注塑成型不良及对策Word文件下载.docx
《注塑成型不良及对策Word文件下载.docx》由会员分享,可在线阅读,更多相关《注塑成型不良及对策Word文件下载.docx(21页珍藏版)》请在冰豆网上搜索。
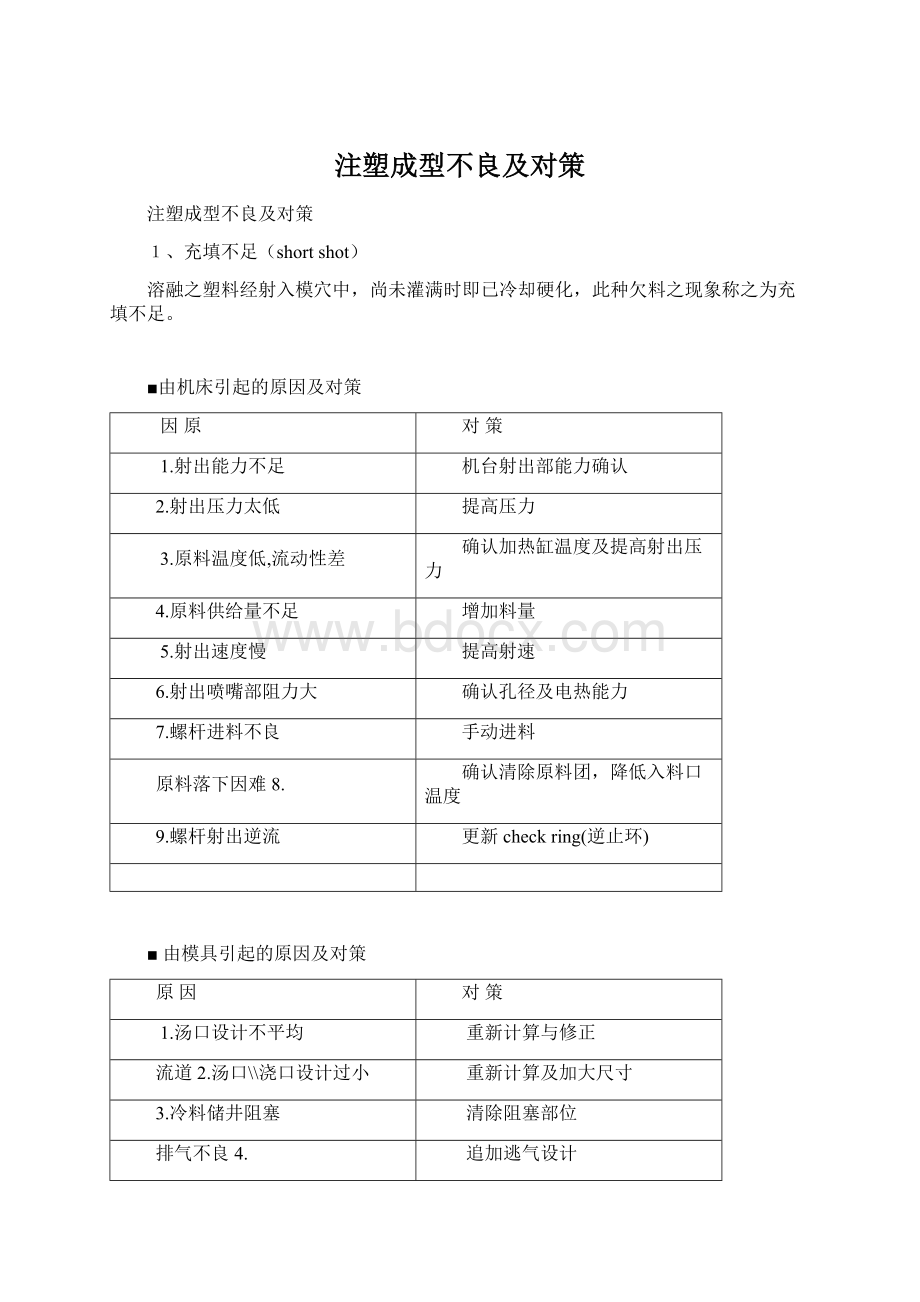
检查电路及温度并检修
8.模具冷却不当
确认水路系统并修改之
■由原料引起的原因及对策
因原
1.材料本身流动性差
确认或材料变更
2.润滑处理不当
修正使用部位及量的多少
3.离喷过多
降低使用量
2、毛边(flash)
塑胶料流出动静模之接合面,形成芒刺壮之现象,称之为毛边。
射出压力大1.
降低压力
2.开模压力不足
重新调整增加
3.射出供料量太多
降低射出供料量
4.原料温度高,流动性过佳
降低原料加热温度
5.保压时是过长
压低保压时间
6.射出速度太快
降低射出速度
7.机台动静模板平行度欠佳
利用长度规测量平长度、调整
■由模具引起的原因及对策
原因
1.公母模接合不良
确认平行度及合模线、调整
合模面附着异物2.
清除异物
模具之投影面积太大3.
重新计算机台能力或换机
4.模具老旧破损
修补破损部位
5.热浇道温度设定过高
调整适当的温度
■由原料引起的原因及对策
1.材料本身的粘度低,流动性良
降低成型温度、模具温度或变更材质
3、缩水(sinkmark):
此种现象在成型品表常会发现到,其发生之主要原因系原料在准却过程中,体积向肉厚的中心部逐渐收缩,而造成成品表面的凹陷状况。
特别是肉厚特别大的部位,其表面更加明显。
1.射速太慢
提高射出速度
2.射压偏低
提高射出压力
3.保压时间不足
增加保压时间
4.原料供应量不足
增加原料供应量
5.原料温度偏高
降低原料加热温度
6.射出喷嘴太长或孔径太小
更换短喷嘴或增大喷嘴孔径
7.射出喷嘴与模具汤口未吻合
重新校正中心度及圆弧度
8.射出喷嘴部温度低
提高喷嘴温度
开模太早、冷却不足9.
增加冷却时间.
10.热流道温度低
提高热流道之温度
射出时原料产生逆流11.
螺杆逆止环更换
■由模具引起的原因及对策
因原
模具温度太高1.
增加冷却水路或降低水路
2.模具温度不一局部过高
确认水路循环系统或增减
汤口或流道细小3.
重新计算及修改汤口或流道
4.模穴有特别厚肉的部位
增加厚肉部位之流道
肉厚设计不均一或不适当5.
依肉厚比例修正
因原
原料流动性太好1.
修正成型条件配合或变更村质或规格级数
2.原料收缩率太高
4、流道痕(flowmark)
熔融的原料射入模穴后,以进料点为中心,呈现年轮状纹路的现象。
1.原料温度低,流动性不够
提高原料加热温度
2.射出速度慢
提高射出速度
3.射出喷口太长、孔径太小
适当修正孔径、更换合适品
4.保压压力低
提高保压压力
5.保压时间不足
6.原料供应略不足
略增加计量值
7.刚成型时冷料流入
可以松退来防止冷却出现
8.射出喷口部温度低
检修喷口部电热圈及能力
因原
1.模温偏低
确认后再适提高
2.模具冷却不当
确认整个水路系统再修正
冷料储陷设计太小3.
增大冷料储陷部位
4.脱气不良
增加逃气槽设计或追加pin
热浇道温度偏低5.
适当提高温度
原料本身之流动性差
修正成型条件来配合变更规格级数或材质
5、银线(silverstreak):
成品表面出现随着原料流动方向的银白色线条之状况。
1.射出能力不足
确认射出容量/可塑化能力
2.原料加热温度太高产生热分解
3.射出速度太快产生热分解
4.射压太高产生热分解
降低射出压力
5.背压不足卷入空气
提高背压
6.原料加热时间太长产生热分解
降低原料加热温度或时间
7.原料加热温度低熔不均
提高原料加热温度
8.螺杆转速太快产生热分解
值r.p.m降低螺杆回转
9.螺杆不洁残留他料所致
徹清除螺杆内异物异质
因原
1.模具温度低
可先行预热模具
2.排气不良不顺
追加顶出梢或逃气槽
3.汤口位置不适当
重新确认与修正
4.汤口、流道、浇口设计太小
重新确认与变大尺寸
冷料储陷设计太小5.
6.肉厚设计不良
7.模面残留水份或过多之润滑剂
徹底去除水份\适当润滑剂
1.原料含水份及挥发物质多
以干燥设备预热干燥
材料受空气湿度影响混合一起2.
先预热干燥提高机台背压
):
lusterless)、光泽不良(cloudymappearance6、表面雾状痕(.
成品光泽面的部分,出现类似云雾状的白色现象。
1.原料熔融程度不均匀、部分过热
增加原料加热时间使之均匀
2.射出喷嘴太冷
检修喷嘴部电热片及提高温度
3.射出喷嘴孔径太小
适当修改孔径或更换合适品
4.射出速度太快或太慢
适当调整射出速度
5.原料过热分解
原因
1.模温过高或过低或不均
检查水路、水温及水量并修正之
2.汤口、流道、浇口过小
重新确认与修改
3.冷料储陷设计过小
4.模面附着水份或油质
清洁及擦拭模面及顶出梢
排气不良5.
6.离型剂使用过多
减少离型剂之量
1.原料本身含水份或挥发物
预备干燥
润滑剂中含挥发物所影响2.
适当地减少润滑剂使用量
3.不同材料混合造成
更新材料
7、融接线(weldline):
塑料射入模具中,流经流道,面后再会合而成的细线。
1.原料温度偏低\流动性不足
射出喷嘴温度太低2.
射出压力低3.
提高射出压力
射出速度慢4.
1.原料流动距离太长
提高模具温度或增加流道数
模具温度太低2.
提高模具温度
3.汤口位置及数量不当
重新计算与修正
4.汤口、流道、浇口太小
5.冷却时间太长
缩短冷却时间
排气不良6.
7.离型剂使用太多
以少量多次来改善
预备干燥时间加长
2.原料流动性不良
提高原料温度
3.原料硬化速度快
4.润滑剂不良或用量过多
适当修正
8.气泡(void)
成型品较厚肉的部位,由于内部中心部之冷却较外部冷却来的慢,而外部以冷却,拉住原料,并将空气包在其中之情况。
1.射出压力低
2.射出保压低
提高射出保压
3.保压时间短
适当调整射出速度
5.原料温度低,流动性不足
6.原料温度过高产生气体
7.螺杆背压不足卷入空气
提高螺杆背压
1.排气不足
变化大成品肉厚设计不良2.()
重新计算肉厚之必要性
汤口位置及数量不当3.
重新计算原料流动的距离
汤口、流道、浇口设计过小4.
模温太低6.
减小冷却水量或提高水温
1.原料本身收率大
以成型条件配合修正或变更规格
2.原料本身含水份或挥发物
原料混入空气3.
9.烧焦痕、黑痕(blackstreak)
成品表面出现黑色条纹,或者是在死角部位有烧焦之痕迹,因而称之。
■由机床引起的原因及对策
1.原料滞留加热缸造成烧焦
重新清洁加热缸内部
2.原料温度设定过高或时间长
降低原料温度或加热时间
3.原料在加热缸内摩擦、压缩而造成烧焦
降低螺杆与缸壁之间隙a.测量螺杆与缸壁之间隙b.
4.料桶下料部位冷却不足
确认水流通过量或增加
5.射出压力太高
6.射出速度太快
降低射出速度
7.射出喷嘴安装不良
重新拆除清洁再安装
1.模内附着油污
撤底擦拭清洁
2.汤口不顺,摩擦过热分解
研磨汤口部使之滑顺
3.排气不良
追加逃气设计
润滑剂太多1.
降低润滑剂之使用量
2.含挥发成份
)cracking.裂痕(10.
由于融熔原料在成品残留应力,而且应力超出了原料的裂断强度而使得成品在脱模后,其面表出现了细小分离的痕迹,此情况称之裂痕。
1.射出压力太高
2.原料温度低,流动性不足
增加原料加热温度
3.射出保压压太高
降低保压压力
4.射出保压时间过长
缩短保压时间
1.汤口设计太大或不顺
以成型条件改善进料情况或重新设计汤口.
2.模温偏低
减少冷却水量
离型不良3.
a.增加离型剂量或次数b.重新修正拔模斜度
内应力集中某部4.模穴设计不良
追加顶出梢及离型剂协助脱模
5.离型时公母模形成真空状态
重新修正拔模斜度
1.原料处理不当,性脆
更新原料
2.混料造成强度不足
11.挠曲(warpage)
成型品由于肉厚的不一致,以及冷却所造成的各部不均一的收缩量,以致成型后甚至经过一段时间,外形因收缩而弯曲变形之现象。
1.射出压力力太高
降低射出压力
2.保压过高
降低保压压力
3.保压时间过长
4.原料加热温度太低
5.射出速度太慢
原料熔融不均6.
提高原料加热温度或时间.
7.射出量过多,应力分布不均
降低射出量
冷却时间不够8.
增加冷却时间
离型不良1.
追加顶出梢平衡成品推出
2.模具突出部分设计不良
加拔模斜度
冷却不足或不均3.
确认与修正水路系统或增加
4.模具温度高
增加冷却水量或降低水温
5.汤口设计太大
重新修正
6.肉厚设计不均一
尽可能设计一致或是有特厚肉部位,冷却水路须足
原料处理不当
更新原料或使之冷却充足
12.离型不良(dartsticking):
在成型品脱离模具或是公母模分离时,以及成型品在顶出时,出现了裂痕、白抡等情况,因而称之。
1.射出压力高
2.原料温度高,流动性太好
3.射出保压过高
4.保压时间太长
降低保压时间
5.原料供给量太多
减少原料供给量
6.冷却不足
增加冷却时间或水量
因原
1.冷却不足或成品附着模具
模具温度高或静模温度高2.
汤口设计太大3.
4.排气不良
追加逃气槽或顶出梢
汤口平衡不良5.
射出口比浇口太6.
重新确认与修正
射出口球面半径比浇口衬套大7.
8.浇口斜度、口径及加工不良
9.模穴及角斜度加工不良
10.顶出不适当或离型剂不足
调整顶出条件或增加离型剂
■由原料引起的原因及对策
策对
原料本身润滑处理不当
增加原料润滑剂使用量
.脆弱(brittleness)13长期间的保管不良所引起,此种成型品材质变为强度不足的主要原因,是原料过热产生分解劣化以及原料
法就是要作好适当的成型温度,模具冷却温度以次要的原因是模温过低所造成,因皮,在确保材质稳定的方雨水、湿气、灰尘破坏了原料的特性。
及良好的原料放置场所,以避免日光、
cleavaga)14.表层剥离(要的原因就在不同材质的此种成型的表面就同云母片段般,可一层一层地逐层剥离的不良现象,其最主
份可逐层剥离,这种不良品的强度是异常地脆混合使用,而造成无法聚合的现象,使得成品表面以至肉厚部
发生方法有二。
其一,要确保使用之原料,不使二处或以上之原料弱,不堪一折即断,而要预防此种情况的
之亦即在变换材质时,过管必须撤底,才能预防混料混合使用。
另者,成型前要确保加热缸中原料之纯净度,发生。
15.分散不良:
材本身之分散性良否。
如成品表面色泽不均一,或出现色条纹之情况,因以称之。
其主要原因,在于色
必须对色材方面,适当地增加分散剂来协助色果调整机台螺杆背压或转速,仍然无法改善色分散性时,就就
分散的能力。
利用射程控制不良对策
不良现象
对策方法
]
的位置向前移[S缩短计量长度0
毛边\尺寸过大
保压切换前射速降低[确保正确保压切换
毛边尺寸不安定
不良现象
/凹陷流路末端/毛边进浇口处
降低第一段保压,待毛边部形成皮层后,再提高
对策方法
龟裂、白化应力残留毛边
全面调降保持压力
短射波纹钝状
提高充填速度提高充填压力;
短射凹陷
向后移动延长计量长度[S0
流路末端焦痕短射
降低充填后期速度[使排气充分进行
凹陷
形成皮层通过肉厚部位减速[
对策方法不良现象.
流路末端凹陷接合线明显接合处脆弱
提高充填速度或充填压力
凹陷尺寸不足
调高保持压力或延长保持时间
接合线明显
或其切换位置前后移动通过接合线部位快速通过[
喷痕、流痕浇口周边云状
低速通过问题区域
到达浇口前的初速降低[让熔胶到达各浇口后再加速]
浇口不平衡