高炉焦槽除尘文档格式.docx
《高炉焦槽除尘文档格式.docx》由会员分享,可在线阅读,更多相关《高炉焦槽除尘文档格式.docx(24页珍藏版)》请在冰豆网上搜索。
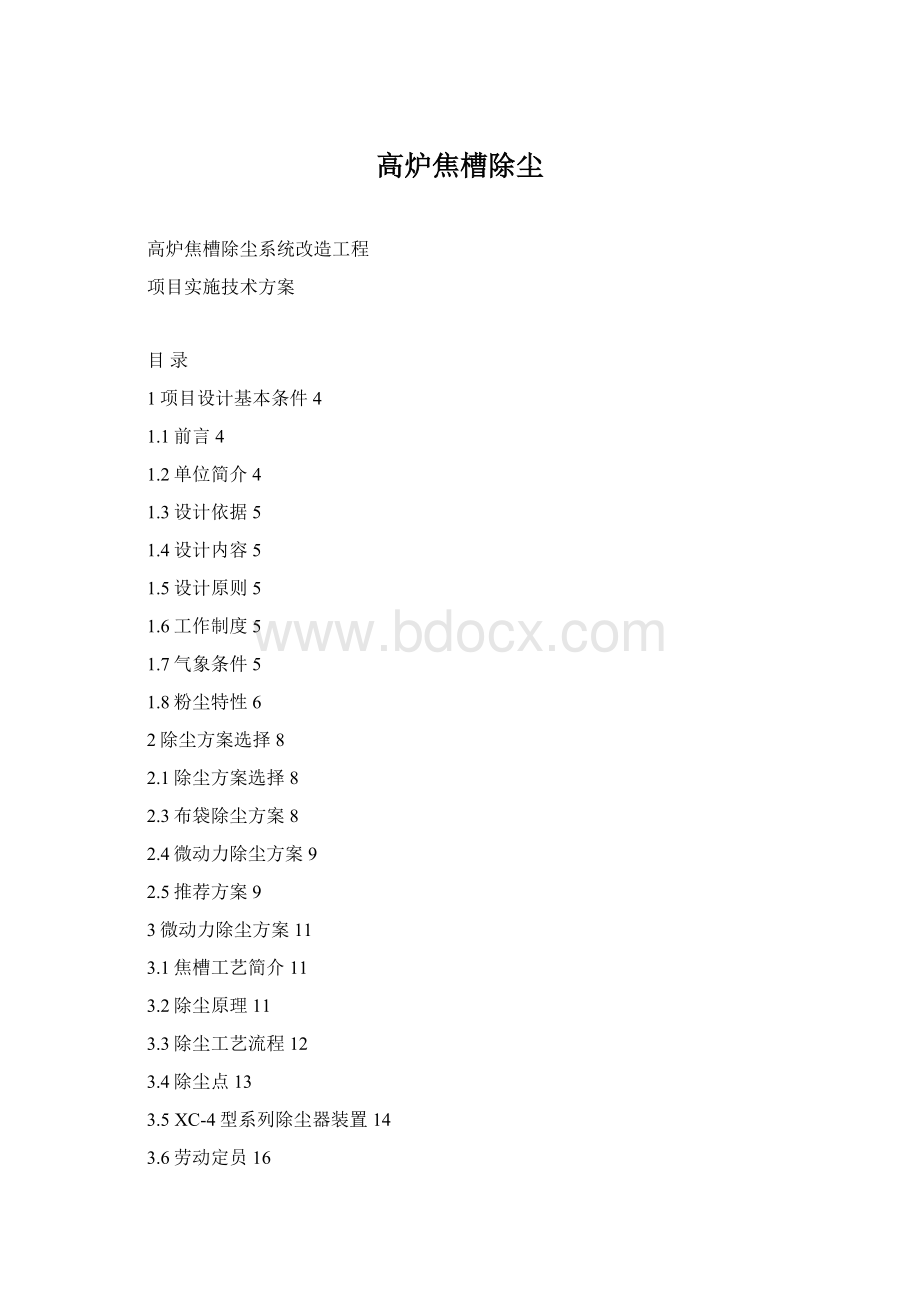
8.4施工工艺流程25
8.5施工前的准备工作26
8.6主要施工步骤26
8.7质量保证计划26
8.8工程进度26
9项目管理机构配备情况28
9.1项目管理机构28
9.2总部对项目部的管理及项目部的责任及权利29
9.3造价控制措施29
9.4质量管理及质量保证体系31
1项目设计基本条件
1.1前言
目前,XX高炉焦槽采用传统的布袋除尘器进行除尘,与矿槽共用一套除尘器。
随着焦槽、矿槽负荷加大,布袋除尘器除尘能力不足。
拟对除尘系统进行改造,将焦槽和矿槽除尘系统分开,保留原有的布袋除尘器,全部用于矿槽除尘系统,增强其除尘能力,保证矿槽除尘效果;
昆钢机械制造安装工程有限公司、丹东利洁环保除尘新技术有限公司和云南省冶金研究设计院(昆明冶金研究院)三个单位,具有各自的强势,形成联合体,利用丹东利洁环保公司的专利除尘技术、昆钢机制公司的加工优势和云南省冶金研究设计院的设计能力,针对XX高炉焦槽目前除尘能力不够,除尘效果不佳的现状提出新的除尘方案。
1.2单位简介
1.3设计依据
(1)对现场踏勘、收集资料。
(2)国家及地方有关法规、标准、规范。
1.4设计内容
本工程包含XX高炉焦槽除尘系统。
包含除尘工艺、设备及除尘系统配套的各项公辅设施。
XX高炉共五个焦槽,分为槽上、筛上和筛下三个运输系统。
五台振动筛机,B=650、B=1200皮带运输机。
焦槽除尘包括槽上(焦仓)、振动筛和皮带运输机等转运点、物料跌落点的除尘。
1.5设计原则
坚持“精确设计、循环经济、合理工艺、技术先进、运行低廉”的设计原则,充分结合现场条件,对除尘系统进行优化设计,综合治理,进一步改善昆钢以及安宁地区的环境质量,改善生产作业环境,保护工人的身体健康,使区域的生活、工作环境得以明显的改善。
1.6工作制度
焦槽工作制度:
年工作330d,3班/d,8h/班。
1.7气象条件
1.8粉尘特性
1.8.1粉尘的成份
高炉冶炼中产生的粉尘多为焦物粉尘,粉尘一般化学成份见表1-1。
表1-1粉尘化学成份
成份%
TFe
SiO2
CaO
MgO
游离SiO2
槽下配料
48.37
12.77
5.84
2.46
11.46
1.8.2烟气粉尘的密度
焦槽配料粉尘的平均密度为:
真密度:
3.89g/cm3,体积密度:
1.36g/cm3。
1.8.3粉尘的粒径分布
粉尘的质量粒径分布见表1-2。
表1-2粉尘的质量粒径分布
粒径
>
40
40-30
30-20
20-10
10-5
<
5
焦槽配料
53.3
10.7
13.2
15.2
5.87
1.73
由此可见,烟气粉尘中粒径>
40μm的粉尘占53.3%左右,微粉不多。
1.8.4粉尘的安息角
粉尘的安息角如下:
运动安息角为33°
~35°
,静止安息角为42°
。
安息角偏大,流动性一般,需在灰仓上设置仓壁振动装置,防止在斗内“架料”。
1.8.5粉尘的磨琢性
根据配焦粉尘的粒质分布得知>
40μm的粉尘占53%以上,对系统壁面的磨损明显。
2除尘方案选择
2.1除尘方案选择
本工程包含收集焦槽生产过程中的粉尘,粉尘主要产生于筛分、转运等过程的物料跌落点。
筛分、运输和给矿机等设备的扬尘点应最大限度地予以密闭,并设置有效的除尘措施。
在生产中,用于输运物料的方法为多段皮带运输,设有转运站,并在上段皮带与下段皮带之间设有物流导槽,在物料导槽上部设有一进料入口,利用该转运站可以使上段皮带中运输物料进入到下段皮带中,由于物料在导料槽中下落时会产生大量粉尘,为降低粉尘,减少粉尘对环境的影响,需设置除尘设施。
除尘器可分为几类:
①干式除尘器:
包括重力沉降室、惯性除尘器、电除尘器、布袋除尘器、旋风除尘器、无动力除尘器。
②湿式除尘器:
包括喷淋塔、冲击式除尘器、文丘里洗涤剂、泡沫除尘器和水膜除尘器等。
最新技术:
微动力除尘装置。
目前常见的运用最多的是旋风分离器、静电除尘器与布袋除尘器。
综合考虑除尘效率、运行成本、电能消耗、二次污染、设备维修量、物料性质的要求影响等因素的对比,布袋除尘及微动力除尘方式较其他方案有显著优势。
2.3布袋除尘方案
本项目除尘系统主要处理原矿在输送过程中筛分、转运等环节的物料跌落点产生的粉尘。
除尘原理为负压吸收。
除尘工艺流程为:
粉尘→吸尘罩→除尘管道→布袋除尘器→除尘风机→消声器→烟囱→大气。
布袋除尘器烟尘→旋转卸灰阀→刮板输送机→集合刮板输送机→斗式提升机→储灰斗→除尘加湿搅拌机→汽车定期运出。
净化后的排放的烟气含尘浓度低于50mg/Nm3,符合国家排放标准;
作业岗位的粉尘浓度低于10mg/m3,符合国家职业卫生的标准。
2.4微动力除尘方案
六高炉焦槽除尘系统主要处理在输送过程中筛分、转运等环节的物料跌落点产生的粉尘。
微动力除尘装置均设置在皮带运输机、振动筛或其它运输设备上,不单独占地。
微动力除尘技术打破了传统的除尘原理,运用空气动力学原理,采用压力平衡和闭环流通方式,最大限度降低物流导管内粉尘空气的压力,试之与外部空间压力趋于平衡,通过自动化控制系统,粉尘空气经抑制、缓解,粉尘的捕集自动往复系统协调工作,实现空气粉尘的闭路良性循环,杜绝了粉尘外溢污染环境的现象。
粉尘气流→(落料管)→多功能除尘室→尘料分流装置→滤尘室→脉冲负压吸尘器→密封帘→滤尘室→空气。
本流程的特点是:
(1)无须人工操作,动力少,维护少,无二次污染;
(2)检测控制准确,自动回旋彻底,除尘效果显著;
(3)投资少,不占地,设备维修费用小,安全可靠。
作业岗位的粉尘浓度低于10mg/Nm3,符合国家职业卫生的标准。
2.5推荐方案
针对六高炉焦槽工艺设备的特点,综合技术经济、节能减排等各方面因素,推荐采用合理工艺、技术先进、运行低廉的微动力除尘方案。
微动力除尘工艺运用高新技术和空气动力学原理开发研制的除尘装置,运用于除尘实践,环境质量均达到并超过国家标准。
已经在河南永龙热电公司、华能营口电厂、唐山钢铁公司焦厂、大庆市新潮热力有限公司、宝鸡第二发电有限责任公司、包钢热电厂等企业应用。
在云南,昆钢焦化厂、昆钢龙山矿已经使用了该技术。
云锡大屯选矿厂正在施工。
唐山市疾病预防控制中心,在唐钢炼焦制气厂13号输煤站全微动力除尘,进行了工作场所职业病危害因素检测。
13号输煤站13#皮带机头,检测浓度为5.67mg/m3;
13号输煤站13#皮带机尾,检测浓度为2.97mg/m3。
国家标准6.0mg/m3。
检测结论:
按照GB5748-1985总粉尘的滤膜称量法,2007年11月对唐钢炼焦制气厂13号输煤站13#输煤皮带机头、机尾工作场所中粉尘中浓度进行检测,检测结果显示:
符合GBZ2-2002《工作场所有害因素职业接触限值》工作场所短时间接触容许浓度。
3微动力除尘方案
微动力除尘技术拥有检测控制准确湿润搅拌均匀,自动回旋彻底,除尘效果显著;
无占地,投资少,动力消耗小;
使用安全可靠,技术新颖合理,维护量小,无须人工操作,无二次污染等优点。
采用微动力除尘技术,无需对厂房进行改造,除尘工艺简捷有效。
微动力除尘器型号为XC-4型。
3.1焦槽工艺简介
XX高炉共五个焦槽。
焦槽上有B=1000皮带运输机及卸料小车,分别为五个焦槽供料。
焦槽顶部原有五个除尘口,设有除尘管道和电动阀门。
槽下设有五台振动筛,筛上成焦和筛下碎焦分别进B=1200、B=650皮带运输机,由西向东运行。
筛上成焦经一个转运站进入高炉上料主皮带。
筛下碎焦经三个转运站进入碎焦仓。
3.2除尘原理
运用空气动力学原理,采用压力平衡和闭环流通方式,最大限度降低物流导管内粉尘空气的压力,使之与外部空间压力趋于平衡。
采用负压消尘的观念,在密封的容器内,在负压状态下实现负压、正压交替循环,使运转过程中产生的冲击粉尘在多功能消尘装置内充分释放,加速循环撞击,充分利用气体压力,含尘气体经抑制、缓解、撞落等过程,粉尘被捕集在脉冲负压吸尘器内,自动往复系统协调工作,实现空气粉尘的闭路良性循环,杜绝了粉尘外溢污染环境的现象。
物料在跌落过程中,产生大量负压气流,气流经多功能除尘室,箱内的空间增大,使在反作用力下爆炸或上扬粉尘在箱内释放,气流撞击到对应的应力板,直线运动变为曲线运动,起到缓压的作用,粉尘在运动中被减弱,在脉冲负压吸尘器内被完全捕集。
其粉尘按要求进入规定的容器内,达到消除粉尘的目的。
3.3除尘工艺流程
针对不同的除尘点的特性,设计不同的除尘工艺,保证除尘效率。
3.3.1槽顶给料小车
在给料小车顶部卸料口设置密封槽和密封胶条,形成多功能除尘室,设置脉冲负压吸尘器,进行综合除尘。
除尘装置随着给料小车一同运行,实现移动除尘。
含尘气体→多功能除尘室→尘料分流装置→滤尘室→脉冲负压吸尘器→滤尘室→密封帘→空气。
3.3.2焦槽
在焦槽顶面原有的空位处,设置脉冲负压吸尘器,捕集含尘气体,经净化后的气体达标排放,捕集下的粉尘经导流管送入焦槽。
含尘气体→脉冲负压吸尘器→空气。
3.3.3振动筛
在振动筛顶部设置密封室,与筛上、筛下落料管形成一各密封容器;
设置脉冲负压吸尘器,捕集含尘气体,经净化后的气体达标排放,捕集下的粉尘经导流管送入碎焦皮带机密封室。
在振动筛筛上落料管,设置回气管,将粉尘引入碎焦皮带机密封室。
3.3.4碎焦转运
碎焦从上段皮带通过物料导料槽落入下段皮带,由物料流速所产生大量负压气流,反作用力使粉尘随气流产生“爆炸”点上扬,气流经多功能除尘室,箱内的空间增大,粉尘在箱内释放,气流撞击到对应的应力板,大颗粒粉尘在撞击作用下,落入下端输运皮带中。
气流的直线运动变为曲线运动,起到缓压的作用,粉尘在运动中沉淀下来,落入皮带中,随物料通过尘气分离室时剩余的粉尘通过所设多层的圆条状胶帘进行再次除尘处理。
含尘气体→多功能除尘室→尘料分流装置→滤尘室→滤尘室→密封帘→空气。
3.3.4筛下成焦转运
成焦从振动筛通过物料导料槽落入成焦皮带,进入多功能除尘室,腔室扩大,高速运动的粉尘速度变缓,进入脉冲负压吸尘器进一步吸收粉尘,剩余的粉尘通过所设多层的圆条状胶帘进行再次除尘处理。
系统实行三层次结构,做到逐级处理,形成一个完整有机结构,达到消除粉尘的目的。
脉冲负压吸尘器捕集下的粉尘排入附近的碎焦皮带密封室内,不排入成焦皮带。
3.3.4成焦主皮带转运点
成焦皮带转运到高炉上料主皮带时,仍产生大量的粉尘。
采用微动力除尘工艺,脉冲负压吸尘器捕集到的粉尘,无法自动返回碎焦皮带,若采用人工输送,将增大除尘成本,降低除尘自动化程度。
本技术方案建议,成焦皮带转运共6个除尘点,仍采用已有的布袋除尘方案。
为保证矿槽除尘有足够的风量,在矿槽上任意6点采用微动力除尘减轻矿槽除尘负荷。
3.4除尘点
输送系统为皮带式输送,带宽B=1000mm,B=1200mm,B=650mm三种,输送物料介质为焦碳;
分为混合状、块状及粉状三类,外载水份微干,(5%以下),落料转运现场粉尘扬溢。
除尘系统改造工程实施安装除尘器型号为XC-4B100、XC-4B120、XC-4B65系列除尘器。
除尘工艺、结构、各装置根据现场实际情况实施。
XC-4型微动力除尘器采用独特的工艺设计,简化安装和维护工作的可行性,装置结构新颖独特、布局巧妙合理、效益节能减排、运行自动联锁、外观整齐美观,无需新增新建用地及土建设施。
微动力除尘点及除尘器设备表见表3-1。
表3-1微动力除尘点及除尘器设备表
序号
除尘点
除尘器型号
台数
物料性质
1
移动小车顶部
XC-4B100
混合焦
2
焦槽顶部
密封治理
3
振动筛
4
筛下成焦Y6-1(尾)
XC-4B120
成焦
筛下碎焦Y6-2(尾)
XC-4B65
碎焦
6
焦槽平台落尘点
7
碎焦转运Y6-2(机头)
8
碎焦转运Y6-3(尾)
9
碎焦转运Y6-3(机头)
焦、粉状
10
碎焦转运Y6-4(尾)
11
碎焦转运Y6-4(机头)
12
成焦转运
合计
33台
3.5XC-4型系列除尘器装置
3.5.1主体装置
每台除尘器的结构形式是根据原设备实际设计,为多元组合装置。
采用国家标准设备。
导料槽及两翼密封侧板长度、结构根据原设备运行技术参数,尽最大输送出力量、取最小减少摩擦系数制造。
多功能除尘室、尘料分流室、释缓室、回融管与流料槽回融切口形成完整的闭路循环;
抑制、缓解、捕集、释放使扩溢性粉尘气体消势,粉尘亲结成重粒落回运行的物料中,达到节能减排目的。
多功能除尘室为多工艺、效能综合设置,以射流、导向缓释为主模式,尘料分流室属多功能吸咐、隔气、通料装置,促使料筒下落皮带上物料与扩溢粉尘气体导向分流;
输送物料流过,粉尘气体隔至导向流向多功能除尘室容室内。
3.5.2附机装置
滤尘室、栈桥微环室组配,对主体装置漏移气体粉尘实施微环处理,进行尘气隔离、气体释缓,隔离后的尘粒压落入运行的物料中融合。
本装置设置3-4级流程工艺,使之排放口净气排出。
3.5.3FG-3脉冲负压吸尘器
本装置由风机、主体、布袋、脉冲清灰装置组成,具体结构简单,易损件少,维护量小,便于检修,方法简便易掌握等特点,除尘效率98%以上。
与其它同类除尘产品不同的是,本除尘器工作运行设置在粉尘含量极微小的除尘段(气体粉尘已经主体装置、附机装置除尘处理),所以其负荷量极小,相应使用寿限大幅延长。
该除尘器设置排入口前端,由于负压吸抽,排放口呈负压净气排放。
XC-4型系列除尘器性能及参数见表3-2,FG-3型脉冲袋式吸尘器技术参数见表3-2。
表3-2XC-4型系列除尘器性能及参数
皮带规格(mm)
性能参数
500
600
800
1000
1200
1400
1600
出料口参数
350
450
650
850
除尘器重量(t)
1.62
2.08
2.47
3.51
4.13
4.26
4.70
平均承荷量kg/m2
270
261
196
177
180.7
175.2
167
安装前粉尘浓度
200-1000mg/m3
安装后粉尘浓度
2.0-6.0mg/m3
需用电功率
配装FG-3负压吸器的1.1-3.0kW
表3-3FG-3型脉冲滤筒式吸尘器技术参数
单
元
数
过滤
面积
(M2)
滤袋
尺寸
(mm×
m)
处理
风量
(m3/h)
压力
损失
(kPa)
风速
(m/min)
允许
温度
(℃)
入口
浓度
(g/m3)
压缩空气
电机
容量
(kW)
质量
(kg)
耗气量
(m3min)
压力(MPa)
39.6
170×
0.8
8000-16000
135
≤30
0.54~0.61
0.4
2.2
428
58.7
1.0
25000-49000
0.4~1.0
2.1~4.2
0.54~0.68
3.0
614
79.2
46000-70000
4.0
1624
3.6劳动定员
采用微动力除尘方案,动力消耗小,无需配备操作工人。
4微动力除尘安装
4.1除尘器机组安装说明
(1)除尘器气流入口经多功能除尘室、缓释室和回融管分别组装在皮带尾部输运皮的导料槽上与溜料槽回融切口相接。
(2)导料槽与多功能除尘室的联接采用焊接方式,以加强除尘密封。
(3)尘料分流室、滤尘室、栈桥微环室联接方式为焊接。
(4)机头除尘器为分组整体联装,联通管与原设备法兰联接。
(5)机头配套智能控制仪采用壁挂式(防尘、防水)所属电辅设管路、管件、电缆、无器件按行业规范、规定实施。
(6)除尘器组装完成后易蚀所属部件做油漆防腐处理,外表颜色整新。
4.2装置基本材料与规格
4.2.1主体设备
(1)多功能除尘室尺寸为1100×
1800×
1000×
δ4,材料Q235
(2)导料槽截面几何尺寸1000×
880×
500×
δ6材料Q235
(3)所用检视门密封采用橡胶压条φ16×
H25
(4)尘料分流室、尺寸为1100×
400×
300×
δ4材料Q235
(5)尘料分流装置适用高强耐磨胶料加工。
单条φ5-6mm,为5-7层,尺寸为1100×
1000。
(6)释缓室为1500×
1500×
δ4组合装置,材料Q235。
4.2.2分离装置
(1)滤尘室尺寸为:
(2)滤尘室尺寸为:
1100×
7层,装置为上下可调试,可调范围100~200mm。
4.2.3栈桥微环
栈桥微环装置尺寸为1000×
600×
δ4,材料Q235。
4.2.4释缓装置
二(三)次释缓装置尺寸为1500×
2000×
δ4组套件,材料Q235。
4.3技术服务与承诺
4.3.1免费现场培训
免费现场培训自控系统运行管理维护和保养、主体设备运行管理维护和保养操作工。
4.3.2承诺
XC-4型系列微动力除尘器投入运行后确保任何带速、温度的条件下运行可靠。
(1)主体设备多功能除尘装置可靠性100%。
(2)除尘器投入运行后,除尘设备处于微压状态。
(3)机头测控系统自动投放准确率大于98%。
(4)现场粉尘浓度指标达到国家标准要求。
(5)施工周期为2~3月,施工期间不影响焦槽正常作业。
4.4除尘技术说明
4.4.1优点
全微动力除尘技术具有无占地、投资少、动力消耗小、维护量小,无须人工操作、无二次污染等优点。
4.4.2不足
在本工程运用上,具有以下不足:
根据焦槽物料的特点,筛下碎焦返回其它流程使用,成焦进入高炉冶炼。
全微动力除尘技术收集下的粉尘,落入皮带运输机,随物料运走。
成焦直接进入高炉冶炼,粉尘落入皮带运输机带入高炉,会增加高炉的负荷。
4.4.3解决方法
在槽下,将成焦系统捕集到的粉尘排入碎焦皮带运输机,进入下一使用流程。
在成焦和成矿转运点,捕集到的粉尘无法返回碎焦皮带运输机,将此除尘点并入矿槽除尘系统。
为避免增加矿槽除尘系统的负荷,可以用替换的方式,在矿槽除尘系统进行6个点的全微动力除尘。
4.5工程进度
微动力除尘分为两期,一期为移动小车除尘一套,焦槽顶部除尘、振动筛除尘各两套,筛下成焦和碎焦各五套。
共15个除尘点。
二期除尘包括焦槽顶部除尘、振动筛除尘各三套,碎焦转运共五套,焦槽平台落尘1点,替换矿槽除尘6点。
共18个除尘点。
具备施工条件后,2个月完成施工,交付使用。
4.6工程资金计划
施工设备进厂之后,在开工前,支付工程费的40%;
工程完工验收合格后,支付工程费的50%;
预留10%的质保金,一年后支付。
5公辅设施
5.1总图布置
采用微动力除尘工艺,除尘罩及除尘器均布置在落尘点,没有管道等引出,也无除尘器、风机、烟尘等引出厂房,不增加占地面积。
5.2供排水
采用微动力除尘方案,为了解决特殊物料在极干燥的条件下所采用的雾化降尘,每个除尘点消耗新水为0.05m3/h。
碎焦返回烧结工艺,可以采用雾化降尘;
成焦直接进入高炉冶炼,不能带入水分,不能采用雾化降尘工艺。
焦槽车间除尘点为33点,焦槽除尘碎焦点为11点,最大消耗新水为0.55m3/h。
5.3供电
采用微动力除尘方案,无高压供电设备,除尘系统装机容量为87.4kW,电耗23.54×
104kWh/a。
5.4自动控制
本项目除尘可沿用炼铁厂工业以太网系统系统,在原有皮带运输机控制室内相应的控制系统上增加I/O模块。
对CPU进行远程编程。
通过连接于计算机的网卡或调制解调器,有可能上局域网或Internet网。
脉冲负压吸尘器的电机,与皮带输送机连锁,以实现自动化控制。
5.5建筑结构
采用微动力除尘方案则无建筑结构等。
6投资估算
6.1投资范围
昆明钢铁股份有限公司炼铁厂XX高炉焦槽除尘工程地点为昆钢炼铁厂。
投资估算的范围主要包括XX高炉焦槽系统除尘工艺、供配电、给排水和总图运输等和工程建设所需的费用。
6.2编制依据
(1)按生产工艺配置,生产性投资原则上不留缺口,以项目综合配套的实物工程量为计算依据。
(2)建筑安装工程:
采用云南省建筑安装工程综合预算定额及费用标准,部分参照类似工程指标并加以调整;
(3)设备价格:
主要设备为询价,其它设备价格按2007年《机电产品价格汇编》,不足部分采用类似工程订货价或合同价以及从厂家直接询价;
(4)设计费按《工程勘察设计收费标准》(2002年修订本)计取;
(5)其它费用按实际需要参照规定计列;
(6)设备基本为厂家实价,工期为0.2~0.6年,基本预备费按直接工程费与其它费用之和的3%计列。
6.3建设投资估算
经概算,项目建设投资为:
918.41万元。
按其投资构成划分的投资分析见表6-1,按其投资用途投资划分的投资分析见表6-2。
总投资估算详见表6-3,设备概算见表6-4。
6.4设投资估算
生产主要考虑因素为:
电耗、水耗和人员工资。
不增加人员。
生产成本:
8.33万元/a。
其中水耗:
2.67