产能分析报告Word文档下载推荐.docx
《产能分析报告Word文档下载推荐.docx》由会员分享,可在线阅读,更多相关《产能分析报告Word文档下载推荐.docx(10页珍藏版)》请在冰豆网上搜索。
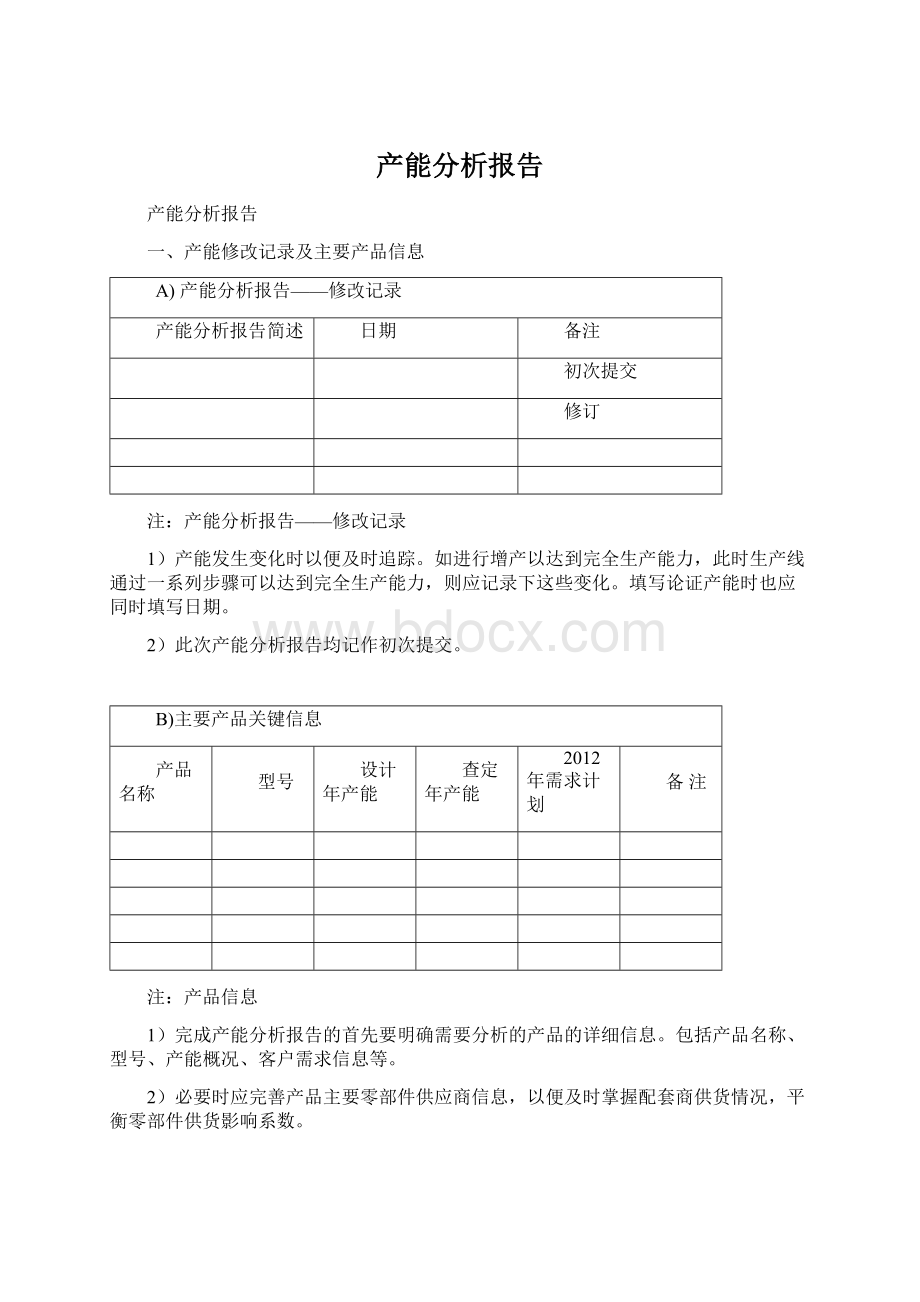
1、预订工作时间标准
A)计划工时
计算公式:
净可用工时e=a*b*c*d
说明
a
单班时间/时
8
根据自身工时计划安排填写
b
班次/班
2
c
作业率(%)
80
d
年出勤天数/天
302
e
净可用时间/时
1)单班时间:
每班总时间-每班的总计可用小时数。
2)班次:
表示的是每天每个工艺操作的班次数。
3)作业率:
(总工时-无效工时)/总工时。
人员休息-如果在人员休息的时候,机器也停止运转,则输入每班中机器不运转的时间长度。
计划的维修时间-这是计划的每班中机器停机用于维护的时间长度。
4)年出勤时间:
年出勤天数-表示的是每年的工艺运作的天数(扣除法定节假日、双休日)。
5)计算举例:
每班8小时、每天2班次、作业率80%、年出勤302天,净可用时间=8*2*80%*302=3865.6时。
2、代表产品制程/线能力计算
产品年产能=净可用时间(年)/瓶颈工序总加工时间
工序名称
设备名称
设备编号
设备台数
加工工时min/件
辅助工时min/件
总加工时间
日加工能力
人员配置
生产线瓶颈工序设备产能描述:
1)瓶颈工序、设备产能
2)其他
1)代表产品:
所谓代表产品指产品制程包含其他所有产品制造过程包含的所有工艺过程;
如存在两种以上产品包含不同工艺过程、需分别取各类型产品代表产品制程并进行线能力分析。
2)评价瓶颈工序应排除可用外协、其他生产线可用设备借代等因素影响。
3)每条生产线选取一种或2种产品作为代表说明制程及瓶颈工序即可,其他产品可直接计算毛产能。
3、毛产能核算
产品年度毛产能=代表产品/产品定额系数
产品系列
工时定额
产品定额系数
线产能
所占比例
实际产能
备注
A
A1
a/a
代表产品
A2
b/a
小计
B
B1
d/d
B2
e/d
B3
f
f/d
合计
1)毛产能核算过程没有排除产品合格率、设备故障率、人员负荷等因素对产能的影响,不能作为需求平衡分析的依据,需进一步平衡。
2)其他产品可根据代表产品计算方法计算出出毛产能。
3、有效产能(净产能)
有效设备产能核算(OEE)及人员负荷平衡
净产能=毛产能*OEE*人员负荷率
产品/生产线
毛产能
设备可用性
性能效率
合格率
OEE
现有人员
人员负荷率
净产能
100%
1)设备生产包括机器检修、保养、待料等时间,实际的工作时间达不到计划工时,且生产的产品有不良品,因此有效产能必须是以毛产能为基础,减去因停机和良率以及人员缺口等综合因素所造成的产能损失。
2)总体设备利用率计算公式:
OEE=设备可用性*性能效率*产品合格率。
根据来自生产验证运转的历史数据来计算总体设备利用率的(OEE)。
性能效率的计算是通过计划的所需周期时间来的。
如果计算单元显示的是100%或者更高,则该单元用红色进行强调。
3)人员负荷率=(现有生产人员/人员配置)*100%
反映了以设备为依据的人员配备情况,这一指标在短期内直接对净产能产生影响。
注释
OEE=可用率X表现性X质量指数。
其中:
可用率=操作时间/计划工作时间
它是用来考虑停工所带来的损失,包括引起计划生产发生停工的任何事件,例如设备故障,原料短缺以及生产方法的改变等。
表现性=(总产量/操作时间)/理想周期时间=(总产量/操作时间)*生产速率
表现性考虑生产速度上的损失。
包括任何导致生产不能以最大速度运行的因素,例如设备的磨损,材料的不合格以及操作人员的失误等。
质量指数=良品/总产量
质量指数考虑质量的损失,它用来反映没有满足质量要求的产品(包括返工的产品)。
利用OEE的一个最重要目的就是减少一般制造业所存在的六大损失:
停机损失、换装调试损失、暂停机损失、减速损失、启动过程次品损失和生产正常运行时产生的次品损失。
下面表格是六大损失的说明及其与OEE的关系:
六大损失类别OEE损失类别事件原因注释
停机损失有效率刀具损坏设备突发故障原料短缺等表示设备因为一些大的故障,或者突发事件所引起的停工。
换装调试损失有效率改变工具设备预热等因改换工具,生产线调试等准备工作而造成的损失,一般位于工位安排,生产布置这一阶段
暂停机损失表现性不通畅的生产流导轨阻塞清洁,检查一般指停工5分钟以下,并不需要维护人员介入的停工
减速损失表现性低于设计产能运行设备磨损员工技术因素等任何阻止设备达到设计产能的因素
启动过程次品损失质量指数报废、重工等设备预热,调节等生产正式运行之前产生的次品
生产过程次品损失质量指数报废、重工等生产稳定进行时产生的次品
表一六大损失与OEE的关系
编辑本段OEE计算实例
我们举一个例子来说明OEE的计算方法:
设某设备某天工作时间为8h,班前计划停机15min,故障停机30min,设备调整25min,产品的理论加工周期为0.6min/件,一天共加工产品450件,有20件废品,求这台设备的OEE。
根据上面可知:
计划运行时间=8x60-15=465(min)
实际运行时间=465-30-25=410(min)
有效率=410/465=0.881(88.1%)
生产总量=450(件)
理想速度x实际运行时间=1/0.6x410=683
表现性=450/683=0.658(65.8%)
(另外解法:
表现性=理想加工周期*生产数量/实际运行时间=0.6*450/410=0.658(65.8%))
质量指数=(450—20)/450=0.955(95.5%)
OEE=有效率x表现性x质量指数=55.4%
另一种OEE算法:
OEE=符合质量要求的产品/最大理论产量
此例中最大理论产量=(8*60-15)/0.6件=775件
符合质量要求产品=450-20=430件
OEE=430/775*100%=55.4%
OEE的作用
实践证明OEE是一个极好的基准工具,通过OEE模型的各子项分析,它准确清楚地告诉你设备效率如何,在生产的哪个环节有多少损失,以及你可以进行那些改善工作。
长期的使用OEE工具,企业可以轻松的找到影响生产效率的瓶颈,并进行改进和跟踪。
达到提高生产效率的目的,同时使公司避免不必要的耗费。
编辑本段OEE数据采集方法
OEE的计算虽然简单,但是,在实际的应用中,当与班次,员工,设备,产品等生产要素联系在一起时,便变得十分复杂,利用人工采集数据计算OEE显得麻烦费事,为了更有效的利用OEE这个工具,OEE数据采集信息化越来越成为人们关心的话题,OEEToolkit是世界上最优秀的OEE系统,它具有自动化数据采集模块,可以轻松地获取有关设备的生产信息,为OEE提供最有价值的数据,同时,该系统也可以生成实时的生产信息报告,包括故障停工,在制品信息和OEE等。
通过这些有价值的数据,企业的管理工作无疑会变得轻松而简单。
该系统已在世界上许多著名公司得到广泛的应用,例如波音飞机,通用电气,阿斯利康,道达尔石油等。
设某设备某天工作时间为8H,班前计划停机10MIN,故障停机30MIN,设备调整35MIN,产品的理论加工周期为1min/件,一天共加工产品400件,有20件废品,求这台设备的OEE。
计划运行时间=8*60-10=470(min)实际运行时间=470-30-35=405(min)有效率=405/470=0.86(86%)表现性=400/405=0.98(98%)质量指数=(400-20)/400=0.95(95%)OEE=有效率*表现性*质量指数=80%在上表中,我们只列举了一些事件原因,在实际应用中它可能包括与生产有关的任何原因。
OEE能准确地告诉你设备效率如何,在生产的哪个环节有多少损失,以及你可以进行哪些改善工作。
长期的使用OEE工具,企业可以轻松的找到影响生产效率的瓶颈,并进行改进和跟踪,以达到提高生产效率的目的。
编辑本段设备综合效率(OEE)
*什么是OEE
*认识OEE的三个构成因素:
可用水平,运行水平,
质量水平
*OEE计算要素与实例:
根据设备维护的历史数据,
选定单元,计算OEE
*OEE的计算与意义的解释
*如何改善OEE:
评价目前的OEE水平,提出改进目标
*如何建立基于OEE的设备管理监控
编辑本段OEE的实质
如果追究OEE的本质内涵,其实就是计算周期内用于加工的理论时间和负荷时间的百分比。
请注意,当展开OEE公式,有
OEE=时间开动率×
性能开动率×
合格品率
=(开动时间/负荷时间)×
[加工数量/(开动时间/理论加工周期)]×
(合格产量/加工数量)
=(开动时间×
加工数量×
理论加工周期×
合格产量)/(负荷时间×
开动时间×
加工数量)
约去分子、分母的公因子,
OEE=(理论加工周期×
合格产量)/负荷时间=合格产品的理论加工总时间/负荷时间
这也就是实际产量与负荷时间内理论产量的比值。
三个环节的管理重点:
时间开动率:
重点管理设备故障时间和调整时间,即减少设备故障时间、产品切换时间。
性能开动率:
重点管理单件生产时间,即,减少单件生产时间。
合格频率:
重点管理成品率,提高制程控制能力,减少不良品的发生。
三、产能需求平衡/预警机制
1、产能负荷率计算
产能负荷率:
需求计划
产能负荷率
预警设置
初步方案
>1
红
中长期扩能
黄
短期扩能
=1
蓝
短期扩能/不需扩能
<1
不需扩能
1)产能负荷率反映了企业中长期、短期需求计划对目前净产能比值的柔性指标,其作为产能预警的基础数据,对产能提升计划起指导性作用。
2)当负荷率反映3个月以内需求产能状态时,初步方案采取短期产能提升计划;
3-6月以上,采取中长期产能提升计划;
超过6个月以上,采取长期产能提升计划。
2)预警设置采取红黄蓝三色,具体设置见(三、2)产能预警。
2、产能预警
1)坐标轴纵轴表示产能,横轴为时间进度,两条黑色虚线分别表示长期扩能预警、短期扩能预警,红色实线为需求线(变化情况可参照历史数据)。
2)当需求线在短期扩能预警线以下时显示为蓝色椭圆。
不设预警,不需扩能;
当需求线在短期扩能预警线与长期扩能预警线之间时,设置黄色预警,采取短期产能提升计划;
当红色需求线超过长期扩能预警线,并长时间处于短期最大可获得差能之上,采取红色预警,并策划中长期扩能计划。
四、需求平衡/产能提升策略
1、约束产能的解决对策
通过设置产能预警线,提前对可能产生约束的时间点提出产能扩充的对策建议,并针对各类扩充对策预留实施提前期。
2、超过短期预警线的解决对策:
可以在标准产能的基础上快速扩充,并在1个月内投入使用,内容概括为(括号内为准备周期):
1)人力资源:
A)增加班次,采取两班制或三班制(1小时-1星期)
B)加班,适当延长工作时间(1小时-1星期)
C)内部支援,其他线暂时借调(1小时-1星期)
D)借用外协员工(培训期在1个月内);
2)增大外协量、外包量(增大现有的计划外协比例,1星期-2星期);
3)设备资源:
内部调配或快速购买(<
1个月);
机器增加开机的台数、开机时间(<
1个月)。
4)场地资源:
内部调配(<
1个月)等.
3、超过长期产能预警线的解决对策:
无法在现有资源基础上扩充达到,需要新增设备、人员,通常这种产能扩充需要一个月或更长的准备周期。
招聘新员工,准备周期超过1个月;
2)设备资源:
需要新申购(>
1个月)
3)新增场地、新设生产线(内部调整、新租/建:
准备周期在1个月以上)
4)新增车间或厂房(需要论证,总裁签字,准备周期1个月以上)
是否进行长期产能扩充要考虑和需求的匹配:
规划期内,如果需求产能超出短期扩充产能达6个月就需要进行长期扩充,小于6个月的通过短期产能扩充来满足;
(注:
以上产能提升计划仅供参考,具体方案,各子公司根据自身经营现状编制执行)