怎样写硫回收学习心得Word格式文档下载.docx
《怎样写硫回收学习心得Word格式文档下载.docx》由会员分享,可在线阅读,更多相关《怎样写硫回收学习心得Word格式文档下载.docx(18页珍藏版)》请在冰豆网上搜索。
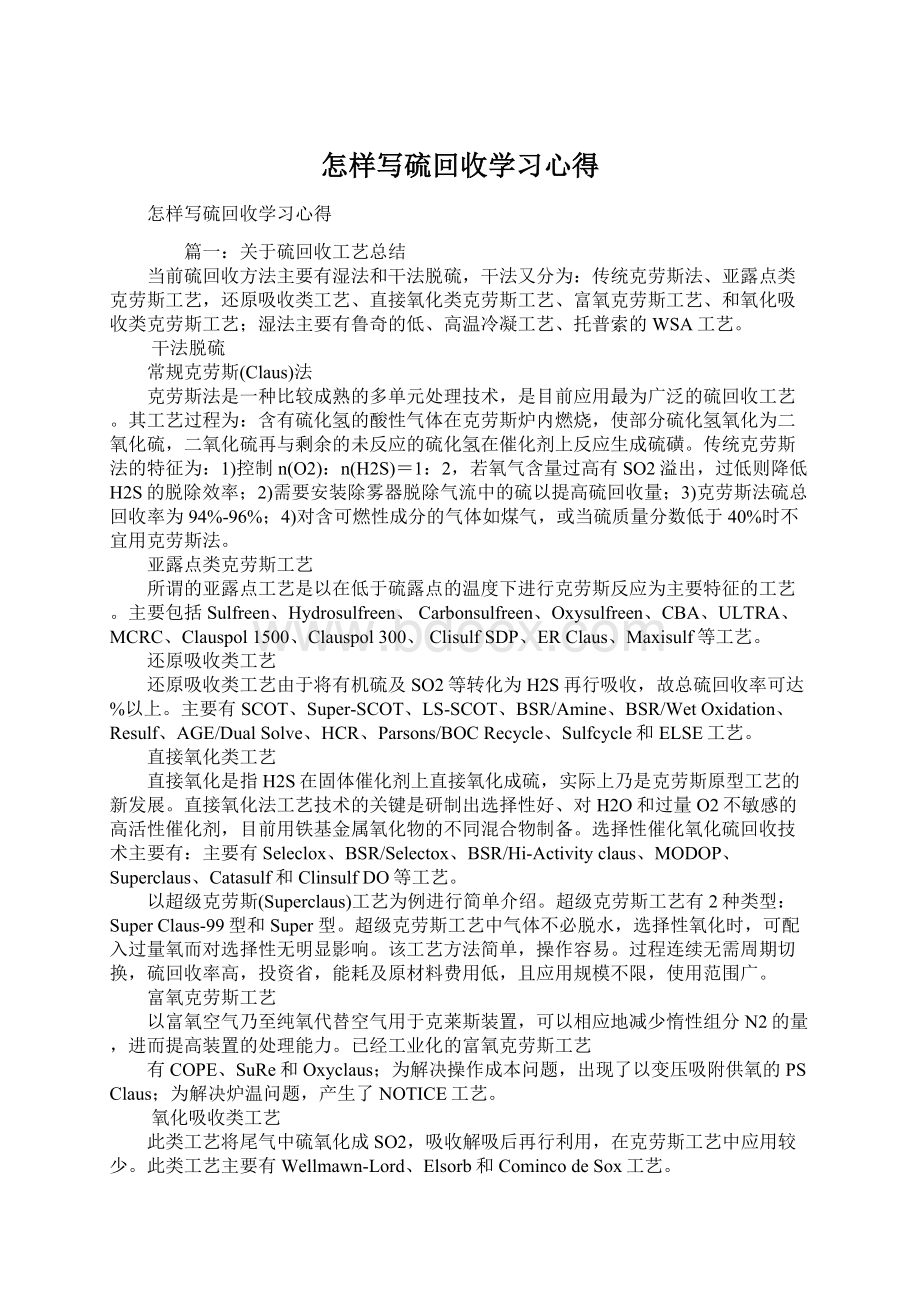
主要有Seleclox、BSR/Selectox、BSR/Hi-Activityclaus、MODOP、Superclaus、Catasulf和ClinsulfDO等工艺。
以超级克劳斯(Superclaus)工艺为例进行简单介绍。
超级克劳斯工艺有2种类型:
SuperClaus-99型和Super型。
超级克劳斯工艺中气体不必脱水,选择性氧化时,可配入过量氧而对选择性无明显影响。
该工艺方法简单,操作容易。
过程连续无需周期切换,硫回收率高,投资省,能耗及原材料费用低,且应用规模不限,使用范围广。
富氧克劳斯工艺
以富氧空气乃至纯氧代替空气用于克莱斯装置,可以相应地减少惰性组分N2的量,进而提高装置的处理能力。
已经工业化的富氧克劳斯工艺
有COPE、SuRe和Oxyclaus;
为解决操作成本问题,出现了以变压吸附供氧的PSClaus;
为解决炉温问题,产生了NOTICE工艺。
氧化吸收类工艺
此类工艺将尾气中硫氧化成SO2,吸收解吸后再行利用,在克劳斯工艺中应用较少。
此类工艺主要有Wellmawn-Lord、Elsorb和ComincodeSox工艺。
2
湿法脱硫
低温冷凝工艺
低温冷凝工艺是20世纪30年代德国鲁奇公司提出的一种湿接触法制酸工艺。
该工艺中,硫酸冷凝装置是喷淋填料塔,其后接除雾器。
该工艺过程是:
1)含硫化氢的洁净气体在焚烧炉内燃烧;
2)二氧化硫在转化器内催化转化;
3)出转化器的气体直接进入冷凝塔,与塔顶喷淋的循环冷硫酸逆流接触,冷凝成酸。
低温冷凝工艺中SO2转化率可达%,产品ω(H2SO4)为78%左右。
缺点是使用范围有限,不能处理燃烧后φ(SO2)低于3%的气体,仅适用于小规模装置。
康开特(Concat)法(高温冷凝工艺)
Concat工艺又称高温冷凝工艺,是继低温冷凝工艺后鲁奇公司又推出的改良的湿法接触催化生产硫酸工艺。
高温冷凝即三氧化硫气体与
水蒸气在高温下凝结成酸。
该工艺的冷凝装置选用文丘里冷凝器。
该工艺过程为:
1)湿的H2S气体与燃料气配合,在焚烧炉内进行燃烧;
2)SO2在转化器内进行氧化;
3)气体进入冷凝文丘里管,与高度分散的热硫酸并流接触,生成硫酸,沉析放热。
最后进行气体的冷却和硫酸雾滴的分离。
该工艺特别适用于处理温度高、H2S,CS2和CO2含量低的气体,可处理燃烧气中φ(SO2) 湿气制酸(WSA)法
湿气体制酸法是由丹麦托普索公司开发的一种含硫湿气直接制酸工艺。
该工艺的冷凝装置为降膜冷凝器。
1)原料气燃烧生成SO2;
2)转化成SO2后的含湿气体经冷却进入SO2转化器生成SO3;
3)SO3和携带的水蒸气进入冷凝器直接冷凝成酸。
该工艺的特点是:
1)硫回收率高,可达99%,产品单一,唯一的产品为达到商品级标准的浓硫酸;
2)该工艺除消耗催化剂外不需要任何化工药品或添加剂;
3)不产生废料,对环境没有二次污染;
4)除启动时需启动燃料和热载体熔盐熔融时需要外加热源外,一旦运转起来便产生大量热能,副产的高压蒸汽除供生产使用外,还可供其他方面使用;
5)适用范围广,可处理各种含硫气体
篇二:
硫回收流程说明
硫回收工艺流程叙述及简要说明
一、酸性水汽提部分
(一)流程简述
自装置外来的混合酸性水,进入原料水脱气罐(V23401)进行脱气,脱出的轻油气送至火炬管。
脱气后的酸性水先后进入原料水罐(23403)沉降脱油,再经原料水加压泵(P23401)加压后进入原料水除油器(V23408AB)进一步脱油,脱出的轻污油间断自流至污油罐(V23402),经污油泵(P23402)间断送至工厂污油罐区。
除油后的酸性水进入原料水缓冲罐(V23404),经原料水进料泵(P23403AB)加压,一部分原料水经冷进料冷却器(E23401)冷却后作为汽提塔的冷进料,其余原料水经原料水-净化水一级换热器(E23402),一级冷凝冷却器(E23403),原料水-净化水二级换热器(E23404A-F)后作为汽提塔(T23401)的热进料进入汽提塔。
塔底用汽提重沸器(E23405)间接加热汽提,以保证塔底温度160℃。
汽提塔底净化水与原料水换热后,送至装置外。
汽提塔顶酸性气送至硫磺回收部分。
侧线提出的粗氨气经过一级冷凝冷却器(E23403)冷却,一级分凝器(V23405)分离冷凝液,二级冷凝冷却器(E23407)冷却,二级分凝器(V23406)分离冷凝液,三级冷凝冷却器(E23408)冷却,三级分凝器(V23407)分离冷凝液后配制成氨水或送往硫磺回收装置尾气焚烧炉烧掉。
二、硫磺回收部分
(一)流程简述
自酸性水汽提来的汽提酸性水经酸性水分液罐(V23502)分液,自溶剂再生来的再生酸性气经酸性气分液罐(V23501)分液后,经酸性气预热器(E23503)加热到160℃。
两股酸性气混合进入硫磺回收酸性气燃烧炉(F23501)燃烧。
两股酸性气分液罐分出的酸性液经酸性液压送罐(V23503)由氮气间断送至酸性水汽提部分进行处理。
由燃烧炉鼓风机(C23501AB)来的空气经空气预热器(E23502)用蒸汽预热至160℃后,进入酸性气燃烧炉。
酸性气燃烧配风量按烃类完全燃烧和1/3硫化氢生成二氧化硫来控制80%的风量和按CLAUS尾气中H2S/SO2=2控制20%的风量。
燃烧产生的高温过程气进入余热锅炉(E23501)冷却至350℃并发生MPa蒸汽,液硫从余热锅炉底部经液液硫封罐(V23505A)进入硫池(V23506),过程气进入一级冷凝器(E23504A),在一级冷凝冷却器冷却至170℃并经除雾后,液硫从一级冷凝冷却器底部经液液硫封罐(V23505B)进入硫池(V23506)。
除雾后的过程气经一级掺合阀与F23501炉内高温气流掺混至240℃进入一级反应器(R23501),在CLAUS催化剂作用下,硫化氢与二氧化硫发生反应,生成硫磺。
温度为287℃的反应过程气经二级冷凝冷却器(E23504B)冷却至160℃并经除雾后,液硫从二级冷凝冷却器底部经液液硫封罐(V23505C)进入硫池。
过程气经二级掺合阀与F23501炉内高温气流掺混至220℃后进入二级反应器(R23502),在CLAUS催化剂作用下,硫化气和二氧化硫继续发生反应,生成硫磺。
℃的过程气经三级冷凝冷却器(E23505)冷却至130℃并经除雾后,液硫从三级冷凝冷却器底部经液液硫封罐(V23505D)进入硫池。
尾气再经捕集器(V23504)进一步捕集硫雾后,进入尾气处理系统。
在捕集器(V23504)出口尾气管线上设置尾气在线分析仪,分析尾气中H2S/SO2的值,反馈调节进酸性气燃烧炉20%的空气量,以保证过程气中H2S/SO2为2:
1,使CLAUS反应转化率达到最高,同时提高硫回收率,减少硫损失。
在硫池中利用液硫脱气泵(P23503AB)进行液硫循环脱气,释放出的少量H2S用蒸汽喷射器(EJ23501AB)抽送到尾气焚烧炉(F23502)。
产品液硫用液硫泵(P23502AB)从硫池抽出,装车送出装置。
经捕集硫雾后的CLAUS尾气在气气换热器(E23508)中与尾气焚烧后的烟气进行换热升温,CLAUS尾气被加热至300℃与PSA制氢装置提纯后的氢气混合后进入加氢反应器(R23503)。
CLAUS尾气在加氢催化剂的作用下,SO2、COS、CS2及液硫、气态硫等均被转化H2S,加氢反应为放热反应,离开反应器温度为℃的过程气直接进入急冷塔(T23501)。
尾气在急冷塔内利用循环急冷水来降温。
70℃的急冷水自急冷塔底流出,经急冷水泵(P23504)加压后,再经急冷水冷却器(E23506AB)冷却至40℃循环到急冷塔顶。
部分急冷水经急冷水过滤器(FI23501)过滤。
因尾气冷却后其中的水蒸汽被急冷水冷凝,产生的酸性水由急冷水泵送至酸性水汽提部分处理。
急冷水管线设置PH值在线分析仪,分析PH值的大小。
急冷后的尾气离开急冷塔顶进入尾气吸收塔(T23502),用浓度为25%的N-甲基二乙醇胺溶液吸收尾气中的硫化氢,同时吸收部分二氧化碳。
从塔顶出来的净化尾气进入尾气焚烧炉(F23502)焚烧,由燃料气流量控制炉膛温度;
尾气中残留的硫化氢和其它硫化物完全转化为二氧化硫。
焚烧后的烟气用余热锅炉取热降温,温度降到430℃,进气气换热器(E23508)与CLAUS尾气换热至300℃后经烟囱(S23501)排空。
硫磺回收在事故状态时,酸性气送装置外酸性气火炬焚烧;
当尾气处理部分处于事故状态时,CLAUS尾气可通过跨线直接进入尾气焚烧炉焚烧后通过烟囱排空。
酸性气余热锅炉和尾气余热锅炉发生的MPa蒸汽除一部分用于酸性气预热和空气预热外,其余部分减压至蒸汽(150℃)管。
一、二级冷凝冷却器产生蒸汽供装置内保温、伴热用。
三级冷凝冷却器产生的乏汽经三级蒸汽空冷器(E23509)冷却,冷凝水循环返回三级冷凝冷却器。
装置保温伴热的凝结水、汽提塔重沸器产生的凝结水及溶剂再生装置的凝结水进入凝结水回收罐(V23507),闪蒸乏汽后进入空冷循环冷却。
凝结水经凝结水泵(P23501AB)升压后作为锅炉给水送至余热锅炉、一二级冷凝冷却器,剩余部分送出装置。
催化干气经过脱硫后进入PSA氢提纯系统,干气中烃类被吸附剂吸附,吸附剩余氢气进入MI23501与CLAUS尾气混合后进入加氢反应器(R23503),脱附后干气作为燃料供F23502使用。
三、溶剂再生部分
来自催化产品精制的富胺与来自硫磺尾气吸收的富溶剂混合后,通过富胺过滤器过滤,经一级贫富液换热器(E26301)与贫液换热至95~98℃进入闪蒸罐(V23601)闪蒸出溶解烃,然后进入再生塔(T23601)。
再生塔底由重沸器(E23604)供热,用蒸汽间接加热。
塔顶气体经酸性气空气冷却器(E23606)、酸性气后冷器(E23603)冷凝冷却后,进入再生塔顶分液罐(V23605)分液。
酸性气返回到硫磺回收部分酸性气燃烧炉(F23501),冷凝液经回流泵(P23603AB)返塔作为回流。
塔底贫液经贫富液换热器(E26301)换热和贫液冷却器(E23602)冷却至40℃后进入溶液剂储存罐(V23602),用脱硫贫液泵(P23602AB)将贫液从溶剂储存罐中抽出送至催化精制部分,用硫磺尾气贫液泵(P23601AB)将贫液从溶剂储存罐中抽出送至尾气吸收塔。
为了减少溶剂损失,本装置采取了以下措施:
再生塔底重沸器(E23604)热源用(150℃)蒸汽,以防重沸器管束壁温过高,造成溶剂的热降解,塔底温度控制123℃。
由于醇胺溶剂与氧作用会生成有机物及其它不能再生的物质,溶剂配制和溶剂系统补水均采用凝结水,溶剂缓冲罐设有氮气保护系统,避免因溶剂氧化变质引起发泡和腐蚀。
富溶剂进装置设置富胺过滤器(FI23601),混合富液进行全量过滤,除去富胺液中因腐蚀等原因产生的杂质。
尾气贫液泵(P23601AB)出口设置溶剂贫液过滤器(FI23602)过滤10%~15%的贫溶剂,以除去溶液剂中的降解物质,避免溶剂发泡。
篇三:
硫回收技术
硫回收技术
一、酸性气的来源及性质
本装置原料为来自上游酸性气脱除及酸性水汽提装置的酸性气,酸性气组成如下:
1.原料规格及供应
2.辅助材料规格及供应
催化剂暂按下列考虑:
二、硫的物理化学性质及应用
本装置主要产品为工业硫磺。
硫磺是一种浅黄色晶体,分子式S,分子量,不溶于水,易溶于二硫化碳,溶点112℃,沸点444℃,自燃点248℃~260℃,在空气中液体硫接触明火即可燃烧,密度/cm3~/cm3。
硫磺在加热冷却时发生如下现象:
℃250℃300℃
黄色固体———→黄色流动液体———→暗棕色粘稠液体———→暗棕色易流动液体——℃650℃900℃
—→橙黄色气体———→草黄色气体———→无色气体
液体硫磺具有独特的粘温特性。
粘度下降,流动性好;
160℃~190℃由于S8
环链开始破裂,成为链状的S8分子,粘度升高,流动性变差;
190℃以上链平均长度缩短,粘度又变小;
250℃以上时,长链的硫分子断裂,粘度急剧减小。
硫分子中的硫原子数目,随温度不同而有所不同,主要存在有S2、S6、S8三种分子状态。
当加热硫磺时存在如下平衡:
3S8—→4S6—→12S2
随温度升高,平衡往右移动。
熔点以下硫分子为S8,温度在熔点与沸点之间时,S6、S8共存。
随温度升高S8逐渐减少而S6逐渐增多。
沸点时S2开始出现,700℃时S8为零,700℃时S2最多而S6为零。
固体硫有α(正交)、β及γ(单斜)三种同素异形体,此外还有聚合型(无定形)的。
α、β及γ硫是环状的S8分子,聚合型硫是环状和链状分子聚合而成的,S8分子的结构如同图1所示:
S8分子结构
三、硫磺回收工艺原理及流程
1.装置简要说明
本装置采用克劳斯制硫法回收硫磺,然后进行尾气灼烧,达到化害为利,消除污染,保护环境的目的。
装置尾气采用120m烟囱高空排放。
2.定义本标准采用下列定义
酸性气:
指含H2S、CO2等气体。
这些气体的湿气体呈酸性。
过程气:
指酸性气燃烧后产生的气体,以示与尾气相区别。
尾气:
指排出制硫装置的气体。
克劳斯反应:
H2S与SO2生成硫的反应。
其特点:
参与反应的H2S与SO2摩尔比为2:
1。
气风比:
风量与酸性气量之比,即:
实际配风量(Nm3/h)
气风比=———————————
酸性气量(Nm3/h)
3.工艺原理
英国的化学家claus发明,现在使用的都是改良克劳斯法。
空气与酸性气体在炉内燃烧,反应十分复杂,其中主要反应及主要副反应如下:
酸性气燃烧炉内的反应:
主要反应:
H2S+3/2O2→SO2+H2O
(1)H2S+1/2O2→H2O+1/2S2
(2)副反应:
H2S+CO2→COS+H2O(7)H2S+1/2CO2→1/2CS2+H2O(8)(15)
上述反应大多数为放热反应,因此,燃烧炉内的温度较高,一般在1000℃以上,有的高达1350℃。
催化转化器中重要的副反应是CS2和COS的水解反应,该反应随温度的升高而增加。
因此,第一反应器温度控制较高,主要是考虑到CS2和COS的水解反应。
第二或第三反应器温度控制较低,主要是为了更有利于反应的进行,从而提高转化率。
反应器内的反应:
2H2S+SO2→3/XSx+2H2O2H2S+O2→2/XSx+2H2O
CS2+H2O→COS+H2SCOS+H2O→CO2+H2S
另外,在废热锅炉中,由于温度发生了较大的变化,硫在其中还存在以下反应:
S2→1/3S6S2→1/4S8
以上两反应均为放热反应。
尾气焚烧炉主要是将H2S、硫等转化为SO2降低对大气的污染。
其中的主要反应为:
H2S+3/2O2→SO2+H2OS+O2→SO2
尾气加氢还原反应原理:
尾气回收部分以还原吸收法为例,克劳斯尾气混合掺入氢以后,被加热到295℃,在钴、钼(CT6-5B)催化剂的作用下,尾气中携带的单质硫、SO2进行加氢反应,COS、CS2进行水解反应。
反应式如下:
SO2+3H2→H2S+2H2OS8+8H2→8H2SCOS+H2O→H2S+CO2CS2+2H2O→2H2S+CO2
经加氢反应后所有的硫都被转化成H2S,然后经过MDEA(N-甲基二乙醇胺)溶剂吸收后送到再生塔部分进行再生,解吸出的H2S返回燃烧炉前重新参加反应。
反应器温度一般控制在该气体中硫的露点温度30℃以上。
4.碎煤酸性气提浓降烃工艺原理
采用MEA(单乙醇胺)或MDEA(二乙醇胺)方法。
MEA(单乙醇胺)具有一个羟基(-OH)和一个氨基(-NH2),羟基能降低化合物的蒸汽压,增大在水中的溶解度,而氨基在水溶液中提供所需的碱度,以促使对酸性气体(H2S、CO2)的化学吸收。
MDEA是胺类中的一种叔胺,它与MEA(单乙醇胺)一样,是一种弱碱,其碱性比MEA(单乙醇胺)弱。
MDEA与H2S、CO2的反应原理如下:
对硫化氢:
篇四:
硫回收操作
三、硫回收(710工号)操作规程
1岗位简述岗位任务
本工序采用荷兰JACOBS公司超优组合克劳斯硫回收工艺,处理来自低温甲醇洗工序含H2S的酸性气体,使经过硫回收装置处理的尾气中H2S、SO2等排放物指标达到国家强制性排放标准,同时生产纯度为%(wt)的固体硫磺产品。
管辖范围
硫回收工序管辖范围包括:
1.反应器:
R1901,R1902,R1903,R1904共4台;
2.塔:
T1901共1台;
3.换热器:
E1901,E1902,E1903,E1904,E1905,E1906,E1907,E1908,E1909,E1910,E1911共11台;
4.罐及分离器:
V1901,V1902,V1903,V1904共4台;
5.机泵:
P1901A/B,P1902A/B共4台;
6.鼓风机:
C1901A/B共2台;
7.其它:
Z1901,Z1902,F1901,F1902,A1901,Y1901A/B/C/D/E/F,Y1902,PIT1901,X1901共14台;
上述设备的附属管线,阀门及就地指示仪表等。
岗位操作原理及流程简述岗位操作原理
工艺过程包括:
传统的克劳斯反应,SO2催化还原为H2S和硫蒸气的超优克劳斯反应,H2S被选择性氧化为硫单质的超级克劳斯反应。
酸性进料气首先通过甲醇洗涤塔预处理,除去酸气中的大部分甲醇。
硫回收装置包括一个高温燃烧反应段,通过纯氧将酸气中H2S部分燃烧,随后是两个克劳斯催化反应段,一个超优克劳斯(EUROCLAUS)催化反应段和一个超级克劳斯(SUPERCLAUS)催化反应段。
从超级克劳斯(SUPERCLAUS)催化反应段出来的尾气送入焚烧炉进行燃烧。
热反应段
超优克劳斯硫回收工艺,是通过一个比例控制控制燃烧氧气的流量,从而使H2S进行部分燃烧。
通过自动控制氧气流量来保证进料酸气中的所有烃类和氨都能完全燃烧,同时控制超优反应器出口的H2S组成为%(v)。
传统的克劳斯工艺是通过控制“氧气(空气)和酸性气”的比例来保证催化反应段出来的气体中H2S和SO2的比例正好是2/1。
然而,超优克劳斯工艺没有采用这种传统的控制理念,而是通过调节“氧气和酸性气”的配比来控制超级克劳斯反应器入口气体中的H2S浓度。
因此,前面的高温燃烧反应段是在偏离“克劳斯比例”下
操作的,即H2S和SO2的比值高于2/1。
也就是说,在前面的高温燃烧反应段的操作是控制H2S浓度,而不是像传统的控制“H2S/SO2”的比例。
采用一台气体分析仪来测量超优克劳斯反应器出口气中的H2S浓度,并通过分析控制器调整进入主燃室的氧气流量以获得期望的H2S浓度。
总的来说,控制理论可做如下概述:
(1)如果进入超级克劳斯段的H2S浓度过高,可增加主燃室中的氧气量。
(2)如果进入超级克劳斯段的H2S浓度过低,可减少主燃室中的氧气量。
主烧嘴和主燃室主要反应如下:
2H2S+3/2O2SO2+2H2O+Q
根据如下的平衡反应,残余气体中大部分的H2S和SO2反应生成单质硫。
2H2S+SO23/2S2+2H2O-Q
通过这个著名的克劳斯反应,在主烧嘴和主燃室中生成气态的单质硫。
克劳斯催化反应段
接下来的克劳斯催化反应段,可以进一步提高硫的回收率。
在第一和第二反应器中主要发生以下化学反应:
2H2S+SO23/xSx+2H2O+Q
通过使用克劳斯催化剂使这个平衡反应向生成硫的方向进行。
通过冷凝分离第一和第二反应器中生成的硫可以提高后面催化反应中的硫转化率。
超优克劳斯段(EUROCLAUS)
由于克劳斯反应是一个平衡反应,不能完全移向生硫侧,因此在第一和第二反应器中出来的气体中仍含有SO2。
由于SO2在最后的超克(SUPERCLAUS)反应器中不参与反应,这会使硫回收率降低。
为了减少SO2带来的这部分损失,在第二反应器后面引入了一个超优反应器,在超优反应器中装填了一种特殊的催化剂,将工艺气中的SO2还原生成单质硫和H2S。
从第二反应器来的工艺气体中含有一定的H2和CO,它们将与SO2在超优反应器的催化床层中发生如下反应:
SO2+2H21/xSx+2H2OSO2+3H2H2S+2H2OSO2+2CO1/xSx+2CO2
超级克劳斯段(SUPERCLAUS)
从超优反应器出来的工艺气与空气进行混和,进入超克反应器中,在超克反应器中通过装填一种特殊催化剂将H2S进行选择性地氧化直接生成单质硫,主要反应如下:
H2S+1/2O21/xSx+H2O
此反应为热力学完全反应,因此反应可以达到很高的转化率。
焚烧炉
从超克反应器来的尾气,以及从液硫池来的排放气中含有一定的硫化物,这些硫化物需要在焚烧炉中进行燃烧反应。
主要反应如下:
H2S+3/2O2SO2+H2O1/xSx+O2SO2COS+3/2O2SO2+CO2
工艺流程简述