不合格项判定参考Word格式文档下载.docx
《不合格项判定参考Word格式文档下载.docx》由会员分享,可在线阅读,更多相关《不合格项判定参考Word格式文档下载.docx(7页珍藏版)》请在冰豆网上搜索。
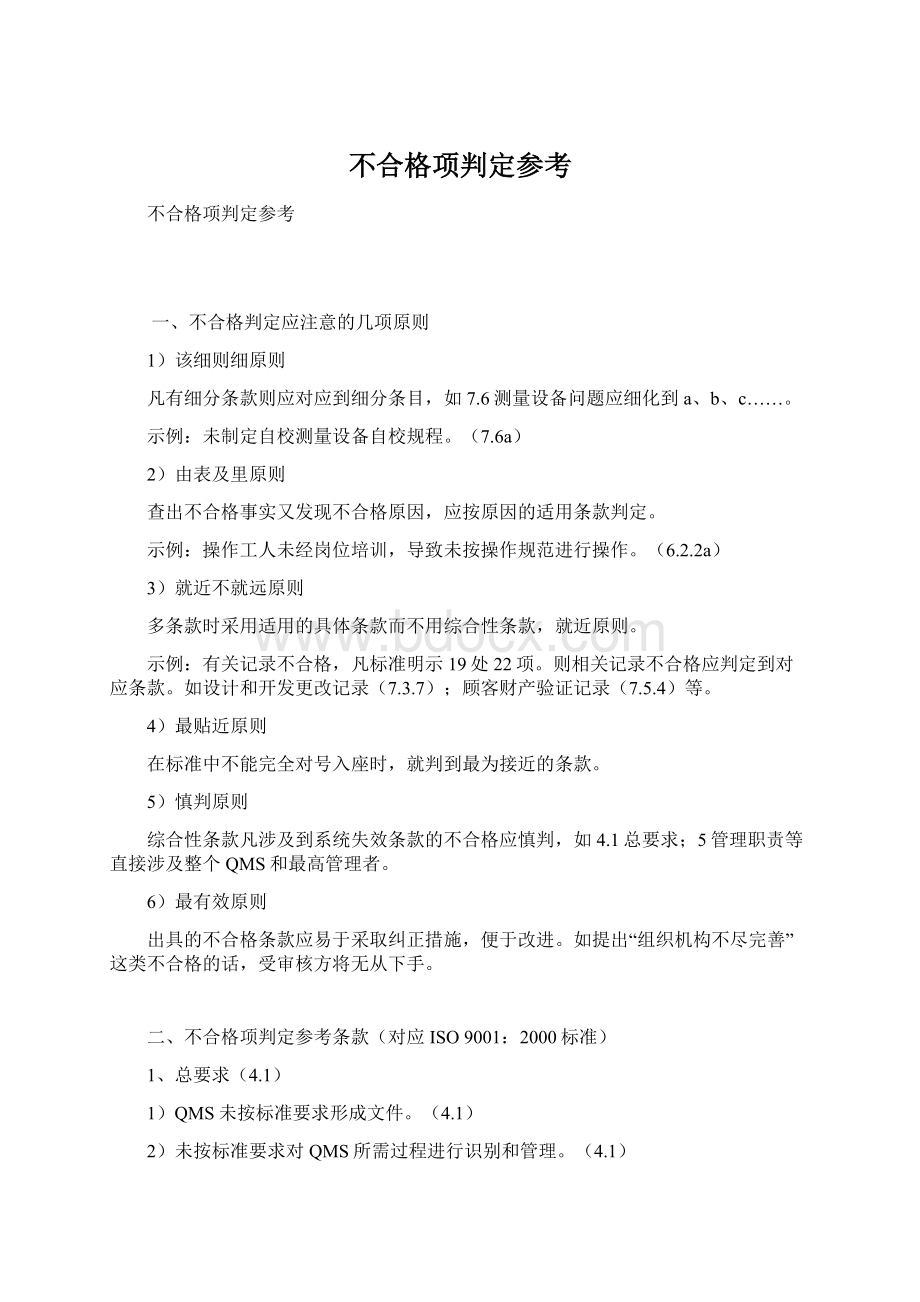
如提出“组织机构不尽完善”这类不合格的话,受审核方将无从下手。
二、不合格项判定参考条款(对应ISO9001:
2000标准)
1、总要求(4.1)
1)QMS未按标准要求形成文件。
(4.1)
2)未按标准要求对QMS所需过程进行识别和管理。
3)对影响产品符合要求的外包过程未进行识别和控制。
2、文件要求(4.2)
1)质量手册删减不合理。
(4.2.2a)
2)质量手册内容的覆盖面不完整。
3)质量手册未包含程序文件主要内容或对其引用。
(4.2.2b)
4)质量手册各过程的描述未反映组织产品的特点。
(4.2.2c)
5)质量手册未按4.2.3文件控制要求进行控制。
(4.2.3)
6)未按标准要求形成文件/记录控制程序。
(4.2.3/4.2.4)
7)文件发布前XX人员审批其适用性。
(4.2.3a)
8)文件修改后未经重新审批。
(4.2.3b)
9)未经修改后未按规定进行标识。
(4.2.3c)
10)使用处不能得到相应文件有效版本,或使用不受控文件。
(4.2.3d)
11)外来文件未得到识别和控制。
(4.2.3e)
12)现场有效版本和作废版本共存。
(4.2.3g)
13)现场只有作废版本。
14)未对作废文件进行标识。
15)文件修改不按规定程序。
16)记录未按规定进行管理。
(4.2.4)
三、管理职责(5)
1)最高管理者不能为管理承诺提供相关证据。
(5.1)
2)最高管理者未能向组织成员传达满足顾客和法律法规要求的重要性。
(5.1a)
3)质量方针/质量目标不符合标准要求。
(5.3/5.4.1)
4)质量方针/质量目标不能在组织内得到沟通和理解。
(5.3d)
5)质量方针/质量目标未经最高管理者签字批准。
(4.2.3a)
6)未对质量方针/质量目标持续适宜性进行评审。
(5.3e)
7)质量目标未能在相关职能和层次上展开分解。
(5.4.1)
8)对质量目标未进行测量。
9)质量目标不能反映产品特性。
10)质量目标与质量方针相矛盾。
11)组织结构不合理、职责和权限不清。
(5.5.1)
12)管理评审未进行。
(5.6)
13)管理评审内容不符合标准要求。
(5.6.2/5.6.3)
14)管理评审未保存原始记录。
(5.6.1)
15)管理评审时间间隔不符合要求。
16)管理评审输出改进措施未进行跟踪验证。
(8.5.2d/8.5.3e)
四、资源管理(6)
1)未能确定相关岗位人员能力要求。
(6.2.1a)
2)岗位人员未经培训考核,不能胜任工作就上岗。
(6.2.2b)
3)虽经培训或采取措施但未对其有效性进行评价。
(6.2.2c)
4)员工不能意识到所从事活动的相关性和重要性。
(6.2.2d)
5)特殊工作人员、检验、计量、内审人员未按规定进行培训。
(6.2.2)
6)未保持教育、经历、培训和资格的适当记录。
(6.2.2e)
7)生产设施/设备不能满足产品实现需求。
(6.3)
8)对基础设施未进行适当维修和保养。
9)现场的工作环境不符合产品实现要求。
(6.4)
五、产品实现(7)
1)对特定产品、项目或合同未进行产品实现策划。
(7.1)
2)产品实现策划不满足要求。
3)产品有关的要求中未反映相关法律法规要求。
(7.2.1c)
4)未在合同签订前进行合同评审。
(7.2.2)
5)只对重大合同进行评审,未对零星、口头、电话订单进行评审。
6)未对顾客特殊要求进行识别。
(7.2.1)
7)签约后发现组织没有履约能力。
(7.2.2c)
8)合同更改未按规定进行。
9)合同更改后的要求未能传递到相关部门/人。
10)网上销售有关的产品信息未进行评审。
11)评审结果及其所引发的措施的记录未保存。
12)对新产品设计和开发未进行策划。
(7.3.1)
13)设计和开发策划中未明确分工和接口管理。
(7.3.1c)
14)设计输入未包括适用的法律法规要求。
(7.3.2b)
15)未对设计输入进行评审。
(7.3.2)
16)设计输出放行前未经审批。
(7.3.3)
17)设计未考虑重大设计特性(如可维修性)。
(7.3.3d)
18)设计未评审或评审不合格仍投产。
(7.3.4)
19)设计评审结果及其采取的记录未保持。
20)设计未验证或验证不合格仍投产。
(7.3.5)
21)验证结果记录未保存。
22)设计确认未进行或确认不合格仍投产。
(7.3.6)
23)确认结果记录未保存。
24)设计确认不符合标准要求。
25)设
计和开发更改未按标准要求进行。
(7.3.7)
26)设计更改评审结果记录未保存。
27)未根据满足产品能力的要求评价和选择供方。
(7.4.1)
28)未按标准要求制定选择评价和重新评价的准则。
29)采购文件中未规定产品质量要求和验收准则。
(7.4.2)
30)未按规定到合格供方进行采购。
31)采购文件发放前未进行审批。
32)委托服务等活动未对供方进行评审。
33)对采购产品的验证方式未在采购文件中规定。
(7.4.3)
34)未对采购产品实施验证。
35)供方评价结果记录未保持。
36)由于缺少书面文件而影响产品质量。
(7.5.1b)
37)未按文件规定要求进行操作。
(7.5.1)
38)生产设备不满足生产能力要求。
(7.5.1c)
39)生产过程未实施监测。
(7.5.1e)
40)未能识别特殊过程或对其过程能力未确认。
(7.5.2)
41)未对特殊过程的设备进行认可和人员资格进行鉴定。
(7.5.2b)
42)未制定特殊过程确认准则。
(7.5.2a)
43)未保存过程确认记录。
(7.5.2d)
44)库房产品未进行标识或标识不清。
(7.5.3)
45)生产现场产品未进行标识或标识不清。
46)有可追溯要求情况,无唯一性标识,致使出了问题无法追溯。
47)原材料紧急放行或半成品例外放行未加标识。
(8.2.4)
48)包装标识不符合要求。
(7.5.5)
49)不合格品未加标识。
(8.3)
50)未对顾客财产进行验证,也未保管好。
(7.5.4)
51)顾客财产不适用或损坏未记录并向顾客报告。
52)交付搬运过程造成产品标识损失或产品损坏。
53)产品贮存不符合产品要求。
54)产品包装不符合产品要求。
55)未按周期检定/校准要求按时间进行检定/校准。
(7.6)
56)无溯源或国家标准时,测量设备未进行自校或无自校规程也无记录。
57)测量设备无检验状态标志。
(7.6c)
58)在搬运贮存过程造成测量设备失准或损坏。
(7.6e)
59)试验软件作为检验手段未对其能力进行确认。
60)当测量设备失准及未对其测量结果的有效性进行评价和记录。
六、测量分析和改进(8)
1)对顾客满意度的信息未进行收集、利用或未进行测量。
(8.2.1)
2)未按标准要求形成内部审核程序。
(8.2.2)
3)未按策划要求进行内部审核。
4)内审计划和检查表中内容均未包括最高管理者。
5)内审员未经培训或资格证实。
6)内审员审核了自己负责的工作。
7)内审后未采取纠正措施或其他验证。
8)内审记录不完整。
9)未
编制检验计划或检验规范。
10)未按检验计划或规范进行检验。
11)产品放行和交付(特例)XX人批准和顾客批准。
12)检验记录检验人员未签字。
13)检验记录或报告不符合标准要求(如项目不全)。
14)检验原始记录未建立或保存。
15)检验规范规定的统计抽样检验方法不全。
(8.1)
16)出了不合格品不标识、不隔离。
17)出了不合格品不评审、不处置。
18)让步使用、放行或接收XX人员批准或顾客批准。
(8.3b)
19)返工/返修产品未进行检验。
20)产品交付或投入使用后发现不合格未采取相应措施。
21)出了不合格品不通知有关部门或由无资格的人员进行处理。
22)未按标准要求保持不合格品相关记录。
23)未能明确收集、分析数据的方法。
(8.4)
24)未采用组织适用的统计技术。
25)数据分析未能用于改进。
26)纠正/预防措施未按标准要求形成文件程序。
(8.5.2/8.5.3)
27)出了不合格不分析原因、不采取纠正措施。
(8.5.2b)
28)对顾客投诉不分析、不处理。
(8.5.2a)
29)对顾客反馈意见不处理也不及时与顾客沟通。
(7.2.3c)
30)纠正/预防措施实施结果未记录也未进行跟踪验证。
(8.5.2e/8.5.3d)
31)对采取的纠正/预防措施未进行评审。
(8.5.2f/8.5.3e)
END