炉区控制功能规格书Word文件下载.docx
《炉区控制功能规格书Word文件下载.docx》由会员分享,可在线阅读,更多相关《炉区控制功能规格书Word文件下载.docx(18页珍藏版)》请在冰豆网上搜索。
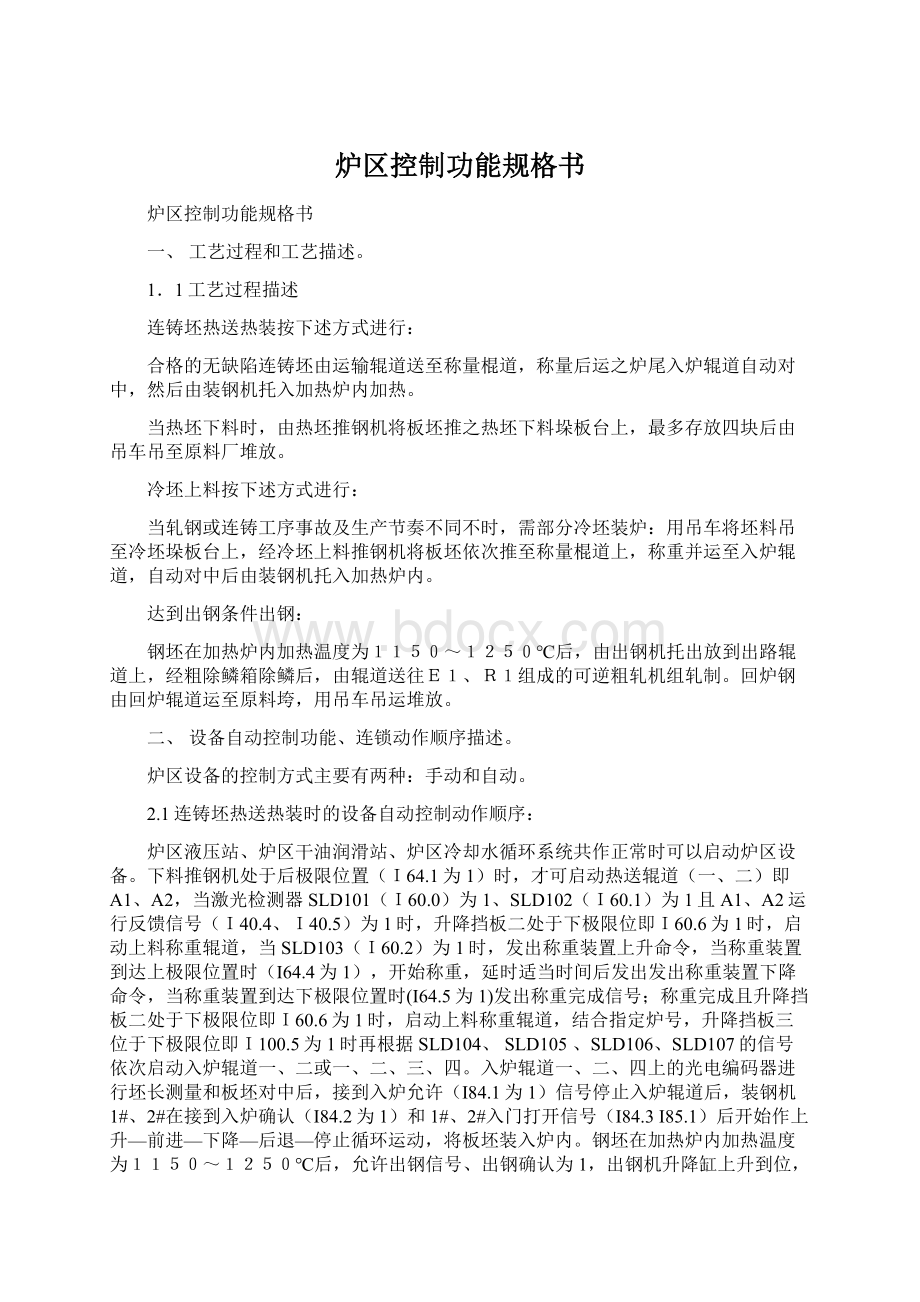
炉尾上料区
1.1热送衔接辊道(A1;
1、A2;
2)
1.1.1用途:
接受来自连铸出坯辊道的热板坯。
1.1.2技术规范:
来料规格:
断面:
160×
750~1400mm。
定尺长度:
12000mm,
最短尺7200mm(少量)。
最大坯重:
21000kg。
实心辊辊径:
Φ400mm。
辊身长度:
1550mm。
辊距:
1000mm。
辊数:
15个。
电机功率:
11.2KW
传动方式:
交流调速电机单独传动。
辊子线速度:
~0.4~0.85m/s。
辊面标高:
+800mm。
1.1.3结构特点:
采用交流调速电机单独传动,辊道架为焊接结构,双止口定位。
实心锻钢辊子,辊子两端用双列调心滚子轴承。
辊子轴承干油集中润滑。
辊道轴承通水冷却,水质为净环水,辊道设边板和托板。
1.1.4控制连锁要求:
手动和自动控制,1CS操作。
手动:
人工起停辊道。
自动:
根据检测到的板坯信号自动起停辊道。
工作时正转,事故及检修时可反转。
工作制度:
起停工作制。
1.2下料推钢机(TG1;
3)
1.2.1用途:
将板坯推至下料垛板台上。
1.2.2技术规范:
推钢尺寸:
12000mm,最短尺7200mm(少量)。
最大坯重:
板坯温度:
900℃(max)。
传动型式:
液压。
推力:
180kN。
推钢速度:
100/200mm/s
推钢时100mm/s
返回时200mm/s。
工作行程:
~2300mm。
最大行程:
~2800mm,考虑辊道电机检修方便。
1.2.3结构特点:
热坯下料推钢机是将辊道上的板坯一块一块地推到热坯垛板台上。
该设备由1个推板、1个推进液压缸、2个导向杆、4套托辊压辊装置及2个机架组成。
在推板前端,铰接有数个推爪,推爪上设有挡块,推钢时,推爪经挡块抵在推板上。
返回时,推爪可自由摆动。
推钢机推钢速度及返回速度及行程由一套光电编码器和PLC进行控制,并装有2个行程开关,用来控制其最大及最小行程。
1.2.4控制连锁要求:
手动:
人工操作推钢机前进与后退。
根据检测到的板坯信号,自动起动推钢机将板坯推至下料垛板上,并自动返回,等待下一块板坯。
推头下端面要略高于辊道上表面。
要求推头端面与辊道的中心线平行。
要求推钢平稳,并在工作行程中任一点可以停止和起动。
下料推钢机设行程保护,即当到达前极限位置自动停止并返回;
当到达后极限位置自动停止。
下料推钢机推头位置及标高应与热送衔接辊道适配。
1.3下料垛板台(DB1;
4)
1.3.1用途:
存放热板坯,存放最多四块后由吊车夹送至原料堆场堆放。
1.3.2技术规范:
板坯尺寸:
12000mm
液压升降。
最大堆放数量:
四块。
最大堆放重量:
84t。
台面尺寸:
长度×
宽度=12000mm×
~1600mm。
台面最高处时的标高:
+790mm。
要求在下料垛板台边部考虑挡钢装置(承受推力180kN),并考虑吊车夹具的夹运空间。
1.3.3结构特点:
热坯下料垛板台架体为铸钢结构。
采用2个液压缸来举升台架。
同时设置4根垂直的导向立柱进行导向。
升降行程用一套直线位移传感器进行控制。
1.3.4控制连锁要求:
人工操作下料垛板台的升降。
根据检测到的板坯信号和下料推钢机返回到位信号,自动升降。
要求下料垛板台升降平稳。
要求考虑板坯在下料垛板台与热送衔接辊道之间的支撑问题。
1.4升降挡板
(一)(SB1;
5)
1.4.1用途:
挡停连铸热板坯,并用下料推钢机将其推至下料垛板台上。
1.4.2技术规范:
板坯运行速度:
0.85m/s(max)。
输送辊道标高:
+800mm。
输送辊道辊身长度:
挡板面与热送衔接辊道最后一个辊子中心间距:
500mm。
1.4.3结构特点:
升降挡板由挡板、弹簧及固定底座组成,当钢板撞到挡板后,缓冲弹簧受压缩退后直至板坯停止运动。
具有一定强度和刚度,能承受运动钢坯的冲击。
1.4.4控制连锁要求:
气动。
手动控制,1CS操作。
升降挡板
(一)上升到位后,下料推钢机方可动作。
1.5称量辊道(A3;
6)
1.5.1用途:
接受来自连铸的热板坯或上料垛板台的板坯并向炉尾方向输送;
板坯在此辊道上由板坯称重装置称量。
1.5.2技术规范:
辊身长度:
辊距:
13个。
11.2KW
~0.4~0.85m/s。
辊道传动侧设置挡钢装置(承受推力180kN),以免误操作将板坯推出辊道外。
1.5.3结构特点:
同1.4.3热送衔接辊道
1.5.4控制连锁要求:
自动:
称量辊道可单动,1CS操作;
可与入炉辊道
(一)、
(二)联动,也可与入炉辊道
(一)~(三)联动,2CS操作。
1.6板坯称重装置(W1;
7)
1.6.1用途:
对连铸板坯称重并计量。
1.6.2技术规范:
型式:
升降式电子秤。
升降高度:
~100mm。
升降速度:
~0.05m/s。
最大称重量:
称重精度:
2.0‰。
1.6.3结构特点:
称量装置由电子钢材秤,称量台架及液压升降机构及限位装置组成。
台架及升降机构为焊接结构由螺栓联接成一体,再固定在电子钢材秤盘上,电子钢材秤由地脚螺栓固定在地基上,升降机构由升降液压缸及台架组成,升降行程由装在其上的两个接近开关来分别控制其上升极限与下降极限位置并发出信号,该升降液压缸由液压站来供给油源,台架平时处于下极限点,即低于辊道面,不影响辊道上板坯的运行,测量时由升降液压缸将台架升起同时将板坯托起离开辊面一定高度后再进行测量,测量应在静态下进行。
1.6.4控制连锁要求:
人工控制板坯称重装置的升起、称重和下降。
根据检测到的板坯信号,自动完成升起、称重和下降全过程。
能进行单根重量计量,也能进行累计计量。
板坯数据可在1CS上显示和打印,显示和打印内容:
日期、钢种、炉号、规格、单根重量、累计重量等等。
板坯称重装置原始位置应略低于称量辊道上表面。
1.7上料垛板台(DB2;
8)
1.7.1用途:
存放冷、热板坯。
1.7.2技术规范:
台面最高处时标高:
+810mm。
要求考虑吊车夹具的夹运空间。
1.7.3结构特点:
热坯下料垛板台架体为铸钢结构。
1.7.4控制连锁要求:
人工操作上料垛板台的升降。
根据检测到的板坯信号,自动升降垛板台。
要求上料垛板台升降平稳。
要求考虑板坯在上料垛板台与称量辊道之间的支撑问题。
1.8上料推钢机(TG2;
9)
1.8.1用途:
将冷、热板坯推至称量辊道上。
1.8.2技术规范:
定尺长度:
12000mm,最短尺7200mm(少量)。
最大坯重:
100/200mm/s。
推钢时100mm/s。
~2800mm,考虑上料垛板台检修方便。
1.8.3结构特点:
同1.2.3下料推钢机
1.8.4控制连锁要求:
根据检测到的板坯信号,自动起动推钢机将板坯推至称量辊道上,并自动返回。
推头下端面要略高于上料垛板台上表面(上料垛板台台面在最高处时)。
1.9升降挡板
(二)(SB2;
10)
1.9.1用途:
挡停板坯。
1.9.2技术规范:
同1.4.2升降挡板
(一)。
1.9.3结构特点:
同1.4.3升降挡板
(一)
1.9.4控制连锁要求:
挡板面与称量辊道最后一个辊子中心间距:
升降挡板
(二)从上升位置下降到位后,称量辊道方可运行。
加热炉区
1.10入炉辊道
(一)(B1;
11)
1.10.1用途:
向入炉辊道
(二)方向运输板坯。
1.10.2技术规范:
来料规格:
10个。
11.2kW
1.10.3结构特点:
同1.1.3热送衔接辊道
1.10.4控制连锁要求:
手动和自动控制,2CS操作。
入炉辊道
(一)可单动;
可与称量辊道及入炉辊道
(二)联动;
也可与称量辊道及入炉辊道
(二)~(三)联动。
1.11入炉辊道
(二)(B2;
12)
1.11.1用途:
接受来自入炉辊道
(一)的板坯并自动对中。
1.11.2技术规范:
定尺长度:
Φ350mm。
12个。
11.2kW
1.11.3结构特点:
同1.1.3热送衔接辊道
1.11.4控制连锁要求:
手动或自动控制,2CS操作。
根据检测到板坯信号,起动或停止辊道运行。
正反转,频繁起制动;
可点动;
小时接电次数:
~600次。
入炉辊道
(二)可单动;
可与称量辊道及入炉辊道
(一)联动;
也可与称量辊道及入炉辊道
(一)、(三)联动。
传动电机要求耐高温。
1.13入炉辊道(三)(B3;
15)
1.13.1用途:
运输板坯。
1.13.2技术规范:
~0.4-0.85m/s。
1.13.3结构特点:
1.13.4控制连锁要求:
入炉辊道(三)可单动;
可与称量辊道及入炉辊道
(一)、
(二)联动。
入炉辊道(三)运行时,推钢机不得动作(含前进和后退);
反之亦然。
1.15装钢机(ZG1;
13/ZG2;
17)
1.15.1用途:
将准备加热板坯由入炉辊道装入加热炉步进梁上。
1.15.2技术规范:
行走电动齿条式,液压升降
移送速度:
500/1000mm/s
5900mm(最大)
维修返回行程:
1000mm
电机功率:
75kW
1.15.3结构特点:
装钢机由升降机构、托钢杆、压辊装置、移入机构等组成,通过液压实现升降。
移入机构为齿轮齿条结构,由电机通过减速机,齿轮齿条实现移入。
移入电机为调速电机,空载出炉时用高速,装钢时用低速,水平移动行程可根据板宽进行设定和调整,当托钢杆退回到炉外辊道下接近终点时,由一个接近开关发出减速信号减速,低速前进。
其余两个接近开关分别控制极限位置。
1.16升降挡板(三)(SB3;
14)
1.16.1用途:
1.16.2技术规范:
1.16.3结构特点:
1.16.4控制连锁要求:
1.17出炉辊道一、二、三(C5;
25、C4;
23、C3;
22)
1.17.1用途:
接受并输送出炉板坯。
1.17.2技术规范:
见平面布置图。
14个。
15kW
交流电机单独传动。
~1.5m/s。
1.17.3结构特点:
1.17.4控制连锁要求:
手动或自动控制,3CS操作。
由热金属器检测到板坯发出起制动信号,起动或停止辊道运行。
正反转:
可单动,也可与回炉辊道
(一)、
(二)及粗轧除鳞辊道联动,3CS操作。
并要求与辊子用较长的万向轴联接,远离炉门。
出炉辊道与出钢机互为联锁。
1.18回炉辊道
(一)(C2;
27)
1.18.1用途:
将回炉钢坯送回原料跨。
1.18.2技术规范:
板柸温度:
1200℃(max)。
1000mm。
11.2kW
~0.8m/s。
1.18.3结构特点:
1.18.4控制连锁要求
手动控制,3CS操作。
工作时正转(向固定挡板方向),事故及检修时可反转。
1.19回炉辊道
(二)(C1;
26)
1.19.1用途:
将回炉钢送回原料跨。
1.19.2技术规范:
同1.18.2回炉辊道
(一)
1.19.3结构特点:
1.19.4控制连锁要求
可单动,也可与回炉辊道
(一)联动。
其它同回炉辊道
(一)。
在固定挡板
(二)前设一热金属检测器,当检测到板坯后辊道自动停止运行。
1.20固定挡板
(二)
1.20.1用途:
1.20.2技术规范:
同1.16.2固定挡板
(一)
1.20.3结构特点:
同1.16.3固定挡板
(一)
1.21出钢机(CG1;
21/CG2;
24)
1.21.1用途:
将已加热好的钢坯自加热炉中托出放于出炉辊道上。
1.21.2技术规范:
行走电动、升降液压;
出料杆速度:
~500/1000mm/s(进退);
0.1m/s(升降);
最大工作行程:
5000mm
移动电机交流调速电机N=75KW
1.21.3结构特点:
出钢机由升降机构、托钢杆、压辊装置、移出机构等组成,通过液压实现升降。
移出机构为齿轮齿条结构,由电机通过减速机,齿轮齿条实现移出。
移出电机为调速电机,空载入炉时用高速,出钢时用低速,水平移动行程可根据板宽进行设定和调整,当托钢杆前进到炉内前面时一个接近开关发出减速信号减速,低速前进。
四.模拟轧钢原理和具体实现方法
在实际轧制中,HMD和LR的ON/OFF变状态主要视轧件的到达和离去的时序而定。
但对于模拟轧钢时,无轧件在轧线上运动,亦要产生HMD和LR的ON/OFF变状态,这就是模拟轧钢时的计算机依据时序通过硬件接口的作用。
首先按实际轧制时的工艺情况和具体的轧制方案,依据模型计算出轧线上各HMD和LR的状态时序,由计算机输出接口将此状态以时序发出去控制实际的HMD和LR二次检测器,再由输入接口采入各检测器状态,则跟踪程序就可像真实轧制时一样正常运行,调度作用同时产生了。
关于实际检测器与计算机硬件接线如图2.5-1所示。
输入
计算机
HMDLR
二次检测
OR
一次检测
计算机输出I/O
轧件
图2.5-1模拟时检测器状态输出示意图
各检测器的模拟状态和时序是按模轧方案事先制定的。
制定模轧方案考虑到了实际生产过程中常生产的产品结构和规格,以及少数特殊生产工艺情况(例如空过机架等)。
模轧程序设置快慢两种形式的模拟。
慢速模轧用于发掘程序和设备故障时使用,快速模轧是模