偏心曲轴零件加工和分析Word文档下载推荐.docx
《偏心曲轴零件加工和分析Word文档下载推荐.docx》由会员分享,可在线阅读,更多相关《偏心曲轴零件加工和分析Word文档下载推荐.docx(20页珍藏版)》请在冰豆网上搜索。
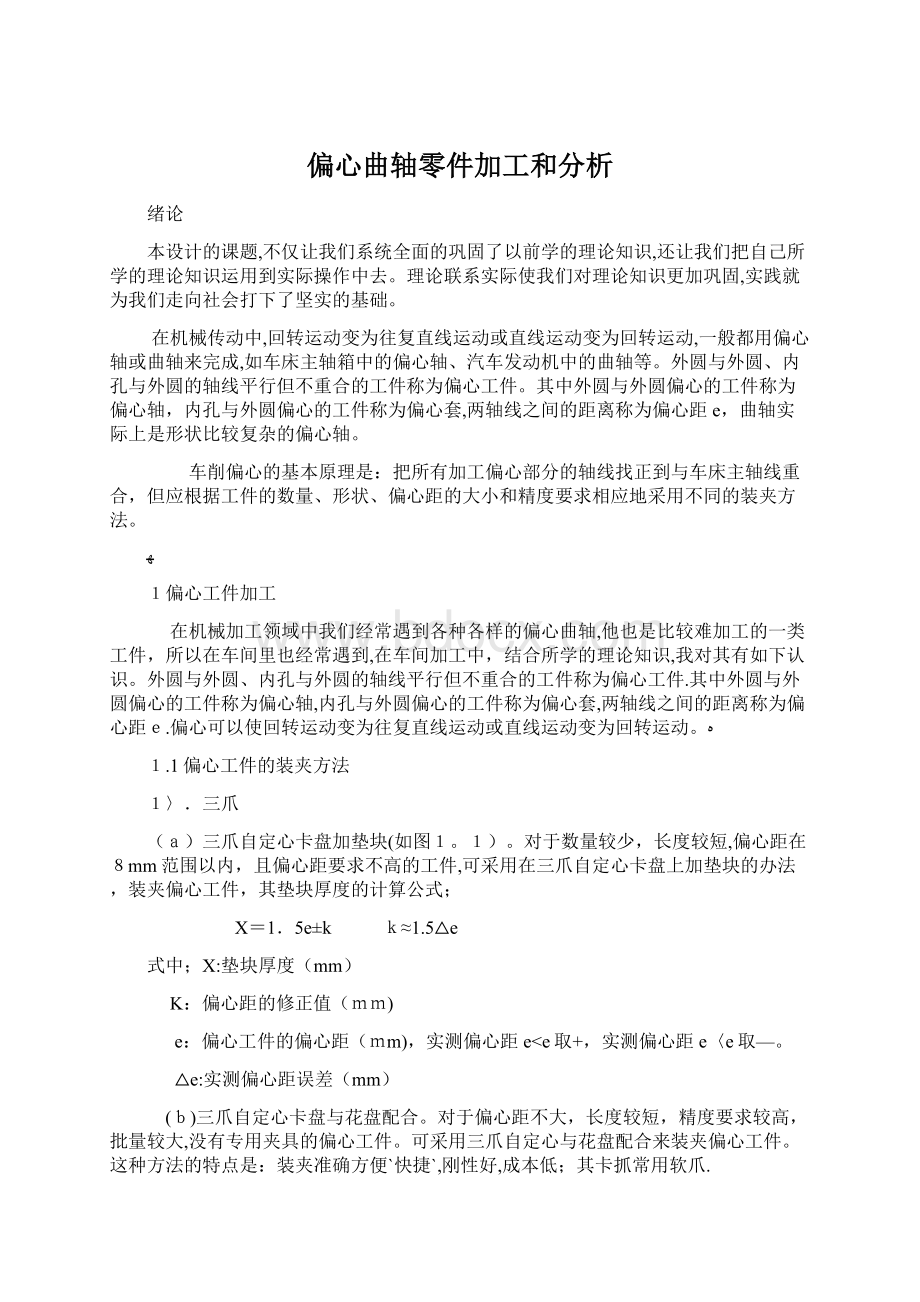
这种方法装卸方便迅速,但刚性较差.(如图1.2)
如偏心轴的偏心距很小,可采用加长毛坯再切去中心孔的加工方法。
。
图1.2
两顶尖装夹
3〉.专用夹具(如图1.3).
对于数量较多、偏心距精度要求较高的短偏心工件,可以采用专用夹具来装夹。
夹具中预先加工一个偏心孔,偏心距等于工件的偏心距,工件就插在夹具的偏心孔中,并把偏心夹具的较薄处铣开一条槽,依靠狭槽部位的弹性变形来夹紧工件,也可以用螺栓螺钉装夹工件.
图1.3(a)偏心套工件
ﻩ
1。
2偏心工件的车削要点
在偏心工件的加工过程中,我们应该注意以下要点。
(1.)适当加平衡块,保持车削平衡。
(2。
)夹紧部分应加垫铜皮,保护工件并增加夹紧力。
(3。
)对于不完整的圆弧形(扇形块)工件,应尽量成对装夹,使之对称平衡,便于测量。
(4.)调整车床主轴轴承、床鞍、中(小)滑板的间隙,提高车削刚度.
(5.)开始车削时,因偏心工件为继续切削,车刀应从偏心工件的最高点逐步进刀,进给量要选择恰当,以避免车刀头崩裂或工件位移.
(6.)进给量的选用,应根据偏心距的大小和平衡重量而定,偏心距大,重量大,进给量要小;
反之则可以略大一些.
(7.)对于偏心工件的车削,应分粗、精车削。
精车削前,偏心工件应注意重新进行找正和夹紧,以保证质量达到图样要求。
1.3偏心工件质量分析
偏心工件质量分析
废品种类
产生原因
预防方法
偏心距不正确
(1)划线及钻中心孔有误差
(2)用三爪自定心卡盘加垫快车削时,计算误差或垫块变形。
(3)找正偏心距方法不当
(4)工件没夹紧或装夹方法不当
(5)车削细长偏心工件时,顶尖支撑时的松紧程度不合适,使工件的回转轴线跳动或弯曲,导致主轴线与偏心工件轴线误差。
(6)测量方法不正确。
(1)
(1)减小划线及钻中心孔的误差
(2)复查计算过程;
通过热处理,提高垫块的硬度,减小变形
(3)反复找正偏心距,夹紧时力度适当
(4)根据偏心工件的特点,选择合适的装夹方法
(5)装夹时顶尖顶力适当,不宜过松或过紧,在找正偏心距的同时,要保证工件的上母线和侧母线与主轴平行.
(6)正确掌握测量方法
主轴轴线与偏心件轴线不平行
(1)画线或钻中心孔误差过大
(2)顶尖顶的过紧,使工件回转轴线弯曲,导致主轴线与偏心轴轴线的平行度误差过大
(3)切削力和切削温度影响,使工件产生弯曲变形,造成偏心工件轴线的平行度误差过大
(7)减小划线及钻中心孔的误差
(8)调整好顶尖的松紧度
(9)分粗、精车削进行,选择合理的车刀角度,浇注切削液
偏心轴端面的圆度误差过大
(1)车削时,偏心工件静平衡差异产生离心力,导致工件回转轴线弯曲,使工件外圆各处车削深度不等,从而使工件外圆出现圆度误差,静平衡差异越大,则圆度误差越大
(2)车床本身精度低,间隙太大
(3)车削速度越高,离心力越大,工件变形越严重。
(1)正确钻好中心孔,使两端相对应的中心孔同一轴线不歪斜,反复仔细找正工件的静平衡用两顶尖轻轻顶住使工件在任何回转位置上都静止和转动,加装和选择配重装置
(2)调整车床主轴床鞍,以及中小滑板的间隙
(3)切削速度选择适当,变化不宜过大
、
1.4曲轴
曲轴其实是形状比较复杂的偏心轴,分为双拐、三拐、四拐等等,在车床上加工曲轴时重要车削主轴颈和曲柄颈主轴颈的加工方法与一般轴类工件相似,而曲柄颈的形状特殊,刚性差,加工时首先要解决装夹问题,其次要采取措施,提高曲轴的刚性。
4。
1曲轴的装夹
(1)一夹一顶:
这种方式适用于单件、少量。
曲轴直径较大曲柄颈偏心距不大的曲轴,这种装夹方法加工曲轴颈,由于每次安装都要找正,曲轴的曲柄颈之间与主轴颈的位置精度完全由操作者技术水平来保证,因此对工人的技能要求很高
(2)两顶尖装夹(如图1.4):
这种方法定位装夹方便,曲轴的曲柄颈之间与主轴颈的位置精度,是由两端的偏心中心孔来保证。
图1.4
(3)偏心夹板装夹(如图1.5):
对于偏心距较大,无法在端面上打偏心中心孔的曲轴,可在经过加工的曲轴两端主轴颈上(直径为留有余量的工艺尺寸)安装一对偏心板并在平板上用V形架等工量具进行找正,找正后,紧固偏心板上的螺钉然后再用两顶尖装夹。
图1.5
1.4.2防止曲轴加工时变形的措施
1、采用两边传动或中间传动的机床进行加工。
以缩小扭矩。
减小曲轴的弯曲和扭矩变形。
2、尽量使用加工过程中的切削力互相抵消(多刀切割),以减少曲轴的挠曲度。
3、适当安排必要的校直工序,以避免前工序的变形影响后工序的加工。
4、防止曲轴变形的方法
(1)螺栓螺母支撑。
当两曲柄臂间距离不大时,可用螺栓螺母支撑。
(2)用木块、木棒支撑。
当两曲柄臂距离较大时,可用材质较硬的木块、木棒支撑。
(3)用压板来夹紧支撑,当曲柄臂内侧为斜面、圆弧面或元球面时,可用一对压板来夹紧曲柄臂。
(4)石膏浇注支撑
(5)特殊撑具支撑。
对于形状比较复杂的曲轴,不宜用上述支撑方法时,可应用(如图1。
6)所示的方法。
撑具主体1被螺钉2旋紧固定在曲轴上,通过撑杆3,一段旋入主体,另一端撑在曲轴臂侧面.
图1。
6
(6)中心架支撑。
曲轴长径比较大时,可以再主轴颈和曲柄颈同轴的轴颈上,直接使用中心架,以提高加工刚度,防止曲轴变形.但应防止轴颈表面被拉毛、划伤.当某个加工轴颈两侧近距离没有同轴颈可供中心架支撑拖住时,可使用中心架偏心过渡套来提高加工刚度,防止曲轴变形。
1.4。
3曲轴的平衡
曲轴是一个形状复杂的回转工件。
由于其质量中心不在回转轴上,所以在切割加工中长生了惯性力,容易引起振动,严重影响加工精度和质量。
在曲轴加工过程中,应特别注意所加平衡质量(配重)的大小及配置方位,要尽可能使曲轴回转时产生的惯性力和惯性力偶的以平衡,消除其不良影响。
2确定曲轴的加工工艺过程
2。
1曲轴的结构及其特点
毛胚图
车的主轴颈
车连杆轴颈
图2—1曲轴的结构图
曲轴一般由主轴颈,连杆轴颈、曲柄、平衡块、前端和后端等组成.一个主轴颈、一个连杆轴颈和一个曲柄组成了一个曲拐
主轴颈是曲轴的支承部分,通过主轴承支承在曲轴箱的主轴承座中.
连杆轴颈是曲轴与连杆的连接部分,在连接处用圆弧过渡,以减少应力集中。
曲柄是主轴颈和连杆轴颈的连接部分,断面为椭圆形,为了平衡惯性力,曲柄处铸有(或紧固有)平衡重块。
平衡重块用来平衡发动机不平衡的离心力矩,有时还用来平衡一部分往复惯性力,从而使曲轴旋转平稳。
2曲轴的主要技术要求分析
1)主轴颈、连杆轴颈本身的精度,即尺寸公差等级IT6,表面粗糙度Ra值为1.25~0.63μm。
轴颈长度公差等级为IT9~IT10。
轴颈的形状公差,如圆度、圆柱度控制在尺寸公差之半。
2)位置精度,包括主轴颈与连杆轴颈的平行度:
一般为100mm之内不大于0.02mm;
曲轴各主轴颈的同轴度:
小型高速曲轴为0.025mm,中大型低速曲轴为0.03~0.08mm。
3)各连杆轴颈的位置度不大于±
20′。
2.3曲轴的材料和毛坯的确定
曲轴工作时要承受很大的转矩及交变的弯曲应力,容易产生扭振、折断及轴颈磨损,因此要求用材应有较高的强度、冲击韧度、疲劳强度和耐磨性。
常用材料有:
一般曲轴为35、40、45钢或球墨铸铁QT600—2;
对于高速、重载曲轴,可采用40Cr、42Mn2V等材料。
本课题采用球墨铸铁QT600-2.
曲轴的毛坯根据批量大小、尺寸、结构及材料品种来决定。
批量较大的小型曲轴,采用模锻;
单件小批的中大型曲轴,采用自由锻造;
而对于球墨铸铁材料则采用铸造毛坯。
2.4曲轴的机械加工工艺过程
曲轴的尺寸精度、加工表面形状精度以及位置精度的要求都很高,但刚性比较差,容易产生变形,这就给曲轴的机械加工带来了很多困难,必须予以充分的重视。
曲轴需要加工的表面有:
主轴颈、连杆轴颈、键槽、φ22的外圆。
由于使用了工艺搭子,铣键槽安排在切除工艺搭子后,磨削外圆安排在保留工艺搭子前。
根据曲轴的结构特点及机械加工的要求,加工顺序大致可归纳为:
铣两端面;
车工艺搭子和钻中心孔;
粗、精车三连杆轴颈;
粗、精车各处外圆;
精磨连
杆轴颈、主轴颈和φ20、φ22外圆;
切除工艺搭子、车端面、铣键槽等。
2.5曲轴机械加工工艺路线
在进行大量的工艺分析之后,制定出大批大量生产曲轴的加工工艺路线:
(1)锻造
(2)热处理
(3)铣两端面
(4)车两端工艺搭子外圆
(5)钻主轴颈中心孔
(6)钻连杆轴颈中心孔
(7)检验
(8)粗车三个连杆轴颈
(9)精车三个连杆轴颈
(10)车工艺搭子两端面
(11)粗车各处外圆
(12)精车各处外圆
(13)检验
(14)磨削连杆轴颈外圆
(15)磨削两主轴颈
(16)磨削φ22—00。
12mm外圆
(17)磨削φ200-00。
021mm外圆
(18)检验
(19)车掉两端工艺搭子
(20)车两端面
(21)铣键槽
(22)倒角
(23)去毛刺
(24)最后检验
3曲轴的机械加工工艺过程分析
3。
1曲轴的机械加工工艺特点
三拐曲轴除了具有轴的一般加工规律外,也有它的工艺特点,主要包括形状复杂,刚性差及技术要求高,针对这些特点应采取相应的措施,分析如下:
3.1。
1形状复杂
曲轴主轴颈与连杆轴颈不在同一轴上线,偏心距有一定的尺寸要求,并且两轴有较高的位置度要求,同时主轴颈与连杆轴颈间有较大的平衡块,因此在工艺设计中应解决以下几点问题:
1)设计加工连杆轴颈的偏心夹具,即连杆轴颈与机床主轴重合,并使夹具能回转180度,加工另一连杆轴颈。
2)为消除加工时的不平衡力的产生,设计夹具时应精确设计平衡重。
2刚性差
因本曲轴长径比较大,同时具有曲拐,因此刚性较差。
曲轴在切削力及自重的作用下会产生严重的扭曲及弯曲变形,特别在单边传动的机床上加工更为严重,在工艺设计中应解决以下问题:
1)粗加工时由于切削余量大,切削力也较大,可用中间托架来增强刚性,减小变形和振动,同时机床刀具及夹具都应有较高的刚度.
2)在加工时尽量使切削力的作用相互抵消,可用前后刀架同时横向进给。
3)合理安排工位次序以减少加工变形,按先粗后精的原则安排加工工序,逐步提高精度。
4)在有可能产生变形的工序后面增设校直工序。
1.3技术要求高
曲轴技术要求较高,加工面多,需要保证的尺寸、形状、位置精度较多.因而总的工艺路线较长,精加工占有相当比例。
加工时应要解决以下问题:
1)正确分配粗加工、半精加工及精加工余量。
2)粗基准选择用曲轴两端的中心孔。
中心孔的加工以主轴颈外圆作为基准,这样能保证曲轴加工径向及轴向加工余量的均匀性.
3)精加工时仍用中心孔作为基准,但要重新修磨中心孔,避免精加工时因中心孔磨损引起加工误差。
也可一端用主轴颈定位,另一端用中心孔定位以提高刚度。
4)曲轴轴向定位以主轴颈轴肩定位,工艺设计时定位基准应尽量与设计基准一致.
3.2曲轴的机械加工工艺特点分析
ﻩ 1)该零件是三拐小型曲轴,生产批量不大,故选用中心孔定位,它是辅助基准,装夹方便,节省找正时间,又能保证三处连杆轴颈的位置精度.但轴两端的轴颈分别是20mm和φ25mm,而三处连杆轴颈中心距分布在φ32mm的圆周上,故不能直接在轴端面上钻三对中心孔。
于是,在曲轴毛坯制造时,预先铸造两端φ45mm的工艺搭子,这样就可以在工艺搭子上钻出四对中心孔,达到用中心孔定位的目的。
2)在工艺搭子端面上钻四对中心孔,先以两主轴颈为粗基准,钻好主轴颈的一对中心孔;
然后以这一对中心孔定位,以连杆轴颈为粗基准划线,再将曲轴放到回转工作台上,加工φ32mm、圆周120°
均布的三个连杆轴颈的中心孔,这样就保证了它们之间的位置精度。
ﻩ3)该零件刚性较差,应按先粗后精的原则安排加工顺序,逐步提高加工精度.对于主轴颈与连杆轴颈的加工顺序是,先加工三个连杆轴颈,然后再加工主轴颈及其他各处的外圆,这样安排可以避免一开始就降低工件刚度,减少受力变形,有利于提高曲轴加工精度。
ﻩ4)由于使用了工艺搭子,铣键槽工序安排在切除中心孔后进行,故磨外圆工序必须提前在还保留工艺搭子中心孔时进行,同时要注意防止已磨好的表面被碰伤。
3曲轴主要加工工序分析
3.3.1铣曲轴两端面,钻中心孔
本工序在钻铣车组合车床上完成,主要保证曲轴总长及中心孔的质量,若端面不平则中心钻上的两切削刃的受力不均,钻头可能引偏而折断,因此采用先面后孔的原则。
中心孔除影响曲轴质量分布外,它还是曲轴加工的重要基准贯穿整个曲轴加工始终.因而直接影响曲轴加工精度.打中心孔在本次工艺设计中因考虑设备因素,采用找出曲轴的几何中心代替质量中心。
打中心孔以毛坯的外表面作为基准,因而毛坯外表面质量好坏直接影响孔的位置误差。
3。
2曲轴主轴颈的车削
由于曲轴年产量不大,主轴颈加工采用车削,在刚度较强的普通车床上进行。
曲轴安装在前、后顶尖上线一端用大盘夹住而另一端用顶尖顶住,用硬质合金车几道工序上完成主轴颈的车削。
由于加工余大且不均匀,旋转不平衡,加工时产生冲击,因此工件要夹牢固。
车床、刀具、夹具要有足够的刚性。
主轴颈车削顺序是先精车一端主轴颈及轴肩,然后以车好的主轴颈定位。
另一侧用顶尖以中心孔定位。
车另一端主轴颈、肩及各个轴颈,半精度及精车都按此顺序进行,逐渐提高主轴颈及其他轴颈的加工精度。
3.3曲轴连杆轴颈的车削
主轴颈及其它外圆车好后,以主轴颈作为加工连杆轴颈的基准,采用专用的车夹具、车削连杆轴颈,车削同样在普通车床上进行.车削连杆轴颈需要解决的是角度定位(两连杆轴颈轴线需要控制在180度+30度或180度-30度)以及曲轴旋转的不平衡问题。
这些都由专用夹具来保证,夹具体为一对用以定位的V型块组成,装在接盘上.接盘与车床过渡接盘靠中间的定位销定位并连接,接盘在过渡接盘上靠棱形定位销可转180度,依次车削两个连杆轴颈。
V型块中心与车床主轴线距离一个曲轴半径。
车削过程中,一端与曲轴主轴颈定位并夹紧,另一端靠偏中心座夹紧,中心座上钻有中心孔,中心孔偏心距同样为一个曲轴半径。
用顶尖顶紧中心孔,这样就能保证连杆轴颈轴线与车床主轴线一致。
安装夹具体的接盘上有平衡块,消除曲轴旋转时不平衡力矩的生.曲轴加工时由于受到离心力和两顶尖的轴向压紧偏心力的作用,容易发生弯曲变形,为了加强工件刚度,用撑杆来撑住另一个曲拐的开移。
车削连杆轴颈时为了使切削力不致于太大,每次车削余量控制在1~1。
5mm内,同时车床旋转不能太高,刀具采用高速钢。
3.3.4键槽加工
这个键槽主要用于飞轮,加工此键槽应安排在主轴颈精车工序之后,这样能保证定位精度及控制键槽的深度以及对称度。
键槽加工是以两主轴颈定位,同样用专用夹具在普通铣床上进行.
3.5轴颈的磨削
由于主轴颈及连杆轴颈精度较高,尺寸精度为IT6级,表面粗糙度1.6~0.8μm,并且具有较高的形状精度及位置精度。
因此主轴颈与连杆轴颈精车后要进行磨削,以提高精度表面粗糙度.
在工艺设计中,首先磨主轴颈然后磨连杆轴颈。
中间主轴颈磨好后才能磨其余轴颈,磨主轴颈和连杆轴颈的安装方法基本上与车轴颈相同,磨主轴颈是以中心孔定位,在外圆磨床上进行,磨连杆轴颈则以经过精磨的两端主轴颈定位,以保证与主轴颈的轴线距离及平行度要求,磨连杆轴颈是在曲轴磨床上进行的。
由于轴颈宽度不大,采用横向进给磨削法,生产率较高,磨轮的外形需仔细地修整,因为直接影响轴颈与圆角的形状,磨削余量根据车削后的精度而定,粗磨余量值每边0.2~0。
3mm,精磨余量控制在0.1~0.15mm内.
在横向进给磨削中,磨轮对工件的压力很大,为避免曲轴弯曲,采用可以调节的中心架,否则就不能去掉上道工序留下的弯曲度,最好待这个轴颈的摆差减小才开始使用中心架.
磨削主轴颈时应把两顶尖孔倒角处抹干净,去砂粒及油泥,确保加工基准--中心孔的精度,磨削工序之前必须修研中心孔.
4机械加工余量、工序尺寸及公差的确定
1曲轴主要加工表面的工序安排
曲轴的主要加工表面为主轴颈、连杆轴颈、各外圆;
次要加工表面为两端面、键槽.此外,还有检验、清洗、去毛刺等工序。
连杆各主要表面的工序安排如下:
(1)、主轴颈:
粗车、精车、磨削;
(2)、连杆轴颈:
(3)、φ220-0.12mm外圆:
(如下图所示)
(4)、φ200—0.021mm外圆:
4。
2机械加工余量、工序尺寸及公差的确定
4.2.1主轴颈工序尺寸及公差的确定
表4-1:
曲轴主轴颈的工序及公差
工序名称
工序余量
经济精度
工序尺寸及公差
铸造
φ30±
1
粗车
3.2mm
IT11
φ26.80-0。
13
精车
1.3mm
IT8
φ25.50-0。
033
磨削
0.5mm
IT6
φ25+0。
021 +0.008
4.2。
2连杆轴颈工序尺寸及公差的确定
表4-2:
曲轴连杆轴颈的工序及公差
φ28±
2.2mm
IT10
φ25.80—0.084
1.3mm
IT8
φ24.50—0.033
0.5mm
IT8
φ24-0.020 -0.053
4.2.3φ22-00。
12 mm外圆工序尺寸及公差的确定
表4—3:
曲轴φ220—0。
12mm外圆的工序及公差
3.5mm
IT11
φ24.50-0.13
2mm
φ22。
50—0。
033
IT11
φ220-0.12
4.2.4φ20-00.021mm外圆工序尺寸及公差的确定
表4—4:
曲轴φ20-0 0。
021mm外圆的工序及公差
φ26±
1
3.5mm
IT11
φ22.50-0.13
2mm
φ20.50—0.033
0。
5mm
IT7
φ20-00.021
3确定切削三要素
工序 8:
粗车三个连杆轴颈至φ25.80-0。
084.选用机床:
CA6140卧式车床。
1)被吃刀量
:
取
=1mm,
2)进给量f:
3)机床主轴转速:
取n=600r/min
工序 9:
精车三个连杆轴颈至φ24。
50-0。
033。
选用机床:
CA6140卧式车床
1) 被吃刀量
=0。
65mm,
2) 进给量f:
取f=0。
3mm/r
3)机床主轴转速:
取n=800r/min
4.4连杆机械加工工艺过程卡片的制订
制订机械加工工艺规程的最后一项工作就是填写工艺卡片,它主要包括工序顺序及内容的填写、工序简略的绘制、合理选择各工序所用机床设备的名称与型号、工艺装备(即刀具、夹具、量具等)的名称与型号。
在此不再说明详见附录:
结论
经过两个多月的学习和研究,我的毕业论文终于完成,看着自己的成果,有说不出的感触。
这段时间的努力,是对我这三年来的学习的系统总结,通过这段时间的努力,我自己的知识和能力也得到了提高。
虽然很多内容只是整理一些科学资料,但从开始接到论文题目到系统的实现,再到论文文章的完成,每走一步对我来说都是新的尝试与挑战,这也是我在大学期间独立完成的最大的项目。
通过此次对发动机曲轴加工工艺的分析,并通过查阅相关参考书籍、图表、等技术材料对曲轴的加工工艺有了更深一层的认识,再仔细分析普通车床的改造技术方面的问题。
通过对曲轴加工工艺的分析掌握了对曲轴在车床上加工的经验,以及确定了解对曲轴的加工的各个方面的方法,为以后的复杂曲轴的加工奠定了实践基础。
本次实践是在仔细分析曲轴零件加工技术要求及加工精度后,合理确定毛坯类型,经过查阅相关参考书、手册、图表、标准等技术资料,确定各工序的定位基准、机械加工余量、工序尺寸及公差,最终制定出曲轴零件的加工工序卡片。
以便于工人的加工
这次做论文的经历也会使我终身受益,我感受到做论文是要真真正正用心去做的一件事情,不是随意敷衍就能过去的事,是真正的自己学习的过程和研究的过程,没有学习就不可能有研究的能力,没有自己的研究,就不会有所突破,那也就不叫论文了。
希望这次的经历能让我在以后学习中激励我继续进步。
致谢
感谢导师敏锐的学术思想、严谨踏实的治学态度、渊博的学识、精益求精的工作作风、诲人不倦的育人精神,将永远铭记在作者的心中,使作者终生受益.他对本设计的构思、框架和理论运用给予了作者许多深入的指导,使得设计得以顺利完成。
感谢所有任课老师三年来对作者的培养。
这个文化底蕴深厚、安详宁静的地方,塑造了作者积极、乐观、淡定的人生态度,刻画了作者永远留恋的青春记忆,让作者在这个即将离别的时候,如此不舍.在此,作者要向诸位老师说声感谢。
当然也要感谢作者的父母,作者所迈出的每一步,都凝聚着你们的心血和汗水,你们始终如一的支持和关爱,是作者一直勇敢向前的动力。