真空抬包设计抬包结构设计Word下载.docx
《真空抬包设计抬包结构设计Word下载.docx》由会员分享,可在线阅读,更多相关《真空抬包设计抬包结构设计Word下载.docx(22页珍藏版)》请在冰豆网上搜索。
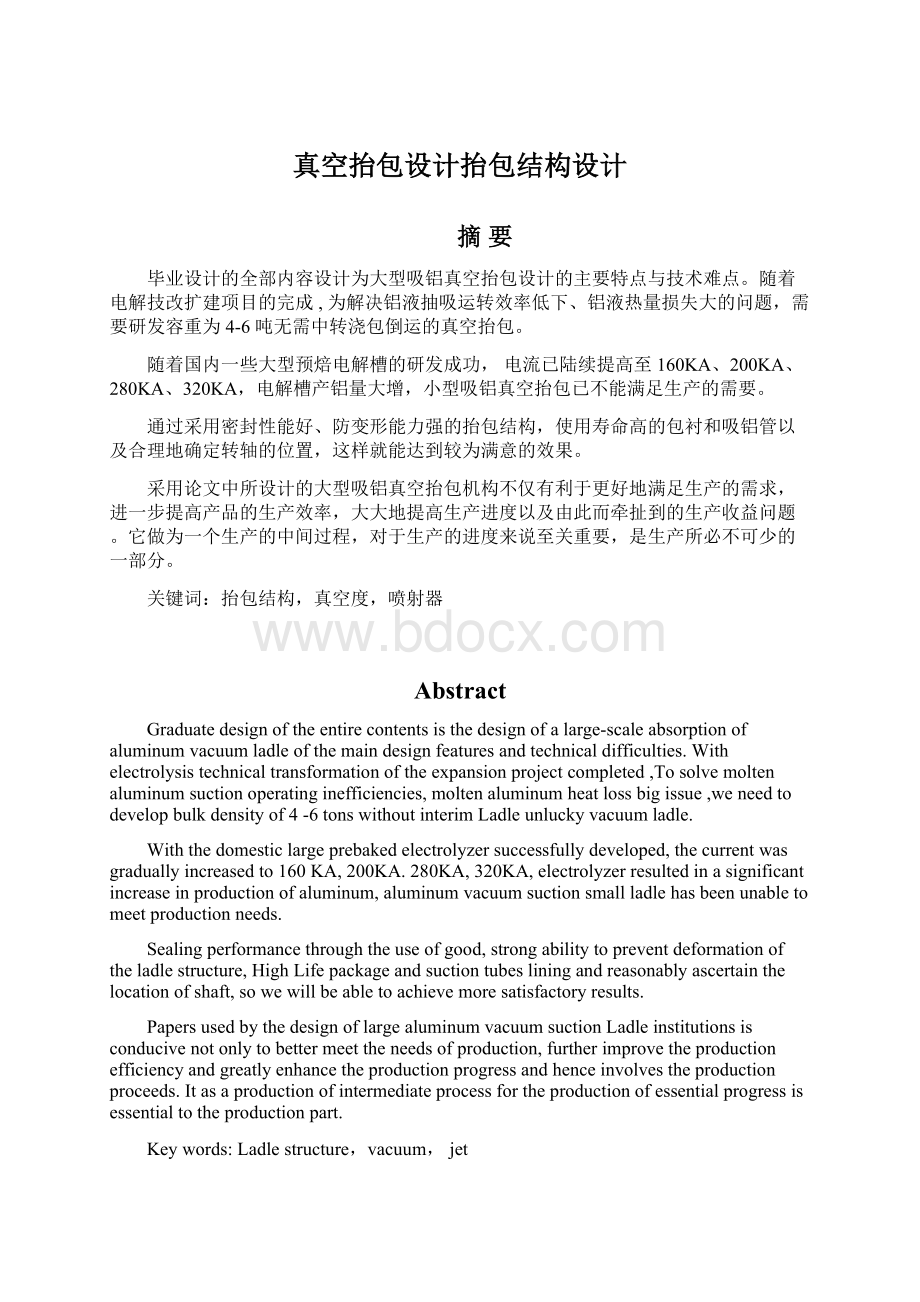
前言3
1.我国铝冶炼技术现状及发展趋势3
1.1 概况4
1.1.1 氧化铝生产所取得的主要技术成就4
1.1.2 存在的主要问题5
1.1.3 氧化铝冶炼技术的发展方向5
1.2电解铝生产技术6
1.2.1 电解铝所取得的主要技术成绩6
1.2.2 存在的技术问题7
1.2.3 铝电解技术的发展方向8
2.研发大型真空抬包在国民经济中的实用价值和需要解决的主要问题8
2.1.大型吸铝真空抬包的研发9
2.2.有待解决的主要关键问题9
2.3.解决这些问题所采用的方法9
3.研发工作的前提及进行的条件10
3.1.研究的前提与假设10
3.2.实验方案的拟定10
3.3.基本概念和理论基础11
4.主要部分的设计计算与校核15
4.1抬包结构设计校核15
4.2真空度分析17
4.3电动机的选择18
4.31选择电动机的种类,类型和结构形式19
4.32选择电动机的功率(容量)19
4.33确定电动机的转速19
5.结构设计部分19
6.工艺及性能参数22
7.技术经济性分析23
8.方案的校验23
总结24
致谢25
参考文献26
附录27
评语28
评语29
前言
随着科学技术的发展,机器的发展速度也较快。
但对原有的设备进行工艺和技术的改造,使其能满足生产的需要,这样不仅造价合理、上马快,而且还可弥补设备的不足,减少投资.用户希望提供满足生产需求,更为合理的生产设备。
随着机械产品国内外市场竞争的日趋激烈,产品更新换代速度进一步加快,新产品开发周期大大缩短,使制造业向多品种、小批量生产方式发展。
不管是哪个国家哪个集团,要想在这场竞争中取胜,就必须使自己的制造业尽早适应这个大市场的变化,将自己的制造业改造成具有精密、柔性、高效的现代自动化制造业。
。
当前,现代自动化制造业的水平已成为衡量一个国家工业化水平和综合实力的重要标志。
真空抬包是电解铝冶炼过程中的一个重要设备,其主要功能是将电解槽中的电解铝液吸出并倒运至混合炉。
中国铝业河南分公司电解厂原电解槽为65KA自焙槽,年产铝量为3万吨,采用容重为2吨的真空抬包来吸铝,并配合5吨的敞口包来倒运即可满足生产的需要。
随着电解技改扩建项目的完成,电解槽变为85KA预焙槽,电解厂年产铝量为5万吨,为解决铝液抽吸运转效率低下、铝液热量损失大的问题,需要研发容重为4-6吨无需中转浇包倒运的真空抬包。
所以,解决这个问题的办法只能是:
一方面要采用大型的真空抬包,以扩大铝液的容量,另一方面提高机器的自动化水平,采用电动式和手动式的倾转机构,使得操作更为方便。
本论文就作者对真空抬包的容量以及抬包结构等进行说明,由于水平有限不免有错误和遗漏之处,望请原谅。
1.我国铝冶炼技术现状及发展趋势
我国的铝冶炼工业经过几十年的发展,取得了前所未有的成绩,2000年氧化铝产量达429万t,铝锭283万t,我国已成为世界铝生产和消费的大国。
这一成绩的取得,与科技的贡献是不可分的。
现就我国氧化铝和电解铝方面所取得的成绩作一回顾,并就我国氧化铝生产技术的发展趋势作一分析。
1.1 概况
氧化铝生产技术我国铝土矿资源绝大多数为一水硬铝石,高铝、高硅、低硫、低铁、中低铝硅比,AL2O3含量一般在40%~75%,SiO2含量一般在4%~18%,铝硅比小于4的占7.42%,4~7的占59.53%,7~10的占26.08%,大于10的仅占6.97%。
由于我国铝土矿资源的这一显著特点,国内氧化铝生产大多采用混联法,此外,还有拜耳法和烧结法。
1.1.1 氧化铝生产所取得的主要技术成就
(1)矿石均化和多碎少磨技术,包括矿山块矿石及进厂碎矿石均化,多碎少磨提高了磨矿效率,降低了磨矿成本;
(2)烧结法熟料烧成强化技术,包括高品位铝土矿强化烧结技术、铝土矿浮选精矿强化烧结技术、生料浆配料、非饱和配方、石灰配料和高浓度碳酸化分解,生料加煤排硫、窑体改造及操作改进、单枪喂料;
(3)烧结法熟料溶出技术,包括低苛性分子比溶出、高碳酸钠浓度二段磨溶出、低碳酸钠浓度一段磨溶出;
(4)粗液脱硅技术,包括高压釜间接加热连续脱硅、管道化间接加热连续脱硅、深度脱硅;
(5)拜耳法强化溶出技术,包括管道化溶出、单管预热—高压釜溶出、管道—停留罐溶出、混联法中的拜耳法不平衡溶出、新型高压隔膜泵;
(6)一水硬铝石选矿—拜耳法生产氧化铝技术,该技术将选矿技术和拜耳法有机结合,有效地利用了我国大量的中低品位铝土矿,降低了氧化铝的生产成本;
(7)赤泥分离技术,包括絮凝沉降分离、Φ42m×
6m大型钢索扭矩沉降槽、100m²
辊子卸料真空转鼓过滤机、385m²
单筒凯利叶滤机;
(8)分解技术,包括连续碳酸化分解、4400m³
大型平底分解槽、245m²
立盘过滤机、51m²
水平盘式过滤机、270m²
大型板式换热器、27m²
水平带式真空过滤机;
(9)氧化铝闪速焙烧技术,包括美国闪速焙烧炉、丹麦气体悬浮燃烧炉;
(10)蒸发技术,包括降膜蒸发器,高效闪蒸器等。
此外,在多品种氧化铝生产,赤泥综合利用、镓回收、仪表及生产过程自动控制等方面也取得了很大的成绩。
1.1.2 存在的主要问题
(1)原料质量差、铝土矿A/S低我国铝土矿资源与国外三水铝石和一水软铝石相
比,原料质量差,铝土矿A/S低,需要高温高压溶出,这给氧化铝生产带来了困难。
(2)能耗高由于混联法既有完整的拜耳法系统,又有完整的烧结法系统,流程异常复杂。
接踵而来的是能耗很高,就是处理铝硅比约为10的优质矿石,能耗仍高达38GJ/t氧化铝,是国外一般拜耳法的3倍多。
很显然,随着矿石品位下降,经济的拜耳法比例减少,昂贵的烧结法比例增加,能耗还要增加。
(3)产品质量不高,多为中间状氧化铝目前国内冶金级氧化铝产品多为中间状氧化铝,产品粒度较细,产品的磨损指数较大,要很好满足现代电解铝工业大型预焙槽的要求,还要加快砂状氧化铝的开发。
(4)产品结构不合理目前我国氧化铝厂多以生产冶金级氧化铝产品为主,产量达406万t,而非冶金级氧化铝产品的年产量23万t左右,与市场需求相比差距很远。
(5)技术的产业化程度需要进一步提高这几年,铝行业开发了不少先进技术,但是推广应用的程度还不够,今后要进一步在项目立项、研发和产业化的各个环节加强与生产的结合,提高技术成果的产业化率
1.1.3 氧化铝冶炼技术的发展方向
(1)加速铝土矿选矿工艺的产业化步伐铝土矿选矿工艺研究通过“九五”科技攻关,已经完成了工业试验,形成了一套完整的工艺路线,“十五”期间要加快该技术的产业化,并开展铝土矿的反浮选技术研究。
(2)强化和革新现有生产方法溶出是拜耳法的关键工序。
我国现在已经有了3种强化溶出技术:
a、长城铝业公司引进的德国管道化溶出;
b、山西铝厂引进的法国单管预热—高压釜溶出;
c、我国自行开发的管道—停留罐溶出。
应该在总结生产实际效果的基础上,尽快推广应用。
强化熟料烧结过程,如降低烧成温度,改变供料方式,改进窑体结构等,其次是提高溶液浓度,强化湿法各工序。
采用各种添加剂,例如沉降絮凝剂、过滤助滤剂、分解添加剂、溶出添加剂等,可以显著强化生产过程,而且很容易被工业上采用。
种子搅拌分解是氧化铝生产中贮存液量最多,时间最长的工序,它的强化必将显著提高工厂的生产能力。
(3)加快砂状氧化铝生产技术的攻关,提高我国氧化铝产品质量我国氧化铝工业由于以一水硬铝石型铝土矿为主要生产原料,致使种分和碳分分解原液的氧化铝浓度高、苛性比值也较高,生产砂状氧化铝的技术难度较大。
“十五”期间要重点解决铝酸钠溶液分解过程粒子成核控制技术、铝酸钠溶液分解过程产品粒度控制技术、铝酸钠溶液分解过程产品强度控制技术和添加剂强化分解技术等。
通过科技攻关,形成一套适合我国砂状氧化铝生产技术。
(4)加快氧化铝技术成果的产业化加快石灰拜耳法、双流法新技术、间接加热连续脱硅、高效沉降槽、降膜蒸发技术等技术在氧化铝生产过程中的产业化应用,进一步降低生产能耗和生产成本。
1.2电解铝生产技术
目前铝全部采用熔盐电解方法生产,其生产设备从较早的单一侧插自焙槽,发展到拥有侧插自焙、上插自焙、预焙槽等各种槽型。
我国已完成了180kA、280kA和320kA的现代化预焙槽的工业试验和产业化。
以节能增产和环保达标为中心的技术改进与改造,促进自焙槽生产技术向预焙槽转化,获得了巨大成功。
我国已经成为大型预焙槽开发的先进国家。
1.2.1 电解铝所取得的主要技术成绩
(1)大型预焙槽的开发
1992年完成180kA预焙槽工业试验,电流效率达到93%,铝直流电耗达13800kW·
h/t左右,生产工艺技术条件与160kA槽基本相同。
1996年完成了280kA预焙槽工业试验,这一技术已成功地应用于焦作万方铝业集团公司。
目前电流效率达到93%以上,铝直流电耗达13400kW·
h/t左右,生产运行平稳。
2000年完成了320kA大型预焙槽工业试验,电流效率达9492%,平均铝直流电耗13192kW·
h/t,达到了法国铝业公司开发的AP-30大型电解槽的技术指标,最近已和印度一家公司签定了技术转让合同,实现了技术的输出。
(2)计算机控制技术目前我国主要电解铝厂均采用了计算机控制。
自适应控制技术、模糊控制技术和智能模糊控制技术的开发应用使吨铝节电在100kW·
h左右。
(3)采用添加剂电解质中添加氟化镁、氟化铝和锂盐等物质可以改善电解质的某些物化性能,从而提高电解过程中电流效率(约2%左右)。
降低电解成本。
在电解质中加入添加剂目前已被广泛应用。
(4)电解槽结构的改进电解槽结构的改进已先后完成了槽壳结构的改进、槽底保温结构的改进、阴极结构及材料的改进、阳极系统的改进和点下料系统的试验和应用。
此外,在电解工艺制度和烟气净化方面也取得了显著成绩。
1.2.2 存在的技术问题
(1)整体机械化装备水平尚待提高尽管我国在铝电解生产实践中研究开发了一系列专用设备,如多功能联合机组、地爬打壳机、筒式下料器等,但与国际先进水平相比,机械化装备水平尚需进一步提高,主要表现在:
a、国产多功能联合机组故障频繁,制造质量还不高,关键部件需要进一步开发,如扭拔机构,空压系统及电气控制部分。
b、相配套的供料系统和槽上部下料系统跑、冒、漏现象严重,多功能机组受料问题需改进提高;
对闸刀式下料和插板式下料装置应改造成点式下料。
c、与工艺操作相配套的设备需研究开发,如出铝及清理抬包的机械化,与电子计算机控制相适应的打壳下料电磁阀的质量及工作性能提高等。
d、保证大型预焙铝电解槽生产用的压缩空气水分较大,这是目前全国各大铝厂普遍存在的问题,尽管设有气水分离器,但效果不理想,极易损坏各种电磁阀,造成一系列设备故障而影响生产。
e、与铝电解工艺操作相配套的其它设备需开发,如阳极更换设备,要求不仅能准确地拆卸和安装,而且在更换时能处理残极周围的结壳及掉入槽中的电解质块,现场卫生清理设备及电解槽一系列技术测试设备等。
(2)铝电解槽寿命短现在国际上的大型预焙铝电解寿命在7年以上,有的已达10年,而我国铝电解槽平均寿命仅4年左右。
尽管经过几年的生产实践,采取了一系列技术措施,基本克服了电解槽早期破损问题,但槽寿命仍与世界先进水平差距较大。
(3)自动控制水平尚待进一步提高尽管我国大部分铝电解厂采用了电解槽槽控技术,但整体的自动控制水平仍然不高,与国外相比差距较大,主要表现在控制电解槽生产过程的信息取样不完整,电解槽专家系统不完备,与计算机控制技术相配套的设备故障较多以及综合的动态研究不充分等。
1.2.3 铝电解技术的发展方向
(1)完善大型预焙槽技术在现有开发成功的180kA、280kA和320kA大型预焙槽的基础上,逐步完善。
使其各项技术指标进一步提高,达国际领先水平。
(2)自焙槽改造技术自焙槽目前约占我国铝的总产能的一半左右,鉴于我国目前的经济状态,在短期内全部淘汰是不可能的,因此,对自焙槽进行技术改造是势在必行的。
(3)加强“三场”技术研究只有认真进行“三场”技术研究,才能从根本解决目前电解槽结构的不足,提高铝电解技术水平。
总之,我国铝冶炼技术水平近些年来得到了迅速的发展,缩短了与发达国家的差距,但我们还应该看到,我国加入WTO,铝冶炼工业所面临的挑战,加快技术进步,提高铝冶炼企业的竞争力是我们迫切的任务。
2.研发大型真空抬包在国民经济中的实用价值和需要解决的主要问题
随着科学技术的发展,机器的发展速度也较快。
2.1.大型吸铝真空抬包的研发
有利于更好地满足生产的需求,进一步提高产品的生产效率,大大地提高生产进度以及由此而牵扯到的生产收益问题。
2.2.有待解决的主要关键问题
随着国内一些大型预焙电解槽的研发成功,需研发出相应的大型吸铝真空抬包以满足生产的需要。
有待解决的主要关键问题有以下几个:
(1)包盖与包体的密封及防变形措施。
(2)包衬及吸铝管使用寿命。
(3)转轴位置的确定及倾转力矩的计算。
2.3.解决这些问题所采用的方法
而需解决这些问题所采用的方法是:
对于大型吸铝真空抬包,包体直径较大,包盖与包体法兰采用凸凹止口密封,密封件为石棉盘根。
由于包盖与包体受热不均以及包体在起吊时的受力不均,容易导致包盖与包体法兰止口错位,从而引起密封不严。
对于这个问题,一方面要加强包体与包盖强度,包体与包盖均需加筋,采用厚法兰。
另一方面要采用合理的密封方式,可将包盖法兰嵌入至包体法兰内,形成双重止口密封,一旦小止口密封失效,可启用大止口密封。
对于小型吸铝真空抬包,由于其直径小、高度低,采用耐火砖砌包衬,其强度足可满足其使用寿命,对于大型吸铝真空抬包,由于其容积大,包衬必需采用浇注料整体浇注,其强度才可满足使用寿命。
吸铝管属耗损件,为提高其使用寿命,可采用耐温900℃以上的耐热铁铸造,并需进行热处理,耐热铁材质中Si含量不可过高,以防止和电解槽中的氟化盐发生化学反应,影响吸铝管使用寿命。
对于大型吸铝真空抬包,由于采用电动操作,从操作安全的观点出发,转轴位置应高于空包和满包的重心。
抬包倾转力矩M包括空抬包包体所引起的转矩M1,以及在浇注过程中由于铝液不断倾出,余留在抬包内的铝液所引起的转矩M2,此外还有转轴与其轴颈的摩擦力矩M3,三者均为转角θ的函数。
M=M1+M2+M3
3.研发工作的前提及进行的条件
3.1.研究的前提与假设
本次的设计课题是由指导老师提出,并对已有的产品进行参观实习,在此基础上,而得来的一些基本前提。
如中国铝业河南分公司电解厂原电解槽为65KA自焙槽,年产铝量为3万吨,采用容重为2吨的真空抬包来吸铝,并配合5吨的敞口包来倒运即可满足生产的需要。
而现在随着电解技改扩建项目的完成,电解槽变为85KA预焙槽,电解厂年产铝量为5万吨,为解决铝液抽吸运转效率低下、铝液热量损失大的问题,需要研发容重为4-6吨无需中转浇包倒运的真空抬包。
为此我们需要对原有的产品进行改进,以满足生产要求。
原有的产品是为2吨左右的小型抬包机构,并且需要中转浇包进行倒运,我们对此进行假设,如果可以撤去中转浇包,与小型抬包合为一体,这样不仅方便,而且简化了操作,便利了生产管理。
同时还考虑到需解决的一系列问题,例如盛铝液的容量要变大,减少热量的损失,撇渣的效果要好,检修方便等等问题。
3.2.实验方案的拟定
从以上对真空抬包机构的分析与假设中,并考虑到一些关于抬包结构中可能存在的问题,如抬包体的使用寿命,吸铝管的使用寿命,包体的密封以及转轴位置的确定及倾转力矩的计算等,综合以上几种情况,设计出了适合生产需要的真空抬包机构。
3.3.基本概念和理论基础
真空泵是由一个水封式的叶轮,在密闭的铁壳内迅速旋转来达到连续抽气的作用。
真空泵放置在专门的室内,它的抽气管与通往电解槽前的真空管道相连,出铝时真空包上的抽气管与真空管道上的一个接头之间接上胶管,就形成真空通路,这样,随着真空泵运转,产生60kPa的负压,通过插入铝电解槽内的吸管把铝水源源不断的吸入到真空包内,完成出铝程序。
在出铝过程中,有几个问题长期困绕着电解生产:
(1)真空管道管路长且每个槽前都设有一个开启阀门,这样就造成整个系统密封点多,每个厂房动密封点120余个,静密封点300余个。
密封性能很难保证,且查找泄漏点比较困难,影响出铝。
(2)每个槽前都设有开启阀门,在开启阀门过程中,极易吸进灰尘及氧化铝粉,造成管道堵塞现象,再就是在吸铝过程中,易将电解质颗粒吸进造成堵塞,影响出铝。
(3)管道中有一部分需通过电解槽底部地沟穿过,管道中须有“
”形,管路中的水分遇寒冷的空气易结冰,堵塞管道,影响出铝。
(4)由于电解系列电流磁场比较大,因此要求电解厂房地坪与电解槽以及槽与槽之间的绝缘都要好,如不注意,很容易造成真空管道带电,打火花击穿管道,造成漏气。
再一个就是易造成触电伤人。
(5)真空泵运转,需要大量动力消耗、人员及检修工时和备件消耗。
改进方案设计新型射流器,用电解加工用压缩空气出铝,代替老真空出铝系统。
新工艺装置见图1,关键部件———射流器见图2。
此方法
既节约又安全,并且提高出铝速度,而且投资少、维修简便,不用专门设备和管路,利用现有厂房内压缩空气即可。
射流器制作简单,成本低,性能可靠,使用周期长,每台