影响smt涂覆质量的因素Word文档下载推荐.docx
《影响smt涂覆质量的因素Word文档下载推荐.docx》由会员分享,可在线阅读,更多相关《影响smt涂覆质量的因素Word文档下载推荐.docx(15页珍藏版)》请在冰豆网上搜索。
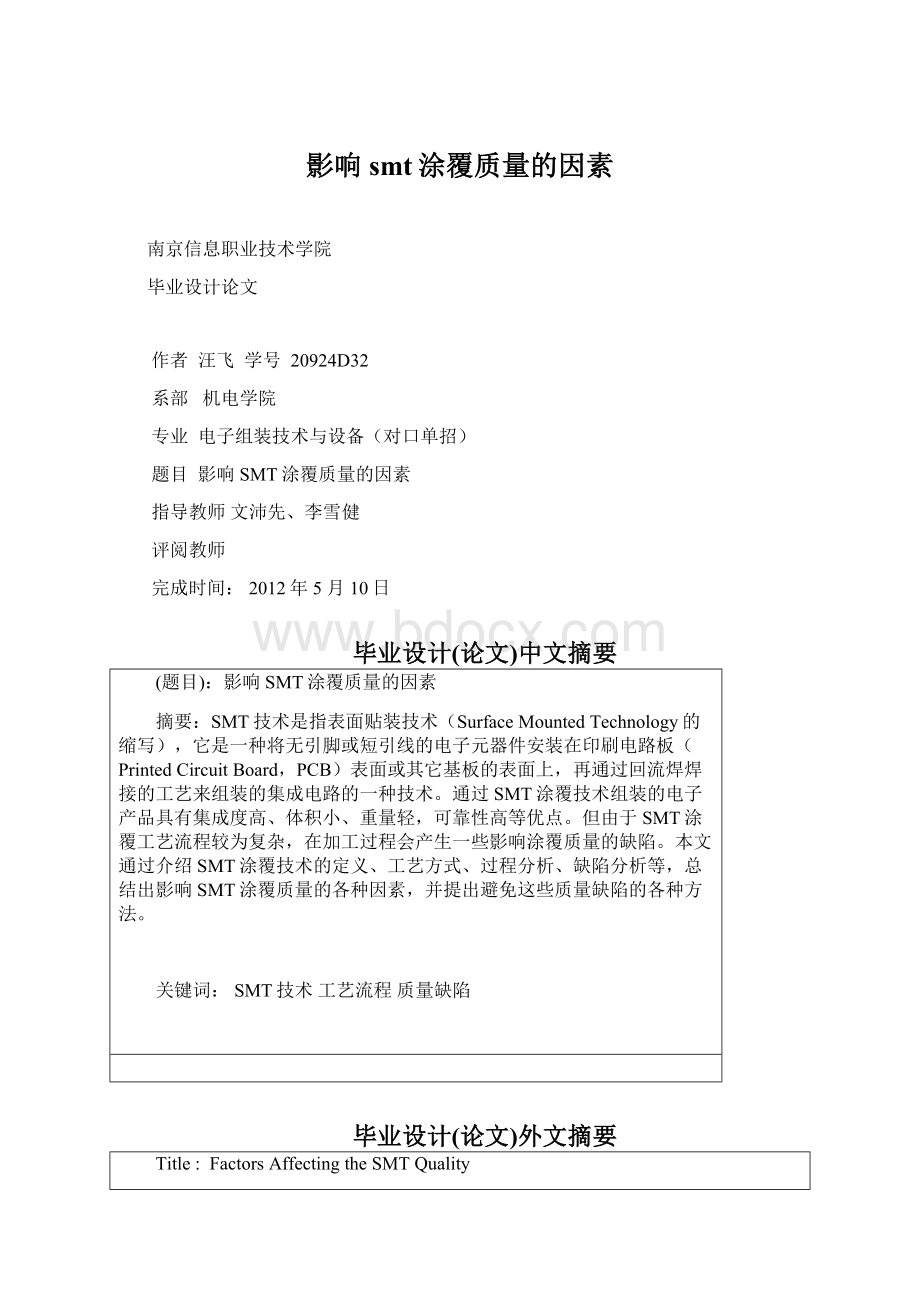
FactorsAffectingtheSMTQuality
Abstract:
SMTtechnologyisSurfaceMountedTechnologyofabbreviation.Itisatechnologyofintegratedcircuits.Itinstallsnopinorshortleadsofelectroniccomponentsmountedonthesurfaceoftheprintedcircuitboardorothersubstrate.ThenReflowassemblyofintegratedcircuitsbyweldingprocess.ElectronicproductsthatUsingofweldingtechnologyishighintegration,smallsize,lightweightandhighreliability.BecausetheSMTcoatingprocessiscomplex,Processingwillproducesomecoatingqualitydefects.ThisarticleintroducestheSMTcoatingtechnology,includingdefinition,Processmethods,ProcessanalysisandDefectAnalysis.Itsummarizesavarietyoffactors,whichaffectingthecoatingquality,andproposesavarietyofmethods,whichavoidingqualitydefects.
Keywords:
SMTTechnology,ProcessAnalysis,QualityDefects
目录
毕业设计(论文)中文摘要1
毕业设计(论文)外文摘要2
1引言4
2SMT技术介绍4
2.1SMT技术的发展4
2.2SMT的技术特点及优势5
2.3SMT涂覆工艺7
2.3.1贴片胶涂覆工艺7
2.3.2焊膏模板印刷工艺8
3涂覆设备9
3.1印刷设备9
3.2点涂设备10
4SMT涂覆质量要求10
5影响SMT涂覆质量的因素及解决办法11
5.1焊膏本身导致涂覆质量的因素11
5.2印刷机及印刷过程导致涂覆质量的因素12
5.3线路板导致的质量缺陷13
5.4贴片胶对涂覆质量的影响13
5.5涂覆工艺技术参数对涂覆质量的影响13
5.6解决办法14
结论15
致谢15
参考文献16
1引言
SMT是SurfaceMountedTechnology的缩写,指的是电子元器件表面安装技术,它是一种将无引脚或短引线表面组装元器件安装在印制电路板(PrintedCircuitBoard,PCB)的表面或其它基板的表面上,通过回流焊等设备加以焊接组装的电路装连技术。
通过SMT技术组装的电子产品广泛应用于计算机、通讯、航空航天等各个领域,是目前电子组装行业里广泛应用的一种技术和工艺。
伴随着SMT技术的不断发展,SMT涂覆设备也在不断更新,但相应的问题也随之产生,在复杂的工艺流程过程中,难免会出现很多影响SMT涂覆质量的因素,下面本文就分析一下SMT涂覆技术的相关设备及工艺流程,并通过多种角度来分析影响SMT涂覆质量的一些因素及相关的解决方案。
2SMT技术介绍
2.1SMT技术的发展
SMT技术诞生于美国,在1963年,美国飞利浦公司生产出了全世界第一块表面贴装的集成电路,在这种产品刚刚产生的时候,主要都是应用于军事,航空航天等高尖端技术,由于其价格因素,民用设备很少使用。
但其集成度高、体积小、可靠性高等诸多优点极大地推动了电子产业的发展。
随着SMT技术迅猛发展,产品成本也不断的下降,后来逐渐应用于计算机硬件、通讯设备、电子产品、汽车工业等各个工业领域。
进入21世纪以来,中国的电子信息产业市场空前巨大,电子产品制造业加快了发展的脚步,每年都以20%以上的速度在高速增长,尤其在长江中下游、珠三角地区的大部分省市,电子产业已经成为其经济支柱产业,整体规模连续三年居全球第2位。
随着中国电子制造业的高速发展,中国的SMT涂覆技术也在同步迅猛发展,整体规模也居世界前列。
SMT技术的发展主要经历了以下几个阶段:
最初阶段:
在上世纪60年代到70年代中期,SMT涂覆技术加工小型化,混合集成电路,这些产品主要应用在计算器、电子表等产品上;
第二阶段:
从1976年之后,SMT技术得到了长足的进步,集成电路的体积大大减小,集成度显著增加,电路功能也日益强大,这个阶段,产品主要应用于摄像机、录像机、数码相机等多媒体产品上;
第三阶段:
进入了80年代以后,SMT涂覆技术无论从材料还是设备来讲,其成本都大大降低,所以产品的性价比显著提高,其竞争优势明显,产生了超大规模集成电路,应用于计算机、通讯设备等诸多领域;
现阶段:
从90年代中期到现在,SMT涂覆技术日趋成熟,正朝着微组装、高密度组装、立体组装的方向发展,无论从产品的性能和价格来讲,其他技术很难撼动其地位。
据国外相关资料报道,从90年代以来,全球采用通孔组装技术的电子产品正以年11%的速度下降,而采用SMT的电子产品正以8%的速度递增。
到目前为止,日、美等国已有80%以上的电子产品采用了SMT。
[1]图2-1为应用SMT技术加工而成的电脑主板。
图2-1运用SMT技术生产的电脑主板
2.2SMT的技术特点及优势
所谓表面贴装技术,是指把片状结构的元器件或适合于表面组装的小型化元器件,按照电路的要求放置在印制板的表面上,用回流焊等焊接工艺装配起来,构成具有一定功能的电子部件的组装技术。
而传统的通孔插装技术采用“插”的方式,这是二者最重要的差别。
此外,两者的差别还在于基板类型的不同、元器件选择的差异、以及组件形态、焊点形态和组装工艺流程等各个方面的差异。
表面组装技术和通孔插装元器件的方式相比,具有很大的优越性,主要有以下几点:
1)元器件实现微型化。
SMT技术使用的电子元件,其几何尺寸和占用空问的体积比通孔插装元器件小得多,一般来讲可以减小60%到70%的体积,甚至可减小90%的体积。
体积的减小导致了重量也随之减轻,一般会减少60%到90%。
更适合小型设备的使用。
2)信号传输速度快。
SMT加工而成的电路板、结构紧凑、集成度高,在双面贴装时,组装密度可以达到5.5~20个焊点/cm,由于电子元件之间连线短、所以延迟很小,极大的提高了信号传输的速度。
同时,电路板的抗振动,耐冲击的性能也大大加强了,这些优点对于电子设备超高速运行有很大的现实意义。
3)高频特性优良。
由于元器件没有引线或者引线很短,所以大大降低了电路的分布参数,降低了射频干扰,所以高频特性好。
4)极大地提高了集成电路的生产效率。
由于片状元器件外形尺寸标准化、系列化以及焊接条件的统一性,SMT涂覆技术生产流程自动化程度很高,不但减少了在焊接过程中失效元件的数量,还降低了焊接时间,提高了电路板的可靠性。
5)材料的成本比较低廉。
现在,除了少量片状化困难或封装精度特别高的电子元件以外,绝大多数SMT元器件的封装成本已经低于同样类型、同样功能的THT元器件,所以SMT技术生产出的电路板的销售价格要更低廉,极大地增加了市场竞争力。
6)SMT工艺流程简单,降低了生产成本。
在加工电路板时,由于元器件没有引线,所以减少了原来整形、打弯、剪短引线的流程,这使整个生产过程缩短很多,大大提高了生产效率。
具有相同功能的集成电路,采用SMT技术加工成本低于通孔插装方式50%左右。
综上所述,由于SMT涂覆技术的诸多优点,现在正在全面取代传统的THT技术,成为电子工业界最常用,最流行的元件组装技术。
2.3SMT涂覆工艺
表面组装涂覆工艺就是把一定量的焊膏或胶水按要求涂覆到PCB上的过程,即焊膏涂覆和贴片胶涂覆,它是SMT生产工艺中的第一道工艺。
焊膏涂覆就是把就是将焊膏涂覆在PCB的焊盘图形上,为SMC/SMD的贴装、焊接提供粘附和焊接材料。
焊膏涂覆有点涂、丝网印刷和金属模板印刷三种方法。
其中金属模板印刷是目前应用最普遍的方法。
贴片胶涂覆就是将胶水涂覆在PCB规定位置上,这样在混合组装中就可把表面组装元器件暂时固定在PCB的焊盘图形上,以便随后的波峰焊接等工艺操作得以顺利进行。
贴片胶的涂覆有分配器点涂、针式转印和印刷三种方法。
应用最多的是分配器点涂。
2.3.1贴片胶涂覆工艺
贴片胶的作用是在混合组装中把表面组装元器件暂时固定在PCB的焊盘图形上,以便随后的波峰焊等工艺操作得以顺利进行;
在双面表面组装情况下,辅助固定SMIC,以防翻版和工艺操作中出现振动时导致SMIC掉落。
因此,在贴装元器件前,就要在PCB上设定焊盘位置涂覆贴片胶。
贴片胶涂覆可采用分配器点涂技术、针式转印技术和印刷技术。
如图2-3、图2-4、图2-5所示。
分配器点涂是将贴片胶一滴一滴的点涂在PCB贴装元器件的部位上;
针式转印技术一般是同时成组的将贴片胶转印到PCB贴装元器件的所有部位上;
印刷技术与焊膏印刷技术类似。
图2-3分配器点涂技术图2-4针式转印技术
图2-5模板印刷技术
分配器点涂技术
分配器点涂是涂覆是涂覆贴片胶最普遍采用的方法。
先将贴片胶灌入分配器中,点涂时,从上面加压缩空气或用旋转机械泵加压,迫使贴片胶从针头派出并脱离针头,滴到PCB要求的位置上,从而实现贴片胶的涂覆。
采用该方法进行贴片胶点涂时,气压、针头内径、温度和时间是重要工艺参数。
分配器点涂技术的特点是适应性强;
易于控制;
性能稳定。
贴片胶点涂涂覆过程如图2-3所示
图2-3贴片胶点涂过程
2.3.2焊膏模板印刷工艺
1.模板印刷原理
焊膏模板印刷工艺目的是为PCB上元器件焊盘在贴片和回流焊接之前提供焊膏,使贴片工艺中贴装的元器件能够黏在PCB焊盘上,同时为PCB和元器件的焊接提供适量的焊料,已形成焊点,达到电气连接。
2.模板印刷的基本过程
焊膏模板印刷的基本过程如图2-2所示,概括起来可分为5个步骤:
对位、填充、刮平、释放、擦网。
与这些步骤有关的主要设备结构有印刷刮刀头模块、印刷工作台模块、CCD照相识别模块、模板调节模块、模版清洗机构、导轨调节模块。
图2-2焊膏模板印刷过程
3涂覆设备
3.1印刷设备
锡膏印刷机的组成部分包括装版、加锡膏、压印、输电路板等机构。
印刷机的工作原理是:
先把要印刷的电路板制成印版,然后在装在印刷机上,然后由人工或印刷机把焊锡膏涂敷于印版上有文字和图像的地方,再直接或间接地转印到电路板上,从而印出和印版相同的PCB板。
在生产线之中,印刷机处在生产线的最前端,印刷机的优劣直接决定了PCB板质量的好坏。
锡膏印刷机分为全自动印刷机和半自动印刷机,一般生产能力强的大型生产线均采用全自动锡膏印刷机。
图3-1-1锡膏半自动印刷机图3-1-2锡膏半自动印刷机
3.2点涂设备
随着元器件越来越小以及愈加复杂,能否准确的在印制电路板指定位置上进行胶水或焊膏微量涂覆已经成为许多工艺对设备的一项重要要求。
点涂可以简单地定义为通过压力的作用使液体发生移位。
点胶机是用途广泛的点涂设备,可注滴瞬间胶(快干胶)、红胶、黄胶、环氧树脂、硅胶、厌氧胶(螺丝胶)、防焊剂、锡浆、润滑油、焊膏等产品。
点胶机可分为手动和自动两种,手动点胶机用于试验或小批量生产,自动点胶机用于大批量生产。
如图3-2-1和3-2-2所示
图3-2-1手动点胶机图3-2-2自动点胶机
4SMT涂覆质量要求
通过SMT涂覆工艺加工制成的优质PCB板具有理想的焊点,理想的焊点具有良好的表面润湿性,即熔融焊料在被焊金属表面上应铺展,并形成完整、均匀、连续的焊料覆盖层,其触角应不大于90度。
正确的焊锡量使焊料足够而不过多或过少,良好的焊接表面保证了焊点表面的完整、连续和圆滑,但不要求很光亮的外观。
在整块PCB板当中,应避免开焊,虚焊,元件位置偏移、焊点拉尖等不良现象。
图5-1表示出SMT涂覆质量的要求。
图5-1SMT涂覆质量的要求
5影响SMT涂覆质量的因素及解决办法
5.1焊膏本身导致涂覆质量的因素
焊膏的黏度。
黏度太大,焊膏不易穿过模版的开孔,印出的线条残缺不全,黏度太小,容易流淌或塌边影响印刷的分辨率和线条的平稳性。
焊膏的粘性。
焊膏的粘性不够,印刷时,焊膏在模板上不会滚动,其直接后果是焊膏不能全部填满模板开孔,造成焊膏沉积量不足。
焊膏的粘性太大则会使焊膏挂在模板孔壁上而不能全部漏印在焊盘上。
焊膏颗粒的均匀性与大小。
一般焊料颗粒直径约为模板开口尺寸的1/5。
焊膏的金属含量。
随着金属所占百分含量的增加,焊料厚度也增加。
但在给定的黏度下,随金属含量的增加,焊料桥连的倾向也相应增大。
5.2印刷机及印刷过程导致涂覆质量的因素
1)印刷机在固定电路板时夹持发生松动。
2)印刷机长时间工作,没有及时补充焊锡膏,导致焊锡膏不足
3)网板有问题,镂孔位置偏移。
4)网板有赃物,未擦拭洁净。
5)网板问题使焊锡膏阻塞,不容易落下。
6)电路板在印刷机内的固定夹持松动。
7)焊锡膏刮刀的压力、角度、速度以及脱模速度等设备参数设置不合适。
8)控制不好,容易造成焊量不足(a)、形成碎片(b)、印刷偏移(c)、焊膏残余(d)、焊坑(e)、桥连(f),图5-2所示
图5-2涂覆常见缺陷
9)焊锡膏印刷完成后,因为人为因素将焊锡膏挤压粘连。
10)印刷机的光学定位系统发生故障。
11)焊锡膏漏印网板开孔与电路板的设计文件不相符。
12)焊锡膏漏印网板上有污染物(如PCB包装纸、网板擦拭纸、空气中漂浮的沙尘、毛发等异物)。
13)焊锡膏刮刀损坏、网板损坏。
14)焊锡膏印刷完成后,造作人员不慎将焊锡膏碰掉。
15)电路板与漏印网板分离时的脱模参数设定有问题。
漏印网板镂孔的孔壁有毛刺。
5.3线路板导致的质量缺陷
1)电路板在设计过程中存在缺陷,焊盘间距太小。
2)电路板上的定位基准点不清晰。
3)电路板上的定位基准点与网板的基准点没有对正。
4)电路板在印刷机内的固定夹持松动,定位顶针不到位。
5)电路板质量出现问题,焊盘上有不显眼的覆盖物,如油墨与FPC直接夹有杂物(图5-3-1所示)
图5-3-1油墨与FPC直接夹有杂物
5.4贴片胶对涂覆质量的影响
1)固化温度较高、固化时间较长
2)贴片胶黏度的变化对胶点的均匀一致性影响较大,影响贴片胶黏度的主要因素是温度和压力
5.5涂覆工艺技术参数对涂覆质量的影响
1)温度将影响黏度和胶点形状,温度升高,贴片胶的黏度会降低
点胶压力的大小影响贴片胶的黏度和点胶量
针头内径决定了胶点内径,针头内径偏大。
将导致胶点内径偏大,胶点量偏多,贴片胶漫流,影响焊盘的焊接质量
5.6解决办法
1)焊膏
选用活性较高的锡膏,改善锡膏印刷参数,特别是模板的窗口尺寸。
选择粘度适中的焊膏
使用搅拌机搅拌(2-3分钟),手动搅拌(3-5分钟,60-80次/分钟)时注意将锡膏整体搅拌。
检查是否为同批次,如果是则为供应商问题,如果不是则为人员保管使用方法不当造成
2)印刷参数设置
根据测量锡膏厚度的CPK值,调整印刷机支撑块及印刷速度、刮刀压力等参数,如图5-3-2所示。
定时检查钢网张力符合标准,根据产品选择适合的自动及手动清洗钢网的方式和频率。
图5-3-2参数取值图
调整印刷脱膜速度(一般0.5-0.8mm/s),钢网使用激光切割或者激光加电抛光,针对工艺要求严格可使用电铸钢网,减少锡膏在钢网上的静止停留时间,使用适合黏加强清洗,增加钢网厚度(考虑有细小间距元件可开Step-up钢网)或者加大开孔尺寸,可开到焊盘以外,另外也可考虑基板和网板的一些特殊设计。
3)印刷过程
严格管控作业,在生产时尽量不人为移动PCB,或者带手套拿板边。
控制贴片压力或者人为因素。
4)物料
改善焊盘设计与布局,如图5-3-2所示
图5-3-2焊盘设计
增加PCB光识别能力
根据产品是否有细小元件选择不同厚度的钢网,
对物料进行检验,看是原料问题还是保存不当,然后采取响应措施。
增加PCB焊盘防氧化层(表面镀金或镀银),增加焊盘可焊性能。
PCB本身工艺特性的改善,据需要可以给PCB添加高温保护胶或者根据实际情况增加治具。
5)环境
生产环境温度控制在25+-3,湿度控制在50%+-10%。
结论
综上所述,SMT涂覆技术是一种将无引脚或短引线表面组装元器件安装在印制电路板的表面或其它基板的表面上,通过回流焊焊接方法加以焊接组装的电路装连技术。
由于SMT涂覆工艺的复杂性,在加工过程中会出现一些质量缺陷,这些缺陷是多种原因作用的结果,有可能是焊接材料造成的,也可能是设备原因造成的,还可能是加工工艺造成的。
所以在做具体的缺陷分析时,一定要从多角度、多侧面进行考虑,不要漏掉任何一个可能产生质量缺陷的环节,这样才能达到标本兼治的效果。
致谢
本人在撰写此论文的过程中,受到了很多老师和同学的帮助,更要特别感谢我的导师文沛先的指导与督促,同时感谢她的对我的谅解与包容。
没有某老师的帮助也就没有今天的这篇论文。
撰写论文的过程是艰苦的,但也是快乐的,每一次的进步都离不开老师和同学对我的帮助。
在这四年的求学之路上,是你没给了我莫大的鼓舞与支撑,让我从一个懵懂的少年变成一名大学毕业生,再次感谢给予我帮助的每一个人,在这一刻,将最崇敬的谢意献给你们。
此外,本论文参考了大量的文献资料,是学术界的前辈孜孜不倦的努力使微电子产业蓬勃的发展,在此,向各学术界的前辈们致敬!
参考文献
1张文典.表面组装技术基础.北京:
电子工业出版社,2009.
2廖芳.电子产品生产工艺与管理.北京:
3贾忠中.SMT工艺质量控制.北京:
电子工业出版社,2010.
4曹元玲.表面贴装技术(SMT)工艺,今日科苑.2008(02).