煤气发生炉使用说明书Word下载.docx
《煤气发生炉使用说明书Word下载.docx》由会员分享,可在线阅读,更多相关《煤气发生炉使用说明书Word下载.docx(15页珍藏版)》请在冰豆网上搜索。
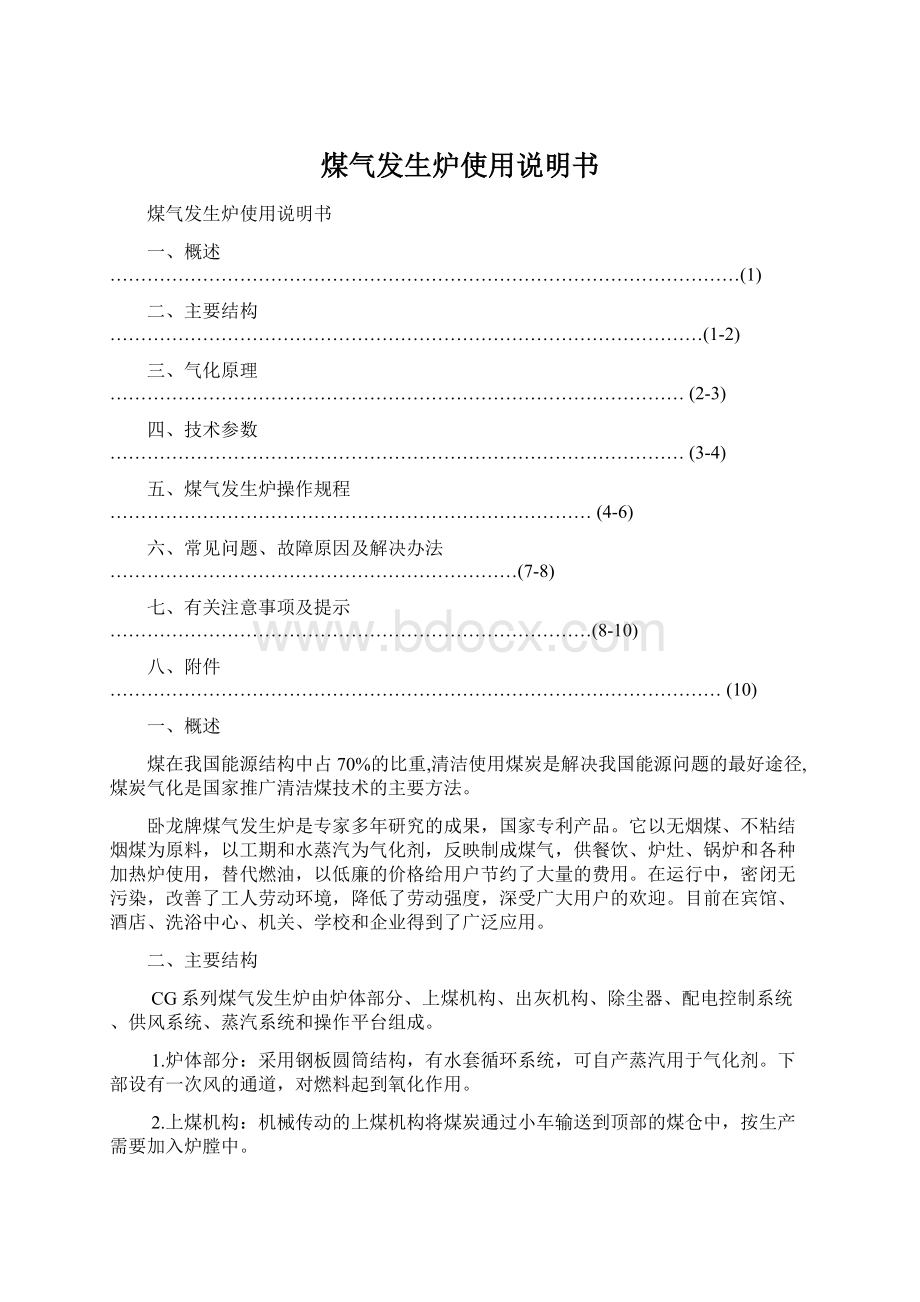
5.操作平台:
钢结构的工作平台。
供工人在上面操作和维护等作业。
三、煤气发生炉的气化原理
在煤气发生炉中,煤由上而下移动,而气化剂则由下而上移动。
煤与气化剂逆向移动分层进行物理化学反应,我们称这个工艺过程为气化。
反应过程分5个层次。
(一)灰渣层
灰渣层在炉篦的上面,是煤炭气化后的残留物,高度在炉篦以上150~250mm。
其作用是:
(1)由于灰渣由氧化层沉降下来,温度比较高,当气化剂经过灰渣层时进行冷热交换,将气化剂预热到200℃以上,为氧化层的热化学反应带来优越条件,加速燃烧;
(2)由于灰渣层被气化剂冷却,对炉篦起到保护作用。
(3)灰渣分布在炉篦上呈疏松状,气化剂经过灰渣层时起到重新均匀分布气流的作用。
(二)氧化层
氧化层又称为燃烧层,氧化层在灰渣层的上面,在这一层中,鼓风机中的氧气和碳进行氧化反应,充分燃烧生成大量的二氧化碳,同时产生大量的热。
煤气的热化学反应靠此来提供热量。
(三)还原层
还原层是生成煤气的区域,氧化层产生的二氧化碳气体上升到还原层后:
(1)和炽热的炭进行吸热化学反应,生成一氧化碳,
(2)水蒸气与炽热的碳进行吸热化学反应,生成一氧化碳和氢气,(3)一氧化碳与多余的水蒸气反应生成二氧化碳和氢气,同时放出热量使煤气炉中温度升高。
(四)干馏层
干馏层位于还原层之上。
煤炭在400~550℃的温度下析出挥发份和其它干馏产物(CH4、CmHn)后变成焦炭,焦炭由干馏层转入还原层进行化学反应。
(五)干燥层
干燥层是料层最上的一层,原煤的水分在这一层被蒸发,为下一层干馏准备好原料。
四、技术参数1.炉膛直径:
0.6~3.0米
2.适用燃料:
无烟煤、焦炭、弱粘结性烟煤,粒度6—13mm、13—25mm、25—50mm。
3.气化剂类型:
空气+水蒸气。
4.气化强度:
≥200kg/m2.h。
5.气化率:
3.5Nm3/kg.
6.煤气热值:
1250~1500kcal/Nm3.
7.煤气炉出口温度:
≤400℃
五、煤气发生炉安全操作规程
(一)、点火前准备
A、各运动部件冷态实验正常。
1.检查各减速机内和其它应润滑部位是否加油。
2.灰盘旋转正常;
转动方向是否正确。
3.风机启动、停止正常;
转向是否正确。
4.自动上煤系统:
料斗加料、上升、落料、下降正常。
5.检查各部位螺栓是否拧紧,系统无泄漏。
6.检查钟罩行程、密封是否合格。
7.检查各阀门开关灵活、无故障。
B、各仪表显示正常。
反映灵敏、准确。
C、各水封水位正常;
水套注满水,水位计显示清晰、进出水时液位显示正常。
D、蒸汽系统循环正常。
1.自动泄压装置正常无堵塞。
2.蒸汽管路畅通,打开蒸汽放散阀。
E、铺炉
用粒度为30~70毫米的炉渣铺炉至炉渣高出炉篦100mm左右,并摊平。
(二)、点火
1.点火:
加入木柴,木柴量以确保引燃煤层为准。
木柴应均匀分布于整个炉膛,点燃木柴并使其全部燃旺,点火时应打开放散阀,放下钟罩、并用上料小车顶开上煤仓盖。
2.待木柴燃旺后,可少量加煤燃烧,启动一次风机,以小量风助燃,如有局部未燃烧时,关小风量或停风,并用探扦适当拨动,使全炉膛均匀着火,如果还不能均匀着火,应重新点燃。
停风观察炉膛是否均匀着火,如着火情况良好,点火过程即完成。
3.逐步加煤待煤层达到一定高度时即可正常产生煤气。
4.待煤气产生正常后,转入供气程序。
(三)、供气
1、加热炉点火前必须先打开喷嘴上的二次风阀,将加热炉炉膛吹扫,清除加热炉内和烟道中可能残存的煤气。
2、关小二次风阀
3、点火棒放在喷咀处,慢慢打开煤气阀,即可点燃煤气。
注意一定要火等煤气,切忌炉内聚集烟气过多,引起爆炸。
4、点火时人不能正对炉门,炉门及各孔洞处严禁站人。
5、喷嘴点燃后,观察燃烧情况,逐步加大二次风量,调整各喷嘴配风阀门,使各喷嘴稳定燃烧。
6、如喷嘴不着火,说明煤气质量不佳或煤气量不足,应当立即关闭煤气阀门,加大二次风将炉内残气吹净,稍停5分钟后再按上述步骤进行第二次送气点火。
7、加热炉炉膛温度在500℃以下时应时刻注意加热炉内是否断火,如果断火,应立即关闭煤气阀,打开加热炉门,再重新按程序点火。
8、任何时间各水封部位和水套内严禁缺水,水套内的水应勤加少加。
9、运行中应时常注意电器控制柜上仪表读数,煤气出口温度不能超过400℃,应及时加煤。
10、工作期间如发现上下水封冒水应减小一次风量。
11、要保持料层高度在700~800mm,煤层过低影响煤气质量和产量,严重时会点不着火。
12、加热炉燃烧温度与煤气量、一二次风量、烟囱抽力有关,生产中应及时调整各阀门大小。
13、煤质粒度应符合要求,以免影响产气量,煤块粒度过大或过小或易结渣都会影响煤气生产,严重时会点不着火。
14、各减速机、转动部位严禁缺油。
15、司炉工必须经过专业培训上岗,严禁非工作人员操作开关、阀门。
16、非工作人员不得进入工作现场。
17、严禁在煤气发生炉运行状态下进行维修,煤气发生炉2米范围内严禁火焰。
(四)停炉
停炉可分为以下几种情况:
①根据用户需要停炉②大修停炉③突然停电停炉,后一种作为停电事故处理。
对热煤气系统停炉简述如下:
1.正常工作停炉前应先检查煤层高度,然后逐渐减小一次风量降低炉内反应温度,并使炉底保持正压,打开放散阀,用水封隔断煤气发生炉与加热炉之间的联系,再依次关闭一次风阀门、停下风机,打开蒸汽阀门,最后关闭电器控制柜总电源。
2.检修停炉:
当计划检修煤气炉停炉时,可在停炉前1~2小时停止加煤,停炉时逐渐减小风量,打开放散阀,用水封隔断煤气发生炉与加热炉之间的联系,将加热炉炉门打开或台车退出炉外,然后关闭风机。
停炉后8小时内不得扒炉,以防空气进入炉内造成爆炸事故。
3.突然停电、停炉:
工作时,遇到突然停电,迅速打开放散阀,加大进炉底蒸汽量,使煤气炉内保持正压,用水封隔断煤气发生炉与加热炉之间的联系。
同时将加热炉炉门打开。
(五)、连续工作的煤气发生炉可省去铺炉和木柴引火步骤。
警告:
加热炉内空气烟尘浑浊时不能点火,一定要用二次风吹扫炉膛,直至炉膛视线清楚无浑浊气体时才可以供气点火。
六、常见问题、故障原因及解决方法
常见问题
故障原因
处理方法
点火困难
助燃风过大
关小二次风阀
煤气量不足
调整煤气炉内状态
煤层偏斜、局部未燃
扒炉重新点火,注意点火均匀
炉膛内煤结渣
更换煤种
加热炉关门后灭火
二次风不足、火焰未稳定燃烧
加大二次风,稳定燃烧后再关炉门
烟囱抽力过大或过小
调整烟囱抽力
火焰易断火
煤气质量不稳定
加煤或加大一次风力
喷嘴或管道有异物堵塞
疏通喷嘴或管道
煤层结渣严重
煤层过低
加高煤层
火焰中有红火星
燃料或介质中有杂质
筛除煤粉
加煤时炉膛爆燃
煤层偏低
加高煤层后可避免
煤渣中黑煤较多
煤气出口温度低
提高煤气出口
卸渣过量
减小卸渣次数
燃料粒度过大或粒度大小悬殊
更换均匀煤种
炉盖掀起、上下
水封冒水
一次风过量
减小一次风量
加热炉内压力过大
疏通管道、加大煤气阀门开度;
调整加热炉烟囱抽力
燃料粒度过大
更换合适粒度煤种
下部水封冒水
一次风量过大
煤块粒度过小或煤粉太多
更换煤粒度
煤炭结渣或粘结
水套漏水
水套缺水损坏
停炉,扒出炉内煤炭重新补焊
七、注意事项
(一)点火前一定要吹扫加热炉内和烟道中可能残存的煤气。
启动风机将空气鼓入加热炉炉膛,使停炉时可能残存炉膛内的煤气吹净,风机吹扫5分钟后方可送气点火。
切忌聚集烟气过多,禁止采用爆炸法点火。
(二)送气及加热炉点火
点燃点火棒放在点火孔旁,火等煤气,此时煤气送入加热炉应被点燃,喷嘴喷出火焰。
如喷嘴不着火,说明煤气不足或煤气质量不佳,立即关闭煤气阀门,调整煤气发生炉操作,并用二次风将加热炉内残气吹净,方可进行第二次送气点火,当喷嘴点燃后逐渐调节二次风阀,使燃烧稳定。
(三)运行
1、注意电器控制柜上仪表读数,煤气出口温度应≤400℃,如发现炉内结渣,蒸汽调节阀应开大一些,调高一次风温度,一次风量根据煤气用量调整,如喷嘴火力不足或煤气出口温度过低,应调大一次风量。
2、保持煤层高度在800~1000mm。
3、煤气出口温度接近400℃时必须加煤,运行中煤气量不足时必须加煤。
4、出渣;
灰渣层达到一定厚度时即可出渣,如果灰分过多,要勤出渣,但应保留渣层不得少于200毫米,以免火层烧坏炉篦。
5、蒸汽系统:
保持水位高度,水套中严禁缺水。
6、各水封部位要保持一定水位,及时清除落入水封的异物。
7、各机械传动部分定期加油,保持良好润滑。
8、焦油凝结会堵塞喷嘴和管道。
如发现喷嘴喷火不畅应及时检查和清除喷嘴和阀门中的焦油,管道应定期疏通,设备应安排定期检查。
9、煤气炉热状态或冷状态运行都会使煤气质量下降。
所谓热状态是指煤气出口温度超过400℃时,冷状态是指煤气出口温度低于100℃。
10、卸渣时应注意电机、减速机是否正常运转,如炉内有异物或煤结渣会导致渣盘卡死,此时不得强行转动卸渣。
11、经常检查自动卸压装置是否可靠。
(四)停炉及交班
停炉时必须将煤气发生炉与加热炉管道隔离,以防回火。
交接班时,一定要交换清楚,所有发生的事情及存在的问题、现在的状态,做好交接班记录。
特别提示:
煤气发生炉的水套内要使用软化水,应按照有关锅炉标准规定,及时清理水垢。
任何时间水套内严禁缺水。
卸渣机构应按箭头所示方向旋转,严禁倒转。
保持渣层厚度,以免炉篦烧坏。
停炉8小时内,严禁打开煤气炉工作,以免炉内爆燃。
煤气发生炉底部渣池内要及时清理,不得使渣池堵塞,否则影响卸渣和损坏炉篦传动系统。
煤气发生炉传动部分(如轴承、滚轮、销轴等部位)不得缺油。
煤气发生炉正常操作时应注意的问题
1、检查灰盘,钟罩阀、鼓风机、逆止阀等封水位置是否正常。
2、煤气管道、水管道是否漏气。
3、探钎测量氧化层和还原层的温度和位置,氧化层的温度要控制使其略低灰熔点。
4、要经常注意炉内料层高度。
5、要根据煤气的成分和热值及时调整炉况。
6、注意炉底压力和送风量有何变化。
7、炉气出口温度,一般为450~550℃。
8、炉出压力一般为0.7-1.17KPa。
9、炉内有否结渣、冒火、偏炉、粘贴等不正常炉况,如果有要及时处理,并向下班如实交待。
10、集汽的水位量是否正常,气压是否规定的常压。
11、要经常从探火孔观察燃料层气化是否均匀,正常的情况下整个炉子都是均匀的暗红色燃料块和红色的缝隙。
序号
故障现象
分析原因
处理方法
1
煤气中含氧量超过规定
1、出灰过多,炉温低
2、料层烧穿,有风洞
3、水套漏水,造成局部灭火
立即与总管断开培养炉温,或改冷备。
2
炉底压力波动
1、炉底退水管堵塞
2、饱和空气带进软化水
疏通退水,严格控制水套软化水液面。
3
炉底压力突然升高,空气流量减少,炉出口压力同时减小
炉箅陪烧坏
停炉处理
4
炉出口压力升高
1、后系统堵塞
2、炉出口堵塞
热备式停炉处理
5
炉底压力和炉出压力同时减少(或炉底着火)
陆地水封失效
开炉底水封阀给水,封炉底水封
6
灰盆水外溢
水位过高
水套漏水
降低水位
停炉改冷设备检查
为了便于更合理地对常压固定床煤气化发生炉内部结构进行设计,我们非常有必要对煤气发生炉内部气化的一些物理与化学过程进行深层次的了解,包括发生炉内部的传热与传质、气相内的反应、气相与固相的运动、固相各阶段的反应等。
本文从一定的层面上对常压固定床煤气化发生炉内部的传热、传质过程进行了简要综述。
常压固定床煤气化发生炉内部的传热、传质过程十分复杂。
就传质来讲,不仅有气相和固相各自的本体运动,还有气固相间、固相颗粒内部向颗粒外部的传质过程。
就传热而言,有气固相间、气固相与炉壁间、固相不同层面之间的各种传热过程。
从机理上讲,传质过程有扩散传质和对流传质,传热过程有传导、对流和辐射等方式。
传热过程包括以下各个步骤:
(1)颗粒内传导;
(2)相接触的颗粒间传导;
(3)颗粒间辐射;
(4)颗粒流体间的对流;
(5)颗粒向流体的辐射;
(6)流体内传导;
(7)流体内辐射;
(8)流体混合;
(9)颗粒炉壁间传导;
(10)颗粒炉壁间辐射;
(11)流体炉壁间对流;
(12)流体炉壁间辐射。
相对来讲,传质过程就要简单的多,其原因有以下三点:
(1)颗粒内扩散经常可以忽略;
(2)没有向炉壁的传质;
(3)没有与辐射传热相对应的传质方式。
传热与传质过程可能伴随化学反应,也可能不伴随化学反应。
下面对常压固定床煤气化反应炉内部的传热与传质进行简单归纳。
气体和固体的许多特性(如热容、粘度、传质系数等)都是温度和压力的函数,当温度变化范围较小时,可以采用平均值的方式来简化传热与传质的数学模型。
但在煤气化反应炉中,温度沿床层高度的变化很大,因而必须确定各种性质与温度之间的函数关系。
在简单的一维均相模型中,床层向炉壁的传热可以用总传热系数来代表。
目前文献中采用的典型数值一般为15~35,即54~126。
这样的数值属于强制对流范围。
也有的模型采用的数值更高一些,比如后面提到的Biba模型,为217。
通过炉壁的热耗主要来自气相,也就是说,由于气相在炉内的运动速率很高,故其径向有效导热系数也很高。
床层向炉壁的总传热系数可以有不同的计算方法,除了选取经验值外,还可以由计算公式得到。
比如用Li和Finlayson给出的公式,或者由Hobbs等人给出的计算公式。
由于煤粒在粒度和形状上的多变性,再加**层不同高度空隙率的不同,总传热系数很难精确地求得,现有公式计算的理论值和实验值之间的偏差达到20%以内时便可以认为足够精确。
除了总传热系数以外,气相和固相之间的传热系数也是一个很重要的参数。
这一系数的计算要更困难一些,炉内气固相间传热的扰动、化学反应的存在、煤粒形状的不规则都有可能带来计算结果的偏差,有时候这种偏差甚至会高达几十倍。
1963年,Gupta和Thodos给出了较好的计算公式,1986年Bhattacharya等人在建立固定床煤发生炉的数学模型时就采用了这一公式[16]。
1992年Hobbs等人在计算这一系数时进行了简化处理,假定沿整个床层的煤粒都是均一的。
<
br/>
1971年DeWasch和Froment给出了一套数学公式,可以计算床层向炉壁的有效传热系数以及这一系数中气相和固相各自的贡献,Yagi也进行过这方面的研究,另外Hobbs等人也给出了一套复杂的计算公式,上面简单回顾了传热过程的计算,现在来讨论一下煤气化反应炉内的流速、升温速率及床层空隙率。
工业化Lurgi炉中煤的停留时间以小时计,而气相的停留时间仅以秒计。
对常压固定床煤气化反应炉,其气固相的运动线速度一般分别低于3m/s和0.1m/s,对高压常压固定床煤气化反应炉,其气固相的运动速度一般分别低于0.3m/s和0.15m/s。
显然,气相线速度的急剧减小是因为压力的存在大大压缩了煤气化反应炉中气体的体积流速,而固相线速度的增加则是因为高压操作时煤气化反应炉的煤处理能力的增加。
上面给出的线速度值仅为估计的平均线速度,实际上,气相和固相在炉内的线速度是不断变化的。
影响气体运动线速度的因素有:
①随着反应的进行,气体总量总是不断增加;
②压力沿床层的变化;
③温度沿床层的变化;
④床层空隙率的变化。
随着气体自下而上的运动,虽然在燃烧区之后床层温度是不断降低的,但气体总量的增加、压力的降低以及床层空隙率的减小都会引起气体线速度的增加。
影响固体线速度的因素有:
①随着固体不断失重而引起的固体质量流速的减小;
②床层空隙率的不断增加。
从物料衡算的观点来分析,由于单位时间内流入气化反应炉和流出气化反应炉的灰分量相等,而入口处的固体物流中灰分含量仅最多占到25%,出口处的固体物流中灰分含量却要占到95%以上,显然入口处的固体物流的质量流量和体积流量均要大大降低,从而造成灰分区的运动线速度极低。
气固相的升温速度与反应器内部的温度分布及气固相的停留时间有关。
一般来讲,气相的升温速度要比固相高出四个数量级。
在燃烧区,由于多相氧化反应的剧烈进行,升温速率较大,而在气化区,气固相的温度变化要平缓的多。
关于煤气化反应炉内的压力降,对于常压操作的煤气化反应炉,比如Wellman和Galusha炉,一般仅为1.1kPa左右(~100mmH2O);
对于高压操作的煤气化反应炉,如Lurgi炉,Hobbs等人的模拟计算结果也在kPa数量级。
因此,在模型计算中,除了进行动量守恒的计算外,假定煤气化反应炉内的压力为恒定常数也可以得到足够精确的计算结果。
床层空隙率是指床层空隙体积与床层总体积之比。
一般情况下,床层顶部的空隙率为0.3,而底部的空隙率甚至可达0.7。
床层顶部的空隙率基本上可以由煤的堆积密度和颗粒密度求得。
显然,空隙率越大,气体流动的阻力就越小,沿床层的压降就越小。
为了便于更合理地对常压固定床煤气化发生炉内部结构进行设计,我们非常有必要对煤气发生炉内部气化的一些物理与化学过程进行深层次的了解,包括发生炉内部的传热与传质、气相内的反应、气相与固相的运动、固相各阶段的反应。
本文从一定的层面上对常压固定床煤气化发生炉内部的气相化学反应进行了简要综述。
以固相温度沿床层的变化曲线为基础,可以对气相浓度沿床层的变化进行一些简单说明。
VanDerHoeven曾研究过煤气反应炉中气体浓度变化的实验值。
在煤气化反应炉底部的灰分区,灰分和供入的气化剂物流进行能量交换。
随着温度的升高,气化剂中的氧气同固体中的碳发生多相氧化反应生成CO2和CO,另外,气化剂中的H2O也有可能同固体碳发生多相气化反应生成H2和CO,这时,由于气相中有O2的存在,可能会发生如下的均相反应:
2CO+O2=2CO2(1-1)
2H2+O2=2H2O(1-2)
这样反应的总效果就是在气相的氧未耗尽之前,不但不会产生H2O的消耗,而且因为均相反应(1-1)的存在,气相中的CO2浓度是逐渐增加的。
总之,在燃烧区,尽管H2O和CO2也会同固体碳发生多相气化反应,但气化反应的产物H2和CO却在气相中又可能按照前述的两个均相反应均被均相氧化成H2O和CO2。
p>
在煤气化反应炉中的气化区,存在着大量的均相气相反应。
除了水煤气变换反应外,还有如下的均相甲烷化生成反应:
CO+3H2=CH4+H2O-219.3kJ/mol(1-3)
CO2+4H2=CH4+2H2O-162.8kJ/mol(1-4)
2CO+2H2=CH4+CO2-247.3kJ/mol(1-5)
这些反应均是体积减小的反应,提高压力,降低温度有助于甲烷的生成。
与此相反,CO和H2O的多相还原气化反应:
C+CO2=2CO-173.3kJ/mol(1-6)
C+H2O=H2+CO-135.0kJ/mol(1-7)
而这些反应又均是体积增加的吸热反应,降低压力、提高温度有利于碳的气化。
显然,压力恒定时,温度越高CO的平衡浓度越高;
温度一定时,压力越高,CO平衡浓度越低。
这样可部分说明由加压气化工艺生产的煤气中的CO2的含量要高于常压气化,CO的浓度却要低于常压气化。
实际上,由于气相和固相的逆流性质,由于气相的快速流动,由于煤气化反应炉内沿床层温度的不断变化,发生炉中生成的各种气体很难达到完全平衡。
在干燥区和脱挥发分的热解区,由于温度的进一步降低,煤气组成更加偏离平衡区。
本文从一定的层面上对常压固定床煤气化发生炉内部的气相和固相的流动进行了简要综述
由于气相和固相的逆流特性,煤粒在气相运动时要遇到向上流动的气流的较大阻力。
影响煤粒运动的结构因素有很