数控加工综合实践周报告谢Word下载.docx
《数控加工综合实践周报告谢Word下载.docx》由会员分享,可在线阅读,更多相关《数控加工综合实践周报告谢Word下载.docx(18页珍藏版)》请在冰豆网上搜索。
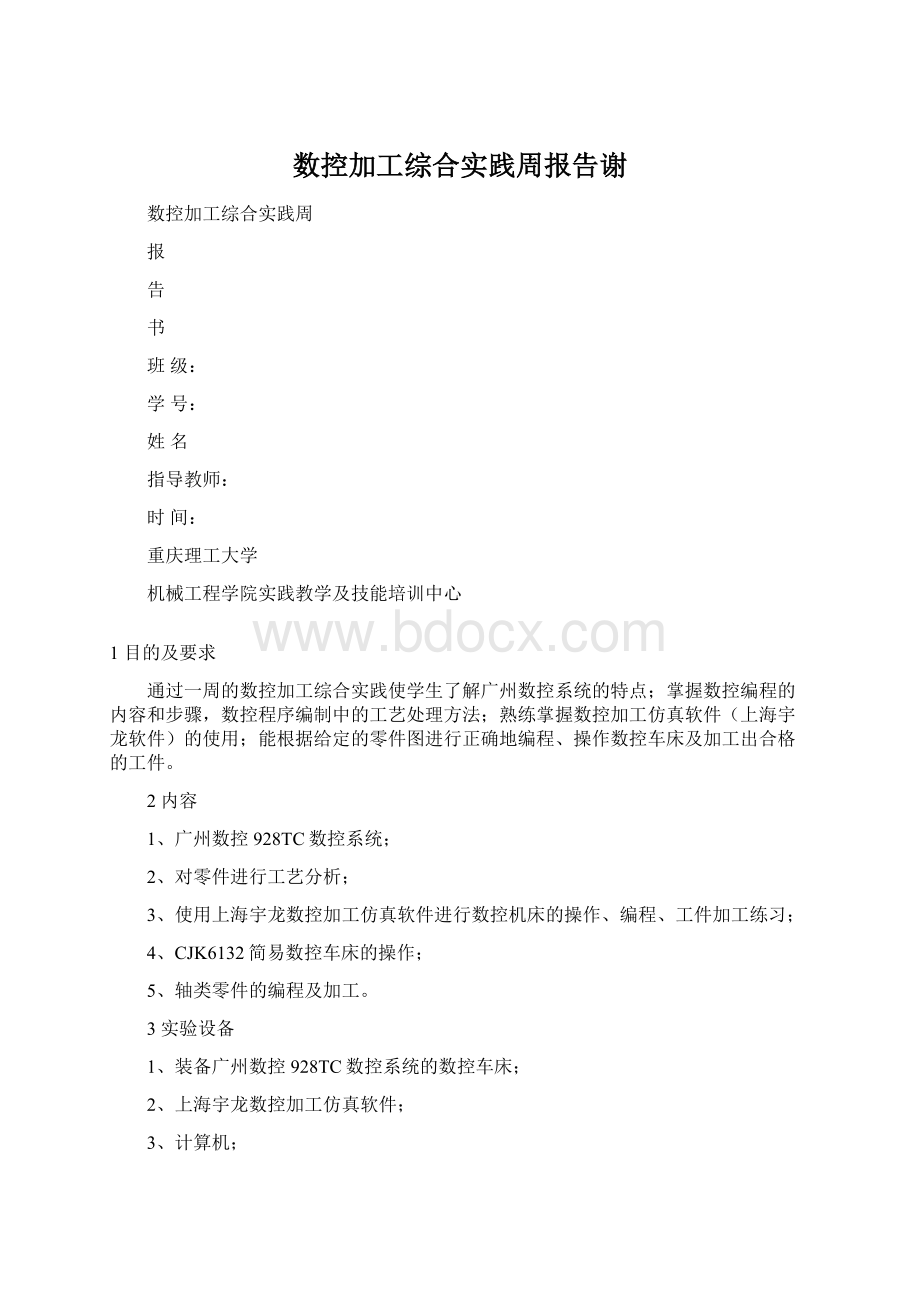
初始方式为单步方式。
按键可以进行手动点动和手动单步方式的相互切换。
当系统配置有电子手轮时还可以选择手轮控制方式。
手动点动方式显示如图11所示
图11手动点动工作方式
第三种自动工作方式
在自动工作方式中,系统按照选定的零件程序逐段执行,加工出合格的工件。
按工作方式选择键进入自动工作方式。
自动工作方式中有机床锁住运行和加工运行方式以及单程序段加工运行和连续加工运行方式,如图15所示
图15自动工作方式
第四种参数设置工作方式
GSK928TC-1数控系统设计了P01~P25共25参数,每个参数都有其确定的含义并决定数控系统及机床的工作方式,在机床安装调试时应对其中的某些参数进行修改。
按工作方式选择键按
进入参数设置工作方式。
第一屏显示P01~P09共9个参数,如图21所示
第五种刀偏设置工作方式
本系统设置了T1~T8共8组刀偏值,每组刀偏有Z轴、X轴方向两个数据。
其中可通过手动对刀操作自动生成的刀偏组数量和使用的刀具总数相同。
其余的刀偏数据只能通过键盘输入。
9号刀偏为回机械零点后的坐标设定值。
在指令中不能使用T*9,否则出现“参数错”报警。
按工作方式选择
键,进入刀偏设置工作方式,显示如图23所示
第六种诊断
本数控系统设置了自诊断功能,可显示输入/输出接口中外部信号的状态及主轴转速等。
按工作方式选择
键,进入诊断方式。
诊断方式显示如图24所
注:
当参数P11的CHCD位设置为0(即不检测主轴编码器)时上图中编码器线数不显示。
若没有安装主轴编码器或没有启动主轴,屏幕显示编码器线数=0000。
按其他任一方式键退出。
5数控机床简介
数控车床是目前使用较为广泛的数控机床之一。
它主要用于轴类零件或盘类零件的内外圆柱面、任意锥角的内外圆锥面、复杂回转内外曲面和圆柱、圆锥螺纹等切削加工,并能进行切槽、钻孔、扩孔、铰孔及锥孔等。
本次数控加工实践周所用的数控机床为CJK6132车床,外形如图2所示,它采用卧式车床布局,具体参数如下表1所示。
图2CJK6132型简式数控车床
表1CJK6132数控车床主要技术参数
项目
参数
最大工件回转直径
320mm
最大车削直径
170mm
最大车削长度
750mm
床面中心高
160mm
纵溜板移动距离
主轴内孔直径
30mm
主轴内孔锥度
莫氏5号锥度
主轴端到外锥体的锥度
1:
4
主轴转速
180~1450r/min
主轴转速级数
8级
横向快速移动速度
2000mm/min
纵向快速移动速度
4000mm/min
刀架进给速度范围
横向:
6mm~2000mm/min;
纵向:
12mm~4000mm/min
回转刀架刀具容量
4把
装刀架支承面到顶尖中心线的高度
20mm
横溜板最大移动距离
尾座导筒最大移动距离
95mm
尾座导筒内孔锥度
莫氏4号锥度
尾座横向移动距离(以主轴中心为准)
±
10mm
主电机功率
3/4.5KVA
步进电机最大静转矩
10N·
m
外型尺寸(长×
宽×
高)
2160mm×
1070mm×
1560mm
控制系统
GSK928TC
控制系统脉冲当量
0.001mm
6数控车床编程
数控机床的自动加工过程,就是按照事先编写好的零件程序自动运行的过程。
所谓编程,就是根据加工零件的图纸和工艺要求,把它用数控语言描述出来,编制成零件的加工程序。
GSK928TC常用指令代码及其功能介绍如下:
1)常用G功能—准备功能
G00—快速定位
指令格式:
G00X(U)Z(W);
G00指令使刀具以快速移动速度移动到指定位置。
其中X(U)Z(W)为指定点坐标值。
G01—直线插补
指令格式:
G01X(U)Z(W)F:
G01指令使刀具按设定速度沿当前点到X(U),Z(W)指定点的连线同时到达指定的终点位置。
其中X(U)Z(W)为指定的终点坐标。
F-进给速度.单位:
mm/min
G02G03—圆弧插补
G02X(U)Z(W)IKF;
圆心坐标编程
G03X(U)Z(W)IKF;
或G02X(U)Z(W)RF;
半径编程
G03X(U)Z(W)RF:
2)循环指令
G90—内外圆柱面车削循环
G90X(U)Z(W)RF;
其中:
X(U)Z(W)—柱(锥)面终点位置,两轴坐标必须齐备,相对坐标不能为零。
R—循环起点与循环终点的直径之差。
省略R为轴面切削。
F—切削速度。
G92—螺纹切削循环
G92X(U)Z(W)P(E)IKRL;
其中I不能取负值。
其中:
X(U)Z(W)—螺纹终点的坐标位置.
P—公制螺纹螺距。
范围:
0.25~100mm
E—英制螺纹导程。
100~0.25牙/英寸
I—螺纹退尾时X轴方向的移动距离。
当K≠0时省略I则默认I=2×
K即45℃方向退尾。
K—螺纹退尾时退尾起点距终点在Z轴方向的距离。
R—螺纹起点与螺纹终点的直径之差(螺纹锥度,省略R为直螺纹)。
L—多头螺纹的螺纹头数(省略L为单头螺纹)范围:
1~99。
当R≠0时R<
0退尾方向为正向(X向正方向移动),R>
0退尾方向为负向(X向负方向移动)。
当R=0K≠0时,由K的符号决定X轴的退尾方向。
K>
0退尾方向为正向,(X向正方向移动),
K<
0退尾方向为负向(X向负方向移动)。
当R≠0K≠0时,R决定锥度方向,K决定退尾方向。
G94—内、外圆端(锥)面车削循环
G94X(U)Z(W)RF;
X(U)Z(W)—终点坐标。
两轴坐标必须齐备,相对坐标不能为零。
R—锥面起点Z向坐标与锥面终点Z向坐标之差。
省略R为端面切削。
G74—端面深孔加工循环
G74X(U)Z(W)IKREF;
X(U)Z(W)—孔底坐标。
省略X为深孔钻循环。
I—每次Z轴进刀量(Z轴)。
K—每次Z轴退刀量(Z轴)。
R—啄钻循环或深孔循环选择。
当省略R或R=0时每次退刀仅退K的距离即啄钻循
环。
当R≠0时每次退刀都退到第一次钻孔的起始点即深孔钻循环。
E—在X轴方向每次的偏移量(直径值)。
F—进刀速度。
G75—切槽循环
G75X(U)Z(W)IKEF;
其中I/K不能为负值。
X(U)Z(W)—槽终点坐标。
省略Z为切断循环。
I—每次X轴进刀量。
K—每次X轴退刀量。
E—在Z轴方向每次的偏移量。
G71-外园粗车循环
G71X(U)IKLF;
X(U)—精加工轮廓起点的X轴坐标值.
I—X轴方向每次进刀量,直径值表示,无符号数.
K—X轴方向每次退刀量,直径值表示,无符号数.
L—描述最终轨迹的程序段数量(不包括自身)。
范围:
1—99
F—切削速度。
G72—端面粗车循环
G72Z(W)IKLF;
Z(W)—精加工轮廊起点的Z轴坐标值;
I—Z轴方向每次进刀量;
K—Z轴方向每次退刀量;
L—描述最终轨迹的程序段数量(不包括自身)。
1-99;
F—切削速度
G22G80—程序局部循环
在实际加工过程中,对于某些局部需要反复加工或已基本成型的零件,可使用局部循环指令
来简化编程。
局部循环的循环体由用户编程,执行后的结束点坐标由程序运行后决定。
在程序中G22和G80必须成对使用。
在循环体中不能再有G22指令,即G22指令不
能嵌套。
G22L
:
G80
L—循环次数范围1-99L=1时不能省略。
若L>
99,则程序将出现“参数错”报警。
3)M功能—辅助功能
指令功能编程格式说明
M00暂停等待启动M00按运行键再启动
M02程序结束M02
M20程序结束M20
返回第一段循环加工
M30程序结束
关主轴、关冷却液M30
M03主轴顺时针转动M03
M04主轴逆时针转动M04
M05关主轴M05
M08开冷却液M08
M09关冷却液M09
M10工件夹紧M10
M11工件松开M11
M41主轴换第一档M41
M42主轴换第二档M42
M43主轴换第三档M43
M78尾座前进M78
M79尾座后退M79
M97程序转移M97P由P指定转移入口程序段号
M98子程序调用M98PL由P指定转移入口程序段号
M99子程序返回由L指定调用次数
M21置1号用户输出有效M21D
M22置1号用户输出无效M22D
M23置2号用户输出有效M23D
M24置2号用户输出无效M24D
M911号用户输出有效时等待M91P由P指定转移入口程序段号直到输入无效
M921号用户输入无效时等待M92P由P指定转移入口程序段号直到输入有效
M932号用户输入有效时等待M93P由P指定转移入口程序段号直到输入无效
M942号用户输入无效时等待M94P由P指定转移入口程序段号直到输入有效
3)S功能—主轴功能
通过地址符S和其后的数据把代码信号送给机床,用于控制机床的主轴转速。
根据机床的具体配置,通过参数P12的MODS位,选择主轴功能是用于控制多速电机还是变
频电机。
0~4(多速电机);
0~15;
0~P11/12(变频主轴).
5)T功能—刀具功能
加工一个工件常常需要几把不同的刀具,本系统可控4~8工位电机刀架(1~4号刀位信号直接输入,5~8号刀位信号采用编码信号输入)。
由于安装误差或磨损,每把刀处于切削位置时的位置均不相同。
为了编程不受上述因素的影响,设置了换刀及刀具补偿功能。
Tab
其中a表示需要的刀具号范围为0-4。
a为0时表示不换刀只进行刀具补偿。
1-4对应四工位电动刀架上的四把刀。
(使用六或八工位刀架时为1—6或1—8号刀);
b表示刀具补偿的数据的编号。
1-8对应刀偏参数中的8组刀偏的组号。
(9号刀偏表示X、Z轴回机械原点后的坐标值)。
本系统最多可选择八把刀,八组刀偏值。
在一般情况下刀偏号只能用于与该偏量号相同的刀号即T11、T22、T33、T44、T55、T66、T77、T88以保证换刀偏置的正确。
而在某些特殊情况下,可以使用与刀具号不相同的刀偏号,如进行特殊的补偿或仅对某一把刀进行微调等。
在定点对刀时,刀偏号小于等于刀位总数的刀偏数据可以由对刀操作自动产生,而其它的刀偏数据由只能键盘输入而不能自动生成(因为没有刀具号)。
使用试切对刀由于可以输入刀补号所以不受刀号限制。
在T指令中如b=0则表示撤消刀偏补偿。
在有刀具偏置情况下,回程序起点或执行G26、G27、G29指令时均撤消刀具偏置。
在使用排刀时,参数P11的TCOD位设置成1,此时按换刀键时无刀具正反转信号输出而直接将刀号设置成新的刀号可按试切对刀或定点对刀方式对刀,从而自动生成刀具偏置.
6)F功能—进给速度功能
F****;
或F**.**
决定刀具切削进给速度的功能。
即进给速度功能。
进给速度功能在每分进给(G98)时,用F****来表示。
范围为0-9999单位:
mm/min;
进给速度功能在每转进给(G99)时,用F**.**来表示。
范围为0.01-99.99单位:
mm/r;
F值是模态值,一旦指定如果不改变可以不重写。
上电复位时为每分进给(G98)状态.
刀具的实际移动速度受F值与进给倍率的控制.
刀具实际切削速度=F×
进给倍率(每分进给)
主轴转速×
进给倍率(每转进给)
7加工编程实例
1)零件分析
如图7-1所示基某轴类零件,图纸要求比较简单,车床加工后还要进行磨床的精加工。
主要柱面、锥面端面。
材料为45钢,毛坯为φ25mm的棒料。
图7-1
2)工件坐标系
工件坐标系原点位置如图7-1所示的A点。
3)工艺分析
(1)确定装夹方案、定位基准、编程原点、加工起点、换刀点
由于毛坯为棒料,用三爪自定心卡盘夹紧定位。
为了使加工路线清晰,加工起点和换刀点可设为同一点,放在Z向距工件前端面100mm,X向距轴心线100mm的位置。
(2)相关数据确定
螺纹编程大径为11.8mm,加工螺纹前,车削外圆到该尺寸;
查表2.27得牙深为2.27mm,进刀次数为8次,进刀量分别为0.3,0.5,0.4,0.4,0.2,0.2,0.1,0.1;
螺纹编程小径为10.02mm,取退尾长度K=1.5mm。
(3)制定加工方案及加工路线
根据工件的图纸要求,加工工艺流程为:
车端面——粗车外圆——精车外圆——车退刀槽——车螺纹——切断。
根据加工工艺选用三种刀进行加工:
车外圆及端面选用90°
车刀,刀号为1号,刀补为1号;
车螺纹选用螺纹车刀,刀号为2号,刀补为2号;
切断选用切断刀,刀号为3号,刀补为3号。
简化的加工工序卡。
加工内容
刀号
刀补号
刀具名称
主轴转速挡位
主轴转速/r/min
进给速度/mm/min
车外圆及端面
1
90度车刀
S4
750
120
车退刀槽
3
切断刀
40
车螺纹
2
螺纹刀
——
切断
4)程序编制
根据所建立的工件坐标系和加工流程,编制数控程序,具体如表xx所示。
表7-2实例加工参考程序
程序号
程序
备注
%25
程序文件名
N0000
G0X100Z100
快速定位于工件坐标系X100,Z100处
N0010
T11
换1号刀,执行1号刀补
N0020
M03S04
开主轴,置4挡主轴转速
N0030
G00X26Z0
刀具靠近工件
N0040
G01X0F80
切端面,速度为80mm/min
N0050
G00X24.5Z1
刀具离开工件端面
N0060
Z-37F120
粗车外圆,速度为120mm/min
N0070
G00X26Z1
刀具离开工件
N0080
X20.5
N0090
G01Z-19
粗车外圆
N0100
G01X24.5Z-29
粗车锥面
N0110
X22Z1
N0120
X16.5
N0130
N0140
X24.5Z-29
N0150
N0160
X12.5
N0170
N0180
G00X13Z1
N0190
G01X0Z0F80
刀具定位到工件原点,速度为80mm/min
N0200
G02X10Z-5R5
精车圆弧
N0210
G01X11.8
N0220
Z-19
精车外圆
N0230
X16
刀具定位
N0240
X24Z-29
精车锥面
N0250
Z-37
N0260
G00X100Z100
返回换刀点
N0270
T33
换3号刀,执行3号刀补
N0280
G00X17Z-16
N0290
G01X9F40
车退刀槽,速度为40mm/min
N0300
G00X100
N0310
Z100
N0320
T22
换2号刀,执行2号刀补
N0330
G00X13Z2
N0340
Z-3
刀具靠近工件
N0350
G92X11.5Z-16.5P1.5K1.5
加工螺纹,退尾长度为1.5mm,进刀0.5mm,
N0360
X11
进刀0.5mm,切第2刀螺纹
N0370
X10.6
进刀0.4mm,切第3刀螺纹
N0380
X10.2
进刀0.4mm,切第4刀螺纹
N0390
X10
进刀0.2mm,切第5刀螺纹
N0400
X9.8
进刀0.2mm,切第6刀螺纹
N0410
X9.7
进刀0.1mm,切第7刀螺纹
N0420
进刀0mm,切第8刀螺纹
N0430
N0440
N0450
G00X26Z-37
定位到切断点
N0460
G01X0F40
N0470
G00X100
N0480
Z100
N0490
M05
停主轴
N0500
M02
程序结束
5)加工准备及加工
使用数控机床加工的流程如下:
(1)开机
数控系统开机,操作如下:
、首先合上机床总电源开关。
、按下数控系统电源开关接通电源,数控系统显示初始画面如图1在显示过程中,按住
键以外的任意键,将显示本系统使用的软件版本号,松开按键,系统进入当前正常工作方式。
(2)返回参考点操作
正常开机,机床返回参考点要通过手动操作(JOG)方式,分别按下方向键中X轴负方向键和Z轴负方向键,使刀具回到换刀位置附近。
(3)车床手动操作
通过数控车床面板的手动操作,可以完成主轴旋转、进给运动、刀架转位、冷却液开关等动作,检查基础机床状态,保证机床正常工作。
(4)输入工件加工程序
选择编缉方式进入加工程序编缉画面,按照系统要求完成加工程序的输入,并检查输入无误。
(5)刀具和工件装夹
根据加工要求,合理选择加工刀具。
刀具安装时,要注意刀具伸出刀架的长度。
合理选择工装夹具,完成工件的装夹,并用百分表等进行找正。
(6)程序校验
程序校验的方法常用有机床锁紧和机床空运行两种。
GSK928TC提供了空运行此种校验方法:
自动工作模式中选择空运行方式,程序运行时,机床坐标轴不移动,S,M,T功能无输出,从而达到检验程序的目的。
(7)工件加工
首先加工完成后,测量各加工部位的尺寸,修改各刀具的刀补值及完善程序,然后加工第二件,确认无误后恢复快速倍率100%,加工全部零件。
(8)零件尺寸检测
首先设置好程序参考点,在手动方式下执行程序回参考点操作。
如果为工件首次试加工,先在空运行模式下,进行机床的空运行,若准确无误,便可进行零件的实际切削加工,加工完成后,检测零件是否各个符合图纸要求,否则对加工工艺方案进行分析,提出解决方案,进行试加工,直到加工出符合图纸要求的零件。
8体会总结