机械制造课程设计方案液压泵箱体说明书Word下载.docx
《机械制造课程设计方案液压泵箱体说明书Word下载.docx》由会员分享,可在线阅读,更多相关《机械制造课程设计方案液压泵箱体说明书Word下载.docx(20页珍藏版)》请在冰豆网上搜索。
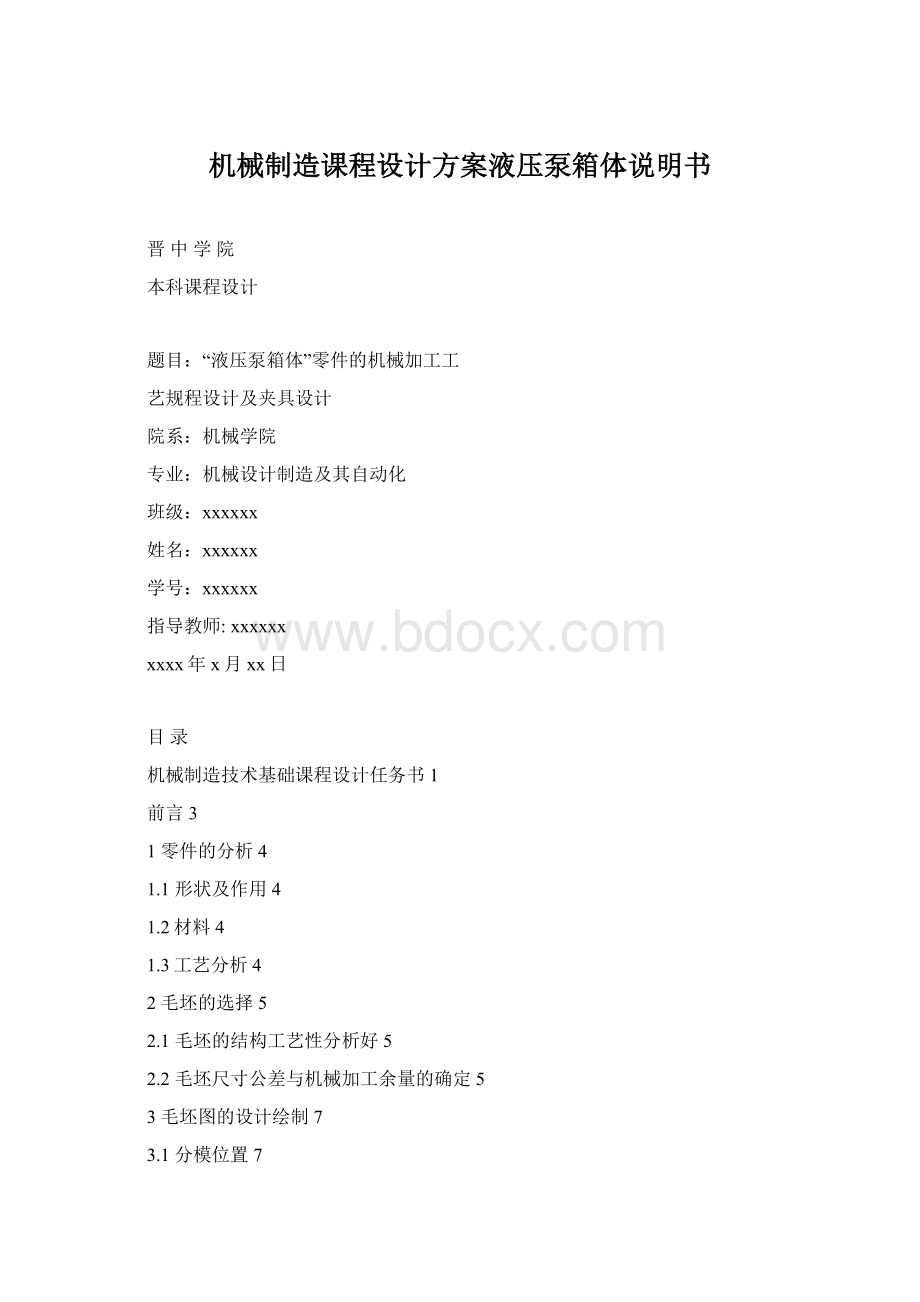
手绘、CAD<
或Solidworks\Pro-E)绘制各1份<
含相应格式电子文件);
2、毛坯图1张;
3、机械加工工艺过程综合卡片1张;
4、机械加工工艺工序卡片2张<
2个典型工序);
5、工艺装备<
夹具)设计装配图1张;
6、课程设计说明书1份<
6000字以上)。
三、设计目的
1、能熟练运用机械制造技术基础、公差与测量技术、工程力学、机械设计基础、机械制图等课程中的基本知识与理论以及在生产实习中学到的实践知识,正确地解决一个零件在加工中的定位、夹紧以及工艺路线安排、工艺尺寸确定等问题,保证零件的加工质量;
熟悉该零件在机器中的工作原理;
2、学会使用手册及图表资料;
3、进一步培养识图、绘图、工艺运算和编写技术文件等基本技能。
四、资料查阅与收集任务:
1、查阅和收集所给题目零件的零件图、该零件在产品或部件中的作用、材料及热处理特点、机械加工工艺性、主要加工表面的技术要求等;
2、查阅和收集对应的毛坯图、了解毛坯的制造过程和要求等;
3、查阅和收集该零件加工工艺规程编制的要求和主要注意点;
4、查阅和收集各工序所采用工、夹、量、刃具、设备;
相应的切削加工用量等;
5、查阅和收集相关加工方法的总余量、工序加工余量、工序尺寸及公差等;
6、其他你认为应收集的相关资料。
前言
这次课程设计的是液压泵箱体。
包括零件图、毛坯图、装配图各一张,机械加工工艺过程卡片一张与工序卡片两张。
根据零件的性质和零件图上各端面的粗糙度确定毛坯的尺寸和机械加工余量。
最后拟定输出轴的工艺路线图,制定该工件的夹紧方案,画出夹具装配图。
机械制造工艺学课程设计是我们学完了大学的全部基础课、技术基础课以及大部分专业课之后进行的.这是我们在进行毕业设计之前对所学各课程的一次深入的综合性的总复习,也是一次理论联系实际的训练,因此,它在我们大学生活中占有重要的地位。
机械制造技术基础课程设计是在全部学完机械制造工艺学及机床夹具设计课程,并进行了生产实习的基础上进行的一个教案环节。
这是我们在进行毕业设计之前对所学课程的一次深入的全面的总复习,也是一次理论联系实际的训练。
就我个人而言,希望通过这次课程设计,对自己今后将从事的工作,进行一次适应性训练,通过设计锻炼自己分析问题、解决问题的能力,为以后的工作打下一个良好的基础,通过这次课程设计对自己未来将从事的工作进行一次实际的训练,从中锻炼自己分析问题、解决问题的能力。
由于能力所限,设计尚有许多不足之处,恳请各位老师给予指导。
此次课程设计的主要意义有:
一.进一步熟悉所学课程,并应用到实践,再从实践中反过来加强对所学知识的熟悉程度。
二.增强知识的综合运用的能力。
此次课程设计,不但设计到《机械制造技术基础》这一门课程,更是对《机械精度设计与检测》、《机械图学》与《机械设计》等课程的一次全面复习,与综合运用能力的锻炼。
三.增强自主解决问题的能力与设计能力。
1零件的分析
1.1形状及作用
课题是小型液压泵的箱体,用于为齿轮液压计、密封装置、端盖、紧定螺栓等元件做承载件,箱体整体外形为长方体。
1.2材料
因零件为箱体类,对于材料无特殊的性能要求,故毛坯选择较为经济的HT200金属型铸造成型即可。
1.3工艺分析
通过对该零件图的重新绘制,知图样的剖切线有误,起改正后的剖切位置已在图纸中体现.
<
1)该零件属于箱体类零件,它的六个表面均有凸台,故该零件的加工面有:
A——底面三个凸台(其中两凸台沿长度方向对称分布相距56mm与另一凸台左右对称相距92mm,凸台高度3mm、其上为M8深12mm的螺纹孔).
B——上表面4个用于安装端盖的螺纹孔(M6>
;
高度为3mm的凸台(其上表面粗糙度为3.2,由Ф26的圆组成的“8”形孔的内表面的粗糙度为6.3;
用于安装密封圈的剖面为半圆(R1.5>
的密封槽及槽内四个Ф3的小孔。
C——左侧面凸台(台高为3mm,凸台上表面粗糙度为6.3>
及凸台上螺纹孔(M27×
1.5,其垂直基准为零件底面,前后基准为零件前后对称中心线>
。
D——右侧面凸台(台高3mm>
及凸台上螺纹孔(M8>
E——前后四个凸台的上表面(台高3mm,粗糙度为3.2m>
及其上螺纹孔(M36×
1.5两轴线平行度为0.06mm>
F——腔体内两轴座的上表面(粗糙度为3.2,其垂直基准为箱体上表面>
孔(2×
Ф10H8,两孔轴线平行度为0.025mm。
轴座上两侧孔(Ф5,粗糙度为12.5>
(2>
根据零件加工表面形位公差等得出该零件的主要加工面为前后四螺纹孔,腔内两轴座孔。
(3>
最终加工方法的确定
A——6个表面的凸台用铣削作为最终加工方法。
B——各个螺纹孔用机用丝锥作为最终加工方法。
C——上表面无螺纹小孔用台钻加工作为最终加工方法,大孔用铣削作为最终加工方法。
D——轴座上表面用铣削作为最终加工方法。
轴座孔用绞削作为最终加工方法。
E——轴座上斜孔用台钻钻削最为最终加工方法。
(4>
夹具的选用
A——底面及四个侧面及其上的孔及螺纹用平口虎钳装夹。
B——加工上表面凸台,回油槽,“8”形孔,内腔上台、孔,四个M6,四个Ф3的孔用设计的专用夹具装夹。
2毛坯的选择
由于所设计零件属于中等规模生产的零件,结构不太复杂,其对生产率没有较高的要求,故选用砂型铸造。
2.1毛坯的结构工艺性分析好
对照零件图分析零件结构可得出箱体前后四孔,上面“8”形孔和前后面上的M36×
1.5可以铸出,其他孔系需通过加工加工出。
2.2毛坯尺寸公差与机械加工余量的确定
(1>
求最大轮廓尺寸
由长134mm,宽86mm,高74mm可得最大轮廓尺寸为134mm
选取公差等级CT
铸造方法为金属型铸造,铸件材料为灰铸铁,得公差等级CT范围为8~10,取为10级。
⑶求铸件尺寸公差
根据加工面的基本尺寸和铸件公差等级,由表2.8查得,公差带相对于基本尺寸对称分布。
⑷求机械加工余量等级
由表2.8,铸造方法按金属型铸造,铸件材料按灰铸铁得机械加工余量等级取为G级。
(5>
求毛坯基本尺寸
对所有加工面取同一个数值,由表2.10查得
A、两侧面属双侧加工,加工余量为5,即毛坯尺寸为134+=140,查表2.7得尺寸公差为3.6mm,该尺寸及公差为<
140±
1.8)mm。
B、前后两面双侧加工,加工余量为5,即毛坯尺寸为86+5=91,查表2.7得尺寸公差为3.2mm,该尺寸及公差为<
91±
1.6)mm。
C、上下两面属双侧加工,加工余量为5,即毛坯尺寸为74+5=79,查表2.7得尺寸公差为3.2mm,该尺寸及公差为<
79±
D、轴承座平面为单侧加工,即毛坯尺寸为22+3.5=25.5≈26,查表2.7得尺寸公差为2.6mm,该尺寸及公差为<
26±
1.3)mm。
E、“8”形孔双侧加工,加工余量等级会下降为H,加工余量一半为3,所以其毛坯尺寸为Φ52-2×
3=Φ46,查表2.7得尺寸公差为2.8,该尺寸及公差为<
Φ46±
1.4)mm。
F、前后面四个孔双层加工,加工余量等级会下降为H,加工余量一半为3,所以其毛坯尺寸为Φ36-2×
3=Φ30,查表2.7得尺寸公差为2.6,该尺寸及公差为<
Φ30±
综合考虑经济性等得出毛坯尺寸公差与加工余量列表:
工程
前后面
两侧面
上下两面
轴座面
“8”形孔
前后面孔
公差等级
8
加工面基本尺寸
86
134
74
22
Φ52
M36×
1.5
加工余量
2.5
3.0
3.5
3
机械加工余量
G
H
毛坯基本尺寸
1.6
1.8
1.3
1.4
3毛坯图的设计绘制
3.1分模位置
箱体类铸件,应采取上下分模,这样便于起模及到较高的铸造精度
3.2确定毛坯热处理方式
箱体毛坯经铸造成型,用退火以消除其金相组织的不均匀,通过重结晶而得到细化、均匀的组织,从而改善加工性。
3.3绘制毛坯图
毛坯图见所绘图纸。
4工艺路线的拟定
拟定零件加工工艺路线是零件加工的总体方案设计,是制订工艺规划中的关键性工作,主要内容是选择定位基准,选择各表面加工方法,安排加工顺序和组合工序,以及选择各工序所用的机床和工艺装备等,对比较复杂的零件,应多设想几种工艺方案,进行分析比较后,从中选择一个比较经济合理的加工方案。
4.1定位基准的选择
⑴粗基准的选择
选择粗基准时应保证各重要支承孔的加工余量均匀,保证装入箱体的零件与箱体壁有一定的间隙。
为了满足上述要求,应选择箱体的主要加工面为主要基准,即以箱体的下表面为主要粗基准,下表面为辅助定位粗基准。
⑵精基准的选择
从保证箱体孔与孔、孔与平面、平面与平面三者间的位置出发,精基准的选择应能保证箱体在整个加工过程中都能用统一的基准定位,分析零件图得知,选择底平面为主要精基准面,相应侧面为辅助精基准。
4.2加工路线计划
⑴铸造毛坯
根据零件图所给技术要求可知该毛坯采用HT200,由于具有较大的生产类型,且外形不是过于复杂,故选用砂型铸造作为其成型方式,并采用上下分型。
⑵热处理
由于箱体是通过铸造成型,会产生金相组织的不均匀,故在机加工前用退火作为预备热处理,通过重结晶而使组织得到细化、均匀,从而改善可加工性。
⑶检验
由于零件在机加工前需要进行其内部质量的检验。
考虑成本及经济性后选择X射线检验。
⑷铣平面
运用万能卧式铣床铣削箱体左右前后底五个平面。
⑸检验
用游标卡尺对加工后的各平面进行检测。
<
6)镗孔
用金刚镗加工前后四个凸台上的螺纹孔,以保证其所要的平行度及尺寸精度。
7)用卡尺和百分表对零件进行检验。
8)加工中心
在加工中心上对上表面、“8”形孔、腔内轴座、上表面8个小孔进行加工。
9)检验
用卡尺、千分尺等工具对上序加工后零件进行检验。
⑽钳工工作台加工
在钳工工作台上对零件侧面两孔底面三孔进行加工达到设计要求。
⑾最终检验
对零件做最终检验。
4.3工艺路线的安排
工序1用夹具夹持工件,粗铣前后左右底5个平面,其中左右面加工到设计尺寸,前后底三面各留精加工余量1mm。
工序2 在金刚镗上铣前后两面到设计尺寸
镗前后四个螺纹孔
用机锥四个螺纹孔。
工序3在加工中心上用立铣刀铣上表面到设计尺寸,用专用夹具装夹。
用立铣刀铣“8”形孔,达到设计要求。
用成型铣刀铣“8”形密封槽。
用立铣刀铣轴座平面,达到设计要求
用Ф9的钻头钻两轴座孔。
换Ф10的绞刀绞两轴承座孔。
换Ф3钻头钻四个回油孔。
换Ф5钻头钻四个顶盖螺纹孔。
工序4用φ25的钻头在台钻上钻左侧孔
用Ф6.7的钻头钻右侧孔,底面三孔。
工序5用Ф5的钻头钻轴座斜孔
用M8机锥锥右侧、底面四个螺纹孔
用M27机锥锥左侧螺纹孔。
5工序设计和工艺计算
5.1选择机床及工艺装备
⑴选择机床
工序1是粗铣,外轮廓尺寸不大,精度要求不是很高,选用X6132(卧式万能铣>
工序2用金刚镗床加工孔及平面。
工序3加工中心加工,因在普通机床上效率过底且质量不高,故在加工中心上加工。
工序4工作为钻孔,故选用Z3050。
⑵选择夹具
本零件除在加底面三螺纹孔时使用设计的专用夹具外,其他各工序使用通用即可,所用到的通用夹具有平口虎钳和台虎钳。
⑶选择刀具
工序1粗铣平面,所加工面为小平面且材质为HT200,故选用D=80mm的镶齿套式面铣刀,YG8硬质合金面铣刀,齿数为10。
工序2在金刚镗床上镗M36螺纹孔,<
用镗刀镗至Ф34.5+0.3+0.2)
工序3①用D=5mm半圆形成型铣刀加工回油槽到设计尺寸。
②用D=20mm高速钢立铣刀铣上表面到设计尺寸
③铣轴座上表面。
④用Ф9的莫式锥柄麻花钻钻轴座孔。
⑤用Ф10机用绞刀绞轴座孔。
到加工尺寸。
工序4①用到Ф25莫式锥柄麻花钻。
②用到Ф6.7莫式锥柄
选择量具
本零件属于批量生产,一般情况下尽量采用通用量具。
根据零件表面的精度要求,尺寸和形状特色。
参考有关资料,选择如下。
工序1
选用可读尺寸为0.02mm,测量最大量程0-150mm的游标卡尺。
工序2
选用读数为0.01mm,最大量程为150mm的游标卡尺,百分表。
工序3
选用最小尺寸为0.01mm,测量最大量程0-150mm深度游标卡尺,百分表。
和读数值为0.01mm,最大量程为50mm的游标卡尺。
5.2确定工序尺寸及公差
综合考虑整个加工路线得:
零件的整个加工过程。
1)平面工序尺寸
1
工序内容
基本尺寸
经济精度
工序尺寸偏差
min
max
粗铣后面
91
10
+0.07
-0.07
0.93
1.07
粗铣前面
89.5
粗铣右面
140
+0.08
-0.08
1.92
2.08
粗铣左面
138.5
粗铣底面
79
1.93
2.07
2
粗铣上表面
77.5
-0.06
+0.06
1.94
2.06
粗铣轴座上表面
26
精铣前面
88
精铣后面
87
2)圆柱表面工序尺寸
前面根据材料已初步确定工件各面的加工余量,现在确定个表面的各个加工工序的加工余量
加工表面
加工内容
精度等级
工序尺寸
表面粗
糙度
工序余量
4×
Ф3
钻
IT14
12.5
M6
5
Ф5
锥丝
0.5
IT8
M8
6.7
Ф6.7
0.7
0.65
手动
2×
Ф10
Ф8
铰孔
IT9
Ф10+0.050
M27×
24
Ф24
镗孔
IT10
Ф25+0.3+0.2
6.3
25
镗螺纹
IT6
M27
粗镗
Ф32
0.95
精镗
Ф34+0.05-0.05
M36
3.2
铣孔
Ф26+0.040
1.9
2.0
6确定切削用量
切削用量指切削速度Vc,进给量f和被吃刀量ap三参数,称为切削用量三要素。
合理的切削用量是指在保证加工质量的前提下,能取得较高生产率和较低成本的切削用量。
约束切削用量的主要条件有:
工件的加工要求,包括加工质量和生产率要求;
刀具材料的求小性能;
机床性能,包括动力特性<
功率,转矩)和运动特性;
刀具寿命。
工序一
加工条件
工件材料;
HT200δb=170-240mpa,砂型铸造;
加工要求:
单侧加工余量2.5mm。
机床:
X6132。
刀具:
YG8硬质合金面铣刀,选择镶齿套式面铣刀,D=80mm,D1=70mm,d=27,L=36mm,L=30mm,齿数为10。
切削用量<
1)ap余量较小,故选用一次走刀即可完成。
2)确定每齿进给量
查表得:
fz=0.15-0.3mm/z,取0.2mm/z.
f=z*fz=10*0.2=2mm,查表得vc=64m/min.
主轴转速n=1000*64/π*80=255r/min,查表得n=255r/min.
计算得vc=255π80/1000=64m/min.
工序二
A在金刚镗上铣削前后两面到加工尺寸材料200,HBS=170-240mpa,用D=80mm,D1=70mm,d=27mm,L=36mm,L1=30mm,齿数为10的YG6硬质合金面铣刀铣面,选择镶齿式面铣刀,所用机床为金刚樘。
1>
确定切削深度ap
因余量较小,选择一次走刀完成即可。
2>
确定每齿进给量fz
Fz=0.01mm/z,f=29×
fz=10×
0.1=1mm/r
查表得vc=124mm/min,
主轴转速n=1000×
124/3.14×
80=495r/min
查表得n=500r/min。
B在金刚镗上镗M36×
1.5的螺纹孔到Ф34.5+0.3+0.2
由于余量较小采用一次走刀完成加工。
确定切削深度ap=0.75mm,f=0.1mm/r,vc=40m/min
转速n=40ⅹ1000/3.14ⅹ34=376r/min。
C在金刚镗上用丝锥加工M36ⅹ1.5的螺纹孔,n=45r/min。
工序三
A<
1)加工条件
工件材料:
HT200,δb=170-240mpa,铸造;
单侧加工余量3mm。
机床:
加工中心;
高速钢铣刀,选择镶齿套式面铣刀,D=12mm,l=38mm,L140mm,齿数六。
2)切削用量
确定切削深度ap
用于余量较小,故选用一次走刀即可完成。
确定每齿进给量fa
查表得:
fz=0.06-0.12,取0.1/z
f=z*fz=6*0.1=0.6mm,
查表得n=490r/min
计算得vc=490*3.14*80/1000=12m/min
B铣“8”形油槽
确定切削深度ap,选择其为3mm,f=0.1mm/r
查表得vc=5m/min
主轴转速n=1000*5/3.14*5=318r/min
查表得其值为300r/min。
C铣轴座上表面同A
Dap=3mm,f=0.1mmr/minvc=40m/min
主轴转速n=1000*40/3.14*9=1592r/min
查表得n=1400r/min
计算得vc=1400*3.14*9/1000=35m/min
E用Ф10绞刀铰孔<
粗铰Ф10的孔)
确定切削深度ap=0.5mmf=0.4mm/rvc=10m/min
轴转速n=1000×
10/3.14×
10=318r/min
查表得n=350r/min计算得vc=3513.14×
10/1000=11m/min.
工序四
A在台钻上用莫式锥柄麻花钻加工M27ⅹ1.5的孔加工为Ф25。
确定切削深度ap=12.5,由于采用手动进给故f选为0.2mm/r,v=17m/min,n=216r/min,根据z3050转速表选择450r/min。
B.在台钻上用麻花钻加工出M8的孔到Ф6.7确定切削深度ap=3.35mm,
查表选f=0.2mm/r,v=17m/min,n=630r/min,根据Z3050钻床转速选630r/min。
C.由于是用手用丝锥锥M8的孔,故根据生产调速即可,不作特别说明。
6.1工时定额计算
1)工时是指完成零件加工的一个工序时间定额。
Td=(Tj+Tf+Tb+Tx+Tz>
/N
其中Td是时间定额Tf辅助时间Tb是布置时间,一般取<
15-20)%Tj;
TjTf和称作业时间。
Tx是休息及生理时间,一般按作业时间的<
2-7)%估算。
Tz是准备和终结时间,大量生产时准备和终结时间忽略不计,N是一批零件的个数。
下表是各个工步基本时间的计算公式及其结果:
工序
计算公式
计算结果<
mm)
A
TJ=<
l+l1+l2)/(f×
n>
l1=0.5[d-<
d2-ae)1/2。
Kd=900。
ae铣削宽度;
铣:
d铣刀直径
0.20
B
0.18
C
D
0.07
E
0.17
0.31
2.7
0.11
TJ=(l+l1+l2>
/(f×
l1=0.5dcotkɑ+<
1~2)l。
钻:
L2:
1~4)
0.09
L1=[<
D-d)/2cotkɑ]+
绞:
1~2)
0.49
2
0.2
Tj=Li/<
f×
n)
=<
l+l1+l2)÷
fn。
l1=ap/tanKɑ+(2~3>
镗孔:
L2=(3~5)
TJ=(l×
i×
q>
÷
(f×
=(l+l1+lz)/fn。
通