硅酸盐水泥资料Word格式文档下载.docx
《硅酸盐水泥资料Word格式文档下载.docx》由会员分享,可在线阅读,更多相关《硅酸盐水泥资料Word格式文档下载.docx(15页珍藏版)》请在冰豆网上搜索。
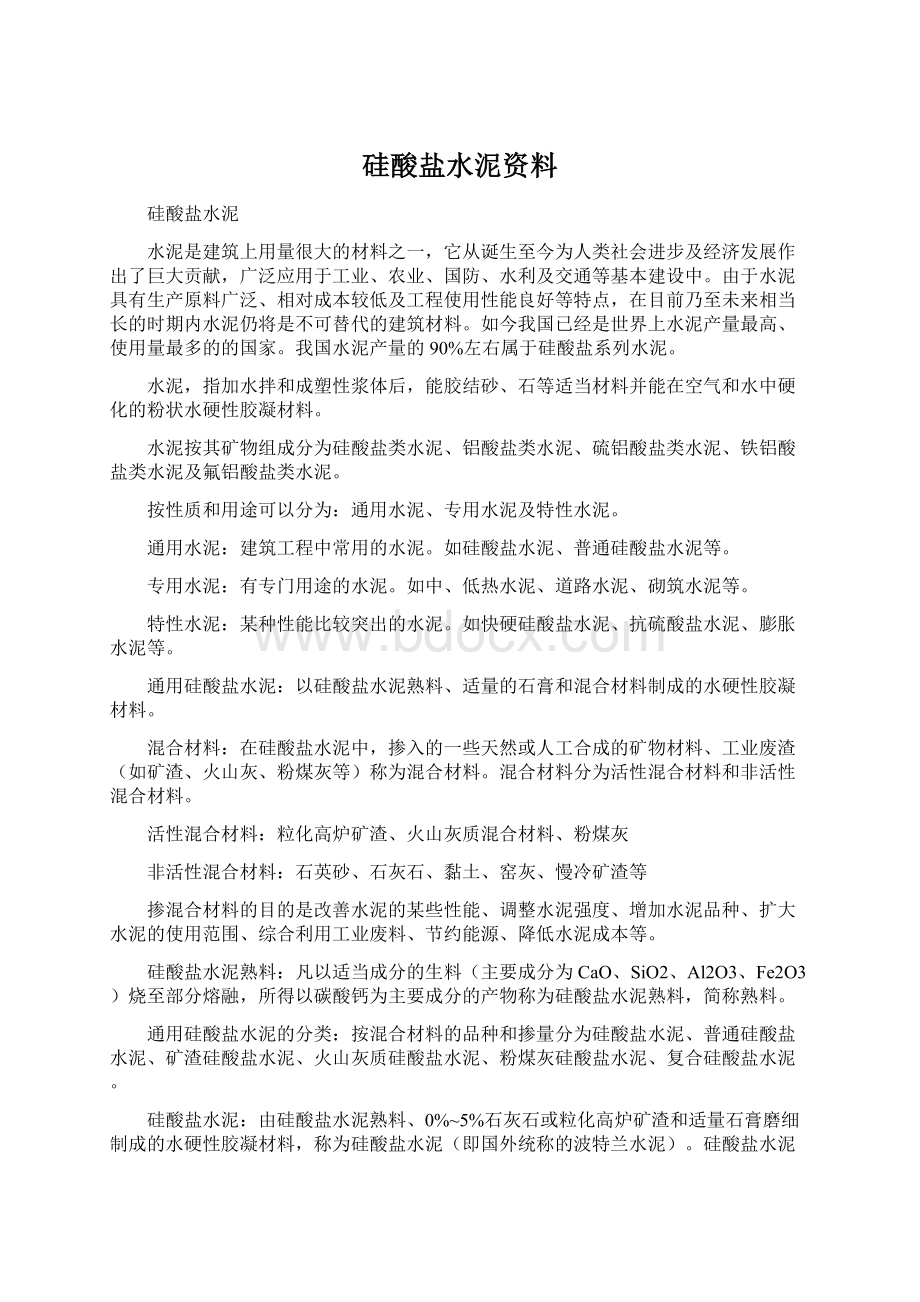
Ⅱ型(掺5%以下的混合材料),代号P·
Ⅱ。
普通硅酸盐水泥:
由硅酸盐水泥熟料,活性混合材料掺加量>5%且≤20%,并允许用不超过水泥质量的8%的非活性材料或不超过水泥质量5%的窑灰代替部分活性混合材料,及适量石膏磨细制成不水硬性胶凝材料称为普通硅酸盐水泥(简称普通水泥),代号P·
O。
矿渣硅酸盐水泥:
由硅酸盐水泥熟料、粒化高炉矿渣和适量石膏磨细制成的水硬性胶凝材料,称为矿渣硅酸盐水泥(简称矿渣水泥)。
矿渣硅酸盐水泥分为A、B型两类。
A型粒化高炉矿渣掺量(按质量百分比计)>20%且≤50%,代号P·
S·
A;
B型矿渣掺量>50%且≤70%,代号P·
B。
其中允许用不超过水泥质量8%的活性混合材料、非活性混合材料和窑灰中的任何一种材料代替部分矿渣。
火山灰质硅酸盐水泥:
由硅酸盐水泥熟料、>20%且≤40%的火山灰质混合材料和适量石膏磨细制成的水硬性胶凝材料,称为火山灰质硅酸盐水泥(简称火山灰水泥),代号P·
P。
粉煤灰硅酸盐水泥:
由硅酸盐水泥熟料、>20%且≤40%粉煤灰和适量石膏磨细制成的水硬性胶凝材料,称为粉煤灰硅酸盐水泥(简称粉煤灰水泥),代号P·
F。
复合硅酸盐水泥:
由硅酸盐水泥熟料、两种或两种以上>20%且≤50%的混合材料、适量石膏磨细制成的水硬性胶凝材料,称为复合硅酸盐水泥(简称复合水泥),代号P·
C。
其中,混合材料允许用不超过水泥质量8%的窑灰代替,掺矿渣时混合材料掺量不得与矿渣硅酸盐水泥重复。
水泥包装袋上的标志:
水泥品种名称、代号、强度等级、出厂日期、净含量、生产单位和厂址、执行标准号、生产许可证标志及编号、出厂编号、包装年月日。
硅酸盐水泥的生产
原料:
生产硅酸盐水泥的主要原料是石灰质原料和黏土质原料。
石灰质原料,如石灰石、白垩等,主要为生产水泥提供CaO;
黏土质原料,如黏土、页岩等,主要为生产水泥提供SiO2、Al2O3和Fe2O3。
有时两种原料中的成分不能满足生产要求,还需要加入少量的调节性原料(校正原料),如铁质校正原料和硅质校正原料。
生产工艺:
1.将原料按一定比例配料并磨细成符合成分要求的生料。
2.将生料煅烧使之部分熔融形成熟料。
3.将熟料与适量石膏共同磨细成为硅酸盐水泥。
石灰石石灰石或矿渣
磨细
1450℃
煅烧
按比例
配合磨细
适量
粘土生料熟料硅酸盐水泥
铁矿粉石膏
总结为“两磨一烧”。
生料:
CaO62%~67%SiO220%~24%Al2O34%~7%Fe2O32.5%~6%
生料在窑内经历过程:
干燥—预热—分解—烧成—冷却
硅酸盐水泥熟料主要矿物组成
在煅烧过程中,生料脱水后分解出CaO、SiO2、Al2O3、Fe2O3,在高温下它们形成了以碳酸钙为主的矿物,所以称为硅酸盐水泥。
1.主要成分
硅酸三钙3CaO·
SiO2,简式C3S,含量为37%~60%,密度为3.25g/cm3。
硅酸二钙2CaO·
SiO2,简式C2S,含量为15%~37%,密度为3.28g/cm3。
铝酸三钙3CaO·
Al2O3,简式C3A,含量为7%~15%,密度为3.04g/cm3。
铁铝酸四钙4CaO·
Al2O3·
Fe2O3,简式C4AF,含量为10%~18%,密度为3.77g/cm3。
在硅酸盐水泥熟料的4种矿物组成中,硅酸三钙和硅酸二钙的总含量约为75%,铝酸三钙和铁铝酸四钙的总含量约为25%。
各种矿物单独与水作用所表现出的特性如下:
表1硅酸盐水泥熟料主要矿物的特性
性能指标
熟料矿物
硅酸三钙C3S
硅酸二钙C2S
铝酸三钙C3A
铁铝酸四钙C4AF
水化速率
快
慢
最快
快,仅次于C3A
凝结硬化速率
28d放热量
多
少
最多
中
强
度
早期
高
低
后期
强度发展
较快
耐化学腐蚀
差
最差
好
干缩性
大
小
水泥熟料是由各种不同特性的矿物所组成的混合物,因此改变孰料矿物成分之间的比例,水泥的性质会发生相应的变化。
2.其他成分
除了这些主要矿物外,硅酸盐水泥中还含有少量的游离氧化钙(CaO)、游离氧化镁(MgO)等,其含量过高将造成水泥的安定性不良;
碱矿物及玻璃体等,其中的Na2O和K2O含量较高时,遇到活性骨料时,易产生碱骨料反应,影响混凝土的质量。
3.石膏
水泥中掺入石膏的主要作用是调节水泥凝结硬化的速度。
如不掺入少量的石膏,水泥浆可在很短的时间内迅速凝结。
掺入少量石膏后,石膏与凝结最快的铝酸三钙(3CaO·
Al2O3)反应,生成硫铝酸钙沉淀包围水泥,延缓水泥的凝结时间,一般掺量为2%~5%,过多的石膏会引起强度下降或产生瞬凝,安定性不良。
硅酸盐水泥的水化
水泥和水拌合,表面的熟料矿物立即与水发生化学反应,各组分开始逐渐溶解,放出一定的热量,固相体积也逐渐增加。
其反应式如下:
2(3CaO·
SiO2)+6H2O→3CaO·
2SiO2·
3H2O+3Ca(OH)2
与水作用特性:
水化速度较快,水化热大,水化产物主要在早期产生,早期强度最高,且能得到不断增长,是决定水泥强度高低的最主要矿物。
2(2CaO·
SiO2)+4H2O→3CaO·
3H2O+Ca(OH)2
水化速度慢,水化热小,其消化产物和水化热主要在后期产生,对水泥早期强度贡献很小,但对其后期强度增加至关重要。
3CaO·
Al2O3+6H2O→3CaO·
6H2O
水化速度最快,水化热最集中,如果不掺入石膏,易造成水泥速凝,它的水化产物大多在3d内就产生,但强度并不高,以后也不再增长,甚至出现倒缩,硬化时所表现出的体积收缩也最大,耐硫酸性能差。
4CaO·
Fe2O3+7H2O→3CaO·
6H2O+CaO·
Fe2O3·
H2O
水化速度介于铝酸三钙与硅酸三钙之间,强度发展主要在早期,强度偏低,它的突出特点是抗冲击性能和抗硫酸盐性能好。
生产水泥时,为调节凝结时间而掺入的石膏也需参加反应,即:
6H2O+3(CaSO4·
2H2O)+20H2O→3CaO·
3CaSO4·
32H2O
当石膏耗尽时,水中未水化的C3A会与钙矾石作用生成低硫型的水化硫铝酸钙,即:
32H2O+2(3CaO·
Al2O3)+4H2O→
3(3CaO·
CaSO4·
12H2O)
纯水泥熟料磨细加水后凝结时间很短,给水泥的施工应用造成不便。
掺入适量石膏,这些石膏与铝酸三钙反应生成水化硫铝酸钙,覆盖于未水化的铝酸三钙周围,阻止其继续快速水化,由于消化硫铝酸钙非常难溶,迅速沉淀结晶形成针头晶体,包裹于铝酸盐矿物表面阻止水分与其接触和反应,因而延缓了水泥的凝结时间。
但如果石膏过多,会引起水泥体积安定性不良。
由上可知,所得主要水化产物(在完全水化的水泥石中)为:
1.水化碳酸钙凝胶70%,是水泥石形成强度的最主要化合物。
2.氢氧化钙晶体20%
3.水化铝酸钙3%
4.高硫型水化硫铝酸钙(钙矾石)7%
水化反应为放热反应,放出的热量称为水化热。
水化热大,放热的周期也较长,但大部分热量(50%以上)是在3天以内,特别是在水泥浆发生凝结、硬化的初期放出。
生成新的化合物称为水化产物。
硅酸盐水泥的凝结硬化
水泥的凝结与硬化过程是很复杂的物理化学过程,水化是水泥产生凝结硬化的前提,而凝结硬化是水泥水化的结果。
水泥加不水拌合后,水泥颗粒分散于水中,成为水泥浆体。
水泥颗粒与水接触后,一些物质溶解于水中,并很快达到饱和状态,开始沉淀形成微小的颗粒;
还有一些物质直接与水反应生成水化产物,并包裹于水泥颗粒表面。
水分透过水化产物包裹层,将可溶的物质溶解并透过水化产物层带出并沉淀,渐渐长大成为晶体。
由于水分渗入速度慢,水泥的水化速度减慢。
随着水分渗入量增多,溶解物质溶液很难渗出,即产生了渗透压力。
可溶物质在包裹层内沉淀形成微小晶体,以及直接与水反应生成的水化产物增多,包裹层发生了破裂。
水分与新的水泥颗粒接触,发生了快速水化反应,水化产物增多,颗粒之间的水分减少,颗粒相互接触,水泥浆粘度增加,渐渐失去可塑性,水泥浆进入凝结过程。
初凝:
水泥浆体开始失去流动性和部分可塑性,但不具有强度,这一过程称为初凝。
终凝:
水泥浆体完全失去可塑性,并开始具有一定强度称为终凝。
由初凝到终凝的过程称为水泥的凝结。
硬化:
随着水化反应的继续进行,水泥浆体孔隙减少,密实度增加,产生了强度且不断增加,最终发展成具有一定强度的石状物(水泥石),这一过程称为水泥的硬化。
硬化的过程在开始时速度很快,28d以后硬化开始减慢。
硬化过程可以持续几所甚至几十年。
水泥的水化和凝结硬化是从水泥颗粒表面开始,逐渐往水泥颗粒的内核深入进行。
开始时水化较快,但由于水化不断进行,规程在水泥颗粒周围的水化产物不断增多,阻碍水和水泥未水化部分的接触,水化减慢,但无论时间多久,水泥颗粒的内核很难完全水化。
因此,硬化后的水泥石由水泥凝胶、未完全水化的水泥颗粒、毛细孔(含毛细孔水)组成的不匀质结构体。
影响硅酸盐水泥凝结硬化的因素
影响硅酸盐水泥凝结硬化的因素主要有:
水泥熟料的矿物组成、水泥细度、石膏掺量、拌合水量、养护湿度、养护温度、养护龄期、外加剂。
水泥熟料的矿物组成:
是影响水泥水化速度、凝结硬化过程及强度的主要因素。
改变熟料中矿物组成的相对含量,可配制成具有不同特性的硅酸盐水泥。
如提高C3S含量,可制得快硬硅酸盐水泥;
减少C3S和C3A的含量,提高C2S的含量,可制得水化热低的低热水泥;
降低C3A的含量,提高C4AF的含量,可制得耐硫酸盐水泥。
水泥细度:
水泥的细度即水泥颗粒的粗细程度。
水泥颗粒越细,颗粒表面与水的接触面积越大,水化反应越快,凝结硬化速度越快,早期强度也就越高。
但过细时,易与空气中的水分及二氧化碳反应而降低活性,并且硬化时收缩也越大,且成本高,因此,水泥的细度应适当,硅酸盐水泥的比表面积应大于300m2/Kg。
石膏掺量:
水泥中掺入少量石膏,可调节水泥凝结硬化的速度。
如果掺入过多的石膏,不仅缓凝作用不大,还会引起水泥安定性不良,一般情况下,掺量约占水泥重量的3%~5%,具体掺量需通过试验确定。
拌合水量:
拌合水量越多,水化后形成的胶体较稀,水泥的凝结硬化就越慢。
养护湿度:
水泥石的强度只有在潮湿的环境中才能不断增长。
若处于干燥环境中,当水分蒸发完毕后,水化作用无法继续进行,硬化即行停止,强度也不再增长。
因此,混凝土在浇筑后两到三周必须加强洒水养护。
养护温度:
温度对水泥的水化以及凝结硬化的影响很大。
当温度高时,水泥的水化作用加快,从而凝结硬化速度也就加快,所以采用蒸汽养护是加快凝结硬化的方法之一;
当温度低时,凝结硬化速度减慢;
当温度低于0℃时,水化基本停止。
因此,冬期施工时,须采用保温措施,以保证水泥正常凝结和强度的正常发展。
养护龄期:
水泥水化硬化是一个较长的时期,不断进行的过程,随着龄期的增长水泥石的强度逐渐提高,水泥在3~14天内强度增长较快,28天后增长缓慢,水泥强度的增长可延续几年甚至几十年。
外加剂:
凡对硅酸三钙和铝酸三钙的水化能产生影响的外加剂,都能影响硅酸盐水泥的水化和凝结硬化。
如加入缓凝剂会延缓水泥的水化、硬化,影响水泥早期强度发展;
掺入早强剂会促进水泥的凝结硬化,提高其早期强度。
硅酸盐水泥的技术要求
化学指标有:
不溶物、烧失量、MgO/SO3、碱含量、氯离子
物理指标有:
凝结时间、体积安定性、强度、细度(选择性指标)、水化热
不溶物:
水泥煅烧过程中存留的残渣,主要来自原料中的黏土和结晶二氧化硅,因煅烧不良化学反应不充分而未能形成熟料产物,经酸或碱处理不能被溶解的残留物,是水泥的活性组分之一,含量高对水泥质量有不良影响。
Ⅰ型硅酸盐水泥中不溶物不得超过0.75%,Ⅱ型硅酸盐水泥中不溶物不超过1.50%。
烧失量:
水泥煅烧不佳或受潮使得水泥在在规定温度加热时产生的质量损失,常用来控制石膏和混合材料中的杂质,以保证水泥质量。
Ⅰ型硅酸盐水泥中烧失量不得大于3.0%,Ⅱ型硅酸盐水泥中烧失量不得大于3.5%。
MgO/SO3:
水泥中游离的MgO和SO3过高时时,会引起水泥的体积安定性不良,氧化镁含量不宜超过5.0%,如果水泥经压蒸安定性试验合格,则水泥中氧化镁的含量可放宽到6.0%。
三氧化硫含量不得超过3.5%。
碱含量:
碱含量(选择性指标)按Na2O+0.658K2O计算值来表示。
水泥中含碱是引起混凝土产生碱骨料反应的条件。
为避免碱骨料反应的发生,若使用活性骨料,用户要求提供低碱水泥时,水泥中碱含量不得大于0.60%。
氯离子:
水泥中的Cl-是引起混凝土中钢筋锈蚀的因素之一,要求限制其含量(质量分数)在0.06%以内。
以上五项,检验结果不符合标准规定的任何一项技术要求,则该水泥为不合格产品。
细度:
水泥的细度表示水泥颗粒的粗细程度,即水泥磨细的程度。
通常用比表面积法或筛分析法来测定,国家标准中规定,硅酸盐水泥比表面积应大于300m2/kg。
水泥的细度对水泥的性能影响很大,水泥颗粒越细,与水接触面积越大,水化反应就越快,这对强度的发展,尤其是早期强度是非常有利的。
但也不宜太细,水泥磨的太细,一方面在储存期间易吸潮而降低强度,另一方面也会大量增加粉磨的能耗。
水泥细度有两种表示方法:
一种是比表面积即单位质量水泥粉末总表面积表示,用勃氏法检测;
另一种是用80μm或45μm方孔筛的筛余百分数表示。
用筛分析法。
《<
通用硅酸盐水泥>
国家标准第1号修改单》(GB175-2007/XGL-2009)规定:
硅酸盐水泥和普通硅酸盐水泥的细度以比表面积表示,其比表面积不小于300m2/kg;
其他四种水泥的细度以筛余率表示,其80μm(0.08mm)方孔筛筛余率不大于10%或45μm方孔筛筛余率不大于30%。
凝结时间:
水泥的凝结时间是影响混凝土施工难易程度和速度的主要指标,分为初凝时间和终凝时间两种。
水泥的凝结时间是指水泥从加水拌和开始,至水泥浆失去流动性,即水泥从可塑状态发展到固体状态所需的时间。
初凝时间:
从水泥加水拌和开始至水泥浆体开始失去可塑性所需的时间称为初凝时间。
终凝时间:
从水泥加水开始至水泥浆体完全失去可塑性所需的时间称为终凝时间。
水泥初凝时间不宜过早,以便施工时有足够的时间来完成混凝土或砂浆的搅拌、运输、浇筑、振捣和砌筑等操作;
水泥终凝不宜过迟,以便使混凝土能尽快地硬化达到一定的强度,以利于下一道工序的进行。
根据《<
6种水泥的初凝时间不得早于45min;
硅酸盐水泥的终凝时间不得迟于390min(6.5h),其他5种水泥的终凝时间不得迟于600min(10h)。
实际上硅酸盐水泥的初凝时间一般为1~3h,终凝时间一般为5~8h。
用维卡仪来测定凝结时间。
影响水泥凝结时间的因素很多,如熟料的矿物组成、水泥的细度、环境的温度和湿度、拌和水量等。
使用时可加入调凝剂来调整水泥的凝结速度。
如:
水泥熟料中铝酸三钙含量越多,水泥中石膏越少,水泥的凝结时间越短;
水泥越细,水灰比越小,水泥浆的凝结时间越短;
温度越高,相对湿度越低,水泥浆凝结时间越短。
对于检验结果不符合凝结时间标准要求的水泥视为不合格品。
体积安定性:
水泥的体积安定性是指水泥在凝结硬化过程中体积变化的均匀性,是水泥在施工中保证质量的一项重要技术性指标。
体积安定性是水泥浆体在硬化后体积变化的稳定性。
若水泥浆体硬化后产生不均匀的体积变化,即所谓的安定性不良,会使混凝土产生膨胀性裂缝,降低工程质量,甚至引起严重事故。
故体积安定性不良的水泥不能用于工程结构中。
引起水泥体积安定性不良的原因主要有:
1.游离氧化钙过量
熟料中含有较多过烧的游离氧化钙,水化速度很慢,在水泥硬化后才发生以下的反应:
CaO+H2O=Ca(OH)2该反应使水泥石体积膨胀,会导致水泥石开裂。
测试方法:
沸煮法检验。
试饼法(代用法)和雷氏法(标准法)
2.游离氧化镁过量
水泥中的游离氧化镁形成结晶方镁石时,其晶体结构致密,水化速度比游离氧化钙还要慢,要几个月甚至几年才发生明显水化反应,生成氢氧化镁,体积膨胀导致水泥石安定性不良。
压蒸法检验。
3.石膏掺量过多
当石膏掺量过多时,在水泥浆体硬化后,过量石膏还会继续与水化铝酸钙反应生成高硫型水化硫铝酸钙,体积约增大1.5倍,从而导致水泥石开裂,即体积安定性不良。
长期在常温水中观察,不便于快速检验。
检验结果不符合标准要求的水泥为不合格品。
强度:
水泥强度是指水泥抵抗外力破坏的能力,是表明水泥品质的重要指标,是评定水泥强度等级的依据。
水泥的强度按《水泥胶砂强度检验方法》(GB/T17671-1999)(ISO法)中的规定进行。
其规定如下:
将水泥、标准砂和水按规定比例(1:
3.0:
0.50)拌和一锅胶砂,制成三条40mm×
40mm×
160mm的标准试件,在标准养护条件下养护,测定其3d和28d的抗折强度和抗压强度,按照3d和28d的抗折强度和抗压强度将硅酸盐水泥的强度等级划分为6个:
42.5、42.5R、52.5、52.5R、62.5、62.5R;
普通硅酸盐水泥划分为4个:
42.5、42.5R、52.5、52.5R;
其他4种水泥的强度等级划分为6个:
32.5、32.5R、42.5、42.5R、52.5、52.5R。
其中:
R型水泥为早强型,主要是3d强度较同强度等级水泥高。
例如:
62.5R表示水泥28d强度不低于62.5MPa,属早强型水泥。
水化热:
水泥与水发生水化反应所放出的热量称为水化热,通常用J/Kg表示。
水化热的大小主要与水泥的细度及矿物组成有关。
颗粒越细,水化热越大;
矿物中C3S、C3A含量越多,水化放出热越高。
大部分的水化热集中在早期放出,3~7d以后逐步减少。
水化热放热对冬季施工的混凝土有利,但对大体积混凝土工程不利。
因为水化热产生较大温差,引起温度应力,使混凝土产生裂缝。
对于大体积混凝土工程,应采用低热水泥,否则应采取必要的降温措施。
硅酸盐水泥石的腐蚀和防止
在某些腐蚀性介质的作用下,水泥石的结构逐渐遭到破坏,强度下降以至全部崩溃的现象为水泥石的腐蚀。
水泥石的抗腐蚀系数用耐蚀系数表示,以同一龄期浸在侵蚀性溶液中的水泥试体强度与在淡水中养护的水泥试体强度之比表示。
耐蚀系数越大,水泥的抗侵蚀性越好。
一、产生水泥石腐蚀的原因主要有以下几种:
1.软水腐蚀(溶出性腐蚀)
雨水、雪水、工业冷凝水、蒸馏水以及含重硅酸盐甚少的河水、湖水均属于软水。
水泥石中的氢氧化钙(Ca(OH)2)在软水中有较大的溶解度。
①在静水中或无压力的水中,溶解仅限于表面,对水泥石影响不大。
②在流动水及有压力的水中,Ca(OH)2不断溶出被带走,腐蚀也在不断进行。
由于水泥石中Ca(OH)2浓度不断降低,还会造成水泥石中其他水化产物的分解,最终引起水泥石强度降低甚至使结构破坏。
③含重硅酸盐甚少的硬水中,产生如下反应:
Ca(OH)2+Ca(HCO3)2→CaCO3+2H2O生成的CaCO3积聚于水泥石的空隙,形成密实保护层,阻止外界水入侵和内部Ca(OH)2析出。
2.酸性腐蚀
①碳酸腐蚀
工业污水及地下水中常溶解有较多的二氧化碳。
水中二氧化碳和水泥石中氢氧化钙反应生成不溶于水的碳酸钙,再与水中的二氧化碳反应生成易溶于水的碳酸氢钙,由于碳酸氢钙的不断溶解,造成氢氧化钙不断溶出,水泥石的其他水化产物不断分解,使水泥石结构破坏。
反应方程式如下:
Ca(OH)2+CO2+H2O=CaCO3+2H2O
CaCO3+CO2+H2O=Ca(HCO3)2
②一般酸的腐蚀
在工业污水、地下水、沼泽水中常含有一定量的不同种类的酸,其中有无机酸和有机酸。
这些酸与水泥石中的氢氧化钙作用,生成的化合物有的易溶于水,有的体积膨胀,使水泥石受到破坏,其中硫酸、盐酸、氢氟酸和醋酸、蚁酸及乳酸等对水泥石的腐蚀最为严重。
如盐酸和硫酸分别与水泥石中的氢氧化钙反应:
2HCl+Ca(OH)2=CaCl2+2H2O氯化钙易溶于水而导致化学腐蚀型破坏
H2SO4+Ca(OH)2→CaSO4·
2H2O石膏对水泥石产生硫酸盐膨胀型破坏
3.盐类腐蚀
海水、地下水中常含有大量镁盐,镁盐与水泥石接触后,会与氢氧化钙发生置换反应,生成无胶凝性的氢氧化镁。
即:
Ca(OH)2+Mg2+=Mg(OH)2+Ca2+
硫酸盐对水泥石的腐蚀与硫酸的腐蚀作用相同,而硫酸镁对水泥石的腐蚀包括镁盐和硫酸盐的双重腐蚀作用。
4.强碱腐蚀
强碱(如氢氧化钠)与水泥中未水化的铝酸钙反应生成易溶的铝酸钠,即
Al2O3+6NaOH=3Na2O·
Al2O3+3Ca(OH)2
当水泥石被氢氧化钠溶液浸透后,又在空气中干燥,氢氧化钠会与空气中的二氧化碳反应,生成膨胀性的碳酸钠,即:
2NaOH+CO2=Na2CO3+H2O
碳酸钠在水泥石毛细孔中结晶深沉,可以使水泥石胀裂。
二、水泥石腐蚀的基本原因
通过上述几种腐蚀类型,可以得出水泥石腐蚀的基本原