国金浇注料施工文档格式.docx
《国金浇注料施工文档格式.docx》由会员分享,可在线阅读,更多相关《国金浇注料施工文档格式.docx(33页珍藏版)》请在冰豆网上搜索。
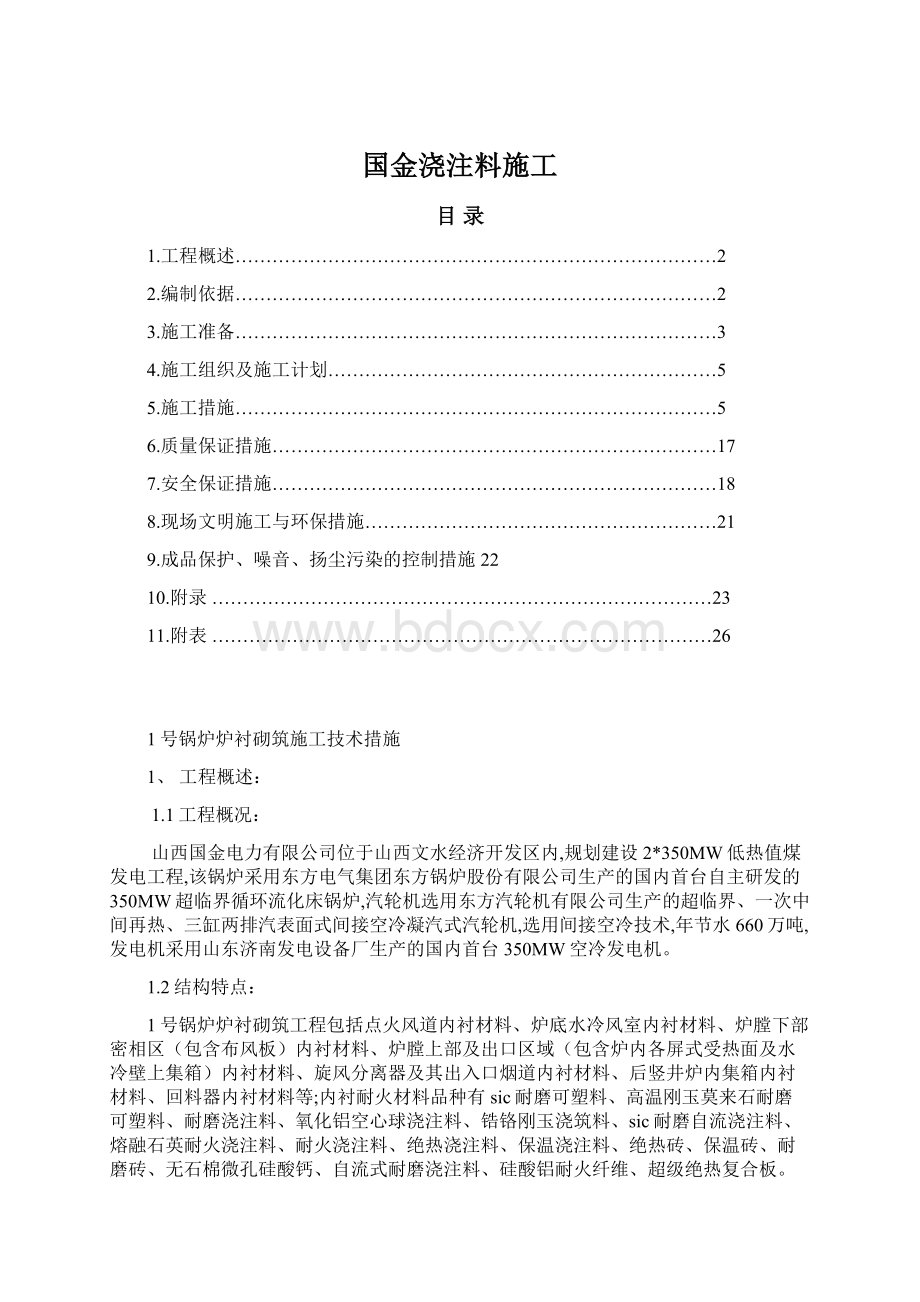
2.8电力建设安全健康与环境管理工作规范
2.9锅炉厂提供的《锅炉安装说明书》
3、施工准备:
3.1参加作业人员必须经岗位考试合格,并经体格检查合格后,方可上岗。
3.2参加作业人员必须是本岗正式上岗人员,并经安全教育,通过安规考试合格后,持正上岗。
3.3参加内衬砌筑工程的施工队伍必须具备专业施工资质证,并经有关单位审查通过后方能进厂施工,焊接人员需持证上岗。
3.4设备、管道及金属结构安装完毕,经验收合格,接受开工报告单,工序交接签证后方可进行。
3.5作业区域、场地已清除干净,保持整洁。
3.6施工机械、施工人员配备表:
运料提升机
2台
强制式砼搅拌机
6台
木工机床
木工手提电刨
4台
电焊机
5台
砼振动器
8台
手提平板振动器
16台
角向磨光机
冲击电锤
3台
手拉翻斗车
15辆
金刚片切割机
通讯对讲机
10对
管理人员
施工人员
项目经理
1人
筑炉工
15人
项目副经理
机械维护工
技术负责人
木模工
6人
质量管理员
电焊工
3人
安全管理员
电工
班长(不脱产)
2人
辅助工
20人
后勤负责人
材料员
合计
9人
55人
3.7作业人员在作业前,必须认真学习有关资料,施工中认真负责。
3.8耐火材料符合设计要求,并经检验合格后方可使用。
3.9现场作业要有电源和足够的照明。
3.10材料运送道路平整畅通,消防设施齐全。
3.11材料运送机械具备,施工升降机安装完毕。
3.12施工人员已接受《施工技术措施》技术交底,并已办理技术交底签证的手续。
3.13材料运输和存放
(1)浇注料等物品需用带有塑料防水层的纺织袋包装运输,在运输和保管中严防雨水和受潮。
(2)水泥、浇注料、硅酸铝制品,最好应存放在库内保管,要按品种、规格分别堆放,并作出标志。
(3)现场的垂直运输,可由施工电梯直接从地面运输至所需要的平台上,也可以通过平臂吊车起吊完成。
将材料运至所需要的平台上,再由人工搬运,运至施工地点。
(4)存放:
耐火材料露天堆放时,堆放四周应由不燃性材料围挡;
堆放场应为禁火区域,其周围10米范围内及上空不得有明火作业,并应显著标识;
堆放场地附近不得放置易燃、易爆等危险物品,堆放场应配备种类适宜的灭火器、砂箱或其他灭火器具,堆放场内材料的存放量不应超过5天的工程需用量,合理进行组织施工,保证保温材料的周转性。
由于现场现正值雨季,在堆放耐火材料时,下部应采用木板或者架板等于地面形成硬隔离,上部用彩条布或塑料布进行防雨遮盖,以免造成耐火材料因下雨淋湿受潮而无法使用,造成损失。
4、施工组织及施工计划
4.1锅炉内衬耐火材料施工前应具备下列条件:
4.1.1施工部位的钢结构、受热面、炉衬零件及其它装置等的组合或安装工作(包括安装焊缝的严密性检查、试验)经验收合格;
4.1.2炉衬施工部位的临时设施,应全部清除,并经检查合格。
4.2主要部位施工组织本次工程大部分都必须在框架和受热面安装结束且水压试验之后进行施工(受热面鳍片狭窄区域的保温钉需在水压试验前完成),施工预定工期大约90天。
(详见施工进度计划表)
5、施工措施:
5.1作业流程图见附图。
5.2作业程序和方法:
技术交底工作由项目负责技术员根据有关图纸、资料及施工技术措施进行交底,技术人员必须认真听讲交底内容,并进行讨论,无疑问后及时办理技术交底签证手续。
5.3内衬耐火材料施工:
设备、管道及仪表测量元件等安装完毕,经验收合格后,施工人员必须对设备、管道表面进行系统检查,将被炉衬面上的灰尘、污垢、铁锈等杂物清理干净,保证下一道工序顺利进行。
炉衬施工时,按炉衬技术规范进行。
5.4材料检验、运送:
施工前,施工技术人员应首先对炉衬材料的理化性能、出厂文件等进行检验并签证,然后,施工人员接受限额领料卡,协同工地材料员、设备员将炉衬材料用汽车运送至施工现场的临时场地,妥善保管。
施工时一般采用升降机、尼龙绳穿定滑轮及人工搬运等方法运送至施工作业点,随施工、随运送,保证施工供应。
5.5脚手架的搭拆:
脚手架的施工必须由专业人员完成,并以安检部验收合格后,挂牌方可使用,认真执行脚手架搭拆技术规范,不得违章作业。
5.6各部位衬里材料典型结构布置
(1)点火风道内衬结构:
炉膛进口段点火风道:
耐火浇注料+保温浇注料=总厚度
点火风道点火段:
顶面:
氧化铝空心球浇注料+绝热浇注料+超级绝热复合板=总厚度
侧面及底面:
氧化铝空心球浇注料+绝热砖+超级绝热复合板
点火燃烧器喷口部位:
四周:
高温刚玉莫来石耐磨可塑料
后端:
高温刚玉莫来石耐磨可塑料+绝热浇注料+无石棉微孔硅酸钙=总厚度
水冷风室:
耐火浇注料
(2)炉膛内衬结构:
炉底布风板及四周台阶:
耐磨浇注料
炉膛密相区及上部出口周边炉墙(左、右、后三面):
sic耐磨可塑料捣打
屏式受热面:
耐磨可塑料+sic耐磨自流浇注料(屏过与屏再、穿墙水冷蒸发屏施工各不同)
炉内集箱:
前后包墙上集箱:
其它集箱:
炉膛出口烟道(至膨胀节止):
sic耐磨可塑料(3)旋风分离器内衬结构:
分离器进口烟道:
sic耐磨可塑料
分离器筒体:
sic耐磨自流浇注料
分离器出口中心筒连接处:
耐磨浇注料+绝热浇注料=总厚度
分离器出口烟道:
耐磨浇注料+绝热浇注料+无石棉硅酸钙=总厚度
(4)回料器内衬结构:
回料器布风板:
熔融石英耐磨浇注料+2%钢纤维+绝热浇注料=总厚度
回料阀(上下两膨胀节之间阀体)排砖处:
耐磨砖+保温砖+无石棉微孔硅酸钙=总厚度
回料器上立管(无排砖处):
耐磨浇注料+绝热浇注料+保温浇注料=总厚度
回料腿(无排砖处):
(5)水平烟道内衬结构:
水平烟道靶区:
锆铬刚玉浇筑料+绝热浇注料+无石棉微孔硅酸钙=总厚度
水平烟道顶部(除靶区外):
自流式耐磨浇注料+绝热浇注料=总厚度
水平烟道其余部分(除靶区外):
耐磨浇注料+绝热浇注料+无石棉微孔硅酸钙=总厚度
5.7本项目锅炉耐火材料施工要领
5.7.1图纸设计砌筑要领(详见施工图纸内容)
5.7.2同类锅炉砌筑经验总结
(1)不同位置采用的耐火材料可能不一样,施工时,每个区域所用的耐火材料的性能不能低于该区域原始设计规定的要求。
(2)所有耐火浇注料内的金属钩钉、穿墙管件等均应涂以石油沥青漆,厚度为2毫米;
或包缠适当厚度的陶纤纸,为了保证沥青厚度,可考虑熬制沥青浸渍待焊抓钉端部。
(3)实践经验表明,根据实际情况适当补焊抓钉,是提高炉体结构稳定性的必要途径,因此,多制作些Y型扁钢抓钉、V型圆钢抓钉或φ6耐热钢筋(材质为0Cr25Ni20Ti)。
如有必要现场应考虑采用φ6耐热钢筋手工制作V型抓钉。
对于应力集中区(如大的开孔周边,膨胀节附近等),扁钢抓钉的使用性能优于圆钢抓钉,坚决杜绝点焊拼接抓钉的使用,尽可能确保抓钉的整体性,防止衬体的脱落及坍塌。
(4)施工浇注料时,其配料、配水、搅拌时间及水温以及初凝时间的控制,必须按施工工艺要求严格控制。
浇注料和可塑料拌和操作时,必须要有材料生产技术人员的监督指导方可进行。
(5)施工浇注料前,其模板的制造安装必须符合要求,采用合理的分隔块施工工艺,并采取有效措施防止模板位移和变形,模面应刷脱模剂。
拆模时,禁止乱撬乱砸,对脱模后的浇注料,应采取适当的养护措施。
凡与浇注料接触的保温材料表面(如硅酸钙、保温浇注料等)应铺置一层防水纸,防止因水份相互渗透对衬里强度产生不良影响。
(6)可塑料必须困料充分后方能使用,否则会鼓胀、起泡,影响衬里强度。
施工可塑料时坚决不允许超厚施工,厚度方向上不允许分层捣打。
可塑料必须捣打密实,表面修理平整,在有绝热保温层的情况下可塑料表面应刺扎排湿孔,半厚切割膨胀缝。
为保证可塑料的作业性能,拌和时促凝剂应分散均匀。
可塑料粘结剂中应含有适量的缓凝剂,以保证有充足的可作业时间,并保持可塑料料一定时期内的可塑性指标。
本项目可塑料的使用量大,面积广,因此可塑料的施工乃重中之重,必须切实采取有效的质量保证和控制措施。
5.8目锅炉各部位内衬结构与施工要点
一、点火风道
施工技术要点
(1)锚固件安装就位前应将风道壳体内表面清理干净,所有锚固件在浇注层部位均涂刷一层2mm的沥青,锚固件端头距内衬表面的距离为15mm。
(详见锚固件典型焊接图)
(2)炉膛进口段点火风道:
总厚度200mm,60mm耐火浇注料+140mm保温浇注料。
(3)点火风道点火段:
风道顶面总厚度为300mm,174mm氧化铝空心球浇注料+116mm绝热浇注料+8mm超级绝热复合板+2mm灰浆,风道底面及两侧面总厚度为300mm,174mm氧化铝空心球浇注料+114mm绝热砖+2mm灰浆+8mm超级绝热复合板+2mm灰浆,风道端板总厚度为225mm,80mm氧化铝空心球浇注料+70mm绝热浇注料+73mm无石棉微孔硅酸钙+2mm灰浆,与膨胀节相连接段顶面总厚度为225mm,99mm氧化铝空心球浇注料+116mm绝热浇注料+8mm超级绝热复合板+2mm灰浆,侧面及底面总厚度为225mm,99mm氧化铝空心球浇注料+114mm绝热砖+2mm灰浆+8mm超级绝热复合板+2mm灰浆,油点火器内衬处:
四周为厚度80mm高温刚玉莫来石耐磨可塑料,后端为100mm高温刚玉莫来石耐磨可塑料+80mm绝热浇注料+两层98mm无石棉微孔硅酸钙+两层2mm灰缝,一次风进点火风道处一周为60mm高温刚玉莫来石耐磨可塑料。
(4)现场施工浇注料各区域膨胀缝为:
点火风道顶部、底部沿长度和宽度方向设置800mm*800mm左右膨胀缝,长度方向膨胀缝宽2mm,深40mm,点火风道侧墙沿长度和宽度方向200mm*400mm设置膨胀缝,长度方向膨胀缝宽2mm,深40mm;
在施工耐火浇注料时,应在耐火层中沿长度及圆周方向每隔600mm左右设置一道膨胀缝,膨胀缝宽3mm(预留膨胀缝时,在缝中塞入两层2mm硅酸铝耐火纤维纸)。
(5)砌筑绝热砖时,砖与砖之间的沿高度和宽度方向的灰缝为2mm,角部地方根据实际尺寸切割后砌筑,砌筑时,如有空隙,用绝热浇注料灌满。
(6)超级绝热复合板与无石棉微孔硅酸钙制品施工时,制品之间以及制品与筒壁之间用灰浆粘贴,两层制品之间注意错缝、压缝;
在施工时,与锚固件相碰处现场切割制品,所有空隙处应填满保温材料,在绝热浇注料和无石棉微孔硅酸钙、超级绝热复合板之间摆放一层防水纸,以防水渗透。
高温刚玉莫来石耐磨可塑料施工配合比:
(骨料100Kg:
磷酸铝溶夜13Kg)
氧化铝空心球浇注料施工配合比:
(骨料100Kg:
水20Kg)
耐火浇注料施工配合比:
水13Kg)
保温浇注料施工配合比:
水25Kg)
绝热浇注料施工配合比:
水22Kg)
二、水冷风室;
(1)风室顶部不敷设耐火材料,其余四周及底部采用49mm厚耐火浇注料。
(2)施工前,所有耐火层中的金属件上应涂刷一层2mm的沥青。
(3)施工侧墙上部时,应对布风嘴采用保护措施,严禁堵塞风嘴。
(4)在密封钢板处耐磨层中,每隔600mm左右留3mm宽膨胀缝,预留膨胀缝时,在缝中塞入两层2mm的硅酸铝耐火纤维毡即可。
(5)耐火浇注料施工时必须立模浇注施工,不得手工涂抹。
三、炉膛布风板
(1)炉底布风板表面敷设70mm厚的耐磨浇注料,四周角部凸台敷设耐磨浇注料,凸台高度为200mm,前墙宽度为70mm,后墙宽度为120mm,两侧墙宽度为150mm。
(2)按图纸要求认真处理好排渣口处的施工,保证导向风管的有效使用,不得堵塞导向风管。
(3)排渣口两侧导向风管与浇注料现场浇注口连接时,要保证导向风帽内气流畅通,不得有杂物或堵塞导向风口,排渣口浇注时,可预先编制钢筋网进行锚固,网眼尺寸为100mm*100mm,钢筋表面涂抹2mm的沥青。
(4)该部位的施工应安排在炉膛上部所有部位完工后再进行,施工前应先清理底板脏物,并用胶布将风帽导管和风嘴包扎好,坚决不允许堵塞风口,严格按设计要求保证浇注料表面与风中心线的距离,以免影响床料的流化。
(4)炉膛布风板台阶使用过程中极易开裂脱落,必须补加长抓钉。
(5)在施工布风板四周200mm高的台阶时,在耐磨层中每隔600mm左右设置3mm膨胀缝,深约40~50mm,但应以不露出水冷壁管子为原则,在缝中塞入两层2mm硅酸铝耐火纤维毡即可。
耐磨浇注料施工配合比:
水6.5Kg)
四、炉膛密相区膜式水冷壁
(1)炉膛密相区大面积未开孔处敷设49mm厚的sic耐磨可塑料,双面水冷壁凸台部位敷设耐磨浇注料,凸台下部双面水冷壁敷设52mm厚sic耐磨可塑料,双面水冷壁上部敷设63mm厚的sic耐磨可塑料。
(2)施工前,所有耐火层中金属件表面涂抹2mm厚的沥青。
(3)炉膛密相区膜式水冷壁原设计全部采用sic耐磨可塑料,考虑到大开孔区(如落煤口、双面水冷壁连通口以及回料口等)可塑料捣打施工不便,难以保证开状和初期结构强度(含脱模强度),所以,大开孔区周边改用sic耐磨浇注料呈方块浇注施工,炉膛密相区大面积未开孔处敷设,最窄处的宽度(距空洞外缘)不得小于250mm。
先施工开孔区浇注料然后再施工周围的sic耐磨可塑料。
(4)大开孔区(如落煤口、双面水冷壁连通口及回料口等)的上半周,应合理设置径向导向膨胀缝,以充分吸收集中应力,保证耐火材料不脱落。
(5)大开孔区(如落煤口、双面水冷壁连通口以及回料口等)往往是让管集中区,水冷壁管上经常没焊销钉,耐火材料极易脱落,因此必须补焊销钉,或补加扁钢抓钉。
(6)孔洞部位的施工要求模具尺寸非常准确,安装牢固,不允许出现孔洞中心线偏心和标高更改,否则会出现在运行使用中的偏心冲刷,运行工艺达不到设计要求的现象发生,空洞钢管端头不得有耐火材料阻止其自由伸缩。
(7)严格按照设计要保证炉膛密相区耐火材料截至线倾角角度,截至线呈齿带状(顺规定角度合适管子在鳍片间捣打而成),不允许出现平台,注意超短抓钉的焊接(现场手工制作)。
双面水冷壁耐火材料截止线平台尺寸必须符合图纸要求,该形状用耐磨浇注料施工而成,注意长短抓钉的密布及搭配使用。
门孔堵塞必须紧凑而且内表面平整,避免出现涡流磨损周边耐火材料。
返料口下沿的形状及尺寸必须充分保证,与返料腿的拐角必须联体,务必采取必要的抓钉补强措施,合理设置伸缩缝。
错缝切割可塑料伸缩缝,尽力减少网状裂纹的产生,热一次风入炉膛处的施工较为复杂,应严格按照图纸要求认真施工。
五、屏过及屏再
(1)炉内屏式受热面:
迎风面、仰面区域敷设49.7mm厚的sic耐磨自流浇注料+2%钢纤维,其余敷设49.7mm厚的sic耐磨自流浇注料。
(2)施工前,所有耐火层中金属件表面涂抹2mm的沥青。
(3)搭好脚手架以后检查屏过及屏再销钉的布置情况,底部采用耐热钢筋与销钉相连,斜底以下采用sic耐磨浇注料浇注施工,上部截至线及前墙截至线附件区域采用sic耐磨可塑料捣打施工,并按要求打成斜坡或斜面,呈“齿带状”,该处注意超短抓钉的焊接。
施工sic耐磨自流浇注料时,沿高度和宽度400mm*600mm左右留取一道膨胀缝,深度约10mm,缝中塞入两层2mm厚的硅酸铝纤维毡即可,膨胀缝错列布置。
六、炉膛出口烟窗
(1)炉膛出口及炉顶有销钉区域烟窗均敷设49.7mm厚的sic耐磨可塑料。
(2)施工前,所有耐火层中金属件涂抹2mm厚的沥青。
(3)依据该部位现场销钉的布置情况补焊抓钉,并注意所有耐火材料截至线处超短抓钉的焊接。
全区域采用sic耐磨可塑料捣打完成,注意施工厚度的变化,要求施工时逆烟气流向叠压捣打施工。
所有耐火材料截至线处必须按设计要求打成斜面。
可塑料施工必须遵从规范要求。
顶棚靠近后墙区域的钢筋网格上必须倒挂抓钉,焊接时抓钉至少保证有两个焊点。
对出口膨胀节周边进行“前斜凸后斜切”的优化处理,以保证膨胀节不会因床料进入而烧坏。
地板的施工在该区域其它部位完工后进行。
sic耐磨可塑料施工配合比:
磷酸铝溶液11Kg)
sic耐磨自流浇注料施工配合比:
(骨料100Kg水6Kg)
七、旋风分离器
(1)进口烟道敷设55mm厚(局部区域为47.5mm厚)、分离器锥段及顶部敷设47.5mm厚的sic耐磨可塑料,分离器筒体敷设47.5mm厚的sic耐磨自流浇注料,分离器下直段内层敷设100mm厚的耐磨浇注料,其余部分敷设195mm厚的绝热浇注料。
(2)施工前,所有耐火层中的金属件涂抹2mm的沥青。
(3)分离器入口烟道采用sic耐磨可塑料捣打完成,施工厚度与分离器侧墙迎烟面施工厚度不同,施工时应注意,要求施工时逆烟气流向叠压捣打施工,并注意厚度变化的圆滑过渡;
地板的施工在该区域其它部位完成后进行,分离器直段、锥体依据该部位现场销钉的布置情况补焊抓钉,尤其注意“牛鼻子”抓钉的补强,“牛鼻子”附过区域(水平外伸至少200mm)采用sic耐磨浇注料浇注施工,直筒其它部位采用sic耐磨可塑料捣打施工;
锥体除上下拐角处300mm范围内采用sic耐磨浇注料浇注施工外。
其余全部采用sic耐磨可塑料捣打施工,要求施工时逆烟气流向叠压捣打施工;
分离器直筒体的结构,先天存在同心度变化,因此要求sic耐磨浇注料施工工作面尽可能保持圆滑过渡,以避免过渡磨损;
分离器顶部与中心筒交接部位,应依据实际结构体的间隙尺寸,来确定抓钉的补焊长度及型状,既要保证中心筒的热膨胀间隙,又要确保床料不会进入交接缝而冲刷炉管以及造成中心筒变形;
直段与锥体变径处可塑料的施工更应认真对待,该处的损毁几率较大,结构性膨胀缝的留设非常必要;
所有可塑料及浇注料的施工必须遵从规范要求。
(4)现场施工sic耐磨自流浇注料时,沿高度和宽度约400mm*600mm左右留取一道膨胀缝,深度约10mm,膨胀缝应错列布置;
施工耐磨浇注料时,沿高度及圆周方向每隔600mm左右设置一道膨胀缝,采用迷宫式结构,膨胀缝中填2mm硅酸铝耐火纤维纸,纵向和横向膨胀缝应呈T形交错。
八、回料器
(1)回料器下降段到阀体间的垂直段、回料器阀体后到炉膛段返料腿内衬总厚度为400mm,130mm耐磨砖+2mm砖缝+116mm保温砖+2mm砖缝+73mm无石棉微孔硅酸钙+2mm灰缝+73mm无石棉微孔硅酸钙+2mm灰缝。
回料器阀体(除底板外)内衬总厚度为400mm,150mm熔融石英耐磨浇注料+2%钢纤维+100mm绝热浇注料+130mm保温浇注料+20mm硅酸铝纤维毡。
回料器阀体底板内衬总厚度为400mm,150mm熔融石英耐磨浇注料+2%钢纤维+250mm绝热浇注料。
进炉膛段回料器内衬总厚度为400mm,150耐磨浇注料+100mm绝热浇注料+130mm保温浇注料+20mm硅酸铝耐火纤维毡耐磨砖墙托架钢板处结构为290mm耐磨浇注料+50mm绝热浇注料+60mm保温浇注料。
(2)现场施工时,所有耐火层中金属件表面涂抹一层2mm沥青。
(3)由于回料器结构形状复杂,几何尺寸变化较多,要求预制模板时,应先放样下料,进行预制和试拼装,以保证浇注后的浇注料厚度及几何尺寸符合设计施工图要求;
施工时,先施工料腿,再施工回料阀,最后施工回料竖井,对局部部位应视结构体,可增加和接长爪钉,以增加浇注料的整体结构强度;
硅酸钙必须现场切割成60~80mm宽的窄长条,拼接圆筒保温层时,其与钢板外壳的间隙以及层间间隙不得大于3mm;
无石棉微孔硅酸钙分两层施工,制品之间以及制品与筒壁之间用灰浆粘贴,两层之间应注意错缝、压缝,所有缝隙处填满保温浇注料;
耐磨砖、保温砖施工时可根据实际现场情况切割,如间隙较小不易安装保温砖时,可用保温浇注料将空隙灌满,施工保温砖和耐磨砖时应错缝和涂抹灰浆,以防止烟气漏泄,砖和硅之间的砖缝为2mm,用专用灰浆粘接;
现场施工耐磨材料时,膨胀缝的尺寸均按照设计图纸要求留置,膨胀缝错列布置。
(4)返料腿为斜立结构,衬里材料在运行中的挠曲作用明显,热冲击频繁,又由于使用过程中未燃烬炉料的二次燃烧,经常导致上半周衬体开裂、外壳发红毁现象,为规避此不良行为的发生,返料腿内衬浇注料的水泥含量应尽可能低,并应含有适量的微膨胀材料,降低超温操作条件下的线收缩,耐磨砖、保温砖、硅酸钙保温层也必须具备足够的耐火性能、隔热性能和体积稳定性;
外壁温度过高将加大衬里的相对位移,无疑也会加剧衬里损毁;
该部位是材