难浸金矿石预处理工艺研究现状概要Word文件下载.docx
《难浸金矿石预处理工艺研究现状概要Word文件下载.docx》由会员分享,可在线阅读,更多相关《难浸金矿石预处理工艺研究现状概要Word文件下载.docx(9页珍藏版)》请在冰豆网上搜索。
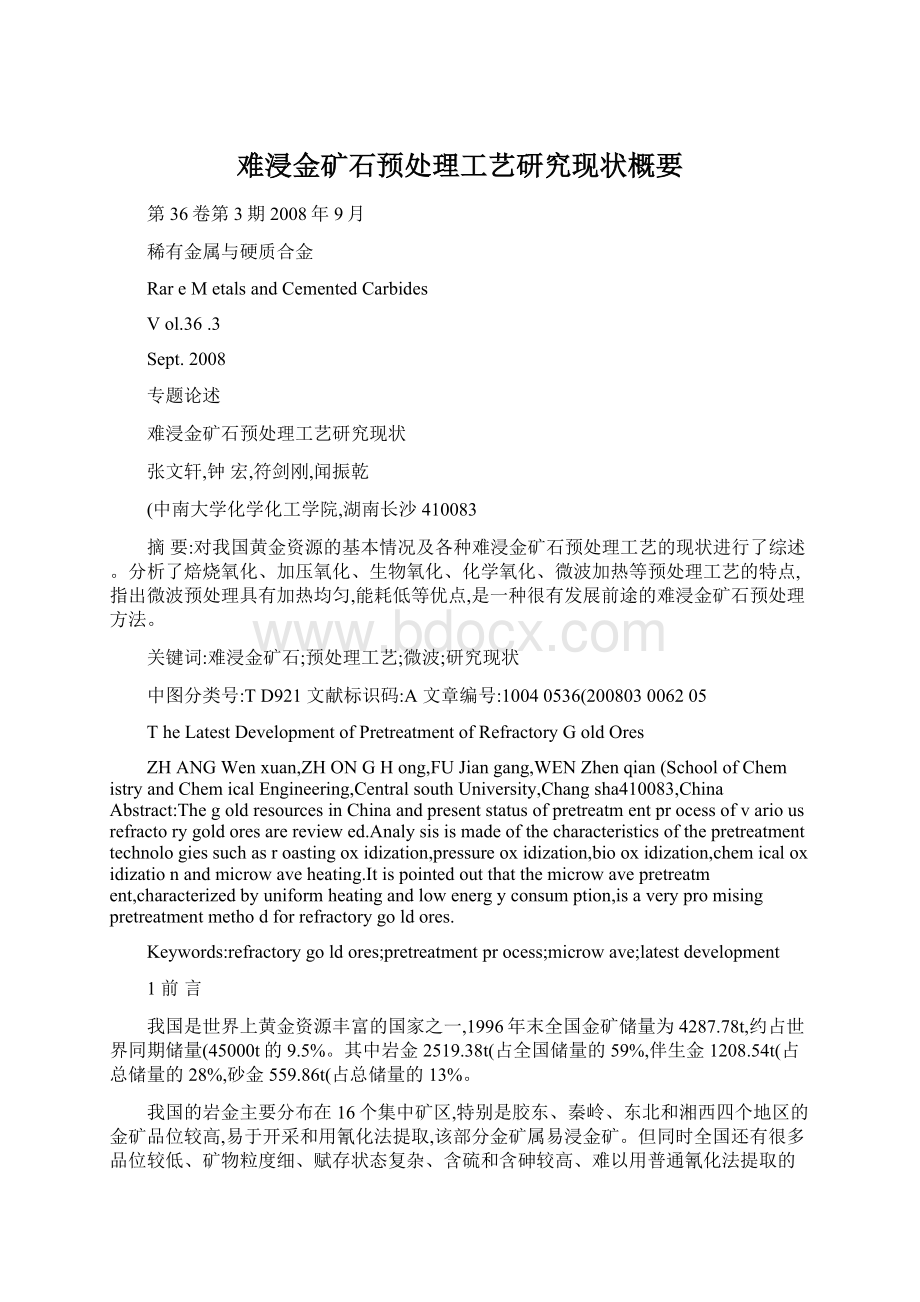
microwave;
latestdevelopment
1前言
我国是世界上黄金资源丰富的国家之一,1996年末全国金矿储量为4287.78t,约占世界同期储量(45000t的9.5%。
其中岩金2519.38t(占全国储量的59%,伴生金1208.54t(占总储量的28%,砂金559.86t(占总储量的13%。
我国的岩金主要分布在16个集中矿区,特别是胶东、秦岭、东北和湘西四个地区的金矿品位较高,易于开采和用氰化法提取,该部分金矿属易浸金矿。
但同时全国还有很多品位较低、矿物粒度细、赋存状态复杂、含硫和含砷较高、难以用普通氰化法提取的难浸金矿。
随着金矿的大规模开采,易浸金矿资源已日益枯竭,难浸金矿将成为今后黄金工业的重要资源[1]。
2难浸金矿预处理工艺的研究现状
难浸金矿石是指那些富含砷、碳等杂质组分,在常规氰化浸出条件下,金浸出率不高的岩金矿石。
根据矿石的内部结构,可将难浸金矿石大致分为以下三类:
第一类为金粒被非硫化脉石(硅石或碳酸盐包裹的金矿石,该类矿石中金粒较小,用普通机械碾磨难以使之与包裹矿物分离,从而造成浸取液氰化物很难与金粒接触;
第二类是金被包裹在硫化矿物(黄铁矿或砷铁矿中,该类矿石同时也是目前储量最大的难浸金矿石;
第三类矿石中金粒虽没有被其他矿物所包裹,但矿石中存在活性炭型有机碳,采用氰化物浸取时,金与氰化物形成的配位化合物能被其吸附,从而影响金的浸出。
正是基于上述原因,难浸金矿石在采用常规氰化物浸出前都要进
收稿日期:
20071015;
修回日期:
20080604
作者简介:
张文轩(1984,男,硕士研究生,研究方向为化学工艺。
第3期张文轩,等:
行预处理以使被包裹的金裸露出来,充分与浸出药剂接触反应,从而提高金的回收率。
目前常规的预处理工艺主要有以下几类。
2.1焙烧氧化法
焙烧氧化法是当前处理难浸金矿石最常用方法之一。
其主要原理是通过高温将包覆金的硫化矿物氧化为气态硫化物,从而达到暴露矿石中金粒的目的。
焙烧温度一般约为650~750!
发生的主要反应为:
3FeS2+8O2∀Fe3O4+6SO2
12FeAsS+29O2∀4Fe3O4+3As4O6+12SO2
2FeAsS+6O2∀Fe2O3+As2O5+2SO2
在焙烧设备方面,早期使用的有回转窑、沸腾炉等。
该类设备具有操作简单、原料适应性强和技术可靠等优点,但也存在污染严重、能耗高的缺点。
随着对环保及浸出率要求的日益提高,后来又推出了富氧焙烧法、闪速焙烧法及固化焙烧等新工艺。
2.1.1富氧焙烧法
富氧焙烧法是在焙烧过程中以氧气作为流动介质对硫化矿物进行氧化。
该法与传统空气焙烧法相比具有烟气体积减少、氧化充分、燃料消耗低、金回收率高、设备投资小等优点。
2.1.2闪速焙烧法
闪速焙烧法可进一步提高生产效率。
在该法中热空气通过喷嘴从炉底进入炉内,原料则从喷嘴上方直接进入热气流,气流以高速与物料同向运动,使细物料焙烧完全,并被夹带出炉,大物料颗粒在沉降到炉下部后被高速运动的气流夹带上升,延长了在炉内的停留时间。
该法的主要优点为:
(1特殊的气体分配方式,加大了物料间的传热和传质。
(2强化了炉内的传质和传热,颗粒在炉内的停留时间短,避免了颗粒的烧结。
(3设备小,固定投资少。
炉内压降低,能耗小。
有利于气体的循环再利用。
2.1.3固化焙烧法
固化焙烧法则是通过在矿石中添加钙、镁的碳酸盐将矿石中硫、砷等有害元素在焙烧过程固定于焙砂中,从而避免As2O3、SO2的产生。
其主要反应如下:
MgCO3∀MgO+CO2
2MgO+2SO2+O2∀2MgSO4
3MgO+As2O5∀Mg3(AsO42
该法既保留了传统焙烧法操作简单、对原料适应力强等优点,又克服了传统焙烧法环境污染重的缺点。
1990年美国的Cortez金矿首次成功采用固化焙烧工艺处理难浸金矿[2]。
根据固化剂的不同,又可将固化法分为钠盐法和钙盐法,钠盐法工艺流程复杂,固化剂成本较高,而钙盐法的工艺简单,成本也较钠盐法低。
2.2加压氧化法
加压氧化法利用高温高压及在富氧条件下,加入酸或碱性物质来分解矿石中硫及砷的化合物,其原理如下:
2FeS2+2H2SO4+O2∀2FeSO4+2H2O+4S
S+1.5O2+H2O∀H2SO4
2FeAsS+6.5O2+3H2O∀2FeSO4+2H3AsO4
2FeAsS+3.5O2+2H2SO4+H2O∀2FeSO4+2H3AsO4+2S
根据加入介质的差异,可分为酸性加压氧化法和碱性加压氧化法。
当原料为酸性或弱碱性时,采用酸性加压氧化法。
通常在温度170~225!
、压力为1~3.2MPa、氧分压为350~700kPa下操作,设备为耐酸砖衬里的碳素钢高压釜,1~3h内基本能将硫化物完全氧化[3]。
该法于1985年由美国的Mclaughlin金矿率先用于工业化生产,此后巴西的SaoBento、美国的Getchell、Goldstrike、LoneTree、加拿大的Campbell等相继建成加压氧化装置。
当原料为强碱性时,采用碱性加压氧化法。
操作温度为100~200!
、总压力约为3MPa,其中的硫和砷以硫酸盐和砷酸盐的形式溶解[4]。
1997年,长春黄金研究院与核工业北京化工冶金研究院合作,采用碱性热压氧化氰化提金工艺从某难浸金矿中回收金,金浸出率可达92%,而采用常规浸出时,金浸出率仅为45%[5]。
加压氧化法处理难浸金矿具有浸出率高、无烟气污染等优点,但也存在对设备的材质要求高,操作技术要求严格,以及对于含有机碳较高的矿石处理效果不理想等缺点。
2.3生物氧化法
该法利用细菌等微生物氧化包裹金的硫化物和砷化物,使矿石中的金颗粒裸露出来。
氧化作用可分为直接和间接两种方式,前者是在微生物的新陈代谢作用下,将不溶性的硫化物直接氧化为可溶性的硫酸盐,后者则是利用细菌新陈代谢所产生的三价硫酸高铁盐将包裹金的硫砷化合物氧化,从而达到暴露金粒的目的。
其反应如下[6]:
63
稀有金属与硬质合金第36卷
2FeAsS+7O2+H2SO4+2H2O∀Fe2(SO43+2H3AsO4
Fe2(SO43+2FeAsS+6O2+4H2O∀4FeSO4+H2SO4+2H3AsO4
生物氧化法的菌种主要为中温菌种,如氧化铁硫杆菌、氧化硫硫杆菌和氧化亚铁钩端螺旋菌等。
目前,该法主要可采用搅拌槽氧化浸出和堆浸。
对精矿一般采用搅拌浸,对于低品位矿则多采用堆浸。
在该法中,提供充足的氧气,控制反应中心温度和保证微生物的生物活性是关键。
生物氧化法主要具有环境友好、流程简单、投资小、操作成本低和能耗低等优点,但同时也存在着对矿浆浓度、酸碱度控制、温度控制条件苛刻及氧化速度慢等缺点,因而用该法处理小规模金矿在经济上更为合理。
2.4化学氧化法
2.4.1次氯酸盐氧化法
次氯酸盐氧化法所采用的浸取药剂为NaClO、Ca(ClO2及NaOH等。
该法具有两种工艺:
一种是采用次氯酸盐对矿石进行预处理;
另一种为直接采用次氯酸盐作为浸出剂直接浸出。
陈红波[7]等采用Ca(ClO2或NaClO对陕西汉阴难浸金矿进行预处理,随后氰化浸出,并研究了预处理的条件和进行了柱浸试验,据报道,金的回收率可达90%。
黎铉海[8]等则采用NaClO和NaOH对含砷难浸金矿进行直接浸出,并通过EpH图和Gibbs自由能分析了以NaClO为浸金药剂一步法的浸金原理和浸出条件;
考察了浸出条件对浸出率的影响,并提出了最优化工艺条件,即在cNaClO=2.3mol/L、cNaOH=1.0mol/L、R=10,t=80min条件下,金的浸出率可达80%以上。
2.4.2电化学氧化法
电化学氧化法是利用电极反应来氧化黄铁矿或砷黄铁矿。
其原理也是将包裹着金的硫、砷化合物氧化成可溶性的砷酸盐和硫酸盐,使金颗粒暴露出来。
该法与其他预处理方法相比,其优点是无有害气体排放、操作条件较为温和、氧化速度快。
据报道,含硫和砷的难浸金矿在电场作用下,矿物的孔隙将变大,从而有利于金的浸出。
Linge[9,10]进行的含砷难浸金矿的电化学氧化试验结果表明,在阳极矿浆浓度为10%、HCl浓度为0.1mol/L、NaCl浓度为3mol/L、温度在60~70!
时,阳极反应产生的氯气能与水作用生成次氯酸进而氧化矿物[11]。
2.5微波预处理
微波是频率大约在300MHz~300GHz,即波长在100cm至1mm范围内的电磁波。
它位于电磁波谱的红外辐射和无线电波之间[12]。
微波加热与传统加热不同,它不需要由表及里的热传导,而是通过微波在物料内部的能量消耗直接加热物料。
根据物料的物理性质(电导率、磁导率、介电常数的差异,微波可以在整个物料的内部产生热量。
微波加热在冶金中的应用具有其他传统加热方式无法比拟的优点,这主要体现在:
(1升温速率高,加热效率高。
(2可以显著降低一些化学反应的温度。
(3使分子发生高速振动,从而使化学反应具备更有利的热力学条件。
(4易于加热极性液体,因而可以提高湿法冶金过程中的浸出速率和降低能耗。
微波冶金作为一种新的冶金技术,20世纪70年代一些发达国家(如美国、英国、德国、日本、加拿大等就开始了对它的研究。
据报道,早在1967年,科研工作者就采用微波(2450MHz,800W对碳及17种氧化物和硫化物进行微波辐射,发现一些化合物在几分钟内就能被加热到摄氏几XX。
他们提出用微波加热来提取金属,并建议在减压条件下用微波分解辉钼矿。
Bilali[13]等则提出采用微波高温分解磷酸盐矿石。
SWKingman[14]等研究了微波在不同照射功率和时间下对矿物预处理的影响。
Amankwah[15]等研究了通过微波处理活性炭再生以回收金。
Haque[16]对矿物处理过程的微波进行了较系统、全面的研究,通过试验证明了微波在矿物加热干燥、氧化矿石的碳热还原、浸出、焙烧、难浸金矿石和金精矿的预处理、活性炭的再生及废弃物处理和金属回收方面均显示出一定的应用潜力,并根据微波在矿物加工过程中的研究和开发现状,主张在干式和湿式条件下,采用加压浸出对难浸金矿石的预处理进行重点研究。
Haque对金精矿进行实验室微波预处理结果表明:
在空气中约550!
时,矿石中的硫和砷开始氧化分解,形成气态As2O3和SO2。
随后对焙砂进行氰化物浸出,金浸出率可达98%,银浸出率为60%。
为避免As2O3和SO2有害物质的产生,可在金精矿中加入NaOH进行微波焙烧,结果表明采用该方法处理后的产物在75!
左右用水浸出,金的浸出率可
64
达99%。
Nanthakumar[17]等对Barrick#sGoldstrikeore低品位难浸金矿的微波预处理进行了研究。
该矿样的化学组成见附表。
附表Barrick'
sGoldstrikeore矿样分析w/%
元素AuCSFeCaMg
含量1.525.951.561.897.284.39
Au含量的单位为gt-1。
其结果表明:
在微波功率700W下,经微波预处理的矿样中总碳可以降低60%以上,硫则基本被氧化为硫的氧化物。
在随后的氰化物浸出试验中,采用微波预处理的矿样中金的回收率能达到95%以上,与在580!
下采用常规氰化物浸出26h的回收率相当。
该法与常规浸出相比具有能耗低,时间短等优点。
国内也于20世纪80年代开始了这一领域的研究工作。
谷晋川[18]等对难浸金矿微波的预处理进行了研究。
试验所用物料A(粒径小于74m占88%为含砷、硫、碳的难浸金矿。
该矿含有黄铁矿、斜方砷铁矿、毒砂、石墨等影响金浸出的矿物,且金的嵌布粒度较细,含23%的包裹金,金含量为29.60g/t。
试验所用物料B(粒径小于74m占75%为山东某金矿浮选精矿,主要金属矿物为黄铁矿,其次为磁黄铁矿及少量的黄铜矿、方铅矿及闪锌矿等,含金量为48.69g/t。
研究结果表明,难浸金矿经微波预处理后,其氰化浸出与常规的氰化浸出相比具有预处理时间短、浸出率高等优点。
魏明安[19]等对江西某难浸金矿的试验研究结果表明,采用微波预处理后,在氰化浸出条件为液固比2.5、pH值为11、NaCN用量5kg/t、室温下氰化24h,金的浸出率可达90%左右。
3结语
随着金矿资源的大规模开采,难浸金矿已逐渐成为提取黄金的主要原料。
在现有的难浸金矿处理工艺中,传统焙烧法虽工艺成熟、技术可靠,但工艺过程中排放大量含As2O3、SO2等有毒、有害气体及废渣,严重污染环境且能耗高;
加压氧化法由于在高温高压下操作,对设备的材质要求高,操作技术要求严格,工艺成本较高;
生物氧化法作为一种环境友好的新技术具有能耗低、流程简单、生产成本低等优点,但也存在着氧化速度慢及对氧化环境(酸碱度、温度、矿浆浓度要求苛刻等难以克服的缺点。
目前,微波作为一种新的能量形式,已广泛用于化工、医药、食品加工等行业。
在矿物加工工程领域,难浸金矿石微波预处理是一种很有前途的新方法,特别适用于含硫、砷、碳等有害成分的难浸金矿,已显示出良好的发展前景。
然而,微波在矿冶工程领域的应用目前还处于研究开发期,其对矿物作用机理的研究尚不够充分;
此外,应用于矿冶工程中微波反应器的设计及其过程的工业放大也还存在着相应的问题,今后仍需在微波设备的设计和改进方面多做工作,以解决矿物加工工程中的一些难题和提高选冶过程的生产效率。
参考文献:
[1]戴永年.金属及矿产品深加工[M].北京:
冶金工业出版
社,2007.
[2]李智伟.难浸金矿处理工艺新进展[J].有色金属设计,
1998(3:
1113.
[3]张秀华.难选冶金矿石预处理工艺现状[J].湿法冶金,
1998,(3:
1518.
[4]李俊萌.难处理金矿石预处理工艺及其选择[J].有色金
属(选矿部分,2002,(5:
1823.
[5]王力军,刘春谦.难处理金矿石预处理技术综述[J].黄
金,2000,(1:
3845.
[6]BreedAW,HansfordGS.Studiesonthemechanismand
kineticsofbioleaching[J].MineralsEngineering,1999,12(4:
383392.
[7]陈红波,封国宁,李铁球.含碳金矿的次氯酸盐预处理氰
化浸出研究[J].铀矿冶,1993,(4:
252255.
[8]黎铉海,粟海锋,黄祖强,等.次氯酸钠一步法浸金的原
理与试验研究[J].化工矿物与加工,2001,5(10:
15
18.
[9]LingeHG.Eletrolyticprocessforrefractoryarsenopy
riticgoldores[J].Mineralsengineering,1995,18(11:
13271332.
[10]LingeHG,WelhamNJ.Goldrecoveryfromarefrac
toryarsenopyrite(FeAsSconcentratebyinsituslurry
oxidation[J].MineralsEngineering,1997,10(6:
557
567.
[11]ArslanFatma.Electrooxidationofpyriteinsodium
chloridesolutions[J].Hydrometallurgy,1997,46:
157
170.
[12]金钦汉.微波化学[M].北京:
科学出版社,1999.
[13]BilaliL,BenchanaaM,ElharfiK,etal.Adetailedstudy
65
ofthemicrowavepyrolysisoftheMoroccan(Youssoufiarockphosphate[J].JournalofanalysisandAppliedPyrolysis,2005,3(21:
115.
[14]KingmanSW,JacksonaK,BradshawbSM,etal.An
investigationintotheinfluenceofmicrowavetreatmentonmineralorecomminution[J].PowderTechnology,
2004,9(29:
176184.
[15]AmankwahRK,PicklesCA,YenWT.Goldrecovery
bymicrowaveaugmentedashingofwasteactivatedcarbon[J].MineralEngineering,2004,8(23:
517526.[16]HaqueKE.Microwaveenergyformineraltreatment
processes∃abriefreview[J].Hydrometallurgy,1998,
12(22:
124.
[17]NanthakumarB,PicklesCA,KelebekS.Microwave
pretreatmentofadoublerefractorygoldore[J].Miner
alsEngineering,2007,10(20:
11091119.
[18]谷晋川,刘亚川.难选冶金矿微波预处理研究[J].有色
金属,2003,55(2:
5557.
[19]魏明安,张锐敏.微波处理难浸微细粒包裹金的试验研
究[J].矿冶,2001,10(1:
7477.
(上接第57页
(1:
3437.
[12]WangAH,YueTM.YAGlasercladdingofanAlSi
alloyontoanMg/SiCcompositefortheimprovementof
corrosionresistance[J].CompositesScienceandTechnology,2001,61:
15491554.
[13]胡乾午,杨泰平.镁基金属复合材料表面激光熔覆铜合
金研究[J].应用激光,2001,(4:
247250.
[14]居毅,郭邵义,李宗全.金属表面激光合金化及熔覆
处理的研究进展[J].材料科学与工程,2002,20(1:
143145.
[15]周笑薇,王小珍.激光熔覆技术在工业中的应用[J].中
州大学学报,2005,22(4:
110111.
[16]唐英,杨杰.激光熔覆镍基粉末涂层的研究[J].热
加工工艺,2004,(2:
1617,22.
[17]SmeggilJG,FunkenbuschAW,BornsteinNS.Arela
tionshipbetweenindigenousimpurityelementsandprotectiveoxidescaleadherencecharacteristics[J].MetalTransA,1986,17:
923932.
[18]TawancyHM,AbbasNM,BennettA.RoleofYdur
inghightemperatureoxidationofanMCrAlYcoatingonanNibasedsuperalloy[J].SurfCoatTechnol,
1994,6869:
1016.
[19]CzechN,SchmitzF,StammW.ImprovementofMCrA
lYcoatingbyadditionofrhenium[J].SurfCoatTechnol,1994,6869:
1721.
[20]KochJL,MaumderJ.Lasermaterialsprocessing,pro
ceedingsofSPIETheInternationalSocietyforOpticalEngineering[J].Wear,2006,(4:
164166.
[21]任爱国,王晓静,丁静.激光熔覆止裂技术研究[J].
表面技术,2006,35(2:
6971.
[22]邱小林.激光熔覆TiC金属基陶瓷涂层的研究[J].热
加工工艺,2006,35(10:
1922.
[23