百万千瓦等级超超临界机组汽轮发电机参数选型Word格式.docx
《百万千瓦等级超超临界机组汽轮发电机参数选型Word格式.docx》由会员分享,可在线阅读,更多相关《百万千瓦等级超超临界机组汽轮发电机参数选型Word格式.docx(14页珍藏版)》请在冰豆网上搜索。
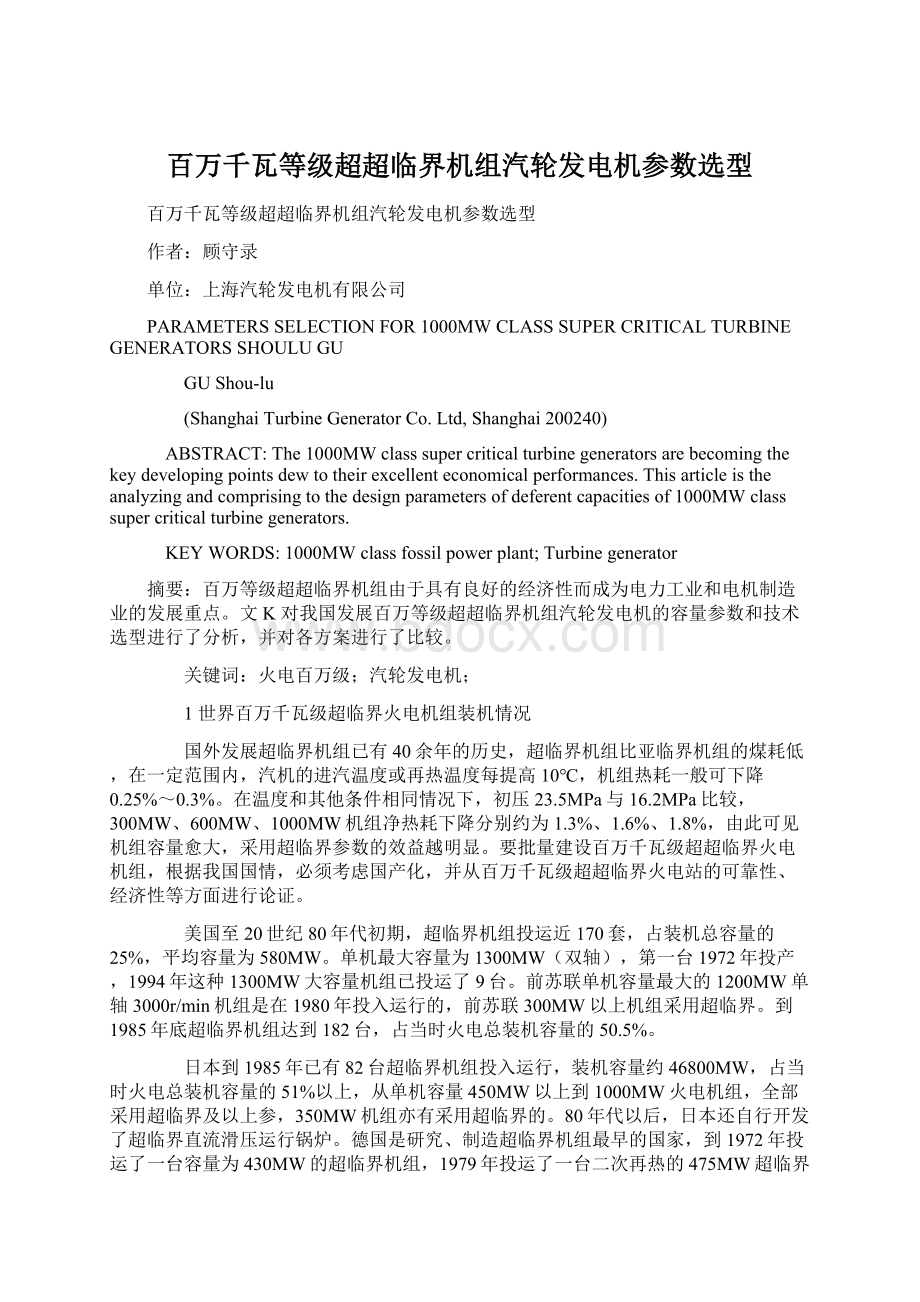
国外发展超临界机组已有40余年的历史,超临界机组比亚临界机组的煤耗低,在一定范围内,汽机的进汽温度或再热温度每提高10℃,机组热耗一般可下降0.25%~0.3%。
在温度和其他条件相同情况下,初压23.5MPa与16.2MPa比较,300MW、600MW、1000MW机组净热耗下降分别约为1.3%、1.6%、1.8%,由此可见机组容量愈大,采用超临界参数的效益越明显。
要批量建设百万千瓦级超超临界火电机组,根据我国国情,必须考虑国产化,并从百万千瓦级超超临界火电站的可靠性、经济性等方面进行论证。
美国至20世纪80年代初期,超临界机组投运近170套,占装机总容量的25%,平均容量为580MW。
单机最大容量为1300MW(双轴),第一台1972年投产,1994年这种1300MW大容量机组已投运了9台。
前苏联单机容量最大的1200MW单轴3000r/min机组是在1980年投入运行的,前苏联300MW以上机组采用超临界。
到1985年底超临界机组达到182台,占当时火电总装机容量的50.5%。
日本到1985年已有82台超临界机组投入运行,装机容量约46800MW,占当时火电总装机容量的51%以上,从单机容量450MW以上到1000MW火电机组,全部采用超临界及以上参,350MW机组亦有采用超临界的。
80年代以后,日本还自行开发了超临界直流滑压运行锅炉。
德国是研究、制造超临界机组最早的国家,到1972年投运了一台容量为430MW的超临界机组,1979年投运了一台二次再热的475MW超临界机组,目前德国具有代表性的超临界机组是1992年8月投运的STARDINGER5号机组,其毛出力为553MW,经试验验证机组的净效率可达到43%。
据统计,至1995年,西屋公司制造850MW及以上容量火电机组共13台,其中超临界火电机组6台,最大超临界双轴机组的容量为1390MW,最大的超临界单轴机组为893MW,最大单轴亚临界机组为890MW。
GE公司生产850MW及以上容量火电机组共约10台,全部是超临界机组,最大的超临界双轴机组为1050MW,最大的超临界单轴机组为884MW。
ABB公司制造的850MW及以上容量火电机组,共约有9台,全部是超临界双轴1300MW—1428MW双速机组。
西门子公司已有10余台3000r/min(27kV)百万千瓦级发电机投入运行或正在安装,其中由西门子公司制造的上海外高桥900MW(1000MVA)超临界单轴机组(共2台,#2发电机定子由上海汽轮发电机有限公司分包)已于2003、及2004年投运。
见下表:
2百万千瓦级超超临界机组汽轮发电机参数与容量的选择
超超临界火电机组的汽轮发电机与亚临界或核电机组一样,它与超超临界的蒸汽压力等参数的选用都没有关系,但它必须由汽轮机拖动,它的容量、转速主要是根据汽轮机来确定。
当汽轮发电机的单机容量达到900MW及以上容量时,由于汽轮发电机设计的固有特点,就必须对其选用的电压及绝缘水平、定子绕组电动力与振动、定子端部损耗与热点、转子各部分的应力水平、转子临界转速、与汽轮机连接一起的轴系振动和扭振、发电机承受调峰、进相、负序和无励磁运行等非额定工况运行的能力等,进行分析论证,检查其已有的运行经验、试验数据和安全裕度。
自从第一台超临界机组在北美问世后,锅炉、汽机和其辅助设备已有了许多改进。
在机组容量、燃料形式(煤粉)和通风型式(平衡通风)相同的情况下,超临界机组的性能、可靠性已与亚临界机组一样好甚至更好。
这些改进也使更大容量的超超界机组的性能与小容量超临界机组或亚临界机组的一样好。
对汽轮发电机而言,单机容量在900MW(2极、50Hz)及以上的火电厂全球有数十家,核电厂也有十余家。
各制造厂商具有运行业绩的最大容量发电机如下:
西门子公司为1100MW,三菱公司为843MW,阿尔斯通为930MW。
由上述情况表明,国内发展百万千瓦级超超临界机组(单轴全速)的容量可在900~1100MW为宜。
3百万千瓦级超超临界机组(单轴全速)分析
国外发展超临界机组已有40余年的历史,超超临界机组比超临界及亚临界机组的煤耗低,在一定范围内,汽机的新汽温度或再热温度每提高10℃,机组热耗一般可下降0.25%~0.3%。
在温度和其他条件相同情况下,初压23.5MPa与16.2MPa相比较,300MW、600MW、1000MW机组净热耗下降分别约为1.3%、1.6%、1.8%,由此可见机组容量愈大,采用超超临界参数的效益越明显。
其优点如下:
1)从汽轮发电机组的布置上来说,单轴机组要比双轴机组节省投资。
2)热耗与机组价格—据ABB提供的资料,双轴双速8排汽型式同单轴型式的1000MW机组机比,其热耗要低0.2%,而双轴双速4排汽型式比单轴型式热耗低0.6%,但常规岛部分相应的成本却分别比单轴形式要高20%和30%。
这是因为双轴机组占地面积大,而且有两个发电机。
从经济角度来看,双轴较单轴(同容量)本体价格高约10%。
3)双轴双速机组由于两个轴系的功率相差很大,两者的转动惯量差距也非常大,且两轴系转速不同,使电气系统、尤其是保护系统的设计比较复杂,也给机组的控制和电厂的运行及管理等方面增加困难。
但由于机组容量的增大,需重点对以下问题进行研究:
1)对于1000MW级的两极汽轮发电机,其定子绕组上的电动力大,定子、转子动态特差,离心力引起的机械应力较大,由转子引起的疲劳应力也较大,对转子锻件、护环锻件等关键材料的要求高。
2)1000MW级机组采用单轴机组,转速只能是单一的3000r/min,此时,低压转子的末级叶片要超过1m以上,为减轻重量及轴受离心力,需采用钛合金长叶片来满足强度的需要。
我国在航空工业的基础上对钛材锻造加工等方面有一定经验,但在研制钛合金大叶片方面尚处于起步阶段。
3)轴系及稳定性设计——1000MW级机组,单轴转子长度增加,而且轴系的重量也比双轴机组大,轴承载荷加大,如采用六排汽式,加上高、中压缸和发电机,将成为一个有6个转子的轴系。
这样长的轴系在3000r/min下可能给机组带来如振动、轴系稳定性、扭振等一系列问题。
从上述分析可知,超临界1000MW级机组,单轴机组厂房占地面积小,机组价格也较低,如果电厂所在位置离制造厂较近,水路运输条件好且地价较高,可考虑选用单轴机组。
大型超超临界火电机组是我国火电机组的发展方向,国内研制超临界机组的起步容量为600MW,随着我国电网容量的不断增大,加上我国已具备开发研制超超临界900~1000MW火电机组的条件,900~1000MW机组已提到日程上来。
就发电机来说,1000MW级单轴全速机组需重点研究。
4百万千瓦级汽轮发电机参数与容量选择对机组造价的影响
一般来说,汽轮发电机的造价是与发电机的容量成正比关系的,如以900MW汽轮发电机(单轴全速)为例,造价约为1.3亿元人民币,那么,1000MW汽轮发电机(单轴全速)就为1.43亿元人民币。
另外,发电机的冷却方式、氢压等参数也与发电机的造价有关系。
5百万千瓦级汽轮发电机(单轴全速)初步方案设计
5.1研究确定方案设计时的基本原则
研究确定百万千瓦级汽轮发电机方案时遵循以下四条基本设计原则
*要设法做到“设计自主化”、“设备国产化”及“以我为主,中外合作”。
设计各方案时,尽量吸取外国的经验,并考虑我国国情,做到每个方案将来如必要与外国公司合作时,都能切实做到国产化。
*性能参数符合IEC、国标对汽轮发电机的要求。
*把可靠性放在首位,各方案所选用的铁心磁通密度等都不应超过其参考方案,并充分考虑在结构设计时采用外国公司百万千瓦级发电机和中国国内制造300MW、600MW机组中成熟可靠结构的可能性。
*在确保可靠性的前提下,力求采用国内材料以降低成本,提高综合经济指标。
5.2两极3000r/min发电机的四个设计计算方案
方案1系按德国西门子公司提供给上海外高桥电厂的超临界火电900MW27kV3000r/min发电机组的设计尺寸复核计算,冷却方式也完全按原设计:
即定子水内冷、转子绕组轴向径向氢内冷,定子铁心轴向氢气冷却,转子本体直径1250mm。
发电机在额定氢压0.5MPa、冷水温度为38℃时,额定功率为900MW,功率因数为0.9,此时氢气温升为33K。
若冷水温度为25℃时,在工况1006MW,功率因数为0.9,氢压为0.5MPa时,氢气温升为37K。
计算中,主要尺寸、槽数及绝缘规范等按有关资料保持不变,但在上层定子线棒中,西门子资料中空实心导线组数由2×
5组改为2×
6组。
方案2系按上海外高桥电厂超临界火电900MW火电机组招标时,美国西屋公司投标书的设计尺寸复核计算。
其冷却方式与方案1相同,即定子水内冷、转子绕组轴向径向氢内冷、定子铁心轴向氢气冷却,该发电机设计是在889MW60Hz3600r/min发电机的基础上放长铁心设计而成(相当于珠海电厂中746MW发电机机座号2-110×
250放长到2-110×
290而来),其转子直径为1168mm,和原WH公司机座号2-118×
280的发电机一致。
在额定氢压为0.5Mpa时,发电机的额定功率为900MW,功率因数为0.9。
计算中,转子槽内布置参照珠海746MW发电机。
方案3系按大亚湾核电站GEC900MW3000r/min发电机的设计尺寸复核计算。
转子本体直径1275mm,通风冷却方式按原设计即定子水内冷、转子副槽槽部(槽部轴向对流再径向)通风氢内冷,定子铁心径向氢冷,抽风式。
根据大亚湾核电站第一台机组在制造厂的温升试验时测量的转子线圈最热点温度最后仍有121.8℃(25槽第4匝),本课题组将转子线圈端部改为两路通风,降低最热点温度。
发电机在额定氢压0.425MPa,海水温度为33℃时,额定功率为900MW,功率因数为0.85;
若氢压为0.5MPa,海水温度为23℃,可运行工况为984MW,功率因数为0.85。
方案4系参照大亚湾核电站GEC900MW3000r/min发电机的基本设计尺寸重新设计,定子完全不变,转子绕组采用气隙取气氢内冷,定子铁心径向氢冷。
转子槽形尺寸、转子铜线外形尺寸都不变,转子绕组为气隙取气而开两排孔,取消转子通风副槽。
由于取消了副槽,使发电机转子满载励磁电流用西屋计算方法减小了约2%,用我国(DZ)28~63计算公式计算约减少为5.5%。
5.3电磁设计方案分析
1)方案1(参考KWU)
方案1和方案2相似,定子铁心为轴向通风孔,转子绕组槽内和端部为线匝中的轴向通风孔冷却。
由于铁心采用轴向通风孔冷却,总铁心散热面积小,需要加快气体流速,又风道长,需要多级串联的风扇率达到高压头。
方案1的风扇为4级串联,压头为23.1KPa。
但定子铁心采用轴向通风孔冷却时,因没有径向风道,在定子铁心相同名义尺寸下,有效定子铁心长度长了,齿轭具有更大的导磁面积。
方案1和方案2的转子绕组为线匝轴向通风孔冷却。
风道长,并且转子电密高,也需要更高风扇压头来达到冷却效果;
相对于方案3,冷却能力更强,特别是转子绕组端部,因此几个方案通风方式中,方案1和方案2的风扇压头最大。
方案1和方案2的转子冷却效果好,转子线圈电密大,在相同的励磁电流下,相对方案3可以取较小的槽形尺寸。
而方案1的转子外径比方案2要大的多,当槽分度数相同时,因为方案1可以取较大的齿槽宽,较少的槽数,并采用矩形槽,其槽分度比为28/45,有利于降低转子绕组和转子加工的成本。
方案1的气隙长度为80mm,在各方案中最小,可以减小励磁电流,但它的短路比也相对较小。
据有关资料介绍,两极汽轮发电机转子本体的直径为1250mm时,其中心孔的切向引力已接近目前锻件许用应力的极限,但1250mm直径的转子已在BBC公司和原苏联电力厂得到应用,1275mm直径的转子已在GEC公司得到应用。
方案1的转子本体直径D2为1250mm,方案2为1168mm。
方案1和方案2的转子通风方式都是线匝中的轴向通风孔通风,冷却能力相似,且额定容量MVA相同时,D22L2差不多,分别为10.51m3和9.98m3,因此方案1转子本体长度L2最短为为6730mm。
方案1的D22L2较小,而其线电压最高,铁心为轴向通风冷却,在齿部要开轴向孔所以必须增大齿宽来维持一定磁密。
为此方案1定子槽形设计较狭长,槽底处直径相对较大,其铁心外径相对也较大,为3280mm,轭部磁密为1.35T,远低于其他两个方案。
而它的定子铁心外径大,叠片总重320吨,定子运输重为450吨。
方案1的定子线圈采用双排导线布置,其空心导线采用不锈钢材料,高度4mm,壁厚0.9mm。
采用不锈钢导线后,附加损耗减小,因壁厚减小,相对的可以增大通水面积。
同时相对于空心铜线,水流速度可以增加,来加强冷却效果。
但采用不锈钢导线使定子线棒导电面积减小,定子直流电阻稍增大。
2)方案2(参考WH)
方案2的转子本体直径D2为1168mm,小于其他方案。
D2为1168mm的转子已在珠海电厂中得到应用。
转子槽数为32,转子槽形为半平行梯形槽,相对于方案1平行槽,可以相对增大槽内铜导线的面积。
定转子间隙δ为96.52mm,比方案1的大,因此短路比也比方案1的大。
方案2的轭部磁密和齿部磁密比方案1大,而且铁心长度长,因此需要更高的风扇压头达到其冷却效果。
方案2计算得出额定励磁电流IfN最大,转子励磁损耗也最大,需要更大的励磁机容量,其对励磁系统的要求更高。
3)方案3(参考GEC)
方案3的转子直径D2为1275mm,是目前世界上两极发电机最大的转子本体外径,GEC公司是基于80年代初期可以提供的锻件最高强度水平,采用副槽通风也需要较大的转子直径,靠近大齿槽采用短槽以减小大齿根部磁密。
由于方案3的转子槽内通风方式为副槽通风,所以MVA/D22L2较小。
方案3和方案4的定子铁心采用径向通风冷却方式,铁心散热面积大,冷却效果好。
总风路通道面积大,风路相对较短,所需风扇压头较小,便于和需风扇压头较小的转子绕组通风方式如副槽通风、气隙取气通风方式相配合。
方案3的转子绕组通风方式为副槽通风,冷却转子槽内导体的气流全部从副槽进入,利用绕组自身的离心风压(加上部分风扇压头)形成冷却气流,从而不需要设置多级高压风扇。
一般全径向出风的副槽通风转子铜线风道的面积约为副槽风道面积的6~8倍,在满足铜线风道风速的前提下,副槽口的风速可能达到难以实现的数据。
而方案3中,从副槽进入铜线的气流先进入径向风道,再流入铜线中的轴向风道,充分冷却铜线。
并且铜线内采用双风道,双风道内的气流按相对方向流动。
使得其铜线风道面积仅为副槽口面积的大约2.4倍。
方案3的转子端部铜线为线匝通风孔轴向冷却,其风扇压头较低,采用加大风道截面积来增加冷却气流。
其转子电密为9.42A/mm2,比方案1(11.6A/mm2)和方案2(11.54A/mm2)的要小。
方案3的转子槽数为32,转子槽形为矩形的梯形槽,可以提高槽满率,加上副槽平均高度后,其槽高为194.5mm。
方案3的定转子间气隙为δ的117.5mm,虽然其功率因数为0.85,但它的短路比仍为最大,静态稳定能力强,但成本也略有增加。
为加大定子线圈通水面积,方案3的所有铜线均采用空心铜线,同时为减小环流附加损耗。
其内两排铜线和外两排铜线分别单独换位。
这样的换位一个线圈需要增加2个空心铜线高度,比一般的换位多1个空心铜线高度。
该方案按其最大出力计算,定子线圈电流密度较大。
方案3的额定励磁电压最高,励磁机的制造更难。
但如果工况与方案1和方案2相同,它的励磁电压将降为473伏。
在相同的工况900MW,功率因数为0.90时,方案1、方案2和方案3的效率根据KWU、WH、GEC分别为98.91%、98.94%、98.88%.在相同工况下,方案3的附加损耗要比方案2大1156kW。
方案3的氢压较小且所需风扇压头较低,根据GEC、WH的资料,方案3的通风损耗比方案2小452kW。
其铁耗比方案2大207kW。
方案3的额定工况为900MW,功率因数为0.85,相对于功率因数为0.90,其转子励磁损耗、定子铜耗、附加损耗分别增加456kW、191kW、316kW,使得其效率降为98.77%。
4)方案4(STGC)
方案4和方案3相比,转子取消副槽,因而其转子额定励磁电流减小,转子铜耗减小,提高效率。
5.4通风系统计算说明
通风冷却方式是大型汽轮发电机设计的主要问题之一,发电机单机容量增加是依靠材料进步和电磁负荷密度提高来实现的。
有效材料主要是转子锻件受机械性能和轴系动力特性的限制,是有限度的。
电磁负荷密度的提高导致单位体积发热的增加,需要通过改进冷却方式来解决。
综观世界各主要发电设备制造厂家的情况,在百万千瓦容量等级,无论是两极或是四极机组,冷却方式主流是水氢氢,定子线圈水内冷是比较普遍的。
各家公司的技术特点主要是转子线圈的氢内冷方法。
在从50年代开始起的半个世纪内,一些具有创新的公司各自发展了自己独特的转子通风系统,并随着单机容量的增加,积累了大量的研究、试验、设计、运行数据,可以说都已趋于成熟阶段,每种通风方式都有许多台机组成功的运行。
只要充分掌握每种通风系统的特点和局限,哪一种方式都是可行的。
气隙取气斜流通风
这是一种自通风方式,维持气体在导体内循环的压力主要来自转子自身的泵压作用,转子槽楔进风斗和出风斗合理的空气动力形状是保证导体内有足够气体流量的关键因素。
在斜流流道内气体具有较高的流速,是充分发展的紊流,流道又呈长径比较大的长方形,因此具有较高的散热系数。
一般用吸风系数表示系统的通风性能
u=kv
u------斜流风道气体速度
k------吸风系数
v-----转子表面线速度
可见这种通风系统在转速高的两极机组上能充分发挥其长处。
在整个转子长度方向,进出风区是交替布置的,形成多个并联支路。
发电机容量增加,只要增加并联风区数。
设计具有很大灵活性。
槽底副槽径向通风
本质上这也是一种自通风方式,转子表面和副槽底部位置处离心力差是构成气体循环之压力。
决定系统流量大小的主要因素是副槽轴向风道面积,副槽进风口流速一般在100m/s,该处具有最大的流动阻力,气流压力降大部分发生在副槽轴向风道内。
发生热交换的导体径向风道内气体流速大约在20m/s左右,相应雷诺数3000~5000范围,是尚未充分发展的紊流区。
转子直径较大也是其设计特点之一。
传统的导体内径风道是单排或双排的径向狭长孔。
近来出现了一些创新的结构,气流并非完全径向流动,有部分路径是轴向,呈轴向和径向混合型。
轴向-径向通风
轴向-径向通风是一种主要依靠外加高压多级风扇来维持气体在导体内流动的通风方式。
气体经位于绕组端部的进风孔从两端分别进入导体的轴向风道,在转子中间经径向孔从槽楔排出。
随着单机容量增加,转子长度放长,需要的风扇级数也增加。
转子冷却风量几乎完全由风扇压力来调节。
导体内轴向流速在60~100m/s范围,雷诺数远大于10,000。
由于高压风扇的存在,定子铁心一般采用轴向通风,这也是本系统的一个特点。
两极900MW发电机通风计算的四种方案
在两极900MW全速发电机中,共列出了三种通风方式4个方案。
方案1和方案2同为轴向?
径向通风系统,定子铁心都是轴向通风。
方案3是副槽通风,方案4是气隙取气斜流通风,两者铁心是径向通风。
方案3是单路抽风式。
方案4是多进多出系统。
各方案计算结果见下表1。
轴向-径向通风的两个方案中,方案1来源于西门子外高桥900MW,方案2是西屋公司系列设计中转子外径46英寸的一个设计。
这种通风系统是西屋公司的传统,从中等容量到大容量,无论是两极还是四极,都是统一的通风系统。
据其发布的信息已经有20余台700MW以上容量的机组投入运行。
对其成熟性是无庸质疑的。
上海汽轮发电机公司分享其全部技术成果。
转子导体高电流密度是其设计特点,与之相应,导体内高气流速度、高雷诺数、高散热系数。
与其他通风方式相比,转轴本体的有效尺寸D2L较小,转子用铜较少。
高压多级风扇是这种通风方式的特点。
这两个方案转子绕组温度计算所用程序都是西屋公司标准程序TG3248和端部TG3255,额定功率时方案1转子绕组最高温升和平均温升分别是56K和36K,最大容量时最高温升70K。
额定功率时方案2转子绕组最高温升和平均温升分别是63.4K和39.2K,最大容量时最高温升79.2K。
副槽通风
方案3是副槽通风,其主要尺寸按大亚湾2极900MW复算。
需要说明的是,大亚湾的转子通风并非传统副槽通风中气体在导体上是单径向流动,它是一种轴向和径向的混合型流动。
由于暂时未获得其结构的详细资料,我们在这里引用了该机组满电流试验的温度数据,转子绕组最高温升80K,平均温升30.5K。
与传统的单径向流动相比,这种混合型流动显然要好。
在单径向流动的副槽通风系统中,尽管可以采用多种方法,如副槽槽形的锥形、阶梯形,槽楔出风口的孔尺寸的多样化,变节距通风孔,总不能使径向风道分布完全均匀,这就导致存在一定的轴向温度差,限制了发电机出力。
混合型通风则克服了这一缺点,使轴向温差更小。
因此下一步的任务是开发这种结构型式的转子风量和温度分布程序,作为起点,应该从单件模型试验入手,再做整机模型,直至编制出符合实际的温度计算分析软件。
方案4气隙取气斜流通风,从通风性能来评价,是最适合两极发电机的。
本公司设计基础是600MW发电机。
该机是1987年中国两家厂的联合设计,集两家多年的设计和制造经验,又吸收了西屋公司的成熟结构。
在首台机组投产前,本公司又做了大量基础性科研工作,其中一项就是转子槽楔进、出风斗的空气动力性能测试,对多种结构形状进行了对比试验,确定了最适合的方案用于产品。
和600MW相比