半导体制造技术复习总结Word文档格式.docx
《半导体制造技术复习总结Word文档格式.docx》由会员分享,可在线阅读,更多相关《半导体制造技术复习总结Word文档格式.docx(18页珍藏版)》请在冰豆网上搜索。
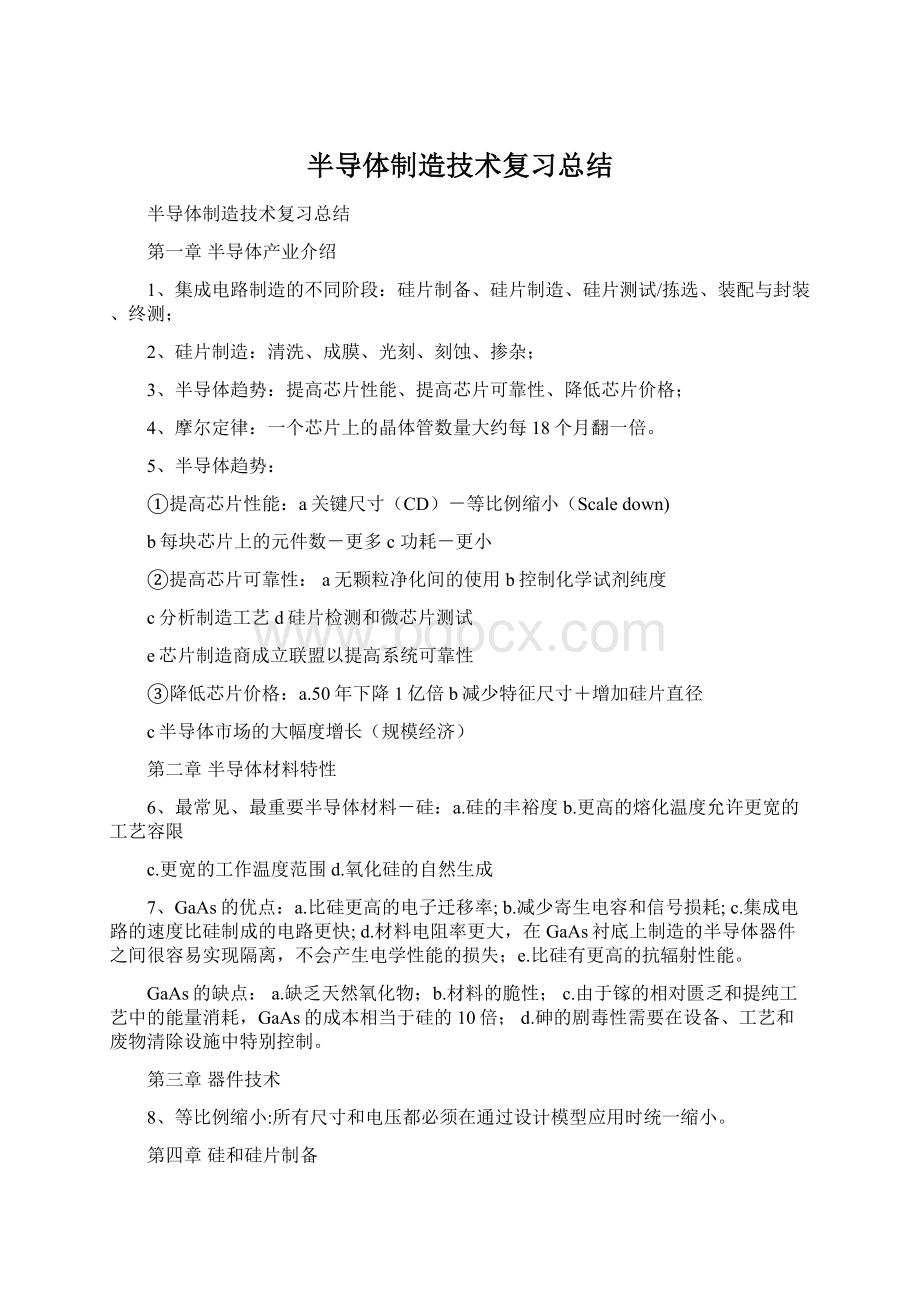
工艺成熟,能较好地拉制低位错、大直径的硅单晶。
缺点:
难以避免来自石英坩埚和加热装置的杂质污染。
b.区熔法:
主要用来生长低氧含量的晶体,但不能生长大直径的单晶,并且晶体有较高的位错密度。
这种工艺生长的单晶主要使用在高功率的晶闸管和整流器上
c.液体掩盖直拉法:
此方法主要用来生长砷化镓晶体,和标准的直拉法一样,只是做了一些改进。
由于熔融物里砷的挥发性通常采用一层氧化硼漂浮在熔融物上来抑制砷的挥发。
直拉法更普遍,更便宜,可加工大晶圆尺寸(如300mm),材料可重复使用。
区熔法可制备更纯的单晶硅(因为没坩锅),但成本高,可制备的晶圆尺寸小(约150mm)。
主要用于功率器件。
11、晶体缺陷:
a.点缺陷(三种基本点缺陷:
空位缺陷;
间隙原子缺陷;
Frenkel缺陷)
b.位错c.层错
12、刻蚀:
为了消除硅片表面的损伤,进行硅片刻蚀;
硅片刻蚀是利用化学刻蚀选择性去除表面物质的过程;
腐蚀掉硅片表面约20微米的硅。
13、外延(epitaxial):
与衬底有相同的晶体结构
用作双级晶体管中阻挡层,可减少集电极电阻同时保持高的击穿电压;
用在CMOS和DRAM中可改进器件性能,因为外延层具有低的氧、碳含量。
第五章半导体制造中的化学品
14、表面张力:
液滴的表面张力是增加接触表面积所需的能量。
随着表面积的增加,液体分子必须打破分子间的引力,从液体内部运动到液体的表面,因此需要能量。
15、通用气体:
控制在7个9以上的纯度(99.99999%)
气体种类
气体
符号
用途
惰性
氮气
N2
排出残留在气体配送系统和工艺腔中的湿气和残余气体,有时也作为某些淀积工艺的工艺气体
氩气
Ar
在硅片工艺过程中用在工艺腔体中
氦气
He
工艺腔气体,真空室的漏气检查
还原性
氢气
H2
外延层工艺的运载气体,也用在热氧化工艺中与O2反应生成水蒸气
氧化性
氧气
O2
工艺腔气体
16、液态化学品的输送过程是通过批量化学材料配送(BCD)系统完成的;
BCD系统由化学品源、化学品输送模块和管道系统组成;
对于使用量很少或者在使用前存放的时间有限的化学品不适合由BCD系统来输送,而采用定点输送(POU)。
17、通用气体:
通用气体存储在大型存储罐里或1000磅的大型管式拖车内,通过批量气体配送(BGD)系统输送。
其优点是:
可靠且稳定气体供应;
减少杂质微粒的沾污源;
减少日常气体供应中的人为因素。
特种气体:
控制在4个9以上的纯度(99.99%)
特种气体通常用100磅金属容器(钢瓶)运送到硅片厂,用局部气体配送系统输送到工艺反应室。
第六章硅片制造中的沾污控制
18、沾污的类型:
沾污是指半导体制造过程中引入半导体硅片的任何危害微芯片成品率及电学性能的不希望有的物质。
a.颗粒(可以接受的颗粒尺寸必须小于最小器件特征尺寸的一半);
b.金属杂质(危害半导体工艺的典型金属杂质是碱金属);
c.有机物沾污(来源包括细菌、润滑剂、蒸气、清洁剂、溶剂和潮气等。
微量有机物沾污能降低栅氧化层材料的致密性;
导致表面的清洗不彻底);
d.自然氧化层(自然氧化层会妨碍其他工艺步骤;
增加接触电阻去除:
通过使用含HF酸的混合液的清洗步骤);
e.静电释放(ESD产生于两种不同静电势的材料接触或摩擦。
静电荷从一个物体向另一物体未经控制地转移,可能损坏微芯片。
虽然ESD静电总量很小,但积累区域也小,可达1A的峰值电流,可以蒸发金属导线和穿透氧化层。
放电也可能成为栅氧化层击穿的诱因。
另外,一旦硅片表面有了电荷积累,它产生的电场就能吸引带电颗粒或极化并吸引中性颗粒到硅片表面)。
ESD控制方法:
防静电的净化间材料;
ESD接地;
空气电离。
19、沾污的源与控制:
空气;
人;
厂房;
水;
工艺用化学品;
工艺气体;
生产设备。
20、典型硅片湿法清洗顺序:
(1)piranha去除有机物和金属;
(2)SC-1去除颗粒;
(3)SC-2去除金属;
(每步结束都要进行清洗,即UPW清洗(超纯水),稀HF去除自然氧化层,UPW清洗;
最后干燥)。
21、湿法清洗设备:
兆声清洗(megasonics)、喷雾清洗、刷洗器、水清洗(溢流清洗器,排空清洗,喷射清洗,加热去离子水清洗)、硅片甩干(旋转式甩干机,异丙醇蒸气干燥)
有氧化物和RCA清洗的硅片表面是亲水性的;
刚经过氢氟酸腐蚀的无氧化物表面由于氢终结了表面是疏水性的。
第七章测量学和缺陷检查
22、测膜厚:
四探针法(测方块电阻);
椭偏仪(主要用于测透明薄膜)。
23、掺杂浓度:
在线测量方法:
四探针法(高掺杂浓度);
热波系统(低掺杂浓度);
线外测量方法:
二次离子质谱仪(SIMS);
电容-电压(C-V)特性测试。
24、套准精度是测量光刻机和光刻胶图形与硅片前面刻蚀图形的套刻的能力。
测量套准精度的主要方法是相干探测显微镜(CPM)。
25、聚焦离子束(FIB,FocusedIonBeam)系统大体上可以分为三个主要部分:
离子源、离子束聚焦/扫描系统(包括离子分离部分)和样品台。
聚焦离子束系统的应用:
①微区溅射和增强刻蚀;
②薄膜淀积;
③高分辨率扫描离子显微成像(SIM);
④半导体器件离子注入;
第八章工艺腔内的气体控制
26、工艺腔是指一个受控的真空环境:
在真空环境中保持预定的压强;
去除不需要的水汽、空气和附加反应;
创建一个能够使化学反应(例如产生等离子体)发生的环境;
控制硅片的加热和冷却;
控制气态化学品的流入,并在尽量靠近硅片的地方发生反应;
27、真空的益处:
a.创建洁净的环境;
b.降低分子密度;
c.增大分子碰撞的距离;
d.加速反应过程;
e.产生一种动力
真空级别:
初级759~100托氧化、光刻、抛光;
中级100~10-3托刻蚀、淀积、金属化;
高级10-3~10-6托离子注入、测量;
超高级10-6~10-9托测量.
28、等离子体(Plasma):
是一种中性、高能量、离子化的气体,包括中性原子或分子、带电离子和自由电子。
是除去固、液、气外,物质存在的第四态。
在一个有限的工艺腔内,利用强直流或交流电磁场或是用某些电子源轰击气体原子都会导致气体原子的离子化。
等离子体可以提供发生在硅片表面的气体反应所需的大部分能量,因此被广泛应用。
29、辉光放电:
当施加电能时,混合气体中的自由电子被加速,穿过混合气体,然后与原子或分子相撞,在碰撞过程中释放出附加的电子。
高能电子与中性原子或离子相撞并激发它们。
这些受激发的原子或离子存在的时间很短,当它们返回其最低能级时,能量以发射声子(或光)的形式释放。
通过在混合气体中施加直流电压或者射频(RF)范围内使用交流电都可以产生辉光放电。
30、在带有真空的工艺腔内,痕量水是最显著的沾污源。
为了降低工艺腔内吸附的水产生的沾污,需要减少以清洗为目的的开启或拆开的工艺反应室。
通过在线清洁技术可以实现这一点。
第九章集成电路制造工艺概况
31、CMOS工艺流程:
薄膜制作(layer)刻印(pattern)刻蚀掺杂。
32、硅片制造厂的分区:
1)扩散区(包括氧化、膜淀积和掺杂):
目的:
扩散区是进行高温工艺及薄膜淀积的区域
方法:
高温扩散炉和湿法清洗设备
功能:
高温扩散炉1200℃,可完成氧化、扩散、淀积、退火以及合金
2)光刻区:
黄光区涂胶/光刻/显影设备
将电路图形转移到覆盖硅片表面的光刻胶上
3)刻蚀区:
刻蚀是在硅片上没有光刻胶保护的地方留下永久的图形。
湿法刻蚀和干法刻蚀
4)离子注入区:
离子注入机是亚微米工艺中最常见的掺杂工具
离子注入+退火常见掺杂元素:
As,P,B
5)薄膜生长区:
薄膜区主要负责各个步骤中介质层与金属层的淀积。
方法:
CVD,PVD,SOG,RTP
6)抛光区:
CMP(化学机械抛光)的目的是使硅片表面平坦化。
化学腐蚀+机械研磨
33.CMOS制作步骤:
⑴双阱工艺;
⑵浅槽隔离工艺;
⑶多晶硅栅结构工艺;
⑷轻掺杂漏(LDD)注入工艺;
⑸侧墙的形成;
⑹源/漏(S/D)注入工艺;
⑺接触孔的形成;
⑻局部互连工艺;
⑼通孔1和金属塞1的形成;
⑽金属1互连的形成;
⑾通孔2和金属塞2的形成;
⑿金属2互连的形成;
⒀制作金属3直到制作压点及合金;
⒁参数测试
第十章氧化
34、氧化膜的用途:
a.保护器件免划伤和隔离沾污b.限制带电载流子场区隔离(表面钝化)
c.栅氧或存储单元结构中的介质材料d.掺杂中的注入掩膜
e.金属导电层间的介质层
35、金属层间的介质层:
二氧化硅是微芯片金属层间有效的绝缘体;
二氧化硅能阻止上层金属和下层金属间短路;
氧化物质要求无针孔和空隙。
36、氧化的化学反应:
干氧:
Si(固态)+O2(气态)SiO2(固态)
湿氧:
Si(固态)+H2O(气态)SiO2(固态)+2H2(气态)
湿氧反应会产生一层二氧化硅膜和氢气。
潮湿环境有更快的生长速率是由于水蒸气比氧气在二氧化硅中扩散更快、溶解度更高。
湿氧反应生成的氢分子会束缚在固态的二氧化硅层内,使得氧化层的密度比干氧小。
这种情况可通过在惰性气体中加热氧化物来改善,以得到与干氧生长相似的氧化膜结构和性能。
37、影响氧化物生长的因素:
①温度②H2O③掺杂效应:
重掺杂的硅要比轻掺杂的氧化速率快。
④晶向:
线性氧化速率依赖于晶向的原因是(111)面的硅原子密度比(100)面的大。
因此在线性阶段,(111)硅单晶的氧化速率将比(100)稍快,但(111)的电荷堆积要多。
在抛物线阶段,抛物线速率系数B不依赖于硅衬底的晶向。
对于(111)和(100)向,在抛物线阶段的氧化生长速率没有差别。
⑤压力效应:
生长速率将随着压力增大而增大。
高压的方法可降低热预算:
允许降低温度但仍保持不变的氧化速率,或者在相同温度下获得更快的氧化生长。
⑥等离子增强:
给硅施以比等离子区低的偏压,这可使硅片收集等离子区内的电离氧。
这种行为导致硅的快速氧化,并且允许氧化物生长在低于600℃的温度下进行。
这一技术带来的问题是产生颗粒、较高的膜应力以及比热生长氧化要差的膜质量。
38、用于热工艺的基本设备:
卧式炉、立式炉、快速热处理(RTP);
39、RTP的主要优点:
①减少热预算②硅中杂质运动最小
③减少沾污,因为冷壁(coldwall)加热
④由于较小的腔体体积,可以达到清洁的气氛
⑤更短的加工时间(指循环时间)
40、RTP的热源:
大多数的RTP采用多盏卤钨灯组装在一起作为热源。
41、RTP应用:
1)注入退火,以消除缺陷并激活和扩散杂质;
2)淀积膜的致密,如淀积氧化膜
3)硼磷硅玻璃(BPSG)回流;
4)阻挡层退火,如氮化钛(TiN);
5)硅化物形成,如硅化钛(TiSi2);
6)接触合金
42、热氧化的目标:
按厚度要求生长无缺陷、均匀的SiO2膜。
干法热氧化最常见的应用是生长用于栅氧的薄氧化膜。
用干法氧化生长的高质量氧化物具有均匀的密度、无针孔、可重复的特点。
第十一章淀积
43、关键层(Criticallayers)是指那些线条宽度被刻蚀为器件特征尺寸(CD)的金属层。
对于ULSI,特征尺寸的范围一般为:
形成栅的多晶硅、氧结构以及距离硅片表面最近的金属层。
关键层对于颗粒杂质(致命缺陷)很敏感,在小尺寸情况下,可靠性问题(如电迁移)会更加显著。
44、非关键层(Noncriticallayers)指处于上部的金属层,有更大的线宽。
对于颗粒沾污不够敏感;
处于上部的非关键层的长导线长度等因素会影响芯片的速度和功耗。
45、薄膜特性:
①好的台阶覆盖能力(FilmStepCoverage);
②填充高的深宽比间隙(HighAspectRatioGaps)的能力:
深宽比定义为间隙的深度和宽度的比值,用来描述小间隙(槽或孔)。
高深宽比的间隙使得难于淀积形成厚度均匀的膜,并且会产生夹断(pinch-off)和空洞
③好的厚度均匀性(ThicknessUniformity):
材料的电阻随薄膜厚度的变化而变化,因此薄膜厚度要均匀。
膜层越薄就会有更多的缺陷,如针孔,这会导致膜本身的机械强度降低。
对于薄膜,要有好的表面平坦度来尽可能减少台阶和缝隙。
④高纯度和高密度(FilmPurityandDensity):
膜中含有H就会使膜特性蜕化。
膜密度也是膜质量的重要指标,它显示膜层中针孔和空洞的多少。
多孔膜密度会降低,有时会导致折射率变小。
⑤受控制的化学剂量;
⑥高度的结构完整性和低的膜应力;
⑦好的电学特性;
⑧对衬底材料或下层膜好的黏附性
46、膜的粘附性(FilmAdhesion):
为了避免薄膜分层和开裂,薄膜对衬底材料要有好的粘附性。
开裂的膜会导致膜表面粗糙,杂质也可以穿过膜;
对于起隔离作用的膜,开裂会导致电短路或者漏电流;
薄膜对表面的粘附性由表面洁净度、薄膜能与之合金的材料类型等因素决定;
金属铬、钛、钴因为它们的粘附性而非常有用。
47、薄膜生长三步骤:
第一步:
晶核形成.第二步:
聚集成束(岛生长).第三步:
形成连续的膜。
48、化学气相淀积(CVD)是通过气体混合的化学反应在硅片表面淀积一层固体膜的工艺。
硅片表面及其邻近的区域被加热来向反应系统提供附加的能量。
化学气相淀积的基本方面:
①产生化学变化,这可以通过化学反应或热分解
②膜中所有的材料物质都源于外部的源
③化学气相淀积工艺中的反应物必须以气相形式参加反应
49、化学气相淀积过程中5种基本化学反应:
高温分解:
通常在无氧的条件下,通过加热化合物分解(化学键断裂);
光分解:
利用辐射使化合物的化学键断裂分解;
还原反应:
反应物分子和氢发生的反应;
氧化反应:
反应物原子或分子和氧发生的反应;
氧化还原反应:
反应3与4组合,反应后形成两种新的化合物。
50、异类反应与同类反应:
CVD工艺反应发生在硅片表面或者非常接近表面的区域,称为异类反应(也叫表面催化)。
某些反应会在硅片表面的上方较高区域发生,这称为同类反应。
同类反应是要避免的,因为反应生成物会形成束状物,这会导致反应物粘附性差、低密度和高缺陷。
在CVD工艺中,需要异类反应来生成高质量的膜。
51、CVD速度限制因素:
①质量传输限制(mass-transportlimited)淀积工艺:
CVD反应的速率不可能超越反应气体从主气体流传输到硅片表面的速率。
(质量传输限制淀积工艺对温度不敏感。
高温高压CVD工艺是受质量传输限制的。
)
②反应速度限制的(reaction-ratelimited)(或动态控制(kineticallycontrolled)):
在更低的反应温度和压力下,由于只有更少的能量来驱动表面反应,表面反应速度会降低。
最终,反应物到达硅片表面的速度将超过表面化学反应的速度。
(即使有更多的反应物,由于低温不能提供反应所需的足够能量,反应速度也不会增加。
52、CVD过程中使用等离子体的好处:
1.更低的工艺温度(250–450℃);
2.对高的深宽比间隙有好的填充能力(用高密度等离子体);
3.淀积的膜对硅片有优良的黏附能力;
4.高的淀积速率;
5.少的针孔和空洞,因为有高的膜密度;
6.工艺温度低,因而应用范围广。
53、低k材料:
线电容C正比于绝缘介质的k值,低k值的绝缘介质可以减小芯片总的互连电容,减小RC信号延迟,提高芯片性能。
(芯片性能的一项指标是信号的传输速度。
芯片的不断缩小导致互联线宽度减小,使得传输信号导线电阻(R)增大。
而且,导线间距的缩小产生了更多的寄生电容(C)。
最终增加了RC信号延迟(RC信号延迟降低芯片速度,减弱芯片性能)。
通常称为互连延迟。
从本质上讲,减小互连尺寸带来的寄生电阻和电容效应而导致更大的信号延迟。
这与晶体管的发展正好相反,对晶体管而言,随着栅长变小,延迟变小,晶体管的速度增加。
54、高k介电常数:
用于DRAM存储器中;
最终取代超薄栅氧。
(MOS晶体管中,栅介质需要承受栅电极和衬底之间很高的电压。
薄栅氧会受到隧穿电流的影响。
在小尺寸的ULSI,电子会在晶体管开或关时隧穿通过栅介质。
这将导致阈值电压的漂移,并最终由于无法切换开关状态而使电路失效。
55、外延生长方法:
气相外延(VPE)、金属有机CVD(MOCVD)、分子束外延(MBE);
第十二章金属化
56、互连指由导电材料(铝、多晶硅或铜)制成的连线将电信号传输到芯片的不同部分。
57、接触(contact)指硅芯片内的器件与第一层金属层之间在硅表面的连接。
58、通孔(via)是穿过各种介质层从某一金属层到毗邻的另一金属层形成电通路的开口。
59、常见的金属和金属合金:
铝、铝铜合金、铜、阻挡层金属、硅化物、金属填充塞
60、铝:
最早的互连金属
铝在20℃时具有2.65µ
Ω-cm的低电阻率,比铜、金及银的电阻率稍高。
铜和银都比较容易腐蚀,在硅和二氧化硅中有高的扩散率,这些都阻止它们被用于半导体制造。
金和银比铝昂贵得多,而且在氧化膜上附着不好。
铝能够很容易和氧化硅反应,加热形成氧化铝(Al2O3),这促进了氧化硅和铝之间的附着。
铝容易淀积在硅片上,可用湿法刻蚀而不影响下层薄膜。
61、铝铜合金:
铝有电迁徒引起的可靠性问题。
由铝和铜形成的合金,当铜含量在0.5~4%时,其连线中的电迁移得到控制,即最大程度地解决电迁徒稳定性问题。
62、铜:
由于铜具有更低的电阻率,因此可取代铝成为主要的互连金属材料。
为什么引入铜?
电阻率的减小:
在20℃时,互连金属线的电阻率从铝的2.65µ
Ω-cm减小到铜的1.678µ
Ω-cm;
减少RC的信号延迟,增加芯片速度。
功耗的减少:
减小了线的宽度,降低了功耗。
更高的集成密度:
更窄的线宽,允许更高密度的电路集成,这意味着需要更少的金属层。
良好的抗电迁徒性能:
铜不需要考虑电迁徒问题。
更少的工艺步骤:
用大马士革方法处理铜具有减少工艺步骤20%到30%的潜力。
铜面临的挑战:
①铜快速扩散进氧化硅和硅,一旦进入器件的有源区,将会损坏器件。
②应用常规的等离子体刻蚀工艺,铜不能容易形成图形。
③低温下(<200℃)空气中,铜很快被氧化,而且不会形成保护层阻止铜进一步氧化。
解决的一些方法:
采用为铜优化的阻挡层金属处理。
用钨塞作为第一层金属,与源、漏和栅区的接触,克服了铜沾污硅的问题。
采用双大马士革法,不需要刻蚀铜。
63、阻挡层金属的基本特性:
1)有很好的阻挡扩散作用;
2)高导电率具有很低的欧姆接触电阻;
3)在半导体和金属之间有很好的附着;
4)抗电迁徒;
5)在很薄的并且高温下具有很好的稳定性;
6)抗侵蚀和氧化。
64、被用于填充的最普通的金属是钨,因此填充薄膜常常被称为钨填充薄膜。
钨具有均匀填充高深宽比通孔的能力,因此被选作传统的填充材料。
钨可抗电迁徒引起的失效,因此也被用作阻挡层以禁止硅和第一层之间的扩散及反应。
钨是难熔材料,熔点为:
3417℃,在20℃时,体电阻率是52.8µ
Ω-cm。
65、溅射:
应用最广泛的系统,溅射的物理特性是轰击靶,以轰击出原子,并在硅片表面淀积这些原子形成薄膜。
溅射的优点:
1.具有淀积并保持复杂合金原组分的能力;
2.能够淀积高温熔化和难熔金属;
3.能够在直径为200mm或更大的硅片上控制淀积均匀薄膜;
4.具有多腔集成设备,能够在淀积金属前清除硅片表面沾污和本身的氧化层(被称为原位溅射刻蚀)。
三类溅射系统:
①RF(射频)溅射产额不高,导致它的沉积速率低,因此应用受到限制。
②磁控;
③IMP(离子化的金属等离子体)离子化金属等离子体为高深宽比淀积改进了方向性。
第十三章光刻:
气相成膜到软烘
66、光刻包括:
①负性光刻:
基本特征是当曝光后,光刻胶会因交联而变得不可溶解,并会硬化。
一旦硬化,关联的光刻胶就不能在溶剂中被洗掉。
负性光刻胶得到了与掩膜版上图案相反的图形。
②正性光刻:
正性光刻工艺中,复制到硅片表面上的图形与掩膜版上的一样。
被紫外光曝光后的区域经历了一种光化学反应,在显影液中软化并可溶解在其中。
67、光刻的8个步骤:
①气相成底膜(Vaperprime):
清洗、脱水和硅片表面成底膜处理
增强硅片和光刻胶的粘附性。
硅片清洗包括湿法清洗和去离子水冲洗以去除沾污物。
脱水、干烘在一个封闭腔内完成,以除去吸附在硅片表面的大部分水汽。
然后立即用六甲基二硅胺烷(hexa-methyl-disilazane,简称HMDS)进行成膜处理,起到粘附促进剂的作用。
②旋转涂胶(Spincoat)
③软烘(Softbake):
目的是去除光刻胶中的溶剂。
软烘提高了粘附性,提升了光刻胶的均匀性,在刻蚀中得到了更好的线宽控制。
典型的软烘条件是在热板上90℃到100℃烘30秒。
④对准和曝光(Alignmentandexposure):
掩膜版与涂胶后硅片上的正确位置对准。
一旦对准,将掩膜版和硅片曝光,把掩膜版图形转移到涂胶的硅片上。
对准和曝光的重要质量指标是线宽分辨率、套准精度、颗粒和缺陷。
⑤曝光后烘培(PEB):
对于深紫外(DUV)光刻胶必须进行曝光后烘培。
⑥显影(Develop):
光刻胶上的可溶解区域被