快速成型技术Word文档格式.docx
《快速成型技术Word文档格式.docx》由会员分享,可在线阅读,更多相关《快速成型技术Word文档格式.docx(11页珍藏版)》请在冰豆网上搜索。
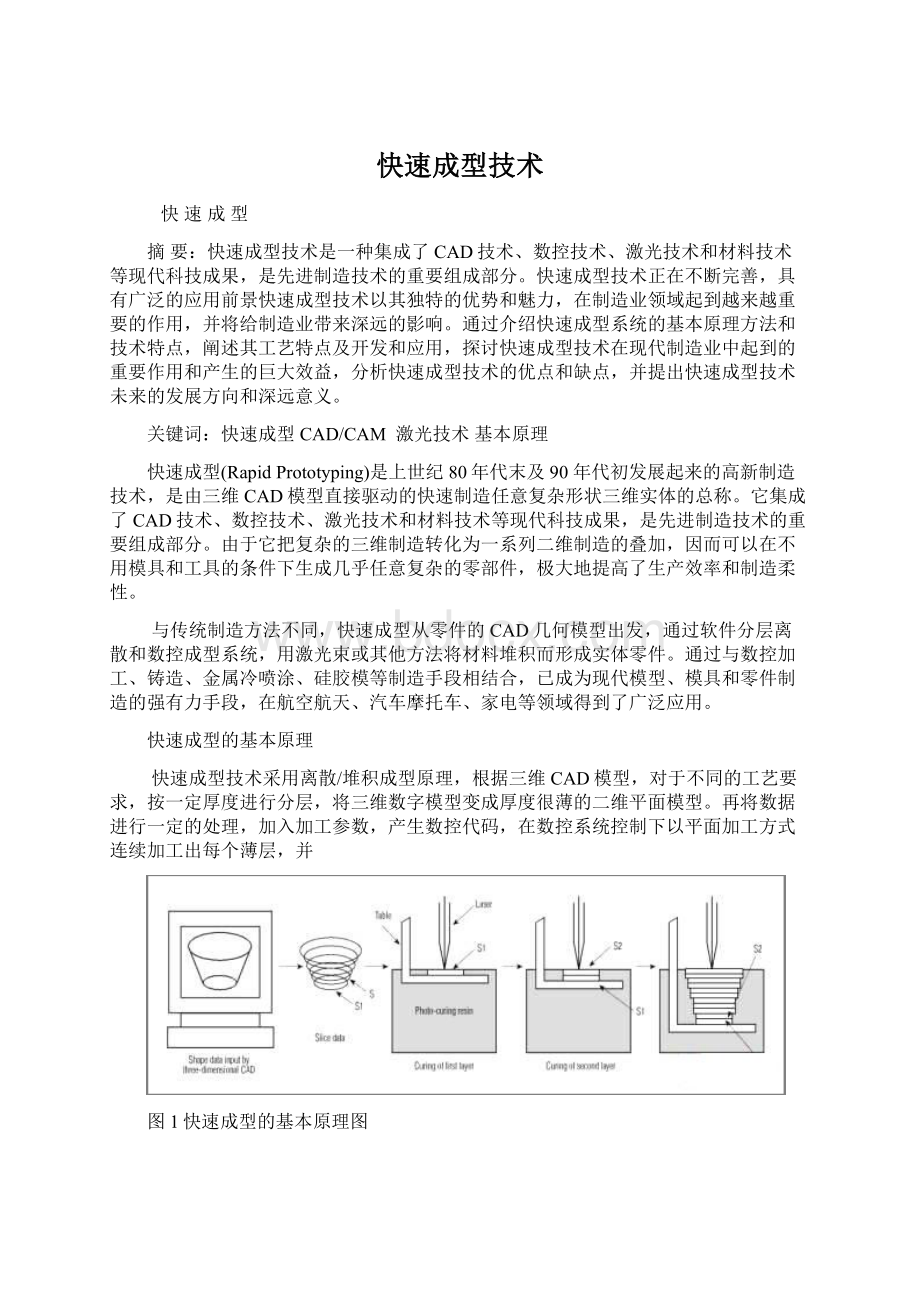
设计制造一体化一直来说是现在的一个难点,计算机辅助工艺(CAPP)在现阶段由于还无法与CAD、CAM完全的无缝对接,这也是制约制造业信息化一直以来的难点之一,而快速成型技术集成CAD、CAM、激光技术、数控技术、化工、材料工程等多项技术,使得设计制造一体化的概念完美实现。
完全再现三维数据
经过快速成型制造完成的零部件,完全真实的再现三维造型,无论外表面的异形曲面还是内腔的异形孔,都可以真实准确的完成造型,基本上不再需要再借助外部设备进行修复。
成型材料种类繁多
到目前为止,各类RP设备上所使用的材料种类有很多,树脂、尼龙、塑料、石蜡、纸以及金属或陶瓷的粉末,基本上满足了绝大多数产品对材料的机械性能需求。
创造显著的经济效益
与传统机械加工方式比较,开发成本上节约10倍以上,同样,快速成型技术缩短了企业的产品开发周期,使的在新品开发过程中出现反复修改设计方案的问题大大减少,也基本上消除了修改模具的问题,创造的经济效益是显而易见的。
应用行业领域广
RP技术经过这些年的发展,技术上已基本上形成了一套体系,同样,可应用的行业也逐渐扩大,从产品设计到模具设计与制造,材料工程、医学研究、文化艺术、建筑工程等等都逐渐的使用RP技术,使得RP技术有着广阔的前景.
快速成型的工艺过程
(1)三维模型的构造:
按图纸或设计意图在三维CAD设计软件中设计出该零件的CAD实体文件。
一般快速成型支持的文件输出格式为STL模型,即对实体曲面做近似的所谓面型化处理,是用平面三角形面片近似模型表面。
以简化CAD模型的数据格式。
便于后续的分层处理。
由于它在数据处理上较简单,而且与CAD系统无关,所以很快发展为快速成型制造领域中CAD系统与快速成型机之间数据交换的标准,每个三角面片用四个数据项表示。
即三个顶点坐标和一个法向矢量,整个CAD模型就是这样一个矢量的集合。
在一般的软件系统中可以通过调整输出精度控制参数,减小曲面近似处理误差。
如Pre/1E软件是通过选定弦高值(ch-chordheight)作为逼近的精度参数。
(2)三维模型的离散处理(切片处理):
在选定了制作(堆积)方向后,通过专用的分层程序将三维实体模型(一般为STL模型)进行一维离散,即沿制作方向分层切片处理,获取每一薄层片截面轮廓及实体信息。
分层的厚度就是成型时堆积的单层厚度。
由于分层破坏了切片方向CAD模型表面的连续性,不可避免地丢失了模型的一些信息,导致零件尺寸及形状误差的产生。
所以分层后需要对数据作进一步的处理,以免断层的出现。
切片层的厚度直接影响零件的表面粗糙度和整个零件的型面精度,每一层面的轮廓信息都是由一系列交点顺序连成的折线段构成。
所以,分层后所得到的模型轮廓已经是近似的,层与层之间的轮廓信息已经丢失,层厚越大丢失的信息越多,导致在成型过程中产生了型面误差。
(3)成型制作:
把分层处理后的数据信息传至设备控制机,选用具体的成型工艺,在计算机的控制下,逐层加工,然后反复叠加,最终形成三维产品。
(4)后处理:
根据具体的工艺,采用适当的后处理方法,改善样品性能。
快速成型工艺方法简介
目前快速成型主要工艺方法及其分类见图2所示。
仅介绍目前较为常用的工艺方法。
图2
光固化法(SLA,StereolithographyApparatus)
光固化法(SLA)是目前最为成熟和广泛应用的一种快速成型制造工艺(如图3)。
这种工艺以液态光敏树脂为原材料,在计算机控制下的紫外激光按预定零件各分层截面的轮廓轨迹对液态树脂逐点扫描,使被扫描区的树脂薄层产生光聚合(固化)反应,从而形成零件的一个薄层截面。
完成一个扫描区域的液态光敏树脂固化层后,工作台下降一个层厚,使固化好的树脂表面再敷上一层新的液态树脂然后重复扫描、固化,新固化的一层牢固地粘接在一层。
此反复直至完成整个零件的固化成型如图3。
图3光固化法原理图
SLA工艺的优点是精度较高,一般尺寸精度可控制在0.01mm;
表面质量好;
原材料利用率接近100%;
能制造形状特别复杂、精细的零件;
设备市场占有率很高。
缺点是需要设计支撑;
可以选择的材料种类有限;
制件容易发生翘曲变形;
材料价格较昂贵。
该工艺适合比较复杂的中小型零件的制作。
选择性激光烧结法(SLS,SelectiveLaserSintering)
图4选择性激光烧结法原理图
选择性激光烧结法(SLS)是在工作台上均匀铺上一层很薄(100μ-200μ)的作金属(或金属)粉末,激光束在计算机控制下按照零件分层截面轮廓逐点地进行扫描、烧结,使粉末固化成截面形状(如图3)。
完成一个层面后工作台下降一个层厚,滚动铺粉机构在已烧结的表面再铺上一层粉末进行下一层烧结。
未烧结的粉末保留在原位置起支撑作用,这个过程重复进行直至完成整个零件的扫描、烧结,去掉多余的粉末,再进行打磨、烘干等处理后便获得需要的零件。
用金属粉或陶瓷粉进行直接烧结的工艺正在实验研究阶段,它可以直接制造工程材料的零件如图4。
SLS工艺的优点是原型件机械性能好,强度高;
无须设计和构建支撑;
可选材料种类多且利用率高(100%)。
缺点是制件表面粗糙,疏松多孔,需要进行后处理;
制造成本高。
采用各种不同成分的金属粉末进行烧结,经渗铜等后处理特别适合制作功能测试零件;
也可直接制造金属型腔的模具。
采用蜡粉直接烧结适合于小批量比较复杂的中小型零件的熔模铸造生产。
熔融沉积成型法(FDM,FusedDepositionModeling)
这种工艺是通过将丝状材料如热塑性塑料、蜡或金属的熔丝从加热的喷嘴挤出,按照零件每一层的预定轨迹,以固定的速率进行熔体沉积(如图4-5)。
每完成一层,工作台下降一个层厚进行迭加沉积新的一层,如此反复最终实现零件的沉积成型。
FDM工艺的关键是保持半流动成型材料的温度刚好在熔点之上(比熔点高1℃左右)。
其每一层片的厚度由挤出丝的的直径决定,通常是0.25~0.50mm。
图5熔融沉积成型法原理图
FDM的优点是材料利用率高;
材料成本低;
可选材料种类多;
工艺简洁。
缺点是精度低;
复杂构件不易制造,悬臂件需加支撑;
表面质量差。
该工艺适合于产品的概念建模及形状和功能测试,中等复杂程度的中小原型,不适合制造大型零件。
分层实体制造法(LOM,LaminatedObjectManufacture)
图6分层实体制造法原理图
LOM工艺是将单面涂有热溶胶的纸片通过加热辊加热粘接在一起,位于上方的激光切割器按照CAD分层模型所获数据,用激光束将纸切割成所制零件的内外轮廓,然后新的一层纸再叠加在上面,通过热压装置和下面已切割层粘合在一起,激光束再次切割,如此反复逐层切割、粘合、切割……直至整个模型制作完成如图6。
LOM工艺优点是无需设计和构建支撑;
只需切割轮廓,无需填充扫描;
制件的内应力和翘曲变形小;
制造成本低。
缺点是材料利用率低,种类有限;
表面质量差;
内部废料不易去除,后处理难度大。
该工艺适合于制作大中型、形状简单的实体类原型件,特别适用于直接制作砂型铸造模。
图7三维印刷法原理图
三维印刷法(3DP,ThreeDimensionalPrinting)
三维印刷法是利用喷墨打印头逐点喷射粘合剂来粘结粉末材料的方法制造原型。
3DP的成型过程与SLS相似,只是将SLS中的激光变成喷墨打印机喷射结合剂如图7。
该技术制造致密的陶瓷部件具有较大的难度,但在制造多孔的陶瓷部件(如金属陶瓷复合材多孔坯体或陶瓷模具等)方面具有较大的优越性。
典型快速成型工艺比较
光固化成型
SLA
分层实体制造
LOM
选择性激光烧结
SLS
熔融沉积成型
FDM
三维打印技术
3DP
优点
(1)成型速度快,自动化程度高,尺寸精度高;
(2)可成形任意复杂形状;
(3)材料的利用率接近100%;
(4)成型件强度高。
(1)无需后固化处理;
(2)无需支撑结构;
(3)原材料价格便宜,成本低。
(1)制造工艺简单,柔性度高;
(2)材料选择范围广;
(3)材料价格便宜,成本低;
(4)材料利用率高,成型速度快。
(1)成型材料种类多,成型件强度高;
(2)精度高,表面质量好,易于装配;
(3)无公害,可在办公室环境下进行。
(1)成型速度快;
(2)成型设备便宜。
缺点
(1)需要支撑结构;
(2)成型过程发生物理和化学变化,容易翘曲变形;
(3)原材料有污染;
(4)需要固化处理,且不便进行。
(1)不适宜做薄壁原型;
(2)表面比较粗糙,成型后需要打磨;
(3)易吸湿膨胀;
(4)工件强度差,缺少弹性;
(5)材料浪费大,清理废料比较困难。
(1)成型件的强度和精度较差;
(2)能量消耗高;
(3)后处理工艺复杂,样件的变形较大。
(1)成型时间较长;
(2)需要支撑;
(3)沿成型轴垂直方向的强度比较弱。
(1)一般需要后序固化;
(2)精度相对较低。
应用领域
复杂、高精度、艺术用途的精细件
实体大件
铸造件设计
塑料件外形和机构设计
应用范围广泛
常用材料
热固性光敏树脂
纸、金属箔、塑料薄膜等
石蜡、塑料、金属、陶瓷粉末等
石蜡、塑料、低熔点金属等
各种材料粉末
表1几种典型的快速成型工艺比较
其他快速成型工艺
除以上五种方法外,其它许多快速成型方法也已经实用化,如实体自由成形(solidfreeformfabrication,SDM)、形状沉积制造(shapedepositionmanufacturing,SDM)、实体磨削固化(solidgroundcuring,SGC)、分割镶嵌(tessellation)、数码累计成型(digitalbricklaying,DBL)、三维焊接(threedimensionalwelding,3DW)、直接壳法(directshellproductioncasting,DSPC)、直接金属成型(directmetaldeposition,DMD)等快速成型工艺方法。
快速成型技术的应用
不断提高RP技术的应用水平是推动RP技术发展的重要方面。
目前,快速成型技术已在工业造型、机械制造、航空航天、军事、建筑、影视、家电、轻工、医学、考古、文化艺术、雕刻、首饰等领域都得到了广泛应用。
并且随着这一技术本身的发展,其应用领域将不断拓展。
RP技术的实际应用主要集中在以下几个方面:
(1)在新产品造型设计过程中的应用快速成形技术为工业产品的设计开发人员建立了一种崭新的产品开发模式。
运用RP技术能够快速、直接、精确地将设计思想转化为具有一定功能的实物模型(样件),这不仅缩短了开发周期,而且降低了开发费用,也使企业在激烈的市场竞争中占有先机。
(2)在机械制造领域的应用由于RP技术自身的特点,使得其在机械制造领域内,获得广泛的应用,多用于制造单件、小批量金属零件的制造。
有些特殊复杂制件,由于只需单件生产,或少于50件的小批量,一般均可用RP技术直接进行成型,成本低,周期短。
(3)快速模具制造传统的模具生产时间长,成本高。
将快速成型技术与传统的模具制造技术相结合,可以大大缩短模具制造的开发周期,提高生产率,是解决模具设计与制造薄弱环节的有效途径。
快速成形技术在模具制造方面的应用可分为直接制模和间接制模两种,直接制模是指采用RP技术直接堆积制造出模具,间接制模是先制出快速成型零件,再由零件复制得到所需要的模具。
(4)在医学领域的应用近几年来,人们对RP技术在医学领域的应用研究较多。
以医学影像数据为基础,利用RP技术制作人体器官模型,对外科手术有极大的应用价值。
(5)在文化艺术领域的应用在文化艺术领域,快速成形制造技术多用于艺术创作、文物复制、数字雕塑等。
(6)在航空航天技术领域的应用在航空航天领域中,空气动力学地面模拟实验(即风洞实验)是设计性能先进的天地往返系统(即航天飞机)所必不可少的重要环节。
该实验中所用的模型形状复杂、精度要求高、又具有流线型特性,采用RP技术,根据CAD模型,由RP设备自动完成实体模型,能够很好的保证模型质量。
(7)在家电行业的应用目前,快速成形系统在国内的家电行业上得到了很大程度的普及与应用,使许多家电企业走在了国内前列。
如:
广东的美的、华宝、科龙;
江苏的春兰、小天鹅;
青岛的海尔等,都先后采用快速成形系统来开发新产品,收到了很好的效果。
快速成形技术的应用很广泛,可以相信,随着快速成形制造技术的不断成熟和完善,它将会在越来越多的领域得到推广和应用。
快速成型存在的问题
材料问题
目前所使用的成型材料成型后的机械性能还不能满足零件的功能需要,必须经过后处理才能达到使用要求。
采用金属材料和高强度材料直接成型是RPM的一个重要发展方向。
美国Michigan大学的Manzumd采用大功率激光器进行金属熔焊直接成型钢质模具的研究。
成型精度和质量问题
目前快速成型制件的精度和表面质量大多不能满足工程使用要求,只能作为概念造型和功能测试的原型使用,必须改进成型工艺和快速成型软件。
美国Stanford大学的Prints采用逐层累加与五坐标数控加工结合的方法,用激光将金属直接烧结成型,可获得与数控加工相近的精度。
应用问题
从制造目标来说RPM主要用于:
快速概念设计及功能测试原型制造;
快速模具原型制造;
快速功能零件制造。
但大多数RPM是作为原型件进行新产品开发和功能测试等。
快速直接制模及快速功能零件制造是RPM面临的一个重大技术难题,也是RPM技术发展的一个重要方向。
根据不同的制造目标RPM技术将相对独立发展,更加趋于专业化。
软件问题
目前已商品化的软件还不完善,功能单一,通用性差,没有统一的数据接口,不易集成。
数据转换模型缺陷较多,对CAD模型的描述不够精确,从而影响子决速成型的成型梢度和表面质量。
快速成型技术的发展方向
快速成型技术虽然有其巨大的优越性,但是也有它的局限性,由于可成型材料有限,零件精度低,表面粗糙度高,原型零件的物理性能较差,成型机的价格较高,运行制作的成本高等,所以在一定程度上成为该技术的推广普及的瓶颈。
从目前国内外RP技术的研究和应用状况来看,快速成型技术的进一步研究和开发的方向主要表现在以下几个方面:
(1)开发性能好的快速成型材料,如成本低、易成形、变形小、强度高、耐久及无污染的成形材料。
(2)提高RP系统的加工速度和开拓并行制造的工艺方法。
(3)改善快速成形系统的可靠性,提高其生产率和制作大件能力,优化设备结构,尤其是提高成形件的精度、表面质量、力学和物理性能,为进一步进行模具加工和功能实验提供基础。
(4)开发快速成形的高性能RPM软件。
提高数据处理速度和精度,研究开发利用CAD原始数据直接切片的方法,减少由STL格式转换和切片处理过程所产生精度损失。
(5)开发新的成形能源。
(6)快速成形方法和工艺的改进和创新。
直接金属成形技术将会成为今后研究与应用的又—个热点。
(7)进行快速成形技术与CAD、CAE、RT、CAPP、CAM以及高精度自动测量、逆向工程的集成研究。
(8)提高网络化服务的研究力度,实现远程控制。
总结
快速成型技术是一种正在不断完善的先进制造技术,具有广泛的应用前景。
目前快速成型技术在欧美、日本等发达国家应用较为广泛,我国仅仅一些高等院校及有关厂家在吸收消化国外技术的基础上开发出了快速成型机,但是在质量和数量以及应用领域方面,都比不上国外。
总之快速成型技术是当今制造业赢得市场的法宝,快速成型技术以其独特的优势和魅力,在制造业领域起到越来越重要的作用,并将给制造业带来深远的影响。
参考文献:
[1]李涤尘,卢秉恒,赵万.快速成形的未来发展—快速产品制造[J].航空制造技术.
[2]董祥忠.特种成型与连接技术[M].化学工业出版社.
[3]杨继全,朱玉芳.先进制造技术[M].化学工业出版社.
[4]王光春,赵国群.快速成型与快速模具制造技术及其应用[M].机械工业出版社.
[5]郑启光,激光先进制造技术[M].华中科技大学出版社.
[6]刘伟军.快速成型技术与应用[M].北京机械工业出版社.