丝杠螺母座文档格式.docx
《丝杠螺母座文档格式.docx》由会员分享,可在线阅读,更多相关《丝杠螺母座文档格式.docx(27页珍藏版)》请在冰豆网上搜索。
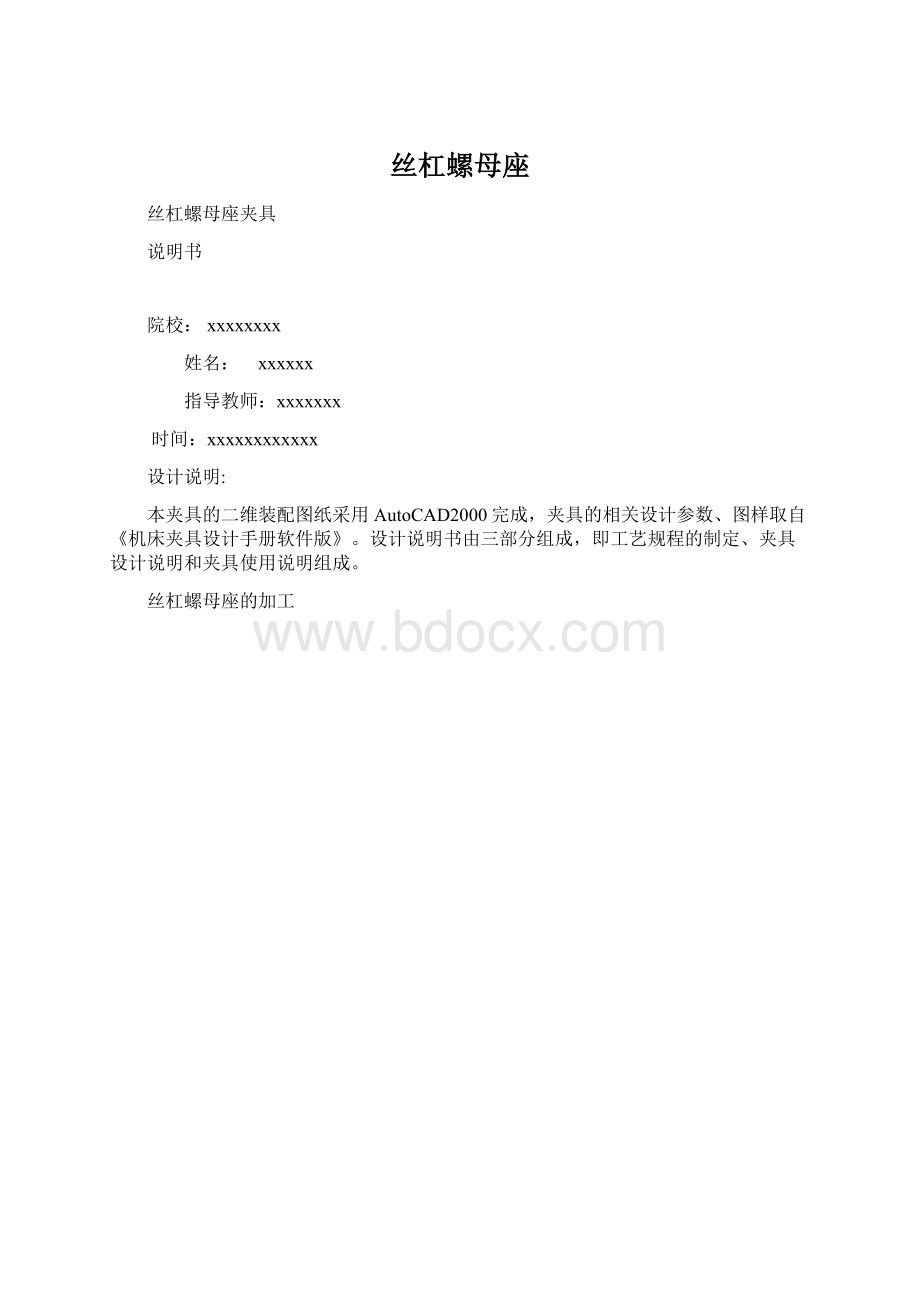
(1)为使加工时工件安装稳定,有些铸件毛坯需要铸造出工艺凸台,工艺凸台在零件加工后一般均应切除。
(2)装配后需要形成同一工作表面的两个相关零件,为保证加工质量并使加工方便,常将这些分离零件先做成一个整体毛坯,加工到一定阶段后在切割分离。
(3)对于形状比较规则的小零件,为了提高机械加工的生产率和便于安装,应将多件合成一个毛坯,当加工到一定阶段后再分离成单件。
有些表面不需要制出,如孔、槽、凹坑等。
因此,由于丝杠的特殊要求及螺母的外形特征,生产批量为200件是小批量生。
所以选择座球墨铸铁QT400用金属型铸造制造毛坯。
2.单个表面的加工方法:
零件表面加工方法,首先取决于加工表面的技术要求。
当明确了各加工表面的技术要求之后,既可据此选择能保证该要求的最终加工方法,并确定需要几个工步和工步的加工方法。
所选择的加工方法应满足零件的质量、良好的加工经济性和高的生产效率的要求。
为此,选择加工方法时应考虑下列因素:
(1)在选择加工方法时,应选择相应的能获得加工经济精度和相应的表面粗糙度的加工方法。
加工精度是指在正常加工条件下(采用符合质量标准的设备、工艺装备和标准技术等级的工人、不延长加工时间)能保证的加工精度。
相应的粗糙度称为经济粗糙度,各种加工可达到的经济加工精度和表面粗糙度见表
(一),详细资料可参阅有关工艺设计手册。
表
(一)各种加工方法的经济精度和表面粗糙度(中批生产)
(2)要考虑工件材料的性质。
例如,对淬火钢应用磨削加工,但对有色金属采用磨削加工就会发生困难,一般采用金刚镗削或高速精细车削加工。
(3)考虑工件结构形状和尺寸大小。
例如,对回转工件可以用车削或磨削等方法加工孔,而对箱体上IT7级公差的孔,一般就不宜采用车削或磨削,而通常采用镗削或铰削加工。
对孔径小的,宜用铰孔,对孔径大或长度较短的孔则用镗孔。
(4)要考虑生产率和经济性要求。
大批量生产时,应采用高效率的先进工艺,如平面和孔的加工采用拉削代替铣、刨和镗孔等加工方法。
甚至可以从根本上改变毛坯的制造方法,如用粉末冶金来制造油泵齿轮,用石蜡铸造柴油机上的小零件等,均可大大减少机械加工的劳动量。
(5)要考虑工厂和车间的现有设备情况和技术要求。
选择加工方法时应充分利用现有的设备、挖掘企业潜力,发挥工人的积极性和创造性。
但也要考虑不断改进现有的加工方法和设备,采用新技术和提高工艺水平,此外,还要考虑设备负荷的平衡。
6)特殊要求,如表纹路方向的要求
表
(二)、表(三)、表(四)分别列出了外圆、平面和内孔的加工方案,可供选择时参考
表
(一)各种加工方法的经济精度和表面粗糙度(中批生产)
被加工表面
加工方法
经济精度等级
表面粗糙度Ra/um
外圆和端面
粗车
半精车
精车
粗磨
精磨
研磨
超精加工
精细车
IT11~IT13
IT8~IT11
IT7~IT9
IT6~IT8
IT5
IT5~IT6
5.0~1.25
6.3~3.2
3.2~1.6
3.2~0.8
0.8~0.2
0.2~0.012
0.2`0.012
0.8~0.05
孔
钻孔
铸造孔的粗扩
精扩
粗铰
精铰
半精镗
精镗(浮动镗)
精细镗(金刚镗)粗磨
IT9~IT11
IT8~IT9
IT6~IT7
50~6.3
50~1.25
6.3~1.6
6.3~1.2
0.8~0.1
航模珩
拉孔
IT6
1.6~0.4
0.4~0.1
1.6~0.8
平面
粗刨、粗铣
半精刨、半精铣
精刨、精铣
拉削
IT7~IT8
50~12.5
表
(二)外圆表面加工方案
序号
加工方案
经济加
工精度
表面粗糙度
Ra/um
使用范围
1
IT11以上
适用于淬火钢以外的各种金属
2
粗车-半精车
IT8~10
3
粗车-半精车-精车
IT7~8
4
粗车-半精车-精车-滚压(或抛光)
0.2~0.025
5
粗车-半精车-磨削
0.8~0.4
主要用于淬火钢,也可用于未淬火钢,但不移机加工有色金属
6
粗车-半精车-粗磨-精磨
IT6~7
7
粗车-半精车-粗磨-精磨-超精加工
10.1~Rz0.
8
粗车-半精车-精车-金刚石车
0.4~0.025
主要用于要求较高的有色金属的加工
9
粗车-半精车-粗磨-精磨-超精磨或镜面磨
IT5以上
0.025~Rz0.05
极高精度的外圆加工
10
粗车-半精车-粗磨-精磨-研磨
0.1~Rz0.05
表(三)平面加工方法
经济精度
等级
适用范围
IT9
端面
粗刨(或粗铣)-精刨(或精铣)
一般不淬硬平面(端铣的表面粗糙度可较小)
粗刨(或粗铣)-精刨(或精铣)-刮研
精度要求较高的不淬硬平面,批量较大时宜采用宽刃精刨方案
粗刨(或粗铣)-精刨(或精铣)-宽刃精刨
粗刨(或粗铣)-精刨(或精铣)-磨削
粗刨(或粗铣)-精刨(或精铣)-粗磨-精磨
精刨-拉削
IT6~IT9
大量生产,较小的平面(精度视拉刀的精度而定)
粗铣-精铣-磨削-研磨
0.1~0.006
高精度平面
表(四)内孔加工方案
表面粗糙
度Ra/um
钻
IT11~IT12
12.5
加工为淬火钢及铸铁的实心毛坯,也有用于加工有色金属(但表面加工精度稍大,孔径小于15~20mm)
钻-铰
钻-粗铰-精铰
钻-扩
IT10~IT11
12.5~6.3
同上,但孔径大于15~20mm
钻-扩-铰
钻-扩-粗铰-精铰
IT7
钻-扩-机铰-手铰
钻-扩-拉
1.6~0.1
大批大量生产(精度由拉刀的精度决定)
粗镗(或扩孔)
出淬火钢外各种材料,毛坯有铸出孔或锻出孔
粗镗(粗扩)-半精镗(精扩)
11
粗镗(扩)-半精镗(精扩)-精镗(铰)
12
粗镗(扩)-半精镗(精扩)-精镗-浮动镗-刀精
13
粗镗(扩)-半精镗-磨孔
主要用于淬火钢,也用于淬火钢,但不宜于有色金属加工
14
粗镗(扩)-半精镗-粗磨-精磨
0.2~0.1
15
粗镗(扩)-半精镗-精镗-金刚镗
0.4~0.05
主要用于精度要求高的有色金属加工
16
钻-(扩)-粗铰-精铰-珩磨,钻-(扩)-拉-珩磨
,粗镗-半精镗-精镗-珩磨
精度要求较高的孔
17
以研磨代替上述方案中的珩磨
IT6以上
A面为φ40的圆孔的内表面,B面为丝杠螺母座的底面,C面为丝杠螺母座主视图的后表面,D面为丝杠螺母座主视图的前表面,E孔为φ40的孔,F孔为φ9的四个圆孔,G孔为φ8H7的两个配作孔。
A.B.C.D面----铣削加工
E孔----------镗削加工
F,.G--------钻削加工
3)粗基准的选择:
选择粗基准时,主要要求保证各加工表面有足够的余量,使加工面与不加工表面间的位置符合图样要求,并特别注意要尽快获得精基准面。
具体选择时应考虑下列原则:
i.选择不加工表面为粗基准。
ii.如果必须首先保证工件某重要表面的余量均匀,应选择该表面作为粗基准。
iii.选择作为粗基准的表面应尽量平整,没有浇口、冒口或飞边等其他表面缺陷,以便使工件定位准确,夹紧可靠。
iv.同一尺寸方向上的粗基准一般只能使用一次,即不应重复使用,以免产生较大的误差。
1.精基准的选择:
选择精基准应考虑如何保证加工精度和装夹准确方便,一般应遵循如下原则:
a)基准重合原则。
即用设计基准作为定位精基准,以避免定位基准与设计基准不重合而引起的基准不重合。
b)基准统一原则。
即当工序以某一组粗基准定位可以方便地加工其它表面时,应尽可能在多数工具中采取此组粗基准定位,以提高表面间的位置精度。
选作统一基准的表面,一般都应是面积较大、精度较高的平面、孔以及其他距离较远的几个面的组合.例如:
i.对箱体零件,用一个较大的平面和两个距离较远的孔作为精基准;
ii.对轴类零件,用两个顶尖孔作为精基准;
iii.
iv.对盘类零件,(如齿轮)用其端面和内孔作为精基准。
c)自为基准原则.即当精基准或光整加工工序要求余量尽量小而均匀时应选择加工表面本身作为精基准,而该加工表面与其他表面之间的位置精度则要求由先行工序保证。
d)互为基准原则.即为了获得均匀的加工余量或较高的位置精度,在选择精基准时可采用两个表面互相作为基准,反复加工,即为“互为基准”原则。
e)精基准的选择应使定位准确,夹紧可靠。
为此,精基准的面积与被加工的表面相比,应有较大的长度和宽度,以提高位置精度。
加工B面时:
以B面为粗基准加工A面,再以A面为精基准加工B面。
加工D面时:
以D面为粗基加工C面,再以C面为精基准加工D面。
加工F孔时:
以B面为精基准加工F孔。
加工E孔时:
以B面为精基准加工E孔。
加工G孔时:
以E孔和B面为精基准,加工G空。
1.工艺路线的划分:
机械加工工艺的拟定是制定工艺过程的总体布局,其主要任务是选择各个表面的加工方法和加工方案,确定各个表面的加工顺序以及整个工艺过程中工序数目和各工序内容。
1)基准的选择
在零件加工过程中,合理选择定位基准对保证零件加工质量起着决定性的作用。
2)表面加工方法的确定
零件表面的加工方法,首先取决于加工表面的技术要求。
当明确了各加工表面的技术要求之后,即可据此选择能保证该要求的最终加工方法,并确定需要几个工序和各工步的加工方法,所选择的加工方法应满足零件的质量,良好的加工经济性和高的生产效率的要求。
3)加工顺序的安排
在一个零件上往往有几个表面需要加工,这些表面不仅本身有一定的精度要求,而且各表面之间还有一定的位置要求。
1)铣削加工A和B面
2)铣削加工C和D面。
3)钻削加工侧孔E
4)镗削加工F孔
5)钻削加工G孔。
2.加工余量。
工序尺寸。
公差:
1)加工余量的确定:
(1)加工余量的概念
指在加工过程中,从被加工表面上切除的金属层总厚度。
加工余量分为工序余量和加工总余量
工序余量是指某一表面在一道工序中切除的金属层厚度,即相邻两工序的工序尺寸之差。
加工总余量,又称毛坯余量,是指零件从毛坯变为成品的整个过程中某一表面所切除金属层的总厚度,亦即零件上同一表面毛坯尺寸与零件设计尺寸之差,等于各工件加工余量之和。
(2)影响加工余量的因素
加工余量的大小对零件的加工质量,生产率和经济性都有较大的影响.确定加工余量的基本原则是在保证加工质量的前提下尽量减少加工余量。
影响加工余量大小的因素如下:
(a)前工序加工面(或毛坯)的表面质量(包括表面粗糙度和表面缺陷层深度);
(b)前工序(或毛坯)的工序尺寸公差;
(c)前工序的各表面相互位置的空间偏差,如轴心线的平行度,垂直度和同轴度误差等;
(d)本工序的安装误差,如定位误差和夹紧误差;
(e)热处理后出现的变形。
(3)加工余量的确定方法
(a)经验估算法。
工艺人员根据经验确定加工余量的方法。
为了避免产生废品,所以估计的加工余量一般偏大。
此法常用于单件小批生产。
(b)查表修正法。
此法是以企业生产实践和工艺实验经验积累的有关加工余量的资料数据为基础,并结合实际加工情况进行修正来确定加工余量的方法,应用比较广泛。
根据有关手册可查得。
(c)分析计算法。
此法是根据一定的实验资料和计算公式,对影响加工余量的各项因素进行分析和综合计算来确定加工余量的方法。
用这种方法确定加工余量最经济合理,但需要全面的实验资料,计算比较复杂,实际应用较少。
2.工序尺寸及公差的确定
工件上的设计尺寸一般要经过几道工序的加工才能得到,每道工序所应保证的尺寸叫工序尺寸,它们是逐步向设计尺寸接近的,直到最后工序才保证设计尺寸。
编制工艺规程的一个重要的工作就是要确定每道工序的工序尺寸及公差。
下面分工艺基准与设计基准重合和不重合两种情况,分别进行工序尺寸和公差的计算。
v.基准重合时,工序尺寸及其公差的计算
当工序基准.定位基准或测量基准与设计基准重合时工序尺寸及其公差的计算是比较容易的。
例如轴.孔和某些平面的加工,计算时只需要考虑各工序的加工余量和所能达到的精度。
其计算顺序是有最后一道工序向前推算,计算步骤如下:
a确定毛坯总余量和工序余量。
b确定工序公差。
最终工序尺寸公差等于设计尺寸公差,其余尺寸公差按经济精度确定。
c求工序基本尺寸。
从零件图上的设计尺寸开始,一直往前推算到毛坯尺寸,某工序的基本尺寸等于后道工序的基本尺寸加上(或减去)后道工序余量。
d标注工序尺寸公差。
最后一道工序的公差按设计尺寸标注,其余工序尺寸的公差按入体原则标注。
(2)基准不重合时,工序尺寸及其公差的计算
a定位基准与设计基准不重合的工序尺寸计算
在零件采用调整法加工时,如果加工面的定位基准与设计基准不重合,就要进行尺寸的换算,重新标注工序尺寸。
b测量基准与设计基准不重合的工序尺寸计算
在加工或检查零件的某个表面时,有时不便按设计基准直接进行测量,就要选择另外一个合适的表面作为测量基准,以间接保证设计尺寸,为此,需要进行有关工序尺寸的计算。
A面的铣削加工:
以底面为基准,在留有足够余量时,粗铣A面。
加工到不留黑皮即可。
为侧孔F和底面的精加工做准备。
B面的铣削加工:
工序名称
工序余量
工序精度
工序基本尺寸
工序尺寸及精度
精铣
1.0
IT7
18
设计尺寸
半精铣
2.4
IT10
19
由入体原则决定
上偏差为零
粗铣
IT12
21.4
C面的铣削加工:
在留有足够的余量情况下,以D面为粗基准加工.
2.4
IT9
66
4.0
IT11
68.4
D面的铣削加工:
0.5
60
1.5
60.5
62
E孔的镗削加工:
精镗
0.4
φ40
1.6
φ39.6
下偏差为零
粗镗
φ38.0
F孔的钻销加工:
G(侧孔)的钻削加工:
φ11孔
钻头直径
铰削
φ9
IT10
钻削
φ8
IT12
φ7
D面上的四个对称孔的钻削加工:
刀具直径
攻螺纹
φ5
IT10
φ4
3)机床刀具:
刀具的选择主要取决于工序所采用的加工方法、加工表面的尺寸、工件材料、所要求的精度和表面粗糙度、生产率和经济性等。
在选择时应尽可能采用标准道具,必要时可采用高生产率的复合刀具和其他一些专用刀具。
3切削用量(v,ap,f)
与确定切削用量有关的因素有:
生产率、加工质量(主要是表面粗糙度)、刀具耐用度、机床功率、切削引起的工艺系统的弹性变形和振动等。
切削用量的确定原则是:
在综合考虑有关因素的基础上,先尽量取大的背吃刀量,其次取较小的进给量,最后去合适的切削速度。
但由于许多工艺文件上一般不规定切削用量,而由操作者根据实际情况自己确定。
4样床及刀具的选择:
立式铣床型号:
X50
主轴端到工作台H|最大:
400
主轴端到工作台H|最小:
10
工作台到床身导轨L|最大:
240
工作台到床身导轨L|最小:
80
主轴轴线到床身导轨距离L1:
270
铣头回转角度:
工作台最大移动量|纵向:
500
工作台最大移动量|横向:
160
工作台最大移动量|垂直:
390
卧式镗床型号:
168*
镗床头和立架间最大距离A:
2270
主轴最大轴向移动量B:
600
主轴箱升降行程:
755
镗床头到工作台中心L|最大:
1660
镗床头到工作台中心L|最小:
520
主轴轴线到工作台H1|最大:
800
主轴轴线到工作台H1|最小:
45
立架上孔径D:
85
工作台离导轨高度S:
345
工作台移动距离|纵向:
1140
工作台移动距离|横向:
850
刀具选择:
刀具名称
刀具材料
尺寸
面铣刀
硬质合金
φ100
单叶镗刀
麻花钻
高速钢
φ10
绞刀
φ11
丝锥
5切削用量的分配:
与确定切削用量有关的因素有:
加工内容
刀具
主轴转速
(r/min)
进给速度
(mm/min)
背吃刀量(mm)
铣A面
面铣刀φ100
300
铣B面
100
30
铣C面
铣D面
镗φ50H7孔
单叶镗刀φ40