建筑铝合金型材的模具设计文档格式.docx
《建筑铝合金型材的模具设计文档格式.docx》由会员分享,可在线阅读,更多相关《建筑铝合金型材的模具设计文档格式.docx(22页珍藏版)》请在冰豆网上搜索。
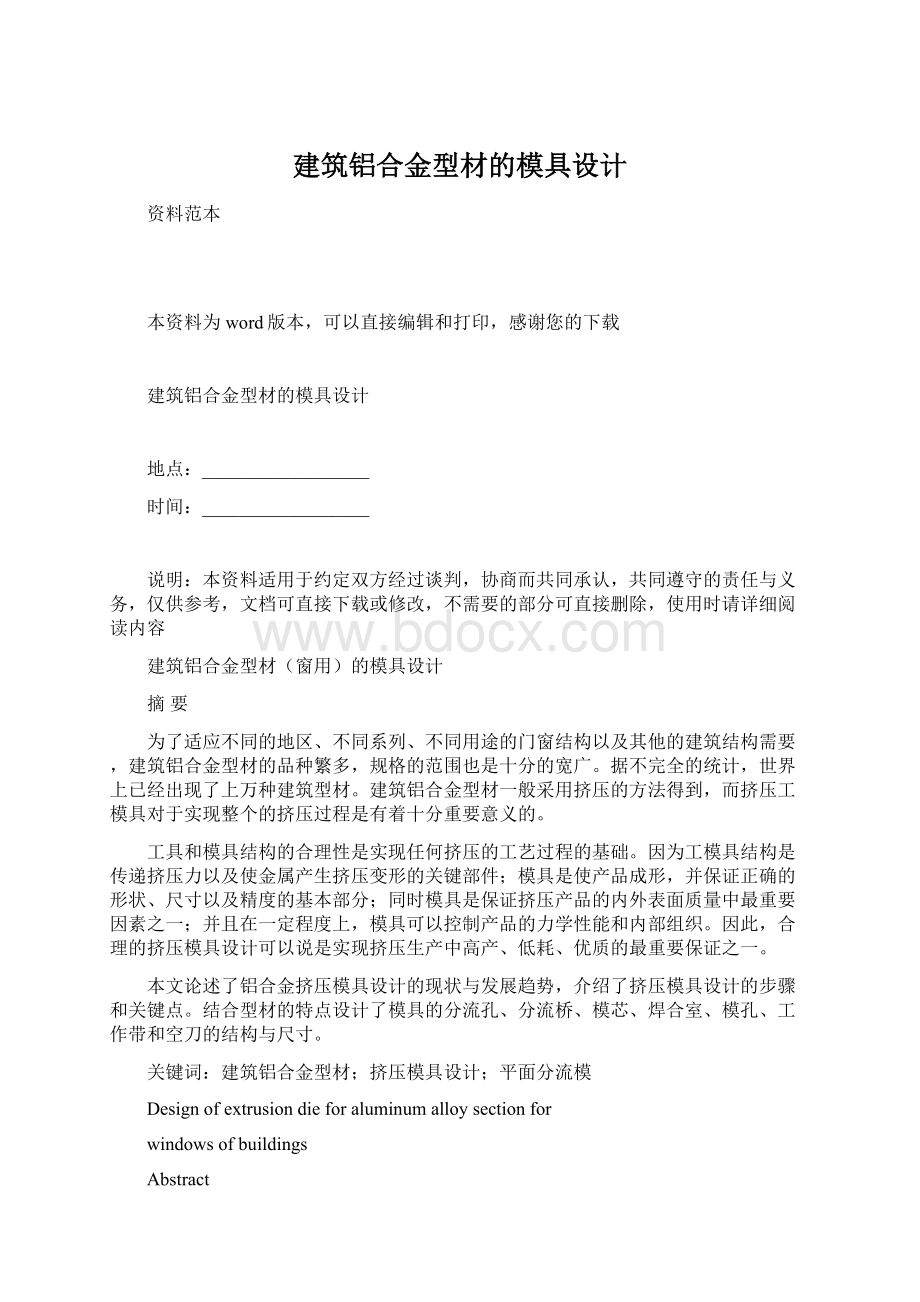
工具和模具结构的合理性是实现任何挤压的工艺过程的基础。
因为工模具结构是传递挤压力以及使金属产生挤压变形的关键部件;
模具是使产品成形,并保证正确的形状、尺寸以及精度的基本部分;
同时模具是保证挤压产品的内外表面质量中最重要因素之一;
并且在一定程度上,模具可以控制产品的力学性能和内部组织。
因此,合理的挤压模具设计可以说是实现挤压生产中高产、低耗、优质的最重要保证之一。
本文论述了铝合金挤压模具设计的现状与发展趋势,介绍了挤压模具设计的步骤和关键点。
结合型材的特点设计了模具的分流孔、分流桥、模芯、焊合室、模孔、工作带和空刀的结构与尺寸。
关键词:
建筑铝合金型材;
挤压模具设计;
平面分流模
Designofextrusiondieforaluminumalloysectionfor
windowsofbuildings
Abstract
Inordertoadapttodifferentregions,differentseriesanddifferentusesofdoors,windowsandotherarchitecturalstructures’needs,architecturalaluminumprofilesandtherangeofspecificationsisverywide.Accordingtoincompletestatistics,theworldhasbeenoutofthetensofthousandskindofbuildingprofiles.Architecturalaluminumprofilesgenerallyareusedbyextrusion,andextrusiontoolingisgreatsignificancetothewholeofextrusionprocess.
Theconsistencyoftoolanddiestructureisthebasisofachievinganyfoundationextrusionprocess.Becausethediestructureisthekeycomponentsofpassingextrusionpressureandproducingmetalextrusion;
Moldistheessentialpartofensuringproduct’scorrectshape,sizeandprecision;
Thesametime,moldisthemostimportantfactorstoensurethesurfacequalityoftheinnerandouterofextrusionproduct;
Themoldcancontrolthemechanicalpropertiesandinternalorganization.Therefore,reasonableextrusiondiedesignisoneofthemostimportantassuranceofachievingextrusionproductionhighyield,lowcostandhighquality.
Thispaperdiscussesthesituationanddevelopmenttrendofaluminumextrusiondiedesign,andintroducesthestepsandkeypointsofextrusiondiedesign.Thepaperdesignthestructureandsizeofmoldsections’diversionhole,splitbridge,moldcores,weldingchamber,thediehole,workingpartandemptyknife.
KeyWords:
Architecturalaluminumprofile;
Designofextrusiondie;
Planarportholedie
TOC\o"
1-3"
\h\uHYPERLINK\l_Toc18534摘要PAGEREF_Toc18534I
HYPERLINK\l_Toc26707AbstractPAGEREF_Toc26707II
HYPERLINK\l_Toc4588第一章绪论PAGEREF_Toc45881
HYPERLINK\l_Toc249471.1概述PAGEREF_Toc249471
HYPERLINK\l_Toc52741.2模具在铝合金挤压生产中的重要作用与特殊地位PAGEREF_Toc52741
HYPERLINK\l_Toc168691.3国内外铝合金挤压模具技术的现状与发展趋势PAGEREF_Toc168692
HYPERLINK\l_Toc86871.3.1铝合金挤压模具设计的现状PAGEREF_Toc86872
HYPERLINK\l_Toc218851.3.2铝合金挤压模具技术的发展与趋势PAGEREF_Toc218853
HYPERLINK\l_Toc239351.3.3国内外模具设计水平比较PAGEREF_Toc239357
HYPERLINK\l_Toc175071.4建筑型材的模具设计PAGEREF_Toc175077
HYPERLINK\l_Toc77241.4.1铝合金民用建筑型材的特点PAGEREF_Toc77248
HYPERLINK\l_Toc9951.4.2民用建筑型材模具设计特点PAGEREF_Toc9958
HYPERLINK\l_Toc241221.4.3建筑铝合金型材模具设计重点与难点PAGEREF_Toc241228
HYPERLINK\l_Toc16049第二章铝型材挤压工艺PAGEREF_Toc1604910
HYPERLINK\l_Toc227902.1铝型材模具的设计原则PAGEREF_Toc2279010
HYPERLINK\l_Toc307952.1.1挤压模具设计时应考虑的因素PAGEREF_Toc3079510
HYPERLINK\l_Toc111052.1.2模具设计的原则与步骤PAGEREF_Toc1110510
HYPERLINK\l_Toc31652.1.3模具设计的技术条件及基本要求PAGEREF_Toc316512
HYPERLINK\l_Toc132832.2确定采用平面分流模的原则PAGEREF_Toc1328312
HYPERLINK\l_Toc292672.3模具材料的选择PAGEREF_Toc2926713
HYPERLINK\l_Toc68312.3.1产品性能分析PAGEREF_Toc683113
HYPERLINK\l_Toc259962.3.2挤压模具的工作条件PAGEREF_Toc2599614
HYPERLINK\l_Toc212452.3.3模具材料的合理选择PAGEREF_Toc2124515
HYPERLINK\l_Toc27628第三章铝型材挤压模具设计PAGEREF_Toc2762817
HYPERLINK\l_Toc93593.1制品的分析PAGEREF_Toc935917
HYPERLINK\l_Toc150463.1.1制品尺寸分析PAGEREF_Toc1504617
HYPERLINK\l_Toc62533.1.2制品结构分析PAGEREF_Toc625317
HYPERLINK\l_Toc154843.2挤压设备的选择PAGEREF_Toc1548418
HYPERLINK\l_Toc326283.2.1挤压系数PAGEREF_Toc3262818
HYPERLINK\l_Toc139673.2.2填充系数PAGEREF_Toc1396719
HYPERLINK\l_Toc104733.2.3挤压力的计算PAGEREF_Toc1047319
HYPERLINK\l_Toc9743.3型材模具结构PAGEREF_Toc97419
HYPERLINK\l_Toc129153.3.1模具外径PAGEREF_Toc1291520
HYPERLINK\l_Toc104863.3.2模具厚度PAGEREF_Toc1048620
HYPERLINK\l_Toc155643.4上模设计PAGEREF_Toc1556420
HYPERLINK\l_Toc243463.4.1分流孔的设计PAGEREF_Toc2434620
HYPERLINK\l_Toc212333.4.2分流桥的设计PAGEREF_Toc2123322
HYPERLINK\l_Toc190933.4.3模芯的设计PAGEREF_Toc1909322
HYPERLINK\l_Toc327343.5下模设计PAGEREF_Toc3273423
HYPERLINK\l_Toc26483.5.1焊合室的设计PAGEREF_Toc264823
HYPERLINK\l_Toc120533.5.2模孔尺寸的设计PAGEREF_Toc1205325
HYPERLINK\l_Toc273423.5.3模孔工作带的长度确定PAGEREF_Toc2734228
HYPERLINK\l_Toc57663.5.4模孔空刀结构设计PAGEREF_Toc576629
HYPERLINK\l_Toc83603.6定位的设计PAGEREF_Toc836029
HYPERLINK\l_Toc73143.6.1凸台的设计PAGEREF_Toc731429
HYPERLINK\l_Toc213323.6.2定位销的选择PAGEREF_Toc2133230
HYPERLINK\l_Toc8273.6.3螺钉的选择PAGEREF_Toc82730
HYPERLINK\l_Toc153443.7强度校核PAGEREF_Toc1534430
HYPERLINK\l_Toc106893.7.1分流桥弯曲应力校核PAGEREF_Toc1068930
HYPERLINK\l_Toc12613.7.2分流孔道抗剪应力校核PAGEREF_Toc126131
HYPERLINK\l_Toc60第四章零件图和装配图PAGEREF_Toc6032
HYPERLINK\l_Toc142794.1上模PAGEREF_Toc1427932
HYPERLINK\l_Toc258434.2下模PAGEREF_Toc2584333
HYPERLINK\l_Toc85774.3装配图PAGEREF_Toc857734
HYPERLINK\l_Toc7058结论PAGEREF_Toc705835
HYPERLINK\l_Toc11781致谢PAGEREF_Toc1178136
HYPERLINK\l_Toc5929参考文献PAGEREF_Toc592937
第一章绪论
概述
铝型材的挤压是指使铝合金的高温铸坯通过专用模具(机头),在挤压机提供的强大压力的作用以及给定速度下,将铝合金从模腔中挤出,来获得所需要的形状、尺寸和具有一定力学性能的铝合金挤压型材[1]。
铝合金型材挤压的成型过程是非常复杂的,除圆形截面的铝型材挤压是属于二维轴对称的问题外,一般而言,其它形状铝型材挤压是属于三维流动的大变形问题。
因此,挤压模具设计制作的质量及其使用寿命就变成了挤压过程是否经济可行的关键之一。
合理的设计和制造是能大大的延长模具寿命的,同时对提高生产效率、降低成本及能耗具有重要的意义。
合理的模具结构是实现任何一种挤压工艺过程的基础。
目前,我国型材的挤压模具设计还基本上停留在依靠传统的工程类比及设计经验积累上,所设计制造的模具必需经过反复的试模与调整,才可以保证其投入使用的成功,造成了企业不定时的停工待模,影响正常的生产,与此同时会造成挤压产品的质量不高,模具的使用寿命不长等诸多的缺陷。
因此,由于铝合金型材的产品不断的向着大型化、薄壁化、扁宽化、复杂化、高精化和多功能、多用途、多品种、长寿命的方向发展,促使传统模具设计方法的改进成为了现在铝合金型材工业发展的需求。
模具在铝合金挤压生产中的重要作用与特殊地位
在现代化大生产中,工具和模具是对实现整个挤压的过程有十分重要意义的,工具和模具结构的合理性是实现任何挤压的工艺过程的基础,因为工模具结构是传递挤压力以及使金属产生挤压变形的关键部件;
同时模具是保证挤压产品内外表面质量中最重要因素之一。
工模具的结构、形状以及尺寸的合理性,可在一定程度上控制产品的内部组织和力学性能,尤其是在控制空心制品力学性能和焊缝组织的方面,分流孔大小、数量、形状以及分布的位置,焊合腔形状及尺寸、模芯结构等等起着决定性作用;
模子、挤压筒和挤压垫片的结构形状、尺寸和表面的质量,是对控制产品的缩尾和粗晶环、成层等等缺陷也会有一定作用;
模具结构形状和尺寸是对金属的流变、应力一应变场、挤压温度一速度场等等都有很大的影响,从而对于提高生产效率、减少能耗以及产品质量是有重大作用的;
工模具设计的合理性对于提高其装卸和更换速度,改善劳动条件,减少辅助时间以及保证生产的安全等方面有重大意义。
新型的工模具结构,对开发新工艺、新产品,研制新设备和新材料,不断的提高挤压技术中起着很大作用。
例如扁挤压筒、组合模、舌型模、变断面模、多层预紧应力模等,扁挤压筒,高比压的优质圆挤压筒以及异形管材模、特种型材模设计与制造的技术等等是铝挤压生产中的关键技术和核心。
其中的技术含量是在整个的挤压技术中占据有很大比例的。
而对中等批量挤压产品来说,工模具的成本是占总成本30%左右。
如果将其使用的寿命提高5~10倍,则产品成本可以大幅度的下降。
因此,模具是质量以及使用寿命可以说是评价某一种挤压方法或者挤压工艺的经济可行决定因素之一,合理的模具设计是实现铝合金挤压生产中高产、低耗、优质的最重要保证之一[2]。
国内外铝合金挤压模具技术的现状与发展趋势
1.3.1铝合金挤压模具设计的现状
工模具的设计一般是包括设计方法和设计理论的选择,模具的结构设计算以及尺寸确定,模具材料的选择,强度的校核和经济的技术指标评价等等。
模子、挤压垫片、挤压筒内衬、穿孔针等是直接参与到金属变形的工具,这种设计与一般的机械零件设计是不同,它是一种介于压力加工与机械加工之间的工艺性设计。
不仅需要考虑机械设计应该遵循的原则,而且需要挤压条件下的各种工艺性因素。
因此,模具的设计远远要比其它的工具设计复杂,要设计出经济并且合理的挤压工模具是一件非常困难的工作[3]。
在挤压技术的发展初期,一般是根据机械的设计原理,采用古典的强度理论与设计者实践的经验结合来设计管材、棒材以及普通的实心型材的模子。
随着挤压基础理论和弹性理论的发展,许多新的实践方法和理论已经开始用于挤压模具的设计及计算。
例如工程计算法、光弹光塑法、金属流动的坐标网络法、滑移线法、上限理论和密栅纹云法等都被广泛的用来确定工模具的工艺要素、结构以及强度的校核。
近些年以来,计算机虚拟设计、热挤压模拟法以及有限元法等发展的很快,同时也取得了良好的效果。
由于电子计算机技术发展,挤压工模具的计算机辅助设计(CAD)的技术已经开始进入实用的阶段,促使挤压工模具的设计来到了一个崭新时代。
现在,在工业发达的国家,挤压工模具的设计已经不再是只凭经验的手工操作,而是变成了连续进行的电子计算机自动控制优化设计的过程。
在我国对于铝合金的挤压工模具CAD技术方面的应用软件采用的是模块化的结构,图形的输入和二维变换来对工模具进行了优化设计。
型材截面的几何性质计算,分流孔的个数、形状、尺寸以及布置的设计,分流桥、模芯和焊合腔的尺寸、位置确定,模具的强度校核,上下模视图和剖面图的绘制,图形的剪裁,模垫的设计等等功能模块。
同时也能完成组合模和平面模的全过程设计,显著的提高了复杂模具设计的效率及质量,操作简单,运行可靠,已经达到了国外的同类系统先进的水平。
而且开发了铝合金型材导流模的设计手段,搞清楚了型材挤压的过程中金属的流动规律以及导流模在控制金属流速方面的机制,成功研制了三维的刚粘塑性方面有限元模拟以及建成导流模的模孔结构尺寸设计方面的数字模型。
经过生产的考核,证明了所开发出导流模的设计办法是正确可靠的,对于增大模具设计的一次性成功率,在提高型材的质量以及模具的使用寿命是具有积极的作用,同时也有了明显经济上的效益。
淘--宝..店--铺搜索:
“两个半学分”化方向发展
根据统计,世界各国已经装备的不同结构、类型、压力、用途的挤压机达了7000台以上,而其中美国有600多台,日本有400多台,德国有200多台,俄罗斯有400多台,中国有3000余台,且大部分都是15~25MN之间的中小型挤压机。
随着大型轰炸机、运输机、舰艇、航母、导弹等军事工业以及地下铁道、高速列车等等现代化的交通运输业的发展,是需大量整体壁板等的结构部件,所以挤压机开始向着大型化方向发展。
经过这几十年的发展,现在全世界已经正式投产使用万吨级以上的大型挤压机大约在20台以上,而拥有的国家是俄罗斯、美国、中国、西欧和日本。
最大的挤压机是位于前苏联的古比雪夫铝合金加工厂里200MN的挤压机,美国在2004年时把一个125MN的水压挤压机重装改造成为了世界上最大150MN的双动油压挤压机,日本在1967年已经把一台95MN的自给式油压机制造成功,德国的VAW波恩工厂于1999年投入生产了一台吨位为100MN双动油压式挤压机,意大利在2004年间投入生产了一台吨位为130MN的铜、铝油压式挤压机。
而我国除在西南铝业的1970年间投入生产了一台吨位为125MN的水压式挤压机外,在2004年以及2007年里分别在山东的丛林及辽宁忠旺投入生产了一台吨位为100MN以及一台吨位为125MN油压机。
据报道,国外的几个工业发达国家都在研究制造形式更为新颖、压力更大的挤压机,例如270MN的卧式挤压机和400~500MN级的挤压大直径管材的立式模锻—挤压联合水压机等等,现在我国正在建造150MN以及拟建225MN的挤压机各一台。
对于挤压机的本体方面,近些年来国外发展了预应力“T”型头板柱结构机架,预应力混凝土机架和钢板组合框架,并且大量的采用了扁挤压筒、活动模架、同定挤压垫片以及内置式的独立穿孔系统。
而传动形式的方面也发展自给油机的传动系统,甚至在100~150MN的挤压机上也同样采用油泵的直接传动装置,易知液压系统已经达到了一个高的水平里。
现代的挤压机以及它的辅助系统采用了CADEX等的控制系统和程序逻辑控制系统,也就是实现速度上的自动控制以及工模具自动的快速装卸、等温等速的挤压、甚至是全机的自动控制功能。
而挤压机所需机前的设备(例如锭坯的运送装置、坯料的热切装置以及长坯料的自动控制加热炉等等)及机后的设备(例如精密的水雾气在线淬火的装置、牵引机、拉伸的矫直机、人工时效炉、前梁锯、活动工作台、冷床及横向的运输装置、成品锯等)已实现了连续化和自动化的生产。
而且挤压的设备正向标准化、组装化和成套化的方向发展。
(2)特种模具技术和大型优质扁、圆挤压筒突破性的进展
从设计计算、装卸方法、结构选择、提高模具寿命、制模技术到新材料的研制等方面来看,挤压模具技术已经有了很大发展。
例如研发出了平面分流组合模、舌型模、前室模、叉架模、可卸模、导流模、水冷模、宽展模等,与此同时也出现多种形式的工具自动装卸机构和活动模架,这样不仅大大的简化了工模具的装卸操作,而且也节约了辅助的时间。
为了生产薄壁、扁宽、大断面的铝合金型材,就需要优质的扁挤压筒和高比压的圆挤压筒,而其使用的寿命短,造成大型高比压扁挤压筒的设计与制造成为了世界性的技术难题。
近些年来,由于有限元计算、淘--宝..店--铺搜索:
“两个半学分”计算机、工模具的材料及热处理等技术的进步,大型扁挤压筒的设计与制造技术出现了突破性的进展,美、俄、德、日等国家已经研制出了850mmx330mm、1100mmx300mm等,比压达了600MPa以上大型扁挤压筒,据悉使用的寿命大概在10000次左右,而我国已经研制出了670mm×
270mmxl600mm大型优质扁挤压筒。
大型的挤压工具装卸快速化、自动化方面也取得了很大进展,为全机的自动化创造出了条件。
在模具的材料方面,高合金化铬镍模具钢,例如德国的2779,美国的H11、H13,日本的SKD61,前苏联的4XMBqb,我国近些年来研制开发用于高温6000度以上,高温的强度要比H13钢还高一倍的YTRl8、YTR3A和SR+l等热挤压的工具钢出现以及新型的热处理方法,例如表面硬化处理、离子氮化处理和真空淬火等的应用,促使工模具的材料品质进步了。
电火花线切割加工(快走丝和慢走丝)和电火花加工技术用于制模,这样不仅提高模孔的硬度、精度,降低工作带的表面粗糙度,而且也大大的提高了制模的生产效率,为实现制模的自动化创造了良好的条件。
挤压模具的设计与制造运用电子计算机及模拟的技术,为实现工模具的设计和制造的自动化,提高模具质量及寿命开辟了新的道路。
(3)挤压工艺不断改进和完善
近些年来,除完善和改进了正向及反向挤压方法和其工艺外,也出现了许多增强挤压过程的新方法和新工艺,同时也获得了实际应用。
例如平面组合模挤压、舌型模挤压、水冷模挤压、变断面挤压、宽展挤压、扁挤压、半固态挤压、精密气水(雾)在淬火挤压、冷挤压、高速挤压、Conform连续挤压、高效反向挤压、等温挤压、连铸连挤、形变热处理、特种拉伸一辊矫等新的技术新的工艺对扩大铝合金型材品种,