方刀架的工艺设计说明文档格式.docx
《方刀架的工艺设计说明文档格式.docx》由会员分享,可在线阅读,更多相关《方刀架的工艺设计说明文档格式.docx(14页珍藏版)》请在冰豆网上搜索。
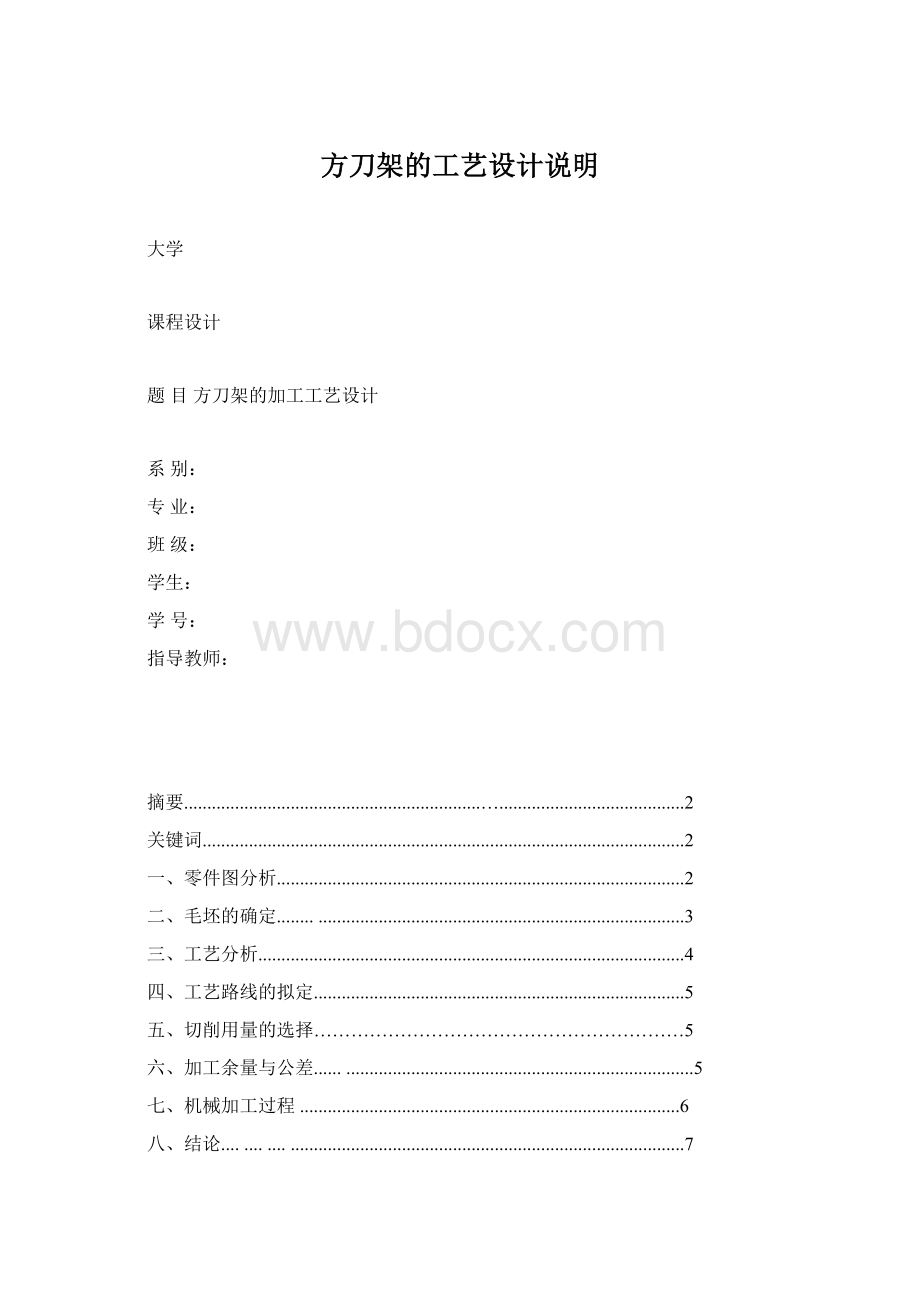
设计题目:
方刀架课程设计
技术要求
1、C面淬火硬度40~45HRC。
2、未注倒角1×
45°
。
3、材料45。
1、零件图样分析
1)φ15
mm孔对基准B的位置度公差为φ0.05mm。
2)图中左端面(方刀架底面)平面度公差为0.008mm。
3)图中左端面对基准B的垂直度公差为0.05mm。
4)C表面热处理40~45HRC。
5)材料45。
2、方刀架机械加工工艺过程卡(表2-49)
表2-49方刀架机械加工工艺过程卡
工序号
工序名称
工序容
工艺装备
1
下料
棒料φ120mm×
135mm
锯床
2
锻造
自由锻,锻件尺寸135mm×
135mm×
82mm
3
热处理
正火
4
粗车
用四爪单动卡盘装夹工作,粗车右端面,见平即可。
钻φ22mm通孔,扩孔至φ33mm,深35mm,车孔至φ36
mm,深39.5
mm,切槽φ37
mm×
3mm,倒角1.5×
C620
5
倒头,用已加工平面定位,四爪单动卡盘装夹工件,车左端面,保证厚度尺寸73
mm(留1mm余量)
6
铣
以φ36
mm孔及右端面定位,装夹工件,铣125mm×
125mm至尺寸126mm×
126mm(留加工余量1mm)
X62W
组合夹具
7
mm孔及右端面定位,装夹工件,铣四侧面槽,保证距右端面24.5mm,距左端面19mm(留加工余量大平面0.5mm,槽面0.5mm),保证75
75
mm及R3mm
8
mm孔及右端面定位重新装夹工件,精铣C面,保证尺寸距左端面18.5mm
9
mm孔及右端面定位,装夹工件,倒八务边角1×
10
C表面淬火40~45HRC
11
车
mm孔及右端面定位,装夹工件,车φ25
mm至图样尺寸,车环槽尺寸至φ103mm×
φ67mm×
2.5mm(因端面有0.5mm余量),倒角1×
12
磨
以φ25
mm孔及左端面定位,装夹工件,磨右端面保证尺寸39
mm
M7120
13
以右端面定位,装夹工作,磨左端面,保证尺寸72
mm和尺寸18mm
14
mm孔及左端面定位,装夹工件,粗、精磨四侧面,保证125
125
mm,并要对B基准对称,四面要相互垂直
15
钻
mm孔及右端面定位,一侧面定向,装夹工件,钻8×
M12-6H螺纹底孔φ10.2mm,攻螺纹M12
ZA5025组合夹具或专用钻模
16
mm孔及左端面定位,一侧面定向,装夹工件,钻、扩、铰4×
φ15
mm孔
17
φ36
mm孔及右端面定位,一侧面定向,装夹工件,钻φ10
mm底孔φ9mm,扩、铰至φ10
mm,其入口深18mm处,扩至φ10.2mm,攻螺纹M12-6H
18
检验
按图样检查各部尺寸及精度
19
入库
涂油入库
方刀架的加工工艺设计
机械制造工艺学课程设计综合了机械制造工艺学和其它专业课知识,充分展现了学生在生产实习中的实践能力。
本说明书是关于方刀架的一个简单工艺设计过程,在这次为期两个星期的设计,不仅让我们对所学课程进行了一次全面深入的总复习,而且为毕业设计提供了一次热身的机会,真正实现了理论联系实际。
就我个人而言,在这次设计中,我最大的收获是我懂得了要当一名合格的设计师是多么的不容易,在此老师和同学们在设计过程中给我的帮助。
本课程设计通过方刀架零件图的分析,确定了该零件的毛坯材料及尺寸规格。
通过对零件的加工工艺分析,确定了该零件的加工工艺路线,确定了该零件的加工工具,编写了详细的机械加工工艺文件:
工艺过程卡片和工序卡片。
由于本人能力和经验有限,难免出现一些错误和不足。
望各位读者和老师指正批评!
.一.零件的分析
a零件的作用
题目所给定的零件是机床上的方刀架。
其主要作用是稳固、可靠、准确的夹持刀具,换刀时能够转动。
零件的Φ25㎜端面用于准确定位,Φ25㎜孔与轴配合,用于夹紧.
b零件的工艺分析
Φ25+0.0230㎜端面与Φ25+0.0230㎜孔、Φ36+0.030㎜孔有一定的位置要求。
1.以Φ36+0.030㎜孔为中心加工的表面
这一组加工表面包括:
Φ25+0.0230㎜孔的端面,8条边的倒角,四方,四侧压刀槽,环型槽,Φ25+0.0230㎜孔及其倒角。
2.以Φ25+0.0230㎜孔为中心加工的表面
4-Φ15+0.0100㎜孔与9-M12-6H螺纹孔及其倒角。
3.以两个端面为基准加工的表面
Φ36+0.030㎜端面,Φ25+0.0230㎜孔端面(互为基准),零件的四个侧面。
这三组表面之间有着一定的位置要求,主要是:
(1)Φ25+0.0230㎜孔端面与Φ25+0.0230㎜孔的垂直度公差为0.05㎜。
(2)4-Φ15+0.0100㎜孔与Φ25+0.0230㎜孔的位置度公差为0.05㎜。
由以上分析可知,先精确加工出Φ36孔㎜,再以其为基准加工其它表面,可保证精度要求。
c、零件图分析
方刀架是作用是通过用螺钉的紧固作用在机床上快速的实现车刀固定,夹紧、转换,为车工提供方便,同时也节省了大量的辅助时间,大大提高了生产效率.方刀架的主要功用就是通过装在刀架上的其它零件夹紧刀具,换刀时,在手柄转动下,带动方刀架回转,以达到换刀的目的。
图一方刀架
零件图中A-A剖面图左端一面要求精度很高,平面度公差为0.008㎜.零件图中以㎜孔的轴线为基准,㎜两大面与其有垂直公差.公差值为0.04㎜.图中4×
㎜和㎜孔的轴线有位置度公差,公差值为㎜.零件图中㎜与㎜孔的公差较小,两孔应同轴.所以加工时应注意保证同轴度.零件图技术要求对C面淬火40~45HRC.零件图中㎜孔偏离基准孔㎜轴线4㎜,外端有8×
M15-6H深18㎜的螺纹孔.零件结构不复杂,单件小批量生产应用自由获得毛坯.
二、毛坯的确定
1该零件时属于箱壳类零件,结构比较简单规则,但某些加工面和孔的尺寸精度、平面度,垂直度、位置精度、表面粗糙度要求比较高,铸件适用于制造复杂形状的毛坯,锻件适用于形状简单,强度要求高的毛坯。
但因此零件并不是很复,因此该零件选择毛坯为锻件,锻件制造的方法有自由锻和模锻两种。
自由锻毛坯精度低、加工余量大、生产率低,适用于单件小批量生产以及大型零件毛坯。
模锻毛坯精度高、加工余量小,生产率高、适用于中批以上生产的中小型零件毛坯。
常用的锻造材料为中、低碳钢及低合金钢
确定毛坯的制造形式
零件材料为45钢,方刀架用于夹持刀具,工作时受到的力与振动较大,因此应该选用锻件,以使金属纤维尽量不被切断,提高零件力学性能和强度,保证零件工作安全可靠。
由于零件年产量为2500件(中批生产),而且零件属于轻型机械,故可采用模锻成型。
这从提高生产率,保证加工精度上考虑,也是应该的。
零件形状并不复杂,因此毛坯形状可与零件形状尽量接近,各孔不锻出。
2确定毛坯尺寸的
.确定毛坯余量、毛坯尺寸及其公差,设计、绘制毛坯图:
钢质模锻件的机械加工余量按JB3834-85和JB3835-85确定。
确定时,根据零件重量来初步估算零件毛坯锻件的重量,加工表面的加工精度,形状复杂系数,由《工艺手册》中的表2.2-25查得除孔以外各外表面的加工总余量(毛坯余量)。
孔的加工余量由表2.2-24查得。
注意表2.2-24、表2.2-25中的余量值为单边余量值。
本零件“方刀架”材料为45钢,硬度为207∽241HBS,毛坯重量估算约为7kg,生产类型为中批量生产,采用在锻锤上合模模锻毛坯,锻件材质系数为M1(表2.2-11)。
(1)Φ25㎜端面、Φ36㎜端面毛坯余量:
加工表面形状比较简单,由《工艺设计》中表2.2-10得锻件形状复杂系数为S1;
由锻件重量为7㎏、加工精度为F1、形状复杂系数为S1、由材质系数为M1、长度方向尺寸>
72㎜,查《工艺手册》表2.2-25得单边余量为Z=2∽2.5㎜,取Z=2.5㎜即可。
另查表2.2-13得长度方向公差为+1.5-0.7㎜,则长度方向毛坯尺寸为77+1.5-0.7㎜。
(2)四个侧面(125㎜×
125㎜)毛坯余量:
由毛坯重为7㎏、加工精度为F1、形状复杂系数为S1、材质系数为M1、长度方向尺寸>
125㎜,查《工艺手册》表2.2-25得单边余量为Z=2∽2.5㎜,取Z=2.5㎜即可。
另查表2.2-13得长度方向公差+1.9-0.9㎜,则长度方向毛坯尺寸为130+1.9-0.9㎜。
(3)四侧压刀槽毛坯余量:
①Φ36㎜孔端面侧压刀槽毛坯余量:
24㎜,查《工艺手册》表2.2-25得单边余量为Z=2∽2.5㎜,取Z=2.2㎜即可。
另查表2.2-13得长度方向公差+1.4-0.6㎜,则长度方向毛坯尺寸为26.2+1.4-0.6㎜。
②Φ25㎜孔端面侧压刀槽毛坯余量:
同理:
由F1、S1、M1、长度方向尺寸>
18㎜,查《工艺手册》表2.2-25得单边余量为Z=2∽2.5㎜,取Z=2.5㎜即可。
另查表2.2-13得长度方向公差+1.4-0.6㎜,则长度方向毛坯尺寸为20.5+1.4-0.6㎜。
(4).Φ25㎜孔、Φ25㎜孔、9-M12-6H螺纹孔、4XΦ15㎜孔、Φ85㎜环型槽均为实心,未冲出孔
二、基准与加工余量
①定位基准的选择
定位基准的选择是工艺规程设计中的重要工作之一。
定位基准选择得正确与合理,可以使加工质量得到保证,生产率得到提高。
否则,加工工艺过程中会问题百出,更有甚者,还会造成零件大批报废,使生产无常进行。
②.粗基准的选择
对于本零件而言,每个表面都要加工,故无法选取不加工表面为粗基准。
由于工艺上的需要,粗加工阶段就要将Φ36+0.030㎜孔加工得很精确,故以毛坯四个侧面为粗基准,利用四爪卡盘夹紧定位,以消除x,X,y,Y,z五个自由度(建立的空间坐标系为:
以Φ36+0.030㎜孔轴线和Φ25+0.0230㎜孔轴线方向为x轴,两个125㎜边分别为y轴、z轴,坐标原点为Φ25+0.0230㎜孔与Φ25+0.0230㎜孔端面的交点,X、Y为
Φ25㎜端面、Φ36㎜端面毛坯余量:
三、工艺分析
零件图中A-A剖面图左端一面平面度为0.008㎜,平面度非常高,所以加工须经磨削后刮削加工此平面。
从零件图可以看出,该零件上的㎜和㎜孔用以装配其它零件,因此必须保证两孔的同轴度,一般采用一次装夹完成车削加工,同时切出×
3㎜的槽及孔口倒角1×
方刀架零件的最高表面粗糙度㎜孔和㎜四个侧面Ra1.6,可通过粗车-半精车-精车及粗铣-半精铣-精铣可达到表面粗糙度要求。
在加工㎜和㎜孔时应遵循“先面后孔”的原则。
为了保证㎜轴线与A-A剖面图左右两端垂直度0.04㎜,须在加工㎜孔之前磨削两面,使其平行,并以此平面定位来加工孔。
㎜孔和㎜孔的轴线应在方刀架的几何中心上,但因尺寸㎜公差较大,以其定位会造成孔系单边,帮应设计自动定心夹具加工㎜孔系。
方刀架底面(A-A剖面图左端面)上的4×
㎜孔,应用夹具定位钻孔、铰孔获得位置度㎜和孔径㎜。
铣削压槽时,首选三面刃铣刀提高切削效率,应对标准三面刃铣刀进行改制,将圆周切削刃两尖角磨成R3的圆角,使其一次切削成型。
方刀架的材料为45钢。
锻件在粗加工之后进行调质处理,以消除粗加工产生的应力。
四、工艺规程的拟定
该零件时属于箱壳类零件,结构比较简单规则,但某些加工面和孔的尺寸精度、平面度,垂直度、位置精度、表面粗糙度要求比较高。
因此方刀架的加工工艺为锻造-粗铣-热处理-精铣-磨削-刮研-车-钳-热处理-检验-入库。
工艺分析
1)该零件为车床用方刀架,中间周圈槽用于装夹车刀,其C面直接与车刀接触,所以要求有一定的硬度,因此表面淬火40~45HRC
2)该零件左端面与车床拖板面结合,并可以转动,φ15
mm孔用于刀架定位时使用,以保证刀架与主轴的位置,其精度直接影响机床的精度。
3)该零件在加工中,多次装夹,均以φ36
mm孔及右端面定位,保证了加工基准的统一,从而保证了工件的加工精度。
4×
mm,可采用铣床加工,其精度可以得到更好的保证。
4)工序中安排了,四个侧面和左、右两端面均进行磨削,其目的是保证定位时的精度。
五、切削用量的选择
1)在保证加工质量和刀具耐用度的前提下,充分发挥机床性能和刀具切削性能,使切削效率最高,加工成本最低。
粗、精加工时切削用量的选择原则如下:
①粗加工时切削用量的选择原则首先尽可能大的选取背吃刀量;
其次要根据机床动力和刚性等限制条件,尽可能大的选取进给量;
最后根据刀具耐用度确定最佳的切削速度。
②精加工时切削用量的选择原则首先根据粗加工后的余量确定背吃刀量;
其次根据已加工表面的表面粗糙度要求,选取较小的进给量;
最后在保证刀具耐用度的前提下,尽可能选取较高的切削速度。
2)确定切削用量:
(切削用量的确定全部采用查表法)
a.背吃刀量asp的确定:
已知端面单边余量为2.1,一次走刀走完,asp=2.1㎜。
b.f的确定:
由《切削手册》表1.4,加工材料为45钢,车刀B×
H=16㎜×
25㎜,asp≤3㎜,工件尺寸为125㎜时:
f=0.6∽0.9㎜/r,修正系数k=0.8(有冲击加工),f=0.5∽0.72㎜/r,参看《切削手册》表1.30,横向进给量取f=0.52mm/r。
c.选择车刀磨钝标准及耐用度:
由《切削手册》表1.9,取车刀后面最大磨损量为1㎜,焊接车刀耐用度T=60min。
d.确定切削速度Vc:
由《切削手册》表1.10,当用YT5硬质合金端面刀横车加工σb=560∽620MPa钢料,asp≤3㎜,f≤0.54㎜/r时,Vc=138m/min。
由《切削手册》表1.28,Vc的修正系数为:
KTV=1.15,KMV=1.0,KSV=0.8,Ktv=0.65,Kkv=1.24,Kkrv=0.81,故
VC查=138×
1.15×
1×
0.8×
0.65×
1.24×
0.81=82.9m/min
N查=1000VC查/λd=1000×
82.9/(λ×
72)=336.498r/min
按C620-1车床的转速选择与337r/min相近的机床转速为:
n机=305r/min。
实际的切削速度为:
VC机=
m/min
e.校验机床功率:
车削时的功率PC采用查表法。
由《切削手册》表1.24,当σb=600Mpa、HBS=207∽241,asp≤3.4㎜,f≤0.6㎜/r,VC≤86m/min时,PC=2.4kw。
由《切削手册》表1.29-2,切削功率修正系数为:
KKrPC=0.5,KKrF=0.89,KroPC=KroFC=1.0。
∴实际切削时功率为:
PC实=2.4×
0.5×
0.89×
1=1.07kw。
由《切削手册》表1.30,当n机=305r/min时,车床主轴允许功率PE=5.9kw,因PC实<PE,故所选择的切削用量可在C620-1车床上进行。
f.校验车床进给机构强度:
车削时的进给力Ff由《切削手册》表1.21查出:
当σb=600MPa,asp=2.1㎜,f≤0.53㎜/r,VC<100m/min时,Ff=630N,
由于实际车削过程使用条件的改变,由《切削手册》表1.29-2,进给力修正系数为:
KroFf=1.0,KkrFf=1.17,KλsFf=1.0,故实际进给力为:
Ff实=630×
1.0×
1.17×
1.0=737.1N。
由C620-1车床说明书,进给机构的进给力Fmex=5100N(横走刀),Ff实<Fmex,故所选择的f机=0.52㎜/r可用。
最后确定的切削用量为:
asp=2.1㎜(一次走刀),f机=0.52㎜/r,n机=305r/min,VC机=69m/min。
七、机械加工过程
1、自由锻制造出零件毛坯。
2、热处理去应力
3、粗、精铣上盖接合面,以平口定心卡盘夹一端,大头顶尖顶另一端定位,同时按用平口钳装夹工件毛坯粗铣六个平面,保证足够的加工余量,而且要保证相邻面一定的相互垂直。
4、钻㎜孔至mm;
调头以平口定心卡盘夹一端,大头顶尖顶另一端定位,同时按㎜孔作为基准加工㎜,取总长㎜(留加工余量1mm)。
5、把工件固定在夹具中,半精镗孔㎜至㎜;
精镗㎜孔图纸要求;
表面粗糙度Ra值为2.5μm。
6、在夹具中,以㎜孔为基准攻8个M12×
18mm螺纹,车倒角1×
,。
7、热处理;
8、检验。
9、入库。
三.夹具设计
为了提高劳动生产率,保证加工质量,降低劳动成本,需要设计专用夹具。
经与指导老师协商,决定设计第Ⅷ道工序