水洗两个挂具存放槽,供清洗浸泡挂具使用,退镀完的挂具取下后直接铜靶接触的一端朝下在酸槽内浸泡5-15分钟后,取出放入清水槽内浸泡清洗,上挂使用时直接取在清水槽内清洗干净的挂具使用。
3)挂具浸泡槽药水配制:
挂具浸泡槽内加100L清水〔槽体的2/3〕,加入3L的硫酸,即可使用。
4)清洗槽配制:
直接在槽内加入自来水即可。
5)挂具清洗浸泡槽和水洗槽使用周期:
挂具清洗浸泡槽和水洗槽每天进行更换。
上板
1)上板前先看流程卡,确定是否要浸泡除油,若需要,则浸泡除油后再上板。
2)上板时严格按上板进行作业。
3)夹板后需对夹棍使用扳手进行加紧处理,确保夹紧。
电流输入
上板后记录上板档案号,根据流程卡和《电流设定作业指导书》进行设置电流,如流程卡有注明,按流程卡设定;
无注明时按《电流设定作业指导书》进行参数设定。
1〕下板时需戴手套下板,下板时需一块一块下,不可多块一起下,插板时切忌两块板插在一个格子里,需避免擦花。
2〕图电的板下板插架后放置在待蚀刻板件摆放区,平板的板放在磨板机,待清洗烘干。
板电的后的挂具视镀铜情况,可以反复,当铜层已明显盖住包胶时,需退镀处理。
可以根据挂具数量,为节约时间,可集中几缸的一起退镀。
生产检查
〔1〕在生产过程中必须三天检测一次电镀铜缸、锡缸的电流输出情况,并如实填写图形电镀线电流检测记录表.当用电镀钳表测检实际输出电流值与设定电流值不相符,误差值超过5%时,应作好记录,并与时填写<
维修单>
至维护部专业人员作调校;
〔2〕在生产过程中必须每班检查一次循环、过滤、振荡、打气、加热棒、自动添加开启情况与飞巴与阴极座接触情况,并填好《图电线点检记录表》。
5.0日常保养
5.1每班对电镀线进行清洁。
5.2对每一飞巴进行檫洗飞巴杆和飞巴铜头。
6.0定期维护保养
6.1每周需对各水洗缸更换一次,并清洗干净水缸缸壁、缸底。
6.2每周需补加铜球、锡球,补加前对铜、锡球进行清洗处理,补加后对铜缸、锡缸进行电解处理。
6.3每月需更换各过滤泵滤芯。
6.4每三个月需对铜缸铜球进行清洗,锡缸锡球进行清洗,同时对铜缸和锡缸进行一次碳芯过滤。
6.5每一年需对铜缸进行碳处理。
6.6当微蚀缸Cu2+≥4g/L时需对微蚀缸换缸。
6.7生产根据生产面积提前安排换缸时间。
7.0维护保养
7.1电气维护
在进行维修前应确信电源是关闭状态,行车处于停止状态。
注意观看感应片与传感器,如不细心会造成不可预料的故障。
不要在槽上、机架轨道、抽风口与槽盖上行走,这样很危险,应使用维修平台进行工作。
电箱、整流机应尽量放置在荫凉、通风、干燥的环境,不得将腐蚀性气体直接吹向电箱,厂房内湿度过大时要加强排气。
环境因素将直接影响电气设备的使用寿命。
加热器、泵等所有器材必须可靠接地,发现对地短路的应与时处理,严禁断开地线继续使用。
发现空气开关、热继电器、变频器跳闸,切记不可盲目反复合闸,应仔细检查排除故障后合闸,以免造成设备损坏。
过滤泵与循环泵都采用磁偶泵,使用中绝对禁止无水开泵,以免损坏泵体。
过滤泵在运行过程中如出现不正常的声响或开关跳闸,应与时修理,看是散风扇碰到罩子,还是吸入杂物,或者是轴承损坏。
震动器、感应器尾部导线被用扎带扎成小圈,这能缓冲外力的作用,如发现小圈松开应与时重新扎好。
车上用扎带扎好的电线如发现扎带松动,应与时重新扎好,以免机械结构摩擦损伤电线。
未经允许,不可擅自修改行车的控制速度。
行车出现电池报警,应与时更换,更换电池必须在5分钟之内完成,否则机内程序记忆将消失。
7.2机械维护
行车
1)纵走轮应保证运行正常,如发现轮周的红色胶有脱胶时应与时更换;
2)行车部件上的所有马达、轴承大约在3~6个月后应加注润滑油以保证正常运行。
路轨
保证路轨表面干净以保证行车运行畅通无阻。
摇摆部分
1)设备运行6-10个月后应检查摇摆马达牙箱内的油位是否需要更换;
2)摇摆运行时严禁在上面放置任何物品。
整流器部分
1)铜杯士表面应保持清洁以保证导电能力,防止整流器负载过大。
2)定期紧固整流器输出线耳螺丝,防止松动。
缸槽部分
1)不要将杂物抛进缸槽以免堵塞过滤泵或循环管路;
2)定期检查打气管的防虹吸孔是否堵塞,以免停打气机时引起缸内液体倒流;
飞巴
飞巴铜头应保持干净无污垢以提高电镀导电性能。
防止整流器负载过大。
7.3药水维护
镀铜液的维护
1)碳处理
在电镀过程中,添加剂的分解产物、干膜或抗电镀油墨溶出物与板材溶出物的积累,会造
成镀液的有机污染,少量的有机污染用活性炭吸附过滤除去。
随着时间的持续,需用双氧水-活性碳处理以取得比较彻底的处理效果,处理每年一次。
其处理步骤如下:
a、将镀液转入已清洗好的备用槽中。
b、连续搅拌边加入3~5ml/L双氧水,充分搅拌1~2小时;
c、升温至65℃,继续搅拌2小时;
d、加优质活性炭粉3~5g/L,搅拌2小时后进行停止搅拌,并进行沉淀降温12H,溶液温度逐渐降至室温后可取小样做赫尔槽实验,确认2A全板镀层无光泽后进行过滤。
e、将无炭粉的澄清镀液转入工作槽内,挂入清洗好的阳极袋〔内充磷铜球〕。
通0.5~2A/dm2电流4~6小时后,按新槽加入HV-101M开缸剂,并搅拌均匀,试镀。
2)挂具使用要得当,绝缘破损的挂具要与时处理,否则会带来镀液的交叉污染和消耗有效电流。
镀锡液的维护
1)Cu2+污染:
当Cu2+浓度达20mg/L时,镀层会产生半湿润现象。
Cu2+污染可以用小电流电解法去除,用瓦楞形阴极,以0.1~0.5ASD电流密度长时间电解,直至整块阴极板上镀层均匀为止。
2)有机物污染:
当有机物污染严重时,镀层热熔时会冒泡。
有机物污染可用活性炭处理,一般可用活性炭滤芯过滤2~4小时。
当污染严重时,需用活性炭粉3~5g/L放入溶液中,充分搅拌,过滤到无炭粉为止。
处理镀液时不可用H2O2和空气搅拌,以防止加速Sn2+的氧化。
7.3.3每季度清洗阳极袋、铜球、锡球各一次。
1)阳极袋的清洗
a、用水将阳极袋浸泡30min,用水冲洗干净
b、将阳极袋反过来用5%的NaOH溶液浸泡6小时以上
c、用清水漂洗2小时
d、用10%的H2SO4浸泡2小时即可
2)铜球的清洗
a、用5%的H2SO4浸泡15min以上,
b、然后用纯水清洗干净即可使用。
c、每次补加铜球后,须以1.8ASD*0.5H--0.5ASD*2H--1.8ASD*0.5共电解3小时。
3)锡球的清洗
a、将锡球用水冲洗干净后,再用10%的H2SO4浸泡30MIN。
b、用纯水冲洗干净。
c、每次补加锡球后,每次补加后用报废板使用1.0ASD电解一挂。
4)滤芯的更换
a、用100ml/L的H2SO4浸泡8小时以上
b、用自来水彻底清洗干净
日常药水维护
工序名称
维护项目
维护频率
备注
倒缸
视退挂具效果
见9.6
换缸
1次/2月
见9.3
滤芯更换
见:
9.4
≥4g/l
9.5
1次/1周
1次/月
电镀铜
镀铜光亮剂AN
自动添加
并1次/月分析
250ml/1000AH
按分析结果补加
镀铜光剂辅助剂BN
按照AH手动添加
130ml/1000AH
镀铜光剂开缸剂M
开缸时和碳处理后
进行添加5ml/L
平时不做添加
磷铜球补加与电解
1.8ASD*0.5H--0.5ASD*2H--1.8ASD*0.5共电解3小时
见
阳极袋清洗
1次/3月
铜球清洗
碳处理
每次/年或视药水污染程度与或生产品质状况
电镀锡
锡添加剂EC.partA
手动补加
与1次/月
锡添加剂EC.partB
125ml/1000AH
锡球补加
每次补加后用报废板使用0.5ASD电解一挂。
锡缸开新缸
1次/2-3年
见9.2
8.0异常情况时板的处理事项
8.1停电
停电后立即进行的作业
1)将所有电源关闭,尤其是整流器电源。
2)立即将微蚀缸内的板和所有板电的板〔包括酸缸和铜缸〕放入水缸,其它缸中的板暂不动。
3)待10分钟内来电后,将所有板件放回原缸位,继续按正常程序生产。
4)所有需要镀铜的图电的板件和停电前镀铜时间超过10min的板电的板件继续完成电镀铜;
停电前镀铜时间不超过10min的板电的板件和所有镀锡时间未够的板重新浸酸后再镀铜、锡
停电超过10分钟且预计半个小时内无法来电时。
1)把所有药水缸中的板取出吹干,务必作好记录、贴好标签;
并对各电镀缸中的板记好缸号、电镀时间。
2)图电的板待来电后:
如未过微蚀,按正常再行返工一次;
如已过微蚀但未电镀,需返过前处理,但需把微蚀时间缩短为30秒内。
对于在镀缸内的板,按正常过前处理,并依据记录电镀至所需时间〔可以相对加10min以补偿第二次微蚀的铜〕。
3)板电的板待来电后:
如未电镀或电镀时间不起过10分钟的板需返沉铜处理;
镀铜时间起过10分钟的板需按图电板一样过所有前处理,并依据记录电镀至所需时间〔可以相对加10min以补偿第二次微蚀的铜〕。
4)已镀锡但电镀时间不够的板可浸酸后重新镀锡。
5)镀锡时间够的板件按正常送下工序。
8.2停水
对已进入各缸中的板继续做完,但必须停止上板,做完在线板后收拉。
8.3坏车
坏车后立即进行的作业
1)先取出微蚀缸中的板和在酸洗缸内需板电的板转到水缸中。
然后将其它缸中的板不动。
2)电镀缸内的板每巴将电流降到总电流的6%维持电镀。
3)记下各电镀缸内板件电镀时间。
坏车时间超过5分钟时。
电镀缸内的板调为正常电流完成电镀,电镀时间达到要求但行车仍未恢复的板将电流降到总电流的6%维持电镀。
预计行车恢复时间将超过半小时以上时
1)将非电镀缸内的板全部取出烘干。
2)已过微蚀但未电镀的板,在第二次过前处理时需把微蚀时间缩短为30秒。
3)过除油的但未过微蚀的图电的板按正常再行过一次。
4)将进缸了的板电的板取出放入泡板槽,如两个小时内行车仍未恢复,所有板都返沉铜。
9.0镀液配制
9.1镀铜液的配制
9.1.1将镀槽擦洗干净,注入10%NaOH溶液,开启过滤机〔无过滤棉芯〕和空气搅拌,将此液加温到60℃,保持4~8小时,然后用水冲洗。
再注入5%H2SO4,同样开启过滤机〔无过滤棉芯〕空气搅拌4~8小时,用水冲洗干净。
同时检查过滤系统和搅拌系统是否配置得当。
备用槽也同样清洗干净。
在备用槽内,注入1/4体积的工业纯水,在搅拌下缓缓加入1600L的硫酸,借助所释放的热量,加入1088kg硫酸铜,搅拌使完全溶解。
9.1.3加入H2O21~2ml/L,搅拌1小时,升温至65℃,保温1小时,以赶走多余的H2O2。
9.1.4加入活性炭3g/L,搅拌1小时,静置半小时后过滤,直至溶液中无炭粉为止。
将溶液转入镀槽中。
9.1.5加入2400ml的盐酸,加入5M/L的HV-101M开缸剂,加纯水至所需体积,挂入预先备好的阳极。
9.1.6以阳极电流密度0.5~2A/dm2电解处理约6个小时,使阳极形成一层致密的黑色薄膜。
镀液可以进行试镀。
9.2镀锡液的配制
9.2.1将镀槽擦洗干净,注入10%NaOH溶液,开启过滤机〔无过滤棉芯〕和
空气搅拌,将此液加温到60℃,保持4~8小时,然后用水冲洗。
再注入5%H2SO4,同样开启过滤机〔无过滤棉芯〕和空气搅拌4~8小时,用水冲洗干净。
9.2.2注入半槽纯水,小心地慢慢地加入360L98%的硫酸,在搅拌下缓缓加入170kg的硫酸亚锡至完全溶解。
9.2.3用活性炭滤芯过滤2~4小时〔若用炭粉处理,必须在备用槽中进行〕,然后换成5µ
m聚丙烯〔PP〕滤芯过滤。
9.2.4待溶液温度降至室温后,缓缓加入EC-A70L、EC-B140L的添加剂,调整液位。
9.2.5用电流密度0.5A/dm2电解1小时,试镀。
9.3除油缸
9.3.1加入2/3体积的纯水,
加入XP-070302-6药水32L。
9.3.3.补加纯水至标准液位,开启循环泵,混合均匀。
9.4微蚀缸
9.4.1预留10%体积原液,加入3/4体积纯水并开启打气搅拌
9.4.2加入16L98%H2SO4,冷却至50℃,停止打气
9.4.3加入20升粗化稳定剂
加入12kg元明粉
加入12LH2O2
9.4.6补加纯水至标准液位,开启循环泵,混合均匀。
9.5酸洗缸
9.5.1加入2/3体积之纯水并开启打气搅拌
9.5.2缓慢加入45L98%H2SO4,补加纯水至标准液位
9.6退镀缸
将缸内药水排掉1/2。
住缸内加120L浓硝酸。
往里补充自来水至液位。
10.0电镀线使用的设备与物料清单
设备与物料名称
牌号
使用目的
药水缸
电镀酸洗除油褪镀微蚀
整流器
提供电镀电源
振动器
消除孔内气泡
过滤泵
清除缸内脏物
压缩空气机
保持缸内浓度均匀,减少浓差极化
加热管
石英
保证缸内温度
挂架
不锈钢
312
夹板和提供导电工具
钛蓝
钛合金
装满铜球作阳极使用
锆蓝
锆合金
装满锡球作阳极使用
排骨架
电镀前后装板使用
猪笼架
铜球
铜磷合金
镀铜阳极材料
锡球
纯锡球
镀锡阳极材料
HV-101AN、
镀铜光亮剂
HV-101BN
镀铜光剂辅助剂
CP和AR级
电镀酸洗微蚀
CP级
镀铜
镀锡
EC-A、EC-B.
镀锡光剂
12.0相关记录
电镀工序生产日报表
电镀线安培小时记录表
电镀线药水添加记录表
电镀线开机点检表
电镀线保养记录表
电镀线电流检测记录表
电镀电流计算表
电镀工序作业流程
操作说明与注意事项
正式生产前先按电镀线点检记录表检查全线,并做记录。
1)上板前确认挂具清洗干净。
2)看流程卡,确定是否要浸泡除油,若需要,则浸泡除油后再上板。
3)上板时严格按要求夹边条。
4)夹板后需对夹棍使用扳手进行加紧处理,确保夹紧。
上板后记录上板档案号,如流程卡有注明,按流程卡设定电流;
无注明时按《电流设定作业指导书》进行参数设定。
1〕下板时需戴手套下板,插板时切忌两块板插在一个格子里,需避免擦花。
2〕图电的板下板插架后放置在待蚀刻板件摆