《机床数控技术》课程设计指导书Word格式文档下载.docx
《《机床数控技术》课程设计指导书Word格式文档下载.docx》由会员分享,可在线阅读,更多相关《《机床数控技术》课程设计指导书Word格式文档下载.docx(10页珍藏版)》请在冰豆网上搜索。
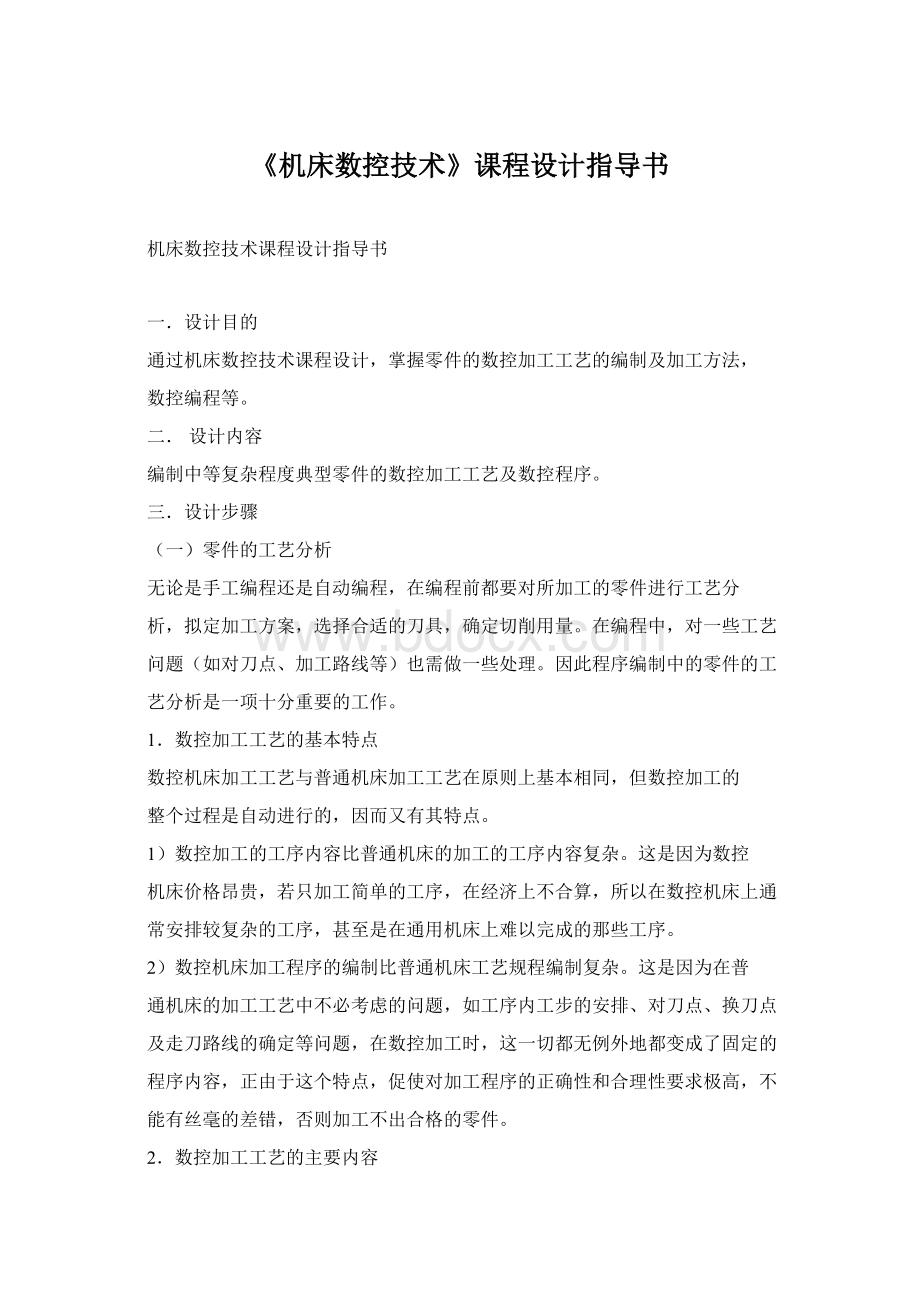
2)零件图纸的数控工艺性分析;
1
3)制订数控工艺路线,如工序划分、加工顺序的安排、基准选择、与非数
控加工工艺的衔接等;
4)数控工序的设计,如工步、刀具选择、夹具定位与安装、走刀路线确定、
测量、切削用量的确定等;
5)调整数控加工工艺程序,如对刀、刀具补偿等;
6)分配数控加工中的容差;
7)处理数控机床上部分工艺指令。
3.
数控加工零件的合理选择
程序编制前对零件进行工艺分析时,要有机床说明书、编程手册、切削用
量表、标准工具、夹具手册等资料,方能进行如下一些问题的研究。
在数控机床上加工零件时,一般有两种情况。
第一种情况:
有零件图样和
毛坯,要选择适合加工该零件的数控机床。
第二种情况:
已经有了数控机床,
要选择适合在该机床上加工的零件。
无论哪种情况,考虑的主要因素主要有,
毛坯的材料和类型、零件轮廓形状复杂程度、尺寸大小、加工精度、零件数量、
热处理要求等。
概括起来有三点,即零件技术要求能否保证,对提高生产率是
否有利,经济上虽否合算。
根据国内外数控技术应用实践,数控机床通常最适合加工具有以下特点的
零件:
(1)多品种、小批量生产的零件或新产品试制中的零件;
(2)轮廓形状复杂,对加工精度要求较高的零件;
(3)用普通机床加工时,需要有昂贵的工艺装备(工具、夹具和模具)的
零件;
(4)需要多次改型的零件;
(5)价值昂贵,加工中不允许报废的关键零件;
(6)需要最短生产周期的急零件。
数控加工工艺性分析涉及面很广,在此仅从数控加工的可能性和方便性两
方面加以分析。
(1)零件图样上尺寸数据的给出应符合编程方便的原则;
A零件图样上尺寸标注方法应适应数控加工的特点,在数控加工零件图上,
2
应以同一基准引注尺寸直接给出坐标尺寸。
B构成零件轮廓的几何元素的条件应充分
在手工编程时,要计算每个节点坐标。
在自动编程时,要对构成零件轮廓
的所有几何元素进行定义。
因此在分析零件图时,要分析几何元素的给定条件
是否充分。
如果构成零件几何元素条件不充分,编程时则无法下手。
(2)零件各加工部位的结构工艺性应符合数控加工的特点
A零件的内腔和外形最好采用统一的几何类型和尺寸。
这样可以减少刀具
规格和换刀次数,使编程方便,生产效益提高。
B内槽圆角的大小决定着刀具直径的大小,因而内槽圆角半径不应过小。
C零件铣削底平面时,槽底圆角半径不应过大,否则铣刀端刃铣削平面的
能力差、效率低。
D应采用统一的基准定位。
在数控加工中,若没有统一的基准定位,会因
工件重新安装而导致加工后的两个面年轮廓位置及尺寸不协调现象。
此外,还应分析零件所要求的加工精度、尺寸公差是否为以得到保证,有
无引起矛盾的多余尺寸或影响工序安排的封闭尺寸等。
4.
加工方法的选择与加工方案的确定
1)加工方法的选择
加工方法的选择原则是保证加工表面的加工精度和表面粗糙度的要求。
由
于获得同一级精度及表面粗糙度的加工方法一般有许多,因而在实际选择时,
要结合零件的形状、尺寸大小和热处理要求等全面考虑。
2)加工方案确定的原则
零件上比较精确表面加工,常常是通过粗加工、半精加工和精加工逐步达
到的。
对这些表面仅仅根据质量要求选择相应的最终加工方法是不够的,还应
正确地确定从毛坯到最终成形的加工方案。
5.
工序与工步的划分
一般工序划分有以下几种方式
1)按零件装卡定位方式划分工序
由于每个零件结构形状不同,各表面的技术要求也有所不同,故加工时,
其定位方式则各有差异。
一般加工外形时,以内形定位;
加工内形时又以外形
3
定位。
因而可根据定位方式的不同来划分工序。
2)按粗、精加工划分工序
根据零件的加工精度、刚度和变形等因素杰划分工序时,可按粗、精加工
分开的原则来划分工序,即先作粗加工再精加工。
此时可用不同的机床或不同
的刀具进行加工。
通常在一次安装中,不允许将零件的某一部分表面加工完毕
后,再加工零件的其它表面。
3)按所用刀具划分工序
为了减少换刀次数,压缩空程时间,减少不必要的定位误差,可按刀具集
中工序的方法加工零件,即在一次装夹中,尽可能用同一把刀具加工出可能加
工的所有部位,然后再换另一把刀加工其它部位。
工步的划分主要从加工精度和效率两方面考虑。
在一个工序内往往需要采
用不同的刀具和切削用量,对不同表面进行加工。
为了便于分析和描述较复杂
的工序,在工序内又细分为工步。
总之,工序与工步的划分要根据具体零件的结构特点、技术要求等情况综
合考虑。
6.零件的安装与夹具的选择
1)定位安装的基本原则
在数控机床上加工零件时,定位安装的基本原则与普通机床相同,也要合
理选择定位基准和夹紧方案。
为了提高数控机床效率确定定位基准与夹紧方案
时应注意下列三点:
(1)力求设计、工艺与编程计算的基准统一;
(2)减少装夹次数,尽可能在一次定位装夹后,加工出全部待加工表面;
(3)避免采用占机人工调整式加工方案,以充分发挥数控机床的效能。
2)选择夹具的基本原则
数控加工对夹具要有两方面要求:
一是要保证夹具的坐标方向与机床的坐
标方向相对固定;
二是要协调零件和机床坐标系的尺寸关系。
此外,尚需考虑
以下四点:
(1)夹具结构应力求简单。
当零件加工批量不大时,应尽量采用组合夹具、
可调式夹具及其它通用夹具,以缩短生产准备时间、节省生产费用;
成批生产
4
时考虑采用专用夹具;
(2)零件的装卸要迅速、方便,以缩短机床的停顿时间;
(3)夹具要开敞,其定位、夹紧机构或其它元件不得影响加工中的走刀;
(4)夹具在机床上的安装及工件在夹具上的安装要准确可靠,以保证工件
在正确的位置上按程序加工。
此外,为了提高数控加工的效率,在成批生产中还可以采用多位、多件夹
具。
7.刀具的选择与切削用量的确定
1)刀具的选择
刀具的选择是数控加工中重要的工艺内容之一,它不仅影响机床的加工效
率,而且直接影响加工质量。
编程时,选择刀具通常要考虑机床的加工能力、
工序内容、工件材料等因素。
与传统的加工方法相比,数控加工对刀具的要求更高。
不仅要求精度高、
刚度高、耐用度高,而且要求尺寸稳定、安装调整方便。
这就要求采用新型优
质材料制造数控加工刀具,并优选刀具参数。
选取刀具时,要使刀具的尺寸与被加工工件的表面尺寸和形状相适应。
生
产中,平面零件周边轮廓的加工,常采用立铣刀。
铣削平面时,应选硬质合金
刀片铣刀;
加工凸台、凹槽时,选高速钢立铣刀。
对一些主体型面和变斜角轮廓形的加工,常采用球头铣刀、环形铣刀、鼓
形刀、锥形刀和盘形刀。
曲面加工常采用和球头铣刀,但加工曲面较低平坦部位时,刀具以球头顶
端刃切削,切削条件较差,因而应采环形刀。
2)切削用量的确定
切削用量包括主轴转速(切削速度)、切削深度或宽度、进给速度(进给量)
等。
对于不同的加工方法,需选择不同的切削用量,并应编入程序单内。
合理选择切削用量的原则是:
粗加工时,一般以提高生产率为主,但也考
虑经济性和加工成本;
半精加工和精加工时,应在保证加工质量的前提下,兼
顾切削效率、经济性和加工成本。
具体数值应根据机床说明书、切削用量手册,
并结合经验而定。
5
8.
对刀点和换刀点的确定
在编制加工程序时,要正确地选择“对刀点”和“换刀点”的位置。
“对刀点”就是在数控机床上加工零件时,刀具相对于工件运动的起点。
由于程序段从该点开始执行,所以对刀点心也叫做“程序起点”或“起刀点”。
选择对刀点的原则是:
1)要便于数学处理和简化程序编制
2)在机床上找正容易;
3)加工过程中检查方便;
4)引起的加工误差小。
对刀点可选在工件上,也可选在工件外面(如选在夹具上或机床上)。
但必
须与零件的定位基准有一定的尺寸联系。
这样才能确定机床坐标系和工件坐标
系的关系。
为了提高加工精度,对刀点应尽量选在零件的设计基准或工艺基准上,如
以孔定位的工件,可选孔的中心作为对刀点。
刀具的位置则以此孔来找正,使
“刀位点”与“对刀点”重合。
所谓“刀位点”是指车刀、镗刀的刀尖;
钻头
的钻尖;
立铣刀、端铣刀刀头底面的中心、球头铣刀的球头中心。
零件安装时,工件坐标系要与机床坐标系有确定的尺寸关系,在工件坐标
系设定后,从对刀点开始的第一个程序段的坐标值,为对刀点在机床坐标系中
的坐标值。
对刀点既是程序的起点,也是程序的终点。
因此在成批生产中要考虑对刀
点的重复精度,该精度可用对刀点相距机床原点的坐标值来校核。
所谓“机床
原点”是指机床上一个固定不变的极限点。
例如,对车床而言,是指车床主轴
回转中心与车头卡盘端面的交点。
“换刀点”是为数控车床、数控加工中心等多刀加工机床的编程设定的,
回为这些机床加工中途需更换刀具,故应规定换刀点。
所谓“换刀点”是指刀
架转位换刀时的位置。
该点可以是某一固定点(如加工中心机床,其换刀机械
手的位置是固定的),也可以是任意的一点(如车床)。
换刀点的位置应设在工
件或夹具的外部,以刀架转位时不碰工件及其它部件为准。
其设定值可用实际
测量方法或计算确定。
6
9.加工路线的确定
在数控加工中,刀具刀位点相对于工件运动轨迹称为加工路线。
编程时,
加工路线的确定原则主要有以下几点:
1)加工路线应保证被加工零件的精度和表面粗糙度,且效率高;
2)使数值计算简单,以减少编程工作量;
3)应使加工路线最短,这样既可减少程序段,又可减少空刀时间。
4)此外,确定加工路线时,还要考虑工件的加工余量和机床、刀具的刚度
等情况,确定是一次走刀,还是多次走刀来完成加工以及在铣削加工中是采用
顺铣还是采用逆铣等。
10.程编误差及其控制
数控机床突出特点之一是:
零件的加工精度不仅在加工过程中形成,而且
在加工前程编阶段就已形成,程编阶段的误差是不可避免的,这是由于程序控
制的原理本身决定的。
在程编阶段,图纸上的信息转换成控制系统可以接受的
形式,会产生如下三种误差:
近似计算误差、插补误差、尺寸圆整误差。
在点位控制加工中,程编误差包含尺寸圆整误差一项,并且直接影响孔位
置尺寸精度。
在轮廓控制加工中,影响轮廓加工精度的主要是插补误差,而尺寸圆整误
差的影响则居次要地位,所以,一般所就的程编误差系指插补误差而言。
因为还有控制系统与拖动系统的误差,零件定位误差,对刀误差,刀具磨
损误差,工件变形误差等等,所以,零件图纸上给出的公差,只有一小部分允
许分配给程编过程中产生的误差。
一般取允许的编程误差等于零件公差的
0.1~0.2。
(二)编程中工艺指令的处理
在数控机床上加工零件的动作都必须在程序中用指令方式事先予以规定,
在加工中由机床自动实现。
我们称这类指令为工艺指令。
这类指令有国际标准,
即准备功能指令
G
辅助功能指令
M
两大类。
在编制加工程序时,必须按程编手
册正确选用和处理。
(三)程序编制及动态模拟软件的使用
具体内容及详见机床使用手册。
7
四、典型零件工艺与程序编制
1、
加工轴类零件如图
1,毛坯为
Φ85㎜×
340㎜棒材,零件材料为
45
钢,
无热处理和硬度要求,图中
Φ85㎜外圆不加工。
对该零件进行精加工。
根据图
纸要求和毛坯情况,编制该零件数控车削工艺与程序。
图
1车削
轴类零件
8
2、典型轴类零件介绍
2
所示为变速器一轴热处理前零件简图。
该零件材料为
20CrMnTi,毛坯为模缎件,硬度为
156-207HBS,是国内某型
号汽车变速器上的零件,为大量生产类型产品。
该零件为由双联齿形、矩形花
键、径向孔、内孔、外圆柱面、外圆锥面、过渡圆角、内外环槽等表面组成的
轴类零件,加工表面较多,适合在数控车上加工。
试编制其数控加工工艺与程
序。
变速器——轴热处理前零件图
9
3、图
3
所示为减速箱箱体图。
零件材料为
HT200,中批量生产,分析其加
工工艺并编制数控程序。
减速箱箱体简图
10
4、图
4
所示为拨叉简图。
HT200,中批量生产,分析其加工工
艺并编制数控程序。
。
拨叉简图
五.实验报告
1.数控加工工艺卡片
2.数控加工程序单
11
12