炼钢原理文档格式.docx
《炼钢原理文档格式.docx》由会员分享,可在线阅读,更多相关《炼钢原理文档格式.docx(19页珍藏版)》请在冰豆网上搜索。
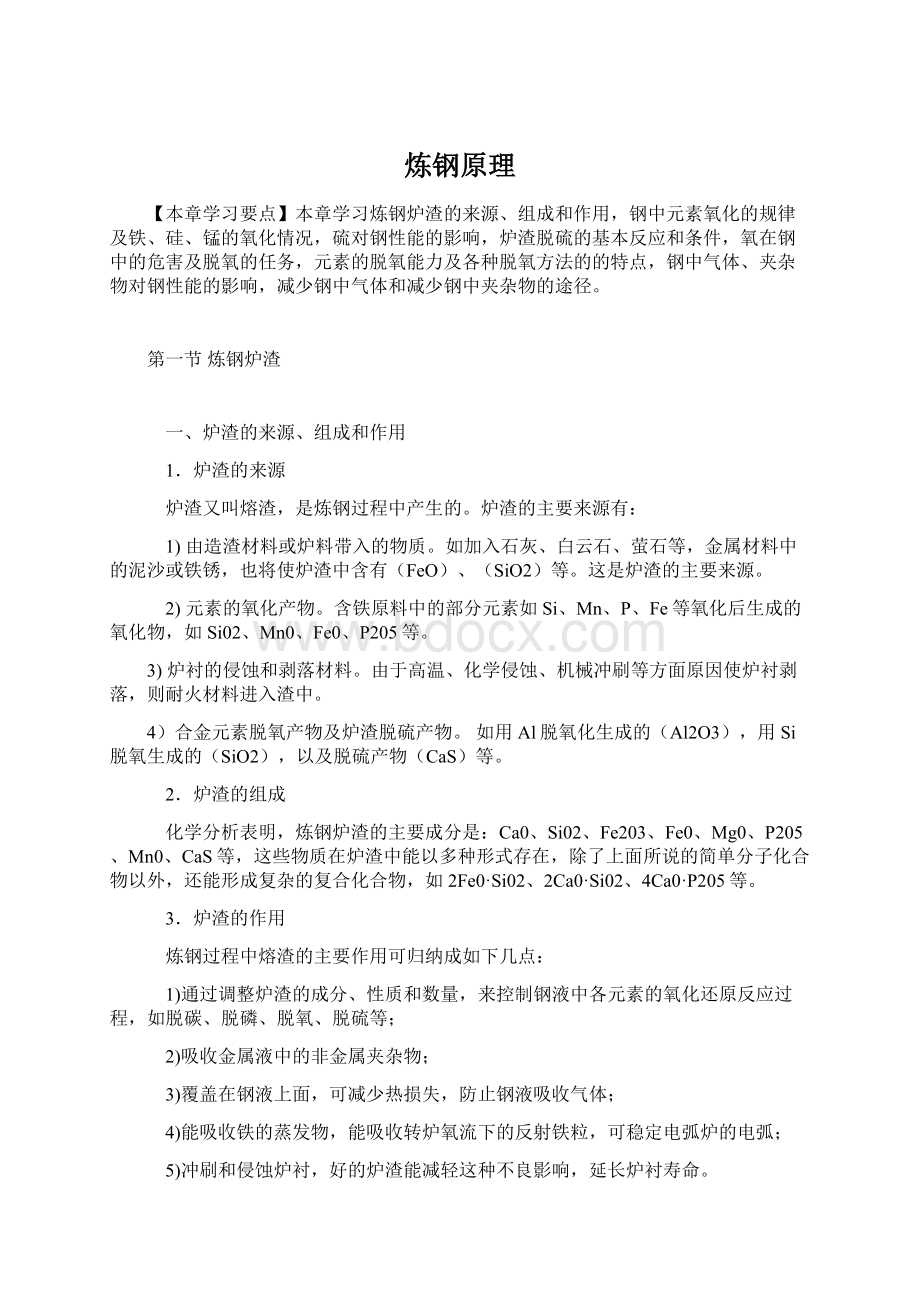
熔渣的物理性质主要是指炉渣的熔点和黏度。
为了准确描述反应物和产物所处的环境,规定用“[
]”表示其中的物质在金属液中,“(
)”表示在渣液中,“{
}”表示在气相中。
1.炉渣的化学性质
(1)熔渣的碱度
炉渣中常见的氧化物有酸、碱性之分,其分类如下:
碱度是指炉渣中碱性氧化物与酸性氧化物浓度的比值,用“R”来表示。
碱度是判断熔渣碱性强弱的指标。
去磷、去硫以及防止金属液吸收气体等都和熔渣的碱度有关,因此碱度是影响渣、钢反应的重要因素。
由于熔渣中Ca0和Si02的数量最多,约为渣量的60%以上,所以在熔渣含磷不高时,常以Ca0与Si02浓度之比表示熔渣的碱度,即:
R
若炉渣中含磷量较高,也可以表示为:
根据碱度高低,熔渣可分为三类:
1)R<
1酸性渣
2)R=1
中性渣
R<
1.5低碱度渣
3)R>
1碱性渣
R=1.8~2.2
中碱度渣
R>
2.5高碱度渣
(2)熔渣的氧化性
炉渣的氧化性是指熔渣所具备的氧化能力的大小。
它对炼钢过程中的成渣速度、去磷、去硫、喷溅、金属收得率和终点钢水含氧量等均有重大影响。
根据炉渣的分子理论,Fe0能同时存在于渣—钢之中,并在渣—钢之间建立一种平衡(FeO)/[FeO],所以一般认为渣中的氧是通过Fe0传递到钢液中的。
因而熔渣中的FeO含量便可代表熔渣所具备的氧化能力的大小,即熔渣的氧化性通常用渣中氧化亚铁总量乏(Fe0)表示。
渣中氧化铁含量即渣的氧化性,它对熔渣的反应能力及物理性能有重要的影响。
转炉熔渣Fe0过低,造渣困难,炉渣的反应能力低。
熔渣Fe0过高,又会造成喷溅,增加金属损失及炉衬侵蚀。
因此,渣中氧化铁的含量应适当,在转炉冶炼过程中,一般控制在10%~20%为好。
(3)熔渣的还原性
熔渣的还原性和氧化性是炉渣的同一种化学性质的两种不同说法。
在碱性电弧炉还原期操作中,要求炉渣具有高碱度、低氧化性、流动性好的特点,以达到钢液脱氧、去硫和减少合金元素烧损的目的。
所以应降低渣中的Fe0,提高渣的还原性。
电弧炉还原期出钢时,一般要求渣中的Fe0质量分数应小于0.5%,以满足出钢时对渣还原性的要求。
2.熔渣的物理性质
(1)熔渣的黏度
黏度是表示熔渣内部各部分质点间移动时的内摩擦力的大小。
黏度的单位是泊(P),1P=0.1Pa·
S(帕·
秒)。
黏度与流动性正好相反,黏度低则流动性好。
冶炼时,若熔渣的黏度过大,则物质在钢液及熔渣之间的传递缓慢,不利于炼钢反应的迅速进行;
但若黏度过小,又会加剧炉衬的侵蚀。
所以在炼钢时,希望获得适当黏度的炉渣。
影响熔渣黏度的主要因素是熔渣成分和温度。
凡是能降低炉渣熔点的成分均可以改善熔渣的流动性,降低渣的黏度;
熔池温度越高,渣的黏度越小,流动性越好。
实际操作中,黏度的调节主要是靠控制渣中的Fe0、碱度和加入萤石等来实现的。
(2)熔渣的熔点
熔渣是多元组成物,成分复杂,当它由固相转变成液相时,是逐渐进行的,不存在明显的熔点,其熔化过程有一个温度范围。
通常熔渣的熔点是指炉渣完全转变成均匀液体状态时的温度。
不同的氧化物和复合氧化物的熔点是不同的,炉渣中各种氧化物的熔点见表8—1。
表8—1
炉渣中各种氧化物的熔点
炉渣中最常见的氧化物大部分都有很高的熔点。
炼钢温度下,这些氧化物很难熔化。
但实际上,它们相互作用生成了各种复杂化合物,这些化合物的熔点低于原氧化物的熔点,从而降低了熔渣的熔点。
降低炉渣熔点的主要措施是:
加入一定的助熔剂,如矿石(Fe203)、萤石(CaF2)等,以便形成低熔点的多元系化合物。
第二节
铁、硅、锰的氧化
在炼钢过程中,氧供入金属熔池后,元素随即开始氧化。
无论是氧气顶吹转炉或是其它炼钢方法,元素的氧化速度可以不同,但都是按一定的次序进行的。
一般地讲,硅、锰最先被大量氧化,而碳随后被迅速氧化,磷的氧化基本上可与碳同时进行。
元素氧化具有不同次序的原因,是由于各元素与氧的亲和力不同,与氧亲和力强的元素可以夺取更多的氧,首先开始大量氧化;
反之,与氧亲和力弱的元素则夺得较小的氧,它的氧化就慢些。
1、当温度T<1400℃时,元素的氧化顺序是:
Si
Mn
C
P
Fe
2、当1400℃<T<1530℃时元素的氧化顺序是:
Si
3、当T>1530℃时,元素的氧化顺序是:
铁和氧的亲和力小于Si、Mn、P与氧的亲和力,但由于金属液中铁的浓度最大,质量分数为90%以上,所以铁最先被氧化,生成大量的Fe0,并通过Fe0使其与氧亲和力大的Si、Mn、P等被迅速氧化。
在转炉中,Si、Mn、P、Fe在冶炼初期的大量氧化,使熔池温度迅速上升,为碳的迅速氧化提供了有利条件;
同时也对炉渣的碱度和流动性等产生了较大的影响。
一、铁的氧化
铁的氧化反应是一个极其重要的氧化反应,它是其他元素进行氧化反应的基础。
向金属液供氧的方式有两种:
一是直接供氧,即吹入氧气;
二是间接供氧,且加入矿石。
因此铁的氧化方式也有两种:
直接氧化和间接氧化。
直接氧化是指钢液中的元素直接和氧分子进行接触,而被氧化的反应,如:
间接氧化反应是指金属液中的元素直接和氧原子或Fe0接触而被氧化的反应,如:
[Fe]+[O]=[FeO]
(放热)
铁被氧化后,其反应产物Fe0一部分进入炉渣,一部分继续存留在金属液中,并在金属液—熔渣之间建立动态平衡,它应服从分配定律,即
在一定温度下,
为一常数,称为氧在炉渣和金属液中的分配系数。
二、硅的氧化
1.硅的氧化反应式
在碱性炼钢法中,Si的氧化对成渣过程、炉衬的侵蚀等都有重要的影响。
理论上Si的氧化反应也有直接氧化和间接氧化之分,但实际上,金属液中的Si、Mn元素很难直接与气态氧反应,所以金属液中Si、Mn、P元素的氧化均以间接氧化反应为主。
硅的间接氧化反应式如下:
Si的氧化产物
只溶于渣,不溶于钢液。
2.Si氧化反应的主要特点
Si氧化反应的主要特点如下:
1)由于Si与氧的亲和力很强,所以在冶炼初期,金属液中的Si便已基本氧化完毕。
例如:
转炉吹氧3min后,Si基本上全被氧化。
同时,由于Si的氧化产物Si02,在炉渣中完全被碱性氧化物如Ca0等结合,无法被还原出来,因此硅的氧化是十分完全彻底的,最后只有微量的硅残留在钢液中。
2)Si氧化反应是一个强烈的放热反应,低温有利于Si氧化反应的迅速进行。
Si是转炉吹炼过程中重要的发热元素。
目前在转炉生产中,为了减少渣量,降低热损失,并提高金属收得率,已在广泛推广使用低Si铁水(叫[Si]<
0.3%),由降低铁水[Si]所失去的部分化学热,正在靠其他方法来解决,如提高铁水温度等。
三、锰的氧化
1.Mn的间接氧化反应式
[Mn]+(FeO)=(MnO)+(Fe)
放热
[Mn]+[FeO]=(MnO)+[Fe]
Mn的氧化产物只溶于渣,不溶于钢液。
2.Mn氧化的特点
Mn氧化有以下特点:
1)Mn的氧化反应是放热反应,低温有利于Mn的氧化,故Mn的氧化主要在冶炼前期进行。
2)由于氧化产物Mn0是碱性氧化物,故碱性渣中不利于Mn的氧化。
因此Mn不可能向Si那样完全被氧化。
3)当熔池温度升高后,Mn的氧化反应会逆向进行,发生Mn的还原,即产生“回锰”现象,使钢液中的“余锰”增加。
碳的氧化
碳的氧化反应是贯穿整个炼钢过程的一个最重要的反应,它是完成诸多炼钢任务的一个重要手段。
一、碳的氧化反应
1.氧气流股与金属液间的C—O反应
该反应放出大量的热,是转炉炼钢的重要热源。
在转炉炼钢的氧流冲击区及电炉、平炉炼钢采用氧管插入钢液吹氧脱碳时,氧气流股直接作用于钢液,均会发生此类反应。
脱碳示意图分别如图8—1和图8—2所示。
流股中的气体氧{02}与钢液中的碳原子[C]直接接触,反应生成气体产物一氧化碳{CO},脱碳速度受供氧强度的直接影响,供氧强度越大,脱碳速度越快。
图8—1
熔池吹氧示意图(吹氧脱碳操作)
图8—2
氧气顶吹转炉氧射流与熔池相互作用示意图
2.金属熔池内部的C—O反应
[C]+[FeO]={CO}+[Fe]
+7600J
该反应为弱放热反应,温度降低有利于反应的进行。
在转炉和电炉炼钢吹氧脱碳时,气体氧{02}会使金属熔池内铁原子[Fe]大量氧化成[FeO],金属液中的[C]与[FeO]接触反应,从而起到间接脱碳的作用。
3.金属液与渣液界面的C—O反应
在转炉泡沫渣和采用矿石脱碳的电炉渣内均含有大量的(Fe0),渣中的(FeO)通过渣—钢接触界面向钢液中扩散,然后与钢液中的碳原子反应生成一氧化碳气体。
反应式如下:
[C]+(FeO)={CO}+[Fe]
-75100J
所谓泡沫渣是转炉炼钢吹氧脱碳时钢液—熔渣—炉气三相物质混合乳化而形成的乳浊液。
在泡沫渣中,钢液被粉碎成很细小的小液滴,使钢—渣的接触界面积大大增加,这是泡沫渣中脱碳速度很快的原因。
电炉采用矿石脱碳的基本条件是:
1)Fe0要多,以满足氧化性要求。
即必须保证一定的矿石加入量;
2)熔池温度要高,因为矿石熔化及(FeO)进入钢液中是强吸热反应;
3)炉渣流动性要好,以满足扩散要求;
4)炉底要经常维护,以便于C0气泡在粗糙的炉底和炉壁处形成。
二、碳氧反应在炼钢过程中的作用
把钢液中的碳含量氧化降低到所炼钢号的规格内。
这是炼钢的任务之一。
碳氧反应时产生大量的C0气泡,这些气泡从钢液中排出时,对熔池有一种强烈的搅拌作用,它均匀了钢液的成分和温度,改善了各种化学反应的动力学条件,有利于炼钢中各种化学反应的进行。
碳氧反应产物C0气泡,对于钢液中的N、H相当于一个小真空室,钢液中的气体很容易扩散到这些上浮的C0气泡中,并随之排除到大气之中,所以脱碳反应是去除钢中气体所必需的手段之一。
非金属夹杂物上浮的速度主要取决于非金属夹杂物的大小。
碳氧反应对熔池的搅拌作用促进了非金属夹杂物的碰撞长大,从而显著地提高了上浮速度。
另外,C0气泡表面也可粘附一部分非金属夹杂物使其上浮入渣。
所以,碳氧反应是去除钢中夹杂物所必需的手段之一。
碳的氧化反应放出大量的热,是氧气转炉炼钢的重要热源。
同时,由于C0气泡的大量产生,使转炉内产生大量的泡沫渣,增加了钢—渣接触面积,有助于反应速度的提高。
第四节
脱
磷
一、磷对钢性能的影响
磷在钢中以磷化铁的形式存在,一般用[P]表示。
它对钢性能的具体影响是:
1)能恶化钢的焊接性能;
2)降低钢的塑性和韧性,使钢产生冷脆性,即在低温条件下钢的冲击韧性明显降低;
3)能提高易切削钢的切削性能;
4)能改善钢液的流动性,提高钢液的铸造性能;
5)能提高合金钢耐大气和海水的腐蚀能力;
6)能提高电工用硅钢的导磁率。
对绝大多数钢种而言,[P]是一种有害元素。
二、脱磷反应的基本条件和方法
将钢中的磷脱除到要求的范围内,是炼钢的任务之一。
1.脱磷的基本反应
2[P]+5(FeO)+4(CaO)=(4CaO·
P2O5)+5[Fe]
从反应式中可以看出:
较低的温度、高(FeO)、高(CaO)有利于脱磷反应的进行。
2.脱磷的基本条件和方法
1)炉渣的碱度要适当高,流动性要好。
研究结果认为,脱磷时的炉渣碱度控制在2.5~3最好。
2)适当提高炉渣的氧化性,即渣中的氧化铁要高。
3)适当的温度。
尽管低温有利于放热反应的进行,但低温不利于石灰的熔化,不利于扩散反应的进行,从而最终还将影响到脱磷反应速度。
所以,为了获得最佳的脱磷效果,熔池应有适当的温度,不能太高也不能太低。
4)大渣量是提高脱磷效果的有效方法之一。
对于电炉来说,采用自动流渣的方法,放旧渣、造新渣就是大渣量的另一种操作形式。
三、回磷
回磷是指冶炼后期钢液中磷含量比中期有所回升,以及成品钢中的含磷量比冶炼终点钢水含磷量高的现象。
1.回磷的原因
1)炉温过高会使脱磷反应逆向进行。
2)冶炼终了以及出钢时,向炉内或钢包内加入铁合金等脱氧,会使渣中的
∑(FeO)大大降低,同时,脱氧产物如
等也会使炉渣碱度大大降低,使脱磷反应逆向进行。
3)铁合金本身带入一定数量的磷。
在上述几种原因中,以∑(FeO)的降低对回磷影响最为显著,而碱度和温度的影响要小些。
2.防止回磷的办法
对于电炉而言,防止还原期回磷的主要措施是扒净氧化渣。
对于转炉而言,防止钢包回磷的主要措施是防止下渣,即防止炉渣进入到钢包中。
生产中常用的办法是:
1)出钢前向炉内加入石灰稠化终渣,同时,进行挡渣出钢。
2)出钢过程中,向钢包内投入少量石灰粉,稠化钢包内的渣,保持碱度。
第五节
硫
一、硫对钢性能的影响
硫在钢中多以硫化物形式存在,如FeS、MnS等,硫对钢性能产生以下影响:
1)使钢产生热脆现象。
所谓热脆现象是指钢坯或钢锭在高温条件下(如1100℃)进行轧制时,会产生断裂的现象。
2)对钢的力学性能产生不利影响。
3)使钢的焊接性能降低。
4)能改善易切削钢的切削性能。
5)使钢的耐腐蚀性能降低。
由于硫对绝大多数钢种而言是有害的,所以脱硫是炼钢的主要任务之一。
二、炉渣脱硫
1.炉渣脱硫的基本反应式
[FeS]=(FeS)
+)
(CaO)+(FeS)=(CaS)+(FeO)
(CaO)+[FeS]=(CaS)+(FeO)
(吸热)
从反应式中可以看出,脱硫的基本条件是:
高碱度、高温、低氧化性。
2.影响脱硫反应的基本条件分析
(1)炉渣碱度研究结果表明:
炉渣碱度在3.0~3.5之间最好,过高会使黏度增加,不利硫在钢—渣之间的扩散,过低则不符合脱硫要求。
(2)氧化性炉渣氧化性对脱硫的影响较为复杂,从脱硫反应式中可以看出,渣中的还原性越强,即∑(FeO)越低越有利于脱硫反应。
但实际生产中氧气转炉的氧化渣中也能去除一部分硫,其主要原因是:
∑(FeO)的存在改善了渣的流动性,能促进石灰的熔化,有利于高碱度渣的形成,从而部分改善了脱硫条件。
尽管氧化渣中也能脱硫,但在其他条件如搅拌、温度、碱度等完全相同的条件下,氧化渣的去硫效果还是远远低于还原渣的。
(3)温度
高温有利于吸热反应的进行,即有利于去硫反应的顺利进行。
(4)钢—渣搅拌情况
去硫是钢—渣界面反应,加强钢—渣搅拌扩大反应界面积有利于去硫。
例如电炉(还原期)出钢时,采用钢—渣混出的方法,使钢液和炉渣强烈混合,钢—渣界面大大增加,充分发挥了电炉还原渣的脱硫能力,使脱硫反应能够迅速进行。
(5)渣量
增加渣量可以减少(CaS)的相对浓度,可促进去硫反应。
三、气化去硫
根据硫的平衡及炉气分析得知,氧气转炉炼钢过程中钢液的硫一部分是以气体状态去除的,其去硫量一般占总去硫量的10%~40%。
由于硫和氧的亲和力比碳、硅和氧的亲和力都低,在金属液中有碳存在时,硫的直接氧化的可能性很小,所以气化去硫是通过炉渣进行的。
气化去硫的反应式如下:
从上式也可以看出:
硫必须首先从钢液中进入熔渣,才有可能气化去除。
所以钢—渣间的去硫反应是气化去硫的基础。
另外还可以看出:
高碱度渣对气化去硫不利。
实践证明:
只要造成流动性良好的碱性渣,就会有一定的气化去硫效果。
实践操作还表明:
炉渣氧化性增大,能强化气化去硫。
第六节
脱氧
一、脱氧的原理和任务
1.氧的危害
各种炼钢方法中,都是利用氧化法来去除钢中的大部分杂质元素和有害物质。
这就使氧化后期钢中溶入了过量的氧。
例如氧气转炉终点ω[C]<
0.1%时,钢中氧ω[O]一般为0.035%~0.069%,而此成分下固体钢中最多只能溶解0.003%的氧。
这些多余的氧在钢液凝固时将逐渐从钢液中析出,形成夹杂物或气泡,严重影响钢的性能,其具体表现是:
1)严重降低钢的力学性能,尤其是塑性和韧性。
2)大量气泡的产生影响浇注的正常进行,将会破坏锭或坯的合理结构,严重影响钢锭质量,甚至造成废品。
3)钢中的氧能加剧硫的热脆危害。
2.脱氧的原理和任务
炼钢过程中脱氧的原理是:
利用对氧的亲和力比Fe大的元素,如Mn、Si、Al等,把钢液中的氧夺走,形成不残留在钢液中的脱氧产物如Mn0、
、
等并上浮到渣中。
能用来对钢液脱氧的元素或合金叫脱氧剂。
脱氧的目的在于降低钢中的氧含量,脱氧的任务是:
1)降低钢液中溶解的氧,把氧转变成难溶于钢液的氧化物如Mn0、
等。
2)将脱氧产物排出钢液之外。
否则钢液中的氧只是改变了存在形式,总含氧量并没有降低,氧对钢的危害依然存在。
3)脱氧时还要完成调整钢液成分和合金化的任务。
二、各种元素的脱氧能力
1.对脱氧元素的要求
1)脱氧元素与氧的亲和力应大于Fe与氧的亲和力,即脱氧产物(MeO)在钢液中应比FeO稳定。
2)脱氧产物MeO在钢液中溶解度应非常低,否则便以另一种形式保留在钢中,未达到脱氧的目的。
3)脱氧产物的密度应小于钢液密度,且熔点应较低,在钢液中应以液态形式存在,这样脱氧产物才容易集聚长大,并能迅速地上浮到熔渣中,完成脱氧任务。
4)未与氧结合的剩余脱氧元素,应该对钢的性能无不良影响,甚至还应产生有利影响。
2.元素的脱氧能力
元素的脱氧能力是指在一定温度和一定浓度的脱氧元素呈平衡的钢中溶解的氧含量。
显然和一定浓度的脱氧元素呈平衡的氧含量越低,这种元素的脱氧能力越强。
在1600℃时,元素的脱氧能力按以下顺序增强:
Cr、Mn、V、P、Si、C、B、Ti、Al、Mg、Ca。
其中最常用的是Mn、Si、Al。
3.常用的脱氧剂
(1)Mn
它的脱氧能力较低,但几乎所有的钢都用Mn来脱氧,因为它可以增加Si和A1的脱氧作用。
此外(MnO)可以与其他的脱氧产物如
等形成低熔点化合物,有利于从钢液中排出。
冶炼沸腾钢时,只用锰脱氧。
(2)Si
Si是一种较强的脱氧元素,它是镇静钢中不可缺少的脱氧元素之一。
Si的脱氧能力高于Mn。
Si的脱氧能力受温度影响而发生变化,温度越高,Si的脱氧能力越弱。
Si的脱氧产物
熔点高(1700度),不易从钢液中上浮排出,所以应与Mn一起使用。
(3)A1
A1是钢中常用的而且是非常强的脱氧元素,它是镇静钢中不可缺少的脱氧元素之一。
A1的脱氧产物
熔点很高(2050℃),形成很细小的固体颗粒,
颗粒表面与钢液间界面张力大,易于上浮,所以常用来做终脱氧剂。
目前炼钢生产中常用的块状脱氧剂有:
锰铁、硅铁、铝、硅锰合金等。
电弧炉还原期炉渣脱氧时常用的粉状脱氧剂有:
碳粉、碳化硅粉、硅铁粉等。
真空脱碳时,钢液中[C]是脱氧剂。
使用块状脱氧剂时,一般用复合脱氧剂最好,因为复合脱氧剂的脱氧能力以及脱氧产物的上浮能力都很强。
若无复合脱氧剂而单独使用各脱氧剂时,应注意脱氧剂的加入顺序,一般情况是先弱后强,即先用锰铁脱氧,再用硅铁脱氧,最后用铝脱氧。
因为先加锰铁后形成的Mn0可提高Si、Al的脱氧效果,同时也有利于几种脱氧产物形成低熔点化合物,从而有利于脱氧产物的上浮。
三、脱氧方法
钢液的脱氧方法有三种:
沉淀脱氧法、炉渣脱氧法和真空脱氧法。
1.沉淀脱氧法
沉淀脱氧法又叫强制脱氧法或直接脱氧法。
它是把块状脱氧剂,如锰铁、硅铁和铝饼等加入钢液内,直接使钢液脱氧。
其反应式可表示为:
[FeO]+[Me]=[Fe]+[MeO]
[MeO]=(MeO)
式中
Me——脱氧元素;
Me0——脱氧产物。
这种脱氧方法的优点是操作简便,脱氧速度快,节省时间,成本低。
其缺点是部分脱氧产物来不及上浮而进入熔渣中,残留在钢液内污染了钢液,影响了钢液的纯净度,使提高钢的质量受到一定的限制。
因此,假若不采取炉外精炼等其他措施,靠这种方法脱氧的转炉就不能