整理压力容器作业工艺指导书Word格式.docx
《整理压力容器作业工艺指导书Word格式.docx》由会员分享,可在线阅读,更多相关《整理压力容器作业工艺指导书Word格式.docx(199页珍藏版)》请在冰豆网上搜索。
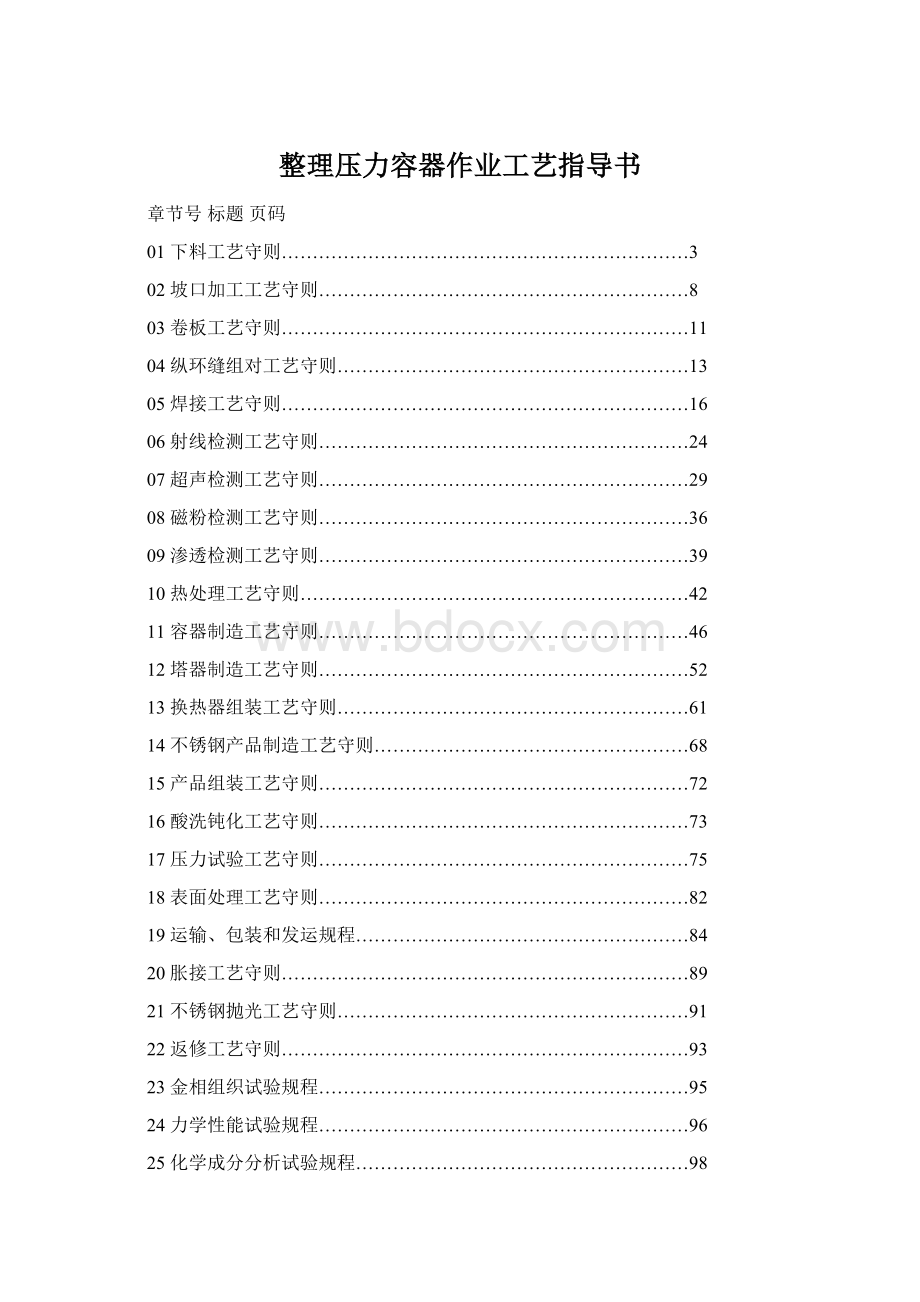
39产品试件工艺守则……………………………………………………139
40焊接工艺评定试件守则………………………………………………142
41低温压力容器制造……………………………………………………144
压力容器作业(工艺)指导书
版本:
B
修改码:
第1页共5页
编号:
第1章
下料工艺守则
标题
1.材料
1.1.1采购部负责供给符合设计图纸、工艺文件要求的合格材料,施工人员领料时应复核以下内容
1.材料标记(钢号、炉批号、复验号)、规格及数量;
2.材料表面质量:
无机械损伤,无严重锈蚀等;
3.如要求进行逐张超探或冲击试验的,其检测报告。
2.排版
对于设备需自己加工的封头、筒体、变径段、裙座以及结构复杂的配件等应进行排版。
具体如下:
2.1根据图样及实际材料规格进行排版。
2.2除图样有特殊规定外,通常按一下规定进行排版:
a.壳体的最短筒节长度不小于300mm;
b.同一筒节纵缝应相互平行,相邻焊缝间距的弧长应不小于500mm;
c.相邻筒节A类接头焊缝中心线外圆弧长以及封头A类焊缝中心线与相邻筒节A类焊缝中心线间外圆弧长应大于钢材厚度δs的3倍,且不小于100mm;
d.排版时焊缝位置应尽量避开开孔位置,容器内件焊缝边缘应避开壳体的纵环缝;
e.卧式容器下部140°
范围内不应设置纵焊缝;
f.封头由瓣片和顶圆板拼接制成时,焊缝方向只允许是径向和环向的,封头各种不相交的拼缝中心线间距离至少应为钢材厚度δs的3倍,且不小于100mm,如图1-1:
h.球壳瓣片最小宽度不小于500mm;
i.筒节展开周长按中径计算
第2页共5页
L=π(Di+δn)-△L+H
Di——圆筒的内直径;
δn——钢板的名义厚度;
△L——钢板的伸长量;
H——焊缝收缩量。
J.材料切割前应先进行标记移植,移植时应有检验员的确认,确保标记移植的准确性。
k.排版图应包括:
度数线、筒节中径展开长度、筒体总长、筒体件号、板规格、材质、筒节编号、筒节尺寸、焊缝编号、开孔编号、开孔中心标高及轴线的距离、收口缝位置、编制、审核、排版日期等内容。
l.排版前应考虑焊缝收缩余量。
m.对于分段出厂的设备,排版图上应标注分段处位置。
分段的基本原则:
(1)根据设备的形状特征、结构,分段线应尽量避开内件焊缝、塔壁不等厚处及材质不相同处。
(2)根据运输条件、起重能力及工艺装备的允许尺寸或合同确定分段。
3.下料划线
3.1按排版图尺寸划线,筒节划线时应留出每道焊缝处收缩量,可参考下表1-1预留焊缝收缩量。
钢板厚度
4~6
8~10
12~18
20~26
28~34
34~50
每道焊缝收缩量
0.5
1
1.5
2
3
3.5
表1-1单位:
mm
3.2划线时板料的标记朝上,根据板料边缘的规整情况确定舍弃部分的宽度,画出切割线;
距切割线50mm画出检查用的基准线,校核对角线差,符合要求后在切割线和标准线上打上冲眼。
见图1-2.
3.3产品试板应与筒体同时下料(必须垂直于钢板的轧制方向);
且与容器用材具有相同钢号、相同规格和相同热处理状态。
第3页共5页
3.4材料标记应标注在压力容器的外壁。
3.5号料时做到线条清晰,粗细均匀,各部分线条符合完整。
并且冲眼相对线条的偏差不大于0.5mm。
3.6下料所用量、卡具应经计量定期校验,符合国家一有关标准。
3.7划线后应经自检以及检验员检查合格后方可进入下道工序。
3.8与封头相邻筒节的下料周长按封头实测周长。
3.9对直筒体划线,应确保交接边线垂直,其展开长度偏差、宽度公差和对角线差公差详细见表1-2.
筒节直径
<
800
800-1200
1300-2400
>
2400
长度偏差
2.5
宽度偏差
对角线差
表1-2单位:
3.10在板料上标明产品编号、件号、筒节排版编号、展开长度、宽、厚、坡口型式,详细见图1-3。
3.11分瓣封头、椎体号料时,瓣片周边留50mm切割余量,同时在小口号出吊耳。
3.12瓣片冲压成型检查合格后,划加工切割线,要求有基准线的也在外圆上同时号出。
3.13椭圆形封头、球形封头、锥形封头根据其直径采用整体或分瓣下料。
3.14椭圆整体封头板坯直径公式1-1.
Dp=1.2(Di+δn)+2h(式1-1)
Dp——板坯直径Di——封头内径
h——封头直径高δn——封头坯料厚度
注:
椭圆封头坯料下料尺寸参考封头压制厂提供的尺寸划线。
第4页共5页
4.补强圈下料
4.1补强圈的材料一般与壳体材料相同,并应符合相应材料标准的规定。
4.2补强圈可采用整版或径向分块下料。
径向分块下料的补强圈,只允许整体补强圈无法安装的场合,拼接焊妥后焊缝表面应修磨光滑并与补强圈母材齐平,并按JB/T4730-2500进行超声检测,Ⅱ级合格。
4.3补强圈须设有M10信号孔,分瓣补强圈每瓣应设信号孔。
4.4标准补强圈的尺寸见表1-3
接管公称直径
补强圈外径
补强圈内径
50
130
按补强圈焊接接头的要求采用下面的相应坡口型式:
A型—适用于壳体为内坡口的填角焊结构;
B型—适用于壳体为内坡口的局部焊透结构;
C型—适用于壳体为外坡口的全焊透结构;
D型—适用于壳体为内坡口的全焊透结构;
E型—适用于壳体为内坡口的全焊透结构。
65
160
80
180
100
200
125
250
150
300
175
350
400
225
440
480
550
620
680
450
760
500
840
600
980
1、表中的补强圈外径为成型后的尺寸;
2、表中的补强圈尺寸为成型后的投影尺寸,当弧长与弦长之差大于8mm时,具体下料尺寸应经放样,补强圈应周边等宽。
表1-3
补强圈坡口型式见下图:
第5页共5页
图1-4
D1——补强圈内径,mm
do——接管外径,mm
δc——补强圈厚度,mm
5.接管下料
按计算最长端长度+10mm。
6.材料标记
6.1允许打钢印的(低应力)应有钢印,位置按QY/QB05-02.04《材料、零部件控制程序》的规定;
不允许打钢印(如低温设备、有防腐要求的不锈钢)的材料,不得打材料钢印;
复合钢板制容器,不得在防腐蚀面采用硬印作为材料的确认标记。
1.复合板的复合层可用记号笔作材料标记,基层外侧按材料标记的一般规定;
2.对有防腐要求的不锈钢,可用记号笔作标记;
3.低温设备用油漆作。
编制
审核
审批
第1页共3页
第2章
坡口加工工艺守则
1.通用要求
1.1操作前首先弄清板面上的各种符号、线条含义,按加工件的规格、材质选择适当的工艺参数;
1.2按切割线加工和检查,原则上留半个冲眼,加工后的公差要求设计工艺文件和本守则的规定,自由尺寸公差一般按GB/T1804-2000《一般公差未注公差的线性和角度尺寸的公差》规定的m级精度;
1.3操作及吊运过程中要防止工件磕碰、划伤,禁止违章作业,确保人身和设备安全;
1.4复合板和不锈钢材料在加工过程中要做好表面的防护工作;
1.5本工艺适用于气割、剪切、刨边工序的质量控制,而不是产品的最终质量标准。
2.气割(机械和手工气割)
2.1气割工件上的材料标记应符合材料、零部件控制程序中的规定,并有确认钢印;
2.2正确执行设计工艺文件规定,凡要求预热后气割的工件,应采用试温笔或表面温度计测定预热温度,并使之达到规定要求。
a.可以用割炬中性焰,均匀加热工作;
b.预热温度一般控制在100℃左右。
2.3对要求预热后气割的工作,当气割环境温度低于5℃时,气割后缓冷。
a.可以用割炬中性焰,均匀加热气割面,逐渐降温;
b.可以用保温材料覆盖切割面区域以保温缓冷。
2.4对于能满足数控切割机穿孔和切割厚度的金属材料均采用数控切割机切割,同时采用手工切割辅助剪切下料。
2.5气割后相对标准线(冲眼)的偏差一般可按表2-1
板厚
≤25
25-50
手工气割
±
机械气割
0.6
表2-1
2.6切割表面的粗糙度、平面度、上缘融化程度、挂渣状态、缺陷的极限间距、直线度和垂直度等要求按JB3092-82《火焰切割面质量技术标准》的规定执行。
2.7气割面上边缘应无明显烧塌,气割面纹路粗细一致,但局部不大于1.5毫米深的沟槽存在。
2.8复合钢板时复层朝下应有基层开始切割。
3.剪切
3.1剪切工作的材料标记应符合《材料、零部件控制程序》的规定。
3.2根据工件材料、厚度调整刀口间隙,刀口间隙与剪切断面的关系如图2-1.
第2页共3页
3.3剪切时以剪切线为准;
3.4对于不刨边的筒体板除外满足表2-2中对长度偏差的规定外,其两对角线的差值不大于2mm;
3.5复合钢板剪切是,复层朝上,应注意防止表面损伤。
4.铣边
4.1根据版面上坡口标记符号及工艺文件的要求加工坡口,用焊缝量尺或板样检查。
一般钝边允许偏差±
1mm,角度偏差±
2.5°
;
4.2根据工作材质、厚度选择合理的切削速度和吃刀深度,加工面(坡口面及削薄面)不应产生挤压或鱼鳞状痕迹,且不得有裂纹、分层等缺陷;
4.3工件放到工作台上后,用画针法找正,先用螺旋千斤顶压平,然后用油压千斤顶压紧,进行刨削加工,加工后除检查坡口形状满足工艺卡所要求的形状外,还应检查长度、宽度、对角线的偏差,其偏差值要满足表2-2,坡口角度偏差为±
。
板料长度
≤2500
2500-4000
4000-7500
7500
长度偏差△A
对角线差|△L|
宽度允差△B
0.7
表2-2
第3页共3页
4.4对于碳素钢和低合金钢用刨边机最小刨边长度一般应≥500mm,对于不锈钢的最小刨边长度一般应≥150mm,对于小件刨边应有加固措施。
a.可用压板辅助压紧工作;
b.机头往返时注意适当停留防止电机过热;
c.采用降低切削速度,减小吃刀深度。
5.坡口表面要求
5.1坡口表面不得有裂纹、分层、夹紧等缺陷;
5.2标准抗压强度下限值δb>540MPa的钢材及Cr-Mo低合金钢材经火焰切割的坡口表面,应进行磁粉或渗透检测。
当无法进行磁粉或渗透检测是,应由切割工艺保证坡口质量;
5.3施焊前,应清除坡口及其母材两侧表面20mm范围内(以离坡口边缘的距离计)的氧化物、油污、熔渣及其他有害杂质。
2.6注意事项
加工前注意所有位置坡口形式是否对应工艺文件一致。
第1页共2页
第3章
卷板工艺守则
1.卷板的准备工作
1.1对板料检查,认清原材料标记,规格、件号、卷圆方向,及正反面;
1.2钢板局部凸凹、拼板焊缝角变形过大、应先校平后再卷圆;
1.3按图样或技术工艺文件要求分别备好卷圆样板,压头样板弦长不得小于300mm。
卷圆样板、卷圆检查样板按以下规定使用:
(1)当Di(筒体内直径)≤800mm是,样板的弦长不得小于300mm;
(2)当800<Di≤1500mm时样板的弦长不得小于500mm;
(3)当1500<
Di≤6000mm是,样板的弦长为1/3Dg(公称直径)且≤1500mm;
(4)当Di>
6000mm时,样板弦长为1/4Dg。
2.压头
压头长度为200-300mm,曲率与样板间隙不得大于1.5mm。
压头时预留0.5-1mm间隙以防止卷圆后端头过卷。
3.卷板
3.1卷圆前应清扫钢板表面和卷轴面;
3.2卷圆后的钢板表面应平整,压痕深度不得超过0.5mm;
3.3卷圆后圆筒两端对口处要平齐,高低差应不大于1/1000Dg,且不得超过2mm;
3.4卷圆后用样板检查筒节曲率与样板间隙△e如图3-1,允许值如表3-1所示。
筒体直径φ
允许间隙△e
800-1800
1800
第2页共2页
3.5对于分片交货的卷圆要求:
1.对分片交货的单节,按以上要求先进行卷圆;
2.将卷完圆的单节筒体立于一水平平台上,用卷圆样板检查曲率直径,样板与筒体单节间的间隙允许差同表3-1。
4.小口直径>
500mm的异径圆筒用卷板机卷制
4.1在钢板上按放射线法等分划线;
4.2压制钢板端头,宽度为200-300mm,曲率误差照图3-1、表3-1要求,可在压制机上压制,也可在卷板机上加胎具压头。
4.3把钢板放进卷板机内,为了在卷板过程中钢板不因斜窜而破坏卷板机头,可紧靠钢板的小口边加挡块;
4.4微量升起大口段的上卷轴,压低小口端的上卷轴,试卷一次;
4.5用样板测量试样,逐步调整大小口差度与两样板之差度相等,即可相等压进两端丝杠,每卷一次即用样板卡量一次。
根据卡量的情况,再调整两端丝杠旋进的程度,卷完之后自上卷轴将异径筒取出。
5.注意事项
卷圆时要注意卷圆方向,保证坡口内外方向正确。
第4章
纵环缝组对
1.焊缝组对
1.1按照埋弧焊为0-1mm,手工焊为2-3mm的要求调整好对口间隙,从对口中间往两端点焊;
1.2筒节两端面平整,若由于下料刨边产生的误差,允许高低差<
D/1000,且<
2mm;
1.3对口错边量按下表4-1:
对口处钢材厚度δs
按焊接接头类别划分对口错边量
A类
B类
≤12
≤1/4δs
12<
δs≤20
≤3
20<
δs≤40
≤5
40<
δs≤50
≤1/8δs
≤1/16δs且≤10
≤1/8δs且≤20
复合钢板
≤50%且≤2(为复层厚度)
表4-1
球形封头与圆筒连接的环向接头以及嵌入式接管与圆筒或封头对接连接的A类接头,按B类焊缝接头的对口错边量要求。
1.4在焊接接头环向形成的棱角度E,用现场等于1/6内径Di,且不小于300mm的内样板或外样检查(见图4-1),E值不得大于(δs10+1mm),且不大于5mm;
在焊接接头轴向形成的棱角度E,用长度不小于300mm直尺检查,E值不得大于(δs/10+1mm),且不大于5mm。
1.5产品试件必须在纵环缝的延长部位与单节同时施焊;
1.6为防止焊接变形,纵缝焊接前可在焊缝内侧或外侧点焊弧形板。
对于直径大于2000mm的筒节,应在每个筒节的两端进行适当加固;
1.7筒节施焊后,应按4.1.4条要求检查焊缝棱角度,其值不得大于(δs/10+2)mm,同时检查筒节的圆度e,应不得大于该断面设计内径Di的1%,否则应校圆。
1.8校圆
(1)加载:
将卷板机的上、下辊调到所需的最大校正曲率的位置;
(2)滚圆:
使筒体在校正曲率下滚卷1-2圈,(着重滚卷焊缝区附近)使整圆曲率均匀一致;
(3)卸载:
逐渐卸除载荷,使筒节在逐渐减少的校正载荷下多次滚卷。
1.9按照排版图在每个筒节外壁划出相隔90°
的四条纵向方位母线并打上冲眼作为标记。
2.环缝组对
2.1环缝组对一般采用卧装法,但对直径大、壁板薄的筒体可以采用倒装法;
2.2卧装法组对筒体时,按照排版图及工艺卡要求的组对间隙按筒体的序号及上、下心进行组对。
组对前应测量筒节的周长,相邻筒节的周长之差不大于πb(b为允许错边量),复合钢板应测量内周长,以保证环缝对口错边量符合要求;
2.3两板厚相等时,错边量应符合表4-1中B类焊缝规定;
2.4板厚不相等时,当薄板厚度≤10mm,两板厚度差超过3mm,或当薄板厚度>
10mm,两板厚度差大于薄板厚度的30%,或超过5mm,均应按GB150-1998图10-8的要求单面或双面削薄厚板边缘,或按同样要求采用堆焊方法将薄板边缘焊成斜面。
当两板厚度差小于上述数值时,则按第4.2.3条要求,且b值以较薄板厚为基准确定。
在测量对口错边量b时,不应计入两板厚度的差值;
2.5承受内压的筒体组对圆度偏差:
(a)筒节同一断面上最大直径与最小直径之差,应不大于改断面内径Di的1%,且不大于25mm;
(b)当被检端面位于开孔中心一倍开孔内径范围内时,则该断面最大最小内径差应不大于该断面内径Di的1%与开孔内径的2%之和,且不大于25mm。
2.6承受外压及真空容器的筒体组对圆度偏差:
按GB150-198中10.2.4.11规定;
2.7换热器壳程的筒体组对对圆度偏差见换热器组装工艺守则。
2.8筒体组对时,通过中心线的水平和垂直面,即沿圆周0°
、90°
、180°
、270°
四个部位拉φ0.5细钢丝测量筒体的直线度。
直立容器的直线度允许差应符合表4-2要求,卧式容器筒体直线度允差L/1000mm。
筒体长度(mm)
直线度允差(mm)
L≤15000
L/1000
L>
15000
0.5L/1000+8
表4-2
测量筒体直线度时,应避开纵环缝100mm,测量计算筒体直线度时,应减去板厚度差值。
第1页共8页
第5章
焊接工艺守则
1.总则
本工艺守则适用于我厂采用手工电弧焊、埋弧焊、钨极氩弧焊工艺的各类钢制压力容器的焊接。
2.焊工
2.1焊工必须按《锅炉压力容器管道焊工考试和管理规则》进行考试并取得焊工合格证,方能在有效期内从事合格项目的焊接工作;
2.2焊接前焊工必须了解所焊件的钢种、焊接材料、焊接工艺要点;
2.3焊工应对施焊后的焊缝作出标识,按QY/QB06-02.07《焊接控制程序》规定打上有效持证施焊焊工的钢印,钢印清晰可见,深度不超过0.3mm;
不锈钢及低温钢制压力容器不允许打钢印时在排版图上注明。
3.焊接方法
3.1下列焊缝一般采用埋弧焊
1.10≤δ≤60mm的拼接焊缝;
2.直径φ≥1000mm且δ≥10mm的A、B缝、外口;
600mm≤直径φ<
1000mm的A、B缝外口;
3.2下列焊缝一般采用手工焊
1.直径φ≥1000mm且δ≤10mm的A、B缝、外口;
2.600mm≤直径φ<
1000mm的A、B缝内口;