OiD联机调试说明文档格式.docx
《OiD联机调试说明文档格式.docx》由会员分享,可在线阅读,更多相关《OiD联机调试说明文档格式.docx(16页珍藏版)》请在冰豆网上搜索。
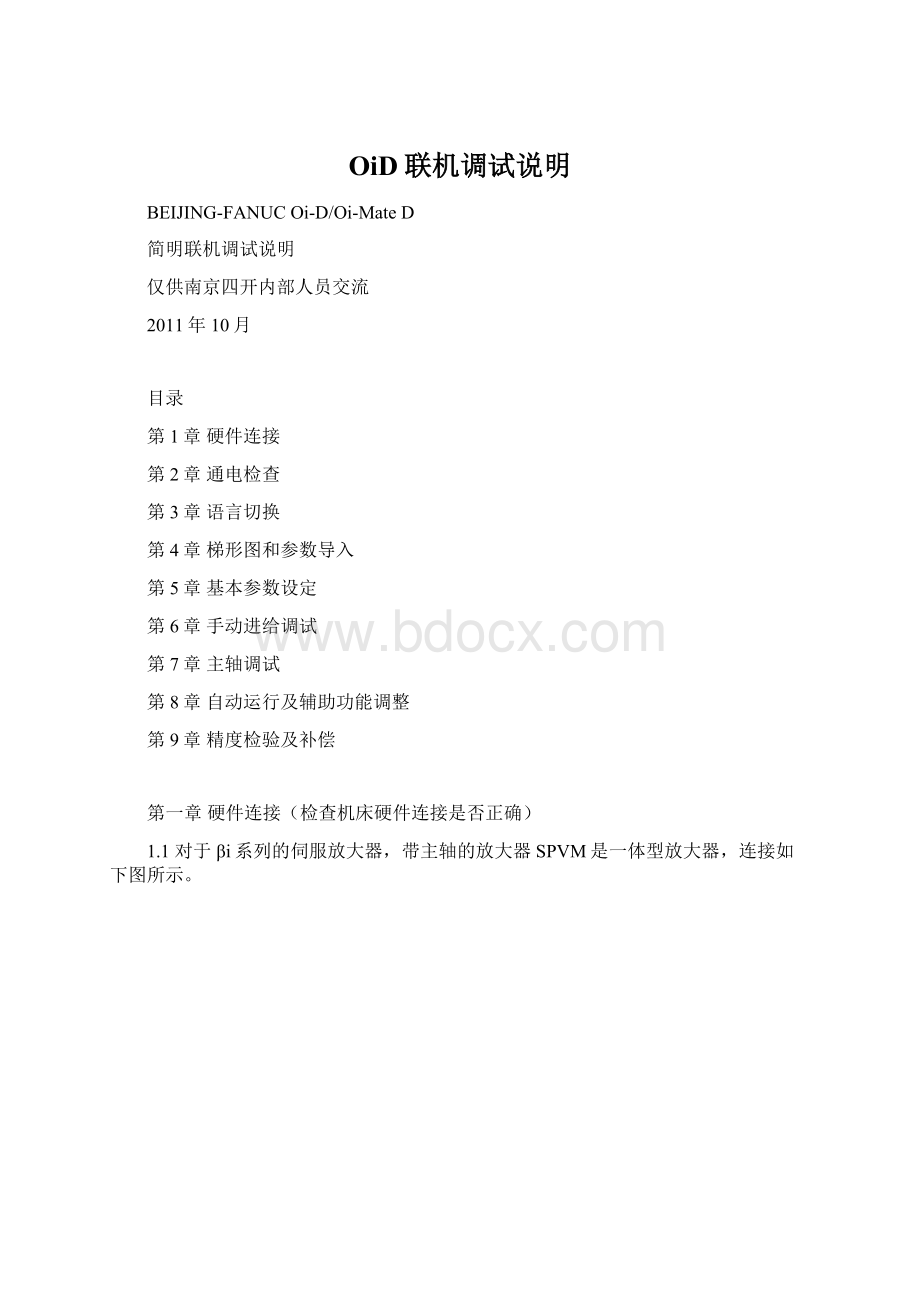
5、TB2和TB1不要接错,TB2(左侧)为主轴电机动力线,而TB1(右端)为三相200V输入端。
1.2操作面板连接
1.2.1系统操作头+MDI面板连接
系统头和MDI面板都是一体的,如下图
1、FSSB光缆一般接左边的插口;
2、风扇、电池、软键、MDI等在系统出厂时已经接好,不要改动。
但可以检查是否松动;
3、电源线插座(CP1),需外部供24V电源,注意正负极性;
4、RS232接口和电脑接口的连接,有两个,若不用,可不接(使用存储卡可以代替232口,且传输速度和安全性都要比232口优越);
5、串行主轴连接,JA41连到SVPM中的JA7B;
6、对于I/O(JD51A)是连接到I/O模块中的JA51B;
7、存储卡插槽(系统的正面),用于连接存储卡,可以对参数、程序、梯形图等数据进行输入/输出操作,也可以进行DNC加工,但是要CF卡和PCMIC(PCCARDADAPTER)才能连接,CF卡容量不超过2G。
1.2.2机床操作面板连接
1、面板背面PLUG1与I/O单元中CB107连接;
2、面板背面A,B,5V,0V要与I/O中JA3连接;
3、系统电源启动和关闭接POWERON和POWEROFF。
1.3I/O单元的连接
1、CP1接24V电源;
2、CB105接外部50位I/O端子;
3、JA3接手轮编码信号;
4、JD51B与系统连接。
1.4其他
其他未说明的按照图纸接线,和图纸不符以图纸为准。
第二章通电检查(检查供电电压正常后,机床上电,系统上电。
)
1、按照电气设计图,通电前,断开所有断路器,逐一检查各个节点电源是否正常。
主要检查24V供电回路,主轴和伺服的220V电源供电回路。
如发生异常,及时断电后排除故障,查清原因;
原因不清,不应再次盲目通电。
2、按照顺序,逐一通电
按照先系统、后I/O接口,先伺服和主轴,后强电的通电顺序逐一通电,如发现异常后,立即断电检查,排除故障。
3、24V驱动电源的连接确认
确认系统、I/O设备的电源指示灯是否点亮。
压下紧急停止按钮,按操作面板上的系统启动键
,启动系统。
对所有的I/O是否被系统识别,可通过下列操作确认;
【SYSTEM】→右扩展两次→【PMCMNT】→【I/OLNK】,有几组I/O设备就在IOLINK画面显示几行。
第三章语言切换(系统启动完成后,先进行语言转换)
对于Oi-D系统,语言切换时无需断电重启,即可生效。
如需语言切换,可进行如下操作;
【SYSTEM】→【OFS/SET】→右扩展几次→【LANGUAGE】→用光标选择语言→【OPRT】
(操作)→【APPLY】
(确定)。
也可以通过参数3281改成15为中文(简体字)。
第4章梯形图和参数导入
1、准备工作
在导入梯形图之前,必须先进行相关的PMC参数设定,使用左右光标操作将“编辑器功能有效”置为“是”状态,否则无法导入梯形图,操作如下:
【SYSTEM】→右扩展两次→【PMCCNF】→【设定】:
用CF卡传输的通道设置(参数0020设置为4),或者在以下界面修改I/O通道。
【OFS/SET】→【设定】
2、梯形图的导入
对于梯形图的创建和编辑,建议使用计算机进行,将编辑好的梯形图(注意梯形图的类型和系统的匹配)编译后转换为卡格式,通过存储卡装入系统,操作如下:
【SYSTEM】→右扩展两次→【PMCMNT】→【I/O】→【列表】→【选择文件】→【执行】。
依次将顺序程序和参数写入PMC。
在系统提示传输完成之后,不得马上断电,而是继续以下操作:
执行之后,梯形图已经被载入系统,但是未写入FLASHROM,由于系统再次上电时是从FLASHROM中读取梯形图来执行扫描,因此此时需要将梯形图写入FLASHROM进行保存,在同样的界面,使用光标操作,将各项选择为如下图所示,按执行就可:
然后修改计数器17号设定为8;
【SYSTEM】→右扩展两次→【PMCMNT】→【计数器】
3、梯形图启动
导入梯形图并保存后,梯形图会处在停止状态,需要手动启动梯形图扫描,具体操作如下:
【SYSTEM】→右扩展两次→【PMCCNF】→【PMC状态】→【操作】→【启动/停止】;
可以对梯形图的扫描进行启动/停止操作。
注:
如果PMC参数设定画面中“PMC程序启动”选择为“自动”,也可直接重启系统。
1.从CF卡传输CNC系统参数、拷机程序、G代码检查程序等。
传输CNC参数:
编辑模式→【SYSTEM】→【参数】→【操作】→+→【F输入】→【执行】
传输程序:
编辑模式→【PROG】→【操作】→+右扩展→【输入出】→【F输入】→CF卡程序号→【F设定】→至系统的程序号→【O设定】→【执行】
2.赛洋面板解密,详见赛洋面板说明书的加、解密步骤部分。
a.根据赛洋面板I/O对应地址,检查所装入的梯形图需要实现对系统的基本控制逻辑,依次将赛洋面板上的各按键功能都要进行检测,例如以下功能等:
1)急停信号的控制;
2)方式模式的切换;
3)伺服切屑倍率,JOG倍率的检查;
4)手动、手轮进给执行,手轮倍率检查;
5)循环启动、进给保持信号的检查。
b.根据电路图分线器的I/O地址检测外部的输入输出信号是否正确,例如:
各轴行程、零点、松紧刀信号、刀库信号、报警灯信号等。
6.检查RS232通讯连接功能(操作步骤详见附录)
第5章基本参数设定(在第四章已经将全部CNC参数以文件形式写入系统,以下为详细的参数介绍)
1、启动准备
当系统第一次通电时,需要进行全清处理,(上电时,同时按MDI面板上RESET+DEL)。
2、基本参数设定概述
基本组
系统的基本参数设定可通过参数设定支援画面进行操作。
操作步骤:
【SYSTEM】→右扩展数次→【PRM设定】
一般的参数都有进行标准值设定,即执行【初始化】。
基本组的参数要进行【GR初期】设定。
没有标准值的参数设定:
18255000伺服位置环增益
182610各轴的到位宽度
18287000移动中位置偏差极限值
1929500停止时位置偏差极限值
主轴组
进行标准值设定后进行
3716#01主轴电机种类为串行主轴
坐标组
1320存储行程检测1的正向边界坐标值
1321存储行程检测1的负向边界坐标值
④进给速度组
14101000空运行速度
142012000快速移动速度
1421120快速移动倍率的F0速度
14232000JOG进给速度
142412000手动快速移动速度
1425300手动返回参考点的FL速度
14283000参考点返回速度
14308000最大切屑进给速度
⑤进给控制组
162040快速移动的直线型加减速时间常数
162264切屑进给的加减速时间常数
16230切屑进给插补后加减速的FL速度
162464JOG进给的加减速时间常数
16250JOG进给的指数函数型加减速的FL速度
设定完后重启CNC。
看看系统还有那些报警,根据报警有目的性设置参数。
3、伺服设定步骤
进入伺服设定画面,进行伺服初始化操作。
然后进行各项设定。
①电机代码
根据电机代码表进行设定。
②AMR设定
相当于伺服电机极数之参数,设为00000000
③指令倍乘比的设定
通常为2
④柔性齿轮比的设定2084/2085
半闭环
⑤电机回转方向设定
111从脉冲编码器看沿顺时针方向旋转
-111从脉冲编码器看沿逆时针方向旋转
⑥速度反馈脉冲数、位置反馈脉冲数设定
⑥-1半闭环
速度反馈脉冲数8192(固定值)
位置反馈脉冲数12500(固定值)
⑥-2全闭环
位置反馈脉冲数电机转一周光栅尺的反馈脉冲数
⑦参考计数器容量
⑦-1半闭环
电机每旋转一周所需的位置脉冲数
⑦-2全闭环
Z相(参考点)的间隔/检测单位
断电后重新启动NC,伺服初始化结束。
4、伺服参数设定
进行参数【初始化】,【GR初期】操作。
快移FF=0,其他都按标准值。
5、高速高精设定
进行参数【GR初期】操作。
圆弧容许加速100,拐角速度533。
6、主轴设定
设定电机型号,主轴最高转速,电机最高转速,主轴编码器种类,完成后设参数3716#0=1,3717=1,3720=4096,4019#7=1,重新启动后确认4019#7=0,然后设定4002#0=1,#1=0。
7、其他
参数8131#0=1手轮有效;
7113=100,手轮倍率;
3003#0,#2,#3=1,设定各轴互锁。
第六章手动进给调试
参数调试完成后,在JOG(手动连续进给)的方式下,移动伺服轴坐标,调整手动倍率开关,确认梯形图的正确与否,主要观察如下内容:
1)轴坐标按钮、方式选择、轴移动方向是否正确;
将联轴器紧固。
2)调整手动进给倍率旋钮,确认进给速度是否正确、实际位置增益是否和参数1825中设定值一致,若不一致,检查位置脉冲数2024的设定、电流百分比要在50%以内;
3)电机移动过程中,机床是否有震动现象,如果震动,可降低1825或者2021的值,如果在启动/停止时震动,可以改变加减速时间类型,同时适当增加时间常数,如果机床在某一特定区域有震动,而通过降低各环路增益无法降低,很可能是由机械引起的,可以用伺服调整软件进行对机械共振点的滤除;
4)手动快速进给操作,检查梯形图中各相关信号的状态以及相关参数;
5)检查多次手动返回参考点的操作,如果返回参考点位置不固定,检查1821(参考计数器容量)的设定,或者检查挡块位置;
6)在零点位置确认后,行走各轴,确认硬件限位后,设定软件限位.。
写入参数1320/1321
7)方式选择为手轮操作,检查梯形图和相关参数;
8)使用伺服调整软件调整伺服特性。
在MDI方式下,进行手动编程设定主轴一个转速,然后执行。
然后在主轴调整界面下观察主轴转速显示是否正常,负载比等。
转动主轴倍率旋钮,观察转速变化。
然后在JOG或者手轮方式下,按面板上的主轴正转按钮,观察主轴的旋转方向。
1)自动运行信号的调整
在自动运行方式下,检查梯形图SKB、DRN、BDT、AFL、MLK、M01、SRN及Z.LOCK等信号的运行,在MDI/自动方式下能够编辑程序,检查程序编辑开关(参数3203)是否有效。
2)G00快速运行
在G00快速运行时,确认是否有冲击,快速停止时,观察伺服误差是否有反向现象,若有可适当增大1620的值。
3)G01切屑进给
以实际加工的速度进行试验,在自动方式下,进给倍率是否有效,操作是否正常,稳定运行时,观察伺服误差的波动,要求在1左右,停止时,是否存在伺服误差反向的现象,若有可以适当增大1622的值。
4)用伺服调整软件调整伺服环增益
5)根据需要加工一个零件或者钢件,检验机床精度和刚性。
6)编制程序检验机床加工需要的各项功能。
如:
G代码、手轮偏置、程序再启动等。
手轮偏置:
在MEM(记忆)模式→加工一段时间后,需要将Z轴位置调整→程序暂停→面板右下角F2(灯亮)→用手轮调整Z轴(机械坐标/相对坐标有变化,绝对坐标不变)→F2(灯灭)→程序启动,继续加工。
程序再启动
加工程序未执行完,而因某种原因中断以后,可以进行程序再启动,从程序中断的位置继续执行。
程序再启动分为P型和Q型两种情况:
在MEM(记忆)模式→程序暂停→手动(JOG)模式下(调整坐标或者更换刀片后)→MEM(记忆)→面板R.PRG(灯亮)→【PROG】→记录程序号Nxx或Bxx→【操作】→+(扩展)→输入Nxx或Bxx→【P-型】或【Q-型】→再启动闪烁→面板R.PRG(灯灭)→检查剩余移动量,确认位置是否正确→程序启动,继续加工。
(显示屏坐上角的BC后面的数字为程序中断时执行完的实际行数,右上角的N后面的数字为程序中断时执行完的程序行的行号。
检查画面的重启动信息,如有M、T、S、B代码,在MDI方式下执行这些代码。
检查剩余移动量是否正确,并确认刀具在移动到重新开始加工位置时是否可能发生碰撞。
按下循环启动键,刀具将按空运行速度一个一个轴的移动到重新开始加工的位置,然后重新开始加工。
第9章精度检验与补偿(机床精度检测与补偿,激光干涉仪)
1、背隙补偿
对应参数1851切屑进给时各轴背隙
1852快速移动时各轴背隙
2、螺距误差补偿
对应参数11350#5=1对应螺补号前显示轴名称
3620各轴参考点螺距误差补偿号码
3621各轴最靠近负侧的螺距误差补偿号码
3622各轴最靠近正侧的螺距误差补偿号码
3623各轴螺距误差补偿倍率
3624各轴螺距误差补偿点的间隔
南京四开·
技术部
2011年10月