乳化液泵的设计毕业论文Word下载.docx
《乳化液泵的设计毕业论文Word下载.docx》由会员分享,可在线阅读,更多相关《乳化液泵的设计毕业论文Word下载.docx(33页珍藏版)》请在冰豆网上搜索。
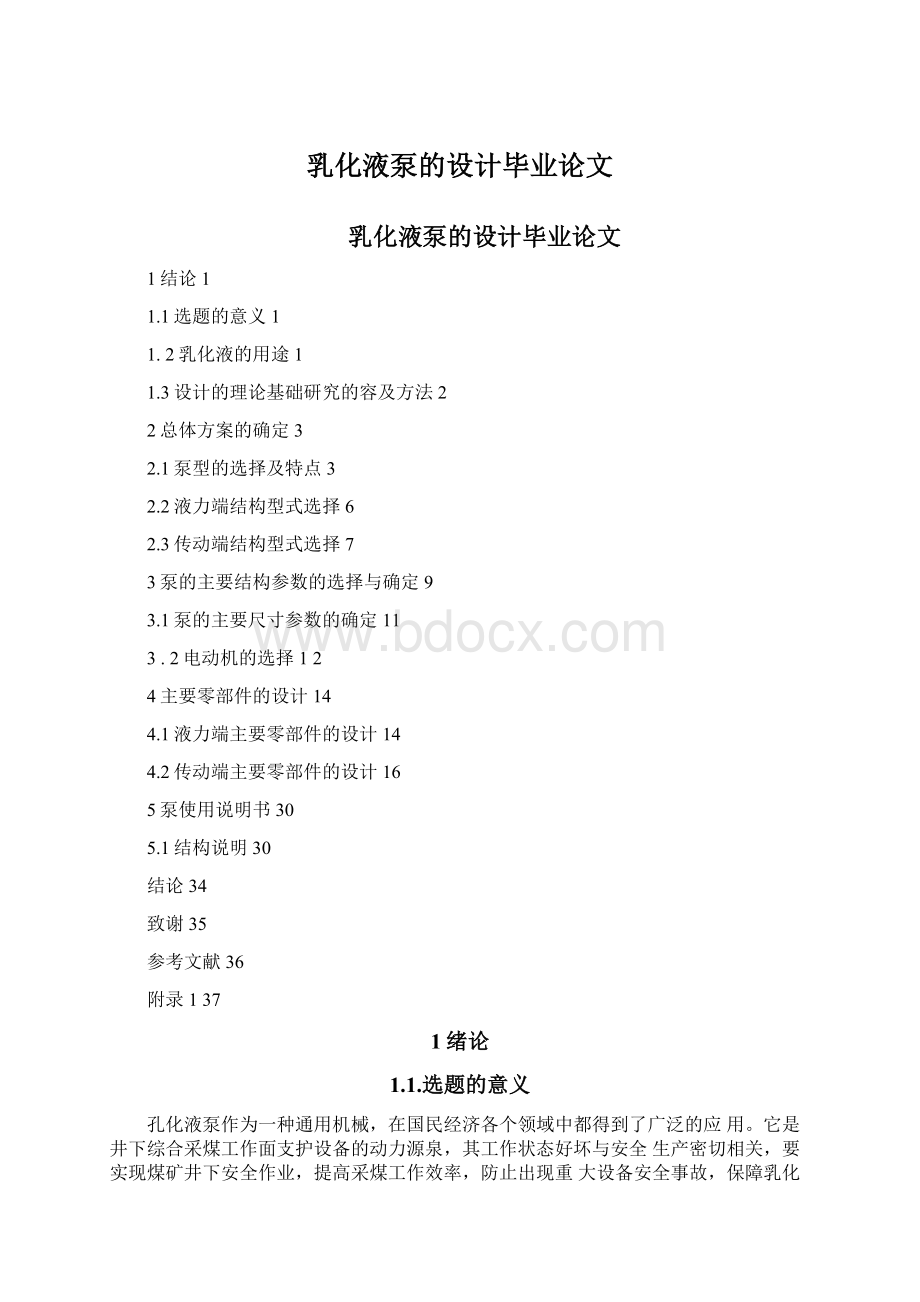
泵型
卧式三联(缸)单作用柱卧式三联(缸)单作用
塞泵
柱塞泵
Q(m3/h)
5.5〜56
0.7-120
P?
(lON//)
25~320
50~500
n(spin)
24〜260
110~800
S(10'
3m)
65~220
20~280
D(10'
45~115
16~160
展%
1.5~2.5
0.7~5.6
fts
=—(m/s)
Vz
0.4-1.0
0.5〜1.8
N0(kw)
7.5〜225
40~550
用独立的旋转原动机(如电动机、柴油机、汽油机等)驱动的泵,称为机动泵。
用电动机驱动的泵又叫电动泵。
机动泵通常由液力端、传动端、减速机,原动机及其附属设备(润滑、冷却系统等)所组成。
机动系的共同特点:
(1).瞬时流量脉动而平均流量(泵的流量)。
只取决于泵的主要结构参数〃(每分钟往复次数)、S(柱塞的行程)、D(柱塞直径)而与泵的排出压力几乎无关,当〃、S、。
为确定值时,泵的流量是基本恒定的。
(2).泵的排出压力P是一个独立参数,不是泵的固有特性,它只取决于排出管路的特性而与泵的结构参数和原动机的功率无关。
2.1.2直接作用泵及其特点
液力端柱塞与动力端直接连接的泵,通称为直接作用泵。
动力端的工作介质可以是蒸汽,压缩气体(通常是空气)或有压液体(一般是油)。
其中最常用的是蒸汽,也叫蒸汽直接作用泵。
2.1.3手动泵及其特点
用人力通过杠杆机构驱动柱塞做往复运动的泵,称为手动泵。
手动泵的特点:
(1).泵的流量和均匀度均无定植,它取决于人力在单位时间的操作次数和操作均匀程度。
(2).泵的排出压力取决于排出管路特性和排出端压力。
泵的额定排出压力则与泵的结构强度,液力端密封质量及人力大小有关。
手动泵主要用于缺少动力或无须其他动力的场合。
例如:
简易水压试验,简易农药喷雾、农村简易深井提水,食品工业提升液状物以及简易消防用泵等。
2.1.4柱塞泵及其特点
在液力端往复运动副上,运动件上无密封元件的叫柱寒。
相应的泵称为柱塞泵.
柱塞泵的特点,
(1).柱塞泵的柱塞形状简单,柱塞直径可制得很小,但不宜过大目前所见到的柱塞直径图大多在。
=3〜150(10-3m),个别的达0.2m。
直径过小,会遇到加工工艺上的困难,直径过大,特别是卧式泵,因柱塞自重过大造成对密封的偏磨,影响密封的使用寿命。
(2).由于结构的原因,柱塞泵大多制成单作用的,几乎不制成双作用泵。
(3).因柱裂密封(填料箱)在结构上易于变形,在材料选择上也比较灵活,故柱塞泵适用的排出压力困较广泛,且宜制成高压泵。
2.1.5隔膜泵及其特点
泵的液力端借助于隔膜(膜片、波纹管等)来组成工作腔,以隔膜周期弹性变形来代替柱塞的往复运动的泵,称为隔膜泵。
隔膜泵的特点:
(1).在泵的液力端以隔膜的好密封代替了柱塞的动密封,因此可作到输送介质绝对不外漏。
因此,隔膜泵适于输送易燃、易爆、剧毒、恶臭以及具有放射性等对人体有害的介质,也用于输送纯度高、价格昂贵的物料。
对于强腐蚀、易挥发、易结晶以及磨砺性很强的悬浮液,有时也采用隔膜泵,以改善柱塞密封的工作条件,延长其使用寿命。
(2).为了保证隔膜的强度和使用寿命,隔膜的弹性变形挠度通常很小,故对隔膜泵来讲,隔膜工作腔的行程容积不可能很大,否则其径向尺寸就会很大。
另外,隔膜泵的每分钟的往复次数也较低。
2.1.6卧式泵及其共同特点
液缸或柱塞中心线为水平布置的泵,均称为卧式泵。
往复泵多为卧式泵,其共同特点如下:
(1).便于操作者观察泵的运转情况,拆、装、使用、维修较为方便。
(2).机组在高度方向尺寸时,不需要很高的厂房;
但在长、宽方向尺寸较大时,占地面积则较大。
(3).因为柱塞做水平往复运动,密封件在工作时须承受柱塞自重,容易产生偏磨,尤其当柱塞较重、悬臂很长时,这种现象更为明显。
⑷.卧式泵的机械惯性力水平分力较大,而泵的基础承受水平分力的能力又较差,故卧式泵对基础的强度和刚度要求较高。
2.1.7立式泵及其共同特点
液缸或柱塞中心线是垂直布置的泵,称为立式泵。
立式泵的共同特点:
(D.高度方向尺寸较大,厂房高,但长、宽方向尺寸小,、占地面积少。
(2).运转时,柱塞密封不承受柱塞自重,不易产生偏磨。
⑶.机械惯性力水平分力小,垂直分力大,而泵基础有较强的承受垂直分力的能力,故对基础要求不高。
(4).一般讲,立式泵的吸排阀、吸排管布置上较困难,拆装、维护也不太方便,特别是当液力端置于下侧时更明显。
但当把液力端置于上侧时,则有所改善。
通过对以上几种型式泵的特点的对比,再结合乳化液泵本身的结构特点及其用途,此次设计选用三联单作用机动卧式柱塞泵。
2.2液力端结构型式选择
在往复泵上把柱裂从滑块外脱开一直到泵的进出口欠的部件,称为液力端,液力端是介质过流部分,通常由液缸体,活塞和缸套或柱塞及其密封(填料箱)、吸入阀和排出阀组件、缸盖和阀箱道.以及吸入和排出集合管(或集液器)等所组成,液力端结构型式的选择应与泵型及总体结构型式时,应遵循下述基本原则:
(1).过流性好,水力阻力损失小,为此,液流通道应力求短而直,尽管避免拐弯和急剧的断面变化。
(2).液流通道应利于气体排出,不允许有死区,造成气体滞留,通常,吸入阀应置于液缸体下部,排出阀应置于液缸体顶部。
(3).吸入阀和排出阀应垂直布置,以利于阀板正常启闭和密封,特殊情况下也可以倾斜和水平布置。
2.3传动端结构型式选择
往复泵上传递动力的部件叫传动端,对于机动泵,传动端是指从滑块起一直到主轴(曲轴)伸出端(动力输入端)为止的部件,如果是泵减速的,则传动端包括减速机构,如果是泵外减速的,则传动端不包括减速机构,减速机独立,如果是直联泵则传动端没有减速机构,也无减速机。
对直接作用泵,传动端即指动力缸(汽缸、气缸)等部件。
机动泵的传动端主要由机体、曲轴连杆、曲柄、滑块及润滑冷却等辅助设备所组成。
传动端结构型式选择也应和泵型及总体结构型式选择同时进行,在选择和设计传动端时应遵循以下基本原则:
(1).传动端所属主要零部件必须满足浆最大柱塞力下是强度和刚度的要求。
(2).传动端各运动副,必须是润滑可靠,满足比压和Pv允许值,润滑油温升也限制在设计要求以,必要时应有冷却设备。
图2-1乳化液泵总体结构图
1机体
2连杆
3滑块
4曲轴
5减速机构
6缸套组件
7柱塞
3泵的主要结构参数的选择与确定
3.1泵的主要尺寸参数的确定
3.1.1给定设计参数
工作介质:
乳化液油(含3%-5%乳油的中性溶液)
排出压力:
P=35MPa排量:
Q=80L/min
往复泵柱塞个数:
Z=3个
泵的排出压力额定值仅取决于结构强度、液力端密封对对质量及原动机的额定功率而与流量无关。
由公式'
Q=&
7,=2^(1+K)].=乃(1+K)%
00240
=D2Un,Z+=D^pnZ10-9m3/s
8八240
式中Q泵的实际流量,lO^m'
/s;
Q,——泵的理论流量,KF,//s;
%泵的容积效率;
A=-D2——柱塞截面积,而;
4
D——柱塞直径,m;
S——柱塞行程长度,m;
n曲轴转数(rpm)或柱塞的每分钟往复次数spm;
Z——泵的联数(柱塞数);
A»
•
K——系数K=l———(Ar一柱塞杆截面积,疗)
=l-(^)2(O,一柱塞杆直径,m);
30
柱塞■的平均速度,ni/s;
S
(p=—程径比。
D
由上式可知,流量。
与〃、s、。
、。
、Z等结构参数有关,如果在总体设计时预先选定了泵型和总体结构型式,那么Z、K即为已知,因此,决定Q的主要结构参数就是〃、s、。
和。
.,对于柱塞泵则只有〃、s、D三个主要结构参数㈤。
3.1.2柱塞直径和行程的确定
1.柱塞平均速度的选择
的大小直接影响泵各运动副零、部件的摩擦和磨损,特别是对柱塞及其密封这一对运动副的影响尤为显著。
不应选择过大,过大摩擦和磨损严重,特别是当柱塞及其密封一旦严重磨损,泄露就将增加,流量下降,排出压力也不能达到额定值。
也不能选择过小,要获得一定的。
值,当一经确定,。
即为确定值如果a.选择过小,。
值就必须较大,这样一来。
不仅使液力端径向尺寸增加,而且因柱塞力是和成正比的,传动端受力也随之聚增,从而会使泵的总体尺寸和重量增大。
⑴.选取值的一般原则和方法
可参考泵的有效功率N,来选取,一般讲,M越大,也越大,反之则宜取较小值,因为N,大,柱塞力趋于增大,为了减小活塞力,或加大S,或提高〃,其结果都使Um增大。
22).活塞平均速度的确定阳
U,“的大小主要与折合成单联单作用泵的有效功率有关a.=K,N「%/s
(3-1)
式中%——柱塞平均速度,m/s;
K,——统计系数K,(0.18〜0.8);
Nez——折合成单联但作用泵的有效功率,kw。
n=(P「P、)Q.PQ
ez612Z(K+1)612Z(K+1)
(3-2)
式中Q——泵的流量,L/min当选取U,”时0,六。
.
P2——泵的排出压力,10卡/小;
片——泵的吸入压力,,当或4为常压事,全压力P「小P1;
Z——泵的联数;
AA
K——系数K=1一二,对于单作用泵二•=1K=0对双作用泵'
AA
A
—<
1,OvKvl(K取0.3)。
A
由公式(3-2)
35x80
612x3x(O+l)
15.25kw
由公式(3-1)
Um=K,N二=0.3x15.25g=0.892m/s
2.曲轴转数〃和柱裂行程长度s的选择
当U,”选定后,柱塞的直径可算出由公式6“=*查表02-6常见泵型的〃值国及建议值⑼,对一般的卧式三联单作用机动泵〃值国现有产品(180〜
720spm)取〃=535r/min
word版木
S=2=3OxO.892=oo5.
〃535
通过圆整取行程5=0.044m
对于机动泵L%(8〜16)S・・.L=10x5=0.44m
3.2电动机的选择
4.2.1原动机功率的选择与确定
1.原动机的选择
27
36.7
式中P——泵的全压力
Q泵的实际流量L/min
也可以按下列公式计算
ZPQPQy
N.===45.75kw
'
612450
式中P——泵的全压力lO'
N/m?
2.泵的轴功率(输入功率)
(3-4)
式中〃泵的效率,
由公式(3-4)
电动泵的效率图〃=Q6〜0.9取〃=0.9
、吟=*=5°
.83心
3.原动机的功率
WORD版木
七=———-kw
“XTldX九
(3-5)
rh
泵的传动装置效率;
原动机的效率取"
二°
・99。
由于泵的效率〃已包括了泵的传动机构的摩擦损失,所以,泵的传动装置效率只与泵的减速机构的机械损失有关。
当采用齿轮传动时17d=。
・%〜0.99(闭式);
采用平皮带传动时方=0.92~0.98,三角皮带传动时也=0.90〜0.94
由公式(3-5)
心=——-kw=————=54.6kw
〃x(x"
d0.9x0.94x0.99
4主要零部件的设计
4.1液力端主要零部件的设计
柱塞泵液力端通常由液缸体和缸盖,吸入和排出阀箱、阀盖、缸套柱塞和填料箱以及进出口法兰等。
液缸体是柱塞泵中主要承受液压的零件之一,由于它的形状复杂、壁后不均,有十字或T型交孔、应力集中大,而且是与输送介质接触,并承受压交变载荷,因此,它的设计合理性,对其弄命有较大的影响。
特别是当输送高温、高压、强腐蚀性介质时,应注意以下几点:
⑴.要选取合适的材料和热火理方式,既要有较高的强度指标和抗腐能力,又要特别注意到材料对应力集中的敏感性。
(2).在结构设计上要求形状简单,壁厚均匀,部流道孔相交也应尽可能减少,实践证明;
在同等条件下,T型交孔要比十字型交孔的液缸体寿命长
(3).如果加工工艺允许,在部流道交孔应予导圆,并对加工表面做强化欠理»
以减弱应力集中的影响。
(4).如果在总体和液力端部件设计时就能注意到把液缸体的高度应力集中部位和高度变载荷区分开来,将会有效地提高液缸的使用寿命。
图4-la直通式布置的液缸体
图4-lb垂直布置的液缸体
4.1.1液缸体壁厚的确定及强度校核
1.液缸体壁厚的确定
假定液缸体为一外圆半径为々,圆半径为八的等厚壁圆筒且壁厚6相对轮薄(G/r\<
L5)时,则可由薄壁筒公式确定壁厚:
pn
♦=「1I+C10。
[小P
(4-1)
一般取C=0.3~0.8(10-2m)对于球墨铸铁6卜600~800105N/m2
式中d——壁厚>
10-2ni;
(P——焊接系数,无焊接夕=1;
P缸最大工作压力'
lOMPa;
D,——液缸体径»
10-2m;
C——考虑铸造偏心及腐蚀所留的裕量。
由公式(4-1)
PD、
:
.6=l-C=0.005ni
2.强度校核
对于薄壁筒(々/八41.5)
(4-2)
因为液缸体一般不焊接支管,所以°
=1由公式(4-2)
=367.5<
3510.04+(0.005-0.003]
2(0.005-0.003)x1
符合要求。
图4-2缸套组件
4.2传动端主要零部件的设计
4.2.1机体的组成及设计
机动往复泵传动端主要由机体、曲轴、连杆、滑块等主要零部件所组成。
机体是传动端主要零部件之一,通常由机身、机盖、轴承盖等主要零部件所构成。
(1)体的主要作用
⑴.作为传动机构和曲柄连杆机构的支承、定位及运动导向用;
(2).承受或传递泵的作用力和力矩;
(3).作为液力端的支承作用并用天安装某些辅助设备。
2.机体的结构设计
机体结构设计的一般原则
(D.应有足够的强度和刚度,在此前提下,力求重量轻
(2).结构上力求简单,外形力求美观。
铸造和机加工工艺性能应良好。
在结构设计上要有便于制造、加工的基准面,以期能较好的保证各加工表面的几何形状、尺寸精度和形状位置分差。
不必要的加工表面应力求减小,简化工表,缩短生产周期,降低成本
⑶.便于曲柄机构和传动机构的拆装,调整和检修,便于机体部的清洗和润滑油的排放和更新
⑷.机体底部应有足够的承重面积,尽可能的降低重心,保证其承载能力和泵运转时的稳定性。
4.2.2曲轴设计
曲轴是把原动机的旋转运动转化为柱塞往复运动的重要部件之一。
工作时,它为承受周期性的交变载荷,产生交变的扭转应力和弯曲应力。
1.曲轴的结构特点和选择
对于孔化液泵采用两支承三曲拐曲轴型式,这种型式的曲轴因具支承少,使曲轴和机体的加式量减少,传动端装配也简单。
相反的,因曲柄错角为120”的三拐二支承曲轴不能简化成平面曲轴,故受力状况复杂,刚度和强度较差,在同等条件下就显得粗笨。
2.曲轴结构设计
图4-4曲轴
(1).曲轴销直径确定
图4-5曲柄销直径的尺寸
曲拐轴的曲柄销直径D(图4-5)㈤可按经验公式初步确定
。
=(5.4〜7.2卜010-2m
(4-5)
式中P——最大柱塞力,t;
匕ax——Rax=(L2-L5*(P,——柱塞力)。
对于二支承三拐曲轴系数应取偏大值
由公式(4-5)
D=5.4"
=0.0358ni
通过圆整后取。
=0.04m
(2).主轴颈,
Dt=(0.9~1.1)0”;
=1.0x0.04=0.04m
一般曲拐主轴颈变形倾角最大,故考虑到主轴承倾角允许值且应根据主轴承径进行圆整,此外,当确定主轴颈尺寸时,还应顾及到轴颈重叠度s/0,应尽可能避免S/。
等于零或接近于零甚至于小于零的情况(见图4-6)[22]
图4-6曲拐主轴颈尺寸
(3).轴颈长度
轴颈长度还应满足曲柄销问题(即液缸中间距)a的要求
a=L+t+2tx
(4-6)
式中i——曲柄厚度,l(r2ni;
t1——曲柄两侧台肩厚度,lO^m。
(4).曲柄厚度
t=(0.5〜0.7)0。
〃=0.62x0.04x0.025m
式中D——曲柄销直径,10-2^。
(5).曲柄宽度〃
/?
=(1.4〜1.8)。
=1.58x0.04«
0.06ni
式中D——曲柄销直径,10-2nM
(6).曲柄半径r
一/2=半=0皿
(7).核算轴颈重叠度
相邻两曲柄销处S()/D=(D-旧r)/D=0.13
式中D——曲柄销直径,lO-m。
主轴颈与曲柄销处S0/O=(监2—r)/0=0.5
2
(8).连杆大头轴瓦宽度
b=(0.4〜0.65)0=0.5xD=0.02m
式中D——曲柄销直径,10-2nio
(9).曲柄长度
L=b+0.02(0.2〜0.5)=0.02+0.02x0.5=0.03ni
(10).曲柄厚度/
长臂。
=(0.5〜0.7)0=0.6x0.04=0.024m取f=0.025m短臂取G=。
2m
(ID.曲柄宽h
〃=(1.4〜1.8)0=1.5x0.04=0.06in
式中D——曲柄销直径,IO-2”。
⑫.校核液缸中心距。
由公式(4-6)
a=L+t+2t,=0.0155+0.015+2x0.0025=0.0355m式中L——曲柄长度,
t——曲柄厚度,10-3ni;
八——长臂曲柄厚度,1(T%。
<
满足已知条件t}=0.0025m>
4.2.3连杆设计
1.连杆结构型式特点
连杆是传动端曲柄连杆机构中连接曲轴和滑块的部件,连杆的运动是一平面运动。
可以把连杆运动看成是沿液缸中心线移动和绕滑块摆动的两种简单的运动的合成。
连杆与曲轴相连的一头称为大头,与滑块相连的一头称为小头。
通常连杆由连杆体、连杆盖、大头轴瓦、小头衬套以及连杆螺栓、连杆螺母等所组成。
1大头轴瓦
4连杆螺栓
2连杆螺母
5连杆体
3连杆盖
6小头衬套
图十一连杆结构
2.连杆的结构设计
(1).一般设计要求
1.连杆应具有足够的刚度和强度,工作时不致破坏或弯曲变形。
2.大、小头结构合理,适合装配有足够承载能力的轴瓦或轴承。
3.在满足上述条件下,应尽可能选取合理的外形、截面尺寸、减轻重量,即可减少运动质量也有利于加工制造和拆装。
(2).连杆定位
连杆定位是用来限制连杆在工作时垂直于连杆体中心线方向的窜动的,定位方式可分为大头定位和小头定位两种。
大头采用厚壁轴瓦或小头采用球面连接时,适合于大头定位,大头采用薄壁瓦时,因没有翻边,故不适合大头定位,特别是大头为闭式结构,装滚动轴承时,不便于大头定位,多采用小头定位。
这里采用小头定位,用小头定位时,以小头衬套端面作为定位面,通过该端面与小头体两侧配合端面之间的间隙来限制连杆的窜动,间隙取(2〜6)10一%。
而在大头欠则允许较大窜动,间隙(2〜6)10-2ni
(3).连杆长L和连杆比("
=选择
连杆长是指连杆大头和小头孔的中心距」连杆比是指曲柄半径”与连杆
;
_5_0,044_
长之比'
曲柄半径即为柱塞行程长度的一半=5=下-=9比2取4=g(2<
;
)则/==0.022/0.169=0.120川
⑷.连杆宽度8
为了便于加工,通常连杆的大、小头宽度相同,只有当小头宽度受十字头尺寸限制时,才把小头宽度取得略小些。
连杆宽度为通常按连杆轴瓦宽度〃,由下列经验公式确定:
B,=(0.88~0.94)61041n
(4-20)
因为采用小头定位,所以〃为小头衬套宽度=0。
30nl(见连杆小头衬套)[22]
由公式(4-20)
B,=(0.88~0.94)6=0.94x0.03«
0.031n
(5).杆的连接孟结构尺寸确定
①.杆的中间截面尺寸