清洗总结报告Word下载.docx
《清洗总结报告Word下载.docx》由会员分享,可在线阅读,更多相关《清洗总结报告Word下载.docx(17页珍藏版)》请在冰豆网上搜索。
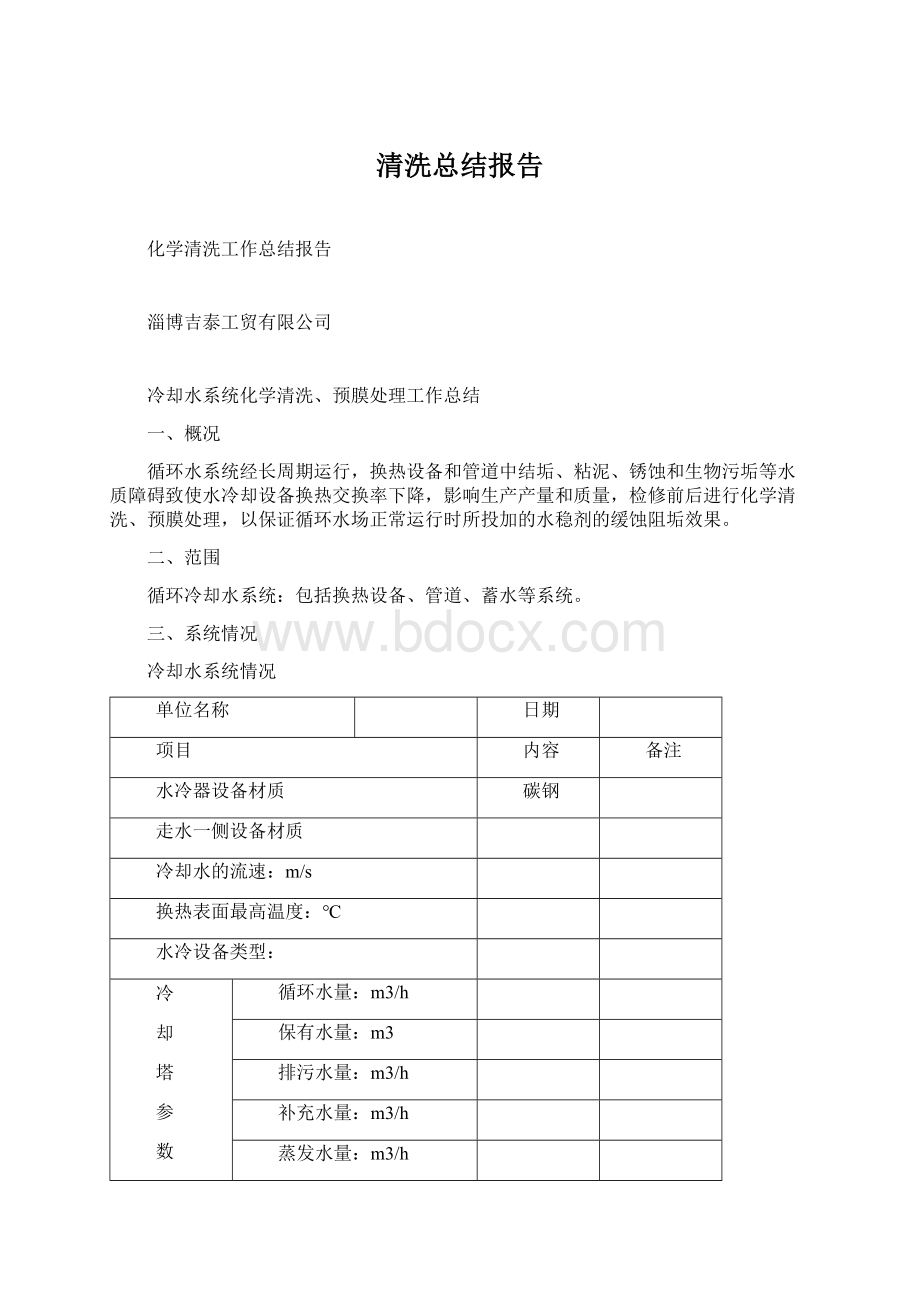
冷却水出口温度℃:
浓缩倍数:
3.5
旁滤水量:
有无处理装置
有无旁滤装置
有
有无加酸装置
有无通氯装置
有无其他防腐措施
目前存在的问题
补充水、循环水水质情况
项目
补充水
循环水
pH
总硬度(以CaCO3计)mg/L
暂硬(以CaCO3计)mg/L
永久硬度(以CaCO3计)mg/L
Ca2+(以CaCO3计)mg/L
Mg2+(以CaCO3计)mg/L
碱度(以CaCO3计)mg/L
HCO3-mg/L
CL-mg/L
SO42-mg/L
CODmg/L
浊度mg/L
电导率μs/cm
K+mg/L
SiO2mg/L
总铁mg/L
含油量mg/L
氨氮mg/L
温度℃
肉眼可见物
总固体mg/L
总溶固mg/L
悬浮物mg/L
细菌总数个/ml
四、化学清洗前的准备
1、委托方的准备
1.1对冷却水系统加药装置、加酸装置、排污阀门、补充水阀、流量计等进行确认,满足清洗时加药、加酸、排污、补水需要。
若不能满足迎接临时管线。
1.2安排1~2名熟悉冷却水处理和生产工艺的技术人员配合协调解决清洗过程中出现的问题。
1.3安排好冷却水操作人员,按方案要求配合清洗过程,进行冷却水量的调节,补水、排水工作。
2服务方的准备
2.1清洗人员在清洗前应熟悉现场,确认加药、加酸设备能否满足清洗要求,加药点、加酸点、药品存放等是否合理进行检查,和委托方一起确定监测挂片和取样口地点。
2.2设立临时化学清洗分析室,配制标准试剂,调试分析仪器,按照方案要求安排分析人员。
2.3安排好加药人员。
2.4工程负责人安排好清洗安全工作,督促所有施工人员遵守清洗安全规程和委托方的各项规章制度,做好全体施工人员的施工前的安全教育。
五、化学清洗
1、水冲洗
新装置水冲洗时不上冷却塔,不进冷水器,若不能循环,应安装临时管线。
采用边排污边补水的方式,冲洗至浊度<30mg/L后,再上冷却塔,进水冷器,继续采取边排污边补水方式进行冲洗,至浊度<20mg/L为止。
必要时应系统排空、清池。
2、油污清洗
2.1清洗配方:
油污清洗剂JTYQ-1400mg/L
消泡剂JTXP-150mg/L
2.2清洗步骤
(1)关闭排污阀,保持水池水位。
(2)按照总保有水量m3计算,一次性投加油污清洗剂JTYQ-1Kg,进行除油污清洗。
如果产生泡沫很大,可加消泡剂JTXP-1Kg,
(3)剥离期间不排污,水位不低时不补水。
剥离期间氯气正常投加。
(4)循环清洗24小时后排污置换,浊度≤20mg/L时进行下一步工作。
2.3分析及监测:
浊度---1次/4小时
3、粘泥剥离
3.1粘泥剥离配方:
粘泥剥离剂QX315JT350mg/L
消泡剂JTXP-1100mg/L
3.2剥离步骤
(2)按照总保有水量m3计算,一次性投加粘泥剥离剂QX315JTKg,消泡剂JTXP-1Kg,进行粘泥剥离处理。
3.3分析及监测:
4、除垢、除锈清洗
4.1化学清洗配方:
化学清洗剂JT-1611200mg/L
4.2清洗步骤
按总保有水量m3计算,向系统一次性投加化学清洗剂JT-161Kg,清洗16~24小时至终点,清洗期间不排污,水位不低时不补水。
化学清洗期间氯气正常投加。
4.3清洗终点
以总铁曲线趋于平稳为清洗终点,pH值曲线、浊度曲线作为辅助终点判断手段,若因系统积垢较重,清洗24小时后PH值曲线、浊度曲线仍未趋于平稳,亦应停止清洗(避免清洗过度),进行排污置换。
当排污置换至浊度≤20mg/L后,停止补、排水,进行下一步预膜工作。
4.4分析及监测:
清洗初期(6小时以前):
pH、浊度---1次/2小时
总铁---1次/4小时
清洗中期(6~16小时之间):
pH、浊度---1次/4小时
总铁---1次/4小时
清洗后期(16小时以后):
pH、浊度---1次/2小时
总铁---1次/2小时
六、系统预膜
1、预膜配方:
V-9605JT400mg/L
2、预膜步骤
按照总保有水量m3计算,向吸水池中一次性投加预膜剂V-9605JTKg,加工业硫酸控制pH在6.0~7.0之间,预膜48小时。
预膜期间,要求总磷控制在32~42mg/L之间,若总磷≤32mg/L,必须按下式追加预膜剂V-9605JT:
追加预膜剂V-9605JT(Kg)=(37-实测总磷)×
X
总磷控制在>
32mg/L的时间必须在16小时以上。
预膜期间,旁滤池停止运行,不排污,水位不低时不补水。
预膜同时进行挂片监测。
3、转入正常运行
预膜24~48小时后,强制排污,以新鲜水置换,向正常运行转换。
当总磷下降至≤15mg/L,可停止加酸。
当总磷降至≤8mg/L,连续往凉水塔补加缓蚀阻垢剂,转入正常运行,按正常运行时指标进行控制。
4、分析监测频率
总磷---1次/4小时pH---1次/2小时
七、实际操作分析数据
整个清洗预膜期间,服务方派专人全天候24小时跟班分析,并严格按照方案进行药剂投加工作(见附表1)。
八、化学清洗、预膜验收
预膜24小时后,取出挂片观察,在挂片表面可以清楚地观察到蓝紫色色晕,冷风吹干、干燥后,检查蓝膜较致密,膜对硫酸铜溶液溶液滴液反应色变时间差13s,效果较为理想。
九、问题及建议
附:
表1分析数据表
时间
浊度
铁
总磷
投加JT-161,挂入监测挂片
FeS钝化清洗工作总结
一、钝化清洗目的
石油加工企业在加工高含硫原油时,加工设备和管道内部会产生大量的FeS,FeS吸附,停工检修打开设备时,与空气中的氧接触能发生强氧化还原反应引发自燃,造成火灾或爆炸事故,设备和管道内的H2S对检修人员造成人身伤害和环境污染。
检修前对石油加工设备和管道进行钝化清洗,去除FeS等污物,消除H2S、RSH等异味,达到检修人员进人设备进行检修作业的条件。
二编制依据
l、GB/T8978污水综合排放标准
2、GB50484石油化工建设工程施工安全技术规范
三、FeS钝化清洗药剂及使用
1、JT-1多功能FeS高效钝化剂,易溶于水,无毒、无害,该产品具有液相进料、气相钝化FeS的特点。
2、该剂能够有效、快速地去除设备和管道内的FeS、Fe203等无机垢,吸收H2S、RSH,消除异味,降低污水的氨-氮含量,对环保无不利影响。
其主要物化指标为:
项目
技术指标
试验方法
密度,g.cm-3(20℃)
≥1.05
GB/T1884
外观
浅黄色
目测
3、配制
根据设备上FeS的集结程度,确定JT-1型FeS钝化剂的用量。
药剂与水比例按1~10(剂:
水)混合均匀后使用,或先注水再注剂,先注剂再注水进行循环。
四、钝化清洗设备
此次列入清洗的设备有:
设备名称:
五、钝化清洗方案
1、钝化清洗前的准备
1.1委托方的准备
1)停工过程中,对设备和管道须进行油洗、水洗及高温蒸汽吹扫,除去内部集结的油污。
2)多年未进行清洗的设备,车间在停工过程中应彻底吹扫、水洗、蒸汽气提干净,除去内部集结的油污,保证下一步清洗工作的顺利进行;
3)清洗过程中车间派1~2名熟悉设备钝化清洗和工艺流程的技术人员协助钝化清洗服务人员的施工,解决施工过程中出现的问题。
4)保证清洗过程中水、电、汽的正常供给。
5)和钝化清洗服务方一起确认清洗设备和药剂的存放位置和地点。
1.2服务方的准备
1)清洗人员在清洗前应熟悉现场,确认加药设备能否满足清洗要求,加药点、药品存放等是否合理进行检查,和委托方一起确定取样口地点。
2)设立临时化学清洗分析室,配制标准试剂,调试分析仪器,按照方案要求安排分析人员。
3)安排好加药人员。
4)工程负责人安排好清洗安全工作,督促所有施工人员遵守清洗安全规程和委托方的各项规章制度,做好全体施工人员的施工前的安全教育。
5)注水及添加药剂流程需要取得车间及有关部门的同意方可进行操作;
6)设备内需提前注入一定量水的,注水量一定要控制在安全线以下,防止水溢流或窜入其它部位。
2、钝化清洗步骤
2.1系统
拆除塔底底循环排空附线阀前法兰(PN,DN),通过三通接临时接线至清洗用循环泵入口、至循环泵出口再接临时线至塔顶入口法兰(PN,DN)。
1)、加水
清洗前请车间向塔注水至塔底部液位计满,清洗开始后将塔底液体经循环泵抽出按清洗循环流程进行循环,如水量不足需向塔内补适量水。
2)、注剂
从临时接线处清洗用循环泵入口前三通处将钝化清洗、将钝化剂注剂塔底;
3)、清洗循环
为了达到清洗要求,需要进行下述工作:
塔底→临时接线→循环泵入口至循环泵出口临时线→塔顶→塔底,进行循环;
上述循环运行6~8小时后,采样分析合格后按照规定排污。
4)、排放流程
从塔底部放空处、临时施工三通跨线处放空。
5)、用药量吨。
六.清洗钝化时间
钝化液循环或浸泡6~8小时后,钝化液循环结束,钝化工作结束,停泵。
根据各装置的开停工方案,恢复各阀阀位。
七.质量要求
化学处理完毕,排放废液及设备在检修过程中不发生FeS钝的自燃问题,达到下表指标要求:
序号
指标
1
系统内硫化氢清除率
100%
2
硫化亚铁清除率
≥95%以上
3
轻油乳化能力
>50g/L以上
4
腐蚀率:
20#碳钢材质
<6g/m2.h
不锈钢、铜材质
<2g/m2.h
5
废液
COD
≯700mg/L
氨氮
≯80mg/L
硫化物
≯30mg/L
八.验收
1、设备和管道钝化清洗后的效果:
所有钝化清洗部位的人孔打开后,会同车间、厂设备部、安环部、生产技术部等单位对有关人员对清洗情况进行了检查,塔壁、人孔壁、容器等部位处理的比较干净,塔内未发现有积存油泥,未出现冒烟、着火情况,达到了清洗的目的,见部分设备钝化清洗后照片。
C-03系统
C-04系统
C-05系统
C-06系统
2、废液
清洗残液经环保监测部门化验COD、氨氮、硫化氢等有害物质指标合格,可排污水处理场,不造成二次污染。
3、通过验收。
九问题及建议
胺液在线净化工作总结
一净化的目的
干气、液化石油气脱硫装置的甲基二乙醇胺溶剂长时间使用后,溶剂中固体颗粒、热稳态盐(HSS)、油类等杂质含量较高,胺液污染较重,溶剂易发泡夹带跑损,脱硫化氢效果差,设备腐蚀严重。
采用胺液在线净化技术可使受污染胺液得到彻底净化。
净化后胺液外观明显改善,胺液中铁离子含量明显降低、热稳态盐脱除明显,胺液脱硫能力明显提高,胺液发泡高度和消泡时间得到改善,各项理化指标接近新鲜胺液的水平,应用效果显著,解决了脱硫溶剂的污染问题,避免了装置一次性更换大量脱硫溶剂,废剂无害化处理的困难。
胺液在线净化装置操作简便,在线净化期间不影响气体脱硫装置平稳运行,仅需对过滤器中的净化介质用少量除盐水冲洗,对吸附罐内的离子树脂用少量质量分数为32%的碱液再生。
气体脱硫装置系统胺液净化一次可平稳运行1~2月,期间不需胺液在线净化装置连续运行。
二净化前的准备
1、泵的准备
1.1轴承充油、油位正常、油质合格。
检查储油室油位(视镜或油杯),必要时加油;
确保电机已加入合格适量的润滑油(脂)。
1.2全开进口阀门,打开放气阀排气,使液体充满泵腔,然后关闭排气阀。
1.3检查各部位是否正常,轴承是否润滑良好,各部位螺栓是否紧固,吸入管是否通畅等,检查轴封漏水情况,填料密封以少许滴水为宜,现场及远传仪表、控制阀门是否合格
1.4用手盘泵2~3圈,应感觉轻松且轻重均匀,并注意辨别泵内有无磨擦声和异物滚动等杂音,如有则应设法排除,并将联轴器的护罩安装好。
对于结构严密的电机,无法用手盘泵的,应对电机进行点动检查。
2、净化设备的准备
2.1检查过滤器,装好滤网,盖盖密封。
2.2检查树脂净化床,或更换树脂,盖盖密封。
2.3净化设备进出口阀门处在灵活好用状态,压力表指示正常。
三净化方案
1、净化原理
利用高性能离子交换树脂,把含有热稳态盐阴离子的贫液溶剂通过阴离子交换树脂床,以OH—交换热稳态盐阴离子,除去胺液中的热稳态盐阴离子,使净化后胺液中的热稳态盐含量降低至0.5%以下,有效去除胺液中的热稳态盐阴离子。
2、净化工艺
胺液净化工艺其主要原理:
高性能离子交换树脂选择性地吸附胺液中的热稳态盐阴离子,在稀碱溶液中热稳态盐阴离子又能从树脂上脱附从而得到再生。
主要设备为过滤器、树脂净化床、碱液储罐、正压防爆控制柜。
进行七个步骤的循环工作:
净化胺液、胺液回收、树脂再生、碱液回收、碱液淋洗、碱液配制、暂停。
3、净化工艺流程
净化后胺液回装置
待净化胺液
胺液净化工艺流程图
注:
过滤器A、过滤器B两个设备去除待净化胺液中的固体悬浮物,设备运行时一开一备;
树脂净化床A、树脂净化床B两个设备去除待净化胺液中的热稳态盐和胺降解物,设备运行时一开一备。
3.1胺液净化设备运到现场后,胺液净化设备的循环泵入口与装置的贫胺液罐相连接,净化后的胺液出口与贫胺液罐泵出口连接,即净化后的胺液进气体脱硫塔。
3.2连接好后要认真检查,确保连接处无泄漏。
3.3达到运行条件后,和车间主任联系开始运行净化循环。
3.4净化期间,操作人员不得擅自离岗,定时巡检做好记录,检查内容包括:
压力、流量、进出口颜色变化等,发现异常及时报请有关部门进行处理。
按时采样进行热稳态盐含量分析做好记录,达到要求后停泵,完成胺液净化任务。
4、循环净化泵的启动
4.1在检查完毕,确认没有问题后可以启动泵
4.2全开进口阀门,关闭出口管路阀门,关闭压力表,流量计出口阀门
4.3起动电机(注意旋向是否正确),转速稳定后缓慢打开压力表,流量计的阀门,一切正常后,逐步开启出口阀,观察压力表、流量表、检查轴封泄漏情况。
调整到所需工况,注意关阀空转的时间不宜超过3分钟
4.4检查电机、轴承处温升≤70℃,如有异常,应及时处理。
5、运行期间的维护与检查
5.1轴承的检查
A、轴承温度不超过75℃。
B、轴承室不能进水、进杂质,油质不能乳化或变黑。
C、滚动轴承稀油润滑时,油面应不低于油标中心线。
D、是否有异音,滚动轴承损坏时一般会出现异常声音。
5.2真空表、压力表读数是否正常
A、真空表指针不能摆动过大,过大可能使泵入口发生汽化,另外真空表读书也不能过高,过高可能是入口阀堵塞,卡住或吸水池水位降低等。
B、出口压力表读书过低,可能是密封环、导叶套严重磨损。
定、转子间隙过大,或者是出口阀开启太大,流量大、扬程低。
C、电机发热,自动跳闸,可能是流量大,或者是定、转子之间产生摩擦。
5.3泵机组是否产生较大的振动,造成振动的原因有:
A、水泵和电机轴心线不对中。
B、水泵或电机底脚螺栓松动,或者基础不牢。
C、转子质量不平衡。
D、泵在小流量运行,产生径向力、回流、气蚀。
5.4密封工作是否正常
A机械密封正常运行时不会有滴漏。
B有冷却水装置的,要检查水流是否正常。
6、停泵
6.1泵停泵应先关闭出口阀,以防逆止阀失灵致使出水管压力水倒灌进泵内,引起叶轮反转,造成泵损坏。
6.2如果惯性小,即断电后泵很快就停下来,说明泵内有摩卡或偏心现象。
6.3如果是长时间停泵,要注意做好泵的维护。
要放空泵内的水,防止结晶堵塞或腐蚀生锈
四树脂再生
混合离子交换柱柱内再生分为反洗分层、树脂再生、正洗等几步。
1、反洗分层
反洗流速为10m/h,反洗时间一般为15~20min,待反洗水清晰后,停止通水,使树脂层落实,检查树脂分层情况。
分层好的树脂在进酸管附近有明显的颜色区别,如分层不明显,可重新反洗分层。
2、树脂再生
从交换柱顶部加入NaOH溶液,再生废液从底部排出,控制NaOH用量为树脂量的3~4倍,注碱浓度3.O%~3.5%,注碱流速为5m/h。
3、正洗
注碱结束后,从交换柱顶部通入试剂水,清洗废水从底部排出,对柱内树脂进行清洗。
正洗终点为清洗水碱度<
O.5mmol/L。
五胺液在线净化监测
在线净化监测项目频率
分析项目
单位
分析频率
1次/每周四
热稳态盐含量
%(m/m)
胺液发泡高度
cm
1次/2周
消泡时间
s
>
1µ
m固体颗粒脱除率
%
有效载荷
mol/mol
六验收
1、胺液净化效果主要考虑:
胺液中的热稳态盐去除率、干气脱硫溶剂循环量的降幅、再生塔负荷降低幅度等。
该装置脱硫胺液在线净化运行天,在净化过程中按方案要求及时采样检验分析,分析结果见表:
胺液在线净化后胺液分析结果
实测结果
合同指标
清澈透明,无沉淀、无悬浮物
≥98%
发泡高度
<
2.5cm
2.5s
胺液中热稳态盐含量
≯1%(m/m)
6
胺液有效载荷
≥0.43mol/mol
2、脱硫胺液在线净化工作结束后,会同车间、生产技术部等单位有关人员对净化胺液跟踪分析结果进行评判,认为各项指标基本达到合同的要求,在整个净化过程中生产正常,产品质量完全满足生产要求,脱硫胺液运行设备运转平稳。
3、胺液在线净化过程中,没有废液胺液排除,工作环境保持较好。
4、同意验收。
七存在问题及建议