工业硅电炉生产和管理Word文档下载推荐.docx
《工业硅电炉生产和管理Word文档下载推荐.docx》由会员分享,可在线阅读,更多相关《工业硅电炉生产和管理Word文档下载推荐.docx(16页珍藏版)》请在冰豆网上搜索。
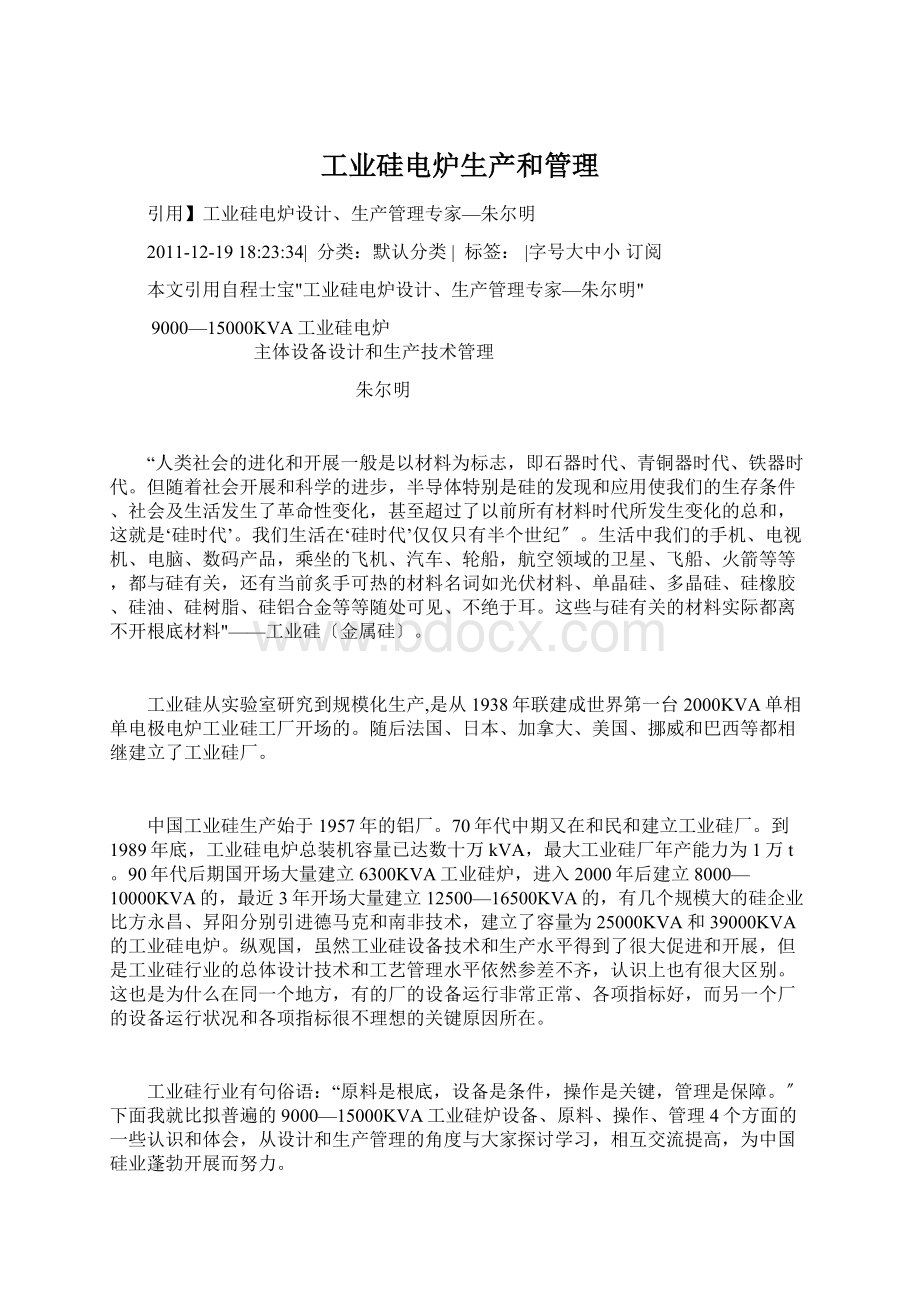
〞2009年初,我们通过对9000KVA以上的硅炉的故障问题和操作特点作了大量数据的收集梳理、总结分析,结合多年设计和生产管理经历,对以往的设计和理念做了重大调整改良和提炼。
对新设计和改造的硅炉,在细节上下功夫,使设备故障率小于1%,保证长期稳定运行,为稳产高产、节能降耗创造条件。
1、厂房的合理设计
重点是保证捣炉机工作时伸缩、旋转自如、空间大;
全方位加料无死角;
出炉口宽阔不设立柱;
液压系统所有元件远离高温区;
电极库房〔我们一般设在冶炼跨三楼平台〕、浇铸车间、精整破碎包装车间、成品库独立分开。
厂房布置有两种形式:
①如果电极采用倒三角布置,那么选用单台三相变压器,尽量靠近炉体但又与高温烟气隔离,可以做到短网最短,而且根本对称,减少强弱相。
主厂房较低,总体投资较省。
〔见图1〕
图1
工业硅三相变压器厂房立面图
②如果采用三台单相变压器布置,那么多一楼层,主厂房增高。
整体投资较高。
〔见图2〕
2、炉衬
高温区采用自焙碳砖与半石墨化碳砖结合的方式,外围用高铝砖、粘土砖、轻质保温砖,炉孔采用全石墨砖或半石墨质—半碳化硅整体转,可以正常使用四年不用大修炉衬。
筑炉方式一般分为有缝和无缝砌法两种。
有缝法〔见图3〕是传统砌法,对碳砖的外形几何尺寸没有要求;
无缝法〔和图4〕是近几年出现的,要求碳砖必须精加工,几何尺寸要求严格。
3、电极把持设备—压力环
电炉容量越大,铜瓦数量越多,压力环构造越复杂。
而压力环是整个电炉的核心设备。
其设计合理与否,直接影响到连续生产、甚至电力单耗和产量指标。
因此选用碟形弹簧式不锈钢压力环,设计时考虑到大电流强磁场的影响,采取了屏蔽磁场的措施来保护碟簧不被磁化发红而影响弹性,这样就做到了免维护,且抱紧力始终大于10吨,可以做到每块铜瓦一对一单独调整,与波纹管效果一样。
但碟簧这种构造比拟简单,无需在高温区设置液压油路。
本设计已经在近30台电炉上使用,实践证明了以上优点。
只要安装调整到位,保证铜瓦与电极之间3.5Kg/cm2以上的接触压力,铜瓦是不会打弧的,压放电极时也不用松铜瓦。
德宏、和有几个公司生产运行一年多没有打过弧,也没有换过一块铜瓦。
铜瓦除被刺火烧坏之外,没有打弧损坏的。
〔见图5〕
4、电极升降与压放
电极升降系统采用液压,用单向调速液压缸〔上升靠油压,下降靠自重〕,电极到炉底自动停顿下降,可以保护电极及设备不受损坏;
压放采用液压与碟形弹簧结合的方式〔也有采用气囊构造的〕,正常生产时弹簧抱紧。
液压只在需要压放电极时工作,提高了的可靠性。
一套液压系统做到了电极升降与压放、烟囱阀门和捣炉门开关的全部功能,所有动作全部在配电柜台上按钮操作实现。
〔图6〕
5、电炉变压器采用有充分裕量的壳式变压器:
这种变压器体积轻,超负荷能力强,只是本钱比传统芯式变压器略高。
因为不少企业习惯超负荷10—30%长期运行,加大电流电压比,使电极深埋,外表上看炉况较好,电耗有所降低,产量有所增加。
但是超负荷运行使变压器和短网电阻损耗加大,降低了电效率,功率因数也同时降低。
因此选用变压器时一定要考虑30%的裕量,这对冶炼生产是很有利的!
6、短网
通常对短网的根本要:
①足够的有效截面积和载流能力;
②充分考虑交变电流肌肤效应和邻近效应的影响,提高板材导体的宽厚比或管材导体的外径和壁厚比;
③尽可能缩短导体长度、减小导体接触电阻;
④防止导体附近铁磁物质的涡流损失;
⑤适当的经济电流密度;
⑥足够小的感抗值;
⑦选用导电性好的T2铜;
⑧降低导体的运行温度。
根据上述8项原那么,我们设计时一般取电流密度为:
水冷铜管1.5—3A/mm2,水冷电缆1—1.5A/mm2,铜瓦与电极间的接触面0.01—0.025A/mm2。
我们一般选用外径为Φ70—80mmT2铜管制作短网。
〔1〕如果选用单台三相变压器,那么采用水冷电缆〔图7〕、水冷铜管短网。
既节约投资,比传统的铜排节约50%的铜材,超负荷能力又强。
倒三角采用我们首创设计的变压器八字形出线〔图8〕的短网布置,这样可以尽可能的缩短变压器到炉心的距离。
阻抗小,压降低。
〔2〕如果选用三台单相变压器,那么三相对称,变压器可以最大限度的靠近炉心。
出线端直接用水冷电缆与铜瓦铜管相连,省去短网。
按照已有的设计,水冷电缆长度根本不超过3米。
从理论上讲,三台单相变压器可以实现分项调压,防止强弱相,短网短而且长度一致。
但是从目前多家企业的运行状况和生产指标看,三台单相变压器的电炉和单台三相变压器相比,并无明显优势。
在德宏和等地,我们设计了上述两种形式的电炉和短网。
7、铜瓦
〔1〕采用钛铬合金铸造铜瓦,与锻造铜瓦比具有高温环境下变形小、强度高、本钱低的优点。
而有些锻造铜瓦存在受热后易翘曲变形导致打弧烧坏引起漏水等故障,不得不停炉更换。
经过测量使用前和使用后烧坏换下的锻造铜瓦,其变形量超过5mm。
这里面有设计原因,也有制造原因。
因此我们在比照后选择了铸造铜瓦。
通常只要保证了足够的接触压力,铸造铜瓦在生产期间很少甚至没有打弧,其变形量几乎为零。
〔2〕如果采用锻造铜瓦,那么构造上需要重新调整,铜瓦后面的受力点需要增加厚度和强度,尽可能减少受热受力后的变形。
目前的锻造铜瓦背后顶头受力处都是加工成凹形,与圆弧接触面之间的厚度只有50mm左右,然后做一道绝缘,实际上就降低了铜瓦的受力后抗变形能力。
如图5所示的铜瓦构造就不易产生变形。
8、半封闭中烟罩
从烟罩构造我们可以看出工业硅设备的开展状况。
最初设计的烟罩构造多为高烟罩。
很长一段时间,人们普遍认为高烟罩冶炼能耗低。
这种意识阻碍了中低烟罩的开展。
由于国家环保政策的强制实施,矮烟罩才得到进一步推广。
但是传统设计的中、低烟罩构造〔如图9所示〕,尽管许多设备隔离在高温区外,而除尘效果却很不理想,反而加剧了操作环境的恶化。
针对这种情况,我们对烟罩构造作了根本性的调整〔如图10〕。
采用我们独创设计的中烟罩+n型副烟罩形式〔也可叫盆式烟罩,即烟罩顶部中间低,周围高〕。
中烟罩顶部中心的骨架和中心盖板选用不导磁的不锈钢材料制作,周围采取隔磁的措施,有利于降低电磁损耗。
副烟罩顶部最高可到达4.5米,既吸取了高烟罩排烟能力强,料面温度低,也吸取了矮烟罩使主要设备远离高温区的优点。
通过、、等多家硅厂的使用,排烟效果相当显著,操作环境大大改善。
同时水冷捣炉门开关采用液压升降,按钮操作。
烟罩周围采用水冷墙板里面砌筑耐火砖或打耐火浇注料,降低周围操作环境的温度,减少热辐射。
目前这种构造的烟罩已被国很多企业认同并开场广泛推广。
如果能够在25000KVA的电炉上推广,结合改良25000KVA电炉烟罩的帘幕构造,那么可以很大程度上改善车间的高温操作环境。
9、水路设计
水路好比人体的血管,冷却水好比人体的血液。
从生产过程中设备的角度上讲,水比电还重要。
因此作为设计和制安人员必须要重视水路的设计和安装。
水的流速要大于0.8米/秒、压力大于0.25MPa,且水路在炉高温区的流动长度最多不超过30米,水路截面必须按照这几个参数计算设计,保证水流在水路的任意位置均为紊流,散热快,且不易沉沙积垢。
进出水的开孔位置尽量坚持低进高出的原那么,防止水冷件里的空气积存影响冷却效果。
在设计或安装时如果没有上述要求,很多电炉就会出现高压蒸汽断水的故障,同时结垢现象异常严重。
另外循环进水温度最好低于30℃,出水温度最好低于45℃。
如果达不到要求,需另外增加降温效果良好的玻璃钢冷却塔。
10、电极选用
在硅冶炼炉中,电极就是心脏,是导电系统的重要组成局部,也是工业硅生产中主要的消耗材料之一。
一般采用石墨电极或碳素电极。
设计时选用电流密度:
石墨电极8—14A/cm2,碳素电极5—6A/cm2。
电极质量的好坏,直接影响电炉的正常生产。
最好采用规模较大、质量可靠而且稳定、售后效劳好的厂家的品牌电极。
对电极的根本要求:
〔1〕导电性好、电阻率小〔石墨电极8—13μΩ.m,碳素电极25—40μΩ.m〕,电能损失少。
〔2〕热膨胀系数小,不易炸裂。
〔3〕灰分、杂质含量低,高温时有足够的机械抗压、抗折强度。
11、电炉参数的选择
电炉参数确实定非常重要,特别是极心圆、电极〔如果选用石墨电极那么电极直径为Φ960—1050mm为宜;
如果选用碳素电极那么电极直径为Φ1060—1100mm为宜〕和炉膛直径,炉膛深度,烟罩高度确实定〔具体的计算方法有很多前辈的资料已经表达得很清楚,这里不再赘述〕。
这些数据直接影响到生产效果和指标。
比方12500KVA硅炉,如果选用Φ960的石墨电极,通常设计时极心圆直径按照经历公式得出的极心圆直径是Φ2400左右。
但是在实际运行过程中,因为原材料构造的不同通常极心圆要调整到在Φ2500以上。
比方用大油焦生产,因为油焦的比电阻小,为了使电极深埋,12600KVA的电炉的极心圆直径应该在2500—2800之间。
如果是大木炭生产,那么极心圆通常在2400—2600之间就能到达比拟理想的指标。
因此选择参数,按公式计算还必须结合原材料、生产工艺和实际生产效果,有所变化和调整。
通常12500KVA工业硅电炉主要设计参数如下表:
序号
参数分类
实选数据
备
注
1
额定容量
12500
超负荷30%
2
电极直径
石墨电极Φ960—1020mm
碳电极Φ1060—1100mm
3
电极电密
石墨电极8—14A/cm2
碳素极5—6A/cm2
4
电极电流
48000—54000A
5
极心圆直径
Φ2500—2800mm
高焦工艺取上限;
木炭工艺取中下限。
6
炉膛直径
Φ6100—6300mm
7
炉膛深度
2500—2600mm
8
铜瓦数量
8块/相
9
烟囱直径
2×
Φ2200
12、捣炉机的设计
捣炉机〔包括25000KVA以上电炉配套使用的加料、拨料捣炉机〕是工业硅生产中重要的必不可少的冶炼辅助设备。
捣炉机的设计原那么:
①可靠的绝缘,特别是用于带电捣炉,绝缘的合理设计显得非常重要;
②较快的伸缩速度35—40m/min;
③整体强度。
捣炉机在工作时处于500—800℃高温环境,相比常温,捣炉杆的强度会大大降低;
如果我们能够设计出水冷构造的捣炉杆,那么捣炉机的使用寿命将大大延长;
④足够的行程〔2.8m以上〕,可以保证捣炉机的工作围,缩小捣炉盲区;
⑤足够的插入和捣炉力量。
力量缺乏,影响捣炉效果。
二、工业硅生产工艺管理
好的设计必须有好的管理,二者相辅相成,相得益彰。
工业硅生产从工艺上来讲,目前大致分为大木炭工艺、高焦低碳、高焦低煤工艺、半焦半煤工艺、全焦工艺。
随着木炭的限制,很多地企业开场采用高焦低煤或半焦半煤工艺。
1、设备管理
设备管理是生产管理的支柱,是节能降耗、稳产增产的根底。
因此如何减少设备热停炉时间,提高设备的作业率;
如何制定科学合理的设备管理制度,就显得尤为重要,也是我们要重点思考的问题。
〔1〕主体冶炼设备实行作业率,每个月只给一定的检修时间。
每节约一个小时给一定的奖励;
工资的上下与停电时间挂靠,检修时间越长,工资越低,反之越高。
〔2〕外围设备如捣炉机、台包车、行车实行维修本钱管理,控制浪费;
检修按照工时制度,检查工作能力和工作状况。
从目前的运行状况来看,这种制度最大限度的提高了检修的效率,促使机修把重点放在了如何预防故障上,也就是由原来的被动维修转变成主动维护。
〔3〕为防止刺火烧坏铜瓦和压力环造成漏水停炉检修,工艺上控制料面,要求料面与铜瓦下端保持100mm左右的距离。
如果发生漏水停电维修,那么事故责任分摊。
这样做的目的就是要提高员工的责任意识。
从某公司的12600KVA硅炉8—10月份的生产产量和设备的热停炉时间的比照可以看出:
在电力状况、冶炼操作和原材料不变的情况下,设备作业率越高,产量越高。
数据如下表:
2、原料管理
〔1〕硅石的控制
寻找优质硅石、控制硅石杂质含量是产品品质的根本保证。
因此对硅石化学成分要求如下:
SiO2>
98.5%,Fe2O3<
0.12%,Al2O3<
0.2%,CaO<
0.2%。
通常硅石中Fe2O3含量x1与产品中Fe含量y1有如下关系:
y1=1.866x1+0.212。
产品中铝的含量可通过提高原料标准并进展炉外精炼来控制,而精炼去铝只能到达75%左右。
通常硅石中Al2O3含量y2与最终产品中杂质铝含量x2有下面关系:
y2=0.847x2+0.095。
钙的含量如果和铝的含量接近,那么对冶炼和炉外精炼是有利的。
钙在冶炼或吹氧精炼过程中是放热反响,因此对提高产品质量,帮助降铝有非常好的作用。
精炼除钙效率可达98%。
但是硅石的高抗爆性和良好的复原性能对冶炼也会产生很大影响。
抗爆性差的硅石,参加炉后,因高温产生晶形转变,引起体积膨胀而爆裂成细小的颗粒,这些细小颗粒直接影响炉透气性,容易导致炉况恶化。
有条件的企业可以用1500℃的箱式电炉测试硅石的抗爆性。
也可以组织少量的硅石入炉试烧,根据炉况来判断其物理性能。
据资料介绍,复原性能和抗爆性好的硅石,电耗降低2—12%,原料消耗降低10%左右。
的昌宁矿就具有良好的物理和化学双重性能,所以冶炼指标非常优秀。
有些企业用几种不用性能的硅石按一定的比例混合搭配使用,同样也取得了较好的生产和质量指标。
硅石粒度要求:
60—100mm占75%,小于60的占10—15%,大于100—120的占10—15%。
硅石的粒度是冶炼的一个重要工艺要求。
硅石适宜粒度受硅石种类、操作状况以及复原剂的种类等多种因素影响。
要根据具体的冶炼条件来决定。
粒度过大,不能与反响速度相适应,易使未复原的硅石进入液体硅中,造成渣量增多〔如果不能及时排除容易积存造成炉底上涨〕,出炉困难,硅的回收率降低,能耗增大,严重时影响正常生产。
粒度过小,虽能增大复原剂的接触外表,有利于复原反响的进展,但反响过程中生成的气体不能顺利排出,又会减慢反响速度。
同时粒度过小,带入的杂质也会增多,影响产品质量。
生产中一般小于5mm的硅石不宜采用。
另外还要挑除杂石、冲水洗净,做到精料入炉。
〔2〕石油焦
石油焦中含有0.1—0.6%灰分,固定碳大于80—95%,挥发分大于3.5—13%。
因此可以提高金属硅的纯度,有利于提高产品质量。
但石油焦的缺点是比电阻低〔一般电阻率3—5Ω.m,经1200℃煅烧后电阻率仅400—500μΩ.m〕,高温下容易石墨化,而且反响活性差。
用量偏大时,导致炉况不好控制,造成炉料不烧结、刺火严重、电耗高、出炉困难。
入炉要求:
磁选去铁,粒度3—15mm占75%,3mm以下的占10—15%,15—20mm以上的占10%左右。
〔3〕洗精煤
上世纪90年代后期,国用精洗煤取代木炭作复原剂生产工业硅获得成功,到本世纪逐渐推广开来,目前我国完全用煤和石油复原剂的工业硅生产厂家占工业硅总厂家的一半以上。
现在我国复原剂烟煤的灰分含量多在3%以上,而国外复原剂烟煤的灰分的含量多在1%左右,采用的化学法精选烟煤,能得到氧化铁含量低于0.1%的精煤。
精煤是很好的复原剂,比电阻较石油焦大,化学活性好,反响能力比拟强。
很多企业根本在大量使用洗精煤,在复原剂中所占比例约10—45%。
质量要求:
挥发份>
25—40%,固定碳>
55%,灰分<
5%(灰分中的Fe2O3<
0.3%,Al2O3<
0.7%,CaO<
0.4%),粘结指数大于85。
磁选去铁,粒度2—15mm。
精煤的烧结性对炉况同样产生很大影响。
烧结性好的洗煤对焖烧是极为有利的。
〔4〕木炭和木片
木炭的比电阻高,化学活性好,是工业硅生产最理想的复原剂。
但是木炭资源是非常有限的〔目前使用木炭生产的企业主要分布在和〕。
因此,木片〔甘蔗渣、玉米芯、中药渣、秸秆、竹片、松果等〕已成为目前地企业进展工业硅生产的主要原料。
但是由于木块着火点、含碳量都低,实际作复原剂微乎其微,主要是增加炉料的透气性和料层的电阻。
木块用量的大小都对炉况产生影响。
木块用量过大,料层疏松没有烧结性,容易导致炉况变坏,电耗上升。
用木炭生产高品位的低铝、低磷、低硼的化学硅,一般木炭都需要精选过筛、水洗泥沙。
粒度20—100mm。
一般用木材切片机直接加工成100mm以下的片状后混合入炉。
如果要生产低硼低磷的产品,最好是木材去皮。
木材同样需要精选,不能参入泥土等杂质。
料比中一般参加10—30%。
3、冶炼操作管理
图中:
Ⅰ—预热区400—1000℃,Ⅱ—反响坩埚区3000—4000℃,Ⅲ—死料区1500—2200℃,Ⅳ—熔融硅液区2000—3000℃。
根据硅的复原冶炼原理:
SiO2+2C=Si+2CO
实际上工业硅高温冶炼反响过程是非常复杂的。
但我们一般简化分析,冶炼过程会产生三种情况:
一是炉料烧结成块状死料;
二是上层炉料中生成的片状SiC积存后容易促使炉底上涨;
其三Si和SiO高温挥发,容易降低硅的回收率。
为此,在冶炼中必须控制Si和SiO挥发,提高硅的回收率,保持SiC的形成与破坏相对平衡。
要到达此目的,必须加强操作细节管理,也就是下面的6个控制:
一控计量误差;
二控外偏加料;
三控频繁塌料生料入坩埚;
四控频繁捣炉;
五控反响区域;
六控敞弧过烧。
还有一句顺口溜:
“要想炉况好,别让弧光跑〞。
①
配料〔有些公司配料系统已采用电子监控计量统计〕。
正确的配料是保证炉况稳定的先决条件。
正确配比应根据炉料化学成分、粒度、含水量及炉况等因素确定,其中应该特别注意复原剂的使用比例和数量。
配比正确,料面松软又有一定的烧结性,透气性好,火焰均匀,能够保证相对稳定的焖烧时间。
炉料配比确定后,应进展准确称量,误差不超过0.5%,均匀混合后依次整批入炉。
炉料配比不准确会造成炉复原剂过多或缺少现象,影响电极下插,坩埚缩小,破坏正常的冶炼炉况。
配碳量与硅回收率——碳平衡的关系〔图14〕:
配碳量过剩50%,硅的回收率为0,生成的SiC积存炉底;
同理缺碳50%,SiO不能被吸收,影响SiC的生成与破坏,造成SiO2过剩。
正常情况下,碳和硅石的分子比为2。
高焦低煤的料比〔以硅石200kg为基准〕一般是:
油焦55—75kg、精洗煤30—55kg;
木片20—30kg。
②加料。
加料的根本原那么是均匀入炉。
沉料捣炉、推熟料操作完毕后,应将混匀炉料迅速集中加在电极周围及炉心三角区,使炉料在炉形成馒头形,并保持一定的料面高度和料层厚度。
一次参加混合均匀的新料数量相当于90分钟左右的用料量。
当炉心沉料不好时,一般是炉心料重或极心圆偏大,可对炉心加轻料;
但当炉心刺火或沉料太快时,一般是极心圆偏小,那么对炉心加偏重料。
新料加完后,开场焖烧,焖烧时间控制在80—100分钟左右。
焖烧和定期沉料的操作方法,有利于减少热损失,有利于提高炉温和扩大坩埚。
加料混合不均同样会造成炉复原剂过多或缺少现象,影响电极下插,缩小坩埚,使炉况变坏。
因原料中采用烧结性好的精洗煤和石油焦,料面容易结壳,难以自动下沉。
为减少反响区热量损失,扩大“坩埚〞,适时捣炉,有利于炉热量集中,为此必须采用一定时间的焖烧和定期集中加料的操作方法。
集中加料后,经一段时间焖烧,容易在料面形成一层硬壳,炉也容易出现块料;
同时炉温迅速上升,反响趋于剧烈,气体生成量急剧增加。
此时为了改善炉料的透气性,调节炉电流分布,扩大坩埚,要用捣炉机或钢棒松动锥体下脚和炉烧结严重部位的炉料,帮助炉气均匀外逸。
操作时间一般在加料后30分钟左右进展。
至于彻底的捣炉,那么要在沉料时进展。
③捣炉。
采用石油焦和洗煤炉料时,因其烧结性好难以下沉,一般需要强制沉料。
当炉炉料焖烧到规定时间时,料面料壳下的炉料根本熔化烧空,料面也开场发白发亮,火焰短而黄,局部地区出现刺火塌料。
此时应该立刻进展强制沉料操作。
沉料90分钟以上时,先用捣炉机从锥体外缘开场将料壳向下轻压,使料层下塌,而后用捣炉机捣松锥体下脚,捣松的热料就地推在下塌的料壳上,捣出的大块粘料推向坩埚区,死料排出,同时铲净电极上的粘料,沉料时预热区外露,热损失很大,因而沉料捣炉操作必须有效彻底快速进展。
④料面。
料面除了围绕电极堆成3个馒头形之外,根据一次电压的变化,料比轻重和料面上下的控制也非常重要。
电压高,料面适当高,料比适当偏重;
电压低,料面也相应低,料面也相应偏轻。
在不调整极心圆的情况下,这样做可以改善炉电流的合理分布和电极的深埋做功。
我们以某公司9000KVA工业硅炉2010年4月和10月的生产数据为例:
4月份的一次电压根本稳定在35—38KV,但是10月份的一次电压却极不稳定,在29—34KV围频繁波动。
但是通过加强料面管理和控制,仍然取得了比拟理想的电耗、产量指标,实际数据如下表:
⑤配电